
Методическое пособие 773
.pdf
41
шипниками. Свободные концы начальной и конечной секций желоба закрыты торцевыми стенками, на которых установлены опоры 2 и 4. Подшипник опоры 4 выполнен как упорный и предназначен для восприятия осевой силы шнека. Подшипник опоры 2 – проходной, для соединения шнека с помощью муфты 8 с выходным валом редуктора 6. Если шнек конвейера будет реверсироваться, подшипник 2 должен быть радиально-упорным. Начальная секция желоба имеет на крышке загрузочную воронку 10, а конечная секция – разгрузочную воронку 12 в днище желоба. Промежуточные разгрузочные воронки с затворами могут быть установлены на любых секциях в соответствии с технологическим процессом.
Шнек для удобства сборки также состоит из секций. Вал шнека выполняется из трубы, к которой крепится винтовая поверхность. Так как винтовая поверхность не раскладывается на плоскость, ее выполняют отдельными фрагментами из листовой стали толщиной 3 – 6 мм и соединяют сваркой между собой и с валом. Винтовая поверхность может быть сплошной (рис. 2.14,а) для транспортирования сухих порошковых и мелкозернистых грузов; в виде ленты (рис. 2.14,б) – для мелкокусковых грузов; в виде фасонной спирали (рис. 2.14,в) - для тестообразных грузов или в виде отдельных лопастей (рис. 2.14,г) – для тестообразных грузов с одновременным интенсивным их перемешиванием.
Рис. 2.14. Виды винтов: а – с сплошной винтовой поверхностью; б - с винтовой поверхностью в виде ленты; в - с винтовой поверхностью в виде фасонной спирали; г - с винтовой поверхностью в виде отдельных лопастей
Радиальный зазор между желобом и шнеком выполняют в зависимости от характера транспортируемого материала в диапазоне от 3 до 8 мм. По числу спиралей шнеки могут быть одно-, двух- и трехзаходными. Для транспортирования грузов шнеки имеют спирали одного направления – правого или левого, при смешивании грузов - разных направлений (рис. 2.15).

42
а)
б)
Рис. 2.15. Схемы винтовых конвейеров: а) для транспортирования; б) перемешивания грузов
Подвесные опоры шнека должны быть небольшого диаметра и длины. Расположенные в них подшипники должны быть хорошо защищены от проникновения транспортируемого материала и иметь смазочные устройства. Это требование распространяется и на подшипниковые узлы концевых опор.
В приводе горизонтальных конвейеров используются серийные цилиндрические редукторы с разнесенными или соосными валами. В последнем случае привод получается более компактным. Привод наклонных конвейеров выполняют с конической передачей для обеспечения горизонтального расположения редуктора, которое необходимо для проектного функционирования его смазочной системы.
Параметры винтового конвейера, которые характеризуют его типоразмер, определяют по заданной производительности и характеру транспортируемого груза.
Производительность конвейера связана с его конструктивными параметрами формулой
П =3600 S Vмγ c, |
т/ч, |
(2.25) |
где S – площадь потока материала в конвейере, м2; Vм – скорость этого |
||
потока, м/с; γ – насыпная плотность материала, |
т/м3; |
c – коэффициент сниже- |
ния производительности наклонного конвейера.
Площадь потока материала в конвейере S составляет небольшую часть площади поперечного сечения шнека. На рис. 2.16 показано рекомендуемое заполнение площади сечения шнека для различных грузов. Заполнение характеризуется коэффициентом Ψ, величину которого следует принимать для легких неабразивных грузов - 0,4; для легких малоабразивных грузов - 0,32; для тя-

43 |
|
желых малоабразивных - 0,25; для тяжелых абразивных – 0,125. |
Величину |
S можно вычислить по формуле |
|
S = ΨπD2/4 =0,785Ψ D2 , м2, |
(2.26) |
где D – внешний диаметр шнека. |
|
Рис. 2.16. Рекомендуемое заполнение площади сечения шнека для различных грузов
Скорость потока материала V зависит от частоты вращения шнека nш (мин-1) и шага винтовой линии tш (м) согласно выражению
V = tш nш /60 , м/с. |
(2.27) |
Частота вращения шнека обычно составляет 50…150 об/мин и зависит от характера груза: тяжелый, тестообразный или легкий, сыпучий соответственно.
Шаг винтовой линии и диаметр шнека определяют угол подъема винтовой линии, а угол ее подъема α с учетом угла наклона всего конвейера должен быть таким, чтобы транспортируемый материал не увлекался лопастью винта во вращательное движение вокруг оси шнека и при этом обеспечивалась максимальная скорость потока материала. Это условие может выполняться при tgα< f, где f – коэффициент трения материала по лопастям шнека.
Опыт транспортирования строительных грузов винтовыми конвейерами определил рациональное соотношение параметров шнека: для горизонтальных конвейеров tш = D, для наклонных – tш = 0,8 D. Диаметры шнеков стандартизированы от 100 мм до 600 мм и должны соответствовать крупности кусков перемещаемого материала: D ≥ 12а – для сортированного, D ≥ 5а – для рядового грузов. Здесь а – размер максимального куска транспортируемого груза. Частоту вращения шнека рекомендуется назначать при транспортировании легких сыпучих грузов до150 мин-1, для кусковых – до 100 мин-1, для тяжелых и тестообразных грузов – до 50 мин-1.
Мощность привода винтового конвейера затрачивается на преодоление следующих сопротивлений передвижению груза в конвейере:
-усилия вдоль винта для подъема груза;
-сил трения груза о желоб;
-усилия вдоль винта вследствие момента трения винта о груз;
44
-усилия, эквивалентного моменту трения в подшипниках;
-внутреннего трения в перемещаемом материале при свободном его передвижение и в местах его скопления возле подвесных подшипников.
Ориентировочную мощность двигателя винтового конвейера можно определить по формуле
N = k П ( L ± H ) /367 , кВт, |
(2.28) |
где k – коэффициент запаса; L – длина конвейера, м; |
– коэффициент |
сопротивления движению: = 4 для тяжелых абразивных грузов ( песок, цемент ); = 2,5 (сухая глина, соль, уголь); = 1,4 для легких сыпучих грузов; Н – высота транспортирования, м; – КПД привода.
Более подробно теоретический материал по винтовым конвейерам изло-
жен в [3, с. 456…463; 4, с.195…205].
2.6. СКРЕБКОВЫЕ КОНВЕЙЕРЫ
Скребковым конвейером называют машины непрерывного транспорта, в которых перемещение грузов осуществляется волочением их по специальному желобу скребками, прикрепленными к цепному тяговому органу.
Скребковые конвейеры применяют для транспортирования хорошо сыпучих зернистых и мелкокусковых грузов: угля, цемента, удобрений, золы, древесных отходов, строительных смесей, их компонентов и т.д. на расстояние до 100 м со скоростью, не превышающей 1 м/с.
Скребковые конвейеры обладают рядом таких положительных свойств, как простота конструкции, возможность транспортировки по сложным трассам и под значительным углом к горизонту вплоть до вертикального перемещения, загрузка и разгрузка в любом месте трассы, возможность герметизации опасного груза при его транспортировании, одновременное перемещение грузов в противоположных направлениях, транспортирование горячих грузов.
К недостаткам этих конвейеров можно отнести их невысокий КПД из-за потерь на трение материала о стенки желоба, истирание, измельчение транспортируемого материала, быстрое изнашивание направляющего желоба, тяговых цепей, скребков, повышенный шум.
Классификация скребковых конвейеров представлена в табл. 2.8.
Конструкция скребкового конвейера предполагает наличие у него сле-
дующих элементов (рис. 2.17): направляющего желоба 1, тягового органа 2, скребков 3, приводной станции с ведущей звездочкой 4, натяжной станции со звездочкой 5, загрузочного бункера 6, разгрузочной воронки 7.
Направляющий желоб промышленного конвейера выполняется из стального листа толщиной 4…6 мм отдельными сварными или штампованными секциями длиной по 3…6 м. Поперечное сечение желоба может быть прямоугольным, трапецеидальным, полукруглым или круглым.
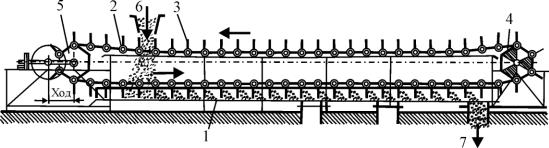
|
45 |
|
|
Таблица 2.8 |
|
Классификация скребковых конвейеров |
||
|
|
|
Признак классификации |
Характеристика конвейера |
|
|
С высокими, с низкими, с контурными |
|
Конструкция |
скребками, трубчатые, ящичные, штан- |
|
|
гово-скребковые, ершовые |
|
Вид трассы |
Горизонтальная, наклонная, вертикаль- |
|
ная, пространственная |
|
|
|
|
|
Расположение рабочих ветвей |
Нижняя, верхняя, обе рабочие |
|
Способ перемещения груза |
Порционного волочения, сплошного во- |
|
лочения |
|
|
|
|
|
Количество тяговых цепей |
Одна, две, три |
|
Положение плоскости движения |
Вертикальная, горизонтальная |
|
цепи |
|
|
|
|
|
|
Стационарный, передвижной, перенос- |
|
Способ установки |
ной, разборный, подвесной, поворотный, |
|
|
встроенный в машину |
|
Рис. 2.17. Схема скребкового конвейера
Стыки секций должны быть надежно уплотнены и не должны иметь уступов. Для повышения долговечности желоба его рабочие поверхности делают съемными для замены или восстановления, футеруют износостойким материалом (каменным литьем, шлакоситаллом). Ширина желоба должна в 3…5 раз превышать размер соответственно наибольших и средних кусков транспортируемого материала.
Тяговым органом в скребковых конвейерах могут служить цепи различного типа, стальные канаты или ленты. Их назначение – передавать тяговое усилие от приводной станции к скребкам для перемещения груза. Наибольшее распространение получили пластинчатые и длиннозвенные цепи благодаря своей прочности, гибкости, достаточной износостойкости и удобству крепления к ним скребков, возможности комплектовать специальные звенья со звеньями приводных роликовых цепей по ГОСТ 13568. Недостатками цепей можно признать их значительную массу, высокую стоимость, повышенные динамические нагрузки. На рис. 2.18 показаны некоторые виды цепей специального исполнения для скребковых конвейеров.

46
Рис. 2.18. Тяговые цепи: а) втулочно-роликовая; б) втулочно-катковая; в) разборная пластинчатая; г) вильчатая
Применение втулочно-катковых цепей снижает сопротивление движению и износ опорных элементов в конвейере, но требует дополнительного ухода за состоянием смазки подшипниковых узлов в катках, очистке направляющих путей катков.
Основными характеристиками цепей являются: разрушающая нагрузка, шаг цепи по осям роликов, шаг установки скребков.
Рабочим органом в зависимости от рода транспортируемого груза служат скребки, планки, прутки, пластины.
Скребки изготавливают из листовой стали толщиной 3…8 мм и усиливают их ребрами жесткости путем штамповки или приварки прокатных профилей (рис. 2.19). В зависимости от способа перемещения груза различают скребки для порционного или сплошного волочения. Скребки для сплошного волочения называют погружными скребками и выполняют их сплошными или контурными (рис. 2.19,в,г). Скребки для порционного волочения (рис. 2.19,а,б) различают высокие и низкие. У высоких скребков отношение ширины скребка b к его высоте h составляет b/h = 2…3. У низких скребков это отношение не превышает 1,6. Наружный контур скребков должен соответствовать внутреннему контуру сечения желоба. Зазор между кромкой скребка и внутренними поверхностями желоба принимают в зависимости от вида и крупности кусков перемещаемого материала 3…8 мм. Шаг установки скребков (1…3)b или два шага цепи. Размеры скребка определяются перемещаемым материалом и производительностью конвейера.

47
Рис. 2.19. Разновидности скребков: а) консольный; б) из прорезиненного ремня; в) контурный; г) дисковый
Приводная станция скребкового конвейера выполняется по схеме, принятой для всех конвейеров, имеющих цепной тяговый орган. На рис. 2.20 показана кинематическая схема такой приводной станции, состоящей из электродвигателя 1, клиноременной передачи 2, редуктора 3, муфты 4, приводного вала 5 со звездочками 6.
Рис. 2.20. Кинематическая схема приводной станции скребкового конвейера
Для взрывоопасных условий работы применяют пневматический привод. Соединение двигателя с редуктором можно осуществлять втулочно-пальцевой муфтой или гидромуфтой. Выходной вал редуктора с приводным валом конвейера обычно соединяется зубчатой муфтой или цепной передачей. Число зубьев z звездочек лучше принимать меньшим и четным, хотя при z <10 в приводе возрастают динамические нагрузки. Для предохранения приводной стан-
48
ции от поломок при образовании заторов и заклинивании кусков груза в зазорах необходимо предусматривать установку предохранительных устройств (срезных штифтов, муфт предельного момента).
Натяжная станция в скребковом конвейере должна обеспечить надежное взаимодействие ведущей звездочки с цепным тяговым органом. Кроме этого натяжение тягового органа должно быть таким, чтобы обеспечивалось устойчивое положение скребков и исключалось их опрокидывание при консольном приложении к ним нагрузки. Чтобы этого не происходило, момент силы натяжения цепи относительно шарнира звена цепи должен быть больше момента силы сопротивления относительно того же шарнира. Натяжное устройство может быть винтовым или пружинно-винтовым. В последнем случае обеспечивается защита от поломок при заклинивании кусков груза между скребком и желобом. Минимальный ход натяжной звездочки должен быть не менее 1,6 шага цепи.
Устройство загрузки и разгрузки представляет собой крутонаклонный лоток, по которому крупнокусковый материал поступает непосредственно на рабочую ветвь сбоку, мелкокусковый – сверху через холостую ветвь. Для разгрузки рабочей ветви используют отверстия в днище желоба или через лотки боковой разгрузки. Разгрузочные отверстия запирают шиберными затворами, управляемыми электромеханическими, гидравлическими или пневматическими приводами.
Определение параметров скребкового конвейера базируется на принци-
пах, которые характерны для конвейеров с замкнутым кольцевым тяговым органом. Основными параметрами, характеризующими скребковый конвейер, являются: производительность П, дальность L, высота транспортирования Н, ширина В, скорость перемещения скребков Vто, их размеры b, h, мощность привода N, передаточное число приводного редуктора iр, усилие натяжения тягового органа Fто и др. Первые три параметра обычно задаются проектным заданием, на основе которого выбираются, назначаются, рассчитываются все остальные.
Производительность скребкового конвейера в общем случае определяет-
ся так же, как и для любого другого конвейера при транспортировании сыпучих материалов:
П = 3600 S Vто , м³/ч, |
(2.29) |
или |
|
Q = 3600 S Vто γ , т/ч, |
(2.30) |
где γ – насыпная плотность материала, т/м³; S - площадь поперечного сечения потока материала, м².
Скорость тягового органа Vто назначается от 0,15 до 1,5 м/с в зависимости от вида и крупности кусков транспортируемого материала. Для хрупких и крупнокусковых материалов скорость транспортирования имеет меньшую величину.
Площадь поперечного сечения потока материала в желобе определяют по заданной производительности конвейера, в соответствии с которой назнача-

49
ют такие конструктивные параметры желоба и скребков, чтобы выполнялось условие
S = Bжhж , м2, |
(2.31) |
где Bж и hж – рабочая ширина и высота желоба для конвейера с высокими скребками, м; – коэффициент использования объема желоба, зависящий от угла наклона конвейера и сыпучести транспортируемого материала. При угле наклона 0° для легкосыпучих материалов ≈ 0,55; для плохосыпучих – ≈ 0,75; при угле наклона 30° для легкосыпучих ≈ 0,28; для плохосыпучих -≈ 0,56. Ширину желоба предварительно можно принять по соотношению
|
|
|
|
Bж = (2,4 4)S , |
(2.32) |
где S вычисляется по формуле (2.31). Большее значение коэффициента в подкоренном выражении принимается для двухцепных конвейеров. Значение Bж округляют до ближайшего большего из ряда предпочтительных чисел. Оно также должно удовлетворять условию, учитывающему кусковатость груза:
Bж ≥ 3 а –для рядовых грузов; Bж ≥ 3,5 а –для сортированных грузов. Тяговый орган (цепь) скребкового конвейера выбирают по разрушающей
нагрузке Fр на одну цепь при коэффициенте запаса kзап = 6…10 (для конвейеров ответственного назначения принимаются большие значения коэффициента запаса) и коэффициенте неравномерности нагрузки в двухцепном конвейере kнр = 1,8
Fр = Fмах kзап / kнр . |
(2.33) |
Максимальную нагрузку Fмах , действующую на тяговый орган конвейера, находят методом обхода по контуру, начиная с точки минимального натяжения цепей. Величину минимального натяжения Fmin для конвейеров с высокими скребками задают из условия отклонения скребков от вертикали на угол не более = 2…3° под действием силы для перемещения порции груза перед скребком:
Fmin = W hl / (z tg θ), Н, |
(2.34) |
где W = m wгр – сила сопротивления движению порции груза массой m перед скребком; hl – плечо приложения силы W; z – шаг цепи; wгр – коэффициент сопротивления движению груза в желобе, величина которого для большинства строительных материалов составляет 0,6 – 0,9.
Угоризонтальных конвейеров Fmin имеет место в точке сбегания цепи с приводной звездочки (рис. 2.21).
Унаклонных и комбинированных конвейеров с наклонной хвостовой частью (рис. 2.22) минимальное натяжение цепи зависит от соотношения длин
проекций наклонного участка на горизонталь lг , на вертикаль lв и коэффициента сопротивления движению опорных частей тяговой цепи wц. Для цепей без катков wц ≈ 0,25, для цепей с ходовыми катками wц ≈ 0,12.

50
Рис. 2.21. Схема горизонтального конвейера
Рис. 2.22. Схемы наклонного (а), комбинированного с наклонной хвостовой частью (б) и комбинированного с горизонтальной хвостовой частью (в) скребковых конвейеров
Если
lг • wц > lв , то минимальное натяжение цепи будет на сбегающей ветви приводной звездочки – точка 1;
lг • wц < lв - минимальное натяжение цепи будет на набегающей ветви натяжной звездочки – точка 2.
Для комбинированных конвейеров с горизонтальным хвостовым участ-
ком (рис. 2.22,в):
lо • wц > lв - минимальное натяжение будет в точке 1;
lо • wц < lв - минимальное натяжение будет в точке 2.
Перемещаясь по контуру тяговой цепи по направлению ее движения, выделяют характерные участки по действию сил сопротивления на тяговую цепь.