
Методическое пособие 751
.pdfплазменные процессы обработки поверхности. Однако, зачастую при подборе режима травления можно столкнуться с появлением дефектности, которая в свою очередь может крайне отрицательно сказаться на процессах пайки кристалла.
Экспериментальные результаты и обсуждение
Внастоящей работе продолжены исследования после утонения кремниевых пластин на установке DTG 8440 с применением шлифовального диска Z2 #2500, позволяющего достигнуть среднеквадратичной шероховатости поверхности 21,2 нм [2]. Сглаживание поверхности методом плазмохимического травления проводилось на установке Corial 200 RL в среде фторсодержащей плазмы
на основе SF6/O2. Кремниевая пластина располагалась на подложкодержателе и помещалась в реакционно-разрядную камеру. При подаче с генератора ВЧ мощности 150 Вт подавался рабочий газ с расходом SF6/O2 = 25/10 см3/мин и устанавливалось рабочее давление процесса в камере 100 мТорр. Скорость травления кремния в этом режиме порядка 130 нм/мин. После травления проводился визуальный анализ пластины, который не выявил каких-либо дефектов. Однако при дальнейшем исследовании качества поверхности, проводившемся с применением сканирования на растровом электронном микроскопе JEOL JSM-6610A, стало очевидно, что методики плазмохимического травления
на установке Corial 200 RL в SF6 в исследуемых режимах показывают отрицательные результаты. РЭМ изображения поверхности ПХТ представлены на рисунке.
Предполагалось, что изотропный характер процесса плазмохимического травления в SF6 должен приводить к выравниванию поверхности кремниевых пластин. Однако, травление на глубину 1 мкм выявило дефект типа «трава». Появление вертикальных нитевидных структур кремния диаметром менее 100 нм, по-видимому, связано с локальными участками загрязнения поверхности после механического утонения кремниевой крошкой, либо физикохимическими особенностями самого процесса травления. Данная структура сохранялась при различных соотношениях мощности и давления в реакционноразрядной камере. Применение дополнительной химической отмывки в деионизованной воде марки A, не привело к существенным улучшениям результатов.
Таким образом, можно отметить, что процесс плазмохимического травления Si в SF6 на установке Corial 200 RL вызывает технологические сложности. Происходит локальное микромаскирование поверхности, приводящее к дефектности конечной структуры. Данное качество поверхности является неудовлетворительным для дальнейших операций. При нанесении металлизации методом магнетронного напыления происходит вспучивание и отслоение металла.
Выводы
Вработе представлены исследования по травлению кремниевых пластин
во фторсодержащей плазме на основе SF6 после механического утонения на установке DTG 8440. Полученные изображения на растровом электронном микроскопе свидетельствует о наличии дефектов структуры типа «трава». Анали-
20
зируются возможные причины появления подобного рода структурных явлений.
a
б
в
РЭМ изображение поверхности кремниевых пластин после ПХТ: вид сверху с увеличением ×10000 (а); вид сбоку с увеличением ×70000 (б);
вид сбоку с увеличением ×17000 (в)
Литература
1.Исследование процессов пайки кремниевых кристаллов мощных транзисторов в их корпуса / В. С. Аносов [и др.] // Материалы электронной техники.
–2017. – T. 20. – № 1. – С. 51-59.
2.Влияние механического утонения и плазмохимического травления на морфологию поверхности кремниевых пластин / И. В. Коняев [и др.] // Электронная техника. Сер. 1: СВЧ-техника. – 2020. – № 3. – С. 84-90.
АО «Научно-исследовательский институт электронной техники», г. Воронеж
21
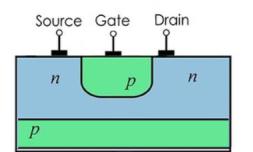
УДК 621.382.3
А.В. Арсентьев, Н.С. Булавина
ПРИМЕНЕНИЕ КАРБИДА КРЕМНИЯ В ИЗГОТОВЛЕНИИ ТРАНЗИСТОРОВ
Применение передовых методов изготовления и прецизионных методов контроля, а также уменьшение размеров полупроводниковых структур привели к тому, что свойства современных силовых приборов подошли к пределам, обусловленным физическими свойствами кремния. Это явилось причиной поиска альтернативных полупроводниковых материалов.
Сейчас из-за постоянного уменьшения размеров полупроводниковых структур начали проявляться печальные последствия, это произошло из-за стремления к постоянному улучшению технологий, так как качество кристаллов достигло запредельного уровня из-за полупроводниковых свойств кремния, который существенно расширяет температурный спектр и снижает потери на высоких частотах.
Карбид кремния имеет более низкие потери при переключении и более широкий тепловой диапазон из-за расширенной запрещённой зоны. Этими свойствами заинтересовались производители полупроводниковых приборов. Также предпосылкой для интереса производителей стал усиленный энергетический зазор между валентностью и зоной проводимости [1, 2].
Типовая структура высоковольтного транзистора на SiC представлена на
рис 1.
Рис. 1. Типовая структура высоковольтного транзистора на SiC
Рис. 2 отображает характеристики материалов для изготовления полупроводниковых приборов.
Карбид кремния внедряется в производство, но не все производители готовы с ним работать из-за высокой цены. Крупные производители взялись за разработку низко дефектных карбидокремниевых подложек, так как выдаю-
22

щиеся качества карбида кремния смогли задержать на себе их внимание. Пытаясь увеличить денежную прибыль на карбидокремниевых приборах, производители исследуют интеграции карбидокремниевых кристаллов в разных корпусах, а также вероятность доработок всех нововведений.
Рис. 2. Характеристики стандартных материалов для изготовления полупроводниковых приборов
Производство карбидокремниевых приборов имеет свои экономические особенности. Обычно кремниевые приборы изготавливаются на условно бездефектных пластинах, что и заинтересовало крупных производителей, диаметров 100 – 200 мм, цена готовых пластин из-за этого сильно возрастает. Так как карбид кремния решает вопрос биполярной деградации, что позволяет выпускать пластины серийного изготовления, то появляется проблема в потребности привыкания тех процессов к нововведенным размерам подложек. В настоящее время идет разработка карбидокремниевых пластин диаметром 150 – мм, что повышает конкурентоспособность подобных приборов на мировом рынке. А возможность занимать минимальные площади делает этот материал пригодных для изготовления специфических пластин. Более высокая плотность тока также является явным преимуществом карбида кремния.
К сожалению, карбид кремния имеет свои недостатки. Качество больших новых подложек стало ниже, в сравнении с предыдущими поколениями, хоть и сильно уменьшилась плотность дефектов, но можно считать, что оно увеличивается с каждым этапов освоения новой технологии. Сейчас существует вероятность понизить цену пластин благодаря диаметру 150 мм, но даже на таких условиях его изготовление остается довольно дорогим.
На данный момент разработчики пытаются адаптировать пластины диаметром 150 мм для масштабного производства. Именно сокращение плотности дефектов стало главным гарантом для гладкого перехода от изготовления меньшего диаметра. Производители утверждают, что совершенствование тех-
23

процессов и качество эпитаксиальных пленок гарантируют равномерные свойства на всей плоскости.
Винтовое смещение мешает соблюдать очередность атомарных плоскостей, располагая их по спирали, оно формирует микропоры, которые увеличивают процент бракованных чипов. Из этого следует вывод, что материал подвержен влиянию как внутреннему, так и наружному, а это, в свою очередь, может приводить к печальным последствиям; например, сдвигам атомарной решетки и увеличению дефектов.
Сейчас важным вопросом является быстро снижающаяся эффективность работы приборов. Так как поверхностные дефекты сильно ограничивают выход годных пластин. Чаще всего они образуются из газовой фазы при химическом осаждении в ходе всего эпитаксиального процесса. Совсем недавно появилась разработка, допускающая наращивание слоя выше 50 мкм, это важно для высоковольтных изделий. Так как габариты дефектов очень зависят от толщины самой плёнки, то необходимо как можно скорее адаптировать к серийному производству 150 мм пластины, ведь именно они обеспечивают приемлемую плотность дефектов.
Так как при изготовлении пластину делят на разные области, то зоны с дефектами отмечаются «браком», так с помощью метода лазерной светорассеивающей спектроктамии оценивается воздействие на выход годных приборов. Распределение Пуассона помогает найти плотность расположение дефектов на пластине.
Воздействие на выход годных приборов оценивается методом лазерной светорассеивающей спектроктамии. Сама пластина делится на определенные области и зоны с дефектами помечаются как бракованные, плотность расположения этих дефектов можно найти с помощью распределения Пуассона. Численность дефектов важна, ведь от нее и зависит процент выхода годных приборов в производстве.
Чтобы разработать конкурентоспособный прибор на основе карбида кремния, необходимо исследовать его термические свойства и блокирующие качества, ведь только тогда станет понятным благодаря чему карбид кремния вырвался вперед в гонке с обычным кремнием. Есть у него и нестандартные свойства.
Одним из значимых достоинств и проблем карбида кремния является его прозрачность, что существенно затрудняет задачу для фотолитографии, так как обнаружить дефекты и обработать пластины автоматически практически невозможно, ведь из-за прозрачности контроль может неправильно трактовать особенность структуры. Из-за того, что стандартные датчики на производстве рассчитаны на непрозрачные изделия, такой несложный процесс как фотолитография может легко привести к браку пластины.
Так как примеси в карбиде кремния активируются при температуре выше +1500 °С, то разумно предположить, что пластину надо защитить, либо могут появиться шероховатости, которые могут испортить прибор. Из этого напраши-
24

вается вывод, что концентрация примесей для легирования сильно влияет на эффективность активации. Процессы имплантации в SiC происходят тяжелее, чем в обычном Si. Тоже самое касается и процесса активации.
Есть очень интересный производственный период, который обязан проводиться в начале всего изготовления пластины – обжиг, ведь у карбида кремния он осуществляется при температуре свыше +800 °С, благодаря этому SiC отличается более высоким сопротивлением. Если сравнивать его с кремнием. Этот период необходимо проводить в начале изготовления потому что такие температуры вполне себе могут испортить пластину. Пусть лучше обжиг сделает это в начале производства, чем почти готовое изделие уйдет в брак. Во время обжига обычно достигают невысокого значения падения напряжения.
Есть не менее интересные, но более трудные задачи производства – сведение к минимуму или избавление от поликристаллических дефектов, которые выявляются с помощью оптической спектроктамии, о которой уже говорилось выше. Так как дефекты могут значительно травмировать поверхность пластины и привести ее к браку, борьба с ними становится чуть ли не первостепенной задачей. При полировке тоже можно создать линейные повреждения поверхности, которые позже обязательно проявят себя в процессе металлизации.
Эти преимущества приводят к более высокой эффективности системы, позволяют использовать более высокие частоты переключения, повышенную удельную мощность и снижение затрат на охлаждение. Благодаря концепции нормально включенного полевого транзистора полностью исключены любые связанные с надежностью проблемы.
Итак, из всего вышеперечисленного, мы можем сделать вывод, что карбид кремния с минимальным уровнем динамических потерь уже превосходит привычный нам кремний, сейчас уже создан невероятный список моделей на основе этого материала, но пока что экспериментальные данные сильно отличаются от данных, полученных при моделировании. На данный момент разработчики отдают все силы на то, чтобы модель оказывала воздействие на параметры пластины, это позволит улучшить эквивалентные схемы, которые принимают в рассмотрение качество самого материала.
Литература
1.Simulation of DIBL effect in 25 nm SOIFinFET with the different body shapes / A. E. Atamuratov [et al.] // Nanosystems: physics, chemistry, mathematics. – 2017. – V. 8. – P. 71-74.
2.Kononchuk O. Silicon-on-insulator (SOI) Technology: Manufacture and Applications / O. Kononchuk, B.-Y. Nguyen. – Elsevier : Woodhead Publishing, 2014. – 503 p.
Воронежский государственный технический университет
25
УДК 621.382
В.А. Буслов, О.Г. Викин, Т.В. Пашнева*
ИССЛЕДОВАНИЕ ВЛИЯНИЯ ДЛИТЕЛЬНОГО ХРАНЕНИЯ НА СВОЙСТВА ЗОЛОТОГО ПОКРЫТИЯ КОРПУСА МОЩНОГО СВЧ ТРАНЗИСТОРА
Работа посвящена исследованию влияния хранения сверх установленных в нормативной документации сроков на свойства золотого покрытия корпуса мощного СВЧ транзистора, а также возможности восстановления этой способности до приемлемого значения путем обработки в плазме. Хранение позолоченных корпусов сверх нормативных сроков приводит к ухудшению их свойств и снижению качества изготовленных с их использованием транзисторов. Обработка в низкотемпературной плазме аргона восстанавливает качество поверхности, но оно не достигает уровня качества корпусов со свежеосажденным золотым покрытием.
В настоящее время отечественное полупроводниковое производство характеризуется выпуском изделий небольшими по объему партиями. В таких условиях остро стоит вопрос обеспечения технологического процесса необходимым количеством комплектующих частей и материалами, так как предугадать будущую потребность невозможно, а сроки хранения запасов жестко ограничены нормативными документами [1].
Целью работы являлось исследование влияния хранения сверх установленных в нормативной документации сроков на способность золотого покрытия корпуса мощного СВЧ транзистора образовывать качественное эвтектической соединение с полупроводниковым кристаллом, а также возможность восстановления этой способности до приемлемого значения путем обработки в плазме.
Мощные СВЧ транзисторы в процессе функционирования рассеивают значительное количество электрической мощности, которая выделяется в полупроводниковом кристалле в виде тепловой энергии. Выделяющаяся тепловая энергия может составлять несколько десятков ватт на квадратный миллиметр активной структуры, и без должного эффективного теплоотвода через толщу полупроводникового кристалла на металлический фланец корпуса и дальше на теплоотвод приведет к перегреву и деградации параметров, или разрушению транзисторного кристалла. Поэтому обеспечение качественного электрического и теплового контакта полупроводникового транзисторного кристалла с металлическим фланцем корпуса имеет большую важность.
Кремниевый транзисторный кристалл монтируется на покрытую золотом поверхность металлического фланца корпуса путем контактно-реактивной пайки с образованием эвтектического сплава кремний-золото. При температуре
26
около 430 С кремниевый кристалл помещается на поверхность покрытого золотом фланца корпуса и при механическом контакте кремния и золотого покрытия происходит взаимное оплавление и образуется соединяющий их эвтектический расплав, обеспечивающий высокую механическую прочность и хороший электрический и тепловой контакт. На качество соединения влияют различные факторы, одним из которых является чистота верхнего слоя золотого покрытия фланца корпуса. В данной работе золотое покрытие было получено гальваническим осаждением из цитратно-фосфатного электролита, толщина покрытия на площадке для монтажа кристалла составляла 5 мкм. Максимально допустимый срок хранения корпуса с таким покрытием в условиях нейтральной атмосферы осушенного азота при комнатной температуре, согласно технологической документации, составляет 45 сут.
Качество теплового контакта оценивалось по величине теплового сопро-
тивления переход-корпус Rt П-К = Т/РРАС, здесь Т = Тp-n ТК – разность температур p-n перехода (места основного тепловыделения) и корпуса. Рассеиваемая в процессе измерения мощность РРАС вычислялась исходя из параметров заданного электрического режима, температура корпуса ТК определялась прямым методом при помощи присоединенной к нему термопары типа К (NiCr-NiAl). Температура p-n перехода Тp-n измерялась бесконтактным методом по интенсивности инфракрасного излучения программно-аппаратным комплексом на основе тепловизора FLIR SC655 по методике, описанной в [2, 3].
В ходе выполнения работы было исследовано три группы образцов. В каждой группе было по три транзистора, изготовленных в одинаковых условиях в рамках одного производственного цикла. Первая группа состояла из транзисторов, изготовленных в корпусах со свежеосажденным золотым покрытием. Вторая группа состояла из транзисторов, изготовленных в корпусах, после осаждения золотого покрытия хранившихся в течении года в герметичном шкафу в нейтральной атмосфере осушенного азота. Третья группа представляла собой транзисторы, собранные в корпусах, хранившихся год в атмосфере осушенного азота и непосредственно перед монтажом кристаллов обработанных на установке плазменной обработки Nordson AP-1000 в низкотемпературной плазме аргона в течение 20 мин. Увеличение длительности обработки свыше указанного значения не приводит к улучшению свойств золотого покрытия.
Результаты контроля качества напайки транзисторных кристаллов по изображениям в инфракрасном спектре и величине теплового сопротивления переход-корпус Rt П-К, полученным при помощи программно-аппаратного комплекса на основе тепловизора FLIR SC655, представлены на рис. 1. К первой группе образцов относятся изображения № 1 - № 3, ко второй группе относятся изображения № 4 - № 6, к третьей относятся изображения № 7 - № 9.
Как следует из представленных на рис. 1 изображений, распределение выделяющегося тепла по площади транзисторных кристаллов во всех трех группах равномерное, без наблюдаемых выраженных областей локального перегрева («горячих пятен»).
27

Рис. 1. Результаты контроля качества напайки транзисторных кристаллов по изображениям в инфракрасном спектре
и величине теплового сопротивления переход-корпус Rt П-К
28

Это свидетельствует о равномерном образовании эвтектического сплава кремний-золото по всей области соприкосновения кристаллов и фланца и формировании однородного качественного паяного соединения между кристаллом и фланцем корпуса.
На рис.2 представлено распределение величины измеренного теплового сопротивления Rt П-К по трем группам транзисторов.
Рис. 2. Распределение величины измеренного теплового сопротивления Rt П-К по трем группам транзисторов
Полученное значение Rt П-К для всех трех групп не превышает значения Rt П-К = 0,45 С/Вт, установленного в нормативной документации для данного мощного СВЧ транзистора. Использование позолоченных корпусов после длительного хранения не приводит к превышению этого значения, следовательно, транзисторы не могут быть забракованы. Из рис. 2 видно, что длительное хранение даже в нейтральной атмосфере азота приводит к изменению поверхности
29