
Методическое пособие 751
.pdfУДК 637.523: 339.13
А.В. Строгонов, М.А. Белых, Д.С. Пермяков
РАЗРАБОТКА АВТОМАТИЗИРОВАННОЙ ТЕХНОЛОГИИ ПОЛУЧЕНИЯ МЕТАЛЛООКСИДНЫХ ПЛЕНОК МЕТОДОМ ПОГРУЖЕНИЯ
Работа посвящена разработке автоматизированной технологии получения металлооксидных пленок по золь-гель технологии методом погружения.
Внастоящее время в мировом сообществе остро стоит вопрос перехода к экологически чистым возобновляемым источникам энергии, таким как ветровые станции и солнечные батареи. Например, страны Европы планируют к 2050 году полностью отказаться от нефти и газа как источников энергии.
Всвязи с этим исследования в области технологии получения новых прозрачных проводящих покрытий на основе полупроводниковых металлооксидов остается весьма актуальными.
Преимущественно покрытия прозрачные для видимого спектра, такие как FTO, ITO, AZO, представлены на рынке производителями из Китая.
Нами разработана рецептура и технологические режимы, по которым методом погружения получены опытные образцы высококачественных прозрачных проводящих покрытий со следующими характеристиками:
– минимальная толщина пленок порядка100 нм;
– поверхностное сопротивление в зависимости от материала и содержания лиганда от 10 Ом/□ и выше;
– прозрачность в видимом диапазоне составляет более 80 %.
Метод погружения – это технологический процесс получения пленок, в том числе и пленок металлооксидов, основанный на погружении подложки в емкость с материалом покрытия или прекурсором (в золь-гель технологии) и состоящий из нескольких этапов:
– погружение;
– выдержка;
– вытягивание;
–сушка;
– отжиг (при необходимости).
Толщина формируемого слоя пленки существенно зависит от скорости вытягивания и вязкости наносимого вещества [1, 2].
Данный метод позволяет изготавливать тонкие пленки оксидов SnO2, ZnO, CuO с различным содержанием легирующего элемента, а также наносить покрытия на различные, поверхности, к примеру, на стёкла для их тонировки и
10

лакокрасочные покрытия на детали машин, что делает метод коммерчески привлекательным [1].
Упрощенная схема изготовления металлооксидных пленок методом погружения приведена на рис. 1.
Рис. 1. Схема получения пленок металлооксида методом погружения
При проведении исследований по отработке технологических режимов получения пленок с требуемыми физическими свойствами должны быть с достаточной точностью соблюдены: скорость погружения и вытягивания, температура сушки и отжига, а также время выдержки на каждом этапе.
Следовательно физические свойства пленок, полученных данным методом, существенно зависят не только от технологии нанесения и компонентного состава прекурсоров, но и от оборудования, на котором наносятся пленки. Поэтому для повышения точности воспроизведения физических свойств металлооксидных пленок, снижения ошибок в повторении технологии и исключения грубых ошибок исследователя, процесс нанесения пленок необходимо автоматизировать.
Нашей командой была сконструирована и изготовлена действующая установка по автоматизированному нанесению тонких пленок со следующими характеристиками:
–габаритные размеры 130 × 160 × 550 мм;
–диапазон скоростей вытягивания: 0,2 – 7,2 мм/с;
–рабочая зона: 450 мм;
–минимальная толщина слоя: порядка 100 нм:
– максимальные размеры подложки 30 × 90 мм.
Схема автоматической установки погружения приведена на рис. 2. Установка оборудована: подъемником на базе коллекторного двигателя, что обеспечивает равномерность погружения подложек, ИК-нагревателем для сушки и отжига плёнок. Управление установкой погружения осуществляется электронным блоком управления на базе программируемого микроконтроллера реализованного на базе Atmega328PU, что позволяет с высокой точностью соблюдать режимы нанесения и обработки покрытий.
11

Рис. 2. Схема автоматической установки погружения: 1 – подъемный механизм; 2 – УФ/ИК-нагреватель; 3 – каркас установки; 4 – закрепленная подложка; 5 – управляющий модуль; 6 – емкость для прекурсора
На ближайшую перспективу запланирована доработка конструкции с внедрением контроля температуры, устройства крепежа для нескольких подложек, гибридного УФ/ИК модуля, пылезащищенного светонепроницаемого кожуха, функции удаленного управления. Это существенно повысит функциональные возможности установки.
Следует отметить, что данную установку можно использовать не только для нанесения металлооксидных пленок для нанотехнологии, но пленок из других материалов в различных отраслях промышленности.
Литература
1. Chaaya A. A. Conception de nanomatériaux à base d’oxyde par ALD: de la détection aux membranes: thèse PhD (Chimie et Physicochimie des matériaux) / A. A. Chaaya; directeur Prof Miele P. – Montpellier: Université Montpellier II – Sciences et Techniques du Languedoc, 2014. – 292 р.
2. Дунюшкина Л. А. Введение в методы получения пленочных электролитов для твердооксидных топливных элементов: монография / Л. А. Дунюшкина.
– Екатеринбург : УРО РАН, 2015. – 126 с.
Воронежский государственный технический университет
12

УДК 538.975
А.В. Строгонов, Т.В. Свистова, А.С. Ханин
ИССЛЕДОВАНИЕ ЧУВСТВИТЕЛЬНОСТИ ЗАРУБЕЖНЫХ И ОТЕЧЕСТВЕННЫХ ГАЗОВЫХ ДАТЧИКОВ НА ОСНОВЕ SnO2
Работа посвящена исследованию и сравнению динамических характеристик газовых датчиков, разработанных на кафедре полупроводниковой электроники и наноэлектроники ВГТУ, и бюджетных датчиков серии MQ, созданных китайской компанией HANWEI. Обнаружено, что время установления равновесия в смеси этанол-воздух одинаковой концентрации у газовых датчиков серии MQ больше, чем у отечественных датчиков, величины газовой чувствительности соизмеримы.
Газовые датчики применяются для детектирования в воздухе токсичных и взрывоопасных газов на химических, горнодобывающих, металлургических и других объектах, и в быту. Большинство импортных газовых датчиков имеет довольно высокую стоимость, поэтому важно иметь отечественный аналог, не уступающий им по характеристикам.
Целью работы является сравнение динамических характеристик газовых датчиков, разработанных на кафедре полупроводниковой электроники и наноэлектроники ВГТУ, и бюджетных датчиков серии MQ, созданных китайской компанией HANWEI.
Для тестирования газовых датчиков был собран стенд, приведенный на рис. 1.
Рис. 1. Стенд для исследования газовых датчиков
13
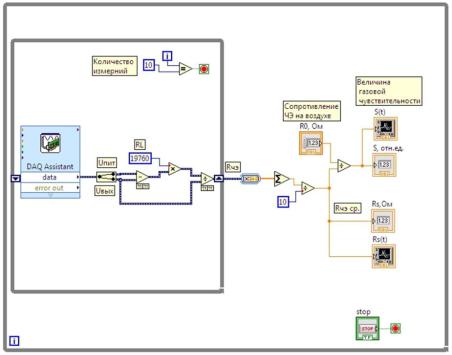
Основой стенда является герметичная ячейка объемом 0,5 л, в которой находится контактная площадка для датчика. Снаружи емкости имеются выводы для подключения стенда к устройству сбора данных NI-DAQ компании National Instruments. DAQ-система – система сбора данных, состоящая из датчиков, измерительных преобразователей, нормирующих устройств (устройств кондиционирования сигналов), соединительных кабелей между различными устройствами и аксессуарами, устройства M серии, программного обеспечение и персонального компьютера (ПК). Измерительные устройства National Instruments содержат набор драйверов NI-DAQ, который представляет собой библиотеку функций и виртуальных приборов (ВП), с помощью которых можно осуществить программирования всех свойств измерительных устройств. Необходимые функции и ВП можно вызвать из среды проектирования, например, LabVIEW. На рис. 2 представлена программа для тестирования датчиков на
LabVIEW [1].
Рис. 2. Блок-диаграмма программы для тестирования датчиков
Устройство сбора данных DAQ измеряет напряжение питания датчика, а также выходное напряжение. Затем происходит вычитание амплитудного значения напряжения питания из выходного напряжения и перемножение полученной разности на величину сопротивления резистора RL. Далее результат умножения делится на величину выходного напряжения, на выходе получается значение сопротивления чувствительного элемента в среде газа. Измерение сопротивления чувствительного элемента в газе производится 10 раз, затем находится среднее арифметическое значение. Известное по технической специфи-
14

кации сопротивление чувствительного элемента на воздухе делится на измеренное сопротивление чувствительного элемента в среде газа, результатом деления является величина газовой чувствительности, которая выводится как в виде числовой информации, а также в виде зависимости от времени (рис. 3), дискретность измерений 1 с.
Рис. 3. Лицевая панель программы для тестирования датчиков
Датчики серии MQ выпускаются в пластиковых, а также в металлопластиковых корпусах с защитой от воспламенения для датчиков взрывоопасных газов. Датчики имеют не стандартную конфигурацию выводов, что затрудняет их монтаж в конечное устройство [2].
Датчики, разработанные на кафедре полупроводниковой электроники и наноэлектроники ВГТУ, собраны в стандартные металлокерамические корпуса DIP-8, однако задействованы только 6 выводов корпуса.
Несмотря на то, что материал, из которого изготовлен чувствительный элемент (ЧЭ) этих датчиков один и тот же – диоксид олова, конструкция их отличается. Датчик MQ-3 выполнен по керамической технологии. Трубка на основе оксида алюминия покрыта оболочкой из диоксида олова, к которой подведены платиновые контакты. Внутрь трубки находится спираль из нихрома, которая служит нагревателем.
Отечественный датчик изготовлен по микроэлектронной технологии. В качестве подложки используется кремний, покрытый слоем диоксида кремния. На подложке находится нагреватель – платиновое тонкопленочное термосопро-
15

тивление и чувствительный элемент на основе диоксида олова, расположенный на токосъемных контактах, изготовленных в виде гребенки.
Несмотря на различную конструкцию параметры этих датчиков схожи, так что их можно считать функциональными аналогами. В таблице представлены основные параметры газовых датчиков.
Параметры газовых датчиков
Параметр |
MQ-3 |
ВГТУ |
Материал ЧЭ |
SnO2 |
SnO2 + 1% Si |
Тип корпуса |
Нестандартный |
DIP-8 |
Газ |
Пары этанола |
Универсальный |
|
|
|
Uпит, В |
5 |
5 |
Rчэ (на воздухе), Ом |
20000 |
15000 |
|
|
|
Rн, Ом |
31 |
31 |
|
|
|
Газовый датчик подключен по стандартной схеме включения газовых датчиков типа MQ (рис. 4).
Рис. 4. Схема включения датчика
Напряжение питания 5 В подается на резистивный делитель, одним плечом которого является чувствительный элемент датчика, а другим балансный резистор, который имеет сопротивление близкое к сопротивлению чувствительного элемента на воздухе. В атмосфере газа сопротивление датчика изменяется и тем самым изменяется выходное напряжение. Зная разницу этих напряжений и сопротивление балансного резистора, можно рассчитать сопротивление чувствительного элемента по формуле [3]:
16

При измерение динамических характеристик газовой чувствительности чувствительный элемент (ЧЭ) газового датчика вначале на воздухе нагревают до оптимальной рабочей температуры исследуемого газа и измеряют сопротивление ЧЭ (Rв), которое будет соответствовать началу отсчета. Затем в измерительную ячейку объемом 0,5 л вводится исследуемый газ заданной концентрации, при этом сопротивление ЧЭ уменьшается. Фиксируется уменьшение сопротивления ЧЭ (Rг) через равные промежутки времени. Измерение уменьшающегося сопротивления производят до тех пор, пока не установится состояние равновесия в системе датчик – исследуемый газ. Далее в измерительную ячейку вводится чистый воздух, и наблюдается восстановление сопротивления Rг до исходного значения Rв с контролем через равные промежутки времени.
Динамические характеристики газовой чувствительности датчика MQ-3 представлены на рис. 5, а датчика ВГТУ – на рис. 6.
Рис. 5. Динамические характеристики газовой чувствительности датчика MQ-3 к парам этилового спирта в воздухе
Время установления равновесия в смеси этанол-воздух у газовых датчиков серии MQ составляет 17 – 322 с в интервале концентраций от 86791,48 до 433987,4 ppm. После удаления датчика из исследуемой смеси исходное сопротивление восстанавливается в течение 49 – 91 с.
17

Рис. 6. Динамические характеристики газовой чувствительности датчика разработки ВГТУ к парам этилового спирта в воздухе
У датчика разработки ВГТУ – время установления равновесия 12 – 199 с, время восстановления сопротивления 20 – 96 с.
Установлено, что время установления равновесия в смеси этанол-воздух одинаковой концентрации у газовых датчиков серии MQ больше, чем у датчиков разработки ВГТУ, величина газовой чувствительности практически одинакова. Таким образом, датчики ВГТУ можно использовать для измерения небольших, но быстро изменяющихся концентраций газа, а датчики MQ лучше подходят для статичного контроля наличия газа.
Литература
1.Васильев А. С. Основы программирования в среде LabVIEW / А. С. Васильев, О. Ю. Лашманов. – СПб. : Университет ИТМО, 2015. – 82 с.
2.MQ-3 Alcohol Gas Sensor [Электронный ресурс] : Manual. – Режим доступа: http:// www.winsensor.com.
3.Топильский В. Б. Схемотехника измерительных устройств / В. Б. Топильский. – М. : БИНОМ. Лаборатория знаний, 2006. – 232 с.
Воронежский государственный технический университет
18
УДК 533.924
И.В. Коняев, Е.А. Сизаск, И.И. Бородкин
СТРУКТУРНЫЕ ДЕФЕКТЫ ПОВЕРХНОСТИ ПОСЛЕ МЕХАНИЧЕСКОГО УТОНЕНИЯ И ПЛАЗМОХИМИЧЕСКОГО ТРАВЛЕНИЯ КРЕМНИЯ
В статье представлены результаты исследований структуры обратной стороны кремниевых пластин после механического утонения на установке DTG 8440 с применением шлифовального диска Z2 #2500. Плазмохимическое травление пластин выполнялось во фторсодержащей плазме на основе SF6/O2 с применением различных режимов обработки поверхности. При анализе качества поверхности на растровом электронном микроскопе было выявлено появление вертикальных нитевидных струк-
тур кремния диаметром менее 100 нм. Выявление дефекта типа «трава», повидимому, связано с локальными участками загрязнения поверхности после механического утонения кремниевой крошкой либо физикохимическими особенностями самого процесса травления. Стоит отдельно отметить, что различные предварительные отмывки перед травлением также не дали существенного улучшения результатов.
Введение
Основным технологическим требованием при работе СВЧ транзисторов является надежная работа, связанная с обеспечением высокой мощности и КПД при рабочих температурах прибора. Процесс механического утонения кремниевых пластин является важным технологическим этапом при производстве изделий микроэлектроники, так как остаточная толщина и площадь чипа влияет на эффективность теплоотвода. Помимо толщины кристалла важнейшее значение имеет качество получаемой поверхности [1]. Наиболее информативной характеристикой в данном случае выступают параметры шероховатости поверхности, значение которых можно определить, применяя специализированные приборы, такие как профилометр или атомно-силовой микроскоп. Среди наиболее информативных показателей качества поверхности при анализе по базовой линии профиля, согласно ГОСТ 25142-82, являются: среднее арифметическое отклонение профиля Ra, наибольшая высота профиля Rz. В работе [2], подробно рассмотрены различные режимы механического утонения и плазмохимического травления (ПХТ) кремния с анализом количественных характеристик поверхности.
На практике, для получения более качественной поверхности после шлифовки, проводят полировку поверхности с применением механической, хими- ко-механической, химической или плазмохимической технологии. Наиболее технологичными, экологически чистыми и экономически выгодными являются
19