
Методическое пособие 722
.pdfгде Р1 и Р2 – начальное и конечное абсолютное давление газа; υ1 иυ2 – удельный объем газа соответственно при давлениях Р1 и Р2.
В описываемом процессе газ сжимается или расширяется при сохранении постоянной температуры. Очевидно, что подобный процесс может иметь место лишь при очень медленном изменении состояния (сжатия или расширения) газа. К такому случаю относится, например, процесс разрядки газогидравлического аккумулятора гидросистемы ПР при упоре в посторонний предмет.
При допущении, что процесс изменения состояния газа протекает без теплообмена с окружающей средой, будем иметь
P υk = const,
где Р и υ – давление и плотность газа;
k – показатель адиабаты; для сухого воздуха k = 1,405.
Процесс, описываемый этими уравнениями, называется адиабатным. В практике процесс, близкий к адиабатному, наблюдается при истечении газа из резервуара через насадку или отверстие в тонкой стенке, когда вследствие кратковременного пребывания газа в пределах насадки можно пренебречь силами трения и теплообмена с окружающей средой (со стенками канала).
При рассмотрении последнего процесса следует иметь в виду, что тепловая изоляция не является (в силу сопротивления трения течению газа, работа которого превращается в теплоту) достаточным основанием для того, чтобы показатель политропы можно было принимать равным показателю изотропы (под изотропным потоком понимают теплоизолированный поток идеального газа, в котором отсутствует сила трения).
В реальных условиях при изменении состояния газа неизбежно происходит некоторый теплообмен между газом и стенками сосуда с жидкостью, представляющий собой нечто среднее из рассмотренных предельных изменений (изотермного и адиабатного процессов).
Уравнение этого состояния, охватывающее все возможные в практике его
изменения, имеет вид |
|
P υn = const, |
k > n > 1, |
где n – показатель политропы (при k = 1 имеем изотермный и при n = k адиабатный процессы).
Соотношения параметров в политропном процессе выражаются уравнениями для адиабаты с заменой коэффициента k на коэффициент n.
В теории течения газов важным параметром является скорость звука, представляющая собой скорость распространения в газе звуковой волны. Скорость течения газа, равная скорости звука, является границей, при переходе которой изменяются закономерности газового потока и расходные характеристики пневмосистем. Связь скорости звука со свойствами газов выражается известным из газодинамики уравнением.
80
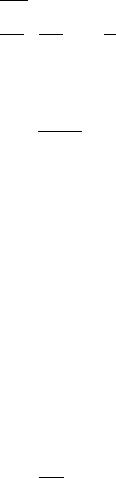
При допущении, что изменения параметров потока газа, вызванные малыми возмущениями, происходят настолько быстро, что можно пренебречь теплообменом между частицами газа, а сами возмущения, создаваемые звуковой волной, настолько малы, что можно пренебречь силами трения, можем написать
√
где Р – давление и υ – плотность газа.
Для идеального газа эта зависимость может быть переписана в виде
√
где R – удельная газовая постоянная.
Инженерные расчеты течения газа в элементах пневмосистемы сводятся к расчетам, связанным с истечением газа из резервуаров (баллонов) и с заполнением их, а также с течением по трубопроводам пневмосистем и через местное сопротивление.
Эти расчеты в силу сжимаемости воздуха представляют известные трудности, обусловленные тем, что течение его в трубопроводах пневмосистем и каналах их агрегатов сопровождается, как это было указано, изменением давления и удельного объема. Ввиду этого при расчетах исходят из условия, что при установившемся процессе течения массовый расход воздуха через любое поперечное сечение трубопровода остается постоянным, в соответствии с чем массовый расход определяется из уравнения сплошности (неразрывности) потока.
где f – площадь сечения газового потока (трубопровода);
u, p – средняя скорость и плотность воздуха в этом сечении
υ– удельный объем воздуха. Поскольку объемный расход
Q = u f
по пути течения воздуха по трубопроводу не сохраняется, а увеличивается вследствие расширения, вызванного понижением давления при течении, средняя скорость воздуха по длине трубопровода также будет возрастать. При этом вследствие расширения воздуха происходит изменение его температуры, что и должно быть учтено при расчетах.
По принципу действия и конструкции элементы пневмосистем подобны, за исключением источников питания, соответствующих элементам гидросистем, а чаще в обеих системах применяется один и тот же тип этих
81
элементов. В частности, преобразование энергии сжатого воздуха в механическую работу производится в этих системах объемными пневмодвигателями вращательного и прямолинейного (силовые пневмоцилиндры) движения. Реже применяются пневмоповоротники (моментные пневмоцилиндры).
Под объемным пневмодвигателем понимается такой, в котором преобразование энергии происходит в процессе попеременного заполнения рабочей камеры рабочим газом и вытеснения его из рабочей камеры.
Во многих случаях применения пневмоприводов оказывается необходимым осуществить торможение поршня пневмоцилиндра в конце его движения во избежание удара, который нежелателен или недопустим по условиям прочности механизмов или характера технологической операции.
Торможение осуществляется внутренними или внешними дроссельными тормозными устройствами, устанавливаемыми на пути отвода воздуха из полости опорожнения (нерабочей полости). Эти устройства уменьшают проходное сечение выходной (отводной) магистрали в некоторой точке хода поршня пневмоцилиндра, в результате в этой полости создается тормозное противодавление, снижающее скорость движения поршня.
Пневматическая схема робота МП-5 (рис. 2.27) обеспечивает подготовку
иподачу сжатого воздуха к соответствующим пневмоцилиндрам по командам устройства управления. Блок подготовки воздуха состоит из вентиля 1, фильтра-влагоотделителя 2, редукционного пневмоклапана 3 с манометром 4
имаслораспылителя 5. Рабочее давление воздуха равно 4 кгс/см2.
Вмеханизме выдвижения схвата исполнительным двигателем служит пневмоцилиндр 8 двухстороннего действия с максимальным ходом поршня 600 мм. В режиме выдвижения схвата сжатый воздух через двухпозиционный пятиходовой воздухораспределитель 11 и редукционный клапан 10 поступает в поршневую часть цилиндра, а воздух, вытесняемый из штоковой полости через воздухораспределитель 11, обратный клапан 12 и распределитель 13, сбрасывается в атмосферу.
Дроссели с обратными клапанами 7 и 9, установленные непосредственно на пневмоцилиндре, служат для регулирования скорости перемещения поршня. При остановке схвата в заданной точке позиционирования по сигналу конечного выключателя производится одновременное переключение воздухораспределителей 11 и 13. При этом поток сжатого воздуха направляется в ту полость пневмоцилиндра, которая для данного движения является тормозной. Например, при выдвижении схвата тормозной является штоковая полость цилиндра.
Одновременно с реверсом воздушных потоков сжатый воздух подается в пневмоцилиндр 6 упора и на выходе обратного клапана 12 создается давление, равное давлению питания. Клапан 12 закрывается. В результате давление в тормозной полости пневмоцилиндра выдвижения резко возрастает и в то же время остается давление в полости движения, так как выхлоп из этой полости может происходить только через закрытый обратный клапан.
82
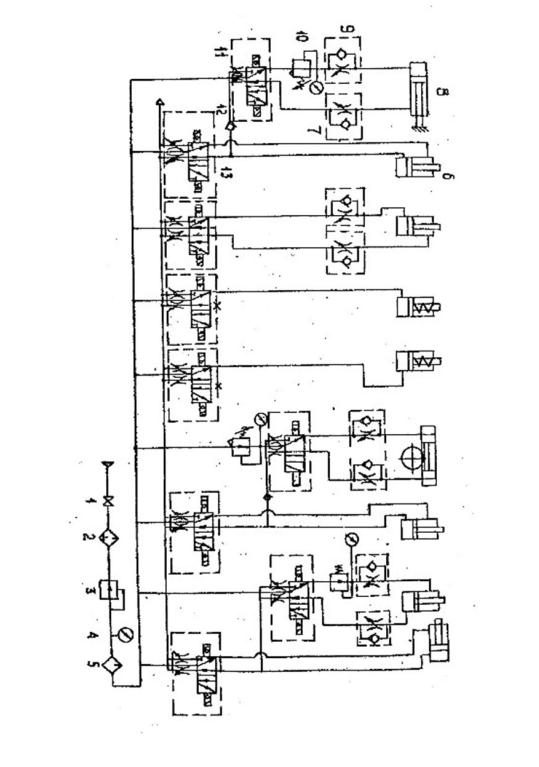
Рис. 2.27
Таким образом, под действием сил трения и разности давлений в поршневой и штоковой полостях происходит торможение поршня. Давление воздуха, подаваемого в поршневую полость устанавливается клапаном 10 такой величины, чтобы результирующая сил, приложенных к поршню в момент остановки, равнялась нулю. Аналогично построена схема поворота.
83
3. НЕКОТОРЫЕ РАЗРАБОТКИ В ОБЛАСТИ ЭЛЕКТРОПРИВОДОВ РОБОТОВ
3.1. Электроприводы с внешними магнитными системами
Повышение технического уровня промышленных роботов (ПР) неразрывно связано с совершенствованием их приводных устройств, выполненных на основе комплексных модульных электромеханизмов.
Это вызвано такими положительными качествами электропривода (ЭП), как отсутствие масла, меньший шум, отсутствие затруднений с дроблением электрической энергии, хорошим сопряжением с современными микропроцессорными системами управления. Эти достоинства повышают общий технический уровень ПР, способствуют повышению надежности.
Вто же время электроприводу присущ и серьезный недостаток – низкие удельные массо-габаритные показатели.
Требования к массо-габаритным показателям приводов ПР существенно зависит от вида движения ПР, обслуживаемого приводом. Так, наименее жесткие требования предъявляются к приводам, установленным на глобальных (транспортных) степенях подвижности ПР. Эти требования не отличаются от аналогичных требований к приводам транспортных устройств и находятся, например для робокаров, в пределах примерно на 10-20 Н/кг – в пересч те на усилие, направленное по прямой. Региональные (переносные) степени подвижности предъявляют существенно повышенные требования к усилию на единицу массы и находятся в пределах примерно 30-70 Н/кг для степеней, непосредственно оснащенных приводами, и несколько меньше – для степеней с приводами, установленными на основании. Локальные (ориентирующие) степени подвижности требуют удельных усилий порядка 70-100 Н/кг, прич м обслуживание локальных степеней приводами, расположенными на неподвижном основании и имеющими, естественно, меньшие удельные усилия, затруднено из-за значительной длины и сложности кинематических цепей. Наивысшие требования к массо-габаритным показателям предъявляются к приводам схватов, находящимся на конце кинематической цепи манипулятора.
Вначальный период развития робототехники глобальные и региональные степени подвижности ПР оснащались станочными ЭП, локальные – авиационными ЭП. В настоящее время промышленность приступила к выпуску приводов, предназначенных специально для ПР. При этом привод выполняется модульного типа, содержит в сво м составе все компоненты, необходимые для успешного функционирования робота.
Совершенствование электрических приводов ПР неразрывно связано с улучшением их массо-габаритных показателей.
Существует несколько путей решения данной проблемы.
84
1.Применение в роботостроении качественных материалов, обеспечивающих функционирование привода при меньших массе и объеме. Однако этот путь приводит к существенному увеличению первоначальной стоимости привода.
2.Увеличение интенсивности энергетических потоков, в частности, повышение плотности тока, удельной магнитной энергии. Однозначно повышаются и тепловые нагрузки, что ведет к необходимости установки системы охлаждения, температурного контроля и регулирования. При этом увеличиваются эксплуатационные расходы, уменьшается срок службы привода.
3.Существует также третий путь улучшения массо-габаритных показателей. Он связан с тщательным весовым анализом, нахождением совершенных конструктивных решений, обеспечивающих заданные требования. Одним из способов его реализации является применение внешних, не связанных конструктивно с роботом, магнитных систем. В зазоре магнитных систем размещаются при позиционировании активные элементы привода. Таким
образом, элемент с наибольшей массой – магнитная система – не входит в состав привода, а располагается отдельно. Это существенно уменьшает массу и габариты привода. При этом уменьшается стоимость за сч т того, что магнитные системы могут выполняться не из редкоземельных металлов и располагаться вне робота.
Кроме того, следует рассматривать не только отдельные, пусть даже достаточно малые, элементы привода с точки зрения их массы, а необходимо проанализировать также уровни использования проводников всех энергетических потоков привода. При этом изменение массы модуля должно обусловливаться не изменением массы элементов, а главным образом перераспределением масс с подвижного основания (манипулятора) на неподвижное. Т.е. задача заключается в наиболее рациональном выборе места разрыва энергетического потока и организации беспрепятственного функционирования данной цепи с уч том соединения подвижных и неподвижных участков.
Граф энергетических потоков простейшего модуля робота представим, как на рис. 3.1. Он включает в себя изображение электрической питающей сети, расположенной на звеньях манипулятора, двигателя или редуктора. Здесь ребро 1 соответствует электрической сети на манипуляторе, ребро 2 – валу двигателя, ребро 3 – магнитной цепи, ребро 4 – редуктору. Входные обозначения напряжения, тока, скорости и момента М имеют индекс 1, выходные – индекс 2.
Практически в модуле имеются четыре энергетических потока с соответствующими проводниками.
1.Поток электрической энергии. Проводником является электрическая сеть (провода), проводящая энергию от источника питания к двигателю.
2.Поток магнитной энергии. Проводником является магнитопровод двигателя.
3.Поток механической энергии (высокоскоростной). Проводником данного потока является ротор двигателя.
85
4. Поток низкоскоростной механической энергии. Редуктор модуля – проводник этого потока.
Отметим три основных направления уменьшения показателей.
1. Увеличение степени использования проводника потока, связанное с уменьшением массы. Обычно это связано с применением более дорогих исходных материалов и, следовательно, с увеличением стоимости модуля.
2.Увеличение КПД преобразования потока, если это не связано с увеличением массы.
3.Уменьшение длины проводника потока, в определенном случае – устранение каких-либо потоков.
Рассмотрим последний случай более подробно. Поскольку полное устранение, а также существенное уменьшение длины какого-либо энергетического потока реального модуля маловероятно ввиду того, что обычно модули ПР выполняются уже с достаточным уровнем использования материалов, есть только один практически приемлемый путь реализации уменьшения длины проводников потока. Имеется в виду перераспределение (перенос) потоков, связанных с подвижным основанием (манипулятор ПР), на неподвижное, связанное, например, с полом цеха. При этом должны соблюдаться два условия:
1.Разрыв (перераспределение) какого-либо из потоков не должен отрицательно сказываться на технологическом процессе, т.е. должны иметься места позиционирования, где возможно перераспределение потоков.
2.Должно соблюдаться условие для разрыва. Обычно со всех точек зрения более предпочтителен бесконтактный разрыв потока. Это связано с тем, что при бесконтактном разрыве отсутствует износ механических узлов, отрицательно сказывающийся на надежности привода. Однако бесконтактный разрыв потока электрической энергии связан с введением дополнительных устройств типа индукционных токосъемников. Разрыв потока механической энергии связан с введением муфт. И в этом, и в другом случае введение дополнительных устройств априорно ухудшает массо-габаритные показатели.
По иному обстоит дело с потоком магнитной энергии. Здесь уже присутствует элемент бесконтактного разрыва потока – воздушный зазор, т.е. уже реализована возможность бесконтактного разрыва потока. Следовательно, для улучшения массо-габаритных показателей необходим только перенос магнитной системы на неподвижное основание. Это не касается железного якоря (ротора), который конструктивно связан с ротором. Теоретически такой перенос возможен для тр х других энергетических потоков. Конечно, нужно учесть наличие неизменяемых компонентов привода. Под неизменяемыми компонентами понимаются разъемы, унифицированные механические соединения, не изменяющие массу при выносе потоков.
Применение метода внешних потоков, основанного на выносе энергетических потоков, а точнее – на перераспределении потоков с подвижного на неподвижное основание позволяет без каких-либо существенных изменений
всоставе модуля уменьшить его массу.
86
Оценим это уменьшение. Ясно, что оно будет существенно зависеть от типа применяемого двигателя, а точнее от соотношения масс ротора (якоря), оставленного в модуле робота, и статора (индуктора), вынесенного на основание. Если предположить, что массы единицы длины ротора и статора одинаковы, то разница в массах будет определяться только диаметрами ротора и статора.
Для двигателя классического типа соотношение между этими диаметрами находится примерно в пределах 2–2.5. Поскольку масса пропорциональна квадрату диаметра, то реальное уменьшение массы составит 4-6 раз. В случае безжелезного якоря это уменьшение еще больше.
3.2. Приводы схватов
Частями общей задачи повышения технического уровня электромеханических модулей (ЭМ) ПР являются разработка и исследование ЭМ захватных устройств ПР, в частности, схватов.
К ЭМ привода схвата предъявляются следующие технические требования.
1.Высокие массо-габаритные показатели, сравнимые с соответствующими показателями пневмо- и гидропривода.
2.Обеспечение максимального быстродействия при срабатывании.
3.Обеспечение надежного фиксирования губок.
4.Совместимость с системой управления ПР.
5.Минимальные первоначальная стоимость и эксплуатационные затраты. В настоящее время для подавляющего большинства приводов схватов,
удовлетворяющих данным требованиям, используют энергию гидро- и пневмосреды.
Основной причиной этого являются высокие массо-габаритные показатели гидро- и пневмоприводов. Однако гидро- и пневомоприводу свойственны такие недостатки, как:
–низкий КПД системы;
–необходимость использования гидростанции (гидропривод) и пневмосети (пневмопривод);
–возможность утечек масла, загрязнения аппаратуры, как следствие – низкая надежность;
–высокий уровень шума;
–высокие эксплуатационные расходы.
Кардинальным образом данные недостатки преодолеваются путем замены гидро- и пневмопривода электроприводом. Однако в настоящее время удельные массо-габаритные показатели электроприводов схватов на порядок меньше, чем у пневмо- и гидроприводов. Эта ситуация сохраняется довольно продолжительное время, несмотря на большой объ м научно-исследова-
87
тельских работ, проводимых в данном направлении. Из-за этого многие чисто электрические роботы, например, Универсал – 5, НЦТМ – 01, М10П, М20П, ТУР – 10 оснащены схватом с пневмоприводом.
В приводе схвата можно выделить три компонента: механическая часть (губки, основание и т.д.), собственно привод и силовые магистрали.
Механическая часть мало зависит от типа привода, е массо-габаритные показатели являются практически постоянными величинами. Показатель усилия на единицу массы пневмопривода находится в пределах 50–80 Н/кг. Величина этого показателя у электропривода, построенного на базе обычных машин постоянного тока, значительно меньше. Путь увеличения усилия электропривода схвата на единицу массы только один – вынос магнитной системы на неподвижное основание, т.е. применение внешних магнитных систем.
Рассмотрим привод схвата с катушками обычного типа. Сущность конструкции иллюстрируют рис. 3.2 (изображен вид сверху роботизированного участка, оснащенного схватом манипулятора с внешними магнитными системами) и рис. 3.3 (вид спереди, сечение по магнитным системам).
Схват работает с магнитными системами, расположенными, например, по прямой линии. Также может быть использована и кривая. Схват имеет систему 1 с односторонними магнитными наконечниками 2. Вблизи нее установлена первая рабочая позиция 3, например, стеллаж с заготовками. Схват манипулирует деталью 4. По другую сторону схвата установлены наконечники 5 второй магнитной системы 6. Эти наконечники выполнены двусторонними, т.е. они продлены на противоположную сторону ко второй рабочей позиции 7, например, технологической машине. Рядом с ней установлены магнитные наконечники 8 третьей магнитной системы 9, также двухсторонние. Заканчивает линейку третья рабочая позиция 10, например, автоматический стеллаж для готовых изделий. Рядом с ней установлены наконечники 11 четвертой магнитной системы 12. Магнитные системы 1, 6, 9 и 12 расположены по линии А-А. Их сечение дано на рис. 3.3. Обозначения систем 1, 6, 9 и 12 совпадают с источниками магнитного поля этих систем.
При необходимости все системы устанавливаются на основаниях. Далее,
всостав участка входит рельсовый путь 13, по которому перемещается манипулятор робота. В его состав, собственно, входит схват 14 с губками, приводимыми в действие активными элементами 15, выполненными, например,
ввиде жестких бескаркасных катушек, которые входят во время позиционирования в зазоры магнитных систем. Схват с элементами установлен
на руке 16 манипулятора 17. Рука имеет возможность передвигаться, а манипулятор 17 – перемещаться по рельсам 13.
Манипулятор показан с рукой в среднем положении у первой позиции 3 со сплошными линиями, а с вытянутой рукой – у второй позиции 7 пунктирными линиями (рис. 3.2).
88
Более подробно кинематика схвата представлена на рис. 3.4. В воздушном зазоре магнитной системы располагаются активные токопроводящие подвижные элементы 15 привода (катушки). На руке 16 ПР закреплено основание 17 с шарнирами 18, в которых вращаются рычаги 19 с губками 20.
Сэлементами контактируют тяги 21, соединенные с пружиной 22.
Вразжатом состоянии положение всех кинематических звеньев показано на рис. 3.4 пунктиром. Фиксация губок в нерабочем, сжатом, состоянии осуществляется пружиной 22.
Работа привода. В состоянии перед включением активные элементы 15 находятся в воздушном зазоре магнитных систем. При подаче тока в активные элементы 15 происходит следующее.
Внешние участки катушек 15 втягиваются в зазор магнитных систем, увлекая за собой рычаги 19, тяги 21, и растягивают пружину 22. Происходит раскрытие схвата. Это состояние сохраняется до тех пор, пока ид т ток по элементам 15 и они находятся в зазоре магнитной системы. Для закрытия схвата достаточно выключить ток. Под действием пружины 22 губки 20 замыкаются, зажимая деталь 4. В данном состоянии рука движется, происходит подъ м-поворот ПР, деталь 4 переносится на новое место позиционирования, например, 3,7 или 10. Далее происходит выдвижение руки, элементы 15 снова в зазоре магнитных систем. Схват оказывается подготовленным для выполнения цикла. Конкретная кинематика может иметь конструктивные отличия при другой форме транспортируемой детали или катушек активного элемента. Особенностью этого привода является то, что таким приводом может оснащаться только ПР с цикловой системой управления, с небольшим числом рабочих позиций. Если число рабочих позиций велико (ПР с позиционной системой), то количество магнитных систем увеличивается, что повышает стоимость робототехнического комплекса.
Выход из данного положения можно найти, применив привод с пружинным аккумулятором (ПА). В этом случае теоретически достаточно лишь одной магнитной системы.
89