
Методическое пособие 722
.pdf3.5. Роботы с рекуперацией энергии и динамической развязкой движений
Ужесточение требований к массо-габаритным показателям привода роботов стимулирует новые технические разработки, направленные на уменьшение энергопотребления и динамических нагрузок на конструкцию. В этой связи можно выделить два направления работ: рекуперация энергии торможения и развязка движений манипулятора робота. Развязка движений предполагает создание таких условий, когда движение одних звеньев манипулятора не влияет на движение других. Например, поворот локтя манипулятора вертикально-мануальной схемы не должен сказываться на изменении момента в плечевом шарнире. Решение такой задачи распадается на статическую балансировку, обычно выполняемую с помощью пружинных и пневматических систем уравновешивания, и динамическую развязку.
Большую работу в данном направлении проводит Институт машиностроения им. A. A. Благонравова, в частности, коллектив под руководством д-ра техн. наук, профессора А. И. Корендясева. Ниже приводится краткое изложение результатов работ этого коллектива.
Приводы с рекуперацией рассмотрим на примере робота с цикловым управлением. Для простоты выделим лишь одну степень подвижности (рис. 3.18). Робот имеет двигатель 1, подвижные массы 2, регулируемые упоры 3 с демпфирующими устройствами 4. Доля движений с постоянной скоростью такого устройства мала. Преобладающими являются режимы разгона и торможения, при этом вся энергия, получаемая системой от двигателя, рассеивается демпферами. Циклограмма работы системы и ориентировочный график изменения момента двигателя МДВ, момента демпфера МДЕМ и момента трения в передачах и опорах МТР в координатах «момент –угол поворота» показаны на рис. 3.19. На полном цикле движения работа источника (двигателя) должна быть равна работе, поглощенной приемником, – работе моментов трения и демпфера. Следовательно, площадь 1 должна быть равна сумме площадей 2 и 3.
Если для увеличения быстродействия увеличивают момент двигателя, то момент демпфера увеличивается гораздо быстрее, так как он действует на меньшем участке перемещения. Это повышает динамические нагрузки, что в сочетании с повышенными массо-габаритными показателями двигателя с увеличенным моментом делает такой путь развития привода практически тупиковым.
Робот с рекуперацией энергии, схема которого приведена на рис. 3.20, включает аккумулятор потенциальной энергии в виде упругого элемента – пружины 5, а вместо демпферов-упоров установлены управляемые упорыфиксаторы 6. При среднем положении массы 2 между упорами 6 пружина 5 находится в свободном состоянии и ее усилие равно нулю. В начальном положении пружина взведена и поджимается к упору. При начале работы магнит фиксатора убирает упор, и масса 2 под действием пружины начинает разгоняться.
100
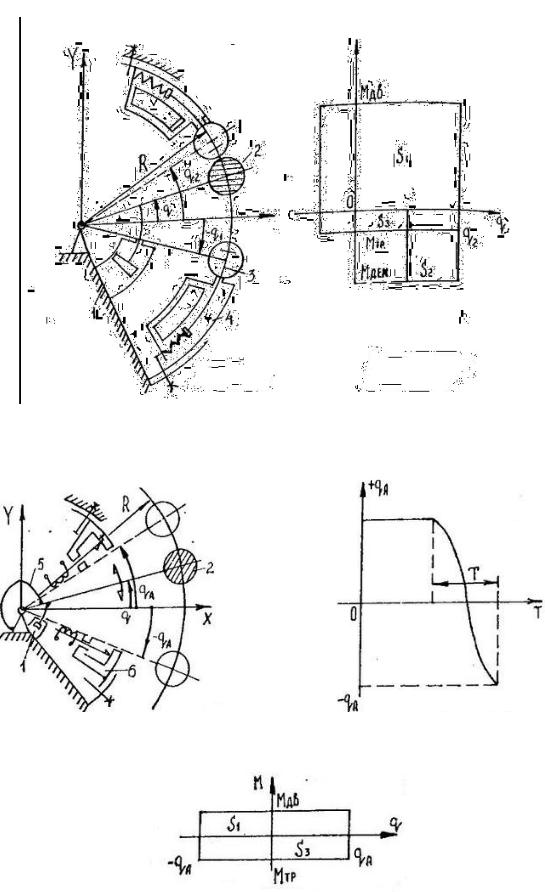
Рис. 3.18 Рис. 3.19
Рис. 3.20 |
Рис. 3.21 |
Рис. 3.22
101
После прохождения среднего положения масса начинает тормозиться за счет перехода кинетической энергии массы обратно в потенциальную энергию пружины. Если бы в системе отсутствовало трение, то масса 2 обязательно пришла бы к симметрично установленному второму фиксатору. Наличие трения обусловливает необходимость наличия привода 1, который восполняет потери энергии на трение.
При такой организации автоматически обеспечиваются такие характеристики, как плавность разгона и торможения, симметрия. Это уменьшает нагрузки в системе, обеспечивает выход на упоры практически с нулевой скоростью, что устраняет необходимость в демпферах. Данные характеристики иллюстрирует закон изменения координат центра массы, показанный на рис. 3.21. На рис. 3.22 представлен график изменения моментов двигателя и скорости звена: за счет организации автоколебательного режима работа двигатели всегда будет равна работе сил трения. Быстродействие системы определяется собственными динамическими свойствами механического колебательного контура и теоретически при известной инерционности можно подобрать жесткость пружины так, чтобы обеспечить требуемое быстродействие. Основные трудности практической реализации подобных систем заключаются в согласовании характеристик механической системы и характеристик привода. Например, при изменении перемещения, в системе целесообразно иметь регулировку, позволяющую изменять пусковой момент в функции перемещения. В качестве регулируемого параметра можно использовать напряжение якоря.
При использовании цикловых роботов требуется большое число точек обслуживания, а не две, как в выше рассмотренном примере. Многопозиционность может быть обеспечена двумя путями. Первый – это увеличение числа степеней подвижности, каждая из которых оснащена описанным аккумулятором. Второй путь связан со специальным исполнением механизма аккумулятора или с использованием дифференциального привода.
В первом случае дополнительно решается и задача динамической развязки.
Если рассматривать простейший двухзвенный вертикально-ангулярный манипулятор, то первая подзадача решается статическим уравновешиванием второго звена относительно оси вращательной пары. Схема такого механизма показана на рис. 3.23. Захват может занимать четыре положения на плоскости, причем обеспечивается однотактный переход из одной позиции в другую.
Дальнейшее совершенствование подобных систем заключается в их адаптивной настройке, т.е. обеспечении инвариантности к действующим возмущениям, например, регулированием подкачки непосредственно в цикле движения, что позволяет поддерживать дозировку в заданных пределах.
102
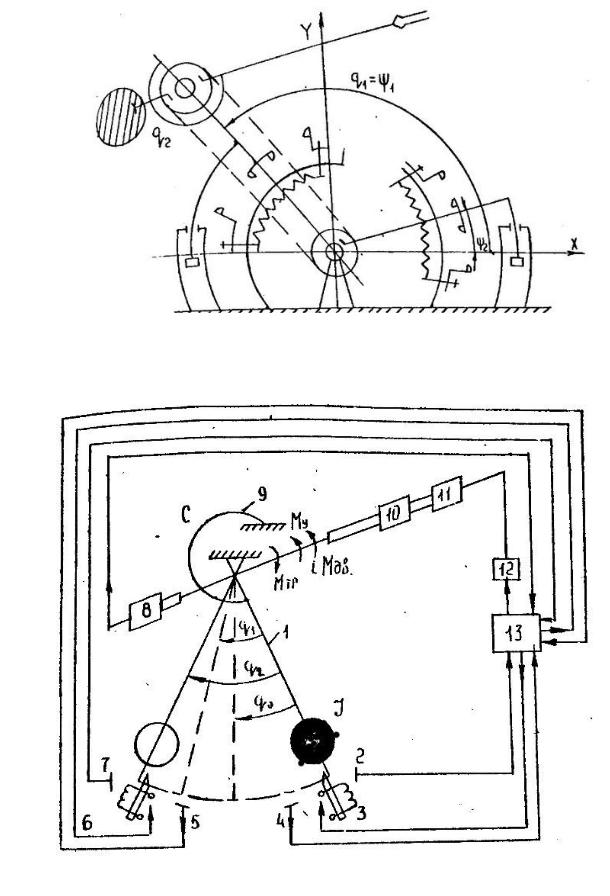
Рис. 3.23
Рис. 3.24
103
Простейшая динамическая модель одной степени подвижности робота, построенная на основе маятника, качающегося в горизонтальной плоскости, показана на рис. 3.24: 1 – звено с приведенным моментом инерции; 2, 7 – датчики крайних положений; 3, 6 – фиксаторы; 4, 5 – датчики фиксированных положений; 8 – датчик углового положения; 9 – накопитель энергии; 10 – редуктор; 11 – двигатель; 12 – усилитель; 13 – управляющий микропроцессор.
Вообще же задача динамической развязки многомерной динамической системы, описываемой системой нелинейных дифференциальных уравнений, разделяется на две подзадачи:
1)обеспечение независимости инерционных коэффициентов от конфигурации манипулятора;
2)поиск системы обобщенных координат, обеспечивающих разделение системы на несколько независимых подсистем.
Компенсация потерь энергии, основанная на применении обратной связи, может быть осуществлена двумя методами: непрерывной коррекцией напряжения на двигателе и дискретной регулировкой на ограниченном интервале.
Идея компенсации непрерывного типа на основе слежения за эталонным законом заключается в непрерывном регулировании подкачки энергии на всем отрезке пути звена 1 между фиксаторами 3 и 6. В режиме обучения запоминаются позиции фиксаторов, регулируются пружины рекуператора, получается
изапоминается приемлемое движение в качестве эталонного. В автоматическом режиме осуществляется периодическое воспроизведение роботом
эталонного движения. Такой метод требует применения высокоточного и помехозащищенного датчика угла, имеющего большую стоимость. Это является серьезным препятствием на пути его реализации.
Рассмотрим метод компенсации импульсного типа. Он основан на оценке кинетической энергии и предполагает подачу компенсирующего воздействия на двигатель только на заключительной отрезке движения звена между фиксаторами. Компенсирующее воздействие определяется переменной составляющей подводимой энергии. Постоянная составляющая, как и в предыдущем случае, сообщается звену за счет эталонного сигнала, запомненного микропроцессором в режиме обучения. Применение метода импульсной компенсации целесообразно тогда, когда момент трения является основным фактором, дестабилизирующим движение робота.
3.6. Орбитальный электропривод
Что требуется от привода робота? Конечно, быстродействие, способность разгона и торможения по возможности без колебаний, высокая точность позиционирования. Однако какой ценой все это делается? Массивный двигатель, тяжелый редуктор, далеко не малогабаритный датчик положения – вот необходимые элементы модуля, которые обеспечат его надежную работу. Везде масса, габариты необходимые, конечно, но одновременно, не лишние ли?
104
Следуя традициям алгоритмов решения изобретательских задач, представим себе идеальную исполнительную систему, т.е. с минимальной массой.
Короче говоря, что-то невесомое и невидимое совершает точные и ловкие движения, тормозит и удерживает звенья робота. Хорошо ли это? Конечно. Облегчение привода позволяет решить одну из двух задач (или обе одновременно, но частично): повысить грузоподъемность или увеличить быстродействие при сохранении потребляемой мощности на прежнем уровне.
Ясно, что и в этом, и в других случаях производительность робота увеличивается.
Сурова критика директора межотраслевого научно-технического комплекса «Ротор», академика Л. Н. Кошкина, высказанная им по телевидению и в печати в адрес промышленных роботов. По его мнению, эти средства гибкой автоматизации – специфический продукт западной буржуазной технологии. Роботы в условиях социализма, уверен он, заведомо невыгодны. По расчетам академика, робот в наших условиях себя не окупает и не является эквивалентной заменой рабочему, обслуживающему станок. Иное дело, считает Л. Н. Кошкин, роторные автоматические линии. Производительность – как у пулемета, ненадежной электроники практически нет, механические цепи коротки и просты. Решается, в принципе, и проблема мобильной переналадки роторов на другое изделие. Во всяком случае, над этим интенсивно работают.
Основной же смысл аргументов в защиту роботов и робототехнических комплексов определяется формулой «каждому – свое». Роторным линиям – массовое производство сравнительно простых изделий. Роботам и на их основе гибким автоматизированным производствам (ГАП) – мелкосерийное и, в принципе, единичное производство изделий высокого уровня сложности. Как говорил академик Д. Е. Охоцимский на IV Всесоюзном совещании по робототехническим системам и ГАП (г. Киев, октябрь 1987 г.): «Роторная линия не сможет сделать автомобиль». Правда, на сегодня и робототехнические линии тоже не могут полностью сделать автомобиль – от сварки листа проката до испытательного стенда. Пока что роботы сваривают кузова, красят их, осуществляют ряд сборок. Но, в принципе, робототехнология вплотную подойдет к решению данной проблемы в ближайшее время.
Роторной же линии это не по зубам. Собрать аэрозольный клапан, цепь, подшипник, аналогичные несложные узлы – пожалуйста! Автомобиль? Не сможет, видимо, и в перспективе – слишком жесткая у него программа. Факт этот не радует. Роторная или иная высокопроизводительная линия, штампующая, к примеру, автомобили десятками в минуту, была бы картиной впечатляющей и эффективной. Одна такая гипотетическая линия способна,
впринципе, заменить несколько автозаводов. На каких же принципах ее организовать? Для ответа на вопрос рассмотрим характерные черты роторной линии и робототехнологического комплекса, а затем попытаемся синтезировать
водном агрегате производительность роторной линии и гибкость промышленного робота.
105
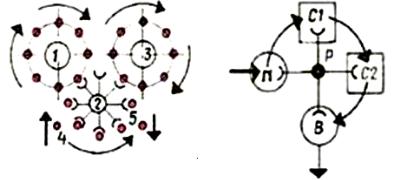
Есть комплексы и с линейной компоновкой, но мы выбрали для анализа комплексы с роботами, действующими в цилиндрической системе координат. Потому что в аналогичной системе фактически трудится и роторная линия. Сравнивая рис. 3.25 с рис. 3.26, видим, что у обоих классов автоматических устройств конфигурация потока деталей фактически одинакова.
Робот Р (рис. 3.26), роботы Р1 и Р2 (рис. 3.27), робот Р с распределителем Рс (рис. 3.28) – это аналоги транспортного ротора (рис. 3.25). Разница лишь в том, что на рис. 3.25 рабочие инструменты вращаются, а на рис. 3.26 технологические позиции (станки С1, С2, С3, С4) неподвижны.
Более глубокая аналогия возникает, если сравнивать конструкцию роботов и транспортных роторов, оснащенных электроприводом с внешними магнитными системами.
Новые разработки в этой области существенно расширили функциональные возможности и роботов, и транспортных роторов. Примеры – на рис. 3.29
и 3.30.
Каков вывод из анализа рассмотренных конструкций? Можно создать новое средство автоматизации на основе синтеза роторной линии и робототехнического комплекса, широко используя устройства так называемой сервисной энергетической среды, например, внешние магнитные системы, а также устройства сервисной информационной среды – разного рода контролирующие позиции с датчиками. Назовем этот гибрид робот-роторной линией с сервисной энергетической средой. Что она будет собой примерно представлять, показано на рис. 3.31.
Рис. 3.25 Рис. 3.26
1. Роторная линия. Рабочие инструменты (например, матрица и пуансоны) закреплены на вращающихся рабочих роторах 1 и 3, изделие 4 с ротора 1 на ротор 3 передает транспортный ротор 2 захватами 5. Технологический процесс на роторах 1 и 3 идет одновременно с транспортировкой изделий по орбитальным траекториям (П – позиция подачи, В – позиция выдачи).
106
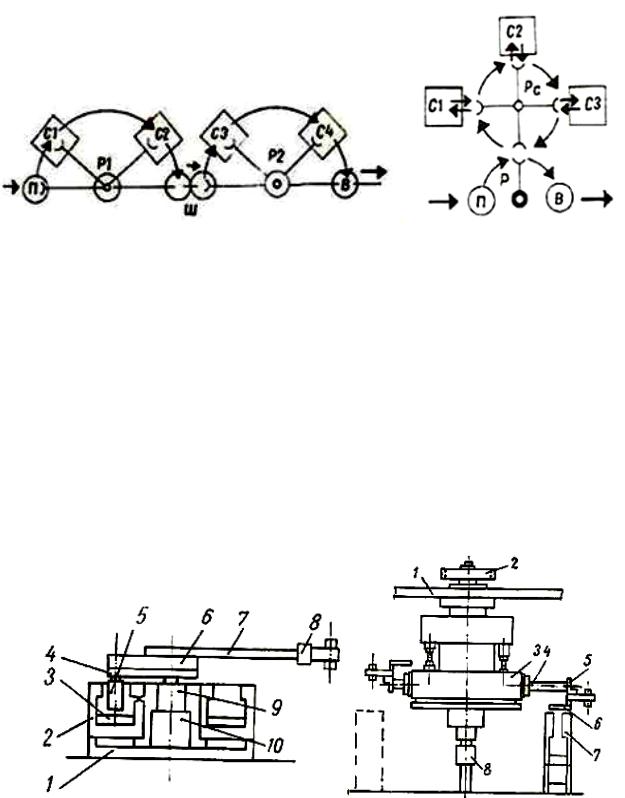
2. Роботизированная станочная система с четырехруким манипулятором. Ротор Р с манипулятором обходит станки С1 и С2. Есть также приемная позиция П и выходная позиция В. Поток деталей движется в направлении, показанном стрелками.
Рис. 3.27 |
Рис. 3.28 |
3.Автоматическая линия (ЭНИКМАШ, г. Воронеж) на основе типового роботизированного технологического комплекса РТК-3 с трехрукими промышленными роботами. Шаговый транспортер Ш связывает робототехнические комплексы (РТК), входящие в состав линии. C1, С2 и т.д. – станки, входящие
вРТК.
4.Робототехнический комплекс с вращающимся распределителем Рс, выполненный в виде крестовины с приводом поворота. Робот Р (однорукий) загружает заготовки в захват распределителя. Затем распределитель поворачивается нужным плечом к соответствующему станку, каждый из которых оснащен механической рукой. После обработки готовую деталь в обратной последовательности передает робот на выходную позицию.
Рис. 3.29 |
Рис. 3.30 |
|
107 |
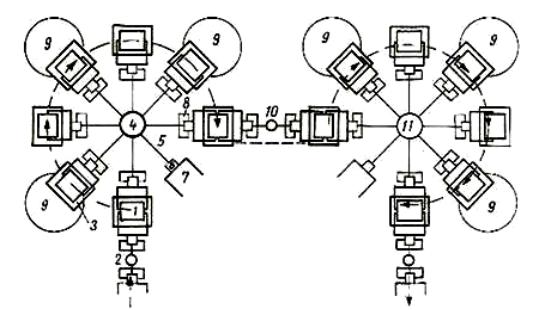
5. Робот с внешней магнитной системой. На основании 1 укреплена концентрическая магнитная система 2 с катушками 3. Якори 5 двигателей закреплены консольно на подвижном поворотном основании 4. Располагаются якори против полюсов. Сверху якорей есть щеточно-коллекторные узлы. На основании 4 смонтированы редукторы 6 приводов выдвижения руки, схвата, ориентации схвата. Магнитная система в нижней части робота показана в разрезе. Робот может иметь несколько якорей и соответствующих приводов. На конце руки 7 установлен схват 8. Есть также 9 – привод поворота, 10 – привод подъема руки.
6. Транспортный ротор роторной линии с внешними магнитными системами (вид сбоку). На основании 1 в подшипниках установлен вал, вращаемый приводом через шестерню 2. На валу закреплен барабан 3 с механизмами выдвижения и ориентации рук 4 со схватами 5. Привод схватов – каркасная обмотка 6, находящаяся в поле внешних магнитных систем 7. Коммутатор 8 управляет величиной тока в обмотках 6. Аналогично можно выполнить не только механизмы схватов, но и приводы выдвижения и другие. При этом громоздкую механику с ее трущимися поверхностями заменяют бесконтактные электромеханические устройства повышенного быстродействия. Одновременно уменьшается и масса подвижной части ротора, что также увеличивает быстродействие.
Обмотки возбуждения внешних магнитных систем можно заменить постоянными магнитами. Ротор будет с несколькими такими внешними магнитными системами, например, в зоне загрузки и в зоне разгрузки. Вторая внешняя магнитная система показана пунктиром.
Рис. 3.31
108
7. Робот-роторная линия по сварке кузовов автомобилей. Исходная заготовка (днище) поступает на позицию 1 с помощью робота-загрузчика 2. Затем она перемещается по сварочным постам 3 транспортным ротор-роботом 4. Он имеет восемь рук 5 с приводами выдвижения, захвата и подъема 6, захватами 7 и внешними магнитными системами 8, установленными радиально. Во вспомогательных зонах 9 можно разместить оборудование, например дополнительные роботы, подающие детали к кузову и перегрузчику 10. Перегрузчик передает изделия на следующий ротор-робот 11, например, окрасочный или сборочный.
Каждый сварочный пост оснащен обычными сварочными роботами или упрощенными цикловыми модулями со сварочным оборудованием.
Таким образом, относительно тяжелое оборудование не вращается, не перемещается вместе с изделием, а заготовка-кузов переставляется роторроботом 4 по позициям.
Сервисная энергетическая среда образована внешними магнитными системами 8, в поле которых расположены активные элементы приводов 6, перемещающие схват. Таким образом, ротор-робот 4 представляет собой увеличенный транспортный ротор, показанный на рис. 3.31, но непосредственно переносящий изделия по позициям 3.
Естественно, для перемещения таких крупных изделий, как автомобильный кузов, важно облегчить подвижные части ротор-робота 4. В частности, привода руки и захвата. Эту задачу и решает сервисная энергетическая среда – внешние магнитные системы.
3.7. Модульные приводы с внешними магнитными системами
Данная система приводов промышленных роботов (ПР) является подсистемой агрегатно-модульной структуры ПР различных компоновочных схем, управляемых системами автоматического управления (САУ) циклового, позиционного и контурного типов. В данном изложении механические конструкции звеньев ПР и CAУ специально не рассматриваются и приводятся лишь в качестве примеров применения приводов с внешними магнитными системами (BMС).
Модули с ВМС представляют собой фактически червячные редукторы (или их комбинации, например, с цилиндрической передачей), на входном валу которых консольно закреплен якорь двигателя постоянного тока (ДПТ) типа ДПР-72.
Якорь ДПТ входит в зазор ВМС при позиционировании. Червячные редукторы выбраны из условия обеспечения самоторможения привода.
Схема различных модулей приведена на рисунках.
109