
Методическое пособие 686
.pdfПогрузчики выпускают с полуповоротным, перекидным и фронталь-
ным рабочим оборудованием. При полуповоротном оборудовании предусмотрена боковая разгрузка ковша в направлении разработки материала. При перекидном же оборудовании материал разгружается назад, а фронтальное оборудование обеспечивает разгрузку ковша со стороны разработки материала. Преимущественно распространены в нашей стране и за рубежом одноковшовые фронтальные погрузчики.
Погрузчики на пневмоколесном ходу монтируются обычно на четырехколесных, двухосных специальных шасси с жесткими рамами и поворотными колесами или с шарнирно-сочлененными рамами. Ходовое оборудование имеет колесные схемы 2x4 и 4х4, а также балансирную подвеску одного из мостов (обычно заднего) для постоянного опирания на грунт всех четырех колес. С этой же целью в машинах с шарнирно-сочлененными рамами предусматривают дополнительные горизонтальные шарниры.
Рабочее оборудование погрузчика состоит из стрелы, рабочего органа, механизмов подъема стрелы и поворота рабочего органа. Навешивают погрузочное оборудование на трактор через специальный портал, на заднюю навеску трактора нередко устанавливают рыхлитель, используемый для предварительного рыхления грунта, разрабатываемого погрузчиком.
Одноковшовые погрузчики являются машинами цикличного действия. В течение одного цикла погрузчик последовательно выполняет следующие основные операции: заполняет ковш и поднимает его в транспортное положение, а после передвижения к месту разгрузки поднимает ковш в положение разгрузки. Далее происходят поворот и разгрузка ковша, опускание его в транспортное положение, после чего погрузчик передвигается к месту загрузки ковша. Некоторые из элементов цикла (например, опускание ковша и движение погрузчика к месту загрузки) можно совмещать.
В зависимости от физико-механических свойств разрабатываемого (погружаемого) материала применяют различные способы заполнения ковша (рис. 5.3). При раздельном способе (рис. 5.3, а) ковш внедряется в грунт под действием напорного усилия ходового оборудования машины. После окончания этой операции машинист поворачивает ковш, внедренный в материал, заполняет его и поднимает стрелу с ковшом в транспортное положение.
Преимущество данного способа работы заключается в его простоте, однако он применим только для работы с легкими (насыпными) материалами, так как при значительных сопротивлениях грунта напорного усилия машины не хватает для достаточного внедрения ковша и он заполняется лишь частично.
К разновидностям данного способа погрузки относят послойную разработку грунта относительно тонкими стружками (скреперный способ), что обеспечивает хорошее заполнение ковша при работе на достаточно прочных грунтах.
31

Рис. 5.3. Способы заполнения ковша:
а – раздельный; б – совмещенный – внедрение ковша с подъемом стрелы и поворотом ковша; в – внедрение ковша с подъемом стрелы
При совмещенном способе ковш заполняется под действием напорного усилия ходового оборудования при одновременном подъеме стрелы и повороте ковша. На практике совмещают операцию внедрения ковша с подъемом стрелы (экскавационный способ, рис. 5.3, б) или операцию внедрения ковша с его поворотом и подъемом стрелы (рис. 5.3, в), в результате чего ковш заполняется лучше и сокращается продолжительность цикла. Совмещать операции можно при установке отдельных насосов для подъема стрелы и поворота ковша или в случае применения делителей потока. Совмещенный способ, требующий высокой квалификации машинистов, особенно эффективен при автоматизированных системах управления погрузчиками.
Для того чтобы грунт не высыпался при подъеме и опускании рабочего оборудования, используют рычажные механизмы поворота ковша параллело-
32

граммного или антипараллелограммного типа, а также применяют гидравлические следящие системы, обеспечивающие подачу жидкости в соответствующую полость гидроцилиндра ковша для сохранения нужного угла запрокидывания.
Базовое шасси или трактор, предназначенные для навески погрузочного оборудования, характеризуются массой, мощностью установленного двигателя Nдв, рабочими υр и транспортными υтр скоростями передвижения, размерами движителя и его маневренностью (В0, L0, rп и др.).
Разгрузка ковша, обеспечиваемая поворотом ковша на выгрузку («от себя»), определяет следующие основные параметры погрузчика: высоту разгрузки Н2, вылет кромки ковша L, углы разгрузки εр и запрокидывания εз ковша (рис. 5.4).
Рис. 5.4. Схема погрузки грунта в автосамосвал
Для обеспечения эффективной совместной работы погрузчиков и авто- мобилей-самосвалов их параметры должны быть взаимоувязаны. Известно, что материал (грунт) в кузове автомобиля распределяется равномерно, если режущая кромка ковша при его разгрузке находится от борта на расстоянии не менее 1/3 ширины кузова.
33
5.3.ПОРЯДОК ПРОВЕДЕНИЯ РАБОТЫ
5.3.1.Используя методические указания, плакаты и кинофильм, изучить общее устройство и назначение одноковшовых погрузчиков.
5.3.2.Определить основные параметры и производительность одноковшового фронтального погрузчика по исходным данным (табл. П.4), используя выражения (5.1) и (5.2).
Техническая производительность одноковшового погрузчика:
ПТ |
60 VК kН |
, т/ч, |
(5.1) |
|
|||
|
ТЦ kР |
|
где VК – геометрическая вместимость ковша, м3; ρ – плотность материала, ρ = 1,6 т/м3; kН – коэффициент наполнения ковша, kН = 1,25; kР – коэффициент разрыхления грунта, kР = 1,08…1,32; ТЦ – время цикла, мин.
Время цикла состоит из четырёх операций:
Т |
|
60 |
|
l |
|
l |
2 |
|
l |
|
l |
|
|
t |
П |
t |
М |
, мин |
|
|
Ц |
|
1 |
|
3 |
4 |
|
|
|
, |
(5.2) |
||||||||||
|
|
|
|
|
|
|
|
|
||||||||||||
|
|
|
Д1 |
|
Д2 |
|
Д3 |
|
|
|
|
|
|
60 |
|
|
||||
|
|
|
|
|
|
|
Д4 |
|
|
|
|
|
|
|
где l1, l2, l3, l4 – пути внедрения ковша в штабель, движения гружёного погрузчика на разгрузку, маневрирования для разгрузки, возвратного хода, в расчётах принимаем l1 = 0,0015 км; l2 = 0,008 км; l3 = 0,003 км; l4 = 0,0015 км; υД1, υД2, υД3,
υД4 – средние действительные скорости при внедрении ковша в штабель, при движении гружёного погрузчика на разгрузку, при маневрировании для разгрузки, при возвратном ходе, км/ч; tП – время переключения передач и золотников гидрораспределителя, tП = 60 с; tМ – время маневрирования транспорта, при челночном способе работы tМ = 5…6 с, при работе с поворотом tМ = 0.
5.4. ФОРМА ОТЧЁТА
5.4.1.Цель работы.
5.4.2.Описание назначения, устройства и классификации одноковшовых погрузчиков.
5.4.3.Определение основных параметров и производительности по формулам (5.1) и (5.2).
5.4.4.Формулирование кратких выводов по лабораторной работе.
КОНТРОЛЬНЫЕ ВОПРОСЫ И ЗАДАНИЯ
1.Назовите классификацию одноковшовых погрузчиков.
2.Поясните назначение и конструкцию одноковшового фронтального погрузчика.
34
3.Охарактеризуйте основные способы заполнения ковша погрузчика.
4.Назовите основные параметры погрузчика.
5.Из каких операций состоит рабочий цикл одноковшового погрузчика?
6.Определите техническую производительность одноковшового погрузчика.
ЛАБОРАТОРНАЯ РАБОТА №6
ИЗУЧЕНИЕ РАБОЧЕГО ПРОЦЕССА И КОНСТРУКЦИИ ГРЕЙДЕР-ЭЛЕВАТОРОВ
6.1. ЦЕЛЬ РАБОТЫ
Цель работы заключается в изучении студентами рабочего процесса, конструкции и определении производительности грейдер-элеваторов.
6.2. ТЕОРЕТИЧЕСКИЕ СВЕДЕНИЯ
Грейдер-элеватор (рис. 6.1) – землеройно-транспортная машина для послойного резания грунта с плужным рабочим органом и транспортирую-
щим устройством непрерывного действия.
Грунт, срезаемый грейдер-элеватором при перемещении, передаётся на конвейер или метатель, который сбрасывает этот груз в валик или слой, образующийся параллельно рабочему перемещению машины. Грунт можно отсыпать в транспортные средства, двигающиеся вместе с грейдер-элеватором.
Грейдер-элеваторы применяются для создания линейных сооружений: насыпей и выемок в дорожном, ирригационном и гидротехническом строительстве, при работе на равнинной местности в грунтах нормальной влажности без включений крупного камня.
Высота насыпи и глубина выемки (до 2 м) ограничена вылетом конвейера, который не может быть большим из условия сохранения устойчивости машины при сравнительно небольшой ширине колеи.
Грейдер-элеваторы классифииируются по типу ножа, по конструкиии и расположению транспортирующего органа, по способу передвижения, приводу, по системе управления и типоразмерам.
По типу ножа различают грейдер-элеваторы с дисковыми, прямыми и криволинейными (полукруглыми) ножами (вторые и третьи получили название стругов). Ножи могут быть поворотными и неповоротными. Грейдерэлеватор с поворотным ножом может работать по челночной схеме с отрывкой одностороннего кювета или односторонней отсыпкой грунта без разворотов всей машины в начале и конце заходки.
35

Рис. 6.1. Грейдер-элеватор самоходный: 1 – одноосный тягач; 2 – генератор; 3
– плужная рама; 4 – дисковый плуг; 5 – конвейер; 6 – двигатель привода конвейера; 7 – гидроцилиндры подъёма
и складывания конвейера; 8 – гидроцилиндр поворота плуга; 9 – основная рама; 10 – гидроцилиндры подъёма плужной рамы и нижней части конвейера
36
По конструкции и расположению транспортирующего органа раз-
личают грейдер-элеватор с ленточными конвейерами (поперечными, диагональными или поворотными), с метателями и конвейерами-метателями.
Грейдер-элеваторы могут также иметь два (продольный и поперечный) конвейера.
По способу передвижения rрейдер-элеваторы делятся на прицепные и полуприцепные к тракторам, навесные на базе автогрейдеров и самоходные на базе одноосных тягачей.
Привод транспортирующего органа может быть механическим (с отбором мощности от двигателя трактора или с самостоятельным двигателем внутреннего сгорания), электрическим и гидравлическим. Наиболее совершенны электрический и гидравлический приводы.
Управление рабочими органами может быть механическим (с отбором мощности для механизмов управления от основной трансмиссии), а также гидравлическим или электрогидравлическим, которые нашли наибольшее применение.
Типоразмеры грейдер-элеваторов определяются производительностью
идальностью перемещения грунта. В свою очередь, производительность зависит от мощности машины и размеров её режущего органа, а дальность транспортирования - от длины и скорости транспортирующего органа.
Являясь машинами непрерывного действия с рациональным процессом перемещения грунта, грейдер-элеваторы отличаются от других землеройно-
транспортных машин высокой производительностью, при работе в отвал она достигает 3000 м3/ч. Эти машины обслуживаются в большинстве случаев одним грейдеристом.
Грейдер-элеватор пpи отсьпке грунта в насыпь, отвал или кавальер дает непрерывный поток грунта, определяемый площадью поперечного сечения срезаемой стружки грунта и скоростью движения машины. Этот поток прерывается в конце и начале захватки. Схема работы грейдер-элеватора показана на рис. 6.2. Рабочий цикл состоит из срезания грунта на длине захватки, подъема ножа, разворота грейдер-элеватора или перехода на противоположную сторону сооружения при пальцевой схеме или маневра для перехода на параллельную стружку при челночной схеме (для грейдер-элеваторов с поворотным ножом) и опускания ножа.
Для прицепных грейдер-элеваторов, обладающих плохой маневренностью, длина захватки должна быть не менее 500 м. Самоходные и челночного действия грейдер-элеваторы могут работать достаточно эффективно
ипри меньшей длине участка. Наиболее распространенными конструкциями грейдер-элеваторов являются полуприцепные машины с автономным двигателем внутреннего сгорания для привода транспортирующего органа и самоходные машины на базе одноосных тягачей.
37
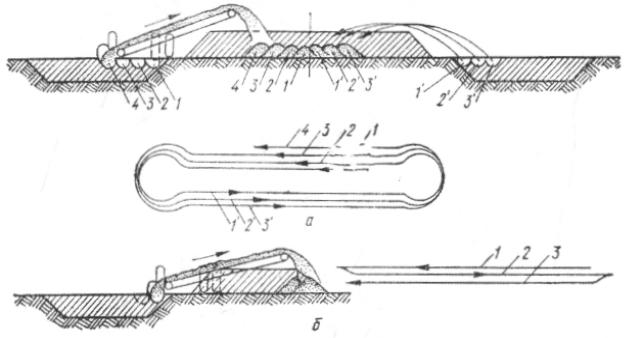
Рис. 6.2. Схемы работы грейдер-элеватора:
а – при возведении насыпи из двухсторонних кюветов-резервов кольцевыми проходами (с разворотом машины в конце каждого прохода); б – при возведении насыпи из одностороннего резерва и челночным движением машины с одной стороны сооружения; 1, 2, 3, 4 – проходы с одной стороны дороги; 1´, 2´, 3´ – соответствующие им проходы с другой стороны
В грейдер-элеваторах широко применяются дисковые сферические ножи (рис. 6.3), укрепляемые при помощи кронштейна 3 на плужной балке 1 или плужной раме, которая, в свою очередь, подвижно соединяется с основной рамой машины. Они располаrаются под углом к горизонтальной плоскости и к направлению движения машины так, чтобы срезаемый ножом пласт грунта, поворачиваясь, ложился на середину ленты конвейера, а процесс резания проходил с минимальной энергоемкостью, что возможно при согласовании положения (грунта) ножа со свойствами разрабатываемого грунта и скоростью резания. Поэтому во всех конструкциях грейдерэлеваторов с дисковыми ножами предусматривается широкий диапазон регулировки положения ножа. Эффективность процесса резания и траектории потока срезанного грунта существенно зависит от формы и размеров ножа. Наиболее рациональной формой является сферический диск с отношением радиуса кривизны сферы к диаметру ножа 0,85…1. С увеличением радиуса кривизны ножа энергоёмкость резания снизится, но ухудшится подача грунта на конвейер.
38

Рис. 6.3. Дисковый режущий орган (плуг) грейдер-элеватора:
1 – плужная балка; 2 – распорка (подкос); 3 – кронштейн; 4 – сферический нож; 5 – зубчатые соединительные диски; 6 – центральный болт
6.3.ПОРЯДОК ПРОВЕДЕНИЯ РАБОТЫ
6.3.1.Используя методические указания, плакаты и кинофильм, изучить общее устройство и назначение грейдер-элеваторов.
6.3.2.Определить основные параметры и производительность грейдерэлеватора по исходным данным (табл. П.5), используя выражения (6.1) и (6.2).
При отсыпке грунта в насыпь из двухсторонних резервов или отрывке канала с отсыпкой грунта на две стороны техническая производительность грейдер-элеватора
ПТ |
F kП L |
, м3/ч, |
(6.1) |
|
|||
|
L /VД tПОВ |
|
где F – проекция площади вырезаемой стружки грунта на плоскость, перпендикулярную к направлению движения грейдер-элеватора, м2; kП – коэффициент, учитывающий потери грунта при подаче его на конвейер, для дискового ножа kП = 0,85…0,95; L – длина захватки, L = 1500 м; VД – средняя действительная скорость грейдер-элеватора, м/ч; tПОВ – время поворота в конце участка, tПОВ = 0,15 ч.
39
Проекция площади вырезаемой стружки грунта: |
|
F h b kФ , м2, |
(6.2) |
где h и b – толщина и ширина срезаемой стружки, находятся из условия заглубления диска на половину; kФ – коэффициент, учитывающий геометрическую форму сечения стружки, для дисковых ножей kФ =0,85.
6.4. ФОРМА ОТЧЁТА
6.4.1.Цель работы.
6.4.2.Описание назначения, устройства и классификации грейдер-
элеваторов.
6.4.3.Определение основных параметров и производительности по формулам (6.1) и (6.2).
6.4.4.Формулирование кратких выводов по лабораторной работе.
КОНТРОЛЬНЫЕ ВОПРОСЫ И ЗАДАНИЯ
1.Поясните конструкцию грейдер-элеватора.
2.Поясните назначение и принцип работы грейдер-элеватора.
3.Назовите виды рабочего органа и привода транспортирующего органа.
4.Из чего состоит дисковый режущий орган?
5.Приведите уравнение производительности грейдер-элеватора.
ЛАБОРАТОРНАЯ РАБОТА №7
ИЗУЧЕНИЕ РАБОЧЕГО ПРОЦЕССА И КОНСТРУКЦИИ МАШИН И ОБОРУДОВАНИЯ ДЛЯ УПЛОТНЕНИЯ ГРУНТОВ
7.1. ЦЕЛЬ РАБОТЫ
Цель работы заключается в изучении студентами рабочего процесса, конструкции и определении производительности машин и оборудования для уплотнения грунтов.
7.2. ТЕОРЕТИЧЕСКИЕ СВЕДЕНИЯ
Насыпи и другие грунтовые сооружения возводятся из грунтов, разрыхленных в процессе разработки и, следовательно, обладающих пониженной прочностью. Поэтому для обеспечения устойчивости земляных сооружений и долговечности возводимых на них инженерных сооружений (зданий, дорожных
40