
Методическое пособие 686
.pdf
талкиваться в ковш между валиком и призмой, а достигнув поверхности отсыпанногогрунта, имеющеговидпологогоконуса, образуетшапкугрунта.
Рис. 3.7. Схемы заполнения ковша грунтом
Эта картина заполнения ковша грунтом не однозначна. Она зависит от вида и состояния грунта. При сыпучих грунтах стружка разрушается сразу же после отделения от массива. Накапливающийся возле ножа грунт не проталкивается вверх, раздвигая отсыпанный ранее грунт, а приподнимает его, оставаясь в нижней части ковша.
3.3. ПОРЯДОК ПРОВЕДЕНИЯ РАБОТЫ
При выполнении работы используется прицепной скрепер ДЗ-111 к колёсному тягачу Т-150К.
3.3.1.Используя скрепер ДЗ-111, лабораторный практикум, плакаты и кинофильм, изучить общее устройство и назначение скреперов.
3.3.2.С помощью рулетки измерить геометрические размеры ковша скрепера (высоту, ширину и длину).
По технической характеристике (табл. П.2) найти средние действительные скорости при операциях рабочего цикла скрепера.
3.3.3.Определить основные параметры и производительность скрепера, используя выражения (3.1) и (3.2).
Техническая производительность скрепера:
ПТ |
3600 VК kН |
, м3/ч, |
(3.1) |
|
|||
|
ТЦ kР |
|
где VК – геометрическая вместимость ковша, м3; kН – коэффициент наполнения ковша, kН = 1,25; ТЦ – время цикла, с; kР – коэффициент разрыхления грунта, kР = 1,08…1,32.
Время рабочего цикла находится по формуле
|
|
l |
|
l |
2 |
|
|
l |
|
l |
4 |
|
tР tМ , с, |
|
ТЦ |
|
1 |
|
|
|
|
3 |
|
|
|
(3.2) |
|||
3600 |
|
VД2 |
|
VД3 |
|
|
|
|||||||
|
VД1 |
|
|
|
|
VД4 |
|
|
||||||
|
|
|
|
|
|
21 |
|
|
|
|
|
|
|
где l1 – длина пути копания грунта, l1 = 0,01…0,02 км; l2 – длина пути разгрузки ковша скрепера, l2 = 0,015…0,03 км; l3 – длина пути транспортировки гружёного скрепера, l3 = 0,5…3 км; l4 – длина пути транспортировки порожнего скрепера, l4 = 0,5…3 км; VД1 – средняя действительная скорость при копании грунта, км/ч; VД2 – средняя действительная скорость при разгрузке ковша, VД2 = 2VД1, км/ч; VД3
– средняя действительная скоростьпри транспортировкегружёного скрепера, VД3 = 0,8VД4, км/ч; VД4 – средняя действительная скорость при транспортировке порожнего скрепера, км/ч; tР – время на разворот скрепера, tР = 10…25 с; tМ – время наманеврированиескрепераитолкача, tМ = 30…60 с.
3.4. ФОРМА ОТЧЁТА
3.4.1.Цель работы.
3.4.2.Описаниеназначения, устройстваиклассификациискреперов.
3.4.3.Определение основных параметров и производительности по формулам (3.1) и (3.2).
3.4.4.Формулирование кратких выводов по лабораторной работе.
КОНТРОЛЬНЫЕ ВОПРОСЫ И ЗАДАНИЕ
1.Перечислите компоновочные схемы скреперов.
2.Поясните назначение и область применения скреперов.
3.Дайте классификацию скреперов.
4.Каким образом можно увеличить наполнение ковша скрепера?
5.Опишите процесс заполнения ковша скрепера.
6.Определите техническую производительность скрепера.
ЛАБОРАТОРНАЯ РАБОТА №4
ИЗУЧЕНИЕ РАБОЧЕГО ПРОЦЕССА И КОНСТРУКЦИИ АВТОГРЕЙДЕРОВ
4.1. ЦЕЛЬ РАБОТЫ
Цель работы заключается в изучении студентами рабочего процесса, конструкции и определения производительности автогрейдеров.
4.2. ТЕОРЕТИЧЕСКИЕ СВЕДЕНИЯ
Автогрейдер (рис. 4.1) широко применяют при строительстве и содержании дорог, а также при аэродромном, промышленном, гражданском, гидротехническом, ирригационном и сельском строительстве.
22

С помощью автогрейдера можно производить профилировочные и планировочные работы при строительстве земляных сооружений, возводить насыпи высотой до 0,6 м, планировать откосы, рыть и очищать кюветы и канавы треугольного и трапецеидального профиля, сооружать корыта для дорожных оснований, перемешивать и разравнивать грунт, щебень, гравийные и вяжущие (цемент, битум) материалы, а также разрушать дорожные покрытия и расчищать от снега площади, улицы и дороги. Они могут разрабатывать грунты до II категории, а при предварительном рыхлении – до категории IV.
Рис. 4.1. Общий вид автогрейдера ДЗ-98
Основным рабочим органом у автогрейдера (рис. 4.2) является отвал. Он расположен в средней части машины между передними и задними колесами. Такое расположение отвала требует увеличения длины машины. Однако при этом локальные неровности грунта, по которому передвигается машина, несущественно или совсем не сказываются на планирующих особенностях машины.
Как видно из рис. 4.3, местные неровности вызывают вертикальное перемещение отвала в основном только при наезде на них передних колес. Когда передние колеса окажутся в зоне возвышения или впадины высотой или глубиной Н, вертикальное отклонение ножа отвала составит h = Н/2. Такая же неровность под задними колесами при наличии у них балансирной подвески может вообще не сказаться на положении отвала.
23

Рис. 4.2. Конструктивная схема автогрейдера:
1 – корчеватель; 2, 5 – система управления; 3, 12 – карданные передачи; 4 – основная рама; 6 – вал рулевого колеса; 7 – кабина; 8 – двигатель; 9 – радиатор; 10 – ведущие колеса; 11 – сцепление; 13 – трансмиссия; 14 – отвал; 15 – поворотный круг; 16 – рама поворотного круга; 17 – цапфа переднего моста; 18 – ведомые управляемые колеса
Рис. 4.3. Влияние неровностей на планирующие свойства автогрейдера
24
Помимо отвала автогрейдер может быть укомплектован примерно еще 20 видами сменного дополнительного оборудования. Среди них наиболее часто используют кирковщик, бульдозерный отвал, плужный снегоочиститель, удлинители отвала, откосник, грейдер-элеватор и др. При работе машины отвал можно установить наклонно к вертикальной и горизонтальной плоскостям, поворачивать в плане и выносить в сторону от продольной оси. Для достижения наибольшей производительности и наилучших условий машины угол наклона отвала к вертикальной плоскости – поперечный наклон – нужно выбирать таким, чтобы угол резания его ножа составлял около 35…40°. Угол наклона отвала к горизонтальной плоскости при резании, перемещении и планировке грунта целесообразно принимать в пределах 15…18°, а при планировке откосов устанавливать до 45°. Угол поворота отвала относительно продольной оси машины – угол захвата, обычно выбирают из условия получения наименьшего сопротивления при отводе грунта в сторону и принимают в пределах 35…45°.
Автогрейдеры классифицируют в зависимости от мощности силовой установки и соответствующей ей массы машины, вида системы управления
иколесной схемы ходового оборудования.
Взависимости от мощности силовой установки и соответствующей ей массы машины автогрейдеры делятся на легкие – мощностью до 50 кВт и массой машины до 9 т, средние – мощностью до 75 кВт и массой до 13 т, тяжелые – мощностью до 120 кВт и массой до 19 т и особо тяжелые – мощностью свыше 180 кВт и массой более 24 т.
По типу системы управления различают автогрейдеры с механической
игидравлической системами управления. На выпускаемых в настоящее время автогрейдерах применяется только гидравлическая система управления.
Ходовое оборудование автогрейдеров выполняется двухосным или трехосным. Колеса передней оси у всех автогрейдеров управляемые, а у тяжелых – еще и ведущие.
Взависимости от конструктивного решения ходового оборудования автогрейдеры принято характеризовать колесной формулой. В ней указывается количество управляемых А и ведущих Б осей из общего числа осей В ходового оборудования машины. Наибольшее распространение на автогрейдерах получила конструкция ходового оборудования с наклонными передними колесами, соответствующая формуле
А х Б х В = 1 х 2 х 3.
Несмотря на простоту конструктивного решения ходового оборудования, автогрейдер имеет хорошие планирующие и тягово-сцепные показатели. Наличие наклоняемых передних колес позволяет надёжно выдержать траекторию движения.
При исполнении ходового оборудования по схеме 1x3x3, применяемого на тяжелых автогрейдерах, повышаются тягово-сцепные свойства, но усложняется конструкция привода передних колес.
25
Рабочий процесс автогрейдера состоит из копания грунта, перемещения, укладки и разравнивания грунта в земляном сооружении.
При копании грунт может разрабатываться как всей шириной отвала, так и одним из его концов. В первом случае режущая кромка отвала устанавливается параллельно поверхности грунта, а во втором – наклонно. При этом отвал может находиться непосредственно под рамой автогрейдера или сбоку от нее. Глубина копания в первом случае может доходить до 250 мм, а во втором – до половины высоты отвала.
При наклонной установке отвала режущая кромка его обычно устанавливается под углом 10…15° к поверхности грунта. Площадь срезаемой стружки грунта в этом случае несколько меньше, чем при горизонтальном положении. Это обусловливает снижение сопротивления при копании и позволяет увеличить скорость передвижения машины и ее производительность. На практике с такой установкой выполняется большая часть земляных работ.
Существенное влияние на сопротивление копанию оказывает выбор угла наклона отвала к вертикальной плоскости. Его обычно принимают таким, чтобы угол резания ножа отвала в слабых и тяжелых грунтах был соответственно равен 45 и 35°.
Срезанный отвалом грунт в дальнейшем может перемещаться перед отвалом или отводиться в сторону от направления движения машины. Это зависит от положения режущей кромки отвала относительно продольной оси машины, определяемого углом между ними, называемым обычно углом захвата. При значении этого угла, близком к 45°, грунт интенсивно скользит по отвалу и отводится в сторону от продольной оси машины. При угле захвата, близком или равном 90°, грунт остается перед отвалом и перемещается им в направлении движения машины. На практике угол захвата назначается в зависимости от вида работ, выполняемых машиной. При зарезании отвала в грунт одним из его концов этот угол принимается равным 35…50°.
При выполнении автогрейдером отделочных и планировочных работ угол захвата устанавливают в пределах 45…90°, причем на первой стадии выполнения этих работ, когда подлежащий планировке слой грунта имеет большую толщину, этот угол имеет меньшее значение. По мере улучшения разравнивания и повышения уплотнения грунта угол захвата постепенно увеличивают, принимая на конечной стадии планировки равным 90°. Поскольку в этот момент сопротивление машине невелико, на отвал обычно устанавливают уширитель. Это увеличивает ширину полосы обрабатываемого грунта и производительность машины.
При копании с отводом грунта в боковом направлении наиболее рациональным считается угол захвата, равный 60°. На отвод грунта в этом случае машина расходует несколько большую энергию, чем при угле захвата в 45°. Однако при этом она обрабатывает более широкую полосу сооружения и отводит грунт на большее расстояние в сторону.
26
В процессе выполнения земляных работ на строительных объектах автогрейдеры совершают круговые или челночные движения. Последнее зависит от длины и ширины участков, на которые разбивается объект строительства.
При применении автогрейдеров на строительстве дорог длина участков, называемых здесь захваткой, зависит от рельефа местности, наличия мостов, труб, сроков и объемов работ и др. и составляет 0,15…1,5 км. При захватках длиной 0,4…1,5 км автогрейдеры перемещаются по круговым траекториям. Двигаясь при каждой проходке в пределах всей длины захватки, они выполняют только одну определенную операцию при одной установке отвала.
При коротких захватках длиной 0,15…0,4 км работы ведутся челночными движениями автогрейдера, причем, если длина захватки близка к 0,15 км, автогрейдер совершает обратное движение вхолостую на повышенной скорости. При захватках длиной более 0,15 км автогрейдер разрабатывает грунт при прямом и обратном движениях, поворачивая отвал на 180° в конце участка перед обратным ходом.
4.3. ПОРЯДОК ПРОВЕДЕНИЯ РАБОТЫ
При выполнении работы используется автогрейдер ЗТМ 1-43.
4.3.1.Используя автогрейдер ЗТМ 1-43, лабораторный практикум, плакаты и кинофильм, изучить общее устройство и назначение автогрейдеров.
4.3.2.С помощью рулетки измерить высоту и длину отвала автогрейдера,
атакже угол поворота отвала в плане.
По технической характеристике (табл. П.3) найти средние действительные скорости при операциях рабочего цикла автогрейдера.
4.3.3. Определить основные параметры и производительность автогрейдера, используявыражения(4.1) и(4.2).
Техническая производительность автогрейдера:
ПТ |
|
L F |
, м3/ч, |
(4.1) |
|
||||
|
|
ТЦ |
|
|
где L – длина участка, в расчётах принимаем L = 400 м; |
F – площадь вырезаемой |
стружки, принимаемдляII категориигрунтаF =0,07…0,09м2; ТЦ – времяцикла, ч. Время рабочего цикла автогрейдера находится по формуле
|
|
|
n |
|
n |
П |
|
n |
|
|
2t |
Р |
n |
|
|
Т |
Ц |
2L |
К |
|
|
|
О |
|
|
|
|
, ч, |
(4.2) |
||
|
|
|
|
|
|
|
|||||||||
|
|
|
|
VД2 |
|
VД3 |
|
|
3600 |
||||||
|
|
VД1 |
|
|
|
|
|
|
где длина участка L подставляется в км; n – общее число проходов; nК – число проходов при копании грунта; nП – число проходов при перемещении грунта; nО – число проходов при отделки насыпи; VД1, VД2, VД3 – средние действительные скорости при копании, перемещении грунта и отделочных проходах, км/ч; tР – время на разворот автогрейдера, tР = 60…180 с.
27
4.4. ФОРМА ОТЧЁТА
4.4.1.Цель работы.
4.4.2.Описание назначения, устройства и классификации автогрейдеров.
4.4.3.Определение основных параметров и производительности по формулам (4.1) и (4.2).
4.4.4.Формулирование кратких выводов по лабораторной работе.
КОНТРОЛЬНЫЕ ВОПРОСЫ И ЗАДАНИЯ
1.Поясните устройство автогрейдера.
2.Какие виды дополнительного оборудования могут навешиваться на автогрейдер?
3.Назовите классификацию и главный параметр автогрейдеров.
4.Какие конструктивные признаки автогрейдера влияют на точность планировки земляного полотна?
5.Что означают цифры в колёсной формуле автогрейдера?
6.Определите техническую производительность автогрейдера.
ЛАБОРАТОРНАЯ РАБОТА №5
ИЗУЧЕНИЕ РАБОЧЕГО ПРОЦЕССА И КОНСТРУКЦИИ ОДНОКОВШОВЫХ ПОГРУЗЧИКОВ
5.1. ЦЕЛЬ РАБОТЫ
Цель работы заключается в изучении студентами рабочего процесса, конструкции и определении производительности одноковшовых погрузчиков.
5.2. ТЕОРЕТИЧЕСКИЕ СВЕДЕНИЯ
Одноковшовый погрузчик состоит из базовой машины и рабочего оборудования шарнирно-сочлененного типа. В комплект сменных рабочих органов погрузчика входят несколько типов ковшей, захваты для работы со штучными грузами, бульдозерный отвал и др.
Одноковшовые погрузчики с ковшовым оборудованием (рис. 5.1) широко применяют для разработки карьерных сыпучих и мелкокусковых материалов с погрузкой их в транспортные средства, для послойной разработки грунта, перемещения его и отсыпки в отвал, а также выполнения погрузочноразгрузочных и транспортных работ с различными сыпучими материалами.
28
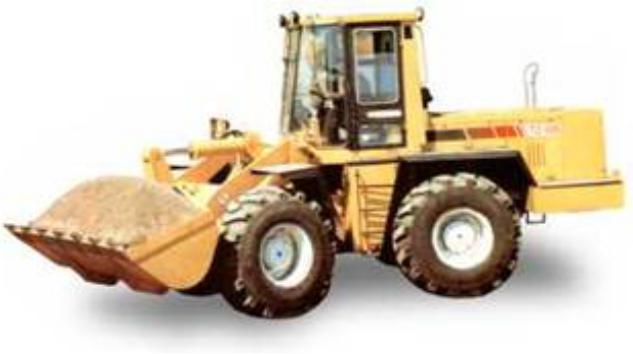
Рис. 5.1. Общий вид одноковшового колёсного погрузчика ТО-18В
Одноковшовые погрузчики со сменными рабочими органами используются для погрузки и разгрузки контейнеров, лесоматериалов, выполнения планировочных работ и др.
По главному параметру – номинальной грузоподъемности, одноковшовые погрузчики разделяют на малогабаритные (менее 5 кН), легкие (5…20 кН), средние (20…40 кН), тяжелые (40…100 кН) и большегрузные (более 100 кН).
Погрузчики классифицируют также по типу ходового оборудования,
базовой машины, расположению, типу и приводу погрузочного оборудования.
По типу ходового оборудования погрузчики подразделяют на гусеничные и колесные. Вследствие более высокой мобильности и транспортабельности наиболее распространены колесные погрузчики (рис. 5.2, а). Гусеничные погрузчики (рис. 5.2, б) используют при работе на грунтах со слабой несущей способностью, а также на взорванных скальных грунтах, где необходимо реализовать большие усилия на ковше и где шины быстро изнашиваются.
По типу базовой машины различают погрузчики на специальных базовых шасси и тягачах, погрузочных модификациях промышленных тракторов и промышленных модификациях тракторов общего назначения.
Специальные шасси и тягачи создают в расчете на агрегатирование с ними погрузочного оборудования. У них более рациональная компоновка узлов и агрегатов, однако погрузчики на базе собственных шасси экономически целесообразны только при большой серийности их выпуска или при создании машин специального назначения.
29

Рис. 5.2. Одноковшовые фронтальные погрузчики:
а – на базе специального колесного шасси с жесткой рамой и поворотными колесами; б – на базе гусеничного тягача; 1 – рабочий орган – ковш; 2 – механизм поворота ковша; гидроцилиндры: 3 – механизма поворота ковша; 4 – механизма подъема стрелы; 5 – шасси; 6 – портал; 7 – трактор; 8 – рыхлитель
30