
Методическое пособие 557
.pdfКаждый из приведенных типов воздействия определяет назначение соответствующего технологического оборудования
ипроцессов:
-для получения монокристаллов или порошков тугоплавких материалов;
-для осаждения толстых или тонких слоев;
-для очистки поверхности от органических или неорганических загрязнений или пленок;
-для травления слоев физическим распылением;
-для травления слоев плазмохимическим способом;
-для полимеризации поверхностных слоев и т. д.
В конкретном технологическом оборудовании может использоваться плазма с различными сильно отличающимися характеристиками и параметрами. Это может быть либо термическая низкотемпературная квазиравновесная плазма с высокой среднемассовой температурой газа, либо холодная неравновесная плазма при пониженном давлении с высокой электронной температурой.
Виды воздействия на обрабатываемый материал могут резко отличаться, однако в любом случае инструментом воздействия служит плазма газового электрического разряда либо ее составляющая. Обычно это плазма с контролируемым составом обновляемой газовой среды в замкнутом объеме.
Чаще всего для передачи энергии в плазму используются такие виды разрядов, которые не вносят загрязнения конструктивных элементов разрядного устройства.
30

2. ПРОЦЕССЫ И ТЕХНОЛОГИИ ПЛАЗМЕННОЙ ОБРАБОТКИ
2.1. Место плазменных процессов в технологии микроэлектроники
Технологический процесс изготовления ИМС можно свести к последовательности повторяющихся типовых операций (рис. 2.1), таких как нанесение покрытий и функциональных слоев (проводящих, изолирующих, полупроводниковых), литографию (формирование топологического рисунка на поверхности), травление и очистку поверхности, диффузию и ионное легирование.
а |
б |
в |
г |
д |
e |
Рис. 2.1. Типовые операции в производстве в производстве ИМС
При постоянно существующей тенденции к повышению степени интеграции ИМС в первую очередь повышаются требования к качеству проведения «размерных» операций, то есть тех, которые непосредственно определяют геометрические параметры получаемых элементов (рис. 2.1 г, д). Важнейшими из таких операций являются операции размерного травления, ко-
31
торые по функциональному назначению подразделяются на следующие группы:
Травление органических материалов. Типичным при-
мером здесь является вскрытие окон в экспонированной фоторезистивной маске (фоторезист - органический светочувствительный полимер) для последующего размерного травления нижележащего слоя.
Травление неорганических материалов. Набор возмож-
ных процессов здесь очень широк и обусловлен широким набором неорганических материалов, применяемых в производстве интегральной кремниевой электроники. Среди таких процессов в первую очередь необходимо отметить размерное травление моно- и поликристаллического Si, диэлектрических пленок SiO2 и Si3N4, а также пленок некоторых металлов (Al, Cu, Au, W, Mo и др.), используемых для создания межэлементных соединений, контактов, промежуточных и согласующих слоев.
При невысокой степени интеграции ИМС и при характерных размерах элементов не ниже 10 мкм все перечисленные процессы могут реализоваться методами жидкостного травления, при этом результат травления является удовлетворительным по всей совокупности выходных характеристик, таких как воспроизводимость, селективность и анизотропия. Тем не менее, при переходе к субмикронной технологии ИМС жидкостные методы травления становятся неприемлемыми в силу двух основных причин: 1) жидкостное травление носит изотропный характер, то есть скорость его одинакова по всем направлениям. Это создает проблему бокового подтравливания под маску, ри этом фактический размер протравленной области в слое под маской существенно превышает заданный размером окна в маске; 2) применение жидкостных методов сопровождается загрязнениями поверхности продуктами реакций и сторонними примесями, содержащимися в исходных реагентах и в воде, использованной для их приготовления. Замена жидкостных методов на «сухие» - плазмохимические и ионно-плазменные - позволяет существенно улучшить анизотропию процесса трав-
32
ления, увеличить его разрешение и дает в руки технолога мощный и гибкий инструмент, с помощью которого можно получать структуры заданной конфигурации и нужных размеров. Меняя состав плазмообразующего газа, параметры разряда можно в широких пределах варьировать скорости целевых процессов, их анизотропию и селективность в соответствии с требованиями, предъявляемыми к размерам и характеристикам изделий.
Анализ литературных данных последних лет, в основном зарубежных, показывает, что развитие технологии плазменной обработки материалов происходит по пути интенсификации и повышения эффективности уже хорошо отработанных и изученных процессов. В этом плане необходимо отметить, что «чистое» плазмохимическое травление, обеспечиваемое только химическим взаимодействием активных частиц плазмы с обрабатываемым материалом, начиная со второй половины 90- х годов, используется очень ограниченно. Подавляющее большинство технологических процессов травления в плазме в настоящее время реализуется в виде ионно-стимулированных и ионно-лучевых процессов, которые сочетают химические и физические эффекты воздействия на обрабатываемый материал. Наибольшее распространение получили такие перспективные методы, как реактивное ионное травление (RIE, Reactive Ion Etching), лазерно- (LIE, Laser Induced Etching) и фотостимулированные процессы (PIE, Photo InducedEtching).
2.2. Классификация плазменных технологических процессов по механизму воздействия
на обрабатываемую поверхность
В основе классификации плазменных технологических процессов по механизму воздействия на обрабатываемую поверхность (рис. 2.2) лежит выделение трех основных видов обработки с использованием плазмы:
-ионной;
-плазмохимической;
33
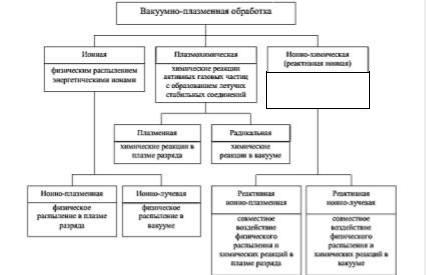
- ионно-химической (иногда называемой реактивноионной).
совместное воздействие физического распыления и химических реакций
Рис. 2.2. Классификация плазменных технологических процессов по механизму воздействия
на обрабатываемую поверхность
Ионная обработка (ИО) представляет собой процесс, при котором поверхностные слои твердого вещества подвергаются бомбардировке ускоренными положительными ионами, как правило, инертных газов, химически не реагирующими с обрабатываемым материалом. Если обрабатываемый материал помещен на электродах или держателях, соприкасающихся с плазмой разряда, то обработку в таких условиях называют ионно-плазменной. Если материал помещен в вакуумную зону обработки, отделенную от области плазмы, то обработка в этом случае называется ионно-лучевой.
При плазмохимической обработке (ПХО) основными ответственными за процесс частицами выступают химически активные нейтральные атомы, молекулы, радикалы, часто объединяемые под общим названием химически активные части-
34
цы (ХАЧ), вступающие в химические реакции с поверхностными слоями материалов. Если обрабатываемый материал находится в области плазмы разряда, то обработку называют плазменной. В этом случае химические реакции на поверхности материала будут активироваться низкоэнергетическими электронной и ионной бомбардировками, а также фотонной бомбардировкой. Если материал находится в вакуумной зоне обработки, обычно называемой в этом случае реакционной зоной и отделенной от области плазмы, то обработку производят ХАЧ без активации электронной и ионной бомбардировками, а в ряде случаев и при отсутствии воздействия фотонов. Такую обработку называют радикальной.
Ионно-химическая обработка (ИХО) представляет сов-
местное воздействие физического распыления и химических реакций с участием ионов различных веществ и поверхностных атомов материала. Если обрабатываемый материал находится в области плазмы, то процесс в этих условиях называют
реактивным ионно-плазменным. Тогда ХАЧ могут достав-
ляться к поверхности материала из плазмы разряда или образовываться на поверхности при ударной диссоциации молекул или нейтрализации атомарных ионов. На поверхность материала воздействуют также электронная и фотонная бомбардировки.
Если же из объема плазмы с помощью системы вытягивающих, ускоряющих или фокусирующих устройств выделяется поток молекулярных или атомарных ионов, такая обра-
ботка носит название реактивной ионно-лучевой.
В процессах ионно-химической обработки трудно выделить вклад физического и химического механизмов, так как физическое распыление активирует поверхность материалов, повышая скорость химических реакций, которые, в свою очередь, ослабляют химические связи поверхностных атомов, увеличивая скорость их поверхностного распыления. Так как заметных скоростей физическое распыление достигает при энергиях ионов больше 1,6 10-17 Дж (100 эВ), то данная энергия ионов, бомбардирующих материал, служит условной гра-
35
ницей между процессами ИХО и ПХО. При Eи < 100 эВ обработка будет относиться к ПХО, а при Eи > 100 эВ - к ИХО.
2.3. Технологические требования и параметры, характеризующие процесс травления
Процесс плазменного травления характеризуется скоростью, анизотропией, разрешающей способностью, селективностью, равномерностью и текстурой, загрузочным эффектом.
Скорость плазменного травления характеризует скорость удаления материала и измеряется в нм/мин или других аналогичных единицах. При выборе скорости процесса необходимо учитывать следующие соображения: во-первых, нежелателен длительный цикл технологической обработки по соображениям снижения производительности аппаратуры. Вовторых, нежелательны и слишком быстрые технологические процессы по причине ухудшения воспроизводимости результатов, равномерности обработки и т.д. Наиболее целесообразны времена обработки от нескольких минут до часа, хотя в реальной технологии могут быть отклонения в ту или иную сторону. Поэтому если глубина травления задана, то скорость процесса может предварительно оценена, и эти оценки могут быть использованы при подборе технологических режимов.
Анизотропия – это фактор, характеризующий искажение изображения при переносе его с маски на объект за счет бокового подтравливания (рис. 2.3). Анизотропия может быть определена как отношение скоростей травления материала по нормали и по касательной к поверхности или как отношение глубины травления h к боковому подтравливанию δ: A = R / R||
= h / δ.
Очевидно, что чем выше анизотропия, тем выше качество получаемых изделий, хотя в ряде случаев изотропное травление позволяет получить положительные результаты.
Разрешающая способность характеризует степень интеграции микросхем и представляет собой максимально возможное число линий рисунка на 1 мм поверхности RS = 1000 / 2l,
36

где l, мм, - ширина раздельно передаваемой линии. Кроме этого, разрешающую способность часто определяют наименьшей шириной линии или наименьшим расстоянием между линиями (в микрометрах), которых удается достичь в технологическом процессе. Разрешающая способность в целом определяется всем комплексом технологических процессов, в том числе и процессом травления материала.
δ
h
а б
Рис. 2.3. Примеры анизотропного (а) и изотропного травления (б)
Селективность травления – это отношение скоростей травления двух разных материалов (обычно основного материала и фоторезистивной маски – см. рис. 2.3) в одних и тех же условиях и в одном направлении. Селективность должна быть такой, чтобы можно было обеспечить травление основного материала на заданную глубину до полного стравливания маски.
Равномерность травления и текстура. Равномерность процесса травления обычно выражается в процентах и может быть найдена как
|
|
− |
|
|
|
|
= 2 |
|
|
∙ 100, |
(2.1) |
||
|
+ |
|
||||
|
|
|
||||
|
|
|
|
|
где Rmax и Rmin - максимальная и минимальная скорости травления, соответственно.
Текстурированность поверхности характеризует изменение ее шероховатости после травления. В зависимости от условий процесса и рабочего газа текстурированность может как уменьшаться, так и возрастать.
37
Загрузочный эффект - это уменьшение скорости травления с увеличением площади обрабатываемых изделий, связанное с обеднением газовой фазы активными частицами из-за их расхода в процессе травления. Наличие загрузочного эффекта свидетельствует о том, что травление материала протекает с лимитирующей стадии доставки ХАЧ к поверхности. Этот эффект необходимо учитывать при групповой обработке пластин.
2.4. Рабочие газы для плазменного травления
Плазмообразующая среда в реакторе в первую очередь должна обеспечить необходимую скорость травления, селективность и анизотропию. В то же время к рабочим газам предъявляется и ряд побочных требований - безопасность в работе и отсутствие в продуктах реакции токсичных соединений, химическая инертность по отношению к конструкционным элементам установок и откачных средств, отсутствие взаимодействия с маслами вакуумных насосов, вызывающих их деградацию, и др.
Необходимость травления широкого ассортимента материалов и обеспечение указанных выше требований привело к использованию большого количества различных газов и их смесей в технологии плазменного травления.
Инертные газы применяются в качестве основного компонента при ионном травлении и входят в состав различных смесей в качестве инертных разбавителей.
Фторсодержащие газы нашли наиболее широкое применение при травлении кремния и его соединений, а также ряда металлов 4 - 6 группы Периодической системы Д.И. Менделеева. Чаще всего используются углеродные галогенсодержащие соединения, имеющие общее название хладоны (фреоны). Общая формула соединений этого типа имеет вид CkHlFm(Cl)Br n, где k, l, m, n - число атомов углерода, водорода, фтора и хлора (брома) в молекуле хладона. Хладоны обычно распознаются по номерам, которые записываются как
38
(k - 1)(l + 1)m. Наибольшее применение из хладонов получил тетрафторметан CF4 (хладон 14). Общие недостатки этой группы газов - возможность образования токсичных продуктов в процессе травления, склонность к полимеризации (особенно для сложных соединений), возможность образования элементарного углерода на обрабатываемой поверхности (для простых хладонов). Для подавления двух последних эффектов в рабочий газ часто добавляют кислород. В то же время широкая номенклатура хладонов и использование их смесей с другими газами (кислородом, водородом, азотом и т.д.) позволяет создавать рабочие смеси, обеспечивающие необходимую скорость, селективность и анизотропию процесса практически для любых объектов, образующих газообразные соединения с фтором. Из других фторсодержащих газов следует отметить шестифтористую серу SF6, применение которой позволяет достичь высоких скоростей травления без осаждения на поверхности твердых продуктов разложения исходного газа. Весьма перспективными являются также фториды азота (в первую очередь NF3) и благородных газов (например, XeF2), позволяющие обеспечить максимальную чистоту процесса плазмохимического травления. Чистый фтор практически не применяется из-за своей высокой химической активности по отношению к конструкционным материалам технологического оборудования и токсичности.
Хлорсодержащие газы используются для травления металлов и соединений, не образующих газообразных продуктов с фтором – полупроводниковые соединения типа A3B5, алюминий, медь и некоторые другие. Источником хлора в плазмохимических процессах могут служить хлорсодержащие хладоны, ибо в условиях разряда отщепление хлора происходит в первую очередь. Общие недостатки хлоруглеродных соединений - высокая степень полимеризации в условиях разряда, что вызывает загрязнение аппаратуры и обрабатываемого изделия, замедление травления, быструю деградацию масел вакуумных насосов. Введение кислорода не устраняет полностью полимеризационные явления, но приводит к образованию ряда ток-
39