
III. хтс
.pdfТак как колчедан, порода, которая содержит высокую долю примесей, его потребуется больше для производства, а также необходима будет более тщательная система очистки, поэтому Сера дороже колчедана, но в итоге получается выигрыш.
2)Использование избытка одного из реагентов в исходной смеси как
правило, более дешевого и доступного. В предыдущем примере H2SO4 используют избыток кислорода по отношению к стехиометрии реакции. Это универсальный прием повышения степени превращения одного из исходных веществ, участвующих в реакции.
3)Противоточный контакт фаз - известное решение, обеспечивающее максимальную движущую силу, как в процессе теплопередачи, так и в процессе массообмена. (используют во всех сорбционных процессах HNO3 H2SO4 поглощение оксидов)
4)Фракционный рецикл используют при неполном превращении исходных реагентов. В системе разделения после реактора выделяют не прореагировавшие реагенты и возвращают их на переработку. Типичный пример - синтез аммиака, 3Н2 + N2 = 2NH3, в котором после выделения аммиака оставшуюся азотоводородную смесь снова направляют в реактор синтеза.
5)Утилизация отходов позволяет получить дополнительные полезные продукты из побочных продуктов реакции, практически всегда образуемых вместе целевым продуктом. Если, например, найдется потребитель огарка в производстве серной кислоты (а в нем есть много полезных и ценных веществ), то производство кислоты из колчедана может оказаться вполне конкурентным.
6)Альтернативное сырье. Использование не возобновляемого сырья (нефть, газ, руды…) заставляет не только искать способы его полного использования, но и другие сырьевые источники. Использование отходов производств - одно из направлений расширения сырьевых источников. Другое направление - альтернативные источники первичного сырья.
7)Комбинирование производств
Комбинированное производство (химико-технологическая система), представляет собой взаимосвязанные технологические процессы для производства одного или нескольких продуктов.
Характерным является совместное производства карбамида СО(NН2)2 и аммиака NН3. Первый из них получают взаимодействием NН3 с СО2:
СО2 + 2NН3 = СО(NН2)2 + Н2О
До этого оба исходных вещества были образованы в аммиачном производстве по следующим реакциям:
СН4 + 2Н2О = СО2 + 4Н2 ;
3Н2 + N2 = 2NН3
Оба технологических процесса получение карбамида СО(NН2)2 и аммиака NН3.связаны не только линиями передачи СО2 и NН3, но и другими вспомогательными связями, материальными и энергетическими. Понятно, что можно организовать и две отдельные ХТС, продукты одной из них являются сырьем для другой.
2. Концепция полного использования энергетических ресурсов
Концепция полного использования энергетических ресурсов направлена на минимизацию затрат на энергетические и тепловые ресурсы, полное использование их в процессе.
1)Регенерация теплоты и энергии. H2SO4 В ряде случаев для проведения процесса (например, в реакторе) необходимо нагреть поток, а после этого - его охладить. Выгодно входящий поток нагреть теплотой выходящего потока. Такая схема была представлена на примере реактора окисления диоксида серы.
Теплоту можно также перевести в пар в котле-утилизаторе и затем использовать как энергоноситель для привода паровых турбин или как теплоноситель в технологических целях в этом же производстве.
2)Утилизация теплоты и энергии подразумевает использование теплоты (энергии) потока для выработки тепловых (пар, горячая вода), электрических и других энергетических ресурсов, используемых не в самом производстве, т.е. они поставляются на сторону.
3)Альтернативные источники энергии. Традиционные источники энергии
-пар, горячие теплоносители, электроэнергия, вырабатываемые при потреблении топливных ресурсов. Перспективными является легко возобновляемые и более дешевые источники как, например, теплота атомных котлов, солнечная энергия и подобное. Их применение специфично, но в ряде случаев может реально привести к уменьшению расхода в производстве более дефицитных топливных ресурсов.
4)Вторичные энергетические ресурсы
Вторичные энергетические ресурсы (ВЭР) - энергетический потенциал продукции, отходов, дополнительных и промежуточных продуктов, образующихся в технологических агрегатах, которые не используются в самом агрегате, но могут быть при умелой организации производства частично или полностью использованы внутри ХТС или для энергоснабжения других предприятий.
Используя ВЭР, само производство не уменьшает теоретический расход энергии (теплоты), но экономия энергии достигается в других энергопотребляющих установках, где потребляются ВЭР.
В зависимости от вида запасенной потоком энергии выделяют следующие виды (группы) ВЭР:
Горючие (топливные) ВЭР - топливные вторичные продукты и отходы, получаемые в технологическом процессе. Они содержат, как правило, Н2, СО
идругие горючие компоненты.
Тепловые ВЭР - тепло отходящих газов, отработанного пара и горячей воды, а также теплота попутно вырабатываемого пара и нагреваемой воды (например, в котлах-утилизаторах и экономайзерах).
ВЭР избыточного давления, или силовые, - газы и жидкости, покидающие технологические агрегаты и обладающие потенциальной энергией (под давлением).
5). Энерго-технологическая система HNO3
Количество энергии, которое необходимо подвести на разных стадиях
химико-технологического процесса, определено его режимом. Затраты на него можно уменьшить путем регенерации энергии между стадиями процесса и использовать потенциал потоков в самом процессе. Но компенсировать полностью затраты энергии не всегда удается. Причин несколько.
Например, имеются затраты на преодоление гидравлического сопротивления потоков в аппаратах и трубопроводах. Далее, в систему подводится высокопотенциальная энергия, но в технологическом процессе образуется много низкопотенциальных потоков, работоспособность которых ниже исходных, несмотря на содержащееся в них такое же, или даже несколько большее общее количество энергии. Часть теплоты (энергии) теряется неизбежно с общими тепловыми потерями. К ним относятся испарение как средство поддержания температурного режима (например, в градирнях и подобных системах), выводы неиспользуемых тепловых потоков, естественные тепловые потери через изоляцию. Т.о. дополнительное потребление энергии неизбежно.
Недостающую энергию можно выработать в технологической системе, потребляя топливо. Для этого необходимо в систему включить энергетический узел как подсистему ХТС.
Химико-технологическая система, включающая энергетический узел, потребляющий топливо и вырабатывающий энергию для компенсации необратимых потерь с целью поддержания технологического режима и обеспечения функционирования ХТС называется энерго-технологической системой.
Классическим примером энерготехнологической системы является ХТС производства азотной кислоты. В современном производстве азотной кислоты под давлением один из сырьевых компонентов - воздух - сжимается в компрессоре и направляется в технологические аппараты. После всех превращений остается практически только азот как отходящий газ под давлением меньшим, чем воздух после компрессора. Потенциал отходящего газа не достаточен, чтобы полностью
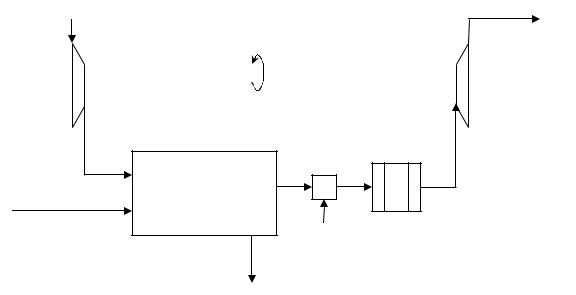
компенсировать затраты на сжатие исходного воздуха, хотя можно его использовать для частичного возмещения затрат. Увеличить энергию отходящего газа как рабочего тела турбины можно увеличением его температуры и массы. Для этого в линию отходящего газа подается топливо - природный газ - и сжигают его с остатками кислорода. Это и есть энергетический узел. Потенциал отходящего горячего газа достаточен для привода компрессора воздуха с помощью газовой турбины. Но функции энергетического узла не только энергетические, но и технологические. Подогрев газа нужен для очистки его от остатков оксидов азота. Используя небольшой избыток метана, создают восстановительную атмосферу в отходящем газе, и на катализаторе в реакторе очистки оксиды азота восстанавливаются до азота. После реактора очистки потенциал горячего газа достаточен для привода компрессора воздуха с помощью газовой турбины. После турбины очищенный газ может быть направлен непосредственно в выхлопную трубу (рис.1).
Воздух |
Отходящие |
||||
|
|
|
|
газы |
|
|
|
|
|
||
|
|
|
К |
ГТ |
|
|
|
|
|
|
|
|
|
|
|
|
|
Р
Г
Аммиак |
ХТП |
|
|
|
СН4
Азотная
кислота
Рис. 1. Энерготехнологическая схема производства азотной кислоты:
К – компрессор, Г – газовая горелка, Р – реактор каталитической очистки, ГТ – газовая турбина
3. Концепция минимизации отходов
Названная концепция направлена на защиту окружающей среды и связана с экологической обстановкой региона, где расположено производство, и с санитарно-гигиеническими условиями для обслуживающего персонала. Основные приемы по реализации этой концепции, в первую очередь, связаны с улучшением использования сырьевых и энергетических ресурсов, а также включает специальные решения экологической безопасности.
1)Полное использование сырьевых и материальных ресурсов.
2)Полное использование энергетических ресурсов. HNO3 H2SO4
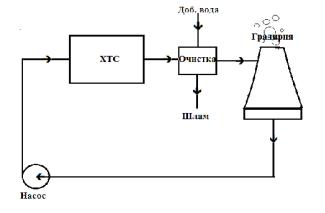
3)Санитарная очистка и обезвреживание выбросов HNO3 H2SO4
предполагает размещение установки (подсистемы ХТС), в которой удаляются вредные (токсичные) примеси из выбрасываемых потоков (санитарная очистка) или они переводятся в нетоксичное состояние (обезвреживание).
4)Уменьшение потребления воды как хладоагента. Пример следующий.
При охлаждении потоков до температуры окружающей среды используют водяные холодильники. Они подвержены коррозии (вода тоже может разрушать аппаратуру из-за наличия растворенных солей и кислорода воздуха), что приводит к возникновению аварийных ситуаций. Кроме того, для охлаждающего агента - воды
-требуется сложная система очистки и отвода тепла от нее - утилизировать теплоту чуть теплой воды нерационально. Замена водяных холодильников на воздушные (охлаждение горячих потоков, протекающих в трубах, идет за счет нагнетания обычного потока воздуха). Это значительно упрощает систему охлаждения и тем самым уменьшает вредные выбросы.
5)Замкнутый водооборот. HNO3 H2SO4. Вода в большом количестве используется как вспомогательный материал в химических производствах. Проходя через технологическую аппаратуру, трубопроводы, она загрязняется и требует дорогостоящей очистки. Используя замкнутый водооборот, исключаются отходы загрязненной воды (рис.2). Загрязненная вода из ХТС поступает в систему очистки, где происходит удаление примесей и солей с образованием шлама. Для восполнения потерь воды добавляют свежую воду. Затем вода направляется в градирню, где происходит удаление из нее растворенных газов. Очищенная и охлажденная вода насосом подается в ХТС.
Рис. 2. Система оборотного водоснабжения
Безотходное и малоотходное производства.
Б е з о т х о д н а я т е х н о л о г и я – способ производства продукции, при котором наиболее рационально и комплексно используется сырье, материалы, энергия и любые воздействия на окружающую среду не нарушают ее нормальное функционирование.
М а л о о т х о д н ы м п р о и з в о д с т в о м считается такое, при котором вредное воздействие на окружающую среду не превышает уровня, допустимого санитарногигиеническими нормами.
Надо иметь в виду, что производство воздействует на окружающую среду не только выбросами, но и своим присутствием.
4. Концепция эффективного использования оборудования
Концепция направлена на минимизацию капитальных затрат на технологическое оборудование путем создания условий протекания в нем процессов с максимально возможной интенсивностью.
1)Внедрение новых технологий, более интенсивных, протекающих с большей скоростью. Типичным примером является переход от замедленных гетерогенных процессов к гомогенным и далее к каталитическим. Так замена термического гомогенного крекинга углеводородов на каталитический позволила увеличить скорость процесса более, чем в 300 раз!
2)Оптимизация процесса H2SO4 - очевидный прием увеличения его
интенсивности (см. оптимизация контактного аппарата для окисления диоксида серы).
3)Организация процесса в аппарате. H2SO4 Почти всегда возможно разными способами провести один и тот же процесс: теплообмен и контакт фаз - в противотоке или прямотоке, гетерогенно-каталитическую реакцию - в неподвижном или кипящем слое катализатора, разделение жидкостей - ректификацией или дистилляцией и так далее. Примеры сокращения затрат рассмотрены выше: теплообменник или массобменный аппарат (абсорбер)- использование противотока. Еще пример. Скорость превращения в процессе "газтвердое" сильно зависит от размера частиц. Однородные условия протекания процесса создает псевдоожиженный слой. В производстве серной кислоты из колчедана переход от обжига крупно кускового сырья в полочных печах к обжигу
впсевдоожиженном слое позволил увеличить интенсивность превращения в единице объема аппарата в 20 раз.
4)Организация технологического процесса в подсистеме ХТС. H2SO4
Здесь использовано свойство ХТС - усовершенствование одного элемента дает выигрыш в эффективности процесса в системе в целом. Некоторые решения общеизвестны. Например, замена периодического процесса на непрерывный. В первом случае требуются дополнительная аппаратура для накопления исходных компонентов и продуктов, очистка периодических аппаратов, временные затраты, связанные с пусками и остановками. В непрерывном процессе таких неудобств нет.
Сокращает расходы на аппараты схема регенерация теплоты реакции, вместо нагрева потока перед реактором и последующее охлаждение его в отдельных теплообменниках (см., например, реакционный узел окисления диоксида серы)
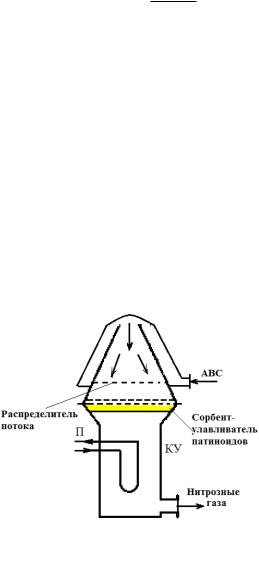
5)Увеличение единичной мощности. Оценим изменение затрат на оборудование
ваппарате при изменении мощности производства. Интенсивность процесса это количество продукта, получаемое в единицу времени и единице объема оборудования. Производительность П (мощность аппарата, установки) пропорциональна его объему V. Объем аппарата V в свою
очередь примерно пропорционален кубу его линейного размера l: П V l3. Затраты на аппарат З, расход материала на его изготовление, примерно пропорциональны квадрату его линейного размера, поверхности корпуса, перегородок: З l2. Из этих соотношений получим: З П2/3, - затраты, естественно, увеличиваются с ростом производительности. Удельные затраты Зуд (на единицу производительности) уменьшаются с увеличением производительности:
Зуд = З/П П-1/3. Можно оценить уменьшение затрат при удвоении мощности: Зуд 2П 0,8
- уменьшаются примерно на 20%. Реальная цифра меньше и составляет 8-13% поскольку с увеличением размера стенки делают толще для обеспечения жесткости конструкции, появляются дополнительные элементы конструкции.
Уменьшение удельных капитальных затрат составляют примерно 11% при удвоении производительности. Но бесконечно наращивать мощность невозможно. Появляются ограничения машиностроительных предприятий, транспортировки крупногабаритного оборудования. Временная остановка крупнотоннажного производства приводит к большим потерям продукции и затратам на восстановление режима. Крупное производство вносит значительное возмущение в экологическое равновесие региона.
Увеличение мощности до разумных пределов рационально для сокращения затрат на оборудование.
6) Совмещение процессов HNO3
Совмещение процессов - осуществление разного типа химико-
технологических процессов в одном аппарате.
Аммиачно-воздушная смесь (АВС) при поступлении в реактор, проходя и контактируя с нагретой конусной частью реактора, нагревается за счет теплового излучения, исходящего от слоя катализатора. Окисление аммиака осуществляется на платиноидном катализаторе, выполненном в виде нескольких сеток, после чего реакционные газы охлаждаются в котле-утилизаторе. Для равномерного распределения потока по сечению тонкого слоя катализатора реактор должен иметь распределительную решетку в конусной части реактора.
Рис.3. Схема реактора окисления аммиака
Кроме того, под слоем катализатора установлен слой из пористого материала, способного улавливать частицы дорогостоящих платиноидов, уносимые реакционным газом с катализатора. Реактор установлен непосредственно на котел утилизатор, т.е. на одной площадке, что уменьшает расходы на аппараты. Итак, в одном аппарате совмещены 5 процессов: окисление аммиака, распределение реакционного потока по сечению реактора, улавливание частиц платиноидов, регенерация тепла реакции и образование энергоносителя – водяного пара (рис.3).
7) Перестраиваемые (гибкие) химико-технологические системы
Перестраиваемая химико-технологическая система позволяют на одном и том же оборудовании после его перенастройки (изменения некоторых связей и режима процессов в аппаратах) реализовать различные химико-технологические процессы и перерабатывать несколько видов сырья, производить различные продукты запрашиваемые рынком.
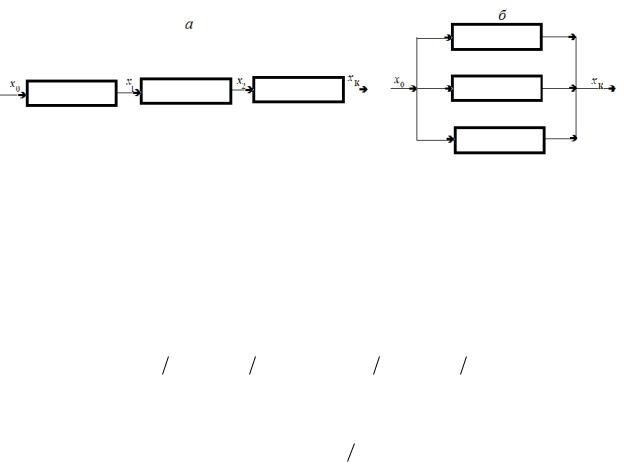
ОПТИМАЛЬНЫЕ СХЕМЫ РЕАКТОРОВ ИВ И ИС
В ХТС можно существуют подсистемы, состоящие из однородных элементов (аппаратов) и предназначенные для проведения определенной химикотехнологической операции. К ним можно, например, отнести реакторный узел, системы разделения, теплообмена. В них протекает химическое превращение, или разделение многокомпонентной смеси, или теплообмен между многими потоками. Каждая из них состоит из однородных аппаратов: реакторов, или ректификационных колонн, или теплообменников. Для выбора системы однородных элементов установлены некоторые общие подходы, позволяющие реализовать концепции синтеза ХТС. Рассмотрим на примере реакторных схем.
5.6.1.Система химических реакторов
Реакторный узел - соединение нескольких реакторов – часто используют для
оптимизации режима процесса, или увеличения общей степени превращения. Рассмотрим параллельное и последовательное соединение реакторов и сопоставим их по интенсивности (общему объему, необходимому для достижения одинаковой степени превращения хк или конечной концентрации Ск) и селективности процесса в них (при протекании сложной реакции).
Системы n реакторов идеального вытеснения (рис. 1).
Математически процесс в реакторе описывается уравнением dx/d = r(x).
В системе последовательно соединенных реакторов их общий объем Vрi
пропорционален сумме времен контакта i |
в |
них: |
Vрi = V0 i. Из описания |
||
процесса в реакторе |
|
|
|
|
|
|
x1 |
x2 |
|
xn |
xn |
i |
dx r x |
dx r x ... |
|
dx r x dx r x |
|
|
xo |
x1 |
|
xn 1 |
xo |
или |
|
|
|
|
|
|
|
Vрi V0 |
xn |
|
|
|
|
dx r x |
(1) |
xo

Из (1) также следует, что Vрi не зависит от того, как распределены объемы реакторов между собой.
В системе параллельно соединенных реакторов полагаем на выходе каждого из них будет одинаковая степень превращения, равная хк. Следовательно, все
xn
i dxr x одинаковые и
xo
xn |
|
Vрi Vi i Vi V0 dx r x |
(2) |
xo
Если в каком-то реакторе уменьшить степень превращения, то в другом ее надо увеличить. Выигрыш в первом из них будет меньше, чем его увеличение во втором: зависимость х( ) - нелинейная затухающая растущая функция (см. рис.2). Поэтому равные i дают максимальную интенсивность.
Как видим из (1) и (2), в обеих схемах реакторов интенсивность процесса в них одинакова (равные Vрi ) и такая же, как в одном реакторе идеального
вытеснения ив. Действительно, рассмотренные схемы реакторов идеального вытеснения сводятся к одному большому РИВ и по интенсивности одинаковые. Соответственно, и по показателю селективности для сложных реакций в этих условиях не будет разницы. Но в параллельной схеме поток распределен между реакторами, его скорость в каждом из аппаратов меньше, чем в их последовательности. Поэтому меньше гидравлическое сопротивление и энергетические затраты в параллельной схеме.
Системы n реакторов идеального смешения (рис. 3).