
теор / Эксплуатация компрессорных станций магистральных газопроводов
.pdf
- для автоматической сигнализации о появлении условий для обледенения в системе защиты агрегата предусмотрен датчик образования льда, контролирующий состояние атмосферного воздуха
по температуре и влажности и сигнализирующий о необходимости включения обогревающего устройства при условиях, благоприятствующих образованию льда на лопатках ВНА осевого компрессора. Датчик образования льда встроен в инжектор, устанавливаемый после пылеулавливающих сеток камеры фильтров ВЗК. К инжектору подводится сжатый воздух из линии нагнетания компрессора, который, расширяясь, подсасывает атмосферный воздух из камеры фильтров. При образовании льда, что сопровождается увеличением перепада давления на сетке датчика, подается сигнал на включение системы обогрева. Перепад давления фиксируется дифманометром, который выдает сигнал через реле.
Агрегаты ГТК-25И имеют аналогичную систему подогрева циклового воздуха, за исключением того,
что смеситель имеет несколько другую конструкцию и расположен перед фильтрующими элементами ВЗК (рис. 3.16).
Рис. 3.16. Система подогрева циклового воздуха (антиобледенительная система) агрегата ГТК-25И
PDF created with pdfFactory Pro trial version www.pdffactory.com
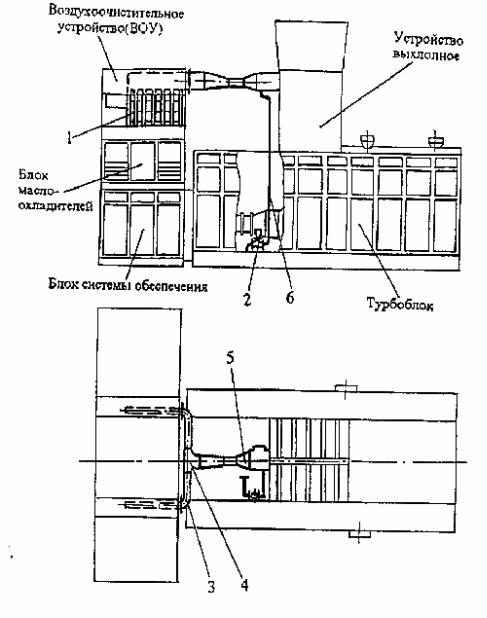
Рис. 3.17. Система подогрева циклового воздуха агрегата ГПА-Ц-6,3:
1 - решетка распределительная; 2 - вентиль с электроприводом; 3 - воздуховод; 5 - эжектор; 6 - трубопровод
Вторая схема с использованием теплоты отработанных выхлопных газов применяется на отечественных агрегатах типов ГПА-Ц-6,3 и ГПА-Ц-16, а также импортных агрегатах типа ГТК-10И.
На рис. 3.17 представлена такая схема подогрева циклового воздуха для агрегата ГПА-Ц-6,3.
Система подогрева циклового воздуха включает в себя две распределительные решетки 1, расположенные с двух сторон ВЗК, к которым при помощи эжектора 5, тройника 4 и воздуховодов 3, подаются выхлопные газы от двигателя НК-12СТ.
Эжектирующий воздух отбирается за осевым компрессором двигателя и по трубопроводу 6
PDF created with pdfFactory Pro trial version www.pdffactory.com
подается в эжектор. В трубопроводе для управления работой системы предусмотрен вентиль с электроприводом 2, включенный в систему автоматического управления агрегатом.
Распределительные решетки аналогичны по конструкции, как и смесители. Распределительные решетки устанавливаются, как и на ГПА ГТК-25И, на входе в воздухоочистительные элементы ВОУ и состоят из прямоугольного короба и короба с отверстиями для выхода газовоздушной смеси.
При температуре наружного воздуха от +3 до -5 °С включается система подогрева циклового воздуха, при этом на пульте управления загорается лампочка "Обогрев ВОУ". При температуре наружного воздуха от +3 до -5 °С необходимо вести постоянное (через 2 часа) наблюдение и осмотр камеры всасывания, защитной решетки и входного устройства двигателя на отсутствие обледенения через окна, предусмотренные конструкцией ГПА.
Схема подогрева воздуха с использованием теплоты от АВО масла, применялась только на первых стационарных агрегатах. При этой схеме АВО масла устанавливались непосредственно под ВЗК.
Оба узла - АВО масла и ВЗК - разделялись горизонтальными жалюзями, которыми регулировались степень подогрева циклового воздуха и степень охлаждения турбинного масла в АВО. Но эта система не нашла применения, так как в летний период через неплотности жалюзей из АВО масла и пространства КВОУ теплый воздух подсасывался в осевой компрессор, что приводило к снижению мощности и КПД ГТУ.
3.10. Противопомпажная защита ЦБН
Помпаж, или неустойчивый режим работы, нагнетателя является наиболее опасным автоколебательным режимом в системе нагнетатель - газопровод, приводящий к срыву потока в проточной части нагнетателя.
Внешне помпаж проявляется в виде хлопков, сильной вибрации нагнетателя, отдельных периодических толчков, в результате чего возможны разрушение рабочего колеса нагнетателя, повреждение упорного подшипника, разрушение лабиринтных уплотнений и т.д. Возникновение помпажа в нагнетателе вызывает колебания частоты вращения и температуры газа РТУ, приводящей во вращение нагнетатель, и, как следствие, к возникновению неустойчивой работы осевого компрессора, что, в свою очередь, приводит к аварийной остановке ГПА.
Причинами возникновения помпажа является изменение характеристики сети (газопровода), вследствие:
-колебаний давления газа в газопроводе;
-влияния параллельно включенных, но более напорных нагнетателей;
-неправильной или несвоевременной перестановки кранов в трубной обвязке нагнетателя.
Изменение режима работы нагнетателя до значительного уменьшения расхода газа (приблизительно до 60% расчетного значения), вследствие:
-снижения частоты вращения нагнетателя ниже допустимой;
-ухудшения технического состояния газотурбинного привода;
-попадания посторонних предметов на защитную решетку нагнетателя и ее обледенение и др.
Режимы работы нагнетателя по расходу газа, как правило, ограничиваются 10%-м запасом от границы помпажа (рис. 3.18) и определяются как:
S = (Q - Qпомп ) / Qпомп ×100% ³10% . |
(3.1) |
PDF created with pdfFactory Pro trial version www.pdffactory.com
Пример 3.2. Определить запас устойчивой работы нагнетателя ГПА-Ц-6,3/56М-1,45, имеющего следующие параметры рабочего режима: давление газа на входе нагнетателя Pвх = 3,9 МПа,
давление газа на выходе нагнетателя Pвых = 5,3 МПа, температура газа на входе t1= 16 °С, частота вращения нагнетателя n0 = 8100 об/мин, производительность нагнетателя Qкомм = 475 тыс.н·м 3 /ч,
плотность газа r0 = 0,676 кг/м 3 .
Решение. Относительная плотность газа по воздуху
r = |
|
r0 |
= 0,56 . |
|
(3.2) |
|
1,205 |
|
|||||
|
|
|
|
|
||
Газовая постоянная |
|
|
|
|
|
|
R= |
29,27 |
= |
29,27 |
= 52,2 кг · м/кг · K 512 Дж/кг · K. |
(3.3) |
|
|
|
r |
|
0,56 |
|
|
Коэффициент сжимаемости газа по параметрам входа определяется по номограмме рис. 1.1, либо по соотношению [2]:
|
|
æ |
0,41 |
|
0,061ö |
|
|
p2 |
|
|
z |
вх |
=1- ç |
|
- |
÷p |
вх |
- 0,04 |
вх |
= 0,93, (3.4) |
|
3 |
3 |
|||||||||
|
ç |
|
÷ |
|
|
|||||
|
|
è |
tвх |
|
tвх ø |
|
|
pвх |
|
где tвх - соотношение температур газа на входе и критической
(tвх = Tвх /Tкр =1,52) ;
πвх - соотношение давлений газа на входе и критического
(pвх = Pвх / Pкр = 0,824) ;
Tкр - критическая температура (Tкр = 190,1 К);
Pкр - критическое давление ( Pкр = 4,73 МПа).
Плотность газа на входе
rвх =104 Pвх / zвх RTвх = 10 4 · 3,9/0,93 · 289,2 · 52,2 = 28,32 кг/м 3 .
Объемная производительность нагнетателя
|
æ |
r |
ö |
|
3 |
|
|
Q = Q |
ç |
|
0 |
÷ |
= 475 · 0,676/0,06/28,32 = 189 м |
/ мин. |
|
|
|
||||||
/ 0,06 |
|
÷ |
|
||||
комм |
ç |
|
|
|
|
||
|
è rвх ø |
|
|
|
Приведенная объемная производительность
PDF created with pdfFactory Pro trial version www.pdffactory.com
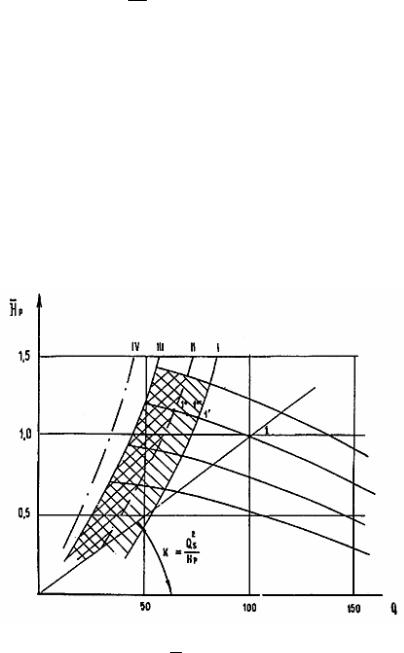
Qпр = Q nn0 = 189 · 8200/8100= 191,3 м 3 /мин.
Запас устойчивой работы нагнетателя
S = (Qпр − Qпр.помп. ) /Qпр.помп. · 100% = (191,3 - 135)/135 · 100% = 41,7%,
где Qпр.помп. = 135 м 3 /мин определяется по характеристике нагнетателя.
Эксплуатационный персонал должен по показаниям штатных приборов периодически контролировать положение рабочей точки на характеристике нагнетателя и не допускать ее приближения к опасной зоне, для чего при работе на частичных режимах необходимо повышать
частоту вращения нагнетателя либо уменьшать напор и расход параллельно работающей группы нагнетателей. При возникновении помпажа необходимо открыть перепускной кран, соединяющий линию нагнетания с всасывающей, при этом расход газа через нагнетатель увеличится, а степень сжатия снизится, рабочая точка нагнетателя переместится вправо от границы помпажа (см. рис. 3.18).
Рис. 3.18. Принципиальная характеристика нагнетателя с линиями ограничения по помпажу; Q - объёмный расход газа; Hp - относительный политропный напор;
1 - нормальный режим работы нагнетателя; 1’ - режим работы нагнетателя после открытия перепускного крана;
1’’ - режим полного открытия перепускного крана;
1’’’ - режим работы нагнетателя с малыми возмущениями. I - линия контроля помпажа;
II - линия ограничения больших возмущений; III - линия границы помпажа; IV - линия ограничения
числа хлопков
В настоящее время существует достаточно много противопомпажных автоматических систем,
позволяющих не допустить попадание нагнетателя в помпаж и сигнализирующих о приближении
PDF created with pdfFactory Pro trial version www.pdffactory.com
рабочей точки к границе помпажа. Наиболее распространенные системы основаны на сопоставлении
величины расхода газа с создаваемым нагнетателем напором с последующим воздействием на перепускной кран. Хорошо известны сигнализаторы помпажа, разработанные НЗЛ, которые укомплектованы пневматическими ППЗ на базе элементов системы "Старт".
Более современные системы включают защиту и регулирование нагнетателя в области помпажных режимов и имеют перепускной кран с регулируемым проходным сечением. К таким системам относится, например, система фирмы ССС ("Компрессор контролс корпорейшн").
Данная система антипомпажной защиты обеспечивает положение рабочей точки нагнетателя в правой зоне от линии границы помпажа (см. рис. 3.18, линия III). Это достигается открытием перепускного (антипомпажного) крана на величину, необходимую для поддержания минимального расхода. Вследствие большой инерционности системы нагнетатель-газопровод воздействие на перепускной клапан должно начаться до того, как рабочая точка достигнет границы помпажа. Точка на характеристике нагнетателя, соответствующая открытию клапана, является линией контроля помпажа (см. рис. 3.18, линия I). Расстояние между линией контроля и линией границы помпажа определяет предел безопасности или зону контроля помпажа (заштрихованная площадь на рис. 3.18). Открытие перепускного клапана увеличивается по мере перехода рабочей точки в зону контроля помпажа. Расстояние между рабочей точкой нагнетателя и границей помпажа рассчитывается с использованием следующего соотношения:
|
|
H p |
|
P · e(m−1) / m -1 |
×m |
|
|
|
||||
|
|
= |
вх |
|
m -1 |
|
, |
|
(3.5) |
|
||
|
|
|
|
|
|
|
|
|||||
|
|
Q2 |
|
|
|
DP |
|
|
|
|||
|
|
s |
|
|
|
|
к |
|
|
|
|
|
где Hр |
- политропный напор; |
Qs |
- коэффициент объемного |
расхода; Pвх - абсолютное |
||||||||
давление |
на входе; |
ε |
- |
|
степень |
сжатия; |
m - |
показатель |
политропы, |
|||
(m -1)/ m = lg(Tвых /Tвх ) / lge ; DPк - перепад давления на конфузоре. |
|
|||||||||||
Отношение значений параметра |
H |
р |
/Q2 =1/ к |
в рабочей точке и на границе помпажа при |
||||||||
|
|
|
|
|
|
s |
|
|
|
|
|
постоянной частоте вращения является соотношением наклонов двух линий, проходящих через рабочую точку и точку на границе помпажа (см. рис. 3.18). Расстояние между границей помпажа и
линией контроля помпажа S рассчитывается как производная от DPк , в результате чего критерий
S будет равен 1,0, когда рабочая точка находится на линии контроля помпажа, и больше 1,0, когда рабочая точка находится в зоне контроля помпажа. Зона контроля помпажа имеет две области регулирования:
-область регулирования между линиями I и II соответствует малым возмущениям потока газа;
-область регулирования между линиями II и III соответствует большим возмущениям потока газа;
Регулятор, рассчитывая расстояние рабочей точки от границы помпажа в случае его работы в области регулирования между линиями I и II (точка 1’’’), воздействует на перепускной регулирующий клапан типа "Моквелд", перепускает часть газа с выхода нагнетателя на вход, восстанавливая режим работы нагнетателя в точке 1’. Если же рабочая точка нагнетателя находится в области регулирования между линиями II и III (точка II), то при быстром приближении к границе помпажа регулирующий клапан полностью открывается, а затем несколько прикрывается по мере удаления рабочей точки от границы помпажа, устанавливая режим работы нагнетателя, соответствующий точке 1’. В случае, если помпаж все-таки произошел, а это значит, что рабочая точка находится между линиями III и IV, регулятор ограничивает число "хлопков" путем удаления линии контроля помпажа от линии границы помпажа.
3.11. Работа компрессорной станции при приеме и запуске очистных
PDF created with pdfFactory Pro trial version www.pdffactory.com
устройств
По окончании строительства и в процессе эксплуатации периодически проводят очистку внутренней полости магистрального газопровода специальными очистными устройствами (ОУ). Необходимость проведения этой операции вызвана тем. что в процессе монтажа образуются участки, предварительная очистка которых невозможна технологически. При работе магистрального газопровода также происходит отложение на его стенках различных органических соединений, приводящих к нарушению расчетного режима движения газа по трубопроводу.
Сложный профиль трассы газопровода, вызванный рельефом местности, образует "карманы", в которых происходит накапливание жидкости, выпадающей из газа. Увеличение расхода по газотранспортной системе ведет к массовым выбросам этой жидкости на входе КС, что может привести к выходу из строя оборудования.
Существует два основных типа очистных устройств, применяющихся в зависимости от того, какую очистку внутренней полости необходимо произвести. Очистное устройство (поршень), предназначенное для очистки полости трубы от сухих загрязнений, состоит из защитного диска, корпуса, устройства для перепуска газа, щетки, уплотнительных манжет и шарнира. Поршень, предназначенный для удаления смеси воды и загрязнений, состоит из защитного диска, корпуса, уплотнительных манжет, воздушной системы уплотнительных манжет. Диаметр поршня выбирается несколько больше диаметра газопровода, длина определяется профилем трассы. Оптимальная скорость движения поршня по газопроводу составляет 5-10 км/ч.
Минимальный перепад давления, необходимый для страгивания с места, составляет 0,05-0,06 МПа.
Работы по запуску и приемке очистного устройства ведутся в строгом соответствии с инструкцией, согласованной с производственно-диспетчерской службой ПДС.
На крановых узлах магистрального газопровода при проведении работ выставляются посты наблюдения, оснащенные связью. Задачей наблюдателей является выделение нитки газопровода, по которой пропускается поршень, путем закрытия перемычек при приближении поршня и включения их в работу после прохождения ОУ (в варианте многониточного газопровода). Также на посты
наблюдения возлагается задача фиксирования времени прохождения ОУ расчетных точек с целью установления отклонения реальной скорости движения поршня от расчетной.
Это необходимо для того, чтобы определить время прибытия ОУ к камере приема. Для выявления места нахождения очистного устройства на линейной части газопровода (крановых узлах), охранных кранах компрессорной станции установлены специальные отслеживающие устройства - сигнализаторы поршня, работающие по принципу либо механического воздействия, либо осуществляющие контроль бесконтактными методами.
После запуска ОУ, по мере приближения поршня к компрессорной станции, периодичность контроля давления на входе КС и крановых площадках сокращается до 20 мин или ведется постоянное наблюдение. Рассмотрим наиболее сложную схему (рис. 3.19) приемки очистного устройства на многониточном газопроводе с работающей компрессорной станцией. Камера приема
поршня предварительно опрессовывается и после вытеснения газовоздушной смеси путем продувки на свечу № 37 заполняется газом под рабочим давлением магистрали от крана № 19, при этом кран остается закрытым.
PDF created with pdfFactory Pro trial version www.pdffactory.com
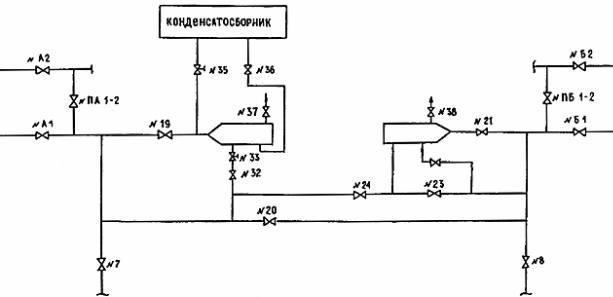
Рис. 3.19. Схема узла запуска и приема поршня на КС
В ходе движения поршня впереди него образуется зона, характеризующаяся повышенным содержанием воды и различных загрязнений. При приближении ОУ к охранному крану А1 перемычка ПА 1-2 закрывается. Сменный персонал компрессорного цеха ведет непрерывный контроль за работой агрегатов, не допуская при этом приближения рабочей точки к зоне помпажа путем включения устройств антипомпажного регулирования. В случае их отсутствия должны быть открыты станционный кран № 6 и его байпасы. Особое внимание следует уделить работе узла подготовки технологического газа: пылеуловителей и фильтр-сепараторов, контролируя перепад давления на них и не допуская превышения больше, чем 0,06 МПа. В противном случае это может привести к разрушению фильтр-патронов.
За 2 ч до расчетного времени прихода поршня в приемную камеру следует произвести продувку пылеуловителей и фильтр-сепараторов, а также удаление собранных механических примесей и жидкости из цеховых систем сбора. Количество одновременно работающих пылеуловителей при
работе КС определяется графиком их производительности в режиме максимальной эффективности очистки. Однако при выходе всей станции для работы на кольцо их может оказаться недостаточно, в
связи с чем на период прохождения поршня необходимо включить в работу количество пылеуловителей, позволяющих обеспечить работу КС в режиме на "кольцо". По температуре газа на выходе КС определяется потребное количество вентиляторов АВО газа, не допуская нагрева газа в выходном коллекторе свыше +45 °С.
Для обеспечения степени сжатия при работе на "кольцо" с целью предохранения от помпажных режимов, может использоваться ручной кран 6Д. Степень его закрытия (в %-м отношении) определяется заранее, исходя из давления в контуре и производительности одновременно работающих агрегатов. При наличии станционной системы помпажного регулирования эти функции выполняются специальными исполнительными механизмами, приводимыми в действие
контроллерами типа " G = f (π) ".
По прохождении поршнем охранного крана А1 компрессорная станция после выполнения указанных выше мероприятий выводится на "кольцо" т.е. открывается станционный кран № 6 и закрываются краны № 7 и 8. Кран № 35 открывают для отвода жидкости и загрязнений в конденсатосборник.
Следующий этап приема поршня в камеру - прохождение тройника, оснащенного решеткой, на входе КС, после него необходимо открыть входной кран № 19 на камере приема и кран № 36 на линии отвода жидкости в конденсатосборник. Под воздействием перепада давлений поршень
PDF created with pdfFactory Pro trial version www.pdffactory.com
заходит в камеру, при этом ведется дренирование жидкости непосредственно из камеры приема. После срабатывания установленного на ней сигнализатора операция считается завершенной. Компрессорная станция включается для работы на магистраль, перемычки открываются, а запорная арматура возвращается в исходное положение.
Процесс запуска поршня из камеры организуется следующим образом. Поршень с помощью автомобильного крана укладывается на специальный лоток-поддон. Посредством грузоподъемных механизмов и приспособлений, являющихся частью оборудования камеры запуска, лоток с поршнем устанавливают в камеру. При этом лоток фиксируют посредством стопорного механизма относительно корпуса камеры. Закрыв затвор камеры, производят ее опрессовку и поднимают давление до рабочего в газопроводе. Выставляются посты на крановых площадках с заданием, аналогичным тому, что выполняют при приеме поршня: контроль давления, времени прохождения ОУ и выделения ниток газопровода при приближении ОУ к крановой площадке. По поступлении от ДУ команды на запуск поршня производят открытие выходного крана № 21 на камере запуска и крана № 23 для расхода газа через камеру. Плавно прикрывая кран № 8 с помощью ручного привода, увеличивают расход газа через камеру. При достижении перепада на поршне, необходимого для страгивания его с лотка, поршень выводят из камеры. После прохождения поршнем тройника на выходе КС кран № 8 плавно открывают, а кран № 23 плавно закрывают. После прохождения охранного крана № Б1 открывают перемычку ПБ 1-2.
3.12. Особенности эксплуатации ГПА при отрицательных температурах
Все показатели для газоперекачивающих агрегатов в соответствии с ТУ на их поставку определены для температуры окружающего воздуха +15°С и барометрического давления 760 мм рт. столба. Параметры атмосферного воздуха оказывают существенное влияние на эксплуатационные характеристики ГПА. На рис. 3.20 показан график зависимости мощности от температуры наружного воздуха. На этом графике наглядно показаны зоны номинальной, выше номинальной и пониженной мощностей ГПА, которые характерны при изменении температуры окружающего воздуха. В
эксплуатации по условиям прочности агрегата нельзя допустить повышение нагрузки ГПА при отрицательных температурах свыше 15% номинальной мощности. Загрузка ГПА обычно определяется по приведенной характеристике нагнетателя.
Работа ГПА при отрицательных температурах предъявляет ряд дополнительных требований к эксплуатационному персоналу по контролю за основным и вспомогательным оборудованием. Так, на агрегатах, находящихся в резерве, необходимо включить подогрев масла, а при пуске их обязательно пользоваться байпасной задвижкой для постепенного прогрева масла, чтобы не допустить повышения давления в трубных досках АВО масла и не вывести их из строя.
PDF created with pdfFactory Pro trial version www.pdffactory.com

Рис. 3.20. Мощность ГТУ АЛ-31СТ в зависимости от температуры окружающей среды:
1 - номинальная мощность; 2 - увеличение мощности при понижении температуры окружающей среды; 3 - понижение мощности при повышении температуры окружающей среды; 4 - максимально
допустимая мощность в зимнее время
При снижении температуры за аппаратами воздушного охлаждения газа в газопроводе могут создаться условия, при которых образуются гидратные пробки. С целью недопущения их
образования необходимо поддерживать температуру газа на всем участке до следующей КС или потребителя выше температуры точки росы, что обеспечивается количеством работающих вентиляторов и отключением секций АВО.
На всасе ЦБН, как указывалось выше, установлена технологическая защитная решетка. При резких понижениях температуры возможно ее обмерзание. Для предотвращения подобных ситуаций
и при наличии роста перепада давлений газа необходимо обеспечить перепуск части газа с выхода нагнетателя на всас.
На выхлопных трубопроводах и выхлопных шахтах устанавливаются утилизаторы теплоты, которые обеспечивают подогрев воды, используемой в системе отопления помещений КС. При
отрицательных температурах наружного воздуха необходимо удостовериться в отсутствии воды в утилизаторах резервных ГПА, следить за состоянием жалюзей во избежание увеличения противодавления выхлопа на работающих ГПА.
Пуск ГПА при отрицательных температурах несколько затруднен из-за повышенной плотности воздуха, т.к. при этом в камере сгорания образуется обедненная смесь. Для обеспечения
нормального пуска ГПА необходимо включить зажигание при меньшем давлении воздуха за осевым компрессором, т.е. при более низких оборотах ТВД. На ряде ГПА на режиме пуска в кольцевых
камерах сгорания наблюдается нестабильность пламени по переходным патрубкам из одной жаровой трубы в другую. В этом случае необходимо очень плавно увеличивать подачу топлива в камеру сгорания. При достижении значительного перекоса температурного поля (свыше допустимого) пуск необходимо прекратить.
Особое внимание эксплуатационный персонал должен обращать на импульсный газ, от качества и своевременной подачи которого зависит успешная перестановка кранов. Сменный персонал обязан знать точку росы импульсного газа при его подготовке. И в случае, если температура окружающего воздуха снизилась ниже этой точки, необходимо проверить наличие газа в коллекторах и работоспособность блока подготовки импульсного газа путем его продувки. При переходе на зимний период работы краны должны эксплуатироваться на зимних смазках и гидрожидкостях.
PDF created with pdfFactory Pro trial version www.pdffactory.com