
Sb95753
.pdfПри скоростях охлаждения до 50 °С/с распавшийся аустенит образует структуру сорбита. Твердость сорбита НB 250 – 350. Структура сорбита встречается в конструкционных сталях после закалки с охлаждением в масле и после закалки и высокого отпуска.
При скоростях охлаждения (80 – 100) °С/с образуется троостит. Твердость троостита НВ 350 – 500. Структуру троостита могут иметь конструкционные стали, закаленные с охлаждением в масле, а также закаленные и отпущенные при температуре (350 – 450) °С.
При скоростях охлаждения (150 – 180) °С/с образуется мартенсит, который характеризуется игольчатым строением, большой хрупкостью и высокой твердостью НВ 500 – 650. Минимальная скорость охлаждения, при которой происходит мартенситное превращение, называется критической скоростью закалки.
Структура стали после термообработки зависит также от температуры нагрева.
При нагреве доэвтектоидной стали до температур выше точки AC3 и
последующим быстрым охлаждением со скоростью, превышающей критическую, структура будет состоять из одного мартенсита. Такая сталь будет обладать высокой твердостью (рис. 5, а).
При нагреве доэвтектоидной стали до температур выше точки AC1 и
последующем охлаждении с той же скоростью в структуре стали наряду с мартенситом будет присутствовать часть феррита и закалка будет неполной. она недопустима (Наличие в закаленной стали феррита будет снижать ее твердость, поэтому такая закалка называется неполной и поэтому рис. 5, б).
Заэвтектоидная сталь, нагретая до температуры выше точки AC1 и
охлажденная с большой скоростью, будет состоять из мартенсита, избыточного цементита (рис. 6, а) и некоторого количества остаточного аустенита (рис. 6, б). Присутствие избыточного цементита в структуре закаленной стали повышает ее твердость и износостойкость, причем важно, чтобы он имел вид зернистого цементита, а не цементитной сетки, которая придает стали хрупкость.
21
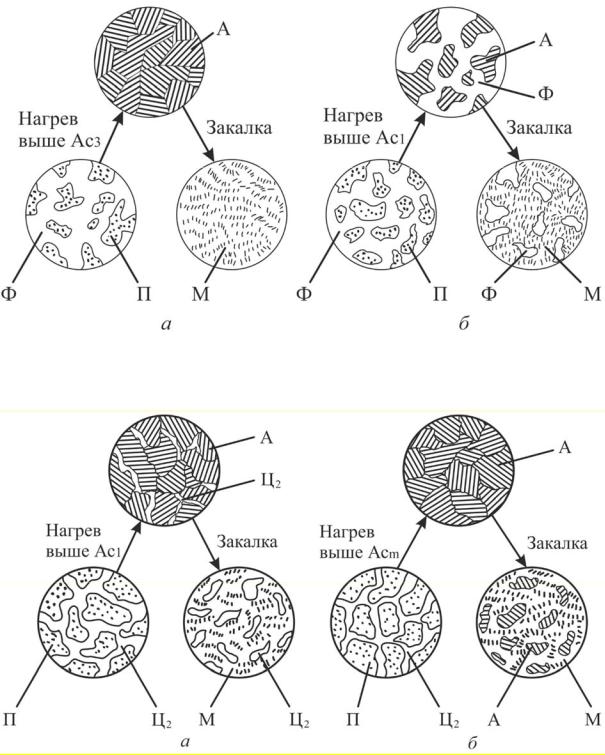
Рис. 5. Кинетика фазовых превращений при закалке доэвтектоидной стали: а – полная закалка; б – неполная закалка
Рис. 6. Кинетика фазовых превращений при закалке заэвтектоидных сталей: а – закалка с остаточным цементитом; б – закалка с остаточным аустенитом
Получающийся при закалке мартенсит имеет игольчатое строение, причем иглы имеют небольшие размеры и поэтому трудно различимы при увеличениях до 600 крат.
22
Троостит и сорбит закалки имеют пластинчатое строение перлита, а троостит и сорбит отпуска – зернистое, округлое.
Троостит закалки и отпуска состоит из измельченных частиц цементита и феррита и поэтому почти не выявляется под микроскопом. Вследствие повышенной травимости троостит при микроанализе выявляется в виде темных образований, и под электронным микроскопом отчетливо рассматривается его пластинчатое строение.
Сорбит закалки и отпуска под оптическим микроскопом выявляется отчетливее, чем троостит, вследствие большой величины частиц цементита и феррита.
Цементацией называется процесс науглероживания поверхностного слоя детали путем, нагрева без доступа воздуха при температуре выше точки AC3 в среде углерода или газов, содержащих углерод.
Цементацию применяют для получения высокой твердости поверхностного слоя при мягкой и вязкой сердцевине, а также для повышения износостойкости и предела усталости стальных деталей, что достигается термической обработкой после цементации.
Поскольку в цементованной детали содержание углерода уменьшается от поверхности к центру, то получаются следующие зоны структурных составляющих: а) заэвтектоидная, содержащая 0,8 – 1,2 % углерода и состоящая из перлита и цементита; б) эвтектоидная, содержащая 0,8 % углерода и состоящая из перлита; в) доэвтектоидная, содержащая менее 0,8 % углерода и состоящая из перлита и феррита. Ближе к середине детали содержание углерода будет снижаться, а следовательно, в структуре стали будет уменьшаться количество перлита и увеличиваться количество феррита.
Цементированная деталь, подвергнутая закалке, будет иметь поверхностный слой из мартенсита и цементита (очень прочный слой), а сердцевина ее будет иметь исходную структуру сырой стали из феррита и перлита.
В результате закалки увеличивается удельной объем стали (до 1%), вследствие чего возникают значительные напряжения. Для уменьшения или снятия напряжений и приведения неустойчивой структуры мартенсита в более устойчивую и получения требуемой твердости закаленную сталь под-
вергают отпуску.
23
Различают три вида отпуска: низкий, средний и высокий.
Низкий отпуск получается при нагреве деталей до 300 °С. При таких температурах в структуре стали остается мартенсит, но с измененной решеткой. Вследствие этого уменьшаются твердость и внутренние напряжения и увеличивается пластичность.
Средний отпуск получается при нагреве от 300 до 500 °С. Структура сталей, отпущенных до этих температур, состоит в основном из троостита отпуска. Изделия приобретают высокую прочность и некоторую пластичность.
Высокий отпуск получается при нагреве изделия от 500 до 700 °С. Структура закаленной стали в этом случав состоит из сорбита отпуска. Сорбит мягче троостита, но тверже перлита. Чем выше температура отпуска, тем меньше твердость стали и тем выше ее пластичность и вязкость (особенно повышается ударная вязкость), поэтому закалку с высоким отпуском называют улучшением стали.
Нормализация углеродистой стали применяется для улучшения микроструктуры и повышения механических свойств, улучшения механической обрабатываемости мягких и вязких сталей.
Технологический процесс нормализации сталей состоит из нагрева стали до температур выше критических точек выдержки при этих температурах и охлаждении на воздухе.
Доэвтектоидные стали следует нагревать при нормализации до температуры на 30 … 50 °С выше точки AC3, а заэвтектоидные – на 30… 50 °С
выше точки AC1.
Структура малоуглеродистой стали после нормализации обычно состоит из перлита и феррита. Структура среднеуглеродистых и низколегированных сталей после нормализации будет сорбитообразной с наличием структурно свободного феррита. Твердость углеродистой стали после нормализации НВ 150 – 300.
24
Порядок выполнения работы
1.Настроить микроскоп на увеличение Х250 – 500.
2.Изучить структуру закаленного поверхностной закалкой образца, последовательно проследив структуры по глубине от поверхности к центру детали.
3.Зарисовать мартенситную структуру полной закалки и неполной. Измерить глубину закаленного слоя по 50 % -му содержанию мартенсита.
4.Изобразить схему структурных превращений при закалке для данного образца.
5.Изучить структуру улучшенной стали (закалка и отпуск).
6.Зарисовать трооститную или сорбитную структуру, обратив внимание на отличие ее от мартенситной структуры. Измерить размер зерна, глубину измененного слоя.
7.Изобразить схему структурных превращений при отпуске.
8.Изучить структуру цементированной стали.
9.Определить глубину заэвтектоидной, эвтектоидной и доэвтэктоидной зон. Сравнить их с исходной структурой.
10.Изобразить схему структурных превращений при цементации.
11.Изучить структуру нормализованной стали. Изобразить схему превращений при нормализации.
12.На всех рисунках указывать увеличение микроскопа, названия изображенных фаз и структурных составляющих.
Содержание отчета
1.Цель работы.
2.Перечень оборудования и образцов.
3.Эскизы микроструктур и схемы превращений для данных структур.
4.Описание проведенных видов термообработки.
5.Выводы.
25
ЛАБОРАТОРНАЯ РАБОТА 6
Микроструктуры чугунов
Цель работы: изучение микроструктуры белых, серых и ковких чугунов. Установление зависимости между структурой и механическими свойствами чугунов.
Структура чугунов. Чугунами называют сплавы железа с углеродом, содержащие углерод выше максимально растворимого в аустените, т. е. более 2 % (рис. 7).
В отличие от стали химический состав чугуна еще не характеризует достаточно надежно его свойства. Структура чугуна и его свойства зависят как от химического состава, так и от технологического процесса производства и режима термической обработки. В зависимости от условий кристаллизации сплаваиформыуглеродаразличаютчугуныбелые, серыеиковкие.
Белый чугун – это сплав, в структуре которого углерод содержится только в связанном состоянии в виде цементита Fe3C. Структура доэвтек-
тического чугуна состоит из перлита, вторичного цементита и ледебурита. В белых чугунах с содержанием углерода около 2 % вторичный цементит выявляется довольно отчетливо, так как в таких чугунах мало ледебурита.
С увеличением содержания углерода увеличивается количество ледебурита и тогда вторичный цементит трудно отличить от цементита ледебурита (они сливаются). Поэтому можно считать, что структура таких доэвтектических чугунов будет состоять из ледебурита и перлита. Структура эвтектического чугуна состоит из одного ледебурита, а структура заэвтектического чугуна – из первичного цементита, выделяющегося в виде крупных пластин и ледебурита.
Белые чугуны отличаются высокой твердостью и хрупкостью вследствие наличия в структуре большого количества цементита (свободного или в составе ледебурита), и поэтому их не применяют для изготовления деталей машин и механизмов.
Серый чугун – это сплав, в котором углерод содержится в виде свободного графита, имеющего форму пластинок различных размеров. Структура серого чугуна более сложна и состоит из металлической основы (со структу-
26
рой феррита, доэвтектоидной и эвтектоидной стали) и включений графита, вкрапленных в эту основу (рис. 7, а).
По структуре металлической основы серые чугуны подразделяют на следующие группы.
1.Перлитные. Структура перлитная с включениями графита. Металлическая основа ее состоит из перлита, а количество связанного углерода равно эвтектоидной концентрации. Такой чугун в отливке обладает наивысшей прочностью и достаточно хорошо обрабатывается резанием.
2.Феррито-перлитные. Структура феррито-перлитная с включениями графита. Металлическая основа ее состоит из феррита и перлита, а количество связанного углерода меньше эвтектоидной концентрации. Этот чугун обладает меньшей механической прочностью, но лучше обрабатывается резанием.
3.Ферритные. Структура ферритная с включением графита. Основа ее состоит из феррита, а содержание связанного углерода практически равно нулю. Такой чугун обладает пониженными механическими свойствами, но легко обрабатывается резанием. Однако такие структуры могут наблюдаться в двухкомпонентной системе железо–углерод при условии очень медленного охлаждения. В состав машиностроительных серых чугунов, кроме углерода, входят Mn, Si, S, Р и другие элементы. Условия получения этих чугунов не соответствуют равновесным. Структура машиностроительных серых чугунов зависит также от температуры чугуна, заливаемого
вформу, от химического состава и скорости охлаждения.
Выделение свободного углерода – графита – ускоряется при наличии в жидком чугуне частиц нерастворившегося графита, при увеличении содержания кремния и уменьшении скорости охлаждения. При увеличении содержания марганца и повышении скорости охлаждения выделение графита замедляется.
Можно качественно оценить влияние графитных включений на механические свойства серого чугуна. Чем меньше графитных включений, чем они мельче и чем больше степень изолированности их друг от друга, тем выше прочность чугуна при одной и той же металлической основе.
Получения структуры серого чугуна с измельченными графитными включениями можно достичь введением в жидкий чугун модификаторов (силикокальция, ферросилиция или магния). Наибольшее влияние на структуру и свойства чугуна оказывает магний. Получаемый при этом вы-
27

сокопрочный чугун характеризуется наличием разобщенных шаровидных, глобулярных включений графита, расположенных обычно на перлитной основе (рис. 7, б).
Структуру серых чугунов сначала определяют на нетравленых шлифах для четкого выявления графитных включений. Хрупкие гранитные включения, залегающие в поверхностном слое металлической основы, при изготовлении шлифа выкрашиваются, и поэтому участки, в которых они находились, будут казаться темными.
Для выявления металлической основы чугун подвергают травлению и затем микрошлиф изучают под микроскопом.
Ковкий чугун получается отжигом отливок из белого доэвтектического чугуна. В результате длительного томления цементит белого чугуна частично или полностью распадается с образованием углерода отжига, находящегося в структуре в виде хлопьев (рис. 7, б). В зависимости от технологии получения нового чугуна различают ферритный, феррито-перлитный и перлитный ковкие чугуны.
При отжиге изделий из белого чугуна в нейтральной атмосфере можно добиться полного разложения цементита, находящегося в белом чугуне, и получить структуру ковкого чугуна, состоящую из феррита и графита, имеющую вид отдельных хлопьевидных включений (рис. 7, в).
Рис. 7. Структуры чугунов: а – включения графита в виде пластинок; б – шаровидные включения графита в высокопрочном чугуне; в – включения графита в виде хлопьев в ковком чугуне
Отжиг деталей можно произвести без разложения цементита перлита или с частичным его разложением, тогда структура металлической основы ковкого чугуна будет состоять из перлита или феррита. При отжиге изделий в окислительной атмосфере с обезуглероживанием поверхностных слоев структура металлической основы ковкого чугуна будет перлитной
28
или феррито-перлитной. При этом структура чугуна будет изменяться от поверхности к сердцевине в сторону увеличения количества перлита и графита.
Порядок выполнения работы
1.Рассмотреть под микроскопом нетравленую поверхность шлифов и зарисовать размеры, форму и характер распределения графитных включений в изучаемых чугунах.
2.Рассмотреть под микроскопом и зарисовать структуру травленых микрошлифов белого, серого и ковкого чугунов, указать стрелками различные фазы и структурные составляющие, написать их наименования, указать увеличение изображения.
3.Дать характеристику основной металлической структуры образцов из серого чугуна и указать структурный класс, данные занести в табл. 6.
|
|
|
|
|
|
Таблица 6 |
|
|
Характеристика включений графита |
|
|
||
|
|
|
|
|
|
|
Но- |
Твер- |
Микро- |
Основная ме- |
Характеристика |
|
Марка |
дость |
таллическая со- |
включений |
Класс |
чугу- |
||
мер |
HВ |
структура |
ставляющая |
графита |
|
на |
|
|
|
|
|
|
|
|
|
|
|
|
|
|
4. Характеристики исследованных образцов указать в таблице 6. В соответствии с ГОСТ 1412-54 и механическими свойствами, указанными на образцах, определить марку серого чугуна.
Содержание отчета
1.Цель работы и задание.
2.Перечисление использованного оборудования и материалов.
3.Зарисовка и описание микроструктур чугунов.
4.Протокол исследований.
5.Выводы о влиянии структуры чугуна на механические свойства.
29
ЛАБОРАТОРНАЯ РАБОТА 7
Поверхностная закалка железоуглеродистых сталей
Цель работы: получение закаленных образцов.
Поверхностная индукционная закалка сталей. Под закалкой стали понимается термическая операция, заключающаяся в нагреве стали выше критических температур (AC1 и AC3) с последующим быстрым охлажде-
нием. Для доэвтектоидных сталей температура закалки равна AC3 + (30 –
50)°С, а для заэвтектоидных сталей она равна AC1 + (30 – 50) °С.
Взависимости от скорости охлаждения может быть закалка на мартенсит или закалка на феррито-цементитную смесь (перлит, сорбит, троостит). Мартенсит образуется при больших скоростях охлаждения (выше vкр). При скоростях охлаждения менее vкр образуются перлит, сорбит,
троостит.
Мартенсит обладает наибольшей твердостью (НВ > 400), но в то же время очень хрупок. Троостит имеет меньшие твердость и предел прочности, чем мартенсит, но обладает достаточной ударной вязкостью.
Сорбит обладает меньшими твердостью и пределом прочности, чем троостит, зато он имеет более высокую вязкость. Поэтому стали, имеющие сорбитную структуру, используются для изготовления ответственных деталей, работающих при ударных нагрузках: коленчатых валов, шатунов и т. д.
Правильное проведение закалки стали сводится к выбору: а) соответствующей температуры нагрева стали, б) времени нагрева, в) скорости охлаждения.
Для проведения работы берем две стали с содержанием углерода 0,5 и 0,3 %.
Для ряда деталей (коленчатые валы, распределительные валы, шестерни и т. д.) требуется высокая твердость на поверхности и большая вязкость ее сердцевины. Эта задача технологически может быть решена не только термохимической обработкой (цементация, азотизация), но и поверхностной закалкой.
30