
Sb95753
.pdf
ном и горизонтальном направлениях. Определяют эти размеры умножением числа делений окуляра в том или ином направлении на цену деления окуляр-микрометра:
lверт nвертD , lгор nгорD ,
lср lверт lгор 2 ,
где п – число делений, D – цена деления, мм.
Принимая средний размер зерна за его диаметр, определяют площадь зерна как площадь круга, мкм2:
S lср2 . 4
Далее по таблице 2 определяют номер зерна.
|
|
|
|
|
|
|
Таблица 2 |
|
|
|
Номер зерна |
|
|
|
|
|
|
|
|
|
|
|
|
Номер |
S, мкм2 |
Номер |
S, мкм2 |
Номер |
S, мкм2 |
Номер |
S, мкм2 |
зерна |
|
зерна |
|
зерна |
|
зерна |
|
–1 |
256000 |
2 |
32000 |
5 |
4000 |
8 |
500 |
0 |
128000 |
3 |
16000 |
6 |
2000 |
9 |
250 |
1 |
64000 |
4 |
8000 |
7 |
1000 |
10 |
12 |
Порядок выполнения работы
1.Отрегулировать освещение микроскопа, используя диафрагму и фильтры.
2.Получить у преподавателя шлифы для исследования и описания.
3.Установить на предметный столик микрошлиф и произвести наводку Фокуса путем подъема (опускания) предметного столика или тубуса с объективом. Предварительное наведение на фокус осуществляют микрометрическим винтом, а точное – при помощи микрометрического винта. Чем больше увеличение объектива, тем меньше должно быть расстояние между шлифом и объективом, так как фокусное расстояние объектива меньше.
11
4.Просмотреть микроструктуру шлифа в различных участках перемещением предметного столика винтами в двух взаимно перпендикулярных направлениях. Выбрать наиболее четкий и характерный участок.
5.Зарисовать видимые-под микроскопом микроструктуры, указать стрелками фазы и структурные составляющие.
6.Определить в исследуемых сталях примерное содержание углерода, используя метод площадей.
7.По содержанию углерода определить марку и механические свойства исследуемой стали, пользуясь справочными данными. Составить таблицу шлифов.
8.Определить номер зерна перлита в шлифах и занести его характеристики в табл. 3.
|
|
|
|
|
|
|
|
|
Таблица 3 |
|
|
|
|
Номер зерна перлита |
|
|
|
||||
|
|
|
|
|
|
|
|
|
|
|
Номер |
Углерод, |
Марка |
σв |
δ, |
ψ, |
Твердость |
aн, |
aт, |
Номер |
|
% |
стали |
кг/мм |
% |
% |
HВ |
кг·мм/мм2 |
кг/мм2 |
зерна |
||
|
||||||||||
|
|
|
|
|
|
|
|
|
|
9.Начертить фрагмент диаграммы железо – углерод в части, относящейся к сталям. Указать на ней исследуемые стали, проведя вертикальные линии, охарактеризовать структурные составляющие исследуемых сталей.
10.Сделать выводы. В выводах на основании анализа микроструктуры объяснить различие в механических свойствах.
Содержание отчета
1.Цель работы.
2.Зарисовки и описание микроструктур.
3.Определение содержания углерода в исследуемых сталях.
4.Таблица с характеристиками шлифов.
5.Расчет средней площади зерна и определение номера зерна.
6.Чертеж части диаграммы железо – углерод.
7.Выводы.
12
ЛАБОРАТОРНАЯ РАБОТА 3
Измерение твердости металлов по методу Роквелла
Цель работы: изучение метода измерения твердости вдавливанием алмазного конуса (метод Роквелла).
Способы измерения твердости. Твердость – свойство металла сопротивляться проникновению в него более твердого тела определенных формы и размера, не получающего остаточной деформации.
Определение твердости является распространенным методом испытания металлов, позволяющим без разрушения изделия и изготовления специальных образцов судить о качестве изделия. Приборы для испытания на твердость просты, обладают высокой производительностью и не требуют высокой квалификации. При испытании на твердость определяют сопротивление металлов деформации при вдавливании наконечника. Эта характеристика связана с пределом прочности, поэтому в некоторых случаях производят испытания только на твердость и по ней судят о пределе прочности материала.
Наиболее широко применяют следующие способы измерения твердо-
сти:
1)вдавливание стального шарика (метод Бринеля);
2)вдавливание алмазного конуса или стального шарика (метод Роквелла);
3)вдавливание четырехгранной алмазной пирамиды (метод Виккерса).
Измерение твердости вдавливанием алмазного конуса (метод Ро-
квелла). Твердость по методу Роквелла определяют по глубине вдавливания в испытываемую поверхность стального шарика диаметром 1,588 мм при нагрузке 100 кг или алмазного конуса с углом при вершине a = 120° и нагрузке 60 или 150 кг.
Твердость измеряют на приборе типа ТК (рис. 3, а), в нижней части неподвижной станины которого установлен столик 4. В верхней части станины укреплены индикатор 7, масляный амортизатор 9 и шток 2, куда устанавливают наконечник с алмазным конусом или стальным шариком. Индикатор представляет собой циферблат, где нанесена шкала и имеются две стрелки – большая (указатель твердости) и маленькая для контроля
13
предварительного нагружения, сообщаемого вращением маховика 6 на ходовом винте 5.
Образец 3 для измерений должен иметь зашлифованную плоскую поверхность, в которую вдавливается конус или шарик. Поворотом маховика по часовой стрелке столик поднимают таким образом, чтобы наконечник мог вдавливаться в поверхность образца; при дальнейшем подъеме столика начинают вращаться стрелки на циферблате. Подъем столика продолжают до тех пор, пока малая стрелка не примет вертикальное положение, указанное на циферблате красной точкой. Это означает, что наконечник проник в образец под действием нагрузки 10 кг. Предварительное нагружение проводят для того, чтобы исключить влияние упругой деформации и шероховатости поверхности образца на результаты измерений, а также выбрать люфт в узлах механизма. Если после предварительной нагрузки положение большой стрелки не совпадает точно с цифрой 0, то, не меняя предварительного нагружения, поворачивают регулировочное колесо, расположенное на маховике таким образом, чтобы цифра 0 на черной шкале совпала с большой стрелкой. Затем рукояткой опорного механизма к рычагам 7, 8 прикладывают груз P1 (10) и тем самым сообщают образцу 3 основную нагрузку. Время приложения нагрузки 2 – 3 с. При этом большая стрелка прибора перемещается по циферблату сначала против часовой стрелки, а затем – по часовой стрелке. Цифра, которую укажет на шкале циферблата большая стрелка, представляет число твердости по Роквеллу. Эту цифру записывают и, поворачивая маховик против часовой стрелки, опускают столик прибора с образцом, снимая предварительную нагрузку.
Прибор измеряет разность между глубиной вдавливания наконечника под действием основной нагрузки и вдавливания под действием предварительной нагрузки. Каждое деление индикатора соответствует глубине вдавливания 2 мкм.
Число твердости по Роквеллу определяют по формуле
HR k h h0 C ,
где k – постоянное значение для шарика k = 0,26, для алмазного конуса k = 0,2; h – глубина внедрения наконечника под действием общей нагрузки (рис. 3, б); h0 – глубина внедрения наконечника под действием предвари-
тельной нагрузки (рис.3, б); С – цена деления циферблата шкалы.
14
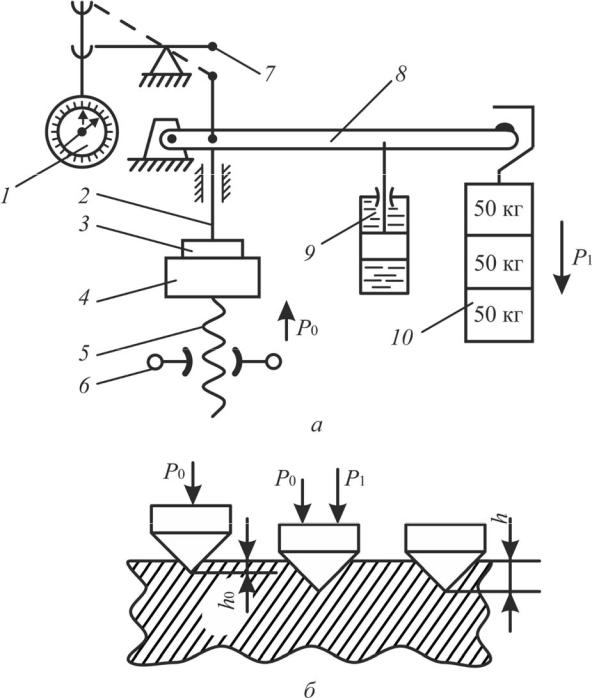
Рис. 3. Измерение твердости по методу Роквелла
Поскольку в числителе стоит разность между постоянными значениями k и h, то чем тверже измеряемый материал, тем меньше h – h0 и тем выше значение HR.
Расстояние от центра отпечатка до края образца или до центра другого отпечатка должно быть не менее 1,5 мм. Толщина образца должна быть не менее 10 глубин отпечатка.
15
К достоинствам метода Роквелла следует отнести высокую производительность, простоту обслуживания, точность измерения и сохранения качественной поверхности после испытания.
Порядок измерения твердости по методу Роквелла. При измерении необходимо:
1.Установить испытываемый образец на столик прибора.
2.Вращением маховика подвести испытываемую поверхность до соприкосновения с наконечником, а затем дальнейшим вращением маховика произвести предварительное нагружение до тех пор, пока малая стрелка индикатора не совпадет с красной точкой на шкале. Если малая стрелка индикатора перейдет за красную точку, то необходимо выбрать на испытываемой поверхности другую точку и испытание начать сначала. Затем повернуть регулировочное колесо индикатора до совпадения нуля черной шкалы с большой стрелкой.
3.Нажать на педаль грузового рычага.
4.Отсчитать по шкале индикатора число твердости, указанное большой стрелкой.
5.Опустить столик вращением маховика против часовой стрелки, снять образец.
6.Результаты измерений внести в табл. 4.
|
|
|
|
|
|
|
|
|
Таблица 4 |
|
|
Результаты измерений |
|
|
|||||
|
|
|
|
|
|
|
|
|
|
Но- |
Наименование |
Нагрузка Р, |
|
|
Измерение |
|
Твердость по |
||
мер |
материала |
кг |
|
|
Твердости |
|
Бринелю НВ |
||
|
|
|
1 |
2 |
|
3 |
|
Среднее |
|
|
|
|
|
|
|
|
|
значение |
|
|
|
|
|
|
|
|
|
|
|
Содержание отчета
1.Цель работы.
2.Схема прибора.
3.Таблицы измерений.
4.Эскизы испытуемых образцов с указанием зон термической обработки и точек измерения твердости.
5.Графики изменения твердости закаленного образца по глубине.
6.Выводы.
16
ЛАБОРАТОРНАЯ РАБОТА 4
Измерение твердости металлов по методу Виккерса
Цель работы: определение твердости сталей вдавливанием алмазной пирамиды (метод Виккерса).
Твердость по методу Виккерса определяют при вдавливании в испытываемую поверхность алмазной четырехгранной пирамиды. Число твердости
по Виккерсу HV представляет собой нагрузку, приходящуюся на единицу поверхности отпечатка, кг/мм, и определяется по формуле
HV |
2P |
sin a |
1,8544 |
P |
, |
(1) |
|
d 2 |
d 2 |
||||||
|
2 |
|
|
|
где Р – нагрузка на пирамиду, кг; d – среднее арифметическое обеих диагоналей отпечатка после снятия нагрузки, мм; а – угол при вершине пирамиды равный 136°.
Испытания проводят на приборе типа ТП (рис. 4, а), имеющем неподвижную станину, в нижней части которой установлен столик 11, перемещающийся по вертикали вращением маховика 12 на ходовом винте 7. Образец 6 устанавливают на столике 11, который поднимают до соприкосновения с торцом защитного чехла 5, предохраняющего тело внедрения – алмазную пирамидку 9 – от ударов. Нажатием педали пускового механизма грузовые гири 10 прикладывают на конец рычага 1, который передает усилие на шток 2 и далее на пирамидку и образец. Для того чтобы усилие передавалось плавно, движение рычага затормаживает амортизатор 8. После приложения нагрузки и короткой выдержки возвратный механизм снимает давление с образца 6 и поднимает рычаг 7 в исходное положение. Столик опускают вниз и поворачивают оптическую головку прибора с микроскопом 4 и осветительной лампой 3 для измерения отпечатка.
Отпечаток пирамиды под микроскопом представляет собой темный ромб (рис. 4, б) на светлом фоне. С помощью микроскопа определяют длину диагонали полученного отпечатка. Отпечаток измеряют при помощи шкалы и двух штрихов, перемещаемых вращением винтов в головке микроскопа. Необходимо измерять обе диагонали и принимать среднее значение измерений. В этом приборе используются нагрузки 49, 98, 196, 294, 490, 981 и 1177 H. Чем больше выбираемая нагрузка, тем глубже проника-
17

ет алмазная пирамида в испытываемый материал. Поэтому для измерения твердости тонких слоев применяют меньшие нагрузки. Значения величин Р и d подставляют в формулу (1). При обозначении твердости по Виккерсу следует указывать применяющуюся нагрузку (HV5, HV50).
Рис. 4. Измерение твердости по методу Виккерса
Твердости по Виккерсу и Бринелю имеют одинаковую размерность и для материалов до HV 450 практически совпадают. Вместе с тем, измерения пирамидой дают более точные значения для металлов с высокой твердостью, чем измерения шариком или конусом. Алмазная пирамида имеет большой угол при вершине и диагональ отпечатка в семь раз больше глубины отпечатка, что повышает точность измерения отпечатка даже при проникновении пирамиды на небольшую глубину.
18
Порядок измерения твердости по методу Виккерса. При данном измерении необходимо:
1.Установить рабочую нагрузку в зависимости ох типа испытываемого образца. Для толстых образцов рекомендуется применять большую нагрузку, так как при этом отпечаток получится больше и погрешность прибора будет меньшей. Однако не следует применять нагрузку больше 50 кг при испытании термически обработанных деталей в целях избежания поломки алмаза.
2.Включить в сеть переменного тока осветительную систему прибора
ипроверить установку микроскопа. Убедиться в том, что поле зрения освещено.
3.Включить механизм грузового привода с помощью рукоятки ввода
иустановить испытываемый образец на столик.
4.Установленный микрошлиф просмотреть через микроскоп и выбрать на нем участок, в котором необходимо измерить твердость.
5.Отвести микроскоп в крайнее левое положение. Поднять опорный столик при помощи маховичка до соприкосновения испытываемого образца с торцом чехла алмазного наконечника.
6.Нажать на педаль пускового рычага, в результате чего автоматически осуществляется испытание и получается отпечаток образца. В момент приложения полной нагрузки сигнальная лампочка загорается, а после окончания выдержки гаснет, и испытание считается законченным.
7.Опустить стол вниз и повернуть оптическую головку в крайнее правое положение до совмещения объектива микроскопа с отпечатком.
8.Осуществитьгрубуюнаводкуфокусаподнятиемилиопусканиемстола.
9.Измерить диагональ отпечатка при помощи микрометрического винта, шкалы и двух штрихов (рис. 4, б). Длину диагонали определяют по шкале, находящейся на объективе (десятые доли миллиметра) и по шкале микрометрического винта, связанного с правым штрихом (сотые и тысячные доли миллиметра).
10.Повернуть образец на 90° (с помощью предметного столика) и измерить вторую диагональ отпечатка.
11.Вычислить среднее арифметическое длины обеих диагоналей от-
печатка.
12.Вычислить или определить по таблице твердость.
13.Результаты измерений и вычислений записать в табл. 5.
19
|
|
|
|
|
Таблица 5 |
|
Результаты измерений и вычислений |
|
|||
|
|
|
|
|
|
Но- |
Наименование |
Нагрузка Р, |
Длина диа- |
Твердость по |
Твердость по |
мер |
материала |
кг |
гонали, мм |
Виккерсу HV |
Бринелю НВ |
|
|
|
|
|
|
|
|
|
|
|
|
14.Измерить твердость вдоль какого-либо направления на поверхности детали не менее чем в 5 точках, обратив особое внимание на переходную зону.
15.Перевести числа твердости по Виккерсу в числа твердости по Бринелю), пользуясь таблицами.
Содержание отчета
1.Цель работы.
2.Таблицы измерений, эскиз схемы твердомера.
3.Эскизы испытуемых образцов с указанием зон термической обработки и точек измерения твердости.
4.Графики изменения твердости закаленного образца по глубине.
5.Выводы.
ЛАБОРАТОРНАЯ РАБОТА 5
Микроструктуры термически обработанной стали
Цель работы: изучение структуры термически обработанной углеродистой стали. Установление зависимости между режимом термической обработки, структурой и механическими свойствами стали.
Способы термической обработки углеродистой стали. Все пре-
вращения в сплавах, происходящие по диаграмме состояния железо – углерод, протекают при медленном охлаждении; они успевают полностью завершиться при температурах, указанных на диаграмме, вследствие чего получаются равновесные структуры. Неравновесное состояние стали образуется при ускоренном охлаждении. Скорость охлаждения является определяющей при образовании структуры термообработанной стали.
Аустинит при быстром непрерывном охлаждении распадается с образованием следующих структур: сорбита, троостита и мартенсита.
20