
- •ВВЕДЕНИЕ
- •1.2. Структура асфальтобетонной смеси
- •1.3. Свойства асфальтобетонных смесей
- •1.4. Хранение смесей в накопительном бункере
- •1.5. Транспортирование асфальтобетонных смесей
- •1.6. Загрузка смеси в кузов
- •1.7. Причины температурной сегрегации
- •1.8. Защита смеси от погодных воздействий
- •Контрольные вопросы
- •2.1. Статическое уплотнение
- •2.2. Трамбование
- •2.3. Виброуплотнение
- •Контрольные вопросы
- •3.1. Методы описания уплотнения асфальтобетонных смесей
- •Контрольные вопросы
- •4.1. Исследование изменения модуля деформаций
- •Контрольные вопросы
- •5. УКЛАДКА АСФАЛЬТОБЕТОННЫХ СМЕСЕЙ
- •5.1. Классификация асфальтоукладчиков
- •5.2.1. Технологическая схема асфальтоукладчика
- •5.2.2. Толкающие ролики
- •5.2.3. Бункер
- •5.2.4. Питатель
- •5.2.5. Распределитель асфальтобетонной смеси
- •5.2.6. Рабочие органы
- •5.2.7. Система подогрева
- •5.3. Основные параметры трамбующего бруса
- •5.4. Основные параметры вибрационных плит
- •5.6.1. Скорость укладки
- •5.6.3. Одновременная укладка двух слоёв
- •Контрольные вопросы
- •6. МАШИНЫ ДЛЯ УПЛОТНЕНИЯ
- •6.1. Общая классификация дорожных катков
- •6.2.2. Основные параметры катков статического действия
- •6.3.1. Классификация вибрационных катков
- •6.6. Классификация вибровозбудителей
- •6.7. Расчет вибровозбудителей
- •6.8. Расчёт на прочность основных узлов дорожного катка
- •6.8.1. Расчёт элементов рулевого управления
- •6.9. Тяговый расчёт
- •6.10. Выбор двигателя
- •6.11. Автоматизация дорожных катков
- •Контрольные вопросы
- •ЗАКЛЮЧЕНИЕ
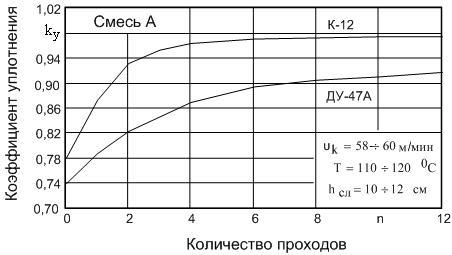
Рис. 2.1. График изменения коэффициента уплотнения в процессе укатки
Повышение плотности вызывает увеличение прочности материала и рост всех составляющих общего сопротивления уплотнения. Требуемая плотность достигается многократным приложением нагрузки, с этой целью применяются многопроходные схемы укатки. На рис. 2.1 приведены графики изменения kу, полученные при уплотнении различными катками [39].
Динамические методы воздействия осуществляются трамбованием и вибрированием смесей.
2.2. Трамбование
Трамбование производится свободным падением плиты массой m с высоты h на поверхность уплотняемого покрытия [6, 44]. В результате удара частицы смеси сдвигаются, накапливая остаточные деформации, либо в случае применения трамбующего бруса на асфальтоукладчиках производится колебание рабочего органа с заданной амплитудой и частотой.
На протяжении десятков лет использования асфальтоукладчика его рабочий орган в части уплотняющей способности постоянно видоизменялся и совершенствовался. Первые образцы трамбующего бруса имели вид скошенной планки или заостренного ножа с размером ударной части 6 – 7 мм по ходу укладчика (рис. 2.2). При вертикальном ходе 2 – 3 мм, частоте ударов в пределах 1000 – 1500 мин-1 и скорости укладки примерно 3 м/мин такой трамбующий брус после каждого своего удара смещался вперед вместе с укладчиком на 2 мм,
29
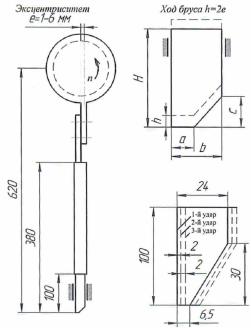
т.е. по одной и той же точке смеси он наносил не более 2 – 3 ударов [26]. С увеличением скорости передвижения асфальтоукладчика количество ударов по месту становилось еще меньше, а этого, как показал практический опыт и исследования, недостаточно для эффективного уплотнения смеси. Поэтому старые модели укладчиков с подобным трамбующим брусом и со статической выглаживающей плитой (вибрационная несколько повышает плотность смеси) не обеспечивали коэффициент уплотнения выше 0,83–0,85.
Увеличение ширины трамбующего бруса до 22–28 мм и повышение частоты ударов до 1700 – 1800 мин-1 увеличили количество ударов по одному месту до 10 – 12 на скорости укладки 3 м/мин и до 6 – 8 на скорости 5 м/мин. Однако прироста плотности не произошло, потому что возросла площадь контакта бруса со смесью и понизилось его статическое контактное давление, а вместе с ним упало контактное давление удара. Нужно было или существенно (до 3 раз) утяжелять брус, или возвращаться к меньшим размерам подошвы его ударной части. Было выбрано второе
Рис. 2.2. Схема трамбующего решение, и размер а (см. рис. 2.2) бруса
составил около 12 – 15 мм. Затем был увеличен ход трамбующего бруса до 3 – 4 мм (для тонких слоев смеси) и до 6–8 мм, а в некоторых случаях до 9 – 12 мм (толстые слои).
Дальнейшее совершенствование трамбующего бруса укладчика привело к различным сочетаниям работы двух и более брусьев, новым формам подошвы бруса и режимам работы.
2.3. Виброуплотнение
Рабочий орган виброуплотнителя вводит массив материала в колебания с частотой . Частицы, различающиеся по массе, форме и размерам, получают разные ускорения и смещаются относительно друг друга [6, 46, 16]. Для создания колебаний на рабочем органе уплотняющей машины (валец катка или вибрационная плита) устанавливается вибровозбудитель колебаний.
30

По своей принципиальной схеме устройства вибрационные плиты могут быть одномассными (рис. 2.3, а) и двухмассными (рис. 2.3, б). В первом случае в колебательных движениях участвует вся масса плиты, во втором вводится в
колебательные движения только ее нижняя часть, а верхняя (подрессоренная) часть не колеблется, воздействуя, однако, на грунты и повышая тем самым общее статическое давление. В верхней части плиты обычно располагается двигатель, который здесь работает в спокойных условиях. При одинаковых контактных поверхностях и весах одномассной и двухмассной вибрационных плит эффект уплотнения грунта приблизительно одинаков. Вместе с тем затрачиваемая на уплотнение
механическая работа меньше в случае двухмассной машины, что объясняется снижением инерционных потерь. Исследования В. Н. Владимирова показали, что меньшие затраты механической работы и устойчивая работа машины обеспечиваются в том случае, когда подрессоривается 0 – 50 % общей массы машины.
Как одномассные, так и двухмассные вибрационные машины, как правило, относятся к вибротрамбующим. Благодаря значительной возмущающей силе, они работают с отрывом от поверхности уплотняемого материала. Амплитуда их колебаний зависит не только от параметров вибратора, но и от свойств смеси и при благоприятных условиях может достигать нескольких миллиметров. По такому принципу работает подавляющее большинство вибрационных машин.
Вибрационные катки являются более производительными и менее металлоёмкими. Недостатком катков вибрационного типа является невысокая надёжность и не всегда удовлетворительные экономические показатели. Кроме того, при ведущем вибрационном вальце значительно снижаются коэффициенты трения и сцепления его с поверхностью уплотняемого слоя, что снижает силу тяги по сцеплению. Если вибровальцом является ведомый валец, то в этом случае затрудняется управляемость катком. Другим недостатком виброкатков является повышенное волнообразование при уплотнении
31
покрытия с низкой начальной плотностью, в связи с чем рекомендуется первые проходы делать в статическом режиме [25, 26, 32].
Сущность виброуплотнения заключается в том, что колеблющаяся с большой частотой масса сообщает кинетическую энергию частицам материала, расположенным в зоне действия вибратора, и приводит их в колебательное состояние. Разные по крупности и массе частицы получают различные ускорения, взаимно перемещаются, поры между крупными частицами наполняются более мелкими, при этом достигается увеличение плотности материала.
Относительные перемещения частиц наступают тем скорее, чем больше различие в массах отдельных частиц, составляющих грунт, и чем слабее будут силы связей между ними. Поэтому успешно уплотняются вибрированием несвязные и слабосвязные материалы. Связный грунт, между частицами которого действуют значительные силы связей, практически может быть уплотнен вибрированием, лишь когда одновременно он подвергается действию нагрузки, которая обычно носит ударный характер.
Колебательные движения характеризуются амплитудами и частотами, а также производными этих параметров – скоростями и ускорениями. Согласно теории П. А. Ребиндера, каждому размеру частиц коллоидных систем соответствует определенная частота колебаний, при которой достигается наибольший эффект уплотнения. При этом отмечается, что чем меньше частицы, тем выше эти частоты.
Асфальтобетонные смеси имеют структуру коагуляционного типа, которую можно рассматривать как двухфазную систему, состоящую из твёрдой минеральной части, и условно однородной – асфальтовяжущего. Поэтому, как и для всякой коллоидной смеси, этому материалу присущи свойства тиксотропии. При колебании смеси с определённой частотой и амплитудой происходит обратимое разрушение вязких связей, что сопровождается уменьшением сопротивления сдвигу частиц и сопротивления уплотнению в целом.
Эффективным является применение пневмошинных катков. При одной и той же скорости движения катков с гладкими металлическими вальцами и катков на пневматических шинах уплотняемый материал находится в напряжённом состоянии более продолжительное время, что обеспечивает бо льшую эффективность уплотнения. Кроме того, они обладают свойством регулирования контактного давления на уплотняемый материал [25]. Для этого на них устанавливается централизованная система подкачки шин, которая обеспечивает в них различное давление воздуха. Однако завершать уплотнение требуется
32
гладковальцовым катком, чтобы устранить неровности, возникшие после прохода шин.
Для упруговязкопластических материалов, к которым можно отнести большинство дорожно-строительных материалов и смесей, важным фактором при их уплотнении является длительность приложения нагрузки. При кратковременном приложении нагрузки большая часть деформации восстанавливается, тогда как при увеличении длительности при той же нагрузке достигается более значительная остаточная деформация уплотняемого слоя материала. Этих недостатков в значительной мере лишены пневмошинные катки. При проходе по уплотняемой поверхности вследствие деформации колеса на площадке его контакта с уплотняемым материалом возникает напряженное состояние, продолжительность которого измеряется десятыми долями секунды. За такое время нагрузка успевает распространиться в глубину уплотняемого слоя и вызвать в нем необходимые деформации [39, 44].
Силовые воздействия уплотняющих машин приводят к изменению плотности. Вместе с этим возрастает сопротивление деформированию и по мере укатки рост деформации завершается. С целью достижения проектной плотности в процессе уплотнения необходимо постоянно увеличивать контактные давления рабочих органов на уплотняемый материал. На практике это достигается использованием различных типов катков (лёгких, средних и тяжёлых) для укатки смеси. Это приводит к усложнению организации процесса уплотнения,в которомзанятынесколькотипоразмеровмашин,а также ухудшает такие удельные технико-экономические показатели, как трудоёмкость, энергоёмкость и металлоёмкость готовой продукции.
Изучение парков машин для уплотнения показывает, что катки статического действия составляют их основу (60 % от всех уплотняющих машин), и завершение процесса уплотнения чаще всего производится именно катками статического действия. Основным их недостатком является невысокая производительность. В связи с этим время, необходимое для уплотнения асфальтобетонного слоя, занимает продолжительный промежуток времени, в течение которого смесь остывает, снижая своюдеформативность. Последнеетребует не только привлечения более тяжёлых катков, но и увеличения времени их работы при уплотнении. Авторами [25, 26, 29, 41, 44] отмечается, что повышение эффективности использования катков статического действия возможно за счёт правильной организации совместной работы катков и асфальтоукладчика.
33
Процесс уплотнения заключается в накоплении остаточных деформаций и считается завершённым, когда материал испытывает преимущественно обратимые деформации. Вначале укатки деформации довольно значительные и состоят из необратимых сдвигов минеральных частиц относительно друг друга. Сдвиг происходит по плёнкам асфальтовяжущего, поэтому свойства плёнок на этом этапе укатки оказывают значительное влияние на уплотнение. Сопротивление материала деформированию определяется его вязкостью и сдвиговой прочностью.
При последующих проходах катка образуются новые контакты между частицами, которые осуществляются через плёнки вяжущего. С увеличением плотности материала возможности взаимных сдвигов частиц становятся всё более ограниченными. Следующий этап уплотнения характерен преобладанием процесса сближения частиц над сдвигом. При этом из зон контактов между частицами происходит выжимание частиц малоструктурированного вяжущего. По мере выжимания вяжущего его плёнки становятся тоньше, прочнее и начинают непосредственно участвовать в деформировании. Процесс уплотнения носит затухающий характер. Сопротивление деформированию значительно возрастает, в то время как доля необратимых деформаций сокращается. Сравнительно небольшое увеличение плотности значительно повышает прочность материала. Например, увеличение коэффициента уплотнения на 1 % в интервале от 0,92 до 1,00 обеспечивает повышение прочности горячего мелкозернистого асфальтобетона на 7–8 % [25, 26], поэтому завершение процесса является наиболее важным. Завершается уплотнение понижением температуры покрытия и увеличением плотности до требуемого значения. Дальнейшее приложение высоких контактных давлений приводит к дроблению зёрен минерального заполнителя в точках их соприкосновения и разрушению плёнок асфальтовяжущего, что отрицательно сказывается на долговечности покрытия. Необходимо отметить, что подобного недостатка лишены пневмошинные катки.
34