
2399
.pdf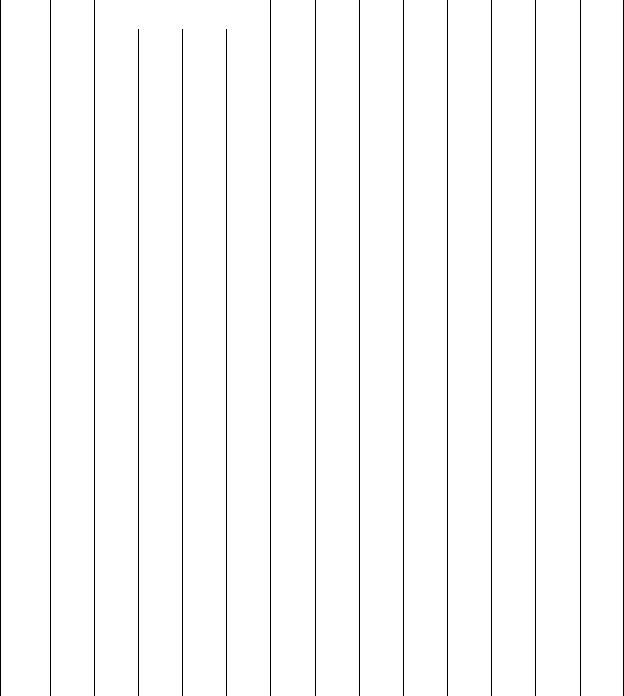
Таблица 4
Швеллеры стальные горячекатаные (по ГОСТ 8240–89)
|
Но- |
|
Мас- |
|
Размеры,мм |
|
А, |
Jx. |
Wx, |
ix. |
Sx |
Jy |
Wy. |
|
|
|
||
|
|
|
|
|
|
|
|
|
||||||||||
С |
|
|
|
|
2 |
4 |
3 |
|
3 |
4 |
3 |
iy, |
z0, |
|
||||
|
мер |
|
са |
|
|
|
|
|
|
|
||||||||
|
швел- |
1 м, |
h |
b |
|
s |
t |
см |
см |
см |
см |
см |
см |
см |
см |
см |
|
|
|
лера |
|
кг |
|
|
|
|
|
|
|
|
|
|
|
|
|
|
|
5 |
|
4,84 |
50 |
32 |
|
4,4 |
7 |
6,16 |
22,8 |
9,1 |
1,92 |
5,59 |
5,61 |
2,75 |
0,95 |
1,16 |
|
|
|
6,5 |
|
5,9 |
65 |
36 |
|
4,4 |
7,2 |
7,51 |
48,6 |
15 |
2,54 |
9 |
8,7 |
3,68 |
1,08 |
1,24 |
|
8 |
|
7,05 |
80 |
40 |
|
4,5 |
7,4 |
8,98 |
89,4 |
22,4 |
3,16 |
13,3 |
12,8 |
4,75 |
1,19 |
1,31 |
|
|
|
|
|
|
|
|
|
|
|
|
|
|
|
|
|
|
|
|
|
10 |
|
8,59 |
100 |
46 |
|
4,5 |
7,6 |
10,9 |
174 |
34,8 |
3,99 |
20,4 |
20,4 |
6,46 |
1,37 |
1,44 |
|
|
|
|
|
|
|
|
|
|
|
|
|
|
|
|
|
|
|
|
|
12 |
|
10,4 |
120 |
52 |
|
4,8 |
7,8 |
13,3 |
304 |
50,6 |
4,78 |
29,6 |
31,2 |
8,52 |
1,53 |
1,54 |
|
|
|
|
|
|
|
|
|
|
|
|
|
|
|
|
|
|
|
|
|
14 |
|
12,3 |
140 |
58 |
бА |
5,6 |
40,8 |
45,4 |
11 |
1,7 |
1,67 |
|
||||||
|
|
4,9 |
8,1 |
15,6 |
491 |
70,2 |
|
|||||||||||
|
|
и |
|
|
|
|
|
|
|
|
|
|||||||
|
14а |
13,3 140 62 4,9 8,7 17,0 |
545 |
77,8 |
5,66 |
45 |
57,5 |
13,3 |
1,84 |
1,87 |
|
|||||||
16 |
|
14,2 |
160 |
64 |
|
5 |
8,4 |
18,1 |
747 |
93,4 |
6,42 |
54,1 |
63,3 |
13,8 |
1,87 |
1,8 |
|
|
|
16а |
|
15,3 |
160 |
68 |
|
5 |
9 |
19,5 |
823 |
103 |
6,49 |
59,4 |
78,8 |
16,4 |
2,01 |
2 |
|
18 |
|
16,3 |
180 |
70 |
|
5,1 |
8,7 |
20,7 |
1090 |
121 |
7,24 |
69,8 |
86 |
17 |
2,04 |
1,94 |
|
|
|
18а |
|
17,4 |
180 |
74 |
|
5,1 |
9,3 |
22,2 |
1190 |
132 |
7,32 |
76,1 |
105 |
20 |
2,18 |
2,13 |
|
|
|
|
|
|
|
|
|
|
|
|
|
|
|
|
|
|
|
|
20 |
|
18,4 |
200 |
76 |
|
5,2 |
9 |
23,4 |
1520 |
152 |
8,07 |
87,8 |
113 |
20,5 |
2,2 |
2,07 |
|
|
|
|
|
|
|
|
|
|
|
|
|
|
|
|
|
|
|
|
|
|
20а |
|
19,8 |
200 |
80 |
|
5,2 |
9,7 |
25,2 |
1670 |
167 |
8,15 |
95,9 |
139 |
24,2 |
2,35 |
2,28 |
|
|
|
|
|
|
|
|
|
|
|
|
|
|
|
|
|
|
|
|
22 |
|
21 |
220 |
82 |
|
5,4 |
9,5 |
26,7 |
2110 |
192 |
8,89 |
110 |
151 |
25,1 |
2,37 |
2,21 |
|
|
|
|
|
|
|
|
|
|
|
|
|
|
|
|
|
|
|
|
|
24 |
|
24 |
240 |
90 |
|
5,6 |
10 |
30,6 |
2900 |
242 |
9,73 |
139 |
208 |
31,6 |
2,6 |
2,42 |
|
|
|
|
|
|
|
|
|
|
|
|
|
|
|
|
|
|
|
|
|
|
24а |
|
25,8 |
240 |
95 |
|
5,6 |
10,7 |
32,9 |
3180 |
265 |
9,84 |
И |
2,67 |
|
|||
|
|
|
151 |
254 |
37,2 |
2,78 |
|
|||||||||||
|
|
|
|
|
|
|
|
|
|
Д |
|
|
||||||
27 |
|
27,7 |
270 |
95 |
|
6 |
10,5 |
35,2 |
4160 308 10,9 178 262 37,3 2,73 |
2,47 |
|
|||||||
30 |
|
31,8 |
300 |
100 |
|
6,5 |
11 |
40,5 |
5810 |
387 |
12 |
224 |
327 |
43,6 |
2,84 |
2,52 |
|
|
|
33 |
|
36,5 |
330 |
105 |
|
7 |
11,7 |
46,5 |
7980 |
484 |
13,1 |
281 |
410 |
51,8 |
2,97 |
2,59 |
|
36 |
|
41,9 |
360 |
110 |
|
7,5 |
12,6 |
53,4 |
10820 |
601 |
14,2 |
350 |
513 |
61,7 |
3,1 |
2,68 |
|
|
|
|
|
|
|
|
|
|
|
|
|
|
|
|
|
|
|
|
|
40 |
|
48,3 |
400 |
115 |
|
8 |
13,5 |
61,5 |
15220 |
761 |
15,7 |
444 |
642 |
73,4 |
3,23 |
2,75 |
|
|
|
|
|
|
|
|
|
|
|
|
|
|
|
|
|
|
|
|
|
Примечание. h – высота швеллера; b – ширина полки; s – толщина стенки; t – средняя толщина полки; А – площадь поперечного сечения; J – момент инерции; S – статический момент полусечения; i– радиус инерции.
41
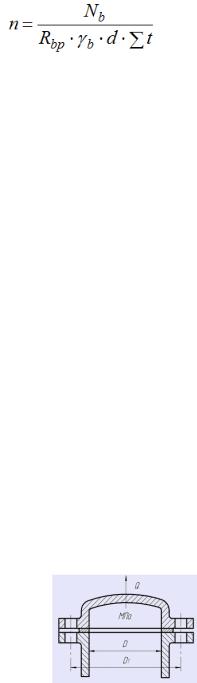
б) на смятие по формуле
.
где ∑t – наименьшая толщина соединяемых элементов, сминаемых в одном направлении, мм. За величину ∑t принимаем наименьшую толщину либо двух швеллеров (∑t=2s), либо накладки (∑t=t1).
5) Проверяем прочность элемента 2 и накладок, учитывая наличие отверстий под болты:
а) Площадь поперечного сечения швеллеров (элементов 2): |
|||||
С |
Аnt 2 ( Ашв d s), |
||||
где Ашв – площадь поперечного сечения, см2; s – толщина стенки, см. |
|||||
Услов е |
|
|
|
|
|
прочности |
|
Nb |
≤ Rbtх. γb. |
||
|
|||||
|
|
Ant |
|||
Сделать вывод. |
|
|
|
|
|
б) Определ ть площадь поперечного сечения накладки по формуле |
|||||
Условие прочности |
|
nt накладки t1(h–d). |
|||
Nb / |
|
nt накладки ≤ Rbtх. γb. |
|||
Сделать вывод. |
|
||||
|
|
|
|
|
|
Задание5. Рассчитать болтовое соединение крышки с цилиндрическим |
|||||
сосудом для бАсжатого газа (рис. 9) при следующих данных: крышка |
|||||
привернута болтами, материал – Ст 10, вид нагрузки – II, максимальное давление |
|||||
паравцилиндреР =1 МПа, внутренний диаметр цилиндра D=500 мм, диаметр |
|||||
по осям болтов D1 =700 мм. |
|
|
Д |
Рис. 9. Крепление крышкиИсосуда (болтовые соединения)
42
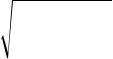
Порядок расчета:
1. Определить силу, открывающую крышку и растягивающую болты по формуле
|
|
|
Q |
D2 |
Р |
, |
|
|
|
|
|
|||
|
|
|
|
|
|
|
|
|||||||
|
|
|
|
|
4 |
|
|
|
|
|
|
|
|
|
где D – внутренн й д аметр сосуда, м;Р – давление внутри сосуда,Па. |
|
|||||||||||||
|
2. Определ тьс лу,передаваемаяодномуболтубезучетаусилиязатяжки |
|||||||||||||
|
|
|
|
Q2 =Q/i, |
|
|
|
|
|
|
|
|||
где i – необход мое ч сло болтов, рассчитывается по формуле |
|
|||||||||||||
С |
|
|
i = π |
D |
|
/ t, |
|
|
|
|
||||
где t – шаг между |
, мм (та л. 5). |
1 |
|
|
|
|
|
Таблица 5 |
||||||
|
|
|
Определение шага болта |
|
|
|
|
|||||||
|
болтами |
|
|
|
|
|
|
|
|
|
|
|
||
|
t, мм |
|
150 |
|
|
|
|
120 |
|
|
100 |
|
80 |
|
|
Р, МПа |
0,5–1,5 |
|
|
2,5 |
|
|
5 |
|
10 |
||||
|
3. Расчетная нагрузка на олт |
|
|
|
|
|
|
|
|
|
|
|||
|
|
|
|
P1 = Q1 + β |
|
Q2, |
|
|
|
|
||||
где Q1 – усилие затяжки одного |
|
олта; β |
|
– коэффициент, зависящий от |
||||||||||
упругих свойств входящих в соединение частей. |
|
|
|
|
||||||||||
|
Ориентировочно коэффициент β для прокладки из резины принимают |
|||||||||||||
|
|
бА |
|
|
|
|
||||||||
равным 0,75, из мягкой меди – 0,35. Если упругие свойства скрепленных |
||||||||||||||
деталей неизвестны, принимают β = 1. |
|
|
|
|
|
|
|
|
||||||
|
Практически можно считать Q1 = Q2, откуда P1 = Q1 |
(1 + β). |
|
|||||||||||
|
4. Рабочее напряжение при растяжении рассчитывают |
по формуле |
||||||||||||
|
|
|
4 Q |
|
|
|
|
|
||||||
|
Диаметр болта |
|
|
|
Д(1+ )/(i π d). |
|
||||||||
|
|
|
d |
|
4 Q (1 ) , |
|
|
|
|
i х[ р ] И
где [ р ] – допускаемое напряжение при растяжении, Па (см. табл. 2).
43
|
Библиографический список |
|
1. |
Детали машин : учебник для вузов / М.Н. Иванов. – 4-е изд., перераб. – М. : |
|
Высшая школа, 1984. – 336 с. |
|
|
2. |
Методика расчёта монтажной и ремонтной оснастки : учеб. пособие / А.Д. Яцков, |
|
С |
|
|
Н.Ю.Холодилин,О.А.Холодилина.–Тамбов:Изд-воТамб.гос.техн. ун-та,2008.– 116с. |
||
3. |
Лебский, .Л. Методика расчета на прочность резьбовых соединений : |
|
метод.указания / сост. . Л. Лебский, М. М. Матлин [и др.]; ВолгГТУ. – Волгоград, |
||
2010. – 32 с. |
|
|
4. |
ТО 0041–2004. Конструкции стальные строительные. Болтовые соединения. |
|
1. Перечислте в ды нагружен я олтов. |
|
|
Проектирован е расчет. –Введ.2005–01–01.–М. : Издательство стандартов, 2005. |
||
5. |
П 16.330.2011. Стальные конструкции. – Введ. 2011–05–20. – М. : |
|
тандартинформ, 2011. |
|
|
|
болта |
|
|
Контрольные вопросы и задания |
|
2. Приведите пр мер о означения олта. |
|
|
3. Перечисл те, на что про зводится расчет |
? |
|
|
А |
|
4. Укажите, как определяется нео ходимое количество болтов в соединении? |
||
|
Д |
|
|
|
И |
44
Лабораторная работа № 4
РАСЧЕТ СВАРНЫХ СОЕДИНЕНИЙ НА ПРОЧНОСТЬ
Цельработы:освоениеметодоврасчетасварныхсоединенийнапрочность.
|
|
|
|
1. Теоретическая часть |
|
|
В маш ностроен |
при |
изготовлении машин и механизмов широко |
||||
применяются разл чные в ды соединений. В соответствии с [1] различают |
||||||
сварки |
|
|
||||
разъемные |
|
неразъемные |
соединения. Основным видом неразъемных |
|||
Ссоединен й в настоящее время являются сварные соединения. Это обусловлено |
||||||
низкой сто мостью сварных соединений, высокой производительностью |
||||||
процесса |
|
, возможностью автоматизации технологического процесса. Во |
||||
|
ресурсосберегающих |
|
|
|||
многих случаях сварка является единственно возможным или наиболее |
||||||
эффективным спосо ом создания неразъемных соединений конструкционных |
||||||
материалов |
|
получен я |
|
заготовок, |
максимально |
|
приближенных |
по геометрии |
к оптимальной форме готовой |
детали или |
соединенияобладаютнетолькоАпрочностью,нои водо-игазонепроницаемостью. Сварные соединения о разуются путем местного нагревания деталей в зоне их соединении. Сваркой изготавливаютДстанины, рамы, корпуса редукторов,
конструкции. Несмотря на то, что основным конструкционным материалом в
сварных конструкциях и изделиях остается сталь, непрерывно увеличивается
применение легких сплавов, полимерных материалов и композитов. Сварные
зубчатые колеса больших размеров, шкивы, цистерны, трубы, корпуса морских судов и т. п. Существует много методов сварки (более 60), которые подразделяются на две основные группы: сварка плавлением (газовая,
высокочастотная, дуговая и др.) и сварка пластическим деформированием (контактная, стыковая, точечная и др.). НаиболееИраспространены дуговая и
контактнаявидыэлектросварки.
Для дуговой сварки применяют электроды Э42, Э42А, Э46 и др. Число после буквы Э, умноженное на 10, обозначает минимальное значение временного сопротивления металла шва; буква А – повышенное качество электрода. Достоинства: экономия материала (сварные конструкции легче клепаных на 20...25%); герметичность соединений; возможность соединения деталей любых криволинейных профилей и толщины; значительно меньшая трудоемкость по сравнению с заклепочными соединениями. Недостатки: невысокое качество шва; высокая концентрация напряжения в зоне сварных швов; при переменных режимахнагруженияпрочностьсварныхшвовневысокая.
45
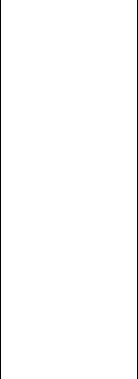
Стандарты, регламентирующие основные типы, конструктивные элементы, размеры и условные обозначения сварных соединений, выполненных различными видами сварки, приведены в табл. 1 (выдержка).
Таблица 1
тандарты, регламентирующие основные типы, конструктивные элементы, размеры и условные обозначения сварных соединений (выдержка)
|
|
ГО Т |
|
|
Наименование |
|
ГО |
Т 5264–80 |
|
Ручная дуговая сварка. Соединения сварные |
|
|
ГО |
Т 8713–79 |
|
под флюсом. Соединения сварные |
|
|
ГО |
Т 11533–75 |
|
Автомат ческая и полуавтоматическая дуговая сварка под флюсом. |
|
Сварка |
Соед нен я сварные под острыми и тупыми углами |
||||
|
ГО |
Т 11534–75 |
|
Ручная дуговая сварка. Соединения сварные под острыми и тупыми |
|
|
|
|
|
|
|
|
ГО |
Т 14771–76 |
|
Дуговая сварка в защитном газе. Соединения сварные |
|
|
ГОСТ 14776–79 |
|
Дуговая сварка. Соединения сварные |
||
|
ГОСТ 14806–80 |
|
Дуговая сварка алюминия и алюминиевых сплавов в инертных газах. |
||
|
|
углами |
|
||
|
|
|
|
Соед нен я сварные |
|
|
ГОСТ 15164–78 |
|
Электрошлаковая сварка. Соединения сварные |
||
|
ГОСТ 15878–79 |
|
Контактная сварка. Соединения сварные |
||
|
ГОСТ 16038–80 |
|
Сварка дуговая. Соединения сварные трубопроводов из меди и медно- |
||
|
|
|
|
никелевого сплава |
|
|
ГОСТ 16310–80 |
|
Соединения сварные из полиэтилена, полипропилена и винипласта |
||
|
ГОСТ 23518–79 |
|
Дуговая сварка в защитных газах. Соединения сварные под острыми и |
||
|
|
|
|
тупыми углами |
|
|
ГОСТ 23518–79 |
|
Соединения контактные, электрические, сварные |
||
|
|
|
бА |
||
|
|
Дефекты |
сварки классифицируются по ГОСТ 30242–97 «Дефекты |
соединений при сварке металлов плавлениемД. Классификация, обозначение и определения» и по ГОСТ Р ИСО 6520–1–2012 «Сварка и родственные процессы. Классификация дефектов геометрии и сплошности в металлических материалах» (дефект – несплошность в сварном соединении или отклонение от
требуемой геометрии; недопустимый дефект – дефект, превышающий норму).
Дефекты классифицированы на шесть следующих групп: 1 – трещины; 2 – |
|
полости, поры; 3 – твердые включения; 4 – несплавления и непровары; 5 – |
|
нарушение формы шва; 6 – прочие дефекты, не включенные в |
|
вышеперечисленные группы. |
И |
При выполнении соединений могут |
возникать пороки шва |
(некачественные участки): в начале движения электрода – непровар, на конце шва при отрыве электрода – кратер (рис. 1).
46
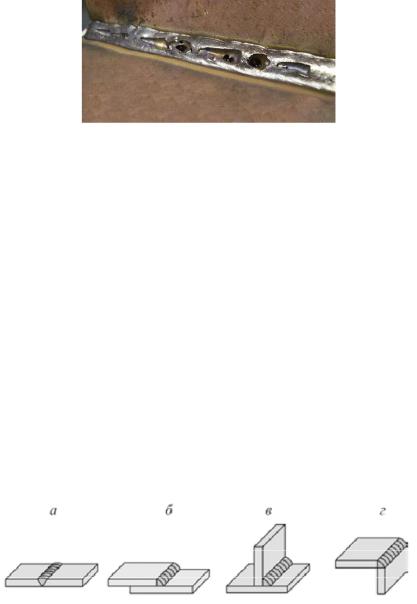
Р с. 1. Внешний вид дефектов сварных швов
Непровар – местное отсутствие сплавления между свариваемыми
элементами, между основным и наплавленным металлом или отдельными |
|
С |
|
слоями шва |
многослойной сварке. В результате непровара уменьшается |
сечение шва |
возн кает местная концентрация напряжений, что в конечном |
итоге сн жает прочность сварного соединения. При вибрационных |
|
нагрузках даже мелк непровары могут снижать прочность соединения до |
|
40%. Больш |
непровары корня шва могут снизить прочность до 70%. |
при |
|
|
обязательно |
В месте кратера толщина шва резко уменьшается, что вызывает |
|
понижен е прочности сварного соединения. При действии динамической |
|
нагрузки разрушение шва почти всегда начинается с кратера, поэтому кратер |
|
необходимо |
заделывать. |
Основные виды сварных соединений определяются взаимным |
|
расположением свариваемых элементов, среди которых выделяют стыковые, |
|
нахлесточные, тавровые и угловые (рис. 2). |
|
|
А |
|
Рис. 2. Виды сварных соединений: а – стыковое; б – нахлесточное; |
|
Д |
|
в – тавровое; г – угловое |
Стыковые соединения простые и надежныеИв сравнении с другими соединениями. Применяется ручная дуговая сварка и автоматическая – шов образуется за счет основного металла. Стыковые соединения применяются в самых простых случаях (рис. 2, а) и в конструкциях, работающих при переменных напряжениях.
Нахлёсточные соединения выполняют угловыми швами с различной формой сечения (рис. 2, б). Основные характеристики углового шва: катет шва k и высота шва h. У нормального шва катеты равны, поэтому h=k.sin450 0,7k. В большинстве случаев принимают k=d.
47
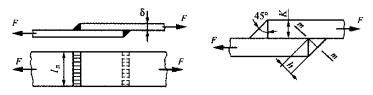
Угловые швы рассчитывают на срез по опасному сечению т–т (рис. 3), совпадающему с биссектрисой прямого угла. Расчетная высота опасного сечения h=0,7k – для ручной сварки, h = К – для автоматической.
СиР с. 3. Геометрия углового сварного шва
Прочность сварных соединений зависит от прочности основного металла соед няемых элементов, прочности наплавленного металла шва,
формы |
бА |
|
в да соед нен |
я и связанного с этим распределения напряжений в |
|
соединен |
, характера |
с лового воздействия на соединение, технологии |
сварки. |
|
|
При некачественном выполнении шва в нем могут оказаться поры,
газовые шлаковые включения и прочие внутренние дефекты, которые являются внутренними источниками концентрации напряжений, которые и будут ослаблять шов при его ра оте на растяжение. Поэтому стыковой шов, работающий на растяжение, принимается равнопрочным основному металлу только в том случае, если он удет надежно проверен одним из физических методов контроля (рентгеновскими или ультразвуком) и признан годным к эксплуатации. На стыковые швы, работающие на сжатие или срез, влияние возможных внутренних источников концентрации напряжений (газовые и шлаковые включения, поры и т.п.) оказывается меньшим, а потому применение физических методов контроля для них не является обязательным. Это позволяет принимать для таких швов расчетные
сопротивления равными сопротивлению основного металла. |
|
||||
Д |
|
||||
Основным критерием работоспособности швов сварных соединений |
|||||
является прочность. |
|
|
|
|
|
Допускаемое напряжение на растяжение сварного шва по формуле |
|
||||
|
|
Т |
, |
|
(1) |
s |
|
||||
р |
|
|
И |
||
|
|
|
|
где Т – предел текучести стали, МПа (см. табл. 1 стр. 3); [s] – коэффициент запаса прочности, [s] =1,4–1,6.
Расчетное напряжение на растяжение сварного шва определяется по формуле
48
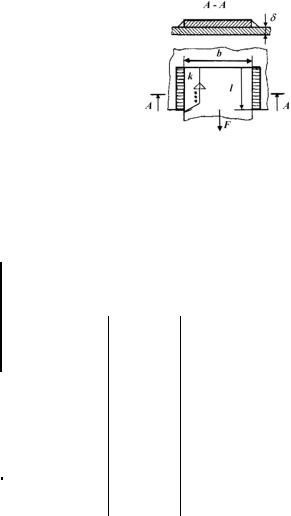
|
|
|
σр=F/(δlш)≤[ ]р, |
|
|
|
(2) |
||||
|
гдеF – нагрузка,действующаяна шов, Н;δ– толщинадетали,мм;lш – длина шва, |
||||||||||
|
мм;[σ/]р–допускаемоенапряжениедля материаласвариваемойдетали,МПа. |
||||||||||
|
Условие прочности шва на срез |
|
|
|
|
|
|
|
|||
|
|
|
ср = F/A = F/(hlш) ≤ [ ]ср, |
|
|
(3) |
|||||
|
где ср и [ ]ср – расчетное и допускаемое напряжения среза для шва, МПа; |
||||||||||
|
h –высота шва, мм; lш – |
расчетная длина шва, мм. |
|
|
|
|
|
||||
|
длину |
|
|
|
|
|
|
|
|
||
|
|
|
2. Расчетная часть |
|
|
|
|
|
|||
СЗадача 1. Определ ть |
стыкового шва, соединяющего две полосы |
||||||||||
|
из т 08 (р с. 4). Толщ на полос δ=8 мм. Сила, действующая на соединение, |
||||||||||
|
F=50 кН, сварка электродуговая Э42. |
|
|
|
|
|
|
|
|||
|
|
бА |
|
|
|
|
|
||||
|
Порядок расчета [4]: |
|
|
|
|
|
|
|
|
||
1. |
Определ ть |
допускаемое |
напряжение |
на |
|
|
|
|
|||
|
растяжен е сварного шва по формуле (1). |
|
|
|
|
|
|
||||
2. |
Определ ть |
расчетное |
напряжение |
на |
|
|
|
|
|||
|
растяжение сварного шва по сечению соединяемых |
|
|
|
|
||||||
|
деталей δ и b=lш по формуле (2). Значения допускаемого |
Рис. 4. Расчетная |
|||||||||
|
напряжения для материала |
свариваемой детали |
|
|
схема |
||||||
|
|
|
Допускаемые напряжения в швах |
|
|
Таблица 2 |
|||||
|
|
|
|
|
|
|
|||||
|
|
|
|
|
|
|
|||||
|
|
|
|
|
|
|
|||||
|
Вид технологического процесса сварки |
|
опускаемые напряжения в швах, |
|
|||||||
|
|
|
|
|
|
|
МПа при |
|
|
|
|
|
|
|
|
|
|
|
|
|
|
||
|
|
|
|
|
|
|
|
|
|
||
|
|
|
|
|
|
И |
|
||||
|
|
|
|
|
|
растяжении |
|
сжатии |
|
cрезе |
|
|
|
|
|
|
Д[ ]р [ ]сж |
[ ] |
|
||||
|
Автоматическая под флюсом, ручная электродами |
[σ]р |
|
[σ]р |
0,65[σ]р |
|
|||||
|
Э42А и Э50А, контактная стыковая |
|
|
|
|
|
|
|
|
||
|
|
|
|
|
|
|
|
|
|
||
|
Ручная дуговая электродами Э42 и Э50, |
|
|
0,9[σ]р |
|
[σ]р |
|
0,6[σ]р |
|
||
|
газовая сварка |
|
|
|
|
|
|
||||
|
|
|
|
|
|
|
|
|
|
||
|
|
|
|
|
|
|
|
|
|
||
|
|
|
|
|
|
|
|
|
|
||
|
Контактная точечная и шовная |
|
|
– |
|
– |
|
0,5[σ]р |
|
49
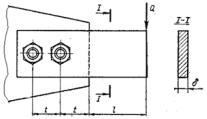
3. Определить длину стыкового шва по формуле b=lш ≥F/(δ.[ ]р).
Задача 2. Определить длину фланговых швов соединения полосы с
косынкой из т 08 (рис. 5) из условия прочности. Сила, действующая на соеди- Снение, F=80 кН, ширина полосы b=200 мм. Сварка ручная электродом Э42.
Толщина деталейδ.
иР с. 5. Соединение косынки с полосой
Порядок расчета:
1. Определ ть допускаемое напряжение на растяжение сварного шва по формуле (1).
2. Определ ть допускаемое напряжение среза шва (табл. 2).
3. Из условия прочности на растяжение определить толщину полосы δ:
бАF F
|
|
|
|
|
F . |
|
|
|
|
|
|
b[ ]р |
|
4. Принимая катет шва к=δ=3 мм, из условия прочности шва на срез |
||||||
найдем длину фланговых швов |
|
|
Д |
|||
|
|
|
|
|
||
ср = |
|
|
|
|
|
[ ]ср. |
|
|
|
|
|||
|
|
|
|
0,7К 2l |
||
Тогда |
|
|
|
|
И |
|
|
|
|
|
|
|
|
|
|
l F / (1,4K [ ]ср). |
Задача 3. Рассчитать стыковое соединение штанги буровой установки на прочность (рис. 6, 7).
Буровая штанга является обязательным конструкционным элементом всех установок бурения скважин. Штанга (буровая труба) выполняет функцию передачи крутящего усилия от привода установки к буру (конструкция, разрушающая породу), который расположен на её конце и выполняет бурение скважин. Штанги изготавливаются в виде стальной трубы, диаметр которой от 60 до 120 мм, а длина от 0,5 до 2 м, вес – до 40 кг. Буровая штанга, по сути, из всех элементов буровой установки переносит
50