
2336
.pdf
|
u |
э |
|
dэ2 |
|
zэ2 |
|
z2 |
|
|
cosδ1 |
|
|
z2 |
ctgδ |
|
|
z2 |
|
|
z2 |
u2 . |
|||||||||||
|
|
|
|
|
|
|
|
z |
|
z |
|
z |
|||||||||||||||||||||
|
|
|
d |
э1 |
z |
э1 |
|
z |
|
|
|
sinδ |
1 |
|
|
|
|
|
1 |
|
|
|
12 |
||||||||||
|
|
|
|
|
|
1 |
|
|
|
|
|
|
1 |
|
|
|
1 |
1 |
|
||||||||||||||
|
Итак, окончательно получим |
|
|
|
|
|
|
|
|
|
|
|
|
|
|
|
|
|
|
|
|
||||||||||||
|
|
|
|
|
|
|
|
|
|
|
u |
э |
|
dэ2 |
|
|
|
zэ2 |
u2 . |
|
|
|
(3.20) |
||||||||||
|
|
|
|
|
|
|
|
|
|
|
dэ1 |
|
|
zэ1 |
|
|
|
||||||||||||||||
|
Откуда |
|
|
|
|
|
|
|
|
|
|
|
|
|
|
|
|
|
|
12 |
|
|
|
|
|
|
|||||||
|
|
|
|
|
|
|
|
u2 d |
|
|
|
|
|
|
|
|
|
|
|
|
r u2 |
|
|
|
|
||||||||
|
|
|
|
|
|
d |
э2 |
э1 |
|
|
или |
r |
. |
|
(3.21) |
||||||||||||||||||
|
|
|
|
|
|
|
|
12 |
|
|
|
|
|
|
|
|
|
|
|
э2 |
|
|
э1 12 |
|
|
|
|
||||||
AO' |
Радиус кривизны зуба шестерни ρ1 |
|
(рис. 3.4) найдем из треугольника |
||||||||||||||||||||||||||||||
П: |
|
|
|
|
|
|
|
|
|
|
|
|
|
|
|
|
|
|
|
|
|
|
|
|
|
|
|
|
|
|
|
|
|
1 |
|
|
|
|
|
|
|
|
|
|
|
|
|
|
|
|
|
ρ1 rэ1 sinα. |
|
|
|
|
|
(3.22) |
|||||||||
|
|
|
|
|
|
|
|
|
|
|
|
|
|
|
|
|
|
|
|
|
|
|
|||||||||||
|
Радиус кривизны зуба колеса ρ |
2 |
определим из треугольника BO' П |
||||||||||||||||||||||||||||||
|
|
|
|
|
|
|
|
|
|
|
|
|
|
|
|
|
|
|
|
|
|
|
|
|
|
|
|
|
|
|
2 |
||
|
|
|
|
|
|
|
|
|
|
|
|
|
|
|
|
ρ2 rэ2 sinα. |
|
|
|
|
|
|
(3.23) |
Кривизной называется величина, обратная радиусу.
Приведенная кривизна 1ρ эвольвентных профилей шестерни и колеса равна сумме кривизны профиля шестерни 1
ρ1 и кривизны профиля колеса 1
ρ2 , т.е.
1 |
|
1 |
|
1 |
. |
(3.24) |
|
|
|
ρρ1 ρ2
Радиусы кривизны эвольвент ρ1и ρ2 в полюсе зацепления П определяются по формулам (3.22) и (3.23).
Для дальнейшего решения формулы (3.24) понадобятся зависимости, которые найдем из рис. 3.1. Радиусы начальных окружностей эквивалентных цилиндрических колес определяются по формулам (3.10).
Синусы и косинусы конусных углов определяются по формулам (3.18)
и (3.19).
Решим уравнение (3.24), используя подстановки, заимствованные из предыдущих формул (3.21), (3.22) и (3.23),
1 |
|
1 |
|
1 |
|
1 |
|
1 |
|
1 |
|
|
1 |
|
. |
|
|
|
rэ1 sinα |
rэ2 sinα |
rэ1 sinα |
r |
u2 |
|
|||||||
ρ ρ1 ρ2 |
|
|
|
sinα |
|||||||||||
|
|
|
|
|
|
|
|
|
|
|
|
э1 |
12 |
|
|
Общим знаменателем этих дробей будет rэ1u122 sinα. После подстановки общего знаменателя и формулы (3.21) получим
1 |
|
|
2u2 |
2 |
2 |
|
u2 |
1 |
|
|
|||
|
|
|
|
12 |
|
|
|
|
12 |
|
|
. |
(3.25) |
ρ |
d |
|
u2 |
|
dэ1 sinα |
u |
2 |
|
|||||
|
э1 |
sinα |
|
|
|
|
|||||||
|
|
|
12 |
|
|
|
|
12 |
|
|
|
61
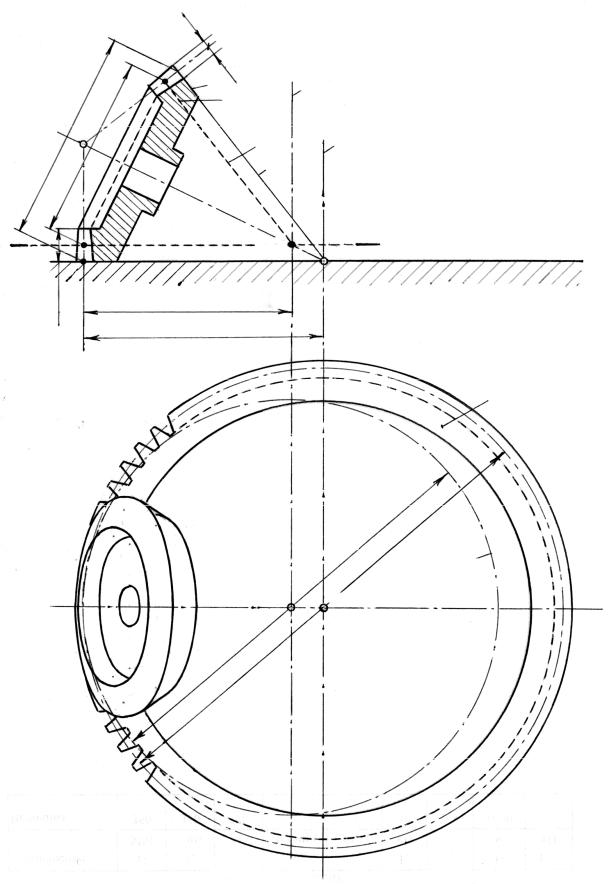
2 |
m2 |
d |
d |
П
N
L
B
b
ha
hf
Т
Tср
2
1
О'2
rэ2 rυ 2
O '2
Ось развертывания дополнительного конуса 2
Ось развертывания дополнительного конуса 1
N
L
O2
7
dэ2 dυ2
8
O2
Рис. 3.3
62
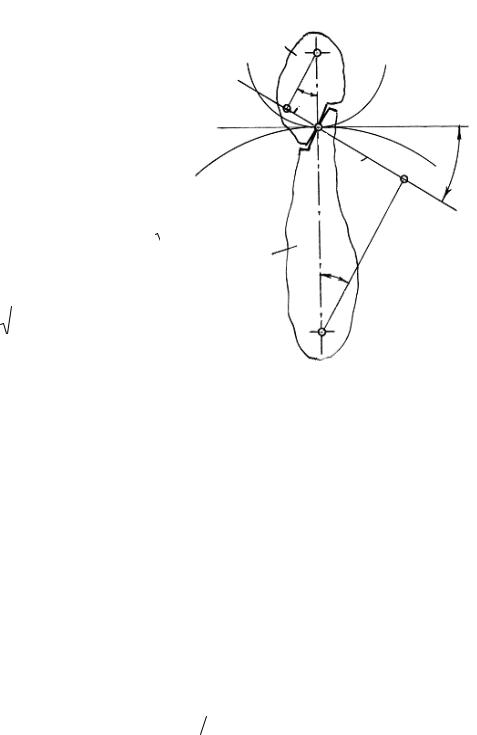
Вместо делительного диа- |
Шестерня |
|
|
|
|
метра эквивалентной шестерни |
|
|
|
|
|
|
|
O'1 |
|
|
|
подставим его значение из фор- |
|
α |
|
|
|
A |
rэ1 |
|
|
||
мулы (3.11), а вместо cosδ1 – его |
ρ1 |
|
|
||
значение из формулы (3.19), то- |
|
|
|
|
|
гда получим |
|
|
П |
ρ2 |
α |
|
|
|
|||
|
|
|
|
В |
|
|
|
|
|
|
1 |
|
2cosδ |
|
1 u2 |
|
|
|
|
2 |
|
|
|
||||
|
|
|
1 |
|
|
12 |
|
|
|
|
|
|
rэ2 |
|||
|
ρ |
dm1 sinα |
|
u2 |
|
|
dm1 sinα |
|
||||||||
|
|
|
|
|
|
|
|
|
|
|
|
|||||
|
|
|
|
|
12 |
|
|
|
|
|
|
|
|
|
||
. |
|
Окончательно будем иметь |
|
|
Колесо |
|||||||||||
|
|
|
|
|
α |
|||||||||||
|
|
|
|
|
|
|
|
|
|
|
|
|
|
|
|
|
|
|
|
|
|
|
|
|
|
|
|
|
|
|
|
O'2 |
|
1 |
|
2 |
|
|
1 u |
2 |
|
|
|
|
|
|
||||
|
|
12 |
|
|
. (3.26) |
|
|
|
||||||||
|
ρ |
dm1 sinα |
|
|
u12 |
|
|
|
|
|
|
|
||||
|
|
|
|
|
|
|
|
|
|
|
|
|
|
Рис. 3.4
Коническое зацепление отличается от цилиндрического тем, что сила давления F зуба шестерни на зуб колеса раскладывается на три составляющие (рис. 3.5). Окружная сила Ft направлена по касательной к начальным окружностям шестерни и колеса. Индексом 2 будем отмечать силы давления шестерни на колесо, приложенные к колесу: Fr2 – радиальная сила, направленная от точки касания П к центру колеса O2; Fa2 – осевая сила, направленная параллельно оси OO2 вдоль радиуса O1П от шестерни; окружная сила Ft , приложенная к колесу и направленная в сторону, куда показывает момент M1.
Силы давления (силы в зацеплении) являются функцией крутящего момента. Силы давления шестерни на колесо определяются величиной и направлением момента M1. Окружная сила рассчитывается по формуле
Ft 2M1 dm1 , |
(3.27) |
где M1 – крутящий момент на шестерне, Н·мм; dm1– средний делительный диаметр шестерни, мм, который соответствует среднему сечению зуба N N и определяется по формуле
dm1 mmz1
или |
|
dm2 mmz2 . |
(3.28) |
63
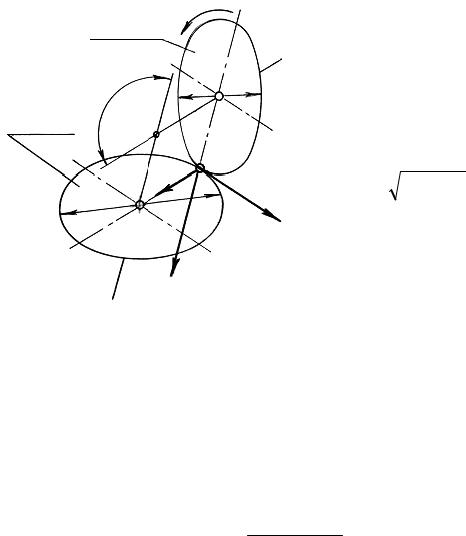
Радиальная сила находится по формуле |
|
Fr2 Ft tgα sinδ1, |
(3.29) |
где α – угол зацепления.
Осевая сила рассчитывается по формуле
М1
Шестерня
O1 dm1
900
Колесо
О
П
O2
Fr2
dm2 Ft
Fa2
Рис. 3.5
Fa2 Ft tgα cosδ1. (3.30)
Силы Fr2 и Ft направлены перпендикулярно к оси OO2 колеса. Если их сложить геометрически, то получим
F2 |
Ft |
2 Fr22 . |
(3.31) |
Эта сила F2 будет использована при расчете вала на изгиб с кручением.
3.2. Расчет зубьев на изгиб
Расчет зубьев на изгиб прямозубых цилиндрических колес приведен в [1. с.166…169], где используется схема, аналогичная рис. 3.6. В результате преобразований получено условие прочности зуба цилиндрического прямозубого колеса на изгиб
σи y z12Mψ1 m3 σи .
Внесем коррективы в это уравнение.
Действительная нагрузка F зависит не только от передаваемого момента M1, но и от неравномерности распределения давления по длине контактных линий, оцениваемой коэффициентом kиα , а также от действия инерционных сил, возникающих вследствие неравномерности вращения колес, связанной с погрешностями изготовления. Эти силы – инерционные, их влияние оценивается коэффициентом динамичности kи . Кроме этого, вводится коэффициент kиβ , учитывающий угол наклона зуба косо-
64
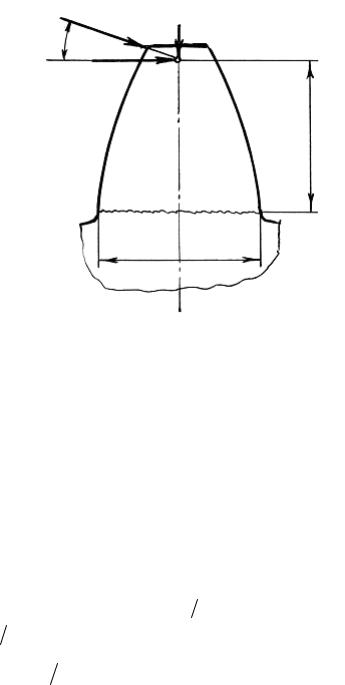
зубых конических колес. Суммарное действие коэффициентов оценивается формулой (5.3) т. 3
kи kuα kuβ ku .
Расчет |
на |
изгиб зуба |
кониче- |
F |
Fr |
|
ских колес проводится (рис. |
α |
|
||||
|
|
|||||
3.1) |
для |
среднего |
сечения |
Ft |
|
|
N N , для которого выполнен |
|
|||||
|
|
|||||
чертеж сечения зуба (рис. 3.6) с |
|
|
||||
приложенными к нему силами |
|
|
||||
согласно рис. 3.5. Напряжения- |
|
|
||||
ми сжатия в сечении 1-1 (см. |
|
|
||||
рис. 3.6) пренебрегают. Напря- |
1 |
1 |
||||
жения от изгиба в этом сечении |
||||||
|
|
|||||
имеют величину |
|
|
lm |
Рис. 3.6
hm
σ |
u |
|
Mu |
|
6Ft hm |
|
2M1 6hm |
|
|
2M1 |
|
6k |
|
|
|
2M1 |
|
. |
|||
|
b l2 |
|
z ψ m3 |
q2 |
y |
|
z ψ m3 |
||||||||||||||
|
|
W |
x |
|
|
d |
m1 |
b l2 |
|
|
э |
|
|||||||||
|
|
|
|
|
m |
|
|
m |
1 |
m |
|
|
|
|
1 |
m |
|
В выводе этой формулы делались подстановки: изгибающий момент Mu Ft hm; hm kmm – плечо силы Ft относительно опасного сечения 1- 1; mm – модуль в среднем сечении зуба; dm1 z1 mm – делительный диаметр в среднем сечении зуба; z1– число зубьев шестерни; b ψmm – ширина зубчатого венца (длина зуба); lm q mm – толщина зуба у его основания для среднего сечения; k и q– коэффициенты формы зуба, зависящие
от и z, т.е. угла зацепления |
и числа зубьев; Wx blm2 |
6 – момент сопро- |
тивления сечения 1–1; Ft 2M1 |
dm1 – окружная сила; |
|
yэ q2 6k |
(3.32) |
– коэффициент формы зуба конического колеса в среднем сечении, который определяется для эквивалентного числа зубьев.
Окончательно условие прочности зуба конического прямозубого колеса на изгиб имеет вид
65
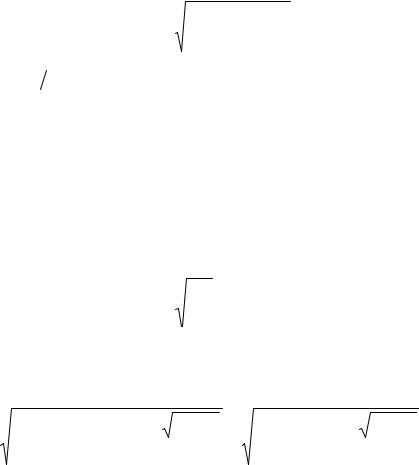
σ |
u |
|
|
|
2M1 ku |
σ |
u |
, |
(3.33) |
|
y |
|
|
||||||||
|
|
э |
z |
ψ m3 |
|
|
|
|||
|
|
|
|
1 |
m |
|
|
|
|
где M1 – крутящий момент на шестерне, Н·мм, выбирается из силового расчета механизма (редуктора); ku – поправочный коэффициент, определяемый по формуле (5.3), т. 3; yэ – коэффициент формы зуба, определяем через эквивалентное число зубьев zэ1 по табл. 2.1; ψ – коэффициент ширины зуба выбирается в пределах 6 ψ 8; σu – допускаемое напряжение для нормализованных конструкционных сталей определяется по фор-
мулам (2.28) и (2.29).
3.3. Расчет зубьев на контактную прочность
Вывод расчетной формулы контактного напряжения для конических колес аналогичен цилиндрическим колесам. Расчет проводится для эквивалентного цилиндрического колеса, соответствующего среднему сечению зуба (см. рис. 3.1 и 3.3). Расчет заключается в определении наибольших контактных напряжений σн [1. рис. 16.7], которые вычисляются по формуле Герца
|
σн |
|
E |
|
|
q |
, |
(3.34) |
|
|
2π(1 μ |
2) |
|
||||
|
|
|
|
ρ |
|
|||
где E 2E1E2 (E1 E2) |
– приведенный модуль упругости; |
E1 и E2 – мо- |
||||||
дули упругости шестерни и |
колеса, т.к. шестерня и колесо-стальные, |
|||||||
E1 E2 , следовательно, |
E E1 |
E2; q |
– |
равномерно распределенная или |
погонная нагрузка на единицу длины зуба, которую можно определить по формуле (16.38), [1, c. 171] q Ft bcosα; μ – коэффициент поперечного сжатия, или коэффициент Пуассона, для сталей можно принимать μ 0,3; 1
ρ – приведенная кривизна, которая определяется по формуле (3.26).
Если подставить значение μ в формулу (3.34), то получим
σн |
0,418 |
qE |
. |
(3.35) |
|
||||
|
|
ρ |
|
После подстановки в формулу (3.35) значений q и 1ρ, а также sinαcosα (sin2α)
2 получим
|
0,35F 2E |
|
1 u2 |
0,7E |
|
F |
1 u2 |
|
|||
σн |
t |
|
12 |
|
|
|
t |
|
12 |
. |
(3.36) |
b cosα dm1 sinα |
|
sin2α |
|
|
|||||||
|
|
u12 |
|
bdm1 |
u12 |
|
|||||
|
|
|
|
|
|
|
|
|
|
|
66 |
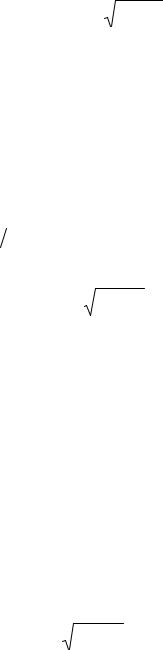
Возведем в квадрат это уравнение
σ2 |
sin2α |
|
Ft |
|
1 u122 |
. |
|
|
|
|
|||||
н |
0,7E |
bd |
m1 |
|
u |
||
|
|
|
|
|
12 |
|
Для стандартного угла зацепления α 20
2 |
sin2α |
Cн |
или Сн |
0,918 |
σ |
н2 |
|
|
σн |
|
|
|
, |
(3.37) |
|||
0,7E |
|
|
||||||
|
|
|
|
E |
|
где Cн – коэффициент контактных напряжений, размерность которого такая же, как напряжение σн .
Если обозначить Ft 2M1 |
dm1 , b ψmm и |
dm1 z1 mm, то получим |
уравнение условия прочности |
|
|
|
|
|
2M |
1 |
|
1 u2 |
C |
|
. |
|
||
C |
н |
|
|
|
|
12 |
н |
(3.38) |
||||
ψ z2 |
m3 |
u12 |
||||||||||
|
|
|
|
|
|
|||||||
|
|
1 |
|
m |
|
|
|
|
|
|
Аналогично расчету зубьев на изгиб в формулу (3.38) нужно ввести поправочный коэффициент kн , расчет которого приводится в §5.1, т. 3, см.
формулу (5.6), т. 3.
Условие контактной прочности прямозубых конических колес можно записать с одним дополнением. Экспериментально установлено, что нагрузочная способность конической передачи составляет 0,85 по сравнению с эквивалентной цилиндрической. Это равносильно тому, что для эквивалентных колес нагрузка (момент M1) увеличивается на 15 %, т.е. расчетный момент нужно принимать равным M10,85. Для учета этого эффекта нужно вместо числового коэффициента 2 подставить 2/0,85=2,35.
Итак, окончательно условие контактной прочности имеет вид
|
|
|
2,35M |
1 |
k |
н |
|
1 u2 |
C |
|
, |
|
C |
н |
|
|
|
|
12 |
н |
(3.39) |
||||
ψ z2 |
m3 |
|
u12 |
|||||||||
|
|
|
|
|
|
|
||||||
|
|
1 |
|
m |
|
|
|
|
|
где kн – поправочный коэффициент, определяемый по формуле (5.6, т.3);Cн – допускаемый коэффициент контактных напряжений, определяемый по формуле (2.22).
4. ВЫБОР И ПРОЕКТНЫЙ РАСЧЕТ ПОДШИПНИКОВ
Подшипники выбирают, исходя из конкретных условий эксплуатации. На работоспособность подшипника влияют следующие факторы:
67
1.Величина и направление нагрузки на подшипник: радиальная, осевая или комбинированная.
2.Частота вращения подшипника.
3.Долговечность, т.е. срок службы, выраженный в часах или миллионах оборотов.
4.Состояние окружающей среды: температура, влажность, запыленность и т.д.
5.Конструктивные особенности подшипникового узла: самоустанавливание подшипника при перекосах вала, тип посадки на вал (скользящая, плотная, тугая, прессовая), способ монтажа, необходимость осевого смещения вала, регулировка и т.д.
В процессе проектирования и эксплуатации машин выработаны рекомендации по выбору типа подшипника. При этом следует руководствоваться следующими соображениями.
1.Шариковые однорядные подшипники наиболее распространенные и дешевые.
2.Шарикоподшипники обеспечивают более точное вращение и более быстроходные, чем роликовые подшипники.
3.При равных габаритах грузоподъемность роликовых подшипников больше, чем шариковых.
4.Шарикоподшипники менее чувствительны, чем роликовые, к перекосам вала при монтаже и во время работы. Они допускают перекос до
0,50.
5.Однорядные радиальные шарикоподшипники предназначены для восприятия радиальной нагрузки, но могут работать при сочетании радиальной и осевой (до 25 % от радиальной) нагрузок.
6.Радиально-упорные шарикоподшипники и роликоподшипники с коническими роликами (конические подшипники) предназначены для восприятия радиальной и осевой нагрузок, но могут работать при чисто радиальной и чисто осевой нагрузке. Обеспечивают жесткую фиксацию осевого положения вала, что важно для правильной установки зубчатых конических и червячных колес. Устанавливаются парными комплектами: для длинных валов – оба подшипника в одной опоре и при коротких жестких валах – по одному в разных опорах. Требуют регулировки осевого зазора или натяга.
7.Упорные шарикоподшипники предназначены для восприятия только осевой нагрузки. Имеют ограниченную частоту вращения.
Суть рекомендации по выбору подшипников сводится к следующему.
В цилиндрических редукторах обычно применяют шариковые радиаль-
ные подшипники. При расчете сначала принимают подшипники легкой серии. Если их грузоподъемность окажется недостаточной, выбирают подшипники средней серии. Если и они не устраивают, тогда применяют роликовые конические подшипники.
68
Осевая нагрузка Fa у цилиндрических колес с косыми зубьями при8 ...150 составляет от полной силы F
Fa /F (0,14...0,27)Ft /1,17Ft 0,12...0,23 12...23 %.
Это укладывается в допускаемые нормы (до 25 %) для радиальных шарикоподшипников.
Передача с шевронными зубьями замыкает осевые силы (уравновешивает) между двумя венцами с противоположно наклоненными зубьями, поэтому осевого давления на подшипники не оказывает.
Вконических и червячных редукторах необходимо точно и жестко фиксировать зубчатые колеса по отношению к конической шестерне или червяку.
Начальные конусы в зубчатой конической передаче должны касаться друг друга по образующей ОВ (т. 3, рис. 4.14 и 4.15), при этом вершины конусов О совмещаются. Это обязательное условие нормальной работы конической передачи. Для осевой регулировки конического колеса предусматривают специальные элементы конструкции, а для жесткой фиксации вал колеса устанавливают на двух радиально-упорных подшипниках, которые затягивают обычно крышками.
Вчервячной передаче (см. рис. 1.3) для ее нормальной работы нужно, чтобы центр резьбы колеса О совпадал с осью червяка. Для осевой регулировки червячного колеса также предусматривают специальные элементы конструкции, а жесткость обеспечивается радиально-упорными подшипниками (см. рис. 1.7).
Шариковые радиально-упорные подшипники обладают меньшей осевой жесткостью, чем роликовые конические, поэтому в силовых передачах предпочитают роликовые конические подшипники для опор валов конических и червячных колес. Вначале выбирают легкую серию, а затем по мере надобности – среднюю серию. Для быстроходных валов при n 1500 об/мин используют, как правило, шариковые радиально-упорные подшипники.
Вал конической шестерни вращается в несколько раз быстрее колеса, поэтому при n 1500 об/мин можно применять роликовые конические и шариковые радиально-упорные, а при n 1500 об/мин используют шариковые радиально-упорные. Начинают также с легкой серии.
Червяк нагружен осевой силой, которая значительно превосходит радиальную. По этой причине выбор подшипников неоднозначен. Применяют обычно радиально-упорные подшипники средней серии. Если редуктор работает с перерывами, то выбирают роликовые конические подшипники средней серии, у которых динамическая грузоподъемность С на 30 % больше шариковых (серия 46000). Если предполагается длительная непрерывная работа, то для снижения тепловыделения в опорах червячного вала
69
применяют шариковые радиально-упорные подшипники средней серии
46300 и 66300.
Шариковые радиально-упорные подшипники используют, как правило, в качестве опор жестких валов, вращающихся с повышенной частотой вращения (n 1500 об/мин).
Согласно методике по выбору и расчету подшипников качения при частоте вращения n 10 об/мин основным критерием работоспособности является динамическая грузоподъемность С, которая связана с долговечностью L в млн. оборотов кольца формулой
|
|
|
С |
|
|
|
|
|
L |
|
|
, |
(4.1) |
|
|
|
||||
|
|
|
|
|
|
|
|
|
Q |
|
|
||
где L |
60 |
nh – расчетная долговечность подшипника млн оборотов за |
||||
|
||||||
106 |
|
|
|
|
|
расчетный срок службы h 10000 ч. (срок службы может быть другой в зависимости от условий работы); С – динамическая грузоподъемность подшипника, кН; Q – приведенная расчетная нагрузка на подшипник, кН;– показатель степени: 3 для шарикоподшипников, 3,33 для роликоподшипников.
Динамическая грузоподъемность – это постоянная радиальная нагрузка, которую может выдержать подшипник с неподвижным наружным кольцом без усталостного разрушения в течение 1 млн оборотов.
Приведенная или эквивалентная нагрузка Q подшипников – это условная постоянная радиальная нагрузка, которая обеспечивает ту же долговечность, что и реальная нагрузка при наличии радиальной R и осевой A сил.
Есть два метода выбора и расчета подшипника. Первый метод относится к эскизному проекту. Суть его заключается в том, что в соответствии с рекомендациями намечают тип подшипника, например для вала червяка. Затем приведенную выше формулу решают относительно С
60 |
1/ |
|||
С Q |
|
|
nh |
|
106 |
||||
|
|
и по ней вычисляют требуемую динамическую грузоподъемность и выбирают по таблицам подшипник, для которого Стабл С .
Второй метод. Согласно методике эскизного проектирования рассчитывают диаметры шеек валов, в том числе и под подшипник, тип и размер которого определяется диаметром отверстия подшипника. Определяют расчетную динамическую грузоподъемность и сравнивают ее с табличной. Если Стабл С , то выбор удовлетворительный.
70