
2336
.pdf7.2. Определение параметров шероховатости
Средняя линия m m профиля делит неровности таким образом, что в пределах базовой длины l площади выступов A1, A3, … An 1 равны площадям впадин A2 , A4 , … An , т.е.
n 1 |
n |
|
|
Aнечет |
A1 A3 ... An 1 Aчет |
A2 A4 ... An. |
(7.1) |
i 1 |
i 2 |
|
|
Базовая длина l это длина участка поверхности, которая выбирается для измерения шероховатости. Числовые значения l выбираются из ряда: 0,01; 0,03; 0,08; 0,25; 0,80; 2,5; 8; 25 мм.
Наибольшая высота неровностей профиля Rmax это сумма наи-
большего значения высоты выступов (Hi max)max и наибольшего значения глубины впадин (Hi min)max в пределах базовой длины l:
Rmax (Hi max)max (Hi min)max. |
(7.2) |
На высоте (Hi max)maxпроводится линия выступов профиля, а на глу-
бине (Hi min)max – линия впадин.
Наибольшая высота неровностей Rmax грубо характеризует шероховатость поверхности, поэтому она практического применения не имеет, т.к. показывает высоту от самой глубокой впадины до самой высокой вершины, тогда как остальная поверхность (90 %) состоит из гораздо меньших вершин и впадин. Более объективно характеризует шерохова-
тость высота неровностей Rz профиля по десяти точкам: пяти вершинам и пяти впадинам. Rz определяют как сумму среднего арифметического пяти вершин выступов Hi max и среднего арифметического пяти вершин впадин Hi min , т.е.
1 |
5 |
|
|
|
5 |
|
|
|
|
|
H1max H2max |
... H5max |
|
|||
|
|
|
|
|
|
|||||||||||
Rz |
|
|
|
Hi max |
|
|
|
Himin |
|
|
|
|
|
|
||
|
|
|
||||||||||||||
5 |
i 1 |
|
|
|
i 1 |
|
|
|
|
|
5 |
|
|
|||
|
H1min H2min ... H5min |
. |
|
|
|
(7.3) |
||||||||||
|
|
|
|
|||||||||||||
|
|
|
|
5 |
|
|
|
|
|
|
|
|
|
|
|
В результате мы получаем среднюю высоту неровностей от среднего значения впадины до среднего значения вершины по пяти точкам.
Наиболее объективно характеризует шероховатость среднее арифметическое отклонение профиля Ra , под которым понимается следующее. Если вычислить сумму площадей Ai всех выступов и разделить ее на ба-
131
зовую длину l, то получится среднее арифметическое всех высот yi' вы-
ступов относительно средней линии. Обозначим эту высоту Hср' , тогда
Hср' |
|
1l |
|
|
|
|
A A |
... A |
|
||||||||
|
|
|
|
|
|
y'(x) |
dx |
1 |
3 |
n 1 |
(7.4) |
||||||
|
|
|
|
|
|
|
|||||||||||
или приближенно |
|
|
|
|
l 0 |
|
|
|
|
|
|
l |
|
||||
|
|
|
|
|
|
|
|
|
|
|
|
|
|
|
|
|
|
Hср' |
1 |
n |
|
|
yi' |
|
|
|
A A ... A |
|
|||||||
|
|
|
|
|
|||||||||||||
|
|
|
|
|
|
|
* x |
1 |
|
3 |
n 1 |
. |
(7.5) |
||||
|
|
|
|
|
|||||||||||||
|
|
l i 1 |
|
|
|
|
|
|
|
l |
|
|
|
||||
|
|
|
|
|
|
|
|
|
|
|
yi"
гда
Аналогично можно определить среднее арифметическое всех глубин впадин относительно средней линии. Обозначим эту глубину Hср" , то-
Hср" |
|
1l |
|
|
A A |
... A |
|
|
|
|
y"(x) |
dx |
2 4 |
n |
|
l |
|
l |
|||||
|
|
0 |
|
|
|
или приближенно
Hср" |
1 |
n |
|
yi" |
|
A A |
... A |
|
|||
|
|
|
|||||||||
|
|
|
|
|
* x |
2 4 |
n |
, |
(7.6) |
||
|
|
|
|||||||||
|
|
l i 1 |
|
|
|
|
l |
|
|||
|
|
|
|
|
|
|
где y' текущее значение высоты профиля выступов; yi' дискретное значение высоты профиля выступов через интервал x, который измеряется между двумя дискретными величинами yi' или yi" и является величиной постоянной, т.е. x const.
Среднее арифметическое Ra будет равно сумме среднего арифмети-
ческого выступов Hср' и среднего арифметического впадин Hср" ,
Ra Hср' |
Hср" . |
|
|
(7.7) |
|||||||
Приближенно Ra можно определять по формуле |
|
||||||||||
Ra |
1 n |
|
yi' |
|
|
|
yi" |
|
. |
(7.8) |
|
|
|
|
|
||||||||
|
|
|
|
|
|
||||||
|
|||||||||||
|
ni 1 |
|
|
|
|
|
|
|
|
|
|
|
|
|
|
|
|
|
|
|
|
||
Числовые значения параметров Ra |
и Rz |
|
разделяют на 14 классов ше- |
роховатости поверхностей (ГОСТ 2789-73), которые сгруппированы в пять разрядов в соответствии с методами обработки: грубая – 1, 2 и 3-й классы, получистовая – 4-й и 5-й классы, чистовая – 6, 7 и 8-й классы, тонкая – 9, 10, 11 и 12-й классы, сверхтонкая – 13-й и 14-й классы. При грубой обработке неровности поверхности видны невооруженным глазом. 1, 2 и 3-й классы назначают при черновой обработке (точения, сверления или фрезерования) после литья, ковки или штамповки для свободных несопрягае-
132
мых поверхностей или сопрягаемых поверхностей в качестве предварительной обработки. Классы 4 и 5 назначают для сопрягаемых поверхностей 11-го и 12-го квалитетов.
Эти классы могут быть получены получистовой обработкой после черновой. Классы 6, 7 и 8 назначают для сопрягаемых поверхностей 8-го и 9-го квалитетов. Эти классы шероховатости достигаются в три перехода: черновой, получистовой и чистовой обработки. Классы 9 и 10 назначают для сопрягаемых поверхностей 7-го и 6-го квалитетов и могут быть получены шлифованием или тонким точением сверхтвердыми материалами (эльбор, искусственный или природный алмаз). Эти классы достигаются минимум в четыре перехода. Классы 11 и 12 получают тонким шлифованием, суперфинишем и тонким растачиванием
|
|
Значения параметров шероховатости |
Таблица 7.1 |
|||
|
|
|
||||
|
|
|
|
|
|
|
Классы |
Базовая |
ли- |
|
|
|
|
шерохова- |
ния l, мм |
|
Ra , мкм |
|
Rz , мкм |
|
тости |
|
|
|
|
|
|
1 |
|
|
50 |
80; 63; |
40 |
320; 250; 200; 160 |
2 |
8,0 |
|
25 |
40; 32; |
20 |
160; 125; 100; 80 |
3 |
|
|
12,5 |
20; 16; |
10 |
80; 63; 50; 40 |
|
|
|
|
|
|
|
4 |
|
|
6,3, |
10; 8; |
5 |
40; 32; 25; 20 |
5 |
2,5 |
|
3,2 |
5; 4; 2,5 |
20; 16; 12,5; 10 |
|
|
|
|
|
|
|
|
6 |
|
|
1,6 |
2,5; 2,0; 1,25 |
10; 8; 6,3 |
|
7 |
0,8 |
|
0,8 |
1,25; 1,0; 0,63 |
6,3; 5; 4; 3,2 |
|
8 |
|
|
0,4 |
0,63; 0,5; 0,32 |
3,2; 2,5; 2; 1,6 |
|
9 |
0,25 |
|
0,2 |
0,32; 0,25; 0,16 |
1,6; 1,25; 1,0; 0,8 |
|
10 |
|
|
0,1 |
0,16; 0,125; 0,08 |
0,8; 0,63; 0,5; 0,4 |
|
11 |
|
|
0,05 |
0,08; 0,063; 0,04 |
0,4; 0,32; 0,25; 0,2 |
|
12 |
|
|
0,025 |
0,04; 0,032; 0,02 |
0,2; 0,16; 0,125; 0,1 |
|
13 |
0,08 |
|
0,012 |
0,02; 0,016; 0,01 |
0,1;0,08;0,063;0,05 |
|
14 |
|
|
|
0,01; 0,008 |
0,05; 0,04; 0,032 |
|
|
|
|
|
|
|
|
Примечания: 1. Жирным шрифтом выделены параметры шероховатости, принятые на предприятиях с единичным характером производства. 2. В третьей колонке приведены предпочтительные числовые параметры Ra , рекомендуемые ГОСТом. 3. Приме-
нение параметра Ra предпочтительно.
алмазными резцами. Классы 13 и 14 получают полированием и специальными доводочными операциями. Эти классы шероховатости достигаются
в6…8 переходов.
Сповышением класса шероховатости повышаются прочность и коррозионная стойкость детали, уменьшаются трение и износ. Но при этом
133
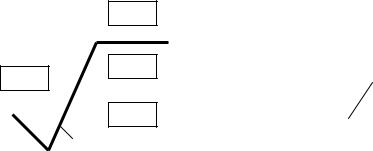
возрастают число переходов, точность и жесткость станков и их стоимость, стоимость режущих инструментов и квалификация станочников.
Одним словом, возрастает стоимость обработки деталей. Поэтому выбор класса шероховатости поверхности должен быть экономически обоснован.
Из табл. 7.1 видно, что для одного и того же класса шероховатости параметр Rz в четыре раза больше Ra .
Примеры нормирования параметра Ra для типовых поверхностей деталей приведены в табл. 7.2…7.3.
Таблица 7.2
Шероховатость поверхностей деталей зубчатых и червячных передач
Деталь, поверхности |
|
Степень точности передачи |
|
|||
6 |
7 |
|
8 |
9 |
10 |
|
|
Рекомендуемое значение Ra , мкм |
|||||
Профили зубьев колес: |
|
|
|
|
|
|
цилиндрических прямозубых, косозубых |
0,4 |
0,8 |
1,6 |
|
3,2 |
6,3 |
и шевронных |
|
|
|
|
|
|
червячных |
0,4 |
0,8 |
1,6 |
|
3,2 |
6,3 |
конических |
0,4 |
0,8 |
1,6 |
|
3,2 |
6,3 |
Окружности выступов |
0,63 |
1,25 |
2,5 |
|
5,0 |
10,0 |
Окружности впадин |
1,6 |
3,2 |
6,3 |
|
12,5 |
25 |
Профили витков червяков |
0,2 |
0,4 |
0,8 |
|
1,6 |
3,2 |
Отверстие и торец ступицы |
0,4 |
0,8 |
1,6 |
|
3,2 |
6,3 |
Торец обода |
0,8 |
1,6 |
3,2 |
|
6,3 |
12,5 |
Примечание. Классы и параметры шероховатости соответствуют первой и третьей колонкам табл. 10.1.
7.3. Обозначения шероховатости поверхности
Структура обозначения шероховатости поверхности определяется ГОСТ 2. 309-73 и приведена на рис. 7.2, на котором изображен знак, применяемый для обозначения шероховатости на чертеже. Информация, сопровождающая знак, распределяется по зонам:
1 – параметры шероховатости и их значения; 2 – вид обработки поверхности, например, полировать, или другие
дополнительные указания;
2
1 3
4
Рис. 7.2
знак
3 – значения базовой длины;
4 – обозначение направления неровностей.
Примечание. Зоны 2, 3 и 4 используют при необходимости.
– знак, соответствующий шероховатости, когда вид обработки поверхности не устанавливается.
134

– знак, соответствующий шероховатости, когда поверхность образована удалением слоя материала (точением, сверлением, фрезеро-
ванием, шлифованием и т.д.).
|
|
Таблица 7.3 |
Шероховатость поверхностей шпоночных соединений |
||
|
|
|
Соединения |
Вид поверхности |
Ra , мкм |
|
|
|
Шпоночные подвижные |
Сопрягаемая (боковая) |
1,6 |
|
Несопрягаемая (дно) |
6,3 |
Шпоночные неподвижные |
|
1,6…3,2 |
Шлицевые |
Сопрягаемая (боковая) |
6,3…12,5 |
|
Несопрягаемая (дно) |
|
|
Центрирующая: |
0,4…0,8 |
|
вал |
0,8…1,6 |
|
отверстие |
|
|
Нецентрирующая: |
1,6…3,2 |
|
вал |
|
|
отверстие |
3,2…6,3 |
|
Несопрягаемая: |
|
|
вал |
1,6…3,2 |
|
отверстие |
3,2…6,3 |
|
|
|
–знак, соответствующий шероховатости, когда поверхность
необрабатываемая или получена методом без удаления слоя материала (литьем, ковкой, объемной штамповкой, прокатом и т.п.).
0,8
– если буквенное значение параметра не указано, то числовое
135

значение относится к параметру Ra .
Rz 20 |
– буквенное обозначение параметра Rz |
указывают перед его |
||||
|
числовым значением. |
|
Таблица 7.4 |
|||
|
|
Шероховатость поверхностей валов |
||||
|
|
|
|
|||
|
|
|
|
|
|
|
Деталь узла вала |
Вид поверхности |
|
|
Квалитеты |
|
|
|
6 |
7 |
8 |
|||
|
|
|
|
Рекомендуемые Ra , мкм |
||
Зубчатое колесо, |
Посадочная поверхность: |
|
|
|
|
|
кольцо подшипни- |
при диаметре до 50 мм |
|
0,4 |
0,4 |
0,8 |
|
ка, муфта |
при диаметре св. 50 мм |
|
0,8 |
0,8 |
1,6 |
|
|
|
Торец заплечика |
|
0,8 |
0,8 |
1,6 |
Уплотнения рези- |
Посадочная поверхность при ско- |
|
|
Квалитеты |
|
|
|
новые |
ростях скольжения: |
|
9 |
10 |
11 |
|
|
до 1 м/с (полировать) |
|
0,63 |
0,63 |
0,8 |
|
|
до 5 м/с (полировать) |
|
0,4 |
0,4 |
0,63 |
Уплотнения вой- |
свыше 5 м/с (полировать) |
|
0,2 |
0,2 |
0,4 |
|
|
|
|
|
|
||
|
лочные |
Поверхность полировать |
|
0,8 |
0,8 |
1,6 |
Уплотнения лаби- |
|
|
|
|
|
|
|
ринтные |
|
|
3,2 |
3,2 |
6,3 |
|
|
|
|
|
|
|
Таблица 7.5
Шероховатость поверхностей корпусных деталей
Наименование поверхностей корпуса |
|
Квалитеты |
|
|
7 |
8 |
|
9 |
|
|
Рекомендуемые Ra , мкм |
|
||
Посадочное отверстие под подшипник: |
|
|
|
|
при диаметре до 50 мм |
0,8 |
0,8 |
|
1,6 |
при диаметре свыше 50 мм |
1,6 |
1,6 |
|
3,2 |
Торец гнезда для подшипника |
0,8 |
1,6 |
|
3,2 |
Поверхность стыка корпуса и крышки |
|
2,5…3,2 |
|
|
Поверхность под крышку люка |
|
6,3 |
|
|
Поверхность под гайку и головку болта |
|
6,3…12,5 |
|
|
Отверстие под болт |
|
6,3…12,5 |
|
|
Опорная поверхность подошвы |
|
3,2…6,3 |
|
Калибровать
0,2
Полировать
0,025
– вид обработки поверхности указывается в случаях, когда он является единственным, обеспечивающим требуемое качество поверхности. При этом в зависимости от вида обработки применяется знак сохранения поверхностного слоя либо знак обязательного удаления слоя.
136

7.4. Примеры обозначения шероховатости
Обозначения шероховатости на чертеже детали располагают (рис.
7.3):
а) на линиях контура, б) на выносных линиях,
в) на полках специальных линий-выносок.
Шероховатость рабочих поверхностей зубьев зубчатых колес, эвольвентных шлицев и т. п., когда на чертеже не приведен их профиль, условно наносят на линию делительной поверхности (рис. 7.4, а).
Если шероховатость одной и той же поверхности различна на отдельных участках, эти участки разграничивают сплошной тонкой линией и наносят соответствующие размеры и обозначения шероховатости (рис. 7.4,
б).
Обозначение шероховатости поверхности профиля резьбы наносят на линии контура, если на чертеже изображен в увеличенном виде профиль резьбы, на продолжении размерной линии (рис. 7.4, в) или на выносной линии (рис. 7.4, г).
|
|
|
Таблица 7.6 |
Шероховатость поверхностей крышек подшипников и колец |
|||
|
|
|
|
Наименование поверхностей Ra , мкм |
|
||
Посадочная цилиндрическая поверхность |
|
3,2…6,3 |
|
Торец, сопрягаемый с кольцом подшипника |
|
1,6…3,2 |
|
Торец фланца, сопрягаемый через прокладки с торцом корпуса |
3,2…6,3 |
||
Торец дистанционного кольца |
|
1,6…3,2 |
|
Внутренняя поверхность дистанционного кольца |
|
3,2…6,3 |
|
Наружная поверхность дистанционного кольца |
|
6,3…12,5 |
|
Подшипники скольжения: |
|
Квалитеты |
|
|
|
|
|
с сухим или граничным трением: |
|
6…9 |
10…12 |
вал |
|
0,4…0,8 |
0,8…1,6 |
отверстие |
|
0,8…1,6 |
1,6…3,2 |
с жидкостным трением: |
|
|
|
вал |
|
0,1…0,4 |
– |
отверстие |
|
0,2…0,8 |
– |
Для поверхностей детали, шероховатость которых не указана на чертеже и ее величина одинакова, в правом верхнем углу чертежа помещают ее обо-
значение и дополнительно условное обозначение ( ). Например, свободные поверхности детали зачастую обрабатывают с шероховатостью поверхности Rz 40. В этом случае в правом верхнем углу чертежа пишут
Rz 40
( )
137
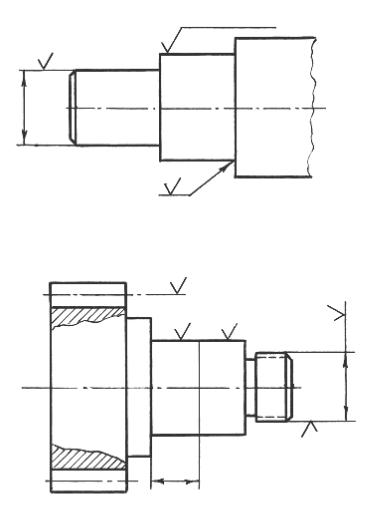
Полировать
а) 0,2
0,4 б)
Ø20k6
2,5
в)
Рис. 7.3
1,6 а)
б)
3,2 0,2
Рис. 7.4
в)
2,5
2,5
г)
8. СИСТЕМЫ СМАЗКИ
8.1. Общие сведения
Система смазки в машинах выполняет следующие функции:
1.Разделяет трущиеся поверхности и снижает потери на трение, повышает КПД.
2.Защищает поверхности от коррозии.
3.Снижает износ и увеличивает срок службы деталей.
4.Уменьшает шум при работе.
5.Охлаждает трущиеся поверхности, отводя от них тепло.
6.Заполняет зазоры в уплотнениях, повышая их герметизацию.
7.Удаляет из зоны трения металлическую пыль.
Выбор смазочного материала зависит от конструкции узлов и трущихся поверхностей, нагрузки на них, свойств жидкости. Для смазки применяют жидкие масла: веретенное, турбинное, машинное, авиационное и др.,
138
а также густые (консистентные) смазки. Густые смазки представляют собой смесь жидкого минерального масла с какими-либо загустителями (натриевые и кальциевые мыла жирных кислот, цезерин, парафин и др.).
В качестве жидких смазочных материалов применяют минеральные масла, которые получают путем переработки нефти. Каждый сорт жидкого масла характеризуется вязкостью, плотностью, температурой вспышки, температурой воспламенения, маслянистостью, температурой застывания.
Вязкость – это свойство масла или его способность проникать в зазоры между деталями или в тонкие отверстия. Вязкость зависит от температуры масла его давления. С повышением температуры масло разжижается (становится жидким) и теряет вязкость. С понижением температуры масло загущается и становится более вязким. С повышением давления масло сгущается. В системах смазки давление низкое, либо его вовсе нет, поэтому фактор давления отсутствует.
Температура вспышки паров нагретого масла определяется в специальном приборе, когда подносят к парам масла пламя, и они вспыхивают.
Температурой воспламенения называют такую, при которой нагретое масло от поднесенного пламени загорается и продолжает гореть.
Маслянистость – это свойство смазочной жидкости образовывать на поверхности смазываемых деталей прочную масляную пленку, которая разделяет трущиеся поверхности. От ее толщины зависит вид трения.
Жидкостное трение, при котором трущиеся поверхности полностью разделены слоем масла. Этот вид смазки может быть обеспечен только специальными устройствами: гидродинамическими или гидростатическими.
Большинство сопряжений в узлах машин работает в условиях неполной смазки, когда между трущимися поверхностями имеет место граничное трение, при котором слой масла имеет толщину, из которой выступает 15…40 % выступов микронеровностей, измеряемую в мкм или в долях 1мкм. Толщина слоя масла зависит от обилия смазки, формы трущихся поверхностей, давления между ними и вязкости масла.
Полужидкостное трение, когда слой масла таков, что из него выступают только самые высокие выступы шероховатости (см. гл. 7), которые составляют порядка 5…10 % площади поверхности. Коэффициент трения ниже сухого трения в 4…5 раз.
Полусухое трение, когда из масла выступает 60…70 % выступов, а коэффициент трения в 1,5…2 раза ниже сухого трения.
Сухое трение, когда смазка отсутствует.
Износ поверхностей зависит от интенсивности смазки: чем обильнее смазка, тем меньше износ.
Густые пластичные смазки применяются для подшипниковых узлов. Масло набивают в подшипниковый узел и закрывают его со всех сторон, чтобы густая смазка сохранялась в подшипниках. Это облегчает обслужи-
139
вание и уменьшает расход масла. Густая смазка применяется для подшипников, удаленных от картерной системы смазки и в других труднодоступных местах. Эта смазка заполняет зазоры между вращающимися деталями и неподвижными и предохраняет подшипниковый узел от проникновения пыли и грязи.
Густая смазка применяется в подшипниковых узлах простой конструкции, удобной для разборки и промывки, которая производится не чаще одного раза в год, и при умеренных температурах, когда масло не теряет своей пластичности. При хорошей герметизации подшипниковых узлов машин густая смазка может не заменяться в течение всего срока службы подшипников.
8.2. Способы смазки жидкими маслами
Наибольшее распространение в редукторах получила картерная система смазки. Нижнюю корытообразную часть (дно и боковые стенки) корпуса редуктора называют картером. В картер заливают масло. Верхний уровень масла имеет большое значение. Способы картерной смазки следующие:
1. Смазка окунанием в масляную ванну применяется как для зубчатых,
так и для червячных редукторов с нижним расположением червяка (рис.8.2), когда червячный вал с подшипниками занимает горизонтальное положение, а его частота вращения n ≤ 3000 об/мин. Верхний уровень масла не должен превышать центр нижнего шарика или ролика подшипника, иначе могут возникнуть нежелательные гидродинамические потери между подшипником и маслом.
В зубчатых редукторах (рис. 8.1,а) в масло погружают зубчатое колесо при окружной скорости v ≤ 12 м/с, а в червячных (см. рис. 8.2) погружают червяк при скорости скольжения v ≤ 10 м/с. Цилиндрическое зубчатое колесо погружают на глубину H1 = (2…5)m, но не менее 10мм, соответствующую нижнему и верхнему уровням масла. Ограничение скорости связано с тем, что при v > 12м/с масло сбрасывается с зубьев центробежной силой, на перемешивание масла колесами затрачивается дополнительная мощность, продукты износа не отстаиваются на дне, а перемешиваются в объеме масла, повышается температура масла. От вершины зубчатого колеса до дна ванны нужно принимать глубину H2 5...10 m, но не меньше
30…40 мм.
В червячных редукторах червяк, расположенный под червячным колесом погружают на глубину H1 = 2m, при этом центр нижнего тела качения подшипника должен соответствовать уровню масла. Когда диаметр подшипников больше диаметра червяка, то последний не погружается в масло. Тогда применяют разбрызгивающие кольца (рис. 8.4, 8.6) или
140