
2146
.pdfнагнетательный патрубки – кованы, приварены к корпусу снаружи, опорные лапы корпуса также приварены. Для герметизации соединений «крышки – корпус» и внутренних полостей проточной части используют кольцевые резиновые шнуры различного диаметра.
Конструкция кованого наружного корпуса позволяет использовать его и для перспективного давления 10 МПа при умеренной толщине стенки (около 120 мм). Необходимые полости получены с помощью тонкостенного литого внутреннего корпуса, также не имеющего горизонтального разъема. Внутренний корпус при сборке вкатывается в наружный на специальных роликах. На внутреннем корпусе закреплены входной направляющий аппарат, представляющий собой систему радиальных ребер, лопаточные диффузоры обеих ступеней и наружная часть обратного направляющего аппарата (ОНА). Внутренняя разъемная часть ОНА извлекается вместе с ротором.
Ротор имеет ступенчатый вал с максимальным диаметром (посередине) около 300 мм, на который насажены рабочие колеса, думмис (разгрузочный поршень), втулки уплотнений, полумуфта для восприятия крутящего момента и упорный гребень. Лопатки рабочего колеса выфрезерованы из тела основного диска, соединены с покрывающим (покрывным) диском с помощью пайки. Ротор приспособлен для многоплоскостной балансировки. Для извлечения ротора нет необходимости доставать внутренний корпус и диффузоры.
Воспринимающий осевые усилия упорный подшипник имеет пакеты колодок с обеих сторон. Каждый опорный подшипник сегментного типа состоит из пяти самоустанавливающихся сегментов. Уплотнения имеют лабиринтную часть и масляную концевую часть в виде щелевого уплотнения с плавающими кольцами.
Выходная сборная камера образована с помощью кольцевого углубления на торцевой крышке и специально присоединенной к ней улитки. Из статорных деталей разъем имеет только внутренняя часть ОНА.
Общее конструктивное решение нагнетателя позволяет сравнительно легко заменять при необходимости детали проточной части и получать различные модификации.
Двухступенчатый нагнетатель типа 235-21 (рис. 3.8) разработан Невским заводом им. В.И. Ленина (НЗЛ) также в нескольких модификациях по параметрам на расчетную частоту вращения 4800 об/мин для ГПА мощностью 10 МВт [27]. Отличительная его особенность – литой корпус и литая крышка с обычным фланцевым соединением. Корпус снабжен достаточно жесткими лапами, которые обеспечивают надежное крепление нагнетателя к опорной раме. Присоединительные сечения патрубков нагнетателя расположены соосно.
79

Рис. 3.8. Полнонапорный двухступенчатый нагнетатель типа 235-21 (с горизонтальным разъемом): 1 – рабочее колесо; 2 − лопаточный диффузор; 3 – корпус; 4 – крышка; 5 – сборная камера; 6 – думмис; 7 – опорный подшипник
80
Ротор нагнетателя конструктивно объединен с закладными деталями проточной части так, что образует единый сборочный блок (пакет). Это позволяет заметно сократить затраты времени на ремонт, так как для группы нагнетателей поставляется запасной комплект. Существует две сборочных модификации нагнетателя: с горизонтальным разъемом закладных частей и без горизонтального разъема. В первом случае при разборке - сборке есть хороший доступ для контроля за зазорами и взаимным положением деталей в проточной части и уплотнениях. Во втором случае (только вертикальные стыки) конструкция лабиринтных уплотнений допускает осевую сборку, а для разборки - сборки ОНА, конструктивно объединенного с лопаточными диффузорами, снимают, а затем устанавливают рабочее колесо первой ступени, которое фиксируется в осевом положении на валу резьбовой втулкой.
Рабочие колеса имеют цилиндрические лопатки, которые выфрезерованы в теле основного диска; покрывающий диск приварен к лопаткам. За рабочим колесом второй ступени на валу расположен разгрузочный поршень.
Упорный подшипник находится в картере, прикрепленном к крышке с помощью болтов и шпилек. Вкладыши опорных подшипников представляют собой разъемные втулки. Картер опорного подшипника со стороны привода конструктивно объединен с корпусом муфты. Достаточно просторная выходная сборная камера образована несколькими деталями нагнетателя.
Рассмотренные примеры конструктивного решения нагнетателей свидетельствуют о достаточно высоком совершенстве отечественных конструкций современных двухступенчатых нагнетателей.
Важной характеристикой нагнетателя является его производительность. Применительно к газопроводу различают объемную V, м3/мин, массовую G, кг/ч, и коммерческую подачи газа VК, млн нм3/сут.
Перевод одних величин в другие осуществляется с использованием уравнения Клапейрона с поправкой на сжимаемость z:
р υ = z R T.
При использовании G кг газа применяется уравнение КлапейронаМенделеева:
р V = z G R T,
где V, G – объемная и массовая подачи, характеризующие количество газа, протекающего в единицу времени через сечение всасывающего патрубка.
Коммерческая подача VК определяется по параметрам состояния во всасывающем патрубке, приведенным к нормальным физическим услови-
81

ям (t0 = 20 0С; р0 = 0,101 МПа). Для определения коммерческой подачи используется уравнение Клайперона для «стандартных» условий:
р0 υ0 = R Т0 ; VК = G / ρ0 ; ρ0 = р0 / R T0 .
Характеристика каждого типа нагнетателя строится при его натурных испытаниях. Под характеристикой нагнетателей принято понимать зависимость степени сжатия π, политропного КПД ηПОЛ и удельной приведенной мощности (Ni / ρH)ПР от приведенного объемного расхода газа VПР . Строятся такие характеристики для заданного значения газовой постоянной RПР , коэффициента сжимаемости zПР , показателя адиабаты, принятой расчетной температуры газа на входе в нагнетатель ТВ в принятом диапазоне изменения приведенной относительной частоты вращения (n/n0)ПР .
Типовая характеристика нагнетателя типа 370-18-1 приведена на рис. 3.9 [10]. Характеристики других типов имеют один вид как для неполнонапорных, так и для полнонапорных нагнетателей.
Пользуются характеристиками следующим образом. Зная фактические значения величин R, z, ТВ , n для данных условий, определяют приведенную относительную частоту вращения нагнетателя
|
n |
|
|
n |
zПР RПРТПР |
|
|
|
|
|
= |
|
|
. |
(3.2) |
|
|
|
n0 |
zB RTB |
|||
n0 |
ПР |
|
|
|
По известной степени сжатия находят приведенный объемный расход газа
VПР =VB |
n0 |
. |
(3.3) |
|
|||
|
n |
|
Затем по соответствующим кривым характеристики нагнетателя (см. рис. 3.9) определяют политропный КПД ηПОЛ и приведенную внутреннюю мощность нагнетателя (Ni / ρH)ПР .
Внутренняя мощность, потребляемая нагнетателем, определяется соотношением
Ni = Ni n 3 сВ. (3.4)
сB ПР n0 ПР
Всоотношениях (3.2)−(3.4) индексом 0 отмечен номинальный режим работы нагнетателя, индексом В − параметры газа на входе в нагнетатель. Плотность газа при всасывании ρВ , кг/м3, определяется по соотношению
82
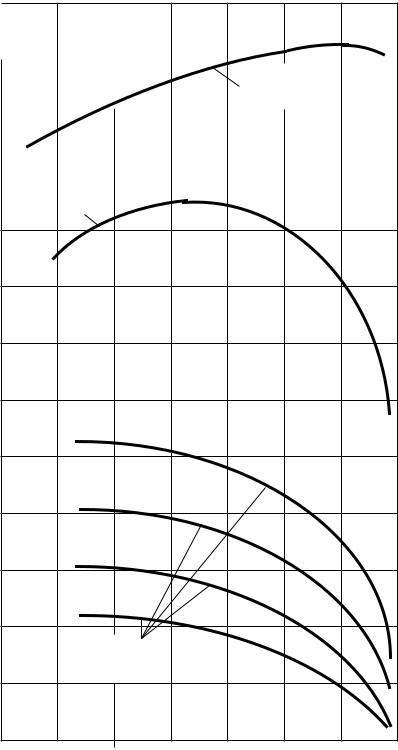
ρВ = рВ 106 / z R T, |
(3.5) |
где рВ , Т – абсолютное давление (МПа) и температура (К) при всасывании.
(Ni / ρB)ПР, |
|
|
|
кВт/(кг/м3) |
|
|
|
|
|
(Ni / ρB)ПР |
|
200 |
|
|
|
|
|
|
|
150 |
|
|
ηПОЛ |
|
|
||
|
|
ηПОЛ |
0,8
0,7
0,6
0,5
ε |
1,1 |
1,30
1,0
1,25
0,9
1,20
0,8
1,15
(n / n0)ПР
1,10
1,05
250 |
300 |
350 |
400 |
450 |
500 (QПР)нПР, м3/мин |
Рис. 3.9. Приведенные характеристики нагнетателя 370-18-1
при (ТН)ПР = 288 К; zПР = 0,9; RПР = 490 Дж/(кг К) [10]
83
Эффективная (фактическая) мощность на муфте энергопривода, кВт,
Ne = Ni + NМЕХ ,
где NМЕХ – механические потери, для газотурбинного привода NМЕХ =
= 100 кВт, для электропривода NМЕХ = 150 кВт.
Расчетный рабочий расход газа VПР для нагнетателей должен быть примерно на 10−12 % больше крайних левых значений расхода на его характеристике, соответствующего условиям начала срыва потока газа по на-
гнетателю (зона помпажа). На рис. 3.9 этому соответствует подача газа
~ 360 м3/мин.
Наличие надежных приведенных характеристик при эксплуатации газотурбинного привода позволяет обслуживающему персоналу определять характеристики работающих агрегатов и выбирать наилучший режим их работы в зависимости от конкретных условий. Для центробежных нагнетателей с электроприводом также можно пользоваться приведенными газодинамическими характеристиками, но только для какого-то вполне определенного значения (n/n0)ПР, так как электропривод в большинстве своем не имеет пока регулируемую частоту вращения.
3.5. Привод газоперекачивающих агрегатов
Вид привода компрессорной станции и их установленная мощность в основном определяются пропускной способностью газопровода и степенью сжатия по станции.
ГПА, применяемые для сжатия газа на компрессорных станциях, по типу привода подразделяются на три основных группы: газотурбинные установки (ГТУ), электроприводные агрегаты и газомотокомпрессорные установки.
Кпервой группе относятся ГПА с приводом центробежного нагнетателя от газовой турбины; ко второй – агрегаты с приводом от электродвигателя и к третьей группе – агрегаты с приводом от поршневых двигателей внутреннего сгорания, использующих в качестве топлива природный газ.
Кагрегатам первой группы – основного вида привода компрессорных станций – относятся: стационарные, авиационные и судовые ГТУ.
Кстационарным ГТУ относятся специально сконструированные для использования на газопроводах страны установки Уральского турбомоторного завода, Невского завода им В.И. Ленина (НЗЛ) и установки импортного производства.
Кавиационным ГТУ относятся ГПА, где приводом нагнетателя является газовая турбина авиационного типа, специально реконструированная для использования на компрессорной станции.
84
Ксудовым ГТУ относятся ГПА, где в качестве привода используется модернизированная газовая турбина судового типа.
Кгазомотокомпрессорным установкам на газопроводе малого диаметра
(300−350 мм) относятся ГПА отечественного и импортного производства типа 10 ГК и 10 ГКМ.
На начало 2000 г. парк ГПА на компрессорных станциях страны распределялся следующим образом: газотурбинный привод составлял примерно 85,5 % общей установленной мощности, электропривод − примерно 13,5 % и поршневой − примерно 1 %. На 253 компрессорных станциях промыслов, магистральных газопроводов и подземных хранилищ газа ОАО «Газпром» эксплуатировалось 734 компрессорных цеха с 4050 газоперекачивающими агрегатами. Общая установленная мощность их составляла свыше 40 млн кВт.
У каждого из указанных типов привода есть свои плюсы и минусы, потенциальные возможности и ограничения дальнейшего развития, направления последующего совершенствования и повышения эффективности использования, что будет оказывать влияние на дальнейшее совершенствование в развитии энергопривода компрессорных станций.
Кпреимуществам ГПА с газотурбинным типом привода следует отнести: высокую удельную мощность на единицу массы; возможность регулирования подачей технологического газа за счет изменения частоты вращения силовой турбины ГТУ; возможность использования перекачиваемого газа в качестве топлива; относительно малый расход воды и масла; непосредственное вращательное движение; реальные возможности дальнейшего увеличения основных показателей ГТУ и прежде всего ее КПД.
Кнедостаткам ГПА с газотурбинным приводом следует отнести: относительно низкий КПД агрегатов, что приводит к излишнему расходу топливного газа на нужды перекачки; относительно высокий уровень шума, особенно в районе воздухозаборной камеры ГТУ.
Преимущества ГПА с электроприводом: экологическая чистота при использовании этого привода; простота обслуживания агрегата; непосредственное вращательное движение.
Недостатки этого типа привода: необходимость подвода электроэнергии; невозможность регулирования подачи транспортируемого газа за счет изменения частоты вращения силового вала.
Кпреимуществам ГПА с поршневым видом привода относятся: боль-
шой диапазон изменения возможных степеней сжатия; относительно высокий КПД агрегатов.
Кнедостаткам этого вида привода следует отнести: сложность конструкции и большую металлоемкость; относительно высокий расход масла и охлаждающей воды; необходимость наличия мощных фундаментов.
85
К ГПА предъявляются следующие требования: возможность варьирования по степени сжатия в больших диапазонах (особенно на головных КС), надежность работы агрегатов, их максимальная автономность, высокая экономичность, экологическая чистота.
В наибольшей степени этим требованиям отвечают ГПА с газотурбинным приводом, получившим наибольшее распространение на газопроводах.
ГТУ по сравнению с поршневыми ГПА имеют более простую конструкцию, позволяют значительно сконцентрировать мощность в одном агрегате, относительно просты, полностью уравновешены, хорошо поддаются автоматизации, имеют относительно небольшие габаритные размеры. По сравнению с электроприводными ГПА они представляют собой автономный вид привода КС, работают на том же газе, что и перекачивают.
Применение электроприводных агрегатов для транспорта газа позволяет упростить условия автоматизации КС, улучшить условия труда обслуживающего персонала. Электроприводные ГПА отличаются пониженной пожарной опасностью, независимостью мощности от времени эксплуатации и температуры наружного воздуха, малым временем пуска ГПА в работу.
Одним из основных препятствий для широкого распространения электрического привода являются высокие капитальные затраты на строительство линий электропередач, высокая стоимость отпускаемой электроэнергии. Особенностью используемых электроприводных агрегатов является и то, что ГПА отечественного производства пока не имеют возможности регулировать подачу газа за счет изменения частоты вращения силового вала.
3.6. Схемы газотурбинных установок
Газотурбинные установки являются в настоящее время основным видом привода центробежных нагнетателей на крупных магистральных газопроводах. ГТУ вырабатывает механическую энергию для привода нагнетателя и тепловую в форме теплоты отходящих газов, подлежащих утилизации.
Все процессы – сжатие, подвод теплоты и расширение – непрерывно осуществляются в различных элементах ГТУ (компрессоре, камере сгорания, газовой турбине), расположенных по ходу рабочего вещества.
ГТУ простейшего цикла в механическом отношении может быть выполнена одновальной (рис. 3.10, а) или двухвальной (рис. 3.10, б).
В одновальных установках все элементы ГПА – осевой компрессор, газовая турбина и нагнетатель − находятся на одном валу и имеют одну и ту же частоту вращения. Различный закон изменения характеристик газопровода и одновальной ГТУ приводит к тому, что при снижении частоты
86
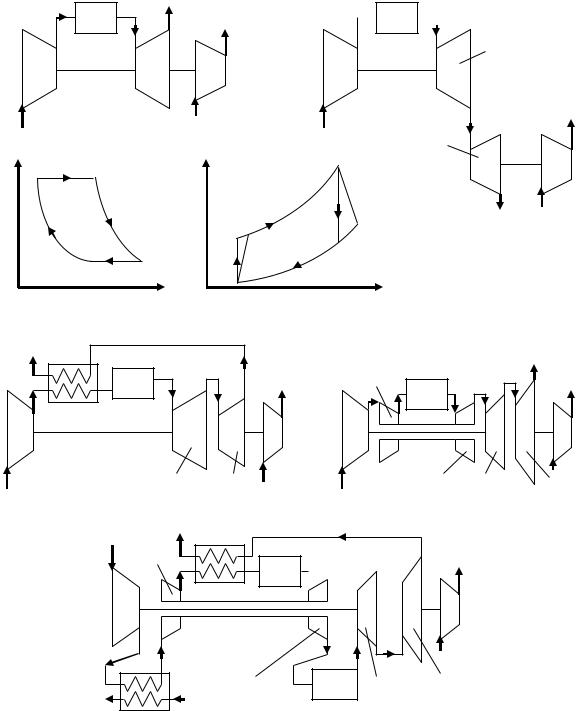
|
КС |
|
|
К |
|
Т |
Н |
|
а |
|
|
р 2 |
3 |
Т |
|
|
|
|
2’ |
|
|
|
2 |
|
1 |
4 |
1 |
|
|
υ |
|
|
|
в |
|
|
P |
|
|
|
|
КС |
|
К |
|
|
Н |
|
|
ТВД |
ТНД |
|
г |
|
|
КС
ТВД
К
ТНД
3 |
Н |
4’
б
4
s
К2
КС |
|
К1 |
Н |
ТВД ТСД |
ТНД |
д |
|
P
К2
КС
К1 |
Н |
ПО |
КС ТСД ТНД |
ТВД |
|
|
е |
Рис. 3.10. Схемы газотурбинных установок: а, б – простейшие схемы ГТУ открытого типа; в – цикл ГТУ в диаграммах; г – ГТУ с регенерацией теплоты отходящих газов; д – ГТУ открытого типа с двумя компрессорами; е – ГТУ с промежуточным отводом теплоты при сжатии и промежуточным подводом теплоты при расширении с регенерацией теплоты отходящих газов; К – осевой компрессор; КС – камера сгорания; Р – регенератор; ТВД, ТСД, ТНД – турбины высокого, среднего и низкого давлений; Н – нагнетатель; ПО – рекуператор (промежуточный холодильник)
87
вращения одновальная ГТУ быстрее теряет мощность, чем снижается мощность, потребляемая нагнетателем. Это приводит к тому, что одновальная ГТУ будет обеспечивать режим работы нагнетателя только в ограниченном диапазоне изменения частоты вращения.
При ухудшении КПД нагнетателя или элементов ГТУ осуществить оптимальную работу ГПА с приводом от одновальной ГТУ без перепуска и дросселирования газа или без существенного повышения температуры газа перед ТВД будет уже трудно. Все это привело к тому, что в настоящее время одновальные ГТУ для перекачки газа на газопроводах не используются.
В установках с разрезным валом, или с независимой силовой турбиной, вал полезной мощности выделен от турбокомпрессора, поэтому между ними нет такой однозначной связи и нагнетатель может иметь любую частоту вращения, ему необходимую.
При постоянной частоте вращения вала осевого компрессора и переменной частоте вращения силового вала температура перед газовой турбиной высокого давления может практически оставаться постоянной в достаточно широком диапазоне изменения частоты вращения вала силовой турбины. Это значит, что полезная мощность ГТУ будет изменяться пропорционально изменению характеристик силовой турбины.
Кроме того, двухвальные ГТУ имеют несколько лучшие экономические характеристики не только на частичных нагрузках, но и на расчетной, когда одновальная установка, имея некоторый запас по мощности, на номинальной нагрузке будет обеспечивать режим работы нагнетателя ниже расчетного.
Благодаря этим особенностям двухвальные установки с регенерацией (рис. 3.10, в) и без регенерации (рис. 3.10, б) теплоты отходящих газов получили широкое распространение на газопроводах.
Рабочий процесс установки с регенерацией теплоты отходящих газов (рис. 3.10, г) осуществляется следующим образом: атмосферный воздух после прохождения системы фильтров и сжатия в осевом компрессоре К поступает в воздухоподогреватель (регенератор) Р, где за счет использования теплоты отходящих из турбины газов его температура повышается на 200−250 0С. После регенератора сжатый воздух поступает в камеру сгорания (КС), куда одновременно извне подводится топливный газ. В результате сжигания топлива температура образовавшихся продуктов сгорания перед газовой турбиной высокого давления (ТВД) доводится до величины, обусловленной жаростойкостью дисков и лопаток турбины. После расширения в газовой турбине продукты сгорания проходят регенератор, в котором они частично охлаждаются, отдавая часть теплоты воздуху, идущему из осевого компрессора в камеру сгорания, и затем через дымовую трубу выбрасываются в атмосферу.
88