
- •Раздел 1. ВИДЫ ИСПЫТАНИЙ И УСЛОВИЯ ИХ ПРОВЕДЕНИЯ
- •Тема 1.1. Виды испытаний
- •Тема 1.2. Условия проведения испытаний
- •Раздел 2. ИЗМЕРЕНИЯ ПРИ ИСПЫТАНИЯХ
- •Тема 2.1. Методика планирования и проведения испытаний
- •Раздел 3. ИЗМЕРИТЕЛЬНЫЕ УСТРОЙСТВА, КОМПЛЕКСЫ И СТЕНДЫ ДЛЯ ПОЛУЧЕНИЯ ПАРАМЕТРОВ АВТОМОБИЛЯ И ШИН
- •Тема 3.1. Определение углов поворотов управляемых колес автомобиля, углов уводов и боковых реакций
- •Тема 3.2. Определение жесткости рулевого управления
- •Тема 3.4. Комплекс исследований шума и вибрации
- •Тема 3.6. Теплотехнический комплекс
- •Тема 4.1. Активная и пассивная безопасность автомобиля
- •Тема 4.2. Полигонные и лабораторные испытания кузовов и кабин
- •Тема 4.3. Правила проведения краш-тестов
- •Тема 4.4. Испытания рулевых управлений
- •Тема 4.5. Аэродинамические испытания
- •Раздел 5. СТЕНДОВЫЕ ИСПЫТАНИЯ АВТОМОБИЛЕЙ И ИХ АГРЕГАТОВ
- •Тема 5.1. Стенды для диагностирования технического состояния автомобилей. Виды стендов для испытаний автомобиля
- •Раздел 6. ИМИТАЦИОННЫЕ ИСПЫТАНИЯ
- •Тема 6.1. Математическое испытание пространственной модели для определения показателей устойчивости и управляемости автомобиля с учетом действия аэродинамических сил и моментов
- •Тема 6.3. Математическое моделирование подвески АТС с учетом особенностей работы гидроамортизатора
- •Контрольные вопросы
- •Контрольные задания
- •Список рекомендуемой литературы
Раздел 2. ИЗМЕРЕНИЯ ПРИ ИСПЫТАНИЯХ
Тема 2.1. Методика планирования и проведения испытаний
Планирование испытаний. Цели и задачи испытаний. Логикоструктурный подход к проведению испытаний. Пример разработки стратегии проведения испытаний на износ.
План рован е спытаний. Процесс изготовления автомобиля от макетного образца до серийной модели – сложный проект, включающий
комплекс разл чных |
спытаний, направленных на решение поставленных |
С |
|
задач, подч ненных одной цели – сделать качественный продукт. Этот |
|
процесс растянут во времени, может включать несколько этапов с разным |
|
уровнем |
разца и различным набором испытаний. Контроль- |
ными точками этап |
являются успешные завершения цикла испытаний и |
переходготовностина следующ й уровень технологической цепочки.
Лог ко-структурный подход (ЛСП) был разработан Агентством ме-
США туация в будущем), для того чтобыДзатем выработать план мероприятий
ждународного разв т я в |
в конце 60-х гг. для оказания помощи в |
планировании, управлении и оценке процессов и мероприятий. С того |
|
времени ЛСПбв качестве инструмента планирования проектов и управле- |
|
ния ими был принят ольшим количеством других учреждений. |
|
Словарь определяет цель как "предмет стремления". Смысл поста- |
|
новки целей состоит в определение предмета стремления (желаемая си- |
для достижения каждой цели. Этот процесс носит название целевого планирования. Ясность целей позволяет четко определить конечную задачу для всей деятельности в рамках программы испытаний, а также провести оценку осуществимости результатов. В ходе осуществления проекта ведется его мониторинг, цель которого – установить, способствует ли ход выполнения проекта достижению поставленных перед ним целей. Если нет, принимаются меры по возвращению проекта в нужное русло. Этот процесс носит название целенаправленного управления проектом.
ЛСП состоит из аналитической фазы и фазы планирования. Анали- |
|
тическая фаза включает следующие этапы: |
И |
|
Анализ заинтересованных сторон – идентификация групп, отдельных лиц и учреждений, интересы которых проект может затронуть, идентификация их основных ключевых проблем, ограничений и возможностей.
17
Анализ проблем – формулировка проблем, определение причин- но-следственных связей и построение дерева проблем.
Анализ целей – выведение целей из определенных проблем, определение отношений "средства достижения – конечный результат",
объединение целей в группы и определение стратегии проекта. Фаза планирования. Выделение логики участия – определение со-
Сставных частей проекта, проверка его внутренней логики, формулировка целей с точки зрения возможностей их измерения. Указание допущений и факторов р ска – выявление условий, могущих оказать отрицательное влияние на выполнен е проекта и не поддающихся контролю со стороны
приятийи– установлен е последовательности и взаимозависимости мероприятий, указанбюджее х предполагаемой продолжительности; расстановка вех распределен е о язанностей. Составление плана расходов – указание требующ хся ресурсов, разра отка графика расходов, подготовка
менеджмента проекта. Определение показателей – определение способов измерен я прогресса, достигнутого в выполнении проекта; формулировка
показателей; определен е средств измерения. Составление графика меро-
подробного |
та. |
|
А |
Основным выходным продуктом ЛСП является логико-структурная |
матрица. По такой матрице излагается краткое содержание проекта, приводятся допущения, лежащие в основе его стратегии, а также указывается способ мониторинга проекта. В та л. 1 обобщенно представлены структу-
ра и содержание матрицы. |
Д |
||||
|
Логико-структурная матрица |
Таблица 1 |
|||
|
|
|
|||
|
|
|
|
|
|
Текст |
Показатель |
|
Измерение |
опущения и риск |
|
достижения |
|
|
|||
|
|
|
|
|
|
Общие цели |
Измерения дости- |
|
Источники и мето- |
- |
|
|
жения общих целей |
|
ды для подтвер- |
И |
|
|
|
|
|
||
|
|
|
ждения достижений |
|
|
Конкретные цели |
Измерения дости- |
|
Источники и мето- |
опущения, влияю- |
|
|
жения конкретных |
|
ды для подтвер- |
щие на связь между |
|
|
целей |
|
ждения достижений |
конкретными и об- |
|
|
|
|
|
щими целями |
|
Результаты |
Измерения дости- |
|
Источники и мето- |
Допущения, влияю- |
|
|
жения результатов |
|
ды для подтвер- |
щие на связь между |
|
|
|
|
ждения достижений |
результатами и кон- |
|
|
|
|
|
кретными целями |
|
Действия |
Требующиеся |
|
Стоимость |
Допущения, влияю- |
|
|
ресурсы |
|
ресурсов |
щие на связь между |
|
|
|
|
|
действиями и ре- |
|
|
|
|
|
зультатами |
|
|
|
18 |
|
|
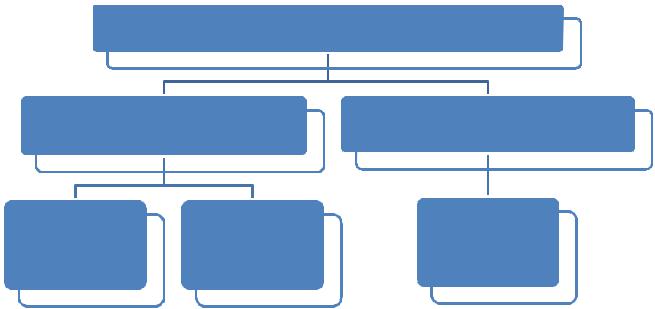
В текстовой части логико-структурной матрицы излагается логика участия проекта, а также указываются лежащие в основе данной логики важные допущения и факторы риска. Таким образом, создается основа для проверки выполнимости проекта и обеспечивается тщательная оценка сомнительных допущений и неоправданных факторов риска.
Анализ проблем включает анализ уже выявленных проблем с учетом мнения каждой заинтересованной стороны, что обеспечивает сбалансированность анализа, при котором принимаются во внимание различные и иногда прот воположные взгляды. Цель состоит в получении общего, по возможности консенсусного представления о ситуации и структуризации
САнал з проблем устанавливает причинно-следственные связи между про лемами. "Дерево проблем" представляет собой ие-
выявленных проблем в форме "дерева проблем".
разнообразнымирархическое расположен е про лем. Обсуждение всего спектра проблем, предлагаемых в качестве центральных, следует вести до тех пор, пока не
будет определена в качестве центральной единственная из предложенного для обсужден я сп ска про лем. Она будет являться исходным пунктом построен я "дерева про лем" (рис. 1).
|
Основная про лема, ее причина и следствие |
||
Проблема 1 первого уровня, |
|
Проблема n первого уровня, причина |
|
бА |
|||
причина и следствие |
|
и следствие |
|
Проблема 1 |
Проблема 2 |
Проблема n |
|
второго уровня, |
|
Двторого уровня, |
|
второго уровня, |
причина и |
||
причина и |
причина и |
||
следствие |
следствие |
следствие |
|
|
Рис. 1. "Дерево проблем" проектаИ |
Все суждения "дерева проблем" трансформируются в задачи, направленные на решение главной цели, формируя "дерево целей". Каждая пара "причина-следствие" превращается в пару "средство–эффект" (рис. 2).
19

тратегия
Цель проекта и ожидаемый эффект
Задача первого уровня, ее |
Задача второго уровня n, ее |
средства и эффекты |
средства и эффекты |
СибАДИ |
|||
Задача второго |
Задача второго |
Задача второго уровня |
|
уровня 1, ее |
уровня 2, ее |
n, ее средства и |
|
средства |
эффекты |
средства и эффекты |
эффекты |
Задача 3 |
уровня, ее |
|
|
средства |
эффекты |
|
|
Р с. 2. "Дерево целей" проекта
Анал з целесоо разно продолжать с обозначения центральной проблемы и второй про лемы, связанной с ней. Затем:
- если проблема является причиной, она помещается уровнем ниже; - если проблема является следствием, она помещается уровнем вы-
ше;
- если проблема не является ни причиной, ни следствием, она помещается на тот же самый уровень.
В то время, как анализ проблем представляет отрицательные аспекты существующей ситуации, анализ целей представляет положительные аспекты желаемой будущей ситуации. Он включает переформулировку проблем в цели – таким образом, "дерево целей" может рассматриваться как положительное зеркальное отображение "дерева проблем".
Схема логико-структурной матрицы состоит из четырех столбцов и четырех строк. Вертикальная логика представляет намерение проекта, выявляет причинно-следственные связи важные допущения. Горизонтальная логика относится к измерению результатов проекта и используемых проектом ресурсов, что производится путем определения основных показателей измерения, а также средств проверки правильности этих измерений. Концептуальная модель представлена на рис. 3.
Обычно предпочтительнее начинать заполнение логико-структурной матрицы, двигаясь вертикально вниз по первому столбцу (текст) до тех пор, пока он не будет заполнен. Как только иерархия общих целей, конкретных целей, результатов, действий и средств может считаться логичной, можно переходить к заполнению столбца допущений. Такой порядок
20
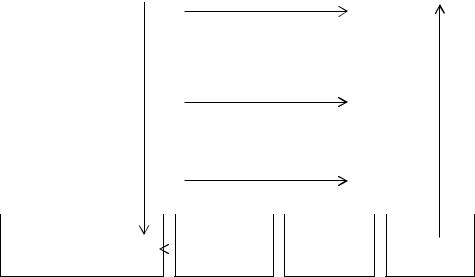
помогает проводить проверку логичности описания проекта, а также выявляет факторы, сдерживающие выполнение проекта, и всевозможные факторы риска, не поддающиеся контролю в рамках проекта. Затем заполняются второй и третий столбцы матрицы для каждого уровня иерархии проекта. Так, для каждого показателя указываются измерения, с помощью которых определяется, действительно ли показатель поддается измерению, эффективному с точки зрения затрат времени и стоимости.
СибАДИРис. 3. Логико-структурная матрица
Общая ( |
е) |
|
|
|
|
|
|
Вертикальная |
цель (и) |
|
|
|
|
|
|
|
логика – наме- |
|
|
|
|
|
|
|
|
рения проекта |
|
|
|
|
|
|
|
|
|
|
|
|
|
|
|
|
|
|
Задачи проекта |
|
|
|
|
|
|
||
(конкретные |
|
|
|
|
|
|
|
|
цели) |
|
|
|
|
|
|
|
|
|
|
|
|
|
|
|
Горизонтальная |
|
Результаты |
|
|
|
|
|
|||
|
|
|
|
|
|
|
|
логика – изме- |
|
|
|
|
|
|
|
|
рение результа- |
|
|
|
|
|
|
|
|
тов проекта и |
|
|
|
|
|
|
|
|
|
Действия |
|
|
Ресурсы |
|
|
|
|
|
|
|
|
|
|
|
используемых |
||
(работы) |
|
|
|
|
|
|
|
ресурсов |
Построение "дерева работ". Целью разбивки работ является обеспечение достаточной их простоты, облегчающей их организацию и управление ими. Такой прием заключается в подразделении действия на составляющие его поддействия, каждое из которых затем подразделяется на составляющие его задания. Каждое задание, в свою очередь, может быть передано отдельному лицу становится его краткосрочной целью.
После того, как произведена разбивка действий на достаточное количество деталей, они должны быть соотнесены друг с другом, для того чтобы установить:
- последовательность – в каком порядке должны предприниматься действия?
- зависимость – зависит ли действие от начала или завершения како- го-либо из других действий?
Например, создание автомобиля сводится к нескольким отдельным, но взаимосвязанным действиям: сборке рамы шасси, установке двигателя, кузова, прокладке проводки и гидравлики, сборке салона. Последователь-
21
ность предписывает сборку шасси и двигателя производить прежде, чем установку кузова. Зависимость же состоит в том, что нельзя начинать установку кабины до установки двигателя или что нельзя закончить сборку кузова, прежде чем будет полностью проведена электропроводка и установлена гидравлика. При проведении одним и тем же лицом действий, не связанных друг с другом в ином случае, зависимость может возникать также и между этими действиями.
СибАДИроки. Определение сроков означает проведение реалистичной оценки продолж тельности каждого действия и затем внесение его в график действ й с целью установления реальных дат начала и завершения. После этого следует распределить задания между членами коллектива и составить граф к работ. Вся содержащаяся в графике действий информация может быть о о щена в графической форме, именуемой диаграммой Гантта.
Определен е ресурсов. После составления графика работ можно переходить к определен ю тре уемых ресурсов, составлению смет и планов расходов. Формат представления заявок на ресурсы и расходы, как правило, завис т от порядка, пр нятого в организации.
Пр мер. Основными постоянно действующими причинами изменения технического состояния автомобиля, его агрегатов и механизмов являются: изнашивание, пластические деформации и усталостные разрушения, коррозия, физико-химические и температурные изменения материалов и деталей. Исследование процессов изнашивания различных деталей помогает выявить основную проблему, трансформировать ее в цели, разработать стратегию проведения испытаний, контролировать результаты на каждом этапе проектного цикла и получить результат с нужным эффектом.
В табл. 2 приведено среднее распределение отказов в процентах при пробеге 100 тыс. км для грузовых автомобилей большой грузоподъемности автобусов среднего класса.
Процесс изнашивания. Процесс изнашивания возникает под действием трения, зависящего от материала и качества обработки поверхностей, смазки, нагрузки, скорости относительного перемещения поверхностей и теплового режима работы сопряжения.
Результат изнашивания, определяемый в установленных единицах, называется износом, который может быть линейным, объемным, массовым. Интенсивность изнашивания – это относительные величины износа (отношение износа к пути трения или показателю, связанному с работой изделия, например километру пробега или часу работы автомобиля, числу циклов и т.д.).
22

Таблица 2
Распределение отказов в процентах при пробеге 100 тыс. км для грузового автомобиля большой грузоподъемности и автобуса среднего класса
|
Внешние признаки |
|
Грузовой автомобиль |
Автобус |
|
|
|
большой |
среднего |
|
|
|
проявления отказов |
|
|
||
|
|
грузоподъемности, % |
класса, % |
|
|
|
|
|
|
||
|
СибАДИ |
37 |
|
||
|
Износ |
|
40 |
|
|
|
Пластическ е деформац |
разру- |
26 |
29 |
|
|
шения |
|
|
|
|
|
В том числе: |
|
20 |
19 |
|
|
обрыв, срыв, разрыв, срез |
|
|||
|
вытяг ван е, зг б, смятие |
6 |
10 |
|
|
|
Усталостные разрушен я |
|
18 |
16 |
|
|
В том числе: |
|
12 |
7 |
|
|
трещ ны |
|
|
||
|
поломки |
|
5 |
8 |
|
|
Температурные разрушен я |
|
12 |
11 |
|
|
В том числе: |
|
|
|
|
|
перегоран е, замыкан е |
5 |
7 |
|
|
|
прогорание |
|
4 |
3 |
|
|
закоксовывание |
|
3 |
1 |
|
|
Прочие |
|
4 |
7 |
|
|
Всего |
|
100 |
100 |
|
Поверхности трения не являются абсолютно ровными; они обладают микронеровностями, величина которых зависит от точности обработки (точение – до 80 мкм, шлифование – от 2 до 20 мкм, полирование – от 0,8 до 1,3 мкм). При трении возникает взаимодействие микронеровностей трущихся поверхностей между собой и с абразивными частицами, попавшими в смазку. Разрушение нескольких слоев микронеровностей приводит к макроповреждениям – изменениям формы поверхности, размеров и формы деталей.
целью управления процессом изнашивания деталей разработана классификация видов изнашивания деталей в зависимости от ведущих процессов разрушения поверхностей трения. Детали автомобилей подвержены практически всем видам изнашивания, которые делят на три основные группы: механическое, молекулярно-механическое и коррозион- но-механическое (рис. 4).
Механическое изнашивание является результатом механических действий и включает резание, царапание, деформирование, отслаивание и выкрашивание микрообъемов материала. Основными видами механиче-
23
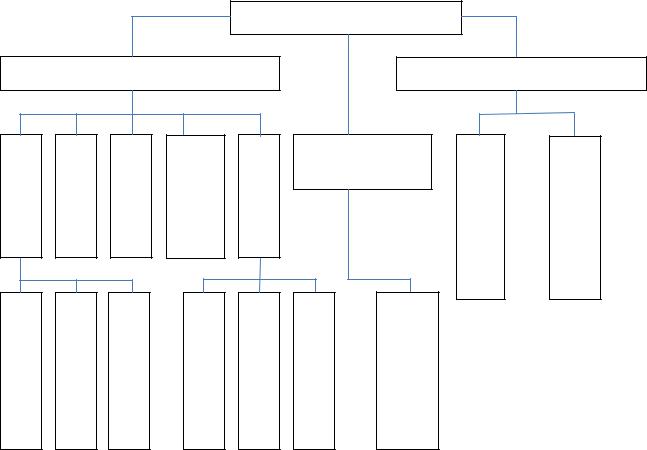
ского изнашивания деталей автомобилей являются: абразивное, гидро- и газоабразивное, гидро-, газо- и электроэрозионное, кавитационное, усталостное, и изнашивание при заедании.
Изнашивание
СибАДИ |
|||||||||
|
|
Механическое |
|
|
|
Коррозионно-механическое |
|||
Абразивное |
Фретт нг |
Усталостное |
- Кав тац он |
ное |
Эрозионное |
Молекулярно- |
Окислительное |
- коррозия Фреттинг |
|
|
|
|
|
|
|
механическое |
|
|
|
Абразивное |
Гидроабразивное |
Газоабразивное |
|
Гидроэрозионное |
Газоэрозионное |
Электроэрозионное |
Схватываниерабоповерхностейчих |
|
|
|
|
|
Рис. 4. Виды изнашивания деталей |
|
|
||||
|
Изменение структуры материала происходит из-за высокого местно- |
||||||||
го нагрева, ударов, неравномерного изнашивания отдельных зерен метал- |
|||||||||
ла |
т. д. В подшипники с антифрикционным слоем абразивные частицы |
вдавливаются и при трении увеличивают износ сопряженного вала. Абразивному изнашиванию в сочетании с другими видами подвержены практически все трущиеся детали автомобиля.
Гидроабразивному изнашиванию, происходящему под действием твердых частиц, взвешенных в жидкости и перемещающихся относительно изнашивающейся детали, подвержены водяные, топливные и масляные каналы, а также детали, смазываемые под давлением. При этом абразивными частицами являются не только частицы кварца (песка) и других соединений, попадающие на трущиеся поверхности снаружи, но и частицы нагара и продукты износа, образующиеся внутри агрегатов автомобиля.
24
Газоабразивное изнашивание возникает под воздействием частиц, взвешенных в газе. Этому виду изнашивания подвержены впускные и выпускные системы автомобильных двигателей, а также наружные лакокрасочные покрытия кузовов автомобилей, особенно при работе в запыленных условиях. Наибольший износ трущихся поверхностей деталей автомобиля вызывают частицы кварца, поэтому обеспечение чистоты воздуха
Си эксплуатационных жидкостей, поступающих во внутренние полости агрегатов автомобиля, является важнейшим методом уменьшения интенсивности разл чных в дов абразивного изнашивания.
Кав тац я представляет собой образование, а затем поглощение
гидравлическпарогазовых пузырьков в движущейся по поверхности детали жидкости при определенных соотношениях давлений и температур в переменных
сечениях потока. Разрушение кавитационных пузырьков сопровождается ми ударами по поверхности детали и образованием каверн (ямок), полостейбА. Пр мером кавитационного изнашивания являются ка-
верны, наблюдаемые на наружных поверхностях гильз цилиндров двигателя, на полостях водяных насосов.
Изнаш ван е при фреттинге возникает при трении скольжения соприкасающ хся деталей при возвратно-поступательных перемещениях в условиях динамической нагрузки с малыми амплитудами. Такое изнашивание проявляется в заклепочных, олтовых, шлицевых и шпоночных соединениях, рессорах.
Усталостное изнашивание является механическим изнашиванием в результате усталостного разрушенияДпри повторном деформировании микрообъемов материала поверхностного слоя детали. Усталостное разрушение проявляется в виде выкрашивания – отделения частиц материала, приводящего к образованию ямок (питтинга) на поверхности трения. Усталостное разрушение имеет место на поверхностях кулачков и зубьев шестерен, в подшипниках качения трансмиссииИ, в антифрикционном слое вкладышей подшипников коленчатого вала двигателя.
Трение потоков жидкостей и газов о поверхности деталей вызывает их эрозионное и кавитационное изнашивание. Эрозионное изнашивание является механическим видом изнашивания в результате воздействия на поверхность детали потока жидкости – гидроэрозионное изнашивание – или газа – газоэрозионное изнашивание. Гидро- и газоэрозионное изнашивания представляют собой процесс вымывания и вырыва отдельных микрообъемов материала. Топливная аппаратура дизелей, жиклеры карбюратора, клапаны газораспределения двигателей подвержены эрозионному изнашиванию.
25
Электроэрозионное изнашивание является видом эрозионного из-
нашивания поверхности в результате воздействия разрядов при прохождении электрического тока. Этому виду изнашивания подвержены контакты прерывателя и свечей системы зажигания автомобильного карбюраторного двигателя.
Изнашивание при схватывании рабочих поверхностей определя-
ется свойствами материалов, трущихся деталей и зависит от скорости скольжения поверхностей, а также от температуры. Для деталей автомобиля, когда матер ал трущихся деталей подобран правильно, схватывание поверхностей может быть вызвано в основном повышением температуры
при сухом трен |
определяется налипанием и переносом частиц размяг- |
|
ченного даже расплавленного металла. Такое явление может произойти |
||
С |
|
|
при отказах |
стем охлаждения и смазки автомобильных двигателей. |
|
хватыван е рабоч х поверхностей может завершаться прекращением |
||
|
дв жен я деталей и вызывать их задир – повреждение по- |
|
верхностей трен я в в де широких и глубоких борозд в направлении |
||
скольжен я, |
заедан |
, как следствие, задиры поршневых колец, порш- |
относительного |
||
ней, гильз ц л ндров, коренных и шатунных подшипников. |
||
Корроз онно-механическое изнашивание является результатом |
||
механического воздействия, сопровождаемого химическим или электри- |
ческим взаимодействиембАматериала со средой. Для деталей автомобиля коррозия при трении в основном связана с окислением материала поверхностей деталей, т. е. ведущее значение имеет окислительное изнашивание, при котором основное влияние на изнашивание оказывает химическая реакция материала с кислородом или окисляющей окружающей средой.
При окислительном изнашивании кислород воздуха или растворенный в масле образует на металле окисную пленку, которая механически удаляется при трении. Затем процесс повторяется. Пластическая де-
формация поверхностных слоев усиливает окисление. знашивание в ус- |
|
|
Д |
ловиях агрессивного действия жидкой среды имеет аналогичный меха- |
|
низм, однако пленки, как правило, малостойки при трении, и скорость |
|
процесса резко возрастает. |
|
Пластические деформации и разрушения. Пластические деформа- |
|
ции и разрушения связаны с достижением или превышением пределов те- |
|
|
И |
кучести или прочности соответственно у вязких (сталь) или хрупких (чугун) материалов. Обычно этот вид разрушений является следствием либо
ошибок при расчетах, либо нарушений правил эксплуатации (перегрузки, неправильного управления автомобилем, дорожно-транспортных происшествий и т.п.). Иногда пластическим деформациям или разрушениям
26
предшествует механическое изнашивание, приводящее к изменению геометрических размеров и сокращению запасов прочности детали.
Усталостные разрушения возникают при циклическом приложении нагрузок, превышающих предел выносливости металла детали. При этом происходят постепенное накопление и рост усталостных трещин, приводящие при определенном числе циклов нагружения к усталостному разрушению деталей. Совершенствование методов расчета и технологии изготовления автомобилей (повышение качества металла и точности изготовления, сключен е концентраторов напряжения) привело к значительному сокращен ю случаев усталостного разрушения деталей. Как правило, оно наблюдается в экстремальных условиях эксплуатации (длительные
перегрузки, н зк е |
ли высокие температуры) в рессорах, полуосях, ра- |
||
С |
|
|
|
мах. |
|
|
|
Техн |
ческое старение деталей и эксплуатационных материалов из- |
||
меняется под действ ем внешней среды. Так, резинотехнические изделия |
|||
теряют прочность |
эластичность в результате окисления, термического |
||
воздейств |
я (разогрева |
охлаждения), химического воздействия масла, |
|
ли |
|||
топлива |
ж дкостей, |
а также солнечной радиации и влажности. В про- |
|
цессе эксплуатац |
свойства смазочных материалов и эксплуатационных |
||
жидкостей ухудшаются в результате накопления в них продуктов износа, |
Детали ибАматериалы изменяются не только при их использовании, но и при хранении: снижаются прочность и эластичность, например, резинотехнических изделий; у топлива, смазочных материалов и жидкостей наблюдаются процессы, сопровождаемые выпадением осадков.
изменения вязкости и потери свойств присадок.
Техническое состояние основной доли деталей автомобилей лимитируется износом его рабочих поверхностей. При этом интенсивность из-
нашивания, являющаяся отношением величины износа к наработке зави- |
|
сит от различных факторов. Поэтому обеспечение износостойкости рабо- |
|
|
Д |
чих поверхностей деталей требует различных мероприятий как на стадиях |
|
проектирования и изготовления автомобилей, так и при эксплуатации. |
|
Испытание на износ можно проводить в условиях эксплуатации |
|
машин и в лабораторных условиях. |
|
Наиболее надежной проверкой правильности выбора материала или |
|
|
И |
способов его обработки применительно к определенной детали машины являются испытания детали на самой машине в условиях эксплуатации.
Такой способ используется часто, но он связан с практическими трудностями: длительностью испытаний, необходимостью разборки машины для определения износа детали, трудностью точного определения величины износа и др. В этом случае результат испытания на износ определяется по
27
изменению эксплуатационных свойств машины (например, понижению точности обрабатываемой заготовки), по косвенным признакам (например, увеличению утечки между плунжером и цилиндром) и непосредственно по изменению размеров или массы деталей.
Обмер деталей получил наибольшее распространение для определения износа путем обмера с помощью микрометрических инструментов до и после испытания. Этим методом с помощью специальной аппаратуры можно точно определить распределение величины износа по поверхности деталей ли образцов, пр чем поверхность должна быть чисто обработана, а вел ч на зноса не превышать 0,1 мм.
Метод определен я железа в масле заключается в том, что в ряде |
||
случаев знос можно определить по количеству железа, которое попадает |
||
С |
в смазочное масло и засоряет его. Количество |
|
в виде продуктов |
||
железа в этом случае определяется химическим анализом золы после сжи- |
||
гания пробы масла. |
Пре муществом этого метода является возможность |
|
оценивать знос |
раз орки механизма или машины, а недостатком – |
|
определен е суммарного |
по всей поверхности трения одной или |
|
износа |
|
|
нескольк х деталей |
невозможность определить распределение величины |
|
износа по поверхности детали. |
|
|
Радиоактивный метод заключается в том, что материалу детали со- |
||
общается радиоактивностьбез(введением радиоактивных изотопов некото- |
||
рых элементов в сплав при выплавке, заполнением углубления в теле де- |
||
тали проволокой из материала, содержащего радиоактивный изотоп, об- |
||
лучением детали в атомном реакторе), и тогда продукты износа, попа- |
||
дающие в масло, такжеАбудут радиоактивными. По интенсивности излу- |
||
чения их в пробе масла можно судить о количестве радиоактивного веще- |
||
|
|
Д |
ства, попавшего в масло за определенный период времени, и о скорости
изнашивания детали. |
И |
Испытания на износ можно проводить и в лабораторных условиях, в этом случае необходимо воспроизведение той же совокупности основных условий на поверхности трения, которые наблюдаются при эксплуатации детали и обеспечивают для одного и того же материала одинаковый процесс износа.
Метод абразивного износа состоит в том, что производят трение испытуемого и эталонного образцов о поверхность с закрепленными на ней абразивными частицами (наждачная бумага) при статической нагрузке и отсутствии нагрева и сравнивают полученные результаты. В пределах одной серии испытаний технология изготовления образцов должна быть одинаковой. Измерение окончательных размеров образца перед испытанием не должно вызывать его повреждения. Перед испытанием эталонные
28
и испытуемые образцы должны подвергаться приработке для достижения полного прилегания образцов к шкурке в условиях, идентичных условиям испытаний. Все образцы одной серии испытывают на одной и той же машине. Испытания проводят при трении торца цилиндрического образца по
поверхности абразивной шкурки по спирали Архимеда в направлении от центра диска к периферии. Радиальная подача образцов на каждый оборот Сдиска составляет 1 мм. Износ испытуемого и эталонного образцов должен быть получен при одинаковых условиях: образцы должны пройти один и тот же путь трен я в пределах всей серии испытаний. За результат испытания матер ала пр н мают относительную износостойкость, вычислен-
ную как среднее ар фмет ческое результатов двух идентичных опытов.
Метод ка проведения экспериментальных исследований. В дис-
сследовании Д.К. Кушалиева (Саратов, 2015) приводится общая схема методов сследования, направленного на повышение эксплуатационной долговечности подвески автомобиля применением инновационных ремонтных комплектов (рис. 5).
Для повышен я эксплуатационной долговечности подвески, а также |
||
сертационном |
|
|
безопасности комфорта ельности движения автомобиля необходимо со- |
||
вершенствовать конструкцию амортизаторов с применением инновацион- |
||
ных ремонтных комплектов. Такой ремонтный комплект включает две |
||
|
б |
|
инновационные конструкции: в поршневом узле и сайлентблоке аморти- |
||
затора. |
|
|
Для проведения сравнительных стендовых испытаний амортизато- |
||
ров со стандартной и новой конструкцией поршневого уплотнения был |
||
использован стенд СИА-04 « |
» производства ООО «ИТЦ-ТЕСТ» |
|
(г. Энгельс). |
ЭНГА |
|
|
|
|
Методика проведения экспериментальных исследований. Задачей |
||
экспериментальных исследований явилось изучение влияния температуры |
Д и скорости перемещения поршня на усилие сжатияИи отбоя. Усилие на
штоке при сжатии амортизатора и усилие на штоке при отбое амортизатора являются функциями отклика. Также в качестве функции отклика может выступать параметр плавности хода штока поршня. Поскольку плавность хода штока поршня определяется чисто визуально по форме кривых, то в нашем случае можно ограничиться параметрами усилия отбоя и сжа-
тия Pсж и Pот. В результате предварительных экспериментов и анализа данных литературных источников выяснено, что эти параметры зависят от таких факторов, как температура То и скорость перемещения поршня Vп.
29
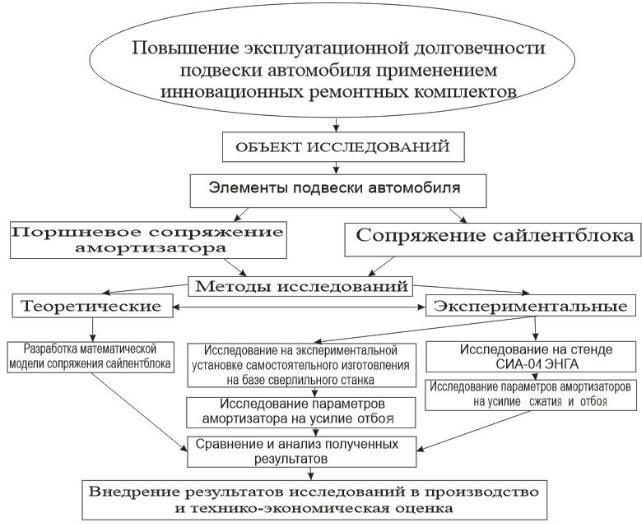
Си
Рис. 5.бАЭкспериментальные методыД, используемые для исследований стандартного и усовершенствованного амортизаторов
При увеличении температуры смазка становится более жидкой, в результате чего могут изменяться усилия отбоя и сжатия амортизатора. При низкой температуре масло густеет, амортизаторыИбудут передавать на кузов автомобиля толчки и вибрацию, а при ходе отдачи – запаздывать. От этого ухудшится комфортабельность машины и могут появиться трещины в местах крепления амортизаторов к кузову, а также увеличатся динамические нагрузки на узлы и детали. Изменение скорости также может влиять на изменения усилии сжатия и отбоя, что в свою очередь скажется и на характеристике амортизатора. В качестве факторов, влияющих на параметры амортизатора, выбраны температура То и скорость перемещения поршня Vп.
При этом план эксперимента должен обеспечивать возможность варьирования каждого фактора не менее чем на трех уровнях. Следовательно, число опытов должно быть не менее числа коэффициентов, равно-
30
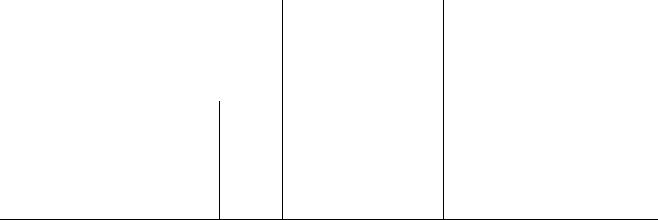
го числу сочетаний k + 2. Таким образом, при двухуровневом варьировании двух факторов общее число независимых опытов составляет
N = Sk,
где S – число независимых факторов.
Для удобства расчета коэффициентов модели в матрицу планирования вводили фиктивную независимую переменную X0, которая во всех опытах принимает значение +1.
целью упрощен я последующих расчетов и представления результатов экспер мента в компактном виде использована матричная форма записи g по метод ке А.Н. Виноградова. Матрица планирования полного
|
факторного экспер |
мента показана в табл. 3. |
|
|
|||||
С |
|
|
|
|
Таблица 3 |
||||
|
|
|
|
Полный план матрицы планирования |
|
||||
|
и |
|
|
||||||
|
|
|
|
|
|
Комбинации |
Действительное значение |
||
|
Номер |
Значен я факторов в |
|
произведений |
показателя параметра |
||||
|
|
факторов |
|||||||
|
точки |
кодовых о означениях |
|
|
оптимизации по |
||||
|
|
в кодовых обозна- |
|
||||||
|
плана |
|
|
|
|
|
реализации эксперимента |
||
|
|
|
|
|
|
|
чениях |
|
|
|
|
X0 |
|
X1 |
X2 |
|
X1 X2 |
|
Y |
|
1 |
+ |
|
- |
- |
|
+ |
|
Y1 |
|
2 |
+ |
|
+ |
- |
|
- |
|
Y2 |
|
3 |
+ |
|
- |
+ |
|
- |
|
Y3 |
|
|
|
бА |
|
|
||||
4 |
+ |
+ + + |
|
Y4 |
|||||
|
|
|
|
|
|
|
Д |
Последовательность выполнения опытов выбрана с применением таблицы равномерно распределенных случайных чисел. Обозначения фак-
торов, их уровни и интервалы варьирования показаны в табл. 4.
|
|
|
Таблица 4 |
|
Исследуемые факторы в действительных значениях |
||||
|
|
|
|
|
|
Факторы процесса в единицах измерения |
|
||
Уровни |
|
И |
|
|
Температура Т, ºС |
|
Скорость V, м/с |
||
|
|
|
||
|
|
|
|
|
Верхний |
45 |
|
0,34 |
|
Нижний |
7 |
|
0,25 |
|
Основной |
26 |
|
0,295 |
|
Интервал варьирования |
19 |
|
0,045 |
|
Кодовые обозначения |
X1 |
|
X2 |
|
31
Требуемое количество опытов в каждой точке плана определено по методике С.А. Айвазяна (М., 1983). Трех повторных опытов достаточно для обеспечения 95% надежности результатов.
В результате экспериментальных испытаний отражены в полной ме-
ре те изменения, которые происходят в амортизаторе на различных режи- |
|
мах работы. Это позволяет сравнить стандартные амортизаторы с усовер- |
|
С |
|
шенствованными ремонтным комплектом, а также оценить влияние изме- |
|
нений в конструкции амортизатора на его скоростные характеристики. |
|
Тема 2.2. Общ е требования, предъявляемые к измерительной |
|
и |
|
|
аппаратуре |
Аппаратура, пр меняемая при испытаниях автомобилей; требова-
|
необход |
ния, предъявляемые к ней. О основание выбора приборов для дорожных |
|
испытан й, размещен е установка аппаратуры на автомобиле. |
|
Измерен я при спытаниях. При испытаниях автомобилей часто |
|
возникает |
мость определения сил и моментов, действующих на |
|
А |
узлы автомобиля. В ольшинстве случаев эти величины переменные, для их регистрации следует применять записывающую аппаратуру. При измерении сил и моментов вращающихся деталей используют токосъемные устройства. В лабораторных условиях при проведении статических измерений применяют динамометры общегоДназначения.
Измерительный прибор – средство измерений, предназначенное для получения значений измеряемой физической величины в установленном диапазоне.
По способу индикации значений измеряемой величины измеритель-
исуммирующие. Различают также приборы прямогоИдействия и приборы сравнения, аналоговые и цифровые приборы, самопишущие и печатающие приборы.
Измерительная установка – совокупность функционально объединенных мер, измерительных приборов, измерительных преобразователей
идругих устройств, предназначенная для измерений одной или нескольких физических величин и расположенная в одном месте.
Измерительную установку, применяемую для поверки, называют поверочной установкой. Измерительную установку, входящую в состав эталона, называют эталонной установкой.
32
Некоторые большие измерительные установки называют измерительными машинами.
Метод хрупких покрытий используют в основном для качественной оценки распределения напряжений и в случае приближенного опреде-
ления главных напряжений на большой площади. Наиболее простым хрупким покрытием является канифоль с добавкой 0,5–2% парафина (зарубежный аналог – покрытие типа Maybach). Порог чувствительности этого покрытия составляет 40–60 МПа. Другое покрытие (более чувствительное, но более сложное по составу) представляет собой резинат бария, который в в де раствора наносят на тщательно подготовленную поверхность (подобное покрытие, применяемое за рубежом, называется
"Stresscoat"). |
|
С |
|
Измерен е с л моментов. При испытаниях автомобилей часто |
|
необход мость определения сил и моментов, действующих на |
|
узлы автомоб ля. В |
ольшинстве случаев эти величины переменные, и |
для их рег страц |
следует применять записывающую аппаратуру. При |
возникаетизмерен с л моментов вращающихся деталей используют токосъем-
ные устройства. В ла ораторных условиях при проведении статических
измерен й пр меняют д намометры |
назначения. |
Для измерения сил выпускают целую серию устройств, например |
|
приборы типаобщегоУ, С, Р, ТДС отечественного производства или LC–KD, |
|
LT–KB японской фирмы "Kiowa". Чувствительный элемент в них – коль- |
|
цо, шарик или стержень. Сферический чувствительный элемент работает |
|
Д |
|
только на сжатие и не реагирует на боковые составляющие нагрузки. По |
|
экватору сферическогоАчувствительного элемента наклеивают тензорези- |
|
сторы, которые включают в измерительную схему. |
|
Типовая схема измерений неэлектрических величин электрическими |
|
методами включает первичный и промежуточный преобразователи и уст- |
|
|
И |
ройство для регистрации. Первичный преобразователь в зависимости от измеряемой величины создает электрический сигнал. Характерным примером такого преобразователя является тензорезистор, применяемый для измерения механических напряжений.
Самописцы, осциллографы, магнитографы и другие устройства предназначены для записи и хранения полученной информации в той или иной форме. Промежуточные преобразователи обеспечивают совместность работы первичных преобразователей и регистрирующих устройств. Примерами промежуточных преобразователей являются усилители, фильтры, переключающие устройства и т. д.
В некоторых случаях для использования электрических методов измерения применяют чувствительный элемент, который превращает одну
33
измеряемую величину в другую, удобную для фиксирования ее первичным преобразователем. Например, для измерения давления используют трубчатый чувствительный элемент, изменения напряжения в котором регистрируются тензорезисторами.
Общие требования, предъявляемые к измерительной аппаратуре.
Аппаратура, применяемая при испытаниях автомобилей, должна отвечать целому ряду требований: прежде всего, быть компактной, не бояться динамических перегрузок, вибрации, большой запыленности воздуха и в то же время обладать достаточной чувствительностью и разрешающей спо-
собностью. Требован е компактности вызвано отсутствием достаточного |
||||
места для размещен я аппаратуры на сиденье в салоне легкового или ка- |
||||
бине грузового автомоб лей. Необходимость установки приборов в сало- |
||||
С |
|
|
||
не |
каб не д ктуется недостаточной виброзащищенностью аппаратуры |
|||
|
или |
|
||
и высок м уровнем коле аний рамы и кузова. При выборе приборов для |
||||
дорожных |
спытан й также нео ходимо учитывать возможность питания |
|||
их от низковольтных |
сточников тока. |
|||
|
Размест в аппаратуру на |
, следует надежно закрепить |
||
приборы, |
сключая |
х произвольное перемещение. Особое внимание не- |
||
обходимо обрат ть на закрепление аккумуляторных батарей, используе- |
||||
мых в качестве автономных источников питания, когда питание от борто- |
||||
вой сети автомобиляавтомобилесоздает различные помехи, вызванные работой элек- |
||||
трооборудования. В некоторых случаях помехи могут быть вызваны изме- |
||||
рительными приборами, ра отающими от общего источника тока. Поэто- |
||||
му целесообразно применять специальные меры защиты или для каждого |
||||
прибора использовать отдельныйАисточник питания. |
||||
|
При установке аппаратуры в труднодоступном месте необходим |
|||
пульт дистанционного управления, с помощью которого можно управлять |
||||
приборами с рабочего места. Перед началом испытаний требуется рассчи- |
||||
тать или предварительными экспериментами определить уровень изме- |
||||
|
|
|
Д |
|
ряемых величин и их частоты, по которым выбирают коэффициент усиле- |
||||
ния, частотный диапазон, скорость записи и другие характеристики аппа- |
||||
ратуры. Все эти данные учитывают при подборе и настройке аппаратуры. |
||||
|
До начала и после проведения испытаний следует соответственно |
|||
определить и проверить характеристики всего измерительного комплекса: |
||||
|
|
|
|
И |
коэффициент калибровки, амплитудно-частотную характеристику, вели- |
||||
чину погрешности. |
|
|
||
|
Калибровку можно проводить при статическом и динамическом на- |
|||
гружении. При динамическом нагружении находят зависимость динами- |
||||
ческого коэффициента калибровки |
от частоты измеряемого процесса |
|||
Ω. |
Зная величины |
статического |
и ддинамического коэффициентов Кс |
|
|
|
|
|
34 |
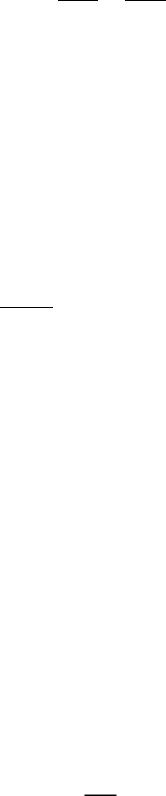
ид (Ω), устанавливают величину A (Ω), определяющую амплитудно-
частотную характеристику аппаратуры (АЧХ):
(Ω)= |
д(Ω) |
= |
д(Ω) |
(1) |
с |
(Ω) . |
|
По этой характеристике нетрудно определить рабочий диапазон частот Ωpaб измеряемых процессов, если задаться допустимым отклонением ±
А коэфф ц ента А (Ω) |
от единицы. При измерении процессов, частоты |
||||||||||||||
которых находятся за пределами рабочего диапазона частот, погрешность |
|||||||||||||||
будет связана с неравномерностью АЧХ. |
|
|
|
|
|
|
|
||||||||
лучайную погрешность исключают многократными измерениями |
|||||||||||||||
С |
|
|
|
|
|
|
|
|
|
|
|
|
|
|
|
одной той же вел ч ны. Результаты этих измерений статистически об- |
|||||||||||||||
рабатывают получают среднеарифметическую величину |
и ее средне- |
||||||||||||||
квадратичное отклонен е |
|
|
|
: |
|
|
|
|
|
|
|
|
|
|
|
|
|
|
|
|
|
|
|
|
|
|
|
|
|||
и |
|
|
|
|
|
|
|
|
|
||||||
|
|
∑ |
|
|
|
|
|
|
|||||||
|
|
|
|
∑ |
|
|
|
( |
) |
|
|
(2) |
|||
|
= |
|
; |
= |
, |
|
|||||||||
|
|
|
|
|
( |
) |
|
|
|
||||||
где n – число измерений; |
|
Ki |
– значение измеряемой величины в i-м из- |
||||||||||||
мерении. |
|
|
|
|
|
|
|
|
|
|
|
|
|
|
|
Зная зависимость плотности вероятностей отдельных измерений, |
|||||||||||||||
можно определить действительное значение измеряемой величины с за- |
|||||||||||||||
данной точностью. Это значит, что фактическое значение коэффициента |
|||||||||||||||
|
бА |
|
± |
|
отно- |
||||||||||
Кф с вероятностью Ф находится в доверительном интервале |
|
||||||||||||||
сительно средней величины |
(рис. 6, заштрихованная зона). |
|
|
||||||||||||
Тензометрирование. Измерение механических напряжений и свя- |
|||||||||||||||
занных с ними величин сил, моментов и давлений распространено при ис- |
|||||||||||||||
пытаниях автомобилей. ИспользованиеДпреобразователей резисторного |
|||||||||||||||
типа или тензорезисторов обеспечивает широкое внедрение метода тензо- |
|||||||||||||||
метрирования при различных видах испытаний автомобиля и его узлов. |
Наклеенный на деталь тензорезистор изменяет свое сопротивление в соот- |
||
ветствии с деформацией поверхностных слоев детали, что позволяет по- |
||
лучить необходимый электрический сигнал. |
И |
|
Коэффициент тензочувствительности тензорезистора |
||
ᵞ =35 |
, |
(3) |
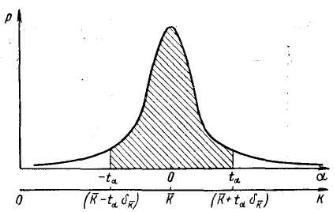
где R – изменение сопротивления тензорезистора; R – номинальное сопротивление тензорезистора; l – упругая деформация на длине тензорезистора; l – база тензорезистора.
С |
|
|
|
|
|
|
|
|
|
|
|
|
|
деформаций |
|
|
|
|
|
|
|
|
|||
|
бА |
|
||||||||||
|
Р с. 6. Плотность распределения вероятностей |
|
||||||||||
|
Связь упруг х |
|
|
|
с напряжениями в деталях определяется |
|||||||
законом Гука. В случае одноосного напряженного состояния эта зависи- |
||||||||||||
мость имеет в д |
|
|
|
|
|
|
|
|
|
|
|
|
|
|
|
|
|
= ε Е , |
|
|
(4) |
||||
где ε – относительная деформация; |
Е – |
модуль упругости материала; |
||||||||||
σ – напряжение. |
|
|
|
|
|
|
|
|
|
|
|
|
|
Подставив ε = l / l в выражение (4), получим |
|
||||||||||
|
|
|
|
|
= |
|
. |
|
|
(5) |
||
|
Для случая плоского напряженногоДсостояния зависимости между |
|||||||||||
напряжениями и деформациями вычисляют по следующим формулам: |
|
|||||||||||
|
|
= |
|
|
|
|
( |
|
+ εИ),; (6) |
|||
|
|
|
|
|
|
|||||||
|
|
|
|
|
|
|
||||||
где |
mах и min – главные |
напряжения; |
ε |
|
и ε – главные относительные |
|||||||
= |
|
|
( |
|
max+ min |
) |
|
деформации; µ – коэффициент Пуассона.
Для определения главных деформаций по величине и направлению применяют метод, основанный на использовании треугольных или прямоугольных соединений тензорезисторов (розеток), или метод хрупких по-
36
крытий. Сигналы от розеток регистрируются приборами. Обрабатывают результаты измерений с помощью формул и диаграмм.
Крутящие моменты валов определяют или по измеренной деформации вала или с помощью специального преобразователя крутящего мо-
мента. В некоторых случаях достаточно найти реакции опор стандартными измерителями сил. Измерить деформацию вала нетрудно с помощью Стензорезисторов, устанавливая их под углом 45° к оси. Для включения их
в измерительную цепь необходимо применить одно из рассмотренных токосъемных устройств. Этот способ не связан с какими-либо изменениями в исследуемой конструкц и. Однако не всегда возможна установка на вал
тензорезисторов токосъемных устройств. Кроме того, все эти приспособления, создаваемые для каждой конструкции отдельно, требуют тарировки оценки погрешностей.
Промышленные прео разователи момента работают в комплекте с типовой змер тельной аппаратурой и их характеристики не изменяются
Измеренбе давлен й. При испытаниях автомобилей часто приходится измерять давления жидкостей и газов. Для определения постоянных значений давления применяют жидкостные (пьезометры) и стрелочные
при переходе от одного о ъекта измерений к другому. Калибровку и оценку погрешностей проводят заранее, а результаты используют при испытании разл чных о ъектов.
(пружинные) манометрыА. В жидкостном манометре на столб жидкости, заключенный в тру ку, действует разность измеряемого и атмосферного давлений. В стрелочных манометрахДприменяют изогнутую манометрическую трубку (Бурдона), которая под действием разности давлений, стремясь выпрямиться, через рычажный механизм перемещает стрелку. Для
измерения переменных давлений применяют преобразователи с чувстви-
тельным элементом. При медленно изменяющемся давлении (с частотой не более 1 Гц) применяют преобразователь давленияИс чувствительным элементом в виде трубки Бурдона. На боковые поверхности трубки наклеены тензорезисторы, соединенные в полумостовую схему. Манометрическая трубка имеет значительную инерционность и поэтому не может реагировать на быстропротекающие процессы. Например, этими преобразователями измеряют давление жидкости в гидравлическом тормозном приводе.
Для измерения усилия буксировки преобразователи должны иметь такую частоту собственных колебаний, которая бы значительно превышала максимальные частоты измеряемых процессов. Наибольшую частоту собственных колебаний имеют преобразователи давления с пьезоэлектрическим чувствительным элементом. Их применяют при широком интерва-
37
ле изменения величин и частот давлений. Высокая жесткость пьезоэлектрических преобразователей обеспечивает частоту собственных колебаний 10–50 кГц. Это дает возможность использовать их для измерения давления в цилиндрах двигателя автомобиля. Следует отметить, что пьезоэлектрический преобразователь имеет ограниченный нижний диапазон частот и не может измерять постоянную составляющую процесса.
Измерение пути, скорости и относительного перемещения. Для измерения пути, пройденного автомобилем, может быть использован счетчик с пр водом от трансмиссии. Однако такой способ не совсем точен, так как колеса автомобиля проскальзывают за счет передачи сил и моментов. Кроме того, радиус качения колеса связан с нагрузкой, давле-
нием в ш не |
ее зносом. Поэтому при испытаниях автомобилей для из- |
С |
|
мерения |
скорости применяют так называемое "пятое колесо". Ко- |
пути |
|
лесо велос педного ли мотоциклетного типа установлено в вилке и шар- |
|
нирно соед нено с автомо илем. Такое крепление обеспечивает самоуста- |
борам относятсябАтахометры и тахоскопы. В тахометре под действием центробежных сил расходятся грузики, которые перемещают стрелку прибора. Тахоскопом определяют суммарный угол поворота вала за промежуток времени, заданный часовым механизмом. Эти приборы имеют высокую точность измерения, их применяют в качестве контрольных.
новку колеса при дв жен и автомо иля. Для получения безотрывного качения колеса его пр ж мают к дороге пружинами, а в некоторых случаях устанавл вают аморт заторы.
Для определен я угловых скоростей используют приборы меха-
нического, электрического или электронного типов. К механическим при-
Строботахометр позволяет измерить частоту вращения без непо- |
|
средственного контакта с вращающейся деталью. При совпадении частоты |
|
вспышек импульсной лампы и частоты вращения вращающаяся деталь |
|
воспринимается как неподвижная. При измерениях угловая скорость дета- |
|
Д |
|
ли должна быть постоянной, а частота вспышек плавно регулируется. В |
|
момент, когда вращающаяся деталь кажется неподвижной, по шкале при- |
|
бора определяют ее угловую скорость. |
|
Для измерения относительных перемещений узлов и деталей ав- |
|
томобиля используют различные устройства и приспособления. Так, на- |
|
|
И |
пример, в условиях статических испытаний нашли применение механические индикаторы часового типа с ценой деления 0,01 мм. При динамиче-
ских испытаниях тензорезисторы наклеивают на кольца и пластины, выбранные достаточно гибкими, но прочными, изготовленными из высокоуглеродистой стали.
38
Измерение температур. Измерительную аппаратуру выбирают в зависимости от диапазона рабочих температур исследуемого агрегата. Для определения температур до 120–150 °С используют аэротермометры. Эти приборы состоят из баллона, заполненного рабочим телом, капиллярной
трубки и стрелочного указателя. При погружении баллона в жидкость, температуру которой надо измерить, давление рабочего тела увеличивается и передается через капиллярную трубку к указателю, перемещая его стрелку.
Стоде измеряется время зрасходования некоторого количества топлива, определяемого взвеш ванием. В автоматических устройствах измерения
Измерен е расхода топлива. При испытаниях автомобиля для измерения расхода топл ва используют два метода: объемный и весовой. Весовой метод пр меняют при лабораторных испытаниях. При этом ме-
расхода топл ва весовым методом время прохождения заданной массы топлива определяется электронным секундомером с помощью фотоэлек-
трических |
, контролирующих положение весов. Запол- |
нение пр бора |
расходом топлива производится электромаг- |
управление |
|
нитными клапанами. При использовании этого метода на результатах из- |
|
мерений не сказываются погрешности, связанные с изменением плотности |
|
топлива при изменении температуры. |
|
Все большеепреобразователейраспространение получают измерительные приборы, |
|
связанные со спутниковым позиционированием объекта. Они дают воз- |
|
можность определять скорость, время и расстояние перемещения. Специ- |
|
альные компьютерные программы позволяют регистрировать большой |
|
объем информации, обрабатыватьАее и получать готовые результаты в ре- |
|
альном времени. Современные автомобили и их системы оснащены мно- |
|
гочисленными |
встроенными контрольно-измерительными приборами и |
датчиками и позволяют снимать необходимуюДинформацию с помощью специальных разъёмов и даже удаленно. И
39