
- •Раздел 1. ВИДЫ ИСПЫТАНИЙ И УСЛОВИЯ ИХ ПРОВЕДЕНИЯ
- •Тема 1.1. Виды испытаний
- •Тема 1.2. Условия проведения испытаний
- •Раздел 2. ИЗМЕРЕНИЯ ПРИ ИСПЫТАНИЯХ
- •Тема 2.1. Методика планирования и проведения испытаний
- •Раздел 3. ИЗМЕРИТЕЛЬНЫЕ УСТРОЙСТВА, КОМПЛЕКСЫ И СТЕНДЫ ДЛЯ ПОЛУЧЕНИЯ ПАРАМЕТРОВ АВТОМОБИЛЯ И ШИН
- •Тема 3.1. Определение углов поворотов управляемых колес автомобиля, углов уводов и боковых реакций
- •Тема 3.2. Определение жесткости рулевого управления
- •Тема 3.4. Комплекс исследований шума и вибрации
- •Тема 3.6. Теплотехнический комплекс
- •Тема 4.1. Активная и пассивная безопасность автомобиля
- •Тема 4.2. Полигонные и лабораторные испытания кузовов и кабин
- •Тема 4.3. Правила проведения краш-тестов
- •Тема 4.4. Испытания рулевых управлений
- •Тема 4.5. Аэродинамические испытания
- •Раздел 5. СТЕНДОВЫЕ ИСПЫТАНИЯ АВТОМОБИЛЕЙ И ИХ АГРЕГАТОВ
- •Тема 5.1. Стенды для диагностирования технического состояния автомобилей. Виды стендов для испытаний автомобиля
- •Раздел 6. ИМИТАЦИОННЫЕ ИСПЫТАНИЯ
- •Тема 6.1. Математическое испытание пространственной модели для определения показателей устойчивости и управляемости автомобиля с учетом действия аэродинамических сил и моментов
- •Тема 6.3. Математическое моделирование подвески АТС с учетом особенностей работы гидроамортизатора
- •Контрольные вопросы
- •Контрольные задания
- •Список рекомендуемой литературы
Раздел 5. СТЕНДОВЫЕ ИСПЫТАНИЯ АВТОМОБИЛЕЙ И ИХ АГРЕГАТОВ
Тема 5.1. Стенды для диагностирования технического состояния автомобилей. Виды стендов для испытаний автомобиля
СМетоды диагностирования технического состояния автомобиля, его агрегатов узлов. Комплексные и простые стенды для диагностирования автомоб лей. Стенды для испытаний автомобилей на динамич-
рационнымность, на в бропрочность. Режимы стендовых испытаний.
Понят е " спытательный стенд" в различных отраслях трактуется по-разному. Так, напр мер, в технике вибрационных испытаний под вибстендомбАпон мается ви рирующий стол, на который устанавливается спытуемое зделие, а весь комплекс средств управления и из-
мерения вместе со столом называют вибрационной установкой. Стенд для испытан я дв гателя, нао орот, включает в себя весь комплекс средств, необход мых для проведения этих испытаний. Имеются большие разноречия в толковании этого термина и в зарубежной терминологии. Поскольку термин "испытательное о орудование" как средство испытаний для воспроизведения условий испытаний полностью охватывает все толкования понятия "испытательный стенд", то распространенный термин "стендовые испытания" определяетсяДкак испытания, проводимые на испытательном оборудовании.
Испытания на стендах статического нагружения. спытание несущей конструкции под действием статической нагрузки на специальных стендах является наиболее простым и достаточно точным методом проверки ее прочности и жесткости. Такие испытанияИпозволяют оценить нагруженность элементов конструкции, выявить ослабленные (перегруженные) участки и соединения, сопоставить жесткости на изгиб и кручение различных несущих систем, изучить влияние отдельных элементов конструкции на ее общую жесткость, т. е. можно получить информацию о достоинствах и недостатках рамы (кабины, кузова), эффективности внесенных в конструкцию изменений, возможных путях повышения прочности несущей системы.
Опыт исследований нагрузочных режимов кузовов легковых автомобилей показывает, что при статических испытаниях несущих кузовов легковых автомобилей наиболее обоснованы два режима нагружения:
75
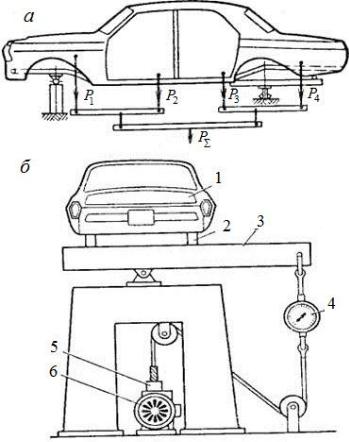
а) изгиб кузова под действием нагрузки, имитирующей реальное распределение (по длине автомобиля) нагрузки от подрессоренных масс, пассажиров и багажа с коэффициентом перегрузки 2,0–2,5 для автомобилей, работающих на дорогах с усовершенствованным покрытием, и с коэффициентом перегрузки 2,5–3,5 для автомобилей, работающих в тяжелых дорожных условиях;
б) закручивание кузова моментом, составляющим 0,7–0,9 максимально возможного для данного автомобиля при одном вывешенном колесе, и одновременно зг б с коэффициентом перегрузки 1,0–1,5 (условия соответствуют случаю переезда автомобилем кювета под углом к его оси).
Уровень напряжен й в элементах кузова при действии указанных
нагрузок не должен дост |
гать предела текучести материала. Для рам гру- |
С |
|
зовых автомоб лей рекомендованы такие же режимы, но коэффициент |
|
при действ |
изги ных нагрузок (режим а) принимают рав- |
ным 3,0–4,5 вв ду олее тяжелых условий эксплуатации и большей жест- |
|
кости подвесок. |
|
перегрузки |
|
бА |
|
|
Д |
|
И |
Рис. 28. Схема нагружения кузова при статических испытаниях: а – на изгиб; б – на кручение
На рис. 28 а представлена схема нагружения кузова (рамы) легкового автомобиля при статических испытаниях на изгиб.
76
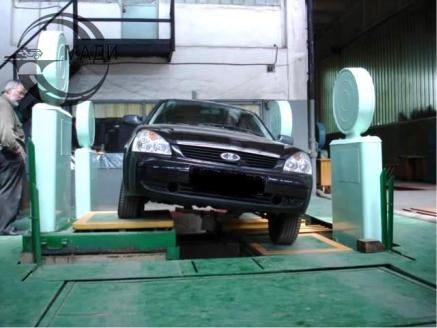
Суммарное усилие РΣ с помощью системы рычагов раскладывается на четыре составляющие Р1–Р4, которые имитируют воздействие на несущую систему автомобиля четырех основных сосредоточенных масс: двигателя в сборе со сцеплением и коробкой передач, переднего сиденья и
двух сидящих на нем пассажиров, заднего сиденья и трех сидящих на нем |
||||||
пассажиров, бензобака с топливом и багажа. Суммарное усилие РΣ = Р1+ |
||||||
С |
|
|
|
|
||
+Р2 |
+ Р3 |
+ Р4 в каждом конкретном случае определяют исходя из характе- |
||||
ристик указанных масс и принимаемого коэффициента перегрузки. При |
||||||
испытан ях кузова легкового автомобиля на изгиб на стенде можно ис- |
||||||
пользовать распределенную по длине салона вертикальную нагрузку |
||||||
нагружения |
|
лабораториях |
компании "Форд" |
|||
4000–4450 Н. В сследовательских |
||||||
( ША) проверка конструкции на изгиб и кручение производится в стен- |
||||||
довых услов ях путем |
|
кузова изгибной нагрузкой, соответст- |
||||
вующей двукратной перегрузке, закручиванием его моментом 3000 Н·м. |
||||||
|
|
бА |
|
|||
|
Жесткость несущей системы на кручение проверяют при нагруже- |
|||||
нии |
ее |
скруч вающ м |
моментом |
измерением |
угла закручивания |
(рис. 28, б). С этой целью кузов 1 на фальшрессорах 2 устанавливают на подвижных опорах – передней скользящей и задней качающейся в поперечной плоскости. К консольной части задней опоры 3 прилагают усилие (измеряемое динамометром 4), вызывающее поворот опоры относительно продольной оси кузова. Таким о разом, на конструкцию действует скручивающий момент. Усилие передается от электродвигателя 6 через редук-
тор 5 с большим передаточным числом. Д И
Рис. 29. Стенд для измерения жесткости кузова автомобиля
77
Одной из задач статических испытаний является определение жесткости конструкции. Прогиб основания и деформации проемов кузова или кабины в момент действия максимальных изгибающих или скручивающих нагрузок не должны превышать допустимых величин, определяемых зазорами между силовыми элементами дверных проемов и соответствующими поверхностями дверей. Дополнительные ограничения на величину допустимых деформаций кузовных элементов могут быть связаны с конструкцией дверных замков, так как самопроизвольное открывание дверей при действии нагрузок на кузов (раму) недопустимо.
На спец альных стендах (рис. 29) можно получать оптимальные ус- |
|
ловия для проведен я тензометрических исследований несущих систем и |
|
кузовов. Для получен я представления о напряженном состоянии всех эле- |
|
С |
измерения в очень большом числе точек. |
ментов необход мо |
|
проводить |
|
Практика тензометр ческ х испытаний показывает, что устанавливаемое |
|
число тензорез сторов может достигать на рамах грузовых автомобилей |
|
200–500, а на кузовах легковых |
и автобусов – до 1500. |
Тема 5.2. Назначен я, о ъекты и условия проведения испытаний |
|
Тематическиеавтомобилейиспытания на надежность. Методы ускоренных ис- |
|
пытаний в реальных эксплуатационных условиях. Схемы стендов для ис- |
|
пытаний. |
|
На рис. 30 показанаАустановка кузова легкового автомобиля для ус- |
|
талостных испытаний по указанной методике на динамическом стенде. |
|
|
Д |
Принцип испытаний деталей арматуры заключается в воспроизведении на |
|
стендах условий работы этих деталей, причем предварительно устанавли- |
|
|
И |
вают базовое число циклов, которое должен выдержать испытываемый |
|
объект. |
|
В настоящее время накоплен большой опыт проведения подобных испытаний. В лабораторных условиях широко используются гидравлические нагружатели и приводные механизмы. Например, на специальном стенде непрерывно производят открывание и закрывание дверей автомобиля, крышки багажника и капота, точно моделируя воздействие руки человека. Петли и замки дверей должны, как минимум, выдерживать 100 тыс. циклов открывания и закрывания, капота – 5 тыс. циклов, а крышки багажника – 20 тыс. циклов.
78
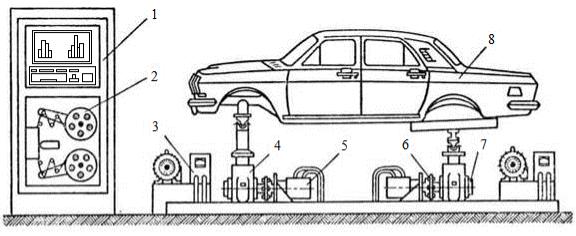
С |
|
|
дроусилитель |
|
|
Рис. 30. тенд для спытан й автомобильного кузова на усталость: 1 – АСУ стенда; |
||
2 – перфолента, задающая углы поворота роторов гидроусилителей момента; |
||
3 – насосная станц я, п тающая гидроусилитель; 4 – кривошипно-шатунный |
||
бА |
||
нагружатель; 5 |
– г |
момента; 6 – соединительная муфта; |
7 – контрольное устройство (датчик о ратной связи); 8 – испытываемый кузов |
||
Аналог чные |
спытания проходят и замки зажигания. Упругие эле- |
менты с ден й в эксплуатации находятся под действием динамических нагрузок. Надежность сидений оценивают, например, по результатам 200 тыс. циклов нагружений их манекеном массой 135 кг.
Испытания в дорожных условиях проводят на одном полностью комплектном автомо иле или на нескольких его образцах. Испытания кузовов и кабин на надежность, долговечность в условиях эксплуатации характеризуются переменной нагрузкойД, действующей на кузов автомобиля, влиянием коррозии на детали и другими факторами. Величина пробега автомобиля при эксплуатационных испытаниях должна быть максимально возможной. Обычно ее принимают равной расчетному пробегу автомобиля до капитального ремонта. По окончании испытаний проводят обследование несущей системы (кабины) и делают заключениеИо ее техническом состоянии. Пробеговые испытания автомобилей при движении по заданным маршрутам дорог общего пользования с загрузкой балластом до номинальной грузоподъемности позволяют исключить простои и холостые пробеги и повысить точность учета условий работы автомобиля.
Одним из видов исследований в дорожных испытаниях кузовов и кабин является определение реальных нагрузочных режимов. Оценивать нагруженность несущей системы в целом и отдельных ее элементов можно различными способами. Наиболее часто измеряют динамические напряжения в различных точках конструкции с помощью тензорезисторов, показания которых записывают на ленту светолучевого осциллографа или многодорожечного магнитографа.
79
Ускоренные испытания на усталостную прочность деталей ходовой части, рам, кузовов и кабин автомобилей проводят на дорогах с покрытием из крупного булыжника, гребенчатых, брусчатых на бетонном основании (типа "бельгийская мостовая") и др. Применяют также искусственно созданные ухабистые дороги или треки со сменными неровностями, которые вызывают сильные перекосы (скручивание) несущих систем автомобилей, и повышенные изгибающие нагрузки, действующие на продольные силовые элементы.
Новый "Volvo FH" подвергся целому ряду испытаний на качество. Методика тест рован я включала испытания, проведение замеров и
улучшен й. |
н х: расчеты и моделирование, стендовые испытания, |
||
проверка |
пр емка компонентов, тестирование автомобиля, моделирова- |
||
Среди |
топлива, камеры с высокой и низкой |
||
ние шума, |
расчет |
|
температурой, грязевые тесты, тормозные испытания, форсированные испытания на выносл вость, испытания на надежность, тест-драйвы в условиях экстремально холодного жаркого климата, полевые испытания в
условиях коммерческ х перевозок с клиентами, тестирование на эконо- |
|
экологичности |
|
мию топл ва, проверка управляемости, оценка комфорта водителя. |
|
Сначала были проведены индивидуальные испытания отдельных уз- |
|
лов, таких как шасси, ка ина система электрооборудования. После их |
|
приемки началосьавтомобиляиспытание |
в целом. Один из опытных по- |
лигонов, используемых "Volvo Trucks" для тестирования своих грузови- |
|
ков, располагается в г. Кируна, в северной части Швеции. Зимой здесь |
|
была зафиксирована рекордно низкая температура –44 °C. Эти испытания |
|
связаны с деятельностьюАводителей: работа, сон и отдых в кабине, про- |
|
верка климата, комфорта и запуска двигателя в зимнее время. |
|
Во время испытаний каждый грузовик прошел не менее 20 000 км по |
|
морозу, при котором одна из самых больших проблем заключалась в том, |
|
что все компоненты грузовика – от стальных деталей до систем электро- |
|
Д |
|
оборудования – становятся хрупкими. Специалистам предстояло разрабо- |
|
тать компоненты, способные выдерживать такие погодные условия без |
|
выхода из строя. |
|
Различные тесты проводились на испытательном полигоне в Хелер- |
|
де. Данный тестовый режим соответствует 10 годам и 1 250 000 км пробе- |
|
|
И |
га автомобиля в условиях реальной эксплуатации. Тест предполагал вож- |
|
дение в экстремальных дорожных условиях, включая передвижение по |
холмам с углом наклона от 10 до 20%, преодоление участков с выбоинами, колейным износом дороги, брусчаткой, лужами и канавами. Процедура испытания включала и другие элементы, например, многократное открывание и запирание дверей.
80
Одним из самых тяжелых видов форсированных испытаний на выносливость является вождение грузовика на треке для определения продолжительности срока службы. При этом грузовик проходит те же препятствия, с которыми он столкнется в стандартных дорожных условиях, но в течение ограниченного количества времени. За счет движения кругами по полигону с многочисленными сложными препятствиями испыта-
Стельный процесс значительно ускоряется.
Еще более форсированное испытание было проведено в лаборатории "Volvo Trucks" на спец альном стенде, где грузовик непрерывно трясли в течение восьми недель. В пересчете на среднего клиента такой износ со-
бованиямответствует пробегу более чем 1 млн км.
Результаты всех проверочных испытаний анализируются, что позволяет разобраться в пр ч нах отказов и разработать надежные технические решения. Вновь разра отанные решения подвергаются новому испытанию. ДанныйбАпроцесс продолжается до тех пор, пока замеры испытываемых комплектующ х не начнут соответствовать всем предъявляемым тре-
(В део 8).
Д И
81