
- •ВВЕДЕНИЕ
- •1. ЦЕЛЬ И ЗАДАЧИ КУРСОВОЙ РАБОТЫ
- •3. РАСЧЁТНАЯ ЧАСТЬ КУРСОВОЙ РАБОТЫ
- •3.1. Разработка технологии восстановления детали
- •3.2. Проектирование и расчёт приспособлений
- •4. ТРЕБОВАНИЯ К ОФОРМЛЕНИЮ КУРСОВОЙ РАБОТЫ
- •4.1. Содержание пояснительной записки
- •4.3. Требования к оформлению графической части
- •БИБЛИОГРАФИЧЕСКИЙ СПИСОК
- •ПРИЛОЖЕНИЕ
- •Приложение 1
- •Приложение 2
- •Приложение 3
- •Приложение 4
- •Приложение 5
эскиза на технологический процесс или на несколько операций допускается обрабатываемые поверхности детали не обводить линией толщиной 2S. Технические требования помещают на свободном поле карты справа от изображения эскиза или под ним и излагают по ГОСТ 2.316–68. Если изображение на эскизе относится к нескольким операциям технологического процесса, то номера этих операций
СибАДИуказывают над изображением детали и подчеркивают. Допускается не указывать все номера операций, если изображение относится к нескольк м последовательным операциям. Например, если изображен е относ тся к операциям 10, 15, 20, 25, то можно записать
10–25.
Если на поле карты содержатся несколько отдельных эскизов для различных операц й технологического процесса, то над каждым эскизом указывают номер операции и подчеркивают. Пример оформлен я карты эскизов приведен на рис. 4. Ведомость оборудован я оснастки по технологическому процессу в целом оформляют на формате А4 по форме 14 (рис. 5). Запись оборудования и оснастки в ведомости производят в следующей последовательности:
– оборудование;
– приспособления;
– режущий инструмент;
– измерительный инструмент;
– слесарно-монтажный инструмент.
Запись оборудования и оснастки производят с указанием полного наименования и обозначения по ГОСТу или ТУ.
3.2. Проектирование и расчёт приспособлений
Приспособление – это составная часть технологического оснащения процессов механической обработки, сборки или ремонта. Основное назначение приспособлений – установка заготовки или детали на станке для механической обработки, т. е. базирование закрепление. К дополнительным функциям приспособлений относятся: направление режущего инструмента; базирование контрольно-измерительных приборов; механизация и автоматизация зажима; увеличение жесткости при установке заготовки; изменение положения заготовки вместе с приспособлением и другие.
37

|
3.2.1. Классификация приспособлений |
|
||
По степени специализации приспособления подразделяют на |
||||
универсальные и специальные. |
|
|
|
|
|
3.2.2. Состав приспособления |
|
|
|
Приспособление состоит из следующих основных элементов: |
||||
|
- корпус; |
|
|
|
|
- баз рующ е (установочные) элементы; |
|
|
|
|
- заж мные устройства; |
|
|
|
|
- пр вод. |
|
|
|
Знач тельную роль в приспособлении играют установочные |
||||
элементы. Установочные элементы (или опоры) делятся на основные |
||||
вспомогательные. Основные опоры для плоских баз заготовки – |
||||
типа палец (р с. 6) ли пластина, для внутренних цилиндрических баз |
||||
(отверст й) – ц л ндр ческий палец (рис. 7) или оправка (рис. 8), для |
||||
наружных ц л ндр ческих аз – призмы (рис. 9). |
|
|
||
|
Рис. 6. Опоры типа «палец» |
|
|
|
|
Рис. 7. Цилиндрический палец |
|
|
|
По технологическому процессу приспособления подразделяют на: |
||||
станочные; сборочные; контрольно-измерительные; ремонтные. |
||||
СибАДИ |
||||
По |
технологическому |
оборудованию, |
для |
которого |
проектируются, они подразделяются: для токарных станков; для |
||||
фрезерных станков; для шлифовальных станков и т.д. |
|
38

Äóáë. |
|
|
|
|
ГОСТ 3,1118-82 Форма 2 |
|
|
|
|
|
|
Âçàì. |
Захаров |
12.02.02 |
Роспись |
|
|
Разроб. |
|
|
|||
Ïðîâ. |
|
|
|
|
|
Н.контр. |
|
|
|
Фланцевая втулка |
|
|
|
|
À |
1 |
|
|
3 |
0.015 |
|
0,03 |
|
|
|
|
|
||
|
|
|
|
+0,006 -0,018 |
1.Твердость |
Ð |
|
|
|
обробатываемой |
|
è |
|
|
|
Ç15,896 |
поверхности 44...52HRC 3 |
ñ |
|
|
|
||
. |
|
|
|
|
|
4 |
|
|
|
2.*Размер для справок. |
|
|
|
|
|
||
|
|
|
|
3.Допуск овальности и |
|
|
|
|
|
|
конусообразности |
|
|
|
R2 |
|
поверхности А не более |
|
|
|
|
0,007ìì |
|
|
|
|
|
|
|
|
|
|
17* |
|
|
ÊÝ/ÎÊÍ |
|
|
|
|
|
|
|
Рис. 4. Карта эскизов |
|
|
|
ИС |
|||||
|
|
39 |
|
|
|

|
|
|
|
|
|
|
|
|
|
|
|
|
|
|
|
|
||
|
|
|
Разраб. |
СибАДИ |
|
|
Литера |
|||||||||||
|
|
|
|
Фамилия |
Подпись Дата |
|
|
Наименование детали |
|
Обозначение |
|
|||||||
Организация - |
|
Пров. |
|
|
|
|
|
|
Ведомость оборудования |
Восстановление |
|
|
|
|
||||
разработчик |
|
Н. контр. |
|
|
|
|
|
|
|
оснастки |
|
|
|
|
|
|
|
|
N |
|
Наименование |
|
|
Обозначение |
|
N |
|
На менован е |
|
Обозначение |
|||||||
стр. |
|
|
|
|
|
|
|
|
стр. |
|
|
|
|
|
|
|
|
|
|
|
|
|
|
|
|
|
|
|
|
|
|
|
|
|
|
|
|
|
|
|
|
|
|
|
|
|
|
|
|
|
Листов |
|
Лист |
|
||
|
|
|
|
|
|
|
|
|
|
|
|
|
|
|
|
|
|
|
|
|
|
|
|
|
|
Рис. 5. Ведомость оборудования оснастки. Форма 14 |
|
|
|
|
40

Приспособления многократного применения делятся на: универсально- |
сборные (УСП); сборно-разборные (СРП); универсальные безналадочные |
(УБП); неразборные специальные (НСБ); универсальные наладочные |
(УНП); специализированные наладочные (СНП). |
Рис. 8. Цилиндрическая оправка |
a |
D |
Рис. 9. Призмы |
СибАДИ |
Вспомогательные опоры подразделяют на регулируемые (рис. 10) |
и самоустанавливающиеся. При этом заготовку устанавливают на |
основные опоры, а затем подводят вспомогательные опоры. |
41

|
|
|
Заготовка |
|
|
|
|
|
Регулируемый палец |
|
|
|
|
|
|
Гайка фиксации |
|
|
|
|
Корпусрпус прприспспосîсоблениялени |
|
|
|
Р с. 10. Регулируемая вспомогательная опора |
|
|||
|
Заготовка |
Зажим |
Регулируемая стойка |
|
|
|
Стяжной болт |
|
|
|
|
|
Рис. 11. Рычажное зажимное устройство |
|
|||
Зажимные устройства приспособлений предназначены для |
|||||
обеспечения надежного закрепления заготовки. Они отличаются |
|||||
многообразием |
конструктивных |
решений, |
наиболее |
часто |
|
используются рычажные устройства (рис. 11). |
|
|
|||
В приспособлениях, предназначенных для направления |
|||||
Сибинструмента, часто используютАДкондукторные втулкиИ(рис. 12). |
|||||
Последние обеспечивают направление сверл и разверток. |
|
||||
Корпуса приспособлений изготовляют литьем из чугуна СЧ 12, а |
|||||
также сварные из проката или сборные из нормализованных деталей. |
|||||
|
|
42 |
|
|
|

|
|
|
Фиксация втулки |
|
|
|
|
болтом |
|
|
Рис. 12. Кондукторная втулка |
|
||
3.2.3. Этапы расчета и проектирования станочных |
||||
|
приспособлений |
|
|
|
Проект рован е станочных приспособлений можно разбить на |
||||
следующ е основные этапы: |
|
|
|
|
1. Эск зная компоновка: |
|
|
|
|
- составляется расчетная схема: |
|
|
||
- определяются число, вид |
конструкция установочных и |
|||
зажимных устройств; |
|
|
|
|
- определяется способ закрепления приспособления на станке. |
||||
2. Расчет приспособления: |
|
|
|
|
- расчет составляющих сил резания; |
|
|
||
- расчет сил зажима заготовки; |
|
|
||
- расчет силового привода; |
|
|
|
|
- расчет точности приспособления. |
|
|
||
3. Разработка чертежа общего вида или сборочного чертежа. |
||||
|
3.2.4. Расчет составляющих силы резания |
|
||
Расчет составляющих силы резания необходим для последующего |
||||
определения силы закрепления заготовки. Разложение силы резания |
||||
СибАДИна составляющие производят в зависимости от технологической |
||||
операции |
механической |
обработки: |
точение, |
сверление, |
фрезерование, шлифование и т.д. Для примера рассмотрим основные |
||||
методы механической обработки: точение, сверление, рассверливание |
||||
и зенкерование, фрезерование [7, 8]. |
|
|
43

|
|
Расчет составляющих силы резания при точении |
|
||||||||||
|
|
|
|
стальной заготовки |
|
|
|
|
|||||
|
|
|
n |
|
|
|
|
|
|
|
n |
|
|
|
|
Pz |
|
Py |
|
|
|
Px |
|
|
|
|
|
|
|
|
|
|
|
|
|
Py |
|
|
|
||
|
|
|
|
S |
|
|
|
|
|
|
|||
|
|
|
|
|
|
|
|
|
|
|
|
||
Рис.13. |
хема с л резан я при точении: PZ – тангенциальная составляющая силы |
||||||||||||
резан я; |
PY – рад альная составляющая силы резания; |
P X – осевая составляющая |
|||||||||||
|
|
|
|
|
силы резания |
|
|
|
|
|
|||
Любая з составляющих силы резания (Н) (рис.13) рассчитывается |
|||||||||||||
по формуле |
Pz,y,x 10 C p tx S y V n K p , |
|
|
(39) |
|||||||||
|
|
|
|
|
|||||||||
где CP – постоянная для данных табличных условий резания (табл. |
|||||||||||||
16); t |
– глубина резания, мм; |
S |
– |
подача, |
мм/об; V |
– скорость |
|||||||
резания, |
м/мин; |
x,y, n |
– показатели |
степени |
(см. табл. |
16); |
K P – |
||||||
поправочный коэффициент, учитывающий фактические условия |
|||||||||||||
резания, |
K p K mp K p K p K p K rp (табл. 17). |
|
|
|
|
||||||||
|
|
|
|
|
|
|
|
|
|
|
|
Таблица 16 |
|
|
|
Значения постоянной резания |
степеней для данных условий |
|
|||||||||
|
|
PZ |
|
|
|
|
PY |
|
|
|
PX |
|
|
CP |
x |
y |
n |
CP |
x |
|
y |
n |
CP |
x |
y |
n |
|
300 |
1,0 |
0,75 |
-0,15 |
243 |
0,9 |
0,6 |
-0,3 |
339 |
1,0 |
0,5 |
-0,4 |
||
СиЗначение коэффициентабА: ДИ |
|||||||||||||
|
|
|
|
K mp |
|
|
|
|
|
|
|
|
|
|
|
|
|
|
в |
n |
|
при |
n 0,75 . |
|
|
|
|
|
|
|
|
K mp |
750 |
|
|
|
|
|
|||
|
|
|
|
|
|
|
|
|
|
|
|
|
44
|
|
|
Значения коэффициентов K p ,K p ,K p ,K rp |
|
Таблица 17 |
|||||
|
|
|
|
|
|
|||||
|
|
|
|
|
|
|
|
|
|
|
Параметр резца |
Величина |
Обозначение |
|
Составляющая силы резания |
|
|||||
|
|
|
|
|
|
|||||
|
PZ |
PY |
|
P X |
|
|||||
|
|
|
|
|
|
|
|
|||
Главный угол в |
45 |
K p |
|
1,0 |
1,0 |
|
1,0 |
|
||
плане |
|
|
|
|
||||||
Передн й |
|
0 |
K p |
|
1,1 |
1,4 |
|
1,4 |
|
|
угол |
|
|
|
|
||||||
Угол наклона |
|
|
K p |
|
|
|
|
|
|
|
главного лезв |
я |
–5 |
|
1,0 |
0,75 |
|
1,07 |
|
||
|
|
|
|
|
|
|
|
|
|
|
|
|
|
|
|
|
|
|
|
|
|
Радиус при |
|
0,5 |
K rp |
|
0,87 |
0,66 |
|
1,0 |
|
|
вершине r,мм |
|
|
|
|
|
|
|
|
|
|
|
Значен я всех коэффициентов и показателей степени для других |
|||||||||
материалов |
резцов пр ведены в табл. 9, 10, 22, 23 [2]. |
|
|
|
||||||
|
Расчет составляющих силы резания при сверлении, |
|||||||||
При сверлении |
рассверливании и зенкеровании |
|
|
|
||||||
|
M кр 10 C m Dq S y K Р ; |
(40) |
||||||||
|
|
|
|
|||||||
|
|
|
|
Po 10 C p Dq S y K Р . |
(41) |
|||||
|
При рассверливании и зенкеровании |
|
|
|
|
|||||
|
|
|
M кр 10 C m Dq t x S y K Р |
; |
(42) |
|||||
|
|
|
Po 10 C p t x S y K Р, |
|
(43) |
|||||
где D – диаметр сверла, мм; t – |
глубина резания, |
t=0,5D при |
СсверленииибАД, t=0,5(D–d) при рассверливании; S – подачаИсверла, мм/об., в зависимости от диаметра и материала сверла принимают S= 0,1– 0,5 более (до 0,8); CP, Cm – постоянные (табл. 18); x, y, z – значения
постоянных степеней
(табл. 18); KP – коэффициент, учитывающий условия работы (табл. 19).
45

Ìêð (Í·ì)
|
|
|
|||||||||||||||||||||||
СибАДИ |
|||||||||||||||||||||||||
|
|
|
|
|
|
|
|
|
Po (H) |
|
|
|
|
|
|
|
|
|
|
|
|
||||
|
|
Рис. 14. хема с л резан я при сверлении: M kp |
– момент крутящий; PO – осевая сила |
||||||||||||||||||||||
|
|
|
|
Значен |
я постоянных резания |
показателей степеней |
Таблица 18 |
||||||||||||||||||
|
|
Обраба- |
|
На ме- |
|
|
|
|
|
|
|
|
|
Коэффициенты |
|
|
|
|
|
|
|
||||
|
|
тывае- |
|
нован е |
|
Материал |
|
|
M кр |
|
|
|
|
|
Po |
|
|
|
|||||||
|
|
мый |
|
опера- |
|
|
сверла |
|
|
|
|
|
|
|
|
|
|
||||||||
|
|
материал |
|
ции |
|
|
|
|
Cm |
|
q |
|
|
x |
|
y |
C p |
q |
|
|
x |
y |
|
|
|
|
|
|
|
Сверле- |
|
Быстрор. |
0,0345 |
|
2 |
|
|
- |
|
0,8 |
68 |
1,0 |
|
|
- |
0,7 |
|
|
|||
|
|
|
|
ние |
|
|
сталь |
|
|
|
|
|
|
|
|
||||||||||
|
|
Сталь |
|
|
|
|
|
|
|
|
|
|
|
|
|
|
|
|
|
|
|
|
|||
|
|
|
|
|
|
|
|
|
|
|
|
|
|
|
|
|
|
|
|
|
|
|
|
|
|
|
|
констр. |
|
Рассвер- |
|
|
|
|
|
|
|
|
|
|
|
|
|
|
|
|
|
|
|
|
|
|
|
в 750 |
|
|
|
|
|
|
|
|
|
|
|
|
|
|
|
|
|
|
|
|
|
|
|
|
|
|
ливание, |
|
Быстрор. |
0,09 |
|
1 |
|
|
0,9 |
0,8 |
67 |
- |
|
|
1, |
0,6 |
|
|
|||||
|
|
МПа |
|
зенкеро- |
|
|
сталь |
|
|
|
|
|
2 |
5 |
|
|
|||||||||
|
|
|
|
|
|
|
|
|
|
|
|
|
|
|
|
|
|
|
|
||||||
|
|
|
|
вание |
|
|
|
|
|
|
|
|
|
|
|
|
|
|
|
|
|
|
|
|
|
|
|
|
|
|
|
|
|
|
|
|
|
|
|
|
|
|
|
|
|
|
|
|
|
|
|
|
|
|
|
|
|
|
|
|
|
|
|
|
|
|
|
|
|
|
|
Таблица 19 |
|||||
|
|
Значения K p – коэффициента, учитывающего условия обработки |
|
|
|
||||||||||||||||||||
|
|
Вид обработки |
|
|
|
Составляющая силы |
|
|
|
K p |
|
|
|
|
|
|
|||||||||
|
|
|
|
|
|
резания |
|
|
|
|
|
|
|
|
|
|
|
|
|
|
|||||
|
|
|
|
|
|
|
|
|
|
|
|
|
|
|
|
|
|
|
|
|
|
|
|
||
|
|
|
|
|
|
|
|
|
|
|
|
|
|
|
|
|
|
|
|
|
|
|
|
|
|
|
|
Сверление |
|
|
|
|
|
M кр |
|
|
|
|
|
|
|
|
1,15 |
|
|
|
|
|
|
||
|
|
|
|
|
|
|
|
|
|
|
|
|
|
|
|
|
|
|
|
|
|
|
|
||
|
|
|
|
|
|
|
Po |
|
|
|
|
|
|
|
|
1,0 |
|
|
|
|
|
|
|||
|
|
|
|
|
|
|
|
|
|
|
|
|
|
|
|
|
|
|
|
|
|
|
|||
|
|
|
|
|
|
|
|
|
|
|
|
|
|
|
|
|
|
|
|
|
|
|
|
|
|
|
|
Зенкерование |
|
|
|
|
|
M кр |
|
|
|
|
|
|
|
|
1,3 |
|
|
|
|
|
|
||
|
|
|
|
|
|
|
|
|
|
|
|
|
|
|
|
|
|
|
|
|
|
|
|
||
|
|
|
|
|
|
|
Po |
|
|
|
|
|
|
|
|
1,2 |
|
|
|
|
|
|
|||
|
|
|
|
|
|
|
|
|
|
|
|
|
|
|
|
|
|
|
|
|
|
|
|||
|
|
|
|
|
|
|
|
|
|
|
|
|
|
|
|
|
|
|
|
|
|
|
|
|
|
46
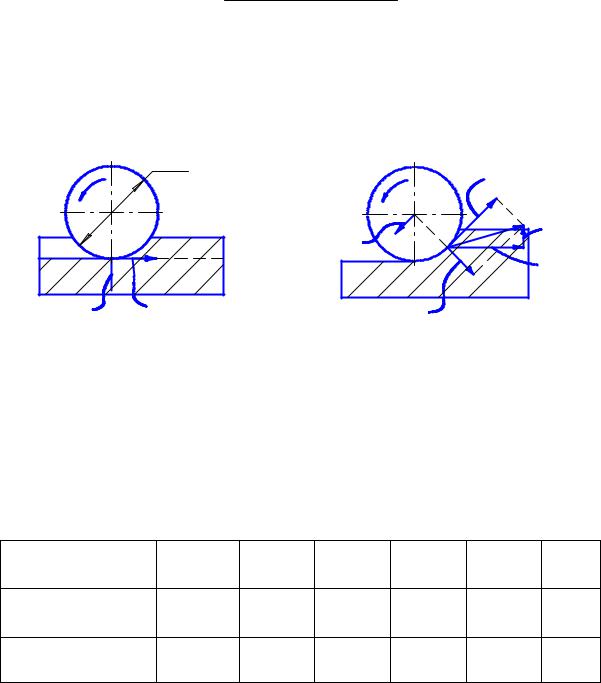
Расчет составляющих силы резания при фрезеровании |
||||||||
Фрезерование характеризуется наиболее сложной схемой сил |
||||||||
резания. Кроме того, схемы сил различны для различных фрез: |
||||||||
цилиндрических, торцовых, дисковых, концевых, шпоночных и т.д. |
||||||||
В качестве примера рассмотрим фрезерование дисковой фрезой. |
||||||||
Расчетом определяется только окружная сила (Н): |
|
|
||||||
|
|
P z |
10 C p t x |
S zy Bu z |
K мр , |
|
(44) |
|
|
|
Dq |
nw |
|
|
|||
|
|
|
|
|
|
|
||
где z – ч сло зубьев фрезы; n – частота вращения фрезы, об/мин; B – |
||||||||
ширина фрезерован я, мм; D – диаметр фрезы, мм; Sz |
– подача на зуб |
|||||||
фрезы, мм; CP – постоянная (табл. 20); x, y, z – показатели степеней |
||||||||
(табл. 20). |
|
|
|
|
|
|
|
|
|
Dô |
|
|
|
|
Pz |
|
|
|
|
|
|
|
|
|
|
|
|
|
|
|
Px |
|
|
|
Pv |
|
|
|
|
|
|
|
|
|
|
|
|
|
|
|
|
|
Ph |
Py |
Pz |
|
|
|
|
Py |
|
|
|
а |
|
|
|
б |
|
|
|
Рис. 15. Схемы сил резания при фрезеровании: а – упрощенная; б – полная; PZ – |
||||||||
окружная составляющая силы резания; PY |
– радиальная составляющая силы резания; |
|||||||
Pv – вертикальная составляющая силы резания; Px |
– осевая составляющая силы |
|||||||
резания; |
Ph – горизонтальная составляющая силы резания |
|
||||||
|
|
|
|
|
|
|
|
Таблица 20 |
Значения CP |
показателей степени для дисковых прорезных и отрезных фрез при |
|||||||
|
|
обработке стали с в 750 МПа |
|
|
||||
Материал режущей |
CP |
x |
y |
|
u |
q |
W |
|
части фрезы |
|
|||||||
|
|
|
|
|
|
|
||
СибАДИ |
||||||||
Твердый сплав |
|
261 |
0,9 |
0,8 |
|
1,1 |
1,1 |
0,1 |
Быстрорежущая |
68,2 |
0,86 |
0,72 |
|
1,0 |
0,86 |
0 |
|
сталь |
|
|
||||||
|
|
|
|
|
|
|
|
|
|
|
|
47 |
|
|
|
|
|

Все прочие составляющие силы резания определяются с использованием значений их соотношений (табл. 21).
|
|
Составляющие силы резания |
Таблица 21 |
|||
|
|
|
|
|||
|
Фрезерование |
Ph : Pz |
Pv : Pz |
P y : Pz |
Px : Pz |
|
|
|
|
||||
СибАДИ |
||||||
|
Встречное (прот в |
1,1 – 1,2 |
0 – 0,25 |
0,4 – 0,6 |
(0,2 – 0,4)tg ω |
|
|
подачи) |
|
|
|
|
|
|
Попутное |
|
|
|
(0,2 – 0,4)tg ω |
|
|
(в направлен |
-(0,8 – 0,9) |
0,7 – 0,9 |
0,4 – 0,6 |
||
|
подачи) |
|
|
|
|
|
Пр мечан е. ω – угол наклона витков фрезы.
3.2.5. Расчет усилия зажима заготовки
Для расчета ус л я зажима необходимо составить схему действия сил резан я на заготовку, сформулировать условие равновесия заготовки.
Рассмотрим пример – фрезерование плоской заготовки. Составим схему базирования заготовки определим направления действия основных составляющих силы резания, силу зажима и силы трения: P2 – окружная составляющая силы фрезерования, стремится сдвинуть
заготовку; P1 – радиальная составляющая силы фрезерования, прижимает заготовку к опорам 1 2; Q – сила зажима; F1,F 2 – силы
трения в местах контакта зажима с заготовкой и опор 1и 2 с заготовкой (рис.16).
Рис. 16. Схема базирования плоской заготовки
48
|
Составим уравнение равновесия заготовки: |
|
|
|
|
||||||||
|
|
|
|
P2 F1 F 2 0 . |
|
|
|
(45) |
|
||||
|
Или |
|
|
P2 f 1 Q f 2 Q P1 0 . |
|
(46) |
|
||||||
|
|
|
|
|
|
||||||||
|
где f1, f2 – коэффициенты трения (табл. 22). |
|
|
|
|
|
|||||||
СибАДИзатупления инструмента, =1,0 – 1,8 ; – коэффициент, |
|||||||||||||
|
Откуда выразим силу зажима: |
|
|
|
|
|
|
||||||
|
|
|
|
Q |
P |
2 P1 f |
2 . |
|
|
|
(47) |
|
|
|
|
|
|
|
|
f 1 f 2 |
|
|
|
Таблица 22 |
|||
|
|
|
Значения коэффициента трения f |
|
|
|
|||||||
|
|
Услов я трен я |
|
|
|
|
|
|
f |
|
|
|
|
|
Контакт заготовки с опорами: |
|
|
|
|
|
|
|
|
|
|||
|
-заготовка обра отана |
|
|
|
|
|
|
0,16 |
|
|
|
||
|
-заготовка не обра отана |
|
|
|
|
|
|
0,2 – 0,25 |
|
|
|
||
|
-опора р фленая |
|
|
|
|
|
|
0,7 |
|
|
|
||
|
-опора сфер ческая |
|
|
|
|
|
|
0,25 |
|
|
|
||
|
Зажим с острыми р флен ями |
|
|
|
|
|
0,7 – 1,0 |
|
|
|
|||
|
Найденная |
сила |
зажима |
|
не |
обеспечит |
надежного |
||||||
|
(гарантированного) закрепления заготовки. Поэтому вводят |
||||||||||||
|
коэффициент запаса K, |
с учетом которого определяется требуемое |
|||||||||||
|
усилие (Н) закрепления заготовки: |
|
|
|
|
|
|
|
|||||
|
|
|
|
Qз Q K , |
|
|
|
|
(48) |
|
|||
|
где K – коэффициент запаса, |
|
|
|
|
|
|
|
|
|
|||
|
|
|
K K 0 K1 K 2 K 3 K 4 K 5 K 6 , |
|
(49) |
|
|||||||
|
здесь K 0 |
- коэффициент гарантированного запаса, |
K 0 =1,5; |
K1 – |
|||||||||
|
коэффициент, учитывающий увеличение силы резания из-за |
||||||||||||
|
случайных неровностей на обработанной поверхности ( K1 =1,2 при |
||||||||||||
|
черновой |
обработке, |
K1 =1,0 при чистовой |
обработке); K 2 – |
|||||||||
|
коэффициент, |
характеризующий |
увеличение |
сил резания |
из-за |
||||||||
|
|
|
|
K 2 |
|
|
|
|
K 3 |
|
|
|
|
|
учитывающий увеличение сил резания при прерывистом резании, |
||||||||||||
|
K 3 =1,2; |
K 4 – |
коэффициент, |
характеризующий постоянство |
силы |
||||||||
|
закрепления, зависит от типа привода ( K 4 =1,3 при ручном приводе; |
||||||||||||
|
K 4 =1,2 при пневмокамерном |
приводе; |
K 4 =1,0 при |
гидро- |
или |
пневмоприводе); K 5 – коэффициент, характеризующий эргономику ручных приводов ( K 5 =1,2 при большом угле поворота рукояти (>90°),
49

K 5 =1,0 при малом угле поворота); K 6 – учитывает вид опор ( K 6 =1,0
–установка на штыри; K 6 =1,5 – установка на опорные пластины). Если расчетное значение K меньше 2,5, то принимают K=2,5.
3.2.6. Расчет рычажных зажимных механизмов
Найденное выше усилие закрепления заготовки служит основой для выбора и расчета зажимного устройства приспособления. Наиболее часто в качестве зажимных устройств используют элементарные заж мные механизмы: винтовые, эксцентриковые,
СприспособленияхбАДИз-за следующих достоинств:
клиновые, |
кл ноплунжерные, реечные, рычажные, рычажно- |
|
шарнирные. Больш |
нство этих устройств обладают самотормозящим |
|
эффектом, в х ра |
оте используется ручной привод, они просты в |
|
изготовлен |
относ тельно дешевы. |
В качестве пр мера рассмотрим расчет рычажных зажимных механ змов, которые получили широкое применение в различных
возможность построения сложных зажимных механизмов;
возможность зменения величины и направления действия сил;
возможность использования различных типов приводов.
На первом этапе расчета необходимо составить или выбрать типовую схему рычажного зажимного механизма (рис. 17).
В зависимости от выбранной типовой схемы механизма определяется реакция в шарнире опоры рычага по уравнениям:
а) R Qпр P з (см. рис. 17, а);
) R Q2пр P2з (см. рис. 17, б); в) R Qпр Pз (см. рис. 17, в),
где Qпр усилие, развиваемое приводом; P з – усилие закрепления заготовки, P з =Q з .
50

СибАДИаР с. 17. Схемы рычажных зажимных механизмов в
51