
1082
.pdf
ных законов измельчения (Риттингера, Бонда, Кирпичева-Кика и др.), каждый из которых справедлив только в области достаточно грубой дисперсности.
Во всех работах по теории измельчения не принималось во внимание, что разрушение твердых тел сопровождается пластической деформацией и т.д., на которую затрачивается некоторая доля подводимой к ним энергии.
Вся полезная работа измельчения складывается из работы диспергации (увеличение поверхности) и работы, необходимой для структурных изменений. Если известно поверхностное натяжение (удельная поверхностная энергия), то можно рассчитать работу диспергации по формуле
А0 s Mf , |
(4.2) |
где А0 – работа диспергации, Дж/г; s– изменение поверхности, м2; М
– масса измельченного материала, кг; f – переводной коэффициент. Эксперименты при измельчении кальцита вибрацией показали, что
всего 0,006 % затрачиваемой на измельчение энергии расходуется на увеличение прочности порошка, при этом КПД измельчения составляет 0,19 %.
В зависимости от условий нагружения до 30 % подводимой механической энергии аккумулируется в измельчаемом материале. Однако существуют представления, что при увеличении скорости механического воздействия величина накопленной энергии увеличивается и может достигать 60 % и более от подводимой к измельчителю энергии. Такой большой разброс численных значений объясняется в первую очередь трудностью измерений и неточностью расчета энергии, а также существенным влиянием условий проведения экспериментов.
Одной из самых первых теоретических зависимостей, устанавливающей математическую взаимосвязь работы дробления с природой разрушения и технологическими условиями производства, является функция, определенная проф. Ю.А. Веригиным /14/:
Ар. |
(К1 К |
2 К3 )dV К4 ln К5dVdFdl . |
(4.3) |
|
|
|
|
Физический смысл коэффициентов можно охарактеризовать следующим образом: коэффициент К1 определяет условия упругого и пластического деформирования, создающие запас потенциальной энергии, необходимой для обеспечения неблагоприятных условий разрушения объема dV до заданной степени измельчения i; К2 – величину дополнительного напряженного состояния в объеме среды за счет температурных градиентов; К3 учитывает дополнительный расход тепловой энергии, диссипирующейся в единице объема; К4 – молекулярно-кинетический оператор; К5 – коэффициент, определяющий условия экстремального хода процесса разруше-

ния межчастичных связей в веществе для достижения заданной тонины помола и степени измельчения материала.
Данная зависимость включает в себя сложно определяемые параметры, что, в свою очередь, приводит к невозможности ее применения на практике либо к искажению подлинного результата.
На основании научно-технического анализа измельчителей /15,16/, можно построить иерархическую зависимость значимости основных видов мельниц от показателей для их выбора при помоле золоцементных материалов (рис. 4.1).
По совокупности значимости характеристик наиболее эффективной мельницей для измельчения золоцементных материалов является дезинтегратор. По своей конструкции его можно разделить согласно рис.4.2 на однороторные и двухроторные. При этом с точки зрения эффективности передачи механической энергии к измельчаемому материалу преимущество имеют двухроторные дезинтеграторные установки с двухсторонним вращением роторов.
ФАКТОРЫ ЭФФЕКТИВНОСТИ ПРОЦЕССА МЕХАНОАКТИВАЦИИ ЗОЛОЦЕМЕНТНЫХ МАТЕРИАЛОВ В ДЕЗИНТЕГРАТОРЕ
Для выбора факторов эффективности механоактивации золоцементных материалов в дезинтеграторе рассмотрим динамику совершенствования дезинтеграторов на основе патентной информации за последние 25 лет с помощью программы расчета на ЭВМ, алгоритм которой приведен на рис.5.1.
Описание типа переменных и массивов
Ввод исходной информации: к, массивы ti, Ni
Блок формирования массивов
Печать и массивов ti, Ni
Вычисление коэффициентов b, y0, yi, D
Печать b, y0, yi, D
D 95 %
Вычисление массивовWi, zi,, коэффициентов r, p, g

Печать массивов Wi, zi,, коэффициентов r,p,g
Рис. 5.1. Блок-схема алгоритма для определения динамики патентования
Отбор патентов осуществляется по смысловому содержанию и годам подачи патентов.
|
y1 yc bti , |
(5.1) |
или |
y1 yc b(t t1), |
(5.2) |
где yc |
– среднеарифметическое значение поданных патентов. |
|
|
k |
|
|
yc yi /k . |
(5.3) |
|
i 1 |
|
Коэффициент перспективности определяется следующим образом:
k |
k |
|
b у1 ус ti |
tc / ti tc . |
(5.4) |
i 1 |
i 1 |
|
Далее проводится анализ полученных экспонент с помощью критерия Стьюдента, который определяется по зависимости
D b/ Sb , |
(5.5) |
где Sb – среднеквадратичное отклонение для коэффициента перспективности,
|
k |
|
|
Sb |
S2 / (ti tc )2 |
, |
(5.6) |
|
i 1 |
|
|
здесь S – среднеквадратичное отклонение для линий регрессий,
|
k |
|
S |
(y1 yi )2 / k 1 . |
(5.7) |
|
i 1 |
|
Отбирались экспоненты, отвечающие на 95 % и более критерию Стьюдента. Если этот критерий менее 95 %, то строится логистическая кривая (нарастающим итогом) с аппроксимацией зависимости вида
W L e ep gti |
, |
(5.8) |
i |
|
|
где Wi – число патентоспособных заявок, поданных за год; p, g – искомые
постоянные коэффициенты (параметры прямой линий регрессий). |
|
L limW . |
(5.9) |
Параметр L вычисляется из выражения |
|
L Wk , |
(5.10) |

где Wk – число патентоспособных заявок, поданных в конечный год, а также из условия максимальности коэффициента корреляций rпар ziti .
Дважды прологарифмировав обе стороны функции (5.7) и проделав элементарные преобразования, получем линейную функцию
|
LnLnL/Wi p qti . |
(5.11) |
Обозначая p qti |
zi , получим |
|
|
zi LnLnL/Wi . |
(5.12) |
Коэффициент корреляции подсчитывается по формуле
k |
k |
k |
r k zi ti ti zi /
i 1 |
i 1 |
i 1 |
k |
2 |
k |
2 k |
2 |
k |
2 |
(5.13) |
||
k ti |
|
ti |
k zi |
|
zi |
. |
|||
|
i 1 |
|
i 1 |
|
i 1 |
|
i 1 |
|
|
|
|
|
|
|
|
|
|
|
|
Параметры функций (5.11) находятся из выражений
k |
k |
k |
k |
2 |
|
k |
|
2 |
(5.14) |
p k zi ti |
ti |
zi |
/k ti |
|
|
ti |
|
; |
|
i 1 |
i 1 |
i 1 |
i 1 |
|
i 1 |
|
|
|
k |
k |
k |
k |
|
k |
|
q ti |
2 zi |
k zi |
ti /k ti |
2 |
( ti )2 . |
(5.15) |
i 1 |
i 1 |
i 1 |
i 1 |
|
i 1 |
|
По вышеуказанной методике анализируется динамика патентования основных показателей совершенствования эффективности процесса механоактивации золоцементного материала в дезинтеграторе. Анализ техникоэкономических показателей выявляет, что тенденция, направленная на снижение металлоемкости, не находит в настоящее время должного внимания у изобретателей (рис. 5.2).
LnNi 6 |
|
|
|
|
|
|
|
|
|
|
|
|
|
|
|
|
|
|
|
|
|
|
|
|
|
|
|
Y1 |
|
|
|
|
|
|
|
|
|
|
|
|
|
|
|
|
|
|
|
||
5 |
|
|
|
|
|
|
||||||||||||||||||
|
|
|
|
|||||||||||||||||||||
4 |
|
|
|
Y2 |
|
|
|
|||||||||||||||||
|
|
|
|
|||||||||||||||||||||
3 |
|
|
|
Y3 |
|
|
|
|
|
|
|
|
|
|
|
|
|
|
|
|
|
|
|
|
|
|
|
|
|
|
|
|
|
|
|
|
|
|
|
|
|
|
|
|
|
|
|||
2 |
|
|
|
|
|
|
|
|
|
|
|
|
|
|
|
|
||||||||
|
|
|
|
|
|
|
|
|
|
|
|
|
|
|||||||||||
1 |
|
|
|
|
|
|
|
|
|
|
|
|
|
|
|
|
|
|
|
|
|
|
|
|
|
|
|
|
|
|
|
|
|
|
|
|
|
|
|
|
|
|
|
|
|
|
|
|
|
0 |
|
|
|
|
|
|
|
|
|
|
|
|
|
|
|
|
|
|
|
|
|
|
|
|
|
1970-75 1975-80 1980-85 1985-90 1990-95 |
|
||||||||||||||||||||||
|
|
|
Годы
Рис. 5.2. Динамика патентования повышения эффективности механоактивации дезинтеграторов по технико-экономическим показателям: Y1 – уменьшение металлоемкости (b=0,1); Y2 – повышение производительности (b=0,18); Y3 –
уменьшение удельных энергозатрат (b=0,26)
Это объясняется тем, что уменьшить металлоемкость можно либо за счет снижения веса, либо за счет повышения производительности мельниц.
Так, снижение веса дезинтеграторов можно достичь путем: 1) использования при их производстве легких материалов, но это приведет к повышению удельного износа; 2) компактности конструкции: а) преобразования привода (например, установка роторов непосредственно на валах электродвигателей); б) уменьшения габаритов мелющих органов, что повлечет за собой уменьшение производительности. Учитывая также, что габариты и масса дезинтеграторов удовлетворяют технологической линии производства большинства дорожно-строительных материалов, можно сделать вывод об отсутствии необходимости вести дальнейшую работу по совершенствованию этого направления.
Повышение производительности также не является главным техникоэкономическим показателем, поскольку производительность дезинтеграторов зависит от критической скорости соударения, выраженной через число оборотов рабочего колеса с внутренними пальцами, а также от основных размеров мелющего оборудования. При этом с увеличением скорости вращения будет увеличиваться сопротивление воздуха, что потребует установки более мощных двигателей, а также будут меняться и другие конструктивные параметры установки. Увеличение основных размеров мелющего оборудования приведет к повышению металлоемкости и износа. Поэтому разрешить проблему данного направления можно лишь путем поиска оптимальной скорости вращения роторов /17/.
Перспективным технико-экономическим показателем является уменьшение удельных энергозатрат. Достаточно указать, что на измельчение (дробление) ежегодно тратится не менее 25 % всей производимой в мире энергии, включая энергию двигателей внутреннего сгорания. К сожалению, необходимо отметить, что весьма значительная часть энергии затрачивается непроизводительно вследствие несовершенства самого помольного оборудования и несовершенства приводных систем. Также необходимо отметить, что наметившиеся тенденции все более широкого применения тонкоизмельченного сырья тоже влекут за собой рост потребления энергии. Таким образом, значение энергозатрат на измельчение в дорожном строительстве, ориентированное на самоокупаемость, очевидно. Поэтому в дезинтеграторах наряду с другими видами помольного оборудования наблюдается тенденция поиска новых технических решений, направленных на уменьшение удельных энергозатрат, что приведет к понижению себестоимости выпускаемой продукции.
Практика показывает, что технико-экономические показатели неразрывно связаны с конструктивными. К важнейшим конструктивным показателям эффективности относится надежность. Надежность помольных установок обуславливается их безотказностью, долговечностью (понижение удельного износа мелющих органов), ремонтопригодностью во времени установленных эксплуатационных показателей. Недостаточная надежность
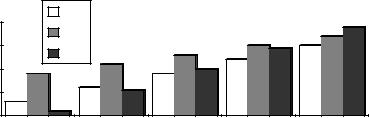
дезинтеграторов может отразиться на работе всей технологической линии изготовления золоцементного вяжущего и может явиться причиной значительных потерь рабочего времени. Интенсивный износ деталей и узлов установки увеличивает количество ремонтов, простоев агрегата, что вынуждает содержать большой штат рабочих-ремонтников. Из вышесказанного следует, что проблема повышения надежности приобретает особую актуальность для дезинтеграторов, используемых в дорожном строительстве. Из анализа критериев надежности (рис. 5.3) можно отметить, что повышение ремонтопригодности находится на более низком уровне применения. Однако коэффициент перспективности этого критерия имеет предпочтительное значение, что можно объяснить подачей большого количества патентов в последние годы.
Это обстоятельство можно охарактеризовать тем, что в настоящее время требуется снизить время простоев оборудования путем повышения удобства обслуживания и быстрой заменой изношенных деталей (узлов). Поэтому наблюдается тенденция развития данного направления.
LnNi |
4 |
Y1 |
|
|
|
|
|
Y2 |
|
|
|
|
|||
3 |
|
|
|
|
|||
Y3 |
|
|
|
|
|||
|
2 |
|
|
|
|
||
|
|
|
|
|
|
|
|
|
1 |
|
|
|
|
|
|
|
0 |
1970-75 |
1975-80 |
1980-85 |
1985-90 |
1990-95 |
|
|
|
Годы |
Рис. 5.3. Динамика патентования ударных мельниц по показателям надежности: Y1 – повышение ремонтопригодности (b=0,12); Y2–повышение безотказности (b=0,08); Y3 – снижение удельного износа (b=0,18)
Один из критериев надежности – повышение безотказности – находится на высоком уровне, но имеет тенденцию к снижению интереса со стороны рационализаторов, так как методы, направленные на повышение безотказности (рациональное распределение нагрузок в узлах и подбор оптимальных запасов прочности, совершенствование системы смазки в подшипниковых узлах и совершенствование привода), практически исчерпали свой ресурс, а новые методы еще не найдены.
Снижение удельного износа является одним из конкурентоспособных направлений совершенствования надежности дезинтеграторов. Уменьшить удельный износ можно путем использования износостойких материалов для изготовления или армирования рабочих органов и совершенствования конструкции рабочих органов или отдельных узлов измельчителя, а также применения износостойких материалов с одновременным усовершенствованием конструкции измельчителя /18/. Однако надо помнить, что повы-

шение ресурса рабочих элементов дезинтегратора не должно приводить к снижению эффективности измельчения. Поэтому следующими показателями, направленными на совершенствование повышения эффективности измельчения, активации и гомогенизации, являются изменения конструкций дезинтеграторов: 1) ударных элементов; 2) роторов (дисков); 3) других основных элементов (узлов).
Анализ динамики патентования изменений конструкций ударных элементов (рис. 5.4) показывает, что изменение угла атаки хоть и имеет тенденцию роста, но оно невелико. Поэтому можно сказать, что поиск оптимального угла атаки практически завершен. Однако этого нельзя сказать о других изменениях конструкции ударных элементов, таких, как изменение формы, числа рядов и количества в рядах ударных элементов. Из рисунка 5.4 видно, что при конструировании дезинтеграторов необходимо обратить особое внимание на форму ударных элементов.
LnNi |
10 |
Y 1 |
|
8 |
|||
|
Y 2 |
||
|
6 |
Y 3 |
|
|
4 |
|
|
|
2 |
|
|
|
0 |
Годы |
|
|
1970-75 |
1975-80 1980-85 1985-90 1990-95 |
Рис. 5.4. Динамика патентования изменения конструкции ударных элементов: Y1 – угла атаки (b=0,08); Y2 – числа рядов и количества в рядах ударных
элементов (b=0,28); Y3 – формы (b=0,34)
Практика показывает, что изменение расположения загрузочного патрубка и шнека относительно ротора не влияет на эффективность механоактивации. Анализ динамики патентования изменения конструкции роторов (рис. 5.5) подтверждает это высказывание. Количество патентов, поданных на изменение формы роторов с целью повышения эффективности измельчения активации, намного больше, чем количество патентов предыдущего направления. Это объясняется тем, что, изменяя форму роторов, можно получить оптимальную скорость соударения размалываемого материала.
LnN |
5 |
Y1 |
|
|
|
i |
4 |
|
|
|
|
|
Y2 |
|
|
|
|
|
3 |
|
|
|
|
|
Y3 |
|
|
|
|
|
|
|
|
|
|
|
2 |
|
|
|
|
|
1 |
|
|
|
|
|
0 |
1975-80 |
1980-85 |
1985-90 |
Годы |
|
1970-75 |
1990-95 |

Рис. 5.5. Динамика патентования изменения конструкций роторов: Y1 – расположение загрузочного патрубка и шнека относительно роторов (b=0,01); Y2 – формы (b=0,1); Y3 – монтаж дополнительных элементов
на роторах (b=0,18)
Однако самым перспективным направлением преобразования роторов является монтаж на нем дополнительных элементов (рабочего оборудования, проточек и т.д.).
Анализ динамики патентования изменения конструкции других основных элементов (узлов) дезинтеграторов показал, что установка дополнительного оборудования в рабочей камере (отражательных плит и т.д.) и преобразование конструкции корпуса исчерпали свои пути решения и перестали быть актуальными (рис. 5.6). Наряду с ними установление сепарации является одним из главных направлений, способствующих повышению эффективности измельчения активации, что подтверждается высоким коэффициентом перспективности.
LnNi |
4 |
Y1 |
|
|
|
|
3 |
Y2 |
|
|
|
|
Y3 |
|
|
|
|
|
2 |
|
|
|
|
|
|
|
|
|
|
|
1 |
|
|
|
|
|
0 |
1975-80 |
1980-85 |
1985-90 |
1990-95Годы |
|
1970-75 |
Рис.5.6. Динамика патентования изменения конструкции других основных элементов: Y1 – корпуса (b=0,02); Y2 – установки дополнительного оборудования в рабочей
камере (b=0,08); Y3 – установки сепарации (b=0,16)
С целью выявления характеристик работы дезинтеграторов в производственных целях проанализируем динамику патентования основных эксплуатационных показателей качества (рис. 5.7).
Повышение эргономичности (безопасности работы, снижения напряженности и утомляемости обслуживающего персонала и т.д.) растет интенсивнее, чем повышение мобильности и универсальности, так как мобильность дезинтеграторов удовлетворяет технологической линии дорожного строительства, а универсальность была широко изучена еще в начальные годы патентования .
Результаты детального исследования совершенствования качества дезинтеграторов, направленные на повышение эффективности механоактивации, приведены в табл. 5.1.
Если в каждой строке оснований деления по максимальным коэффициентам перспективности обвести кружком один из элементов, а затем со-

единить обведенные элементы, то получится цепочка, факторов направленная на повышение эффективности механоактивации минеральных материалов.
[p1m3] [p2m3] [p3m3] [p4m3] [p5m3] [p6m1].
Эти перспективные факторы могут быть использованы при разработке более совершенного варианта дезинтегратора.
LnNi |
3 |
|
|
Y1 |
2,5 |
|
|
Y2 |
|
|
|
|
||
|
2 |
|
|
Y3 |
|
1,5 |
|
|
|
|
|
|
|
1
0,5
0 1970-75 1975-80 1980-85 1985-90 1990-95 Годы
Рис.5.7. Динамика патентования дезинтеграторов по эксплуатационным показателям: Y1 – повышение эргономичности (b=0,12); Y2 – повышение мобильности (b=0,1); Y3 – повышение универсальности (b=0,06)
Таблица 5.1
Распределение коэффициента перспективности по классификации, направленной на повышение качества дезинтеграторов
Основания |
|
Варианты исполнения |
|
|
|
|
|
|
|
деления Рi |
у1 |
у2 |
|
у3 |
Р1 |
0,10 |
0,18 |
|
0,26 |
Р2 |
0,12 |
0,08 |
|
0,18 |
Р3 |
0,08 |
0,28 |
|
0,34 |
Р4 |
0,01 |
0,1 |
|
0,18 |
Р5 |
0,02 |
0,08 |
|
0,16 |
Р6 |
0,12 |
0,1 |
|
0,06 |
|
|
|
|
|
6. ЭФФЕКТИВНАЯ ЭНЕРГИЯ АКТИВАЦИИ ПРИ ДЕЗИНТЕГРАЦИИ ЗОЛОЦЕМЕНТНОГО МАТЕРИАЛА
6.1. Устройство и принцип работы дезинтеграторной установки
Схема дезинтеграторной установки приведена на рис. 6.1.
Установка состоит из прямоугольной станины, изготовленной методом сварки из двутаврового профиля прямоугольного сечения, на которой

смонтированы два электродвигателя 1 мощностью 4,0 кВт каждый. Электродвигатели соединены с помощью полумуфт сцепления 7 непосредственно с валами дезинтеграторной установки. К рабочей камере жестко закреплен приемный бункер 5, а в нижней части имеется отверстие с патрубком 9. Патрубок через уплотнительное устройство 10 соединен с накопительным бункером 11. Сам дезинтегратор расположен на станине между двумя двигателями. Он состоит из корпуса 3, дисков (левого и правого) 4, пальцев (бил) 8 и шнека 6. Скорость вращения дисков снимается с помощью тахометров 2.
Принцип работы дезинтеграторной установки заключается в следующем: после подачи напряжения на электродвигатели их роторы и соединенные с ними диски дезинтегратора начинают вращаться в разные стороны, затем измельчаемый материал засыпается в приемный бункер, откуда он шнеком подается в рабочее пространство мельницы. Далее частицы материала, попав на первый круг пальцев, получают скорость, соответствующую скорости пальцев, и с этой скоростью вылетают из круга. При этом их путь направлен в одну сторону с вектором скорости тех пальцев, от которого они ушли, и пересекают траекторию движения второго ряда пальцев (движущегося в противоположном направлении). После многократного соударения с пальцами частицы размалываемого материала, вылетев из внешнего круга пальцев, ударяются о внутреннюю часть кожуха и самотёком опускаются в нижнее его отверстие, попадая затем в накопительный бункер.
Рис. 6.1. Схема лабораторной дезинтеграторной установки:
1 – электродвигатель; 2 – тахометр; 3 – корпус; 4 – диск; 5 – приемный бункер; 6 – шнек; 7 – полумуфты сцепления; 8 – палец; 9 – патрубок; 10 – уплотнительное устройство; 11 – накопительный бункер
6.2.Схема движения материала в дезинтеграторе
Кнастоящему времени теоретические работы в этой области практиче-