
521
.pdf
|
|
|
10 12875000 24000 5500 |
|
||||
rx4 Y |
|
|
|
|
|
|
0,897. |
(2) |
|
|
|
|
|
||||
10 57860000 24000 2 |
|
|
||||||
|
|
10 3530000 5500 2 |
|
Аналогично формуле (2) рассчитать оставшиеся три коэффициента корреляции.
3. Сделать выводы по каждому из рассчитанных коэффициентов корреляции. Так как, rx4 Y 0,897, то это свидетельствует о на-
личии обратной линейной зависимости между х4 и Y , т.е. этот ЕПК в значительной степени влияет на конкурентоспособность процессора компьютера: чем значение наработки на отказ (х4 ) меньше, тем стоимость компьютера (Y ) выше. Этот противоречивый вывод можно объяснить следующим образом: чем миниатюрнее (меньше) комплектующее компьютера при тех же функциональных возможностях, тем его рабочий ресурс становиться меньше.
4.Аналогично сделать выводы по трем оставшимся коэффициентам корреляции.
5.Сформулировать общий вывод по задаче, следующим образом: те коэффициенты корреляции, которые отражают четкую прямую или обратную линейную зависимость, указывают на ЕПК, которые оказывают значительное влияние на конкурентоспособность оцениваемой продукции. Поэтому, улучшая значения этих показателей, можно повысить уровень качества, а значит, и уровень конкурентоспособности оцениваемой продукции (услуги).
Лабораторная работа №3
Инструменты контроля качества: контрольный листок, гистограмма, диаграмма Парето
Цель – изучение теоретических принципов и практического построения основных инструментов статистического контроля качества: контрольных листков, гистограммы и диаграммы Парето.
Теоретические аспекты
Одной из основных функций управления качеством является контроль. Его значение заключается в возможности выявления несоответствий с последующим их оперативным исправлением с минимальными потерями для бизнеса.
Контроль качества осуществляется путем сравнения запланированных показателей качества с действительными их значениями. Соб-
10
ственно контроль качества состоит в том, чтобы проверяя показатели качества, обнаружить их отклонение от запланированных значений. В случае обнаружения такого отклонения необходимо найти причину его появления, и после корректировки процесса вновь проверить соответствие скорректированных показателей качества их запланированным значениям. Именно по такому непрерывному циклу осуществляется управление и обеспечение требуемого качества и дальнейшее его улучшение.
Требования к качеству устанавливаются и фиксируются в нормативных и нормативно-технических документах.
Отклонение качества продукции от заданных параметров происходит, как правило, в худшую сторону и имеет как общие, так и частные проявления.
К числу общих относятся моральный износ, физическое и моральное старение продукции, то есть потеря первоначальных свойств при эксплуатации.
Частные отклонения качества от установленных требований чрезвычайно разнообразны и обусловлены уже не экономической и технологической природой, а условиями внешнего характера:
нарушениями правил эксплуатации;
ошибками разработчиков и изготовителей;
нарушениями производственной дисциплины;
дефектами оборудования, с помощью которого изготавливается и используется продукция, и т.д.
Таким образом, можно сделать вывод, что качество продукции находится в постоянном движении и представляет собой хронически неустойчивый объект, требующий контроля. Научной основой современного технического контроля является математико-статистические методы.
Управление качеством продукции может обеспечиваться двумя методами:
1)разбраковкой изделий;
2)повышением технологической точности.
Традиционно методы контроля сводились, как правило, к анализу брака путем сплошной проверки изделий на выходе.
При массовом производстве такой контроль очень дорог: контрольный аппарат должен в пять – шесть раз превышать количество производственных рабочих, и даже при этом нет полной гарантии от
11
брака. Поэтому от сплошного контроля переходят к выборочному с применением статистических методов обработки результатов.
Японские специалисты из всего множества статистических методов выбрали семь основных. Их заслуга состоит в том, что они обеспечили простоту, наглядность, визуализацию этих методов, превратив их фактически в эффективные инструменты контроля качества.
1.Контрольный листок – инструмент для сбора данных и их автоматического упорядочения для облегчения дальнейшего использования собранной информации.
2.Гистограмма – инструмент, позволяющий зрительно оценить распределение статистических данных, сгруппированных по частоте попадания данных в определенный (заранее заданный) интервал.
3.Анализ Парето – инструмент, позволяющий объективно представить и выявить основные факторы, влияющие на исследуемую проблему и распределить усилия для ее решения.
4.Стратификация (расслоение) – инструмент, позволяющий произвести селекцию данных в соответствии с различными факторами.
5.Причинно-следственная диаграмма Исикавы – инстру-
мент, который позволяет выявить наиболее существенные факторы (причины), влияющие на конечный результат (следствие).
6.Диаграмма разброса – инструмент, позволяющий определить вид и тесноту связи двух рассматриваемых параметров процесса.
7.Контрольная карта – инструмент, позволяющий отслеживать ход протекания процесса и воздействовать на него (с помощью соответствующей обратной связи), предупреждая его отклонения от предъявленных к процессу требований.
Эти методы можно рассматривать и как отдельные инструменты,
икак систему методов. Последовательность применения семи инструментов может быть различной в зависимости от поставленной цели.
Известный японский специалист в области качества профессор К. Исикава говорил: «Основываясь на опыте своей деятельности, могу сказать, что 95% всех проблем фирмы могут быть решены с помощью этих семи приемов». Поэтому статистические методы – это то средство, которое необходимо изучать, чтобы внедрить управление качеством. Они – наиболее важная составляющая комплексной системы контроля Всеобщего управления качеством (TQM) производственной организации.
12
Задания
1. Рассмотреть основные типы контрольных листков и их назначение.
Выделяют три основных типа контрольных листков:
контрольныйлистокдляраспределенияпараметровизделия(рис.1);
контрольный листок длярегистрациивидов дефектов(рис.2);
контрольныйлистокдляанализастабильностипроцесса(рис.3).
Размер |
Отклонение |
|
Результат |
Частота |
Примечание |
|||||||
|
|
0,05 |
|
х |
|
|
Деталь – |
|
вал |
|||
|
|
0,04 |
|
хх |
|
|
Дата – |
21.03.2011 |
|
|||
|
|
0,03 |
|
хххх |
|
|
Станок – |
2345 |
|
|||
|
|
0,02 |
|
хххххх |
|
|
Рабочий – |
|
Иванов И.И. |
|||
10 мм |
|
0,01 |
|
ххххххххх |
|
|
|
|
|
|
||
|
0 |
|
ххххххххххххххх |
|
|
|
|
|
|
|||
|
|
-0,01 |
|
ххххххххххх |
|
|
|
|
|
|
||
|
|
-0,02 |
|
ххххххх |
|
|
|
|
|
|
||
|
|
-0,03 |
|
ххх |
|
|
Всего |
|
|
|
||
|
|
-0,04 |
|
х |
|
|
|
|
|
|||
|
|
-0,05 |
|
х |
|
|
|
|
|
|
||
|
Рис.1. Контрольный листок для распределения параметров изделия |
|||||||||||
|
|
|
|
|
|
|
|
|
|
|||
Дефект |
|
|
|
Результат |
|
Итог |
|
Примечание |
||||
Царапина |
|
|
/// |
|
|
|
Деталь – |
штампованная |
|
|||
|
|
|
|
|
деталь |
|
||||||
Трещина |
|
|
/ |
|
|
|
Дата – |
21.03.2011 |
|
|||
Заусенец |
|
|
/// /// // |
|
|
Контролер – |
Петров И.А. |
|
||||
|
|
|
/// /// /// /// /// /// /// /// /// /// |
|
|
|
|
|
|
|
||
Деформация |
/// /// /// /// /// /// /// /// /// /// |
|
|
|
Участок – |
1 |
|
|||||
|
|
|
|
/// /// // |
|
|
|
|
|
|
|
|
Вмятина |
|
/// /// /// /// /// /// /// /// /// /// |
|
|
|
Партия – |
4516 |
|
||||
|
/// /// /// /// /// / |
|
|
|
|
|||||||
|
|
|
|
|
|
|
|
|
|
|||
Раковина |
|
|
/// / |
|
|
|
|
|
|
|
||
Скол |
|
|
/// /// /// |
|
|
|
|
|
|
|
||
Прочие |
|
|
// |
|
|
|
Всего деталей – 1400 |
|
||||
|
|
|
Итого дефектов |
|
|
|
|
|||||
Дефектные |
|
/// /// /// /// /// /// /// /// /// /// |
|
|
|
|
|
|
|
|||
детали |
|
/// /// /// /// /// /// /// /// /// /// |
|
|
|
|
|
|
|
|||
|
|
/// /// /// /// // |
|
|
|
|
|
|
|
|||
|
|
|
|
|
|
|
|
|
|
|
||
|
|
Рис.2. Контрольный листок для регистрации видов дефектов |
13
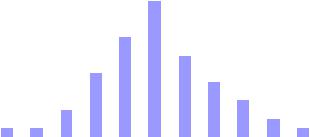
Цех – литей- |
|
|
Деталь – вал |
|
Характерис- |
Объем |
Дата – |
|||||||||||
|
|
тика – отклоне- |
выбо- |
|||||||||||||||
|
ный |
|
|
|
|
|
|
ние диаметра |
рок – 5 |
21.03.2011 |
||||||||
Операция – |
Рабочий – Ива- |
|
Предельные |
Частота |
Расчеты |
|||||||||||||
|
значения – |
выборок |
выпол- |
|||||||||||||||
|
литье |
|
|
|
нов И.И. |
|
||||||||||||
|
|
|
|
|
90-110 мкм |
– 30 мин |
нил – |
|||||||||||
|
|
|
|
|
|
|
|
|
|
|
||||||||
Время |
|
8:00 |
|
8:30 |
|
9:00 |
9:30 |
|
10:00 |
|
10:30 |
11:00 |
|
11:30 |
12:00 |
12:30 |
13:00 |
|
|
|
|
|
|
|
|
|
|
|
|
|
|
|
|
|
|
|
|
Х1 |
|
2 |
|
3 |
|
3 |
4 |
|
2 |
|
4 |
2 |
|
5 |
3 |
2 |
4 |
|
Х2 |
|
3 |
|
2 |
|
5 |
2 |
|
5 |
|
5 |
3 |
|
4 |
3 |
4 |
2 |
|
Х3 |
|
2 |
|
2 |
|
2 |
1 |
|
3 |
|
5 |
3 |
|
2 |
6 |
4 |
5 |
|
Х4 |
|
5 |
|
1 |
|
2 |
3 |
|
6 |
|
3 |
5 |
|
2 |
2 |
3 |
3 |
|
Х5 |
|
3 |
|
4 |
|
3 |
5 |
|
2 |
|
2 |
4 |
|
1 |
1 |
5 |
3 |
|
Хср. |
|
|
|
|
|
|
|
|
|
|
|
|
|
|
|
|
|
|
R |
|
|
|
|
|
|
|
|
|
|
|
|
|
|
|
|
|
|
Рис.3. Контрольный листок для анализа стабильности процесса
2.Заполнить недостающие данные в каждом типе контрольного листка, исходя из информации о проведенных замерах, контролируемых параметров качества изделия. Сделать выводы.
3.По результатам контрольного листка для распределения контролируемого параметра построить гистограмму (рис. 4).
|
|
|
|
|
|
|
|
|
|
|
|
|
|
|
|
|
|
|
|
|
|
|
|
|
|
|
|
|
|
|
|
|
|
|
|
|
|
|
|
|
|
|
|
|
|
|
Частоты |
||
|
|
|
|
|
|
|
|
|
|
|
|
|
|
|
|
|
|
|
|
|
|
|
|
|
|
|
|
|
|
|
|
|
|
|
|
|
|
|
|
|
|
|
|
|
|
|
|
|
16 |
|
|
|
|
|
|
|
|
|
|
|
|
|
|
|
|
|
|
|
|
|
|
|
|
|
|
|
|
|
|
|
|
|
|
|
|
|
|
|
|
|
|
|
|
|
|
|
|
|
|
|
|
|
|
|
|
|
|
|
|
|
|
|
|
|
|
|
|
|
|
|
|
|
|
|
|
|
|
|
|
|
|
|
|
|
|
|
|
|
|
|
|
|
|
|
|
|
|
|
14 |
|
|
|
|
|
|
|
|
|
|
|
|
|
|
|
|
|
|
|
|
|
|
|
|
|
|
|
|
|
|
|
|
|
|
|
|
|
|
|
|
|
|
|
|
|
|
|
|
|
|
|
|
|
|
|
|
|
|
|
|
|
|
|
|
|
|
|
|
|
|
|
|
|
|
|
|
|
|
|
|
|
|
|
|
|
|
|
|
|
|
|
|
|
|
|
|
|
|
|
12 |
|
|
|
|
|
|
|
|
|
|
|
|
|
|
|
|
|
|
|
|
|
|
|
|
|
|
|
|
|
|
|
|
|
|
|
|
|
|
|
|
|
|
|
|
|
|
|
|
|
|
|
|
|
|
|
|
|
|
|
|
|
|
|
|
|
|
|
|
|
|
|
|
|
|
|
|
|
|
|
|
|
|
|
|
|
|
|
|
|
|
|
|
|
|
|
|
|
|
|
10 |
|
|
|
|
|
|
|
|
|
|
|
|
|
|
|
|
|
|
|
|
|
|
|
|
|
|
|
|
|
|
|
|
|
|
|
|
|
|
|
|
|
|
|
|
|
|
|
|
|
|
|
|
|
|
|
|
|
|
|
|
|
|
|
|
|
|
|
|
|
|
|
|
|
|
|
|
|
|
|
|
|
|
|
|
|
|
|
|
|
|
|
|
|
|
|
|
|
|
|
8 |
|
|
|
|
|
|
|
|
|
|
|
|
|
|
|
|
|
|
|
|
|
|
|
|
|
|
|
|
|
|
|
|
|
|
|
|
|
|
|
|
|
|
|
|
|
|
|
|
|
|
|
|
|
|
|
|
|
|
|
|
|
|
|
|
|
|
|
|
|
|
|
|
|
|
|
|
|
|
|
|
|
|
|
|
|
|
|
|
|
|
|
|
|
|
|
|
|
|
|
6 |
|
|
|
|
|
|
|
|
|
|
|
|
|
|
|
|
|
|
|
|
|
|
|
|
|
|
|
|
|
|
|
|
|
|
|
|
|
|
|
|
|
|
|
|
|
|
|
|
|
|
|
|
|
|
|
|
|
|
|
|
|
|
|
|
|
|
|
|
|
|
|
|
|
|
|
|
|
|
|
|
|
|
|
|
|
|
|
|
|
|
|
|
|
|
|
|
|
|
|
4 |
|
|
|
|
|
|
|
|
|
|
|
|
|
|
|
|
|
|
|
|
|
|
|
|
|
|
|
|
|
|
|
|
|
|
|
|
|
|
|
|
|
|
|
|
|
|
|
|
|
|
|
|
|
|
|
|
|
|
|
|
|
|
|
|
|
|
|
|
|
|
|
|
|
|
|
|
|
|
|
|
|
|
|
|
|
|
|
|
|
|
|
|
|
|
|
|
|
|
|
2 |
|
|
|
|
|
|
|
|
|
|
|
|
|
|
|
|
|
|
|
|
|
|
|
|
|
|
|
|
|
|
|
|
|
|
|
|
|
|
|
|
|
|
|
|
|
|
|
|
|
|
Отклонения |
|
|
|
|
|
|
|
|
|
|
|
|
|
|
|
|
|
|
|
|
|
|
|
|
|
|
|
|
|
|
|
|
|
|
|
|
|
|
|
|
|
|
|
|
|
|
|
|
0 |
|
|
|
|
|
|
|
|
|
|
|
|
|
|
|
|
|
|
|
|
|
|
|
|
|
|
|
|
|
|
|
|
|
|
|
|
|
|
|
|
|
|
|
|
|
|
|
|
0,06 |
0,05 |
0,04 |
0,03 |
0,02 |
0,01 |
0 |
0,01 |
0,02 |
0,03 |
0,04 |
0,05 |
0,06 |
|
||||||||||||
- |
- |
- |
- |
- |
- |
|
|
|
|
|
|
|
Рис.4. Гистограмма качества
4. По результатам контрольного листка для регистрации видов дефектов построить диаграмму Парето, выполняя следующие этапы:
14
– проранжировать виды дефектов в зависимости от их количества, «прочие» дефекты при построении диаграммы Парето всегда будут по рангу последними (см. табл.5);
Таблица 1
Ранжирование значимости видов дефектов продукции
Дефект |
Количество |
Царапина |
3 |
Трещина |
1 |
Заусенец |
8 |
Деформация |
68 |
Вмятина |
46 |
Раковина |
4 |
Скол |
9 |
Прочие |
2 |
– создать таблицу для расчета данных, необходимых для построения диаграммы Парето (табл. 2);
|
|
|
Таблица 2 |
|
|
Данные для построения диаграммы Парето |
|||
|
|
|
|
|
|
Количество дефек- |
Накопленное |
Накопленный |
|
Дефект |
количество |
процент |
||
тов |
||||
|
дефектов |
дефектов |
||
|
|
|||
Деформация |
68 |
68 |
48 |
|
Вмятина |
46 |
114 |
81 |
|
Скол |
9 |
123 |
87 |
|
Заусенец |
8 |
131 |
93 |
|
Раковина |
4 |
135 |
96 |
|
Царапина |
3 |
138 |
98 |
|
Трещина |
1 |
139 |
99 |
|
Прочие |
2 |
141 |
100 |
–по данным табл. 6 построить диаграмму Парето (рис. 5);
–кривая на рис. 5, построенная по данным накопленного количества дефектов, называется кумулятивной кривой или кривой Парето; прямая, построенная на уровне 80% накопленных дефектов, исходя из принципа Парето (принципа 20-80), показывает, какие виды дефектов являются наиболее многочисленными. Так, в нашем случае наиболее многочисленными дефектами являются деформация и вмя-
15

тина; устранив причины возникновения этих дефектов, можно сни- |
|||||||||
зить общую дефектность продукции на 80%. |
|
|
|||||||
Количество |
|
|
|
|
|
|
|
Накопленное |
|
дефектов |
|
|
|
|
|
|
|
число |
|
160 |
|
|
|
|
|
|
|
|
дефектов |
|
|
|
|
|
|
|
|
|
|
140 |
|
|
|
|
131 |
135 |
138 |
139 |
141 100 |
|
|
|
|
|
|
|
|
||
|
|
|
|
123 |
|
|
|
|
|
120 |
|
114 |
|
|
|
|
|
80 |
|
|
|
|
|
|
|
|
|||
|
|
|
|
|
|
|
|
||
100 |
|
|
|
|
|
|
|
|
|
80 |
68 |
|
|
|
|
|
|
|
60 |
|
|
|
|
|
|
|
|
||
60 |
68 |
|
|
|
|
|
|
|
|
46 |
|
|
|
|
|
|
|
40 |
|
|
|
|
|
|
|
|
|
||
40 |
|
|
|
|
|
|
|
|
|
20 |
|
|
|
|
|
|
|
|
20 |
|
|
9 |
8 |
|
4 |
3 |
|
2 |
|
|
|
|
|
1 |
|||||
|
|
|
|
|
|
||||
0 |
|
|
|
|
|
|
|
|
0 |
Деформация Вмятина |
Скол |
Заусенец РаковинаЦарапина |
Трещина |
Прочие |
Вид дефектов |
||||
|
|||||||||
|
|
|
|||||||
|
|
|
|
Рис.5. Диаграмма Парето |
|
Лабораторная работа №4
Инструменты контроля качества: диаграмма разброса, стратификация, причинно-следственная диаграмма Исикавы
Цель – изучение теоретических принципов и практического построения основных инструментов статистического контроля качества: диаграмма разброса, стратификация, причинно-следственная диаграмма Исикавы.
Теоретические аспекты
Одним из наиболее простых и эффективных статистических методов, широко используемых в системе управления качеством, является стратификация или, как ее еще называют, метод расслаивания. В
16
соответствии с этим методом производят расслаивание статистических данных, т.е. группируют данные в зависимости от условий их получения и производят обработку каждой группы данных в отдельности. Данные, разделенные на группы в соответствии с их особенностями, называют слоями (стратами), а сам процесс разделения на слои
– расслаиванием (стратификацией).
Существуют различные методы расслаивания, применение которых зависит от конкретных задач. В производственных процессах часто используется метод 5M, учитывающий факторы, зависящие от человека, машины, материала, способа производства, измерения и дополнительно – управления (6M).
Расслаивание может осуществляться примерно так:
по исполнителям – квалификации, полу, стажу работы и т.д.;
по машинам и оборудованию – новому и старому оборудованию, марке, конструкции, выпускающей форме и т.д.;
по материалу – месту производства, фирме производителю, партии, качеству сырья и т.д.;
по способу производства – температуре, технологическому приему, месту производства и т.д.;
по измерению – методу измерения, типу измерительных средств или их точности и т.д.
Стратификация – основа для построения других инструментов,
например таких, как диаграммы рассеивания. Такое сочетание инструментов делает их более мощными.
Диаграмма рассеяния применяется для исследования зависимости между двумя видами данных. Она строится как график зависимости между двумя параметрами. Если на этом графике провести линию медианы, он позволяет легко определить, имеется ли между этими двумя параметрами корреляционная зависимость.
Диаграмма рассеяния строится в таком порядке: по горизонтальной линии откладываются измерения величин одной переменной, а по вертикальной оси – другой переменной.
Диаграмма рассеяния также используется для выявления при- чинно-следственных связей показателей качества и влияющих факторов при анализе причинно-следственной диаграммы Исикавы.
Причинно-следственная диаграмма Исикавы является очень мощным инструментом для анализа ситуации и получения информации о влиянии разных факторов на основной процесс. Здесь появляет-
17
ся возможность не только выявить факторы, влияющие на процесс, но и определить приоритетность их влияния.
Причинно-следственная диаграмма Исикавы рассматривает такие компоненты качества, как «человек», «методы», «средства», «материал», «управление» и «среда» (прил. 4).
Применительно к решаемой задаче квалиметрического анализа:
для компоненты «человек» необходимо определить факторы, связанные с удобством и безопасностью выполнения операций;
для компоненты «средства» – взаимоотношения элементов конструкции анализируемого изделия между собой, связанные с выполнением данной операции;
для компоненты «методы» – факторы, связанные с производительностью и точностью выполняемой операции;
для компоненты «материал» – факторы, связанные с отсутствием измененийсвойствматериаловизделиявпроцессевыполненияданнойоперации;
для компоненты «управление» – факторы, связанные с достоверным распознаванием ошибки процесса выполнения операции;
для компоненты «среда» – факторы, связанные с воздействием среды на изделие и изделия на среду.
Задания
1.Построить диаграммы рассеяния по данным о рекламациях по деталям А и В и сделать выводы (табл. 1).
|
|
|
|
|
|
Таблица 1 |
|
|
Рекламации по деталям А и Б за три периода наблюдения |
||||||
|
|
|
|
|
|
|
|
|
|
|
РЕКЛАМАЦИЯ |
|
|
|
|
№ |
1-й период |
2-й период |
3-й период |
|
|||
наблюдения |
наблюдения |
наблюдения |
|
||||
п/п |
|
||||||
изделие |
изделие |
изделие |
изделие |
изделие |
изделие В, |
|
|
|
А , (x1) |
В, ( y1) |
А , (x2) |
В, ( y2) |
А , (x3) |
( y3 ) |
|
1 |
2 |
3 |
4 |
5 |
6 |
7 |
|
1 |
5 |
5 |
1 |
10 |
6 |
7 |
|
2 |
6 |
4 |
1 |
8 |
7 |
8 |
|
3 |
7 |
7 |
3 |
9 |
8 |
9 |
|
4 |
2 |
9 |
5 |
7 |
5 |
6 |
|
5 |
3 |
6 |
7 |
4 |
0 |
4 |
|
6 |
4 |
2 |
8 |
3 |
7 |
7 |
|
7 |
5 |
8 |
6 |
4 |
5 |
5 |
|
8 |
6 |
6 |
7 |
3 |
3 |
5 |
|
9 |
9 |
4 |
7 |
3 |
2 |
4 |
|
10 |
5 |
1 |
8 |
3 |
2 |
3 |
|
18
|
|
|
|
|
|
Окончание табл. 1 |
||
|
|
|
|
|
|
|
|
|
1 |
2 |
3 |
4 |
5 |
6 |
|
7 |
|
11 |
4 |
2 |
8 |
2 |
0 |
|
6 |
|
12 |
2 |
0 |
7 |
3 |
5 |
|
7 |
|
13 |
5 |
1 |
9 |
1 |
1 |
|
5 |
|
14 |
6 |
0 |
8 |
1 |
1 |
|
3 |
|
2.Провести стратификацию данных, приведенных в табл. 2, представив их виде табл. 3, на ее основе построить диаграмму стратификации (рисунок) и сделать выводы.
|
|
|
Таблица 2 |
|
|
Данные о причинах возникновения дефектов |
|||
|
|
|
|
|
Причины |
Количество |
Причины |
Количество |
|
дефектов |
дефектов |
дефектов |
дефектов |
|
Оборудование 1 |
5 |
Поставщик 2 |
8 |
|
Смена 2 |
7 |
Смена 2 |
4 |
|
Рабочий 3 |
2 |
Рабочий 2 |
2 |
|
Поставщик 1 |
3 |
Поставщик 2 |
1 |
|
Смена 1 |
4 |
Смена 2 |
2 |
|
Оборудование 3 |
7 |
Оборудование 1 |
4 |
|
Поставщик 2 |
9 |
Рабочий 3 |
5 |
|
Смена 2 |
5 |
Рабочий 1 |
7 |
|
Рабочий 4 |
8 |
Оборудование 1 |
1 |
|
Поставщик 1 |
4 |
Смена 2 |
3 |
|
Смена 1 |
6 |
Поставщик 1 |
5 |
|
Оборудование 3 |
3 |
Рабочий 1 |
6 |
|
Оборудование 1 |
8 |
Оборудование 1 |
9 |
|
Смена 2 |
7 |
Смена 2 |
7 |
|
Рабочий 1 |
2 |
Рабочий 4 |
8 |
|
Поставщик 1 |
9 |
Смена 1 |
5 |
|
Смена 1 |
5 |
Оборудование 2 |
2 |
|
Оборудование 2 |
6 |
Оборудование 1 |
5 |
|
Смена 2 |
7 |
Рабочий 2 |
4 |
|
Таблица 3
Стратификация данных
Оборудование |
Поставщик |
Рабочие |
Смена |
17 |
11 |
9 |
11 |
4 |
10 |
3 |
26 |
5 |
|
4 |
|
|
|
9 |
|
19