
Лекция 8. Футерование и плакирование деталей и аппаратов
.pdfЛекция 8.
ФУТЕРОВАНИЕ И ПЛАКИРОВАНИЕ ДЕТАЛЕЙ И АППАРАТОВ
8.1 Футерование листовым титаном
Титан - единственный материал, коррозионностойкий в средах, содержащих двуокись хлора, хлораты, гипохлориты и влажный хлор. Из-за высокой стоимости титана возможность его широкого применения для изготовления оборудования ограничена. Сокращение расхода титана достигается применением оборудования, футерованного листовым титаном.
Футеровка химического оборудования листовым титаном осуществляется следующими способами:
-вставным вкладышем;
-листом или сварной картой, согнутой в обечайку, с заваркой замыкающего стыка внутри аппарата на остающейся титановой подкладке;
-панелями (компенсаторами) с приваркой их к остающимся титановым подкладкам.
Для футеровки применяют титан марок ВТ 1-0 и ВТ 1-00. Детали, выполняемые методом, связанным с пластической деформацией заготовки, рекомендуется изготовлять из титана ВТ1-
00.Для футеровки аппаратов применяют титановые листы толщиной 1,5-2 мм и в отдельных случаях для аппаратов небольших размеров, работающих в менее активных средах, толщиной 1 мм; а для футеровки заготовок - толщиной до 5 мм.
При футеровке аппаратов вставным вкладышем вначале штампуют из сварных пакетных заготовок днища из титана. При этом одновременно получают днища из углеродистой стали для корпуса аппарата. Затем по фактическим размерам наружного диаметра титанового днища и внутреннего диаметра корпуса аппарата изготовляют титановую обечайку. Для этого заготовку из титана изгибают и на специальном стенде сваривают автоматической аргонодуговой сваркой. К титановой обечайке приваривают
64
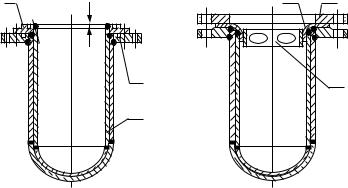
титановое днище ручной аргонодуговой сваркой без присадочного металла.
Корпус аппарата перед футеровкой тщательно очищают и обезжиривают. Титановую обечайку с приваренным днищем вставляют в корпус аппарата до плотного прилегания к поверхности днища из углеродистой стали. Затем на плоскость фланца, изготовленного из углеродистой стали, накладывают титановый фланец или воротник и плотно прижимают их винтами. После сборки титанового фланца или воротника с титановой обечайкой их сваривают.
Корпус аппарата с футеровкой из листового титана, выполненный способом «вставного вкладыша» со сваркой титановой обечайки с титановым днищем встык, показан на рисунке 8.1.
1 |
1-2 |
2 |
3 |
1 |
2 |
|
3 |
а) б) Рисунок 8.1 – Корпус аппарата с футеровкой из листового
титана, выполненной способом «вставного вкладыша» со сваркой титановой обечайки с титановым днищем встык:
а – с плоским титановым фланцем:
1 – титановый фланец; 2 – технологическая кольцевая канавка,
3– футеровка корпуса;
б– с титановым воротником, изготовленным из листовой заготовки
обкаткой:
1 – титановый воротник; 2 – технологический фланец; 3 – разжимное кольцо
65
Для упрощения технологии изготовления аппаратов целесообразно футеровать корпус, крышку и днище отдельно. В этом случае внутреннюю поверхность корпуса аппарата подвергают механической обработке и футеруют титановой обечайкой, предварительно сваренной на стенде автоматической сваркой. Титановую обечайку запрессовывают в корпус аппарата на прессе или на специальном приспособлении.
Футеровку фланцев из углеродистой стали титаном производят плоским титановым фланцем или воротником, выполненным из листового титана. Футеровка углеродистых фланцев плоскими титановыми фланцами менее трудоемка по сравнению со вторым способом футеровки воротником, обеспечивает наиболее надежную конструкцию и применяется при изготовлении аппаратов, работающих под давлением.
Плоские титановые фланцы изготовляют из полосового проката или нарезанных из листов полос. Гибку полос ведут в штампе или на профилегибочных машинах. Рабочую полость штампа и канавки в валках выполняют соответственно профилю обрабатываемой полосы. При необходимости гибки полос с относительно небольшой толщиной гнут одновременно несколько заготовок. Согнутые полосы сваривают встык.
При изготовлении емкостей и аппаратуры, футерованной листовым титаном и работающей при давлении 0,7 кгс/см2 углеродистые фланцы футеруют титановыми воротниками. Воротники изготовляют из цилиндрической сварной заготовки на карусельных станках в приспособлении или штамповкой из плоской кольцевой заготовки. Вторым способом получают более широкую отбортованную часть воротника, но расходуют значительно больше листового титана.
Длину развертки титановой обечайки принимают по фактическим размерам диаметра корпуса аппарата после механической обработки. Заготовку титановой обечайки вставляют внутрь корпуса, разжимают специальными кольцами, тщательно пригоняют кромки и прихватывают сваркой. После этого обечайку вы-
66
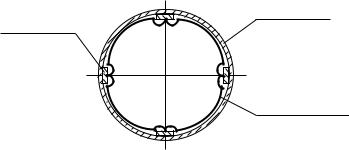
нимают из корпуса и сваривают продольный шов на стенде автоматической сварки. Сваренную обечайку запрессовывают в корпус и приваривают к титановым фланцам, укрепленным на фланцах из углеродистой стали корпуса аппарата. После приварки титановой обечайки обрабатывают привалочные плоскости (шип и паз) титановых фланцев.
Так как аппараты, футерованные указанным способом, изготовляют небольших диаметров, крышки для них целесообразнее выполнять методом пакетной штамповки. В этом случае из отштампованной пакетной заготовки после подрезки торцов вынимают только внутреннее днище из углеродистой стали. Титановое днище, выполняющее функцию футеровки, приваривают к титановому фланцу, прикрепленному к фланцу днища из углеродистой стали.
Футеровку с компенсаторами применяют для изготовления аппаратуры больших габаритных размеров. Футеровка данным методом производится отдельными панелями, размеры которых зависят от габаритных размеров аппарата и размера титановых листов. Панели имеют по продольным стыкам отогнутые кромки, которые после сварки служат компенсаторами. Высота отогнутой кромки и радиус ее закругления зависят от толщины футеровки
(рис. 8.2).
Титановая |
Обечайка |
подкладка |
|
Компенсатор
Рисунок 8.2 – Футеровка с компенсаторами
67
Количество компенсаторов, необходимое для футеровки аппарата, зависит от внутреннего диаметра, высоты корпуса и температуры среды в аппарате.
Толщина |
Радиус закругления |
Высота отогнутой |
|
футеровки, мм |
кромки, мм |
кромки, мм |
|
1 |
10 до |
20 |
3 |
1,5 |
св. 20 до 25 |
5 |
|
2 |
св. 25 |
до 30 |
6 |
Количество компенсаторов принимают из следующего расчета: один компенсатор может снять разницу в расширении между футеровкой и корпусом в 1,5-2 мм. При этом для аппаратов, работающих при резких колебаниях температур и давлений, количество компенсаторов в футеровке принимают по меньшему значению компенсирующей способности одного компенсатора.
8.2 Плакирование элементов аппаратов
При плакировании заготовок из стали латунью ЛО-62-1 толщина слоя латуни должна быть в готовом изделии не менее 10 мм, поэтому плакирование производится из расчета получения слоя латуни толщиной 20 мм. Для предотвращения окисления латуни применяется флюс следующего состава (%):
-техническая бура - 50;
-борная кислота - 25;
-плавиковый шпат - 25.
Бура и борная кислота переплавляются для полного удаления из них влаги, плавиковый шпат прокаливается. Бура и борная кислота в виде стекловидной массы и плавиковый шпат после остывания перемалываются по отдельности и хранятся в стеклянной посуде с притертыми пробками. Флюсы, повторно использованные, дают лучшие результаты, чем вновь приготовленные.
Для увеличения поверхностного сцепления наплавленного и основного металлов на поверхности трубной решетки прота-
68
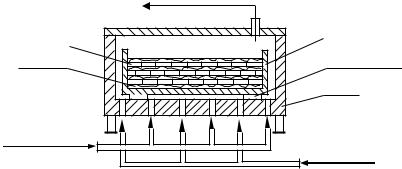
чиваются кольцевые риски глубиной 1-1,5 мм с шагом 8 мм.
Для плакирования применяется листовая латунь, нарезанная кусками размером не более 100x100 мм и обезжиренная промывкой в ацетоне непосредственно перед плакированием, которое производится в газовой печи. Заготовка устанавливается на опорах в печь, обезжиривается ацетоном и проверяется на горизонтальность поверхности по уровню (рис. 8.3).
После удаления ацетона на всю поверхность решетки равномерно насыпают флюс слоем толщиной 6-8 мм. На поверхности флюса укладываются ровными рядами вплотную один к другому куски латуни из расчета толщины наплавляемого слоя 20 мм. Между слоями и на поверхность латуни насыпают флюс слоем 3-4 мм толщиной.
|
Отходящие газы |
Латунь |
Заготовка |
|
|
Флюс |
Подкладки |
|
Печь |
Природный газ |
|
|
Воздух |
Рисунок 8.3 – Установка для плакирования заготовок латунью
Температура в печи в течение 1 ч медленно поднимается до 400-450°С, затем газовые горелки открываются полностью. Процесс ведется при температуре 950-1050°С до полного расплавления латуни. Температура контролируется термопарой и потенциометром. В момент расплавления последнего куска латуни в печь вводится приспособление для обдува заготовки снизу сжатым воздухом, после чего горелки гасятся. Обдув обеспечивает направленную кристаллизацию жидкой латуни. Плакирование в печи длится 3-4 ч.
69
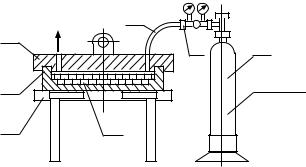
Качество плакирования проверяется визуально. Отслаивание выявляется простукиванием со стороны наплавленного слоя молотком. Браковочным признаком является глухой звук. Газовые раковины и другие дефекты после механической обработки не допускаются и устраняются повторной переплавкой латуни.
Принципиальное отличие метода плакирования заготовок в среде аргона состоит в исключении применения флюсов, роль которых выполняет инертная среда (рис. 8.4).
|
Воздух |
5 |
|
|
|
|
|
4 |
|
|
7 |
|
|
6 |
|
2 |
|
|
Аргон |
|
|
|
|
1 |
|
3 |
|
Рисунок 8.4 – Схема установки для создания инертной среды при плакировании заготовок латунью
На стол 1 устанавливают предварительно обезжиренную ацетоном или бензином заготовку 2. На наплавляемую поверхность заготовки ровными слоями укладывают куски латуни 3, после чего заготовки покрывают специальной крышкой 4 с двумя отверстиями 10 мм, необходимое условие при этом - плотное прилегание крышки к заготовке. Через одно из отверстий с помощью резинового шланга 5 через редукционный клапан 6 из баллона 7 в пространство под крышку нагнетается аргон под давлением 0,3-0,4 атм., а через другое - аргоном вытесняется воздух. После полного вытеснения воздуха (о чем судят по угасанию поднесенного ко второму отверстию зажженного запальника) подачу аргона прекращают, а отверстия в крышке заглушают огне-
70
упорной глиной.
В таком виде заготовка подается на нагрев. Положительной стороной этого метода является и то, что он не требует специального нагревательного агрегата. Качество плакирования обеспечивается при нагреве в любой печи, где можно получить температуру до 1000°С. Заготовка устанавливается в строго горизонтальном положении с помощью специального механизма, предусмотренного конструкцией печи, или вручную с использованием стальных или асбестовых прокладок. Заготовку нагревают до температуры 950-1000°С с выдержкой не менее 1ч. После этого печь отключают и заготовка, во избежание расплескивания расплавленной латуни при транспортировке и для получения равномерного слоя латуни по высоте, охлаждается до 600°С в печи. Дальнейшее ее охлаждение происходит на воздухе.
71