
- •Содержание
- •1.11.1 Описание конструкции и принцип работы станочного приспособления
- •4 Обоснование экономической эффективности разработанного варианта технологического процесса
- •4.1 Подготовка исходных данных для сравнения вариантов технологического процесса
- •4.2 Определение себестоимости машино-часа работы оборудования
- •4.3 Определение технологической себестоимости детали по вариантам техпроцесса
- •4.4 Определение показателей экономической эффективности спроектированного варианта технологического процесса
- •5 Технико-экономические показатели производственного участка
- •Список литературы:
1.11.1 Описание конструкции и принцип работы станочного приспособления
В проектируемом технологическом процессе на операцию 45 используется цанговая концевая оправка с пневмоприводном, предназначенная для комплексной обработки на токарном станке, а именно фрезерования 4 выборок, наружного точения, точения конической поверхности фланца и сверления 24 отверстий.
Данная оправка соединяется с переходным фланцем 8, установленным на шпинделе станка. Работа оправки осуществляется следующим образом. В исходном состоянии клин 4 находится в крайнем правом положении, а цанга 17 освобождена от упругих деформаций. Обрабатываемая заготовка свободно (с зазором) устанавливается на наружную цилиндрическую часть цанги до упора в планшайбу 15. Затем с помощью пневмопривода 1, установленного на заднем конце шпинделя передней бабки станка и закреплённым клемовым зажимом 3, шток 18 перемешается влево, и за счет наличия конусов на деталях 15 и 4, цанга разжимается и фиксирует заготовку по отверстию.
Для подвода сжатого воздуха к вращающемуся цилиндру применяется муфта двустороннего действия. Принцип её действия следующий: воздух поступает в рабочие полости цилиндра и выходит в атмосферу поочередно через сопла 12, во избежание просачивания воздуха между внутренней поверхностью муфты и воздуховодом 14 помещаются кольцевые манжеты 20. Наличие шарикоподшипника 20 позволяет применять муфту на станках, работающих с повышенной частотой вращения.
Приспособление отличается простотой конструкции, удобством в эксплуатации, необходимой точностью и надежностью закрепления.
-
Расчет приспособления на точность
а) Изображаем теоретическую и практическую схемы базирования:
Точки 1,2,3,4 лишают заготовку четырех степеней свободы: перемещений вдоль оси OZ и OY и вращений вокруг этих осей. Точка 5 лишает заготовку 1-ой степени свободы – вращения вокруг оси OX. Точка 6 лишает заготовку 1-ой степени свободы – перемещения вдоль оси OX. |
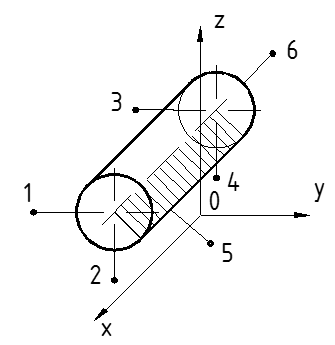
Рисунок 1.11.1 – Теоретическая схема базирования
Точки 1,2,3,4 - двойная направляющая база Точки 5,6 - опорные базы |
Рисунок 1.11.2 – Практическая схема базирования
б) Проверяем приспособление на точность
Уравнение соблюдения условия точности:
,
(1.11.1)
где
- допуск на размер детали, точность
выполнения которого зависит от точности
применяемого приспособления,
(данные из технологии).
- допуск на неточность
изготовления установочных элементов
приспособления, влияющий на точность
обработки, вычисляется по формуле
(1.11.2);
- погрешность,
зависящая от метода обработки заготовки,
([2], стр. 19);
–
погрешность
установки, мм; вычисляется
по формуле (1.11.3):
,
(1.11.2)
,
(1.11.3)
где
–
погрешность закрепления, мм;
=
0,03 мм, ([2], стр. 45);
–
погрешность
базирования,
=0
мм;
Подстановкой значений в формулы (1.11.3), (1.11.2), (1.11.1) получено:
мм
мм.
Вывод: условие соблюдается, т.е. точность обеспечивается
1.11.3 Расчёт зажимного усилия заготовки в приспособлении
При закреплении детали в приспособлении должны соблюдаться следующие правила:
-
не должно нарушаться положение детали, достигнутое при её базировании;
-
закрепление должно быть надёжным, чтобы во время обработки положение детали оставалось неизменным;
Для расчета сил закрепления приспособления необходимо знать условия обработки - величину, направление и место приложения сил, сдвигающих заготовку, также схему ее установки и закрепления. Расчет сил закрепления может быть сведен к задаче статики на равновесие заготовки под действием приложенных к ней внешних сил.
а) Изображают схему сил, действующих на заготовку:
Рисунок 1.10.1 - Схема сил, действующих на заготовку
Под действием окружной силы Pу заготовка пытается провернуться вокруг своей оси, этому препятствуют силы трения в местах контакта заготовки с лепестками цанги.
б) Расчёт производят следующим образом:
,
(1.11.4)
Отсюда следует:
,
(1.11.5)
где Q – сила зажима, Н;
К – коэффициент запаса, К = 2…2,5 – лезвийная обработка, принимаю К = 2;
f – сила трения в местах контакта заготовки с приспособлением, Н;
f = (0,5…0,6), применяем f = 0,6 Н;
D = 232 мм [чертеж детали];
d = 60 мм [чертеж детали];
Pу – окружная сила резания, Н; находится по формуле
,
(1.11.6)
где Сp = 204, ([6], стр. 371);
x = 1, ([6], стр. 371);
y = 0,75, ([6], стр. 371);
n = 0, ([6], стр. 371);
t – глубина резания, t = 3 мм;
S
– подача, S
= 0,1;
Кр – коэффициент, учитывающий фактические условия резания:
,
(1.11.7)
где Кφ = коэффициент, учитывающий главный угол в плане, Кφ = 1;
Кγ = коэффициент, учитывающий передний угол, Кγ = 1;
Кλ = коэффициент, учитывающий угол наклона лезвия, Кλ = 1;
Кr = коэффициент, учитывающий радиус при вершине, Кr = 0,93;
Кмр – коэффициент, учитывающий влияние обрабатываемого материала:
,
(1.11.8)
где пр – показатель степени, пр = 0,75 [6, стр. 412];
Подставив значения в формулы (1.11.8), (1.11.7), (1.11.6), (1.11.5) получаем:
1,147;
;
Н;
Н.
в) Определяют исходное усилие приспособления:
Рисунок 1.10.2 – Схема действия привода
В данном приспособлении применяют цанговый зажим с пневматическим приводом двухстороннего действия. Исходное усилие определим по формуле (1.11.9):
,
(1.11.9)
где
-
исходное усилие, Н;
Q- зажимное усилие, Q=16089,045 Н;
α- половина угла корпуса цанги, α=15º;
-
угол трения между цанговой и корпусом,
=8.53º
,
(1.11.10)
где Е-
модуль упругости материала цанги, Е=2×
МПа;
L- длина лепестков цанги от места заделки до середины конуса, L= 90 мм;
n- число лепестков в цанге, n = 4;
y – стрела прогиба, т.е радиальный зазор между цангой и заготовкой;
I
– момент инерции сектора сечения цанги
в месте заделки лепестка,
,
(1.11.11)
где D = диаметр в месте заделки лепестка цанги; D = 60 мм;
h- ширина лепестков цанги, h = 4мм;
-
половина угла лепестка цанги,
=
45º;
(1.11.12)
где Smin – минимальный зазор в посадке заготовки на оправку, Smin = 0.025мм;
Подставив значения в формулы (1.11.12), (1.11.11), (1.11.10), (1.11.9) получаем:
;
мм4;
Н;
Н
г) Размеры пневмокамеры диаметра пневмоцилиндра двухстороннего действия вычисляется по формуле:
Тянущая сила
,
(1.11.13)
Отсюда следует:
,
(1.11.14)
где Ри - исходное усилие, Н;
диаметр поршня,
мм;
диаметр штока, d
= 20 мм;
давление сжатого
воздуха, Мпа;
МПа, принимаю
;
КПД,
.
Подстановкой значений в формулу (1.11.14) получено:
мм
1.12 Описание конструкции и расчет контрольно-измерительной оснастки
1.12.1 Описание конструкции и принцип работы
Контрольно-измерительное приспособление, предназначенное для контроля торцевого и радиального биения отверстия наружной цилиндрической поверхности и прилегающего торца детали после шлифования.
Контролируемое изделие устанавливается вручную на цангу с продольными прорезями 36, перемещаясь с помощью гайки 39 по конусу 35, упруго разжимается и закрепляет деталь 38. Штифт 37 удерживает цангу от поворота, а гайка 40 служит для отжатия при снятии.
Сама оправка устанавливается в центрах 5 и 6, которые монтируются в передней и задней стойках 2 и 9 соответственно, установленных на общей плите 1. Стойка 2 неподвижная, крепится болтами 14 и штифтами 13 к плите. Стойка 9 перемещается по плите и крепится на ней при помощи рукоятки 22 и винта с прямоугольной головкой 16 в направляющей, выравнивается при этом по планке. Центр 6 находятся под постоянным действием сжатой пружины 10 и при раскручивании гайки 12 он зажимает оправку, после чего стопорится винтом 7.
В пазу плиты 1 устанавливается стойка 32 и прижимается гайкой 34, на ней при помощи разжимных втулок 42 крепятся стержни 41 с вилками 45, в которых зажимаются ножки индикаторов 46 винтами 44. Деталь в ручную вращается на оправке и ножки индикаторов, контактируют с контролируемыми поверхностями. Стрелка покажет отклонение от контролируемого параметра.
Настройка индикатора настраивается по эталону детали. После проверки эталон снимается, смотрят контролируемый размер.
Приспособление дополнено измерителями не только для радиального, но и - для торцового биений. Такая комплексная проверка даст высокую производительность процесса контроля.
1.12.2 Расчет контрольно-измерительного приспособления на точность
Расчет суммарной погрешности измерения и сравнение ее с допуском контролируемого параметра. Должно выполняться следующее условие:
или
,
(1.12.1)
где IT- допуск на контролируемый размер; IT=0,01
Суммарная погрешность измерения на контрольно-измерительных приспособлениях определяется по формуле:
,
(1.12.2)
где
погрешность
изготовления, установочных элементов,
мм;
,
принимается
;
погрешность,
вызванная неточностью изготовления
передаточных элементов, мм; принимается
;
погрешность,
учитывающая отклонения установочных
размеров от номинальных, мм ([2],таблица
1); принимается
погрешность
базирования, мм;
погрешность
смещения измерительной базы контролируемой
детали относительно рабочих поверхностей
установочных элементов, мм;
,
принимается
;
погрешность
закрепления детали в КИП, мм ([2],таблица
2);
,
принимается
;
погрешность от
зазоров между осями рычагов, мм;
погрешность при
настройке КИП на размер из-за искажения
геометрической формы эталонной детали,
мм ([2],таблица 4);
,
принимается
;
погрешность метода
измерения, мм ([2],таблица 5);
,
принимается
.
Подстановкой значений в формулу (1.12.2) и затем в (1.12.1) получено:
мм
Условие выполняется, следовательно, приспособление обеспечивает необходимую точность измерений.
1.13 Выводы по технической части проекта
Методы обработки, применяемые в технологическом процессе, влияют на качество обработки детали. К передовым методами, применяемых в данном технологическом процессе, можно отнести:
1. Применение метода получения заготовки – штамповка на ГКМ. Данный метод получения заготовки позволит получить заготовку с наименьшими затратами на изготовления детали в целом.
2. Применение станков с ЧПУ на токарных операциях.
Эти станки имеют ряд преимуществ по сравнению с другими станками: производительность станков с ЧПУ в 1,5-2,5 раза выше, по сравнению с универсальными станками.
Применение токарно-фрезерного станка ЧПУ позволило объединить ряд токарных операции в одну, что повысило производительность технологического процесса, точность, т.к. уменьшилось количество переустановок, а также позволило отказаться от применения токарного-винторезного станка.
3. Применение внутришлифовального станка с круглошлифовальным приспособлением позволило объединить операции наружного и внутреннего шлифования в одну, тем самым сократить количество применяемого оборудования.
4. Применение специального контрольно-измерительного приспособления позволит максимально эффективно контролировать послеоперационные размеры.
5. Применение специального станочного приспособления на токарно-фрезерном станке позволяет проводить сверление, фрезерование точение на одной операции. Это также позволит повысить производительность труда, снизит трудоемкость изготовления детали и улучшит условия работы.
В результате увеличится производительность труда за счет снижения времени обработки детали, это приведет к снижению себестоимости детали.
Для наглядного представления о перечне внесенных изменений в технологический процесс составляем таблицу 1.13.1
Таблица 1.13.1 - Сравнение технологических маршрутов
№ оп. |
Заводской вариант (наименование операции) |
Оборудование |
№ оп. |
Проектный вариант (наименование операции) |
Оборудование |
00 |
Заготовительная |
Молот |
00 |
Заготовительная |
ГКМ |
05 |
Нормализация |
Печь |
05 |
Нормализация |
Печь |
15 |
Токарная с ЧПУ |
DF2CNC |
10 |
Токарная с ЧПУ |
DF2CNC |
20 |
Токарная с ЧПУ |
DF2CNC |
15 |
Токарная с ЧПУ |
DF2CNC |
25 |
Контрольная |
Стол ОТК |
20 |
Контрольная |
Стол ОТК |
30 |
Закалка |
Печь |
25 |
Закалка |
Печь |
35 |
Токарная с ЧПУ |
DF2CNC |
30 |
Токарная с ЧПУ |
DMC DL 21MB |
40 |
Токарная с ЧПУ |
DF2CNC |
35 |
Токарная с ЧПУ |
DMC DL 21MB |
45 |
Токарная с ЧПУ |
DF2CNC |
40 |
Шлифовальная |
Si6/1 ASA 315 |
50 |
Круглошлифовальная |
BU28x1000 |
45 |
Долбёжная |
7Д430 |
55 |
Токарная |
1К62Д |
50 |
Токарно-фрезерная с ЧПУ |
DMC DL 21MB |
60 |
Внутришлифовальная |
3М227ВФ2 |
55 |
Слесарная |
Верстак |
65 |
Долбёжная |
В-5020 |
60 |
Токарная с ЧПУ |
DMC DL 21MB |
70 |
Токарная |
1К62Д |
65 |
Слесарная |
Верстак |
75 |
Токарная |
1К62Д |
70 |
Промывка |
Ванна моечная |
80 |
Внутришлифовальная |
3М227ВФ2 |
75 |
Контроль магнитный |
Стол ОТК |
85 |
Специальная фрезерная |
ГФ – 2171С6 |
80 |
Операционный контроль |
Стол ОТК |
90 |
Токарная с ЧПУ |
DF2CNC |
85 |
Пассивирование |
Устройство |
95 |
Токарная с ЧПУ |
DF2CNC |
90 |
Приемочный контроль |
Стол ОТК |
100 |
Спец. фрезерная |
ГФ – 2171С6 |
95 |
Транспортирование |
Электрокар |
105 |
Слесарная |
Верстак |
|
|
|
Продолжение таблицы 1.13.1 |
|||||
№ оп. |
Заводской вариант (наименование операции) |
Оборудование |
№ оп. |
Проектный вариант (наименование операции) |
Оборудование |
110 |
Промывка |
Ванна моечная |
|
|
|
115 |
Контроль магнитный |
Стол ОТК |
|
|
|
120 |
Операционный контроль |
Стол ОТК |
|
|
|
125 |
Пассивирование |
Устройство |
|
|
|
130 |
Приемочный контроль |
Стол ОТК |
|
|
|
135 |
Транспортирование |
Электрокар |
|
|
|
Для обоснования целесообразности внедрения варианта технологического процесса проводится сравнение вариантов технологического процесса и расчёт показателей экономической эффективности экономически выгодного варианта.
2 Организация работы производственного участка
Без новейших технологий остановился бы технический прогресс. Каждая из новейших разработок имеет свои особенности и определенный потенциал. Одни могут лишь незначительно улучшить существующие решения, другие способны совершить настоящий переворот в той или иной отрасли.
Использование перспективных технологий ведет к увеличению объема производства и более эффективному использованию природных и материальных ресурсов, энергии, необходимых для реализации производственных процессов, а главное экономии времени. Обработка деталей, имеющих сложные поверхности, производятся обычно на станках с ЧПУ, использованием приспособлений и наладок и многими другими способами. Благодаря новым технологиям достигается сокращение трудоемкости изготовления деталей, позволяет снизить разряд рабочего персонала и уменьшить его количество, т.к. это оборудование может обслуживать один оператор.
Технологический процесс должен обеспечивать качественное изготовление деталей и изделия в целом с минимальными затратами времени и средств с максимальной механизацией и автоматизацией процесса труда, с тем, чтобы продукция получалась с минимальной себестоимостью.
Сопоставление экономичности технологических вариантов и расчеты себестоимости обработки и технологической оснастки являются обязательной частью проектирования технологических процессов. Цель данной работы - обосновать экономическими расчетами проект организации участка изготовления детали «Стакан»; доказать, что разработанный вариант технологического процесса экономически более выгоден, чем базовый.
-
Определение годовой приведённой программы, уточнение и расчёт коэффициента закрепления операции и оптимальной партии.
2.1.1 Обоснование типа производства
Для обоснования типа производства определяется коэффициент закрепления операций Кзо по формуле:
,
(2.1.1)
где
-
действительный фонд времени работы
единицы оборудования, час/год;
= 4055 час/год, ([5], приложение 1);
- годовая программа
запуска детали, шт.;
- среднее штучное
время технологического процесса, мин.
Среднее штучное время разработанного технологического процесса определяется по формуле:
,
(2.1.2)
где
- суммарное штучное время технологического
процесса, мин;
О – количество операций технологического процесса.
При подстановке в формулу (2.1.2) получаем:
мин
Для расчета Кзо, определяем годовую программу запуска детали по формуле:
=
,
(2.1.3)
где
- годовая программа выпуска детали, шт;
а - коэффициент, учитывающий выпуск деталей на запасные части, %;
b - коэффициент, учитывающий неизбежные потери, %;
принимаем a = 2%;
принимаем b = 0,2%, [5].
При подстановке в формулу (2.1.3) получаем:
шт.
Подстановкой в формулу (2.1.1) получаем:
В соответствии с ГОСТ 31108-74 на участке крупносерийное производство.
2.1.2 Определение годового приведённого объёма производства
Приведённая производственная программа определяется по детали-представителю с учетом коэффициента трудоемкости Кт, который показывает долю трудоемкости заданной детали от трудоемкости всей годовой программы участка. Коэффициент трудоемкости определяется по формуле:
,
(2.1.4)
где
- нормативное число
единиц оборудования на участке, шт;
принимаем
= 25 станков.
Годовая приведённая производственная программа запуска определяется по формуле:
Nпр
,
(2.1.5)
При подстановке в формулу (2.1.4) получаем:
При подстановке в формулу (2.1.5) получаем:
Nпр
шт.
Принимаю Nпр= 13363 шт.
2.1.3 Определение размера партии деталей
Для расчета оптимального размера партии запуска детали определяется длительность выполнения месячной производственной программы tмес по формуле:
,
(2.1.6)
где
.
–
норма штучного
времени ведущей операции тех. процесса,
мин;
- длительность
смены, мин;
= 480 мин.
Ведущей операцией
технологического процесса является
та, в которой отношение: Тп-з / Тшт = max.
В данном технологическом процессе
ведущей операцией является долбёжная
операция 45.
=
2,57 мин.
смены
Пользуясь таблицей приложения 2 [5], определяю размер оптимальной партии детали. Он соответствует значению унифицированного ряда периодичности запуска (выпуска) – М. Это значит, что оптимальная партия равна месячной производственной программе.
Оптимальный размер партии определяется по формуле:
nопт
=,
(2.1.7)
При подстановке в формулу (2.1.7) получаем:
nопт
=
шт.
2.2 Определение необходимого количества оборудования на участке механического цеха
2.2.1 Расчёт норм штучно-калькуляционного времени
Нормы штучно - калькуляционного времени определяются по формуле:
,
(2.2.1)
где Тп-з – норма подготовительно-заключительного времени, мин.
При подстановке в формулу (2.1.8) получаем:
мин.
мин.
мин.
мин.
мин.
мин.
мин.
мин.
Результаты расчетов занесены в таблицу 2.1.1
Таблица 2.2.1 – Расчёт норм штучно-калькуляционного времени
№ опер. |
Наименование операции |
Тшт, мин. |
Тп-з, мин. |
nопт, шт |
Тшт-к, мин |
1 |
2 |
3 |
4 |
5 |
6 |
10 |
Токарная с ЧПУ |
87,25 |
30 |
341 |
87,33 |
15 |
Токарная с ЧПУ |
139,81 |
30 |
341 |
139,89 |
30 |
Токарная с ЧПУ |
37,14 |
30 |
341 |
37,22 |
35 |
Токарная с ЧПУ |
82,43 |
30 |
341 |
82,51 |
40 |
Шлифовальная |
10,80 |
30 |
341 |
10,89 |
45 |
Долбёжная |
2,57 |
26 |
341 |
2,62 |
50 |
Токарно – фрезерная с ЧПУ |
79,82 |
19 |
341 |
79,92 |
60 |
Токарная с ЧПУ |
15,01 |
16 |
341 |
15,08 |
|
Итого |
454,83 |
– |
– |
455,442 |
2.2.2 Определение загрузки оборудования в соответствии с плановыми нормами
Расчёт плановой загрузки оборудования производится по моделям оборудования по формуле:
,
(2.2.2)
где
- суммарное время обработки детали на
станке данной модели, мин.
При подстановке в формулу (2.1.9) получаем:
-
нормо-часы
-
нормо-часы
-
нормо-часы
-
нормо-часы
Результаты расчетов занесены в таблицу 2.1.2
Таблица 2.2.2 – Расчёт потребного количества оборудования и коэффициентов его загрузки
Наименование и модель станка |
№ оп. |
∑Тшт-к |
Qплан |
Квн |
Qфакт |
FД |
Кол-во станков |
Кз |
|
Расч. |
Прин. |
||||||||
1 |
2 |
3 |
4 |
5 |
6 |
7 |
8 |
9 |
10 |
Токарный с ЧПУ модели DF2 CNC |
15,30 |
227,22 |
50604,58 |
1 |
50604,57 |
3935 |
12,860 |
13 |
0,989 |
Токарный с ЧПУ модели DMC DL 21MB |
30,35,50,60
|
214,73 |
47822,17 |
1 |
47822,17 |
3935 |
12,153 |
13 |
0,935 |
Внутришлифовальный модели Si6/1 ASA 315 |
40 |
10,89 |
2424,94 |
1,04 |
2331,68 |
4055 |
0,575 |
1 |
0,575 |
Долбёжный модели 7Д430 |
45 |
2,62 |
582,85 |
1,04 |
560,43 |
4055 |
0,138 |
1 |
0,138 |
Итого: |
- |
455,44 |
101434,5 |
- |
101318,8 |
- |
25,5 |
28 |
Кзср 0,659 |
2.2.3 Определение пропускной способности оборудования (фактической загрузки) с учётом планового перевыполнения норм выработки
Фактическая загрузка оборудования рассчитывается по формуле:
,
(2.2.3)
где
- плановый коэффициент выполнения норм
выработки рабочими участка.
Принимаю:
-
для универсальных станков -
=1,04
-
для станков с ЧПУ
=1
При подстановке в формулу (2.2.3) получаем:
-
станко-часы
-
станко-часы
-
станко-часы
-
станко-часы
Результаты расчетов занесены в таблицу 2.2.2
2.2.4 Определение потребного количества оборудования и коэффициентов его загрузки
Рассчитываю количество станков по каждой модели по формуле:
,
(2.2.4)
где
-
действительный
годовой фонд времени работы единицы
оборудования, часов:
-
для универсальных станков Fд=4055 часов ([5],приложение 1)
-
для станков с ЧПУ Fд=3935 часов ([5],приложение 1)
При подстановке в формулу (2.2.4) получаем:
-
станков, (принимаем 13 станков)
-
станков, (принимаем 13 станков)
-
станка, (принимаем 1 станок)
-
станка, (принимаем 1 станок)
Результаты расчетов занесены в таблицу 2.2.2
Коэффициент загрузки оборудования определяется по моделям станков по формуле:
,
(2.2.5)
где
- расчётное
количество станков данной модели, шт.;
- принятое количество
станков данной модели, шт.
При подстановке в формулу (2.2.5) получаем:
Результаты расчетов занесены в таблицу 2.2.2
Средний коэффициент загрузки оборудования на участке определяется по формуле:
,
(2.2.6)
где
- суммарное расчётное количество станков,
шт.;
- суммарное приятое
количество станков на участке, шт.
При подстановке в формулу (2.2.6) получаем:
По результатам расчётов числа станков по каждой модели, занесённым в таблицу 2.2.2 и определения коэффициентов загрузки оборудования строится график загрузки оборудования участка.
Рисунок 2.2.1 – График загрузки оборудования участка
Ведомость применяемого оборудования составляется на основании расчётов таблицы 2.2.2
Цены применяемого оборудования взяты из ([5],приложение Ж). Мощность применяемого оборудования взята из ([5],приложение Ж).
Таблица 2.2.3 – Ведомость применяемого оборудования
Наименование оборудования |
Модель |
№ опер. |
Кол-во |
Мощность, кВт |
Цена, тыс.руб |
||
Одного станка |
Всех станков |
Одного станка |
Всех станков |
||||
1 |
2 |
3 |
4 |
5 |
6 |
7 |
8 |
Токарный станок с ЧПУ |
DF2 CNC |
15,20 |
13 |
29,5 |
383,5 |
900 |
11700 |
Токарный станок с ЧПУ |
DMC DL 21MB |
30,35,50,60 |
13 |
11 |
143 |
2500 |
32500 |
Внутришли-фовальный |
Si6/1 ASA 315 |
40 |
1 |
16 |
16 |
400 |
400 |
Долбёжный |
7Д430 |
45 |
1 |
10 |
10 |
630 |
630 |
Итого |
- |
- |
28 |
67 |
553 |
4430 |
45230 |
2.2.5 Определение производственной площади, занимаемой оборудованием
Размер производственной площади, занимаемой оборудованием, с учётом проходов и проездов в соответствии с требованиями техники безопасности и промышленной санитарии, определяется по формуле:
,
(2.2.7)
где
- площадь, занимаемая одним станком,
рассчитанная по габаритным
размерам станка,
м2;
- коэффициент,
учитывающий дополнительную площадь,
[5,приложение 3];
- количество станков
данной модели, станков.
При подстановке в формулу (2.2.7) получаем:
-
м 2
-
м 2
-
м 2
-
м 2
Результаты расчетов занесены в таблицу 2.4
Таблица 2.2.4 – Расчёт производственной площади
Вид оборудования |
Модель станка |
Кол-во станков |
Габаритные размеры станков, м |
Площадь станка, м2 |
Коэффициент, учитывающий площадь |
Площадь Оборудования, м2 |
|
|
1 |
2 |
3 |
4 |
5 |
6 |
7 |
|
|
Токарный с ЧПУ |
DF2 CNC |
13 |
5х2,2 |
11,00 |
3,5 |
500,50 |
|
|
Токарный с ЧПУ |
DMC DL 21MB |
13 |
2,65х1,17 |
3,09 |
4,5 |
180,60 |
|
|
Внутришлифовальный |
Si6/1 ASA 315 |
1 |
3,5х2,4 |
8,40 |
4 |
33,60 |
|
|
Долбёжный |
7Д430 |
1 |
3,3х2,18 |
7,18 |
4 |
28,71 |
|
|
Итого |
- |
28 |
- |
29,66 |
- |
743,41 |
|
2.3 Определение численности производственных и вспомогательных рабочих
2.3.1 Расчёт численности основных рабочих-сдельщиков
Численность рабочих-сдельщиков определяется на основе трудоёмкости производственной программы по формуле:
,
(2.3.1)
где
- эффективный фонд времени одного
рабочего, час/год;
принимается равным
1860 час/год ([5], стр.20).
При подстановке в формулу (2.8) получаем:
человек;
человек;
человек;
человека.
Результаты расчетов занесены в таблицу 2.3.1
Таблица 2.3.1 – Расчёт численности основных рабочих-сдельщиков
Профессия |
№ оп. |
Qфакт, ст - час |
Час/год |
Численность рабочих |
|
расчётная |
принятая |
||||
1 |
2 |
3 |
4 |
5 |
6 |
Оператор токарного станка с ЧПУ 4 разряда |
10, 15 |
50604,567 |
1860 |
27,21 |
28 |
Оператор токарно - фрезерного станка С ЧПУ 4 разряда |
30, 35, 50, 60 |
47822,168 |
1860 |
25,71 |
26 |
Шлифовщик универсал 5 разряда |
40 |
2331,672 |
1860 |
1,25 |
2 |
Долбёжник универсал 4 разряда |
45 |
560,432 |
1860 |
0,30 |
1 |
Итого |
- |
- |
- |
54,47 |
57 |
Списочная численность основных производственных рабочих учитывает плановые невыходы на работу по причинам отпусков, болезней, выполнения государственных обязанностей и определяется по формуле:
,
(2.3.2)
где
- коэффициент потерь, учитывающий
плановые невыходы на работу;
= 1,1…1,2. [5,стр.21];
принимаю
=1,2.
При подстановке в формулу (2.9) получаем:
человека
Составляем ведомость состава основных производственных рабочих.
Таблица 2.3.2 – Ведомость состава производственных рабочих участка
Профессия |
Численность рабочих |
Средний разряд |
Средний тарифный коэффициент |
||||||||||
Всего |
в том числе по сменам |
в том числе по разрядам |
|||||||||||
1-ая чел. |
2-ая чел. |
ІІ |
ІІІ |
ІV |
V |
VІ |
|||||||
тарифные коэффициенты |
|||||||||||||
1,089 |
1,209 |
1,358 |
1,552 |
1,806 |
|||||||||
1 |
2 |
3 |
4 |
5 |
6 |
7 |
8 |
9 |
10 |
11 |
|||
оператор |
59 |
30 |
29 |
- |
- |
59 |
0 |
- |
- |
- |
|||
шлифовщик |
2 |
1 |
1 |
- |
- |
0 |
2 |
- |
|||||
долбёжник |
2 |
1 |
1 |
- |
- |
2 |
0 |
- |
|||||
ИТОГО |
63 |
32 |
31 |
- |
- |
61 |
2 |
- |
4,032 |
1,364 |
Средний разряд рабочих участка определяется по формуле:
,
(2.3.3)
где
- численность
рабочего i-го
разряда, чел.;
- разряд рабочих;
- списочная
численность рабочих, чел.
При подстановке в формулу (2.3.3) получаем:
Средний тарифный коэффициент определяется по формуле:
,
(2.3.4)
где
- тарифный коэффициент
i-го
разряда.
При подстановке в формулу (2.3.4) получаем:
2.3.2 Определение численности вспомогательных рабочих
Для определения численности вспомогательных рабочих на участке, необходимо установить состав вспомогательных рабочих.
Состав вспомогательных рабочих:
-
подготовитель-распределитель работ
-
контролеры
-
наладчик оборудования
-
подсобные и транспортные рабочие
Расчет численности наладчиков можно определить по формуле:
,
(2.3.5)
где
- норма обслуживания при наладке
оборудования данного вида, ([5],приложение
5).
При подстановке в формулу (2.3.5) получаем:
-
;
-
;
-
;
-
.
Результаты расчетов занесены в таблицу 2.3.3
Таблица 2.3.3 – Расчёт численности наладчиков
Наименование оборудования |
Модель станка |
Число станков |
Норма обслуживания |
Численность наладчиков в 2 смены |
1 |
2 |
3 |
4 |
5 |
Токарный с ЧПУ |
DF2 CNC |
13 |
10 |
2,60 |
Токарный с ЧПУ |
DMC DL 21MB |
13 |
6 |
4,33 |
Внутришлифовальный |
Si6/1 ASA 315 |
1 |
16 |
0,13 |
Долбёжный |
7Д430 |
1 |
10 |
0,20 |
Итого |
- |
28 |
- |
7,26 ≈ 8 |
Принимаем численность наладчиков - 8 человек
Расчёт численности вспомогательных рабочих других профессий рассчитывают по формуле:
,
(2.3.6)
где
- норматив численности вспомогательных
рабочих данной профессии на 100
человек основных рабочих [5,приложение
10];
- списочная
численность основных рабочих на
проектируемом
участке, человек.
При подстановке в формулу (2.3.6) получаем:
человека
человек
человек
Результаты расчетов занесены в таблицу 2.3.4
Средний разряд основных рабочих определяется по формуле:
(2.3.7)
При подстановке в формулу (2.3.7) получаем:
Средний тарифный коэффициент основных рабочих определяется по формуле:
(2.3.8)
При подстановке в формулу (2.3.8) получаем:
Результаты расчетов занесены в таблицу 2.3.4
Таблица 2.3.4 – Ведомость состава вспомогательных рабочих участка
Профессия |
Численность рабочих |
Средний разряд |
Средний тарифный коэффициент |
|||||||
Всего |
в том числе по сменам |
в том числе по разрядам |
||||||||
1-ая, чел. |
2-ая, чел. |
ІІ |
ІІІ |
ІV |
V |
VІ |
||||
тарифные коэффициенты |
||||||||||
1,089 |
1,209 |
1,358 |
1,552 |
1,806 |
||||||
1 |
2 |
3 |
4 |
5 |
6 |
7 |
8 |
9 |
10 |
11 |
Подготовители-распределители работ |
4 |
2 |
2 |
- |
- |
4 |
- |
- |
- |
- |
Контролер |
8 |
4 |
4 |
- |
4 |
3 |
1 |
|
||
Наладчик |
8 |
4 |
4 |
- |
2 |
4 |
2 |
|
||
Подсобные и транспортные рабочие |
6 |
3 |
3 |
6 |
- |
- |
- |
- |
||
Итого |
26 |
13 |
13 |
6 |
6 |
11 |
3 |
- |
3,4 |
1,28 |
3 Экономические расчёты
3.1 Определение годового расхода и стоимости основных материалов
Потребность в основных материалах и их стоимость на годовую программу определяется на основе исходных данных:
Цмат= 190,56 руб/кг
mзаг = 24,36 кг
Цотх= 19,07 руб/кг
mотх= 19,86 кг
(Цена отходов принимается равной 10% от цены материала)
Цены на материалы устанавливаются ([5],приложение 7)
Расход материалов и их стоимость на годовую программу определяется по формуле:
, (3.1.1)
где
- цена материала, руб/кг;
- масса заготовки,
кг;
- цена отходов,
руб/кг;
- масса отходов,
кг.
При подстановке в формулу (3.1.1) получаем:
тыс.руб./год
Таблица 3.1.1 – Расчёт потребности и стоимости основных материалов
Наименование и марка материала |
Потребность |
Затраты |
||
на 1 изделие, кг |
на всю программу, кг |
на 1 изделие, руб. |
на всю программу, тыс. руб. |
|
1 |
2 |
3 |
4 |
5 |
Жаропрочная высоколегированная сталь 13Х11Н2В2МФ |
24,36 |
325522,68 |
4642,042 |
62031,602 |
Отходы |
19,86 |
265389,18 |
378,452 |
5057,256 |
Итого |
4,5 |
60133,5 |
4263,589 |
56974,346 |
Приводим расчёт коэффициента использования заготовки (КИЗ) по формуле:
(3.1.2)
При подстановке в формулу (3.1.2) получаем:
3.2 Определение годового фонда оплаты труда основных производственных рабочих-сдельщиков участка
3.2.1 Расчёт операционных сдельных расценок
Расчёт планового фонда оплаты труда начинается с определения зарплаты по сдельным расценкам на деталь.
Пооперационные сдельные расценки рассчитываются по формуле:
,
(3.2.1)
где
- часовая тарифная ставка i-ой
операции, руб/час;
- учитывает оплату
труда при многостаночном обслуживании.
Принимаем
= 1 ([5], стр.26).
При подстановке в формулу (3.2.1) получаем:
1.
руб/шт
2.
руб/шт
3.
руб/шт
4.
руб/шт
Результаты расчетов занесены в таблицу 3.2
Таблица 3.2.1 – Расчёт пооперационных сдельных расценок
№ оп. |
Разряд |
руб/час |
мин |
руб/шт |
10,15 |
4 |
59,646 |
227,215 |
225,87 |
30,35,50,60 |
4 |
59,646 |
214,722 |
213,46 |
40 |
5 |
92,57 |
10,888 |
16,80 |
45 |
4 |
59,646 |
2,617 |
2,60 |
ИТОГО: |
- |
- |
455,442 |
Рсд = 458,730 |
Расчёт затрат планового фонда оплаты труда основных производственных рабочих – сдельщиков участка производится в соответствии со структурой фонда оплаты труда и с учётом доли доплат и выплат.
Статьи затрат рассчитываются следующим образом:
-
Зарплата по сдельным расценкам определяется по формуле:
,
(3.2.2)
где
- коэффициент увеличения зарплаты,
учитывающий финансовое состояние
предприятия на момент выплаты заработной
платы.
Принимается
= 2 ([5],стр.27)
При подстановке в формулу (3.2.2) получаем:
тыс.руб/год
-
Премия по положению – 40% от строки 1.
-
Фонд мастера – 3% от строки 1.
-
Доплата за работу в ночные часы – 5% от строки 1.
-
Доплата неосвобождённым бригадирам – 1% от строки 1.
Часовой фонд – сумма строк 1…5.
-
Доплаты подросткам – 0,5% от часового фонда.
-
Доплаты кормящим матерям от часового фонда
Дневной фонд – это сумма часового фонда и доплат до дневного фонда.
-
Оплата отпусков – 10% от дневного фонда.
-
Доплата за выполнение государственных и общественных обязанностей – 0,5% от дневного фонда.
Полный фонд – это сумма дневного фонда и доплат до полного фонда.
Результаты расчетов занесены в таблицу 3.2.2
Проверка:
Расчёт среднемесячной заработной платы:
,
(3.2.3)
где
- полный плановый фонд оплаты труда,
тыс. руб.;
- списочная
численность основных производственных
рабочих, чел.
При подстановке в формулу (3.5) получаем:
тыс. руб/чел
Таблица 3.3.2 – Расчёт планового ФОТ основных производственных рабочих участка
Виды выплат |
% |
Сумма, тыс.руб. |
1 |
2 |
3 |
|
- 40 3 5 1 |
12260,005 4904,002 367,800 613,000 122,600 |
Итого: часовой фонд |
|
18267,407 |
|
0,5 - |
91,337
|
Итого: дневной фонд |
|
18358,744 |
|
10 0,5 |
1835,874 91,794
|
Итого: полный годовой фонд оплаты |
|
20286,412 |
3.3.2 Составление калькуляции себестоимости детали
Калькуляция цеховой себестоимости детали «Стакан» составляется на основе ранее произведённых расчётов.
Транспортно-заготовительные расходы принимаются в размере не ниже 10% от стоимости материалов, комплектующих изделий и покупных полуфабрикатов.
Расчет выполняется в таблице 3.3.3
Таблица 3.3.3 – Калькуляция себестоимости детали «Стакан»
Статья калькуляции |
Себестоимость |
Примечания |
|
детали, руб. |
всей программы тыс.руб. |
||
1 |
2 |
3 |
расчёт, табл.3.1,стр.32 расчёт, табл.3.1,стр.32
10%
расчёт, табл.3.3,стр.35
500% |
|
5851,716 554,911 585,172
1371,023
6855,115
|
73860,365 7004,083 7386,037
17305,051
86525,257
|
|
Итого: цеховая себестоимость |
12775,056 |
170713,075 |
Статья 3 Транспортно- заготовительные расходы
тыс.руб.
(3.6)
тыс.руб.
тыс.руб.
Статья 4 Основная заработная плата производственных рабочих
(3.7)
тыс.руб.
Результаты расчетов занесены в таблицу 3.4