
В.И.Чуешов, Л.А.Мандрыка, А.А. Сичкарь Оборудование и основы проектирования химико-фармацевтических производств
.pdf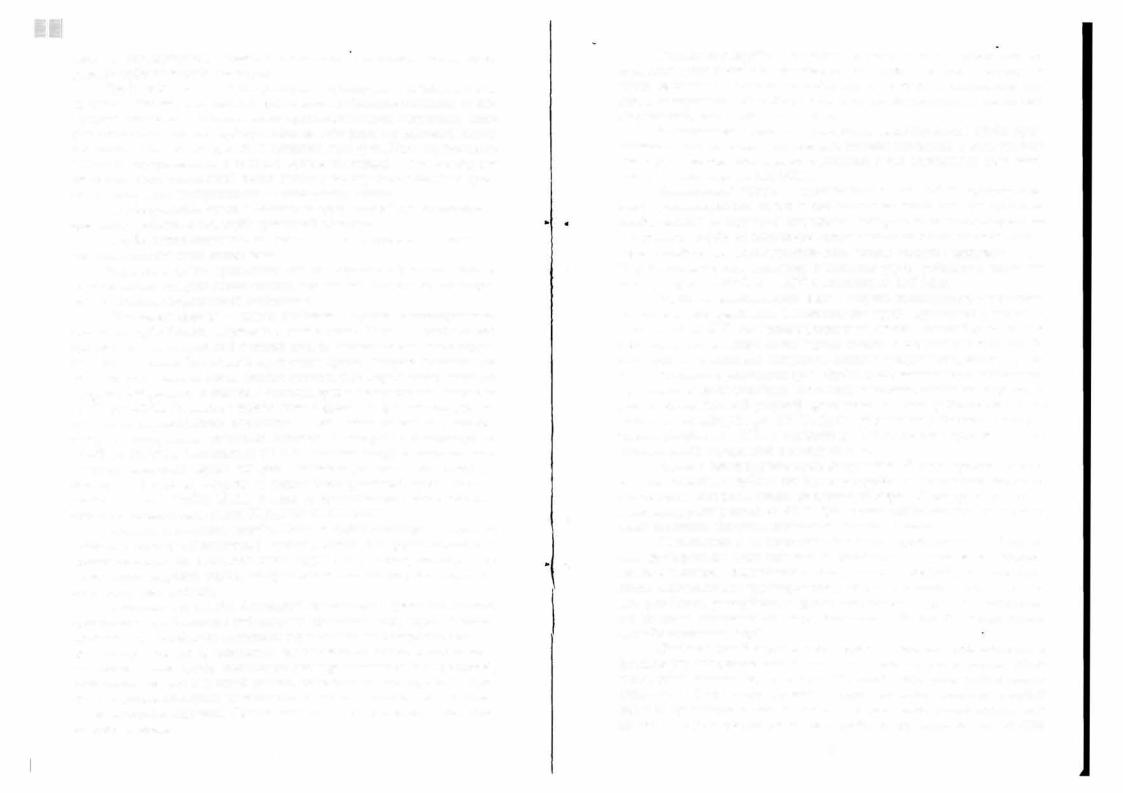
рами и термометрами; предохранительными клапанами; указателями уровня; трубопроводной арматурой.
Тр бощюноды и трубо11ронод11ая арматура. Тр)'боnронодш,1е
системы. Перемещение жидких сред в химико-фармацевтических произ водствах относится к повседневным производственным операциям, кото рые осуществляются по.трубопроводам за счет разности давлений между
начальньш и конечным пунктами движения этих сред. Если перемещение жидкости осуществляется с высшего уровня на низший - это происходl-\,1' самотекоч. Если жидкостной поток необходимо передать с низшего уров
ня на высший или по горизонтали - используются насосы. Трубопроводная система состоит из труб, деталей для соединения и
крепления трубопроводов, трубопроводной арматуры.
Трубы изrо:rавливаются из различных конструкционных материа
лов в зависимости от их назначения.
Чугунные трубы - применяют главным образом в канализационных трубопроводах, которые укладываются под землей. Эти трубы характери зуются высокой коррозионной стойкостью.
Стальные трубы - нашли наиболее широкое распространение.
Стальные трубы бывают сварньши и бесшовными. Сварные трубы имеют продольный или спиральный сварной шов, за счет этого они менее надеж ны в эксплуатации. Это водогазопроводные трубы, которые применяются для транспортирования воды, сжатого воздуха, газа, пара низкого давления и других ней альных и невзрывоопасных сред в интервале температур от -I5°C до +200 С. Бесшовные трубы более надежны и применяются для пе ремещения разнообразных продуктов, в том числе токсичных, взрыво опасных, коррозионно активных веществ в интервале температур от -180°С до +8ОО0С и давлениях до 20 кПа. Бесшовные трубы изготавливают из сталей различных марок: для труб массового назначения это углероди стые стали 1О и 20, но в случае необходимости применяют трубы из леги
рованны>.. сталей 12МХ; l5XM; и даже из высоколегированных кислото стойких II жаропрочных сталей Xl8HlOT; Х17Н13М2Т.
Медные и латунные трубы. Медные трубы используют в т хнике глубокого холода; органического синтеза, пищевой и фармацевтической промышленности, но стоимость таких труб очень высока, поэтому чаще применяюrся латунные трубы, которые незначительно уступают по своим характернстикам медным.
А.110.ш,ниевые трубы. Алюминий применяется в фармацевтической промышленности благодаря небольшому удельному весу, хорошей тепло проводности, способности алюминия образовывать на поверхности защит ную пленку, которая предохраняет поверхность от дальнейшего окисле
ния. Алю иниевыf трубы используют для перемещения по ним уксусной, разбавленной серной и азотной кислот, органических растворителей. Про дукты коррозии алюминия не токсичны· и чем чище алюминий, тем мень ше он подвержен коррозии. Однако алюминий не очень стоек в растворах
сильных щелочей.
20
"4
•4
•
Т11т1mщ1ые трубы - в настоящее время нашли широкое распро
странение в том числе и в фармацевтической промышленности, потому что титан по своим механическим свойствам не уступает углеродистым ста
лям, а по коррозионной стойкости значительно их превосходит, кроме того по удельному весу титан легче сталей.
Керамиковые трубы - керамиковые кислотоупорные трубы пред назначены для транспортирования агрессивных жидкостей и применяются для внутрицеховой канализации и уличных сетей канализации (они бо тают под давлением до 0,25 МПа).
Стекля1111ые трубы - применяются в пищевой и фармацевтиче ской промышленности, поэтому они устанавливаются там, где требуется особая чистота продуктов и визуальный контроль за транспортируемыми продуктами. Трубы из кварцевого стекла характеризуются высокой терми ческой стойкостью, кислотоупорностью, однако щелочи разрушают кварц. Вырабатываемые толстостенные стеклянные трубы работают в интервале температур от -50°С до +150°С и давлении до 0,75 МПа.
Трубы из пластических масс - широко используются в фармацев
тической промышленности. Винипластовые трубы применяют в интервале температур до 40°С для транспортирования кислот, щелочей (исключение
составляют концентрированная серная кислота и сильные окислители). Из этих труб изготавливают вакуумные линии и воздуховоды, которые рабо тают в условиях агрессивных сред. Трубы из полиэтилена и полипропилена
применяют в тех же условиях, что и винипластовые, только они характери зуются более высокой ударной прочностью и могут работать при более высоких температурах (до I ОО0С). Трубы из фаолита работают в темпера турном режиме до II0°t и давлении до lМПа. Из этих труб выполняют коммуникации внутри цеха и между цехами.
Трубы с антикоррозионным покрытием. К таким трубам относят ся гуммированные трубы - это стальные трубы, на внутренние поверхно сти которых наносится резина специальных марок. Такие трубы работают в температурном режиме до 65°С. Кроме того, трубы защищают полимер ными пленками, эмалями, антикоррозионными красками.
Соединения и соединительные части трубопроводов. Соедине ния трубопроводов подразделяют на разъемные и неразъемные. Неразъ е.Jtньtе соединения выполняют сваркой, пайкой и клейкой (для некоторых видов пластмассовых трубопроводов). Разъемные соединения - фланце вые, резьбовые, раструбные, и другие специальные виды. Для трубопрово дов из стали возможны оба вида соединений. На рис. 2.2 представлены способы соединения труб.
Цельносварной трубопровод предпочтительнее трубопроводов с фланцевыми или резьбовыми соединениями, так как в этом случае дости гается более высокая герметичность. Но такой трубопровод нельзя приме нять, если: а) транспортируемый продукт вызывает коррозию сварных
швов; 6) транспортируются загрязненные или застывающие жидкие сре ды, так как при этqм -rребуется частая разборка трубопровода для очистки
21
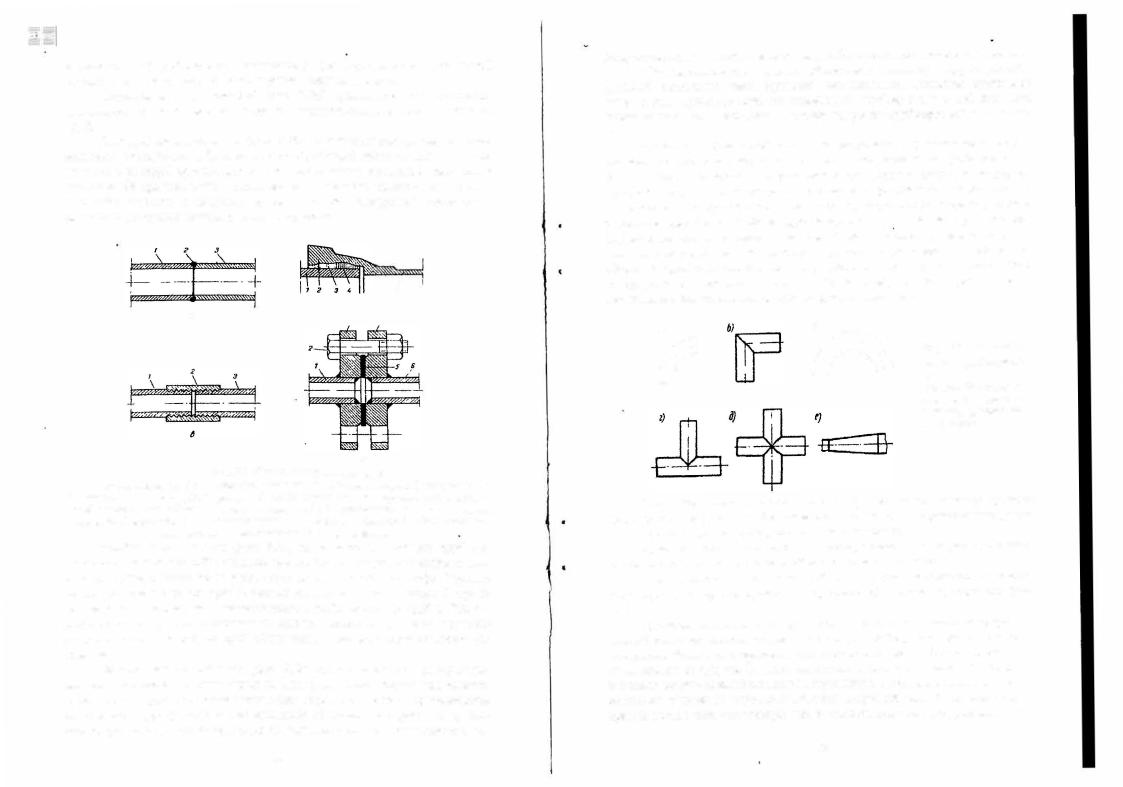
и промывки; в) трубопровод расположен в производстве со взрывоопасной |
||
средой, где не допускается производство сварочных работ. |
||
Соедииеиие труб свар«ой (рис. 2.2а) применяется для стальных, |
||
алюминиевых, титановых, |
а иногда для винипластовых и полиэтиленовых |
|
труб. |
|
|
Раструбиые соедсше11ш1 (рис. 2.2б) применяют для чугунных, кера |
||
миковых, стеклянных и фаолитовых труб, гладкий конец одной трубы по |
||
мещают в раструб другой. |
Кольцевое пространство заполняют пеньковоri |
|
или льняной прядью, а затем заливают увлажненным цементом или масти |
||
кой, либо асбестом и кислотоупорной замазкой. Раструбные трубы укла |
||
дываются навстречу течению потока жидкости. |
|
|
|
|
! |
|
|
.i |
|
|
5 |
а |
З |
4 |
|
г
Рис. 2.2. Способы соединения труб: |
|
а) сваркой встык· / и 3 - концы свариваемых труб; 2 - место сварки; б) раструбное. |
/ и |
5 - концы соединяемых труб; 2 - раструб; 3-слой цемента или кислотоустойчивой замазки, ./ |
-слой пеньковой или асбестовой пряди; в) резьбовое: 1 и 3 - концы труб с нарезкой; 2 - муфта
снарезкой. г) фланцевое. / и 6-концы соединяемых труб; 3 и ./-фланцы; 2 - болт, стягиваю-
щий фланцы; 5 -уплотняющая прокладка (набивка) РеЗ1,бовые соединения (рис. 2.2в) применяют для газовых труб при
невысоких давлениях и безопасных средах (вода, воздух, пар низкого дав ления). Трубы соединяlОт на резьбе при помощи резьбовых муфт. Трубная
резьба отличается от крепе,жной резьбы меньшим шагом и меньшей глуби ной нарезки, поэтому она незначительно ослабляет стенку трубы. Резьбо
вые соединения для гидравлических систем высокого давления выполня ют конической резьбой, которая обеспечивает высокую герметичность со
единений. Фланцевые соединения (рис. 2.2г) являются самыми распростра ненными разъемными соединениями. Вид фланцевого соединения зависит от материала труб и от технологических параметров среды. Применяются следующие виды фланцевых соединений: а) приварные фланцы; б) сво бодные фланцы для трубопроводов из цветных металлов, винипласта и по-
липропиле11а; в) съемные фланцы на резьбе в условиях высокого давления. |
||||
Сосд1111итv11,11ые |
чttспш |
(фс1со1шые детш1и) |
трубопровlн)о(t |
|
(рис.2.3) выполняют такие функции, как: изменение диаметра, изменение |
||||
направления трубопровода, ответвление от трубопровода одной или двух |
||||
линий того же или меньшего диаметра, закрытие трубопровода на его кон |
||||
це. |
|
|
|
|
Арматура. Арматурой называют устройства, предназначенные для |
||||
управления потоками жидкостей и газов, движущихся по трубопровод'ам. |
||||
В зависимости от назначения различают: арматуру запорную, арматуру ре |
||||
гулирующую, клапаны предохранительные, |
перепускные и обратные, ар |
|||
матуру специальную (это указатели уровня, |
конденсатоотводчики, пробно |
|||
спускные краны и др.). Арматура запорная -предназначена для полного |
||||
перекрытия потока жидкости или газа. Арматура регулирующая - предна |
||||
значена для регулирования расхода и давления транспортируемой среды. |
||||
Клапа111,1 предохра11ительные и перепуск11ые служат для выпуска избыт |
||||
ка среды при повышении давления. Клапа11ы обратные - предназначены |
||||
для исключения движения среды в обратном направлении. |
|
11} |
1) |
|
|
||
{f |
Рис. 2.3. Фасонные |
|
части |
трубопрово |
дов. |
|
а) отвод, |
б) колено, в) |
двойник («калач»), r} |
|
тройник; |
д) крестови |
на, е) переход. |
Основные параметры арматуры: 1) Ду - условный диаметр прохода; 2) Рг условное давление. Из линейных параметров - строительная длина,
равная длине отрезка трубы, который она замещает. Арматура устанавливается на трубопроводах, на аппаратах, а в неко торых случаях является составной частью самого аппарата. В зависимости от принципа действия и формы запорного устройства
запорную арматуру разделяют на: а) краны; 6) вентили; в) задвижки (рис.
2.4). Кранами называют арматуру, которая открывает и закрывае-r про
ходной канал поворотом притертой к гнезду пробки, имеющей сквозное отверстие. Чаще всего применяются пробки конической формы. Краны из готавлрвают из чуrуна, бронзы, алюминия, стекла и керамики. К преиму ществам кранов относится: малое гидравлическое сопротивление и воз можность прочистки трубопровода через открытый кран. Кнедостаткам кранов можно отнести: плохую герметичность при высоких давлениях и
23
22
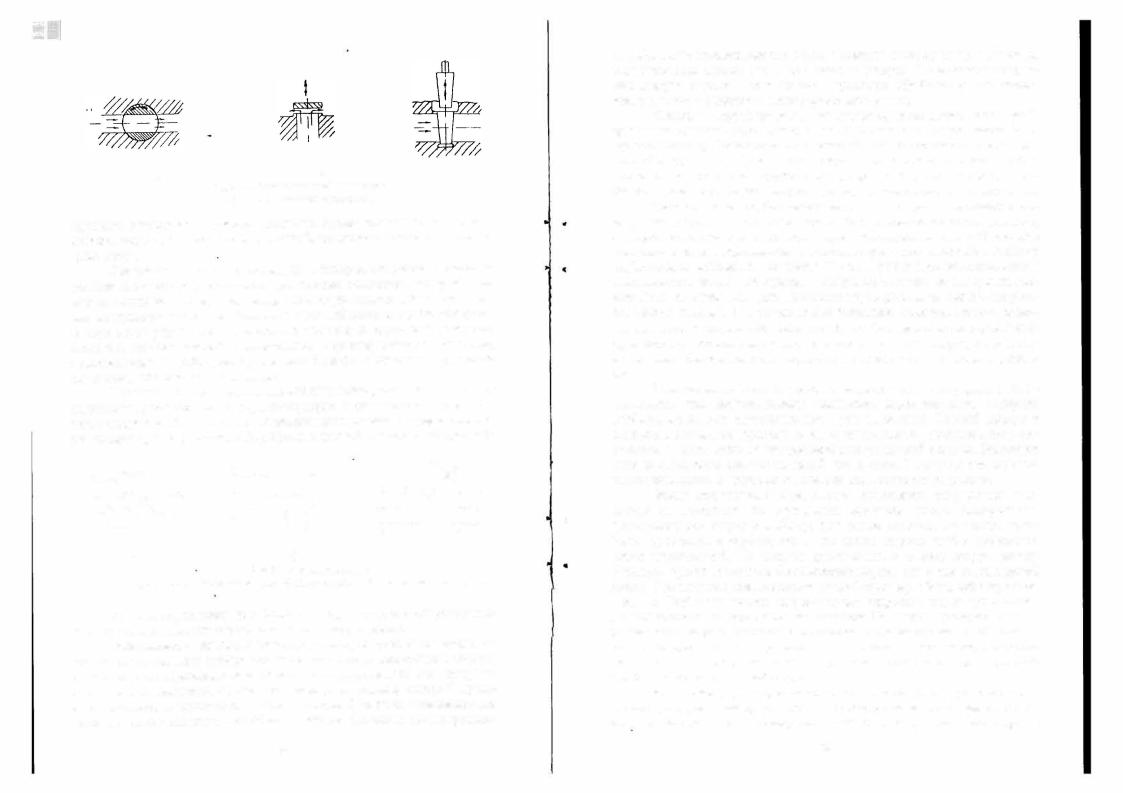
а |
|
б |
|
|
в |
|
|
|
|
|
|
|
Рис. 2.4. Схема запорной арматуры: |
|
|||
|
а) 1,.раны; б) вентили; в) задвижки |
|
|||
трудность регулирования расхода жидкости. Краны применяют на линиях |
|||||
сжатого воздуха, вакуума, кислот, щелочей, |
жидкостей вязких и 9ильно за |
||||
грязненных. |
, в |
которой |
открытие и закрытие |
||
|
|||||
Вентилями - называют арматуру |
|
|
, который наса |
||
прохода для среды осуществляется при помощи золотника |
|
||||
жен на шпиндель и совершает возвратно-поступательное движение. Ниж |
|||||
няя поверхность золотника (клапана) пришлифована к краям отверстия |
|||||
(седлу) перегородки. |
Для возможности подъема и |
опускания |
золотника |
||
шпиндель снабжен резьбой и ввинчивается в крышку вентиля. |
По методу |
||||
присоединения к трубопроводу вентили бывают с |
концами под резьбу |
||||
(муфтовые) или сварку и фланцевые. |
|
|
|
|
|
В зависимости от направления оси шпинделя различают вентили со |
|||||
шпинделем, расположенным перпендикулярно к оси вентиля и с наклон |
|||||
ным шпинделем. В зависимости от направления движения среды различа |
|||||
ют вентили прямые (проходные), угловые и косые (прямоточные) (рис.2.5). |
|||||
L-cl |
|
|
|
|
- |
Г]t+ |
|
|
- |
||
|
|
|
|||
|
|
|
|
|
|
а |
б |
|
|
|
в |
|
Рис.2 5. Схема вентилей: |
|
|
||
а) прячой с прямым шпr1нделе 1. б)) главой, в) косой с наклонным шпинделеч |
|||||
Вентили характеризуются большим гидравлическим сопротивлени |
|||||
ем и не применяются для работы с загрязненными средами. |
|
||||
Задвижка.ми - называют арматуру, в которой проход для среды от |
|||||
крывается при подъеме шибера или диска, которые расположены в корпусе |
|||||
задвижки. Диск перемещается в вертикальном направлении или поворачи |
|||||
вается вокруг вертикальной оси при помощи шпинделя, который приво |
|||||
дится в движение вручную или автоматически. |
Задвижки применяют для |
||||
трубопроводов с диаметром от 50 мм до 2QO мм. |
Задвижки характеризуют- |
ся нсбол1.шим гидравлическим сопротивлением, поэтому их примс1 яют на магистрал1,11ых линиях воды, газа, сжатого воздуха. К недостаткам задви жек следует отнести - громоздкость, трудность обработки уплотняющих поверхностей и сложность антикоррозионной защиты.
Систе111ы трубопроводов ш, хшtико-фарм,щевmtt'tесюtх пред приятиях. Система трубопроводов на ХФП занимает важное место. Ино
гда стоимость трубопроводов составляет 40-50% от стоимости всего цехо вого оборудования. Применяются следующие основные системы трубо проводов: материальные трубопроводы, паро- и конденсатопроводы; тру бопровод сжатого воздуха, вакуумопровод, производственная канализация.
Материальные трубопроводы служат для передачи исходного сы рья, полупродуктов, готового продукта. Дл.11 материальных трубопроводов,
передающих жидкости, используют трубы диаметром не менее 40 мм. Для транспортировки загрязненных и кристаллизующихся жидкостей диаметр трубопровода составляет не менее 70 мм. Трубопровод прокладывают с минимальным числом поворотов, а радиус закругления на поворотах дол жен быть не менее 8Ду. Для прочистки трубопровода на поворотах уста навливают штуцера с заглушками или фланцевые разъемы. Иногда преду сматривается продувка воздухом или паром. При передаче по трубопрово ду продуктов, которые застывают при комнатной температуре, применяет ся паровой обогрев, который осуществляется при помощи паровой рубаш
ки.
Газопроводы. Сжатый воздух и инертные газы (азот, аргон и др.) - применяют для передавливания жидкостей, перемешивания, продувки трубопроводов, для пневматических приспособлений. Сжатый воздух к аппаратам подают по трубопроводам от компрессоров, которые либо уста новлены в цехах, либо из центральной компрессорной станции. Инертные газы используются для тех же целей, что и сжатый воздух в тех случаях, когда применение воздуха по технологии категорически запрещено.
Вакуумопроводы0 В ХФП вакуум применяется для удаления жид
.. костей из аппаратов; для проведения процессов сушки, выпаривания, фильтрации под вакуумом. Вакууыные схемы делаются по возможности более простыми, а трубопроводы как можно короче, чтобы уменьшить число неплотностей. Не следует присоединять к одному вакуум-насосу большую группу аппаратов. Нежелательны крутые повороты на вакуумной линии. Разреженные газы движутся по трубопроводу с большой скоростью - 90 м/с. Чтобы уменьшить гидравлическое сопротивление вакуум-прово ды выполняются из труб большого диаметра. На вакуум-проводах с целью уменьшения гидравлического сопротивления в качестве запорной армату ры используют краны и задвижки, но не вентили. Перед вакуум-насосом устанавливают ловушку, заполненную раствором соды, через кщ·орый барботирует отсасываемый воздух.
Водопроводы. На предприятиях вода используется для технологи ческих целей, как сырье, для промывки оборудования, охлаждения, хозяй ственно-бытовых нужд, пожарных целей. На предприятиях как пр вило
24 |
25 |
|
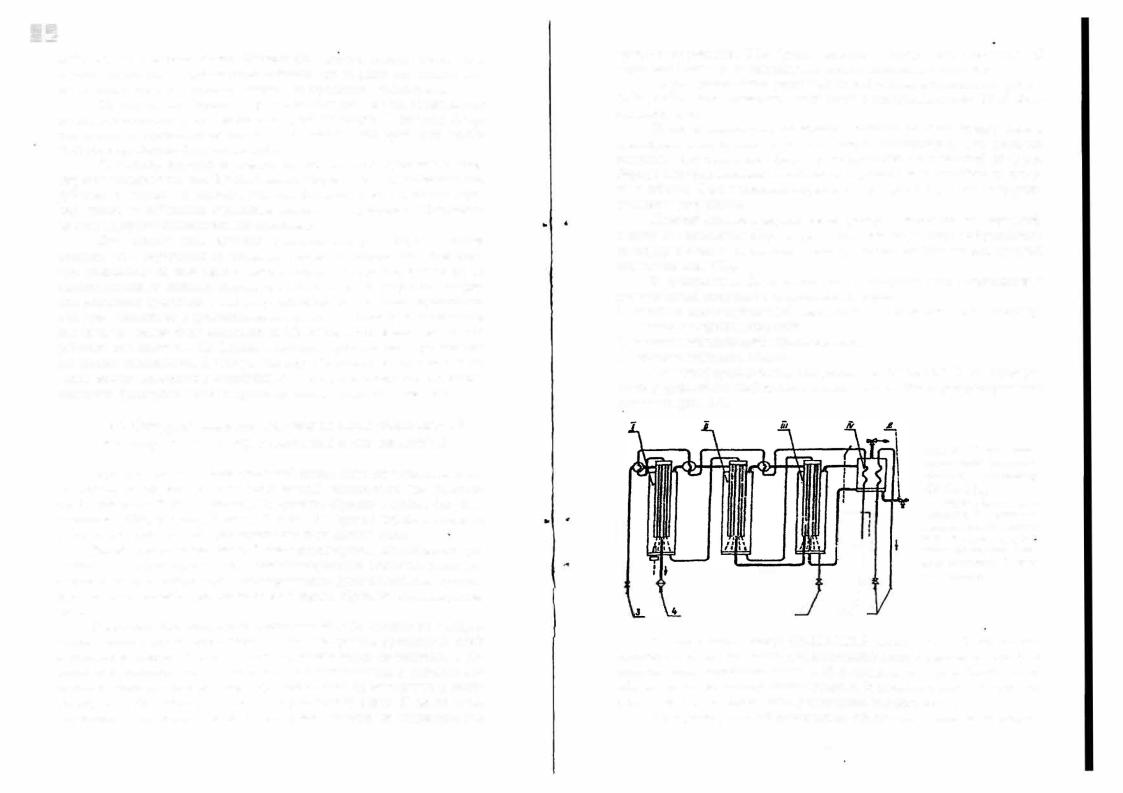
m• 1
rиботаюг две системы водоснабжения: для технологических целей воду подщот и 1 1аводских артезианских скважин или из реки; для хозяйствен- 1ю-б1,1·1u111,1х целей и пожарных кранов - из городского водопровода.
Парш11ю1юды. Водяной лар применяется для нагрева реакционных аппаратов, проведения процессов сушки, ректификации. В качестве запор ной аrматуры применяютs;я вентили и задвижки, а для прокладки трубо проводов применяют бесшовные трубы.
Конденсат, который отводится из отопительных приборов и кало риферов используется для бытовых целей. Конденсат из теплообменников рубашек, змеевиков не используется для бытовых целей и питания паро вых котлов, во избежание отравления токсичными продуктами. Конденсат
из этих аппаратов используют для отопления.
Каwализационная система предназначена для сбора и отвода сточных вод с территории предприятия в очистные сооружения. Канализа ция разделяется на дворовую и внутрицеховую. Жидкость, удаляемая по
канализационным линиям, неоднородна по составу. В результате смеше ния различных продуктов в ней могут образоваться ядовитые, взрывоопас ные газы, смолистые и кристаллические вещества. Поэтому канализацион ная система должна быть заполнена на l/2-2/3 своего сечения и не должна работать под напором. На фармацевтических предприятиях применяется
раздельная канализация. В чистую систему сбрасываются воды от охлаж дения машин, аппаратов и конденсат, а в грязную систему все отбросные
жидкости, фильтраты, воды от промывки аппаратов, фекальные воды.
2.4. Оборудование для получения воды обессоленной (деминерализованной), очищенной и для инъекций
Вода очищенна,я и для инъекций может быть подготовлена с ис пользованием: а) процесса многоступенчатой дистиnляции (по Европей ской и Британской Фармакопеям); б) процесса обратного осмоса (по Фар макопеям США, Японии, России). И в том и в другом случае в качестве питательной используется предварительно обессоленная вода.
Для получения обессоленной воды используются ионообменные ус тановки, в которых применяют высокомолекулярные вещества, нераство римые в воде и содержащие иони.зированные функциональные группы. Эти группы с ионами противоположного заряда образуют нерастворимые
соли. Установки для получения обессоленной воды состоят из четырех
колонн, через которые водопроводная вода как правило проходит в такой последовательности: 1) вначале колонну, заполненную катионитом, в ко торой идёт удаление ионов щелочных, щелочноземельных и тяжёлых ме таллов в обмен на ионы водорода; 2) далее в колонну, наполненную анио нитом, где идёт обмен анионов на гидроксильные ионы; 3) затем вода, очищенная от катионов и анионов, поступает в колонну на дегазацию, где
происходит удаление СО2; 4)после ко.,онны дегазации вода пrоходит ещё через одну колонну со смешанными слоя.1,1и катионита и анионита.
Производительность установок по получению обессоленной воды - 4м3/ч, 8м3/ч. Одна установка между дву:,,.1я регенерациями даёт 50 м3 обес соленной воды.
Коло11ны катионита, анионита 11 коло,ша со смеша11ным11 слоями кamuo11u111a и а11ио11ита имеют одинаковую конструкцию. Это стальные аппараты цилиндрической формы диа,1етром 650 мм и высотой 300(} мм. Внутри они гуммированы во избежание коррозионного воздействия кисло ты и щёлочи. Вода в колонны подается снизу через специальное распреде лительное устройство.
Колонна дегазации внутри также гуммирована и заполнена насадкой,
|
а внизу нее находится сборник дегазированной воды. Вода разбрызr11вает |
||||
|
ся сверху и стекает по насадке колонны, а снизу подаётся воздух, который |
||||
.. . |
удаляет из воды СО2• |
|
|
|
|
|
|
В производстве фармацевтических препаратов воду очищенную и |
|||
|
для инъекций получают в однотипном оборудовании: |
|
|||
|
1) методом многоступенчатой дистилляции с использованием многокор |
||||
|
2) |
пусных выпарных установок; |
|
|
|
|
методом механической термокомпрессии; |
|
|
||
|
3) |
методом обратного осмоса. |
|
|
|
|
|
Многокорпусная выпарная установка FINN-AQUA. На предпри |
|||
|
ятиях фармацевтической промышленности это наиболее распространенная |
||||
|
установка (рис. 2.6). |
|
|
|
|
|
|
|
|
Рис.2 6 Схема трёх |
|
|
|
|
|
стуnенчатой дистилля |
|
|
|
|
|
ционной |
установки |
|
|
|
|
FINN-AQUA: |
|
|
|
|
L |
1 - подача воды на дис |
|
|
|
|
тилляцию; 2 - дистилли |
||
|
1' |
|
|
||
|
|
|
рованная вода; 3 - подача |
||
|
|
Jli6 |
нагревающего |
пара; 4 |
|
|
|
|
отвод конденсата;S - вы |
||
.. |
|
- |
пуск конденсата. 6 - вода |
||
|
|
охлаждающая |
|
||
|
|
|
|
||
|
|
s |
|
|
В состав дистиллятора ФИНН-АКВА входит три и более колонн, столько же теплообменников для питательной воды и один конденсатор. В дисту:лляторе, вырабатывающем 1 ООО л дистиллята в час и более, тепло обменники устроены отдельными блоками. В моделях с меньшей произво дwrельностью теплообменники установлены внутри колонн.
Метод мно кратной дистилляции обеспечивает экономию потреб-
26 |
27 |
|
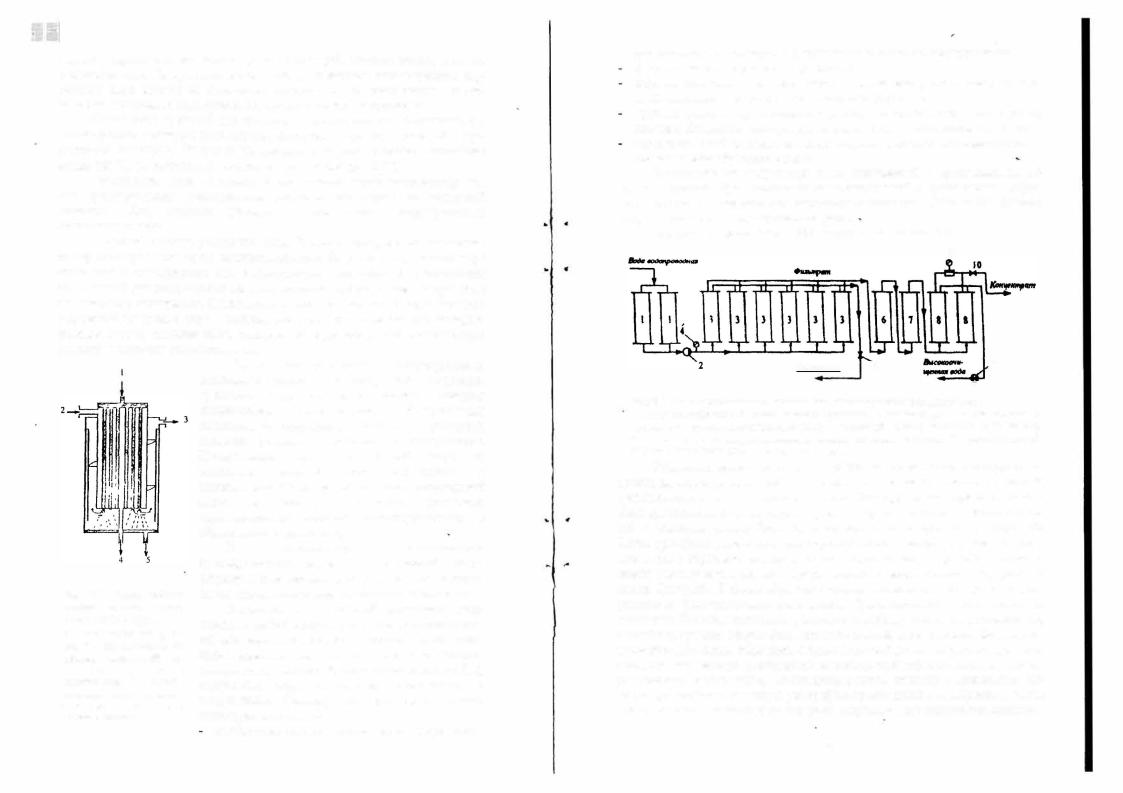
ЛЯСМОЙ ЭllеJ)ГИИ, Т.К. ОНа 11СПОЛЬЗуеТСЯ СТОЛl,КО раз, СКОЛЬКО КОЛО\111 ИМСеТСЯ в дистилляторе. 1 la практике это означает, что энергия используемого пер
вичного пара делится на количество колонн, причем температура по1 реб ляемого первичного пара снижается до температуры конденсата.
Первичный греющий пар подается в первую колонну установки, а в последующих колоннах и пользуется вторичный пар, образованный в пре дыдущих колоннах. Температура кипения в первой колонне составляет около 160°С, а в последней колонне она снижается до L 00°С.
Питательная вода поступает в дистиллятор через конденсатор, где |
|
она предварительно подогревается апирогенным паром из последней |
|
колонны. |
Для питания установки используется предварительно |
обессоленная вода. |
|
В первой колонне установки (рис.2.7) за счет конденсации первично |
|
го пара выпаривается часть питательной воды. Конденсат первичного пара |
|
отводится |
в канализацию или рециркуляционную систему. Питательная |
вода тонкой пленкой стекает по поверхностям трубок колонн и при этом |
|
она частично испаряется. Испарившаяся часть питательной воды подается |
|
в качестве греющего пара в следующую колонну установки. Не испарив |
|
шаяся в первой колонне часть питательной воды поступает в следующую |
колонну в качестве питательной воды.
Разница между первой и последующими
Рис 2 7 С\ема работы
первой колонны уста новки FINN-AQUA
1 - вода питательная; 2 -
пар; 3 - пар вторичный на |
|
обогрев следующей |
ко |
лонны; 4 - конденсат пер
вичного пара, 5 - неиспа |
|
рившаяся |
часть питатель |
ной воды на питание сле |
|
дующей колонны |
колоннами состоит |
в |
том, |
что |
конденсат |
|
греющего пара |
из |
этих |
колонн |
является |
апирогенным дистиллятом. Апирогенный дистиллят от предыдущих колонн и п,оследней
колонны установки подается в конденсатор. Испарившаяся часть питательной воды из последней колонны тоже подводится к конденсатору. Неиспарившаяся часть питательной воды из последней колонны установки характеризуется высоким солесодержанием и сбрасывается в канализацию.
В конденсаторе производится· предварительный подогрев питательной воды; регулирование температуры дистиллята; конден сация апирогенного пара от последней колонны.
Выпарные аппараты этой установки пред ставляют собой кожухотрубчатые теплообменни ки, все элементы которых изготовлены из высо колегированной нержавеющей стали с полиро ванной поверхностью. В установках FINN-AQUA получается вода очищенная, стерильная и апирогенная. Однако, эти установки имеют некоторые недостатки:
необходима система предочистки воды (обес-
соливанис), что принодит к удорожанию стоимости оборудован я; большой рuсход воды и электроэнергии;
образование накипи на поверхностях испарителей, что снижает их про изводителыюсть и приводит к износу оборудования; труднее удалить органические примеси, которые имеют температуру
кипения близкую к температуре кипения воды и захватываются паром; стоимость всей системы в целом дороже системы водоподготовки с
применением обратного осмоса.
Установки по получению воды очищенной с применением об ратного осмоса. Для подготовки воды очищенной с применением обрат
ного осмоса на предприятиях используют установки Шарья-200, Шарья500, а также установки зарубежных фирм.
Схема установки Шарья-500 представлена на рис. 2.8'.
,.... |
s |
11 |
Рис.2.8. Схема установки получения высокоочищенной воды Шарья-500
1 - патронные фильтры;2 - насос высокого давления; 3 - элементы рулонные обратноосмо тические; 4 - манометр электроконтактный; 5 - вентиль;6 - фильтр катионитный; 7 - фильтр анионнтный; 8 - ультрафнлырационный аппарат на полых волокнах; 9 - разделительный модуль с манометром;IОвентиль; 11 - кондукrометр.
Установка позволяет очищать до 500 л/ч водопроводной воды с по лучением высокоочищенной воды, свободной от механических примесей, органических и неорганических веществ. Водопроводная вода поступает в блок предварительной фильтрации, где для удаления механических приме сей с размером частиц более Sмкм применяются патронные фильтры. Из блока предфильтрации вода посредством насоса высокого давления пода ется в блок обратного осмоса, где происходит удаление до 70% молекул и ионов растворенных веществ органической и неорганической природы, а также бактерий. В блоке обратного осмоса используют аппараты со спи ральными фильтрующими элементами. Достоинствами таких аппаратов являются: большая плотность упаковки мембран, малая металлоемкость, механизированная сборка фильтрующих элементов и высокая производи тельность"' Из блока обратного осмоса вода поступает на финишную очи стку, где она вначале доочищается от ионов, проходя последовательно че рез колонну, заполненную катионитом, а затем колонну с анионитом. Да лее вода поступает в аппарат у11ьтрафильтрационный с мембранами ввиде полых волокон, на выходе из которого получают воду высокоочищенную.
29
28
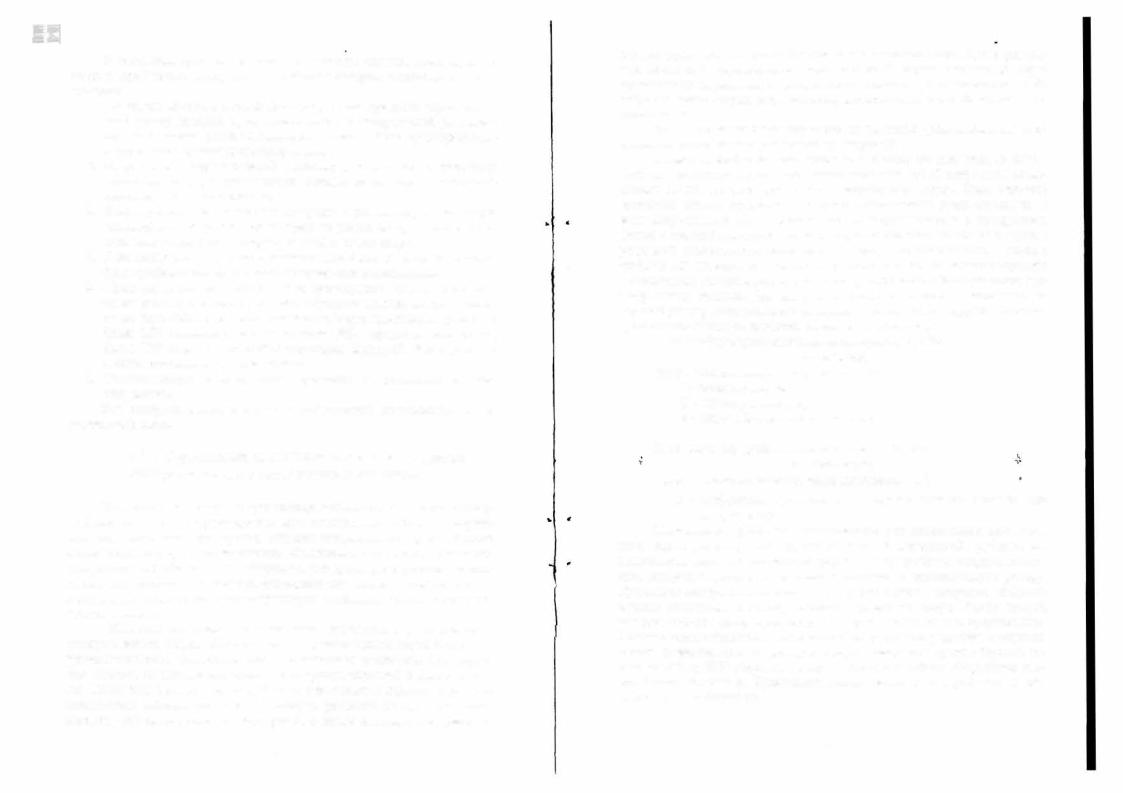
|
В настоящее время на предриятиях внедряют системы водоподготов |
|
|
ми инс1rуме111ами являются барdба1111ые и дисковые ножи Лля и1резыва |
|||||||||||||||
|
|
|
ния пло1111,1х |
и дсренянистых частей |
растений (корни, корнсв11ща, кора) |
||||||||||||||
ки ряда зарубежных фирм, принцип действия которых заключается в сле |
|
|
|||||||||||||||||
|
|
применяюrся 1<ор11ерез1<и с гильотинными ножами, для измельчения особо |
|||||||||||||||||
дующем: |
|
|
|
|
|
|
|
|
|
||||||||||
|
|
|
|
|
|
|
|
|
твёрдого сырья (корни элеутерококка) |
используются малогабаритные дис |
|||||||||
1. |
На стадии предварительной фильтрации вода проходит через |
песча |
|
|
|||||||||||||||
|
|
ковые пилы. |
|
|
|
|
|
|
|||||||||||
|
ный фильтр, который представляет собой цилиндрический |
резервуар |
|
|
|
|
|
|
|
|
|||||||||
|
|
|
|
Для |
проведения окончательного |
измельчения (порошкования) при |
|||||||||||||
|
из нержавеющей с.тали, заполненный песком. Песок предварительно |
|
|
|
|||||||||||||||
|
|
|
меняются изм |
е |
и |
|
|
|
|||||||||||
|
|
|
|
|
|
|
|
|
|
|
|
|
|
||||||
|
подвергается промывке и хлорированию. |
|
|
|
|
|
|
|
льч тели различных конструкций. |
|
|
||||||||
|
|
|
|
|
|
|
|
В11mшвые дробш,ки - для среднего и тонкого помола (размер частиц |
|||||||||||
2. |
Вода после предварительной |
фильтрации |
поступает в |
установку |
|
|
|
||||||||||||
|
|
1-10 |
мм) |
используют дробилки, представляющие собой спаренные парал |
|||||||||||||||
|
обессоливания, |
где производится очистка от катионов щелочнозе |
|
|
|||||||||||||||
|
|
|
лельно валки, |
которые вращаются навстречу друг другу. Если скорость |
|||||||||||||||
|
мельных и тяжелых металлов. |
|
|
|
|
|
|
|
|
||||||||||
3. |
|
|
|
|
|
|
|
|
вращения |
валков одинаковая, материал измельчается раздавливанием, а |
|||||||||
После удаления катионов вода |
поступает в установку, заполненную |
|
|
||||||||||||||||
|
|
если |
скорость вращения валков разная, то раздавливанием и истиранием. |
||||||||||||||||
|
активированным углем, где из |
воды устраняются органические со |
|
|
|||||||||||||||
|
|
|
Валки с гладкой поверхностью используются для тонкого помола; валки с |
||||||||||||||||
|
единения с малой молекулярной массой и следы хлора. |
|
|
|
|
||||||||||||||
|
|
|
|
|
рифлёной |
поверхностью используют для среднего измельчения, |
а валки с |
||||||||||||
4. |
Вода поступает на фильтр с размером пор 5мкм и !мкм. В качестве |
|
|
||||||||||||||||
|
|
зубьями для |
измельчения плодов, ягод |
и семян. Один из валков |
.. |
||||||||||||||
|
фильтрующего материала здесь |
используется полипропилен. |
|
• |
с |
закреплен |
|||||||||||||
|
|
|
|
в подвижных подшипниках с пружинами, чтобы можно было регулировать |
|||||||||||||||
5. |
Предварительно подготовленная на предыдущих стадиях |
вода про |
|
|
|||||||||||||||
|
|
зазор |
между |
валками. Для втягивания материала в зону измельчения ис |
|||||||||||||||
|
ходит очистку в системе двойного обратного осмоса, которая |
состо |
|
|
|||||||||||||||
|
|
|
ходный размер измельчаемого материала должен быть о••,,•.120. Произво |
||||||||||||||||
|
ит из двух блоков по шесть элементов. Здесь происходит |
удаление |
|
|
|||||||||||||||
|
|
|
дителыюсть |
валковой дробилки может |
быть рассчитана |
|
|||||||||||||
|
более 96% одновалентных ионов; |
более 98% двухвалентных ионов; |
|
|
|
||||||||||||||
|
|
|
|
1) по объёму перерабатываемого |
3 |
/ч: |
|
||||||||||||
|
более 97% кремния; более 98% |
пироrенов, |
бактерий. Фильтрующие |
|
|
|
материала V, м |
|
|||||||||||
|
|
|
|
|
|
|
|
V=Ьl1tDn·60, |
|
|
|||||||||
|
элементы - полиамидные мембраны. |
|
|
|
|
|
|
|
|
|
|
|
|
|
|||||
|
|
|
|
|
|
|
|
где Ь - |
ширина зазора между валками, м; |
|
|
||||||||
6. |
Окончательную |
очистку вода |
проходит |
в |
установке |
с |
УФ |
|
|
|
|
|
|||||||
|
|
|
|
1 - длина валков, м; |
|
|
|
||||||||||||
|
облучением. |
|
|
|
|
|
|
|
|
|
|
|
|
|
|
||||
|
|
|
|
|
|
|
|
|
|
|
|
D |
- диаметр валков, м; |
|
|
|
|||
|
Все аппараты данной системы |
водоподготовки изготовлены |
из не |
|
|
|
|
|
|
|
|||||||||
|
|
|
|
|
n - число оборотов валка в минуту; |
|
|
||||||||||||
ржавеющей стали. |
|
|
|
|
|
|
|
|
|
|
|
|
|
||||||
|
|
|
|
|
|
|
|
|
|
|
|
|
|
|
|
|
|
|
2.5. Оборудование для измельчения и сортировки |
||
|
лекарст енных и вспомогательных веществ |
|
|
|
Процессы измельчения и просеивания широко применяются в хими |
||
ко-фармацевтических производствах при изготовлении сборов и |
|
ореш |
|
ков, |
экстракционных препаратов, твёрдых лекарственных форм, |
мягких |
|
лекарственных форм, суппозиториев. Измельчение позволяет увеличить |
|||
поверхность обрабатываемых материалов, что приводит к ускорению про |
|||
цессов растворения, химического взаимодействия, экстрагирования, а в ле |
|||
карственных формах это интенсифицирует выделение биологически ак |
|||
тивных веществ. |
|
|
|
|
Машины для измельчения твердых продуктов и растительного |
||
лекарственного сырья. Для измельчения растительного сырья в химико |
|||
фармацевтической промышленности используется различное оборудова |
|||
ние, |
которое во многом заимствовано из других отраслей промышленно |
||
сти. |
Поскольку растительное сырьё имеет волокнистую структуру, |
для его |
|
измельчения применяются машины, которые работают по принципу изре |
|||
зывания - это траво-, соломо-, корнерезки. В трава-соломорезках режущи- |
2) по массе перерабатываемого материала G, т/ч: |
||||
|
|
G=60Ьl1tDnp\j/, |
|
|
где р |
- |
|
3 |
; |
плотность измельчаемого материала, т/м |
||||
\\f |
- |
коэффициент, учитывающий неравномерность питания вал |
||
|
|
ков, \j/=0,5+0,7. |
|
|
Молотковые дробwrки - |
используются для измельчения раститель |
|||
ного сырья |
(корней, стеблей), |
сахара, соли В молотковой дробилке из |
||
мельчаемый материал подается сверху и на лету дробится ударами молот |
||||
ков, которые шарнирно закреплены стержнями к вращающемуся ротору |
||||
Дробление материала происходит при ударах кусков материала, отбрасы |
||||
ваемых молотками о плиты, которыми футерован кожух. Внизу кожуха |
||||
имеется съемное сито, через которое материал после помоГ!а про_сеивается |
||||
Степень измельчения материала можно регулировать размером отверстий |
||||
в сите. В зависимости от размеров кожуха изменяется число оборотов ро |
||||
тора от 500 до 2500 оборотов в минуту. Ротор может быть оборудован 1ще |
||||
сто молотков ножами. Производительность молотковых дробилок Q, т/ч, |
||||
определяют по формуле: |
|
|
31 30
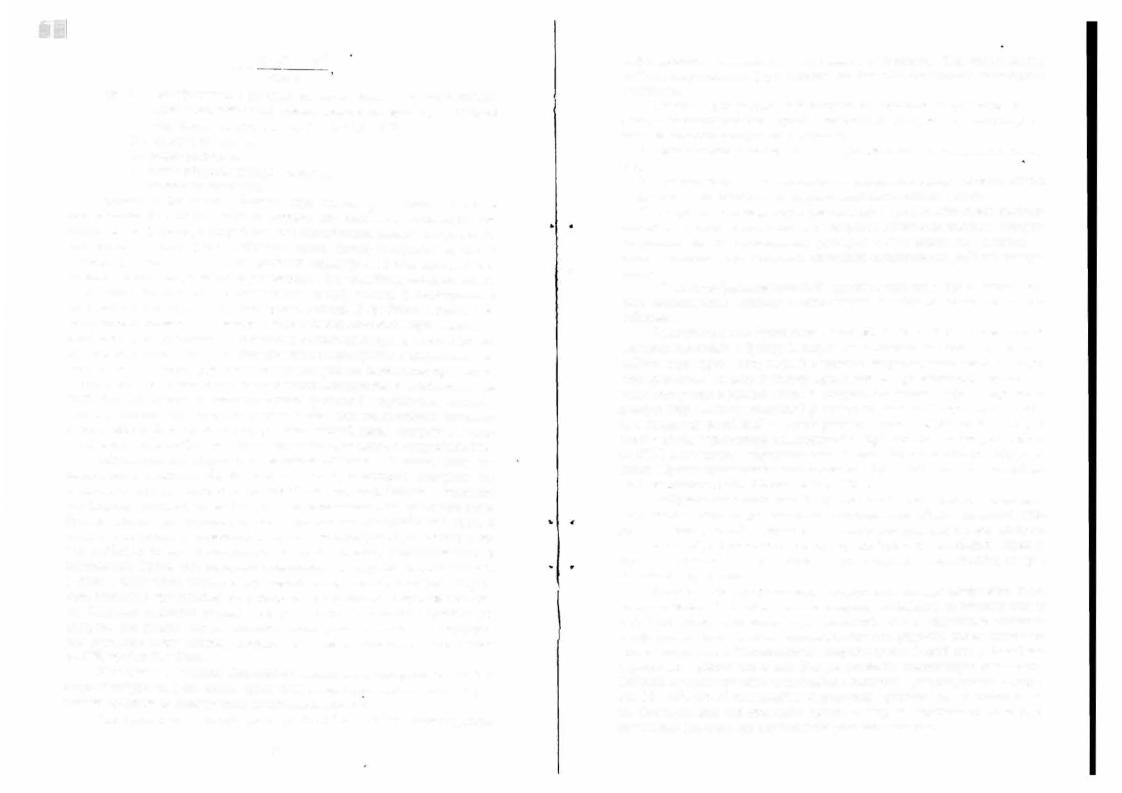
|
K·D |
2 |
·L·п |
2 |
|
|
|
|
|
|
|
|
0= |
|
|
|
|
|
|
|
|
|
|||
|
3600(i- l) |
|
|
|
|
|
|
|
|
|||
|
|
|
|
|
|
|
|
|
|
|||
rде К - коэффициент, величина которого зависи1 |
от конструкции |
|||||||||||
дробилки, твёрдости измельчаемого материала, и который |
||||||||||||
определяется опытным путём, К= 4,6 .;- |
|
6,2; |
|
|
||||||||
D - диаметр ротора, м; |
|
|
|
|
|
|
|
|
|
|
|
|
L - длина ротора, м; |
|
|
|
|
|
|
|
|
|
|
|
|
п - число оборотов ротора в минуту; |
|
|
|
|
|
|
||||||
i - степень измельчения. |
|
|
|
|
|
|
|
|
|
|
|
|
Дисковые дробилки - бывают двух типов: а) |
|
с одним |
диском и |
|||||||||
контрножом; б) с двумя дисками. |
Первый вид дробилок используют для |
|||||||||||
измельчения фруктов, а второй тип для измельчения семян, плодов, стеб |
||||||||||||
лей растений. Плоды (вишня, абрикос, |
алыча, слива) поступают |
·на диск с |
||||||||||
прямоугольными шипами и отверстиями диаметром |
I О мм, которые раз |
|||||||||||
мещены по концентрическим окружностям. При вращении диска со скоро |
||||||||||||
стью 1000 об/мин материал измельчается между диском и неподвижным |
||||||||||||
контрножом и отводится через отверстия в диске. В дробилке с двумя дис |
||||||||||||
ками сырьё измельчается между рабочими плоскостями |
двух дисков. К |
|||||||||||
этой категории оборудования относятся дезинтеграторы |
и дисмембрато |
|||||||||||
ры. Все перечисленные виды оборудования используются в фармацевтиче |
||||||||||||
ской промышленности для измельчения материалов невысокой прочности, |
||||||||||||
а также вязких, волокнистых растительных материалов с влажностью до |
||||||||||||
10%. Это оборудование характеризуется простотой устройства; |
компакт |
|||||||||||
ностью; высокой производительностью и степенью измельчения; |
надёжно |
|||||||||||
стью в работе. Однако ему присущи: повышенный износ штифтов в дезин |
||||||||||||
теграторах и дисмембраторах, большое |
пылеобразование и энергоёмкость. |
|||||||||||
Из.мельчители ударно-истирающего |
действия. |
К этому типу из |
||||||||||
мельчителей относятся барабанные мельницы, |
в которых материал из |
|||||||||||
мельчается внутри вращающегося барабана под воздействием мелющих |
||||||||||||
тел (шаров, стержней, гальки) или самоизмельчением. При вращении бара |
||||||||||||
бана мелющие тела увлекаются под воздействием центробежной силы и |
||||||||||||
силы трения вместе с поверхностью стенок на определенную высоту, а за |
||||||||||||
тем свободно падают и измельчают материал ударом, |
раздавливанием и |
|||||||||||
истиранием. Кро:-.1е того материал измельчается между мелющими телами, |
||||||||||||
а также между этими телами и внутренней поверхностью барабана. В фар |
||||||||||||
мацевтической промышленности чаще всего применяют шаровые мельни |
||||||||||||
цы Шаровая мельница состоит из вращающегося закрытого барабана (из |
||||||||||||
фарфора или стали), внутри которого размещены стальные или фарфоро |
||||||||||||
вые дробящие шары разных размеров, |
которые загружаются в количестве |
|||||||||||
40-50% объёма барабана. |
|
|
|
|
|
|
|
|
|
|
|
|
Кольцевые , tельницы. Для тонкого измельчения материалов малой и |
||||||||||||
средней твёрдости (мел, тальк, красители) используют компактные, но до |
||||||||||||
вольно сложные по конструкции кольцевые мельницы. |
|
4 |
|
|
|
|||||||
Для сверхтонкого измельчения до 75· 10- |
5 |
.;- 1·10- |
мм используются |
|||||||||
|
|
|
ftuбpm(t101t11ыe, струй11ые и коллоид11ые .111елы111t(Ы.Для изrотооления |
|||||
|
мягких лекаре I uсн11ых форм суспензио111ю1·0 гипа пр11меняют коллоидные |
|||||
|
мельницы. |
|
|
|
|
|
|
Ма11111111.1 для разделе11ия с1,111у•111х маt'сриалов 11а фракци ,. В |
|||||
|
химико-фармацевтической промышленности используют три способа раз |
|||||
|
деления сыпучих материалов на фракции: |
|
|
|||
|
1) механическая классификация - рассев сыпучих материалов на си |
|||||
|
тах; |
|
|
|
|
|
|
2) гидравлическая классификация - разделение смеси твердых частиц |
|||||
|
на фракции в зависимости от скорости осаждения частиц в воде; |
|
||||
|
3) воздушная классификация (сепарация) - разделение смеси твердых |
|||||
|
частиц на фракции в зависимости от скорости осаждения частиц в еоздухе. |
|||||
|
Разделение частиц определенных размеров в просеивающих машинах - |
|||||
|
ситах происходит при движении материала относительно рабочей поверх |
|||||
.. . |
ности. |
|
|
|
|
|
|
в химико-фармацевтической промышленности в большинстве слу |
|||||
|
чаев используются машины с качающимся и вибрационным принципом |
|||||
|
действия. |
|
|
|
|
|
|
Вращательно-вибрационное сито ВС-2 (рис. 2.9). Просеиваемый |
|||||
|
материал засыпают в бункер !, откуда он поступает на сито 2, где за счет |
|||||
|
работы двух грузов вибратора 3 создается вибрация, заставляющая поро |
|||||
|
шок вращаться по ситу и конусу приемника 4. Просеиваемый порошок и |
|||||
|
отсев поступают в разные лотки, с которых ссыпаются в заранее приготов |
|||||
|
ленную тару. Частоту колебаний регулируют ременной передачей привода |
|||||
|
5, а амплитуду колебаний-углом раствора грузов вибратора. Сито в про |
|||||
|
цессе работы герметизируется крышкой 6. Вращательно-вибрационное си |
|||||
|
то ВС-2 выпускается Мариупольским заводом технологического оборудо |
|||||
|
вания. Производительность сига составляет 80 - 300 кr/ч при потребляе |
|||||
|
мой мощности 0,4 кВт. Масса машины 132 кг. |
|
|
|||
|
Вибрационное сито (рис. 2.10). Основной предпосылкой качествен |
|||||
|
ного рассева служит равномерное распределение обрабатываемого про |
|||||
|
дукта по всей рабочей поверхности, а также непрерывная подача материа |
|||||
|
ла. Подача обрабатываемого продукта, возбудитель колебаний ткани и |
|||||
|
угол сита должны быть согласованы друг с другом в зависимости от про |
|||||
|
сеиваемого м;;териала. |
|
|
|||
|
Привод сита осуществляется посредством электромагнитного гене |
|||||
|
ратора колебаний. Ситовая ткань и генератор колебаний соединены между |
|||||
|
собой по форме замыкания через толкатель, что обеспечивае |
|
точечное |
|||
|
возбуждение ткани. |
Каждая просеивающая поверхность имеет |
несколько |
|||
|
точек возбуждения. |
_ |
|
_ |
||
|
Расположение генераторов колебании под рабочеи по |
|||||
|
верхностью грохота позволяет быстро заменять изношенную ткань сита. |
|||||
|
Рабочая поверхность сита установлена с наклоном, регулируемым в преде |
|||||
|
лах 20-40 |
° |
, что обеспечивает передвижение продукта по поверхности си |
|||
|
|
|||||
|
та. Одновременно это позволяет решить задачу неподвижности присоеди |
|||||
|
нительных фланцев"при перестановке угла просеивания. |
|
|
32 |
33 |
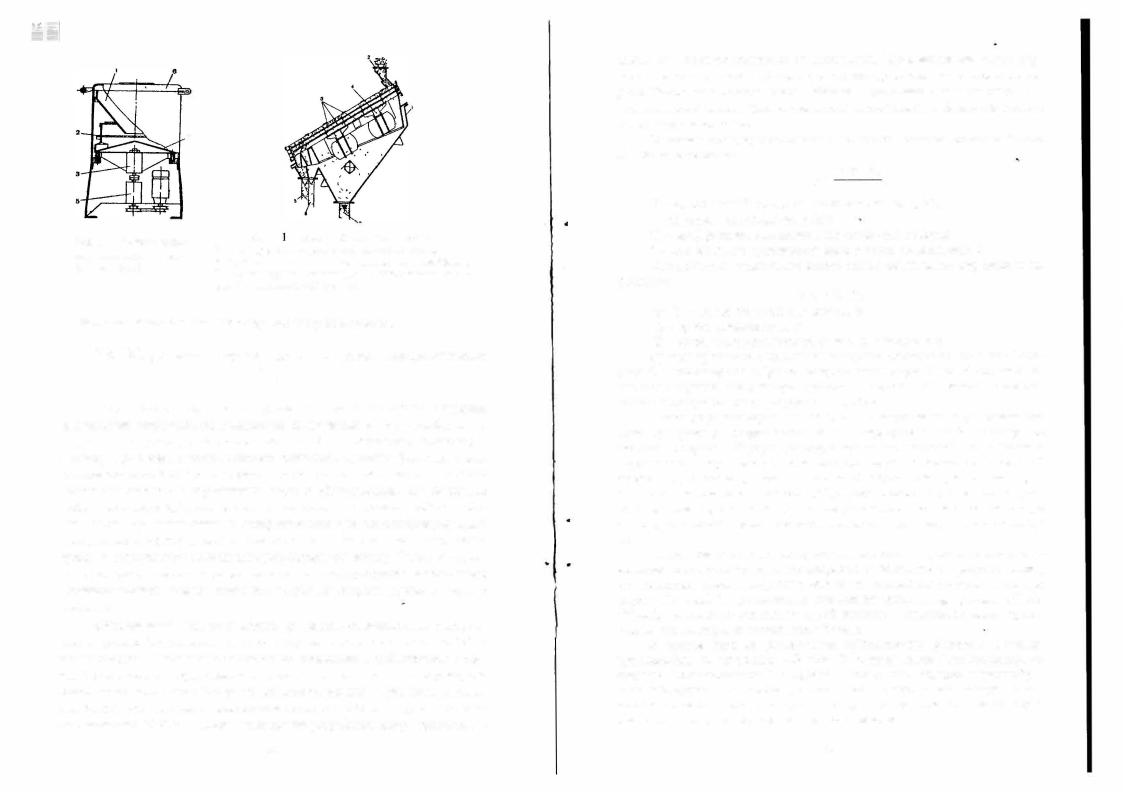
4
Рис. 2. . ·Вращательно |
Рис. |
Схема вибрационного сита |
||
1 - корnус, 2 - воронка для nодачи материала, 3 - |
||||
вибрационное |
сито |
|||
(модель ВС-2). |
|
сита, 4 - электромагнитные возбудители колебаний, |
||
|
5 - выход круnной фракции, 6 - выход сред11ей фрак |
|||
|
|
ции, 7 - выход мелкой фракции
Интенсивность качания вибратора можно регулировать.
2.6. Оборудование производства твердых лекарственных форм
Производство твердых лекарственных форм включает опер;щии: смешивания ингредиентов; грануляции полученной смеси; калибровки и опудривания гранул; таблетирования; нанесения покрытий; упаковки в блистеры, флаконы, пеналы; упаковки блистеров, пеналов, флаконов в кар тонные коробки. GMP рекомендует проводить технологические процессы получения твердых лекарственных форм в оборудовании, где возможно последовательное проведение нескольких операций в одном рабочем объ еме, напр11мер: смешивание и гранулирование (смесители-грануляторы); грануляцию и сушку (грануляторы-сушилки); смешивание, грану яцию, сушку и опудривание (смесители-грануляторы-сушилки). Такое оборудо вание позволяет избежать загрязнения сырья, полупродуктов, максимально автоматиз11 ровать ведение ,процесса; сократить затраты ручного труда и
времени.
Оборудование для проведения процессов смешивания, грануля ции и сушки. Смешивание твёрдых сыпучих материалов между собой, а также твёрдых материалов с жидкими компонентами в таблеточном и дру гих производствах осуществляется, в осно.вном, в смесителях периодиче ского действия с двумя Z-образными лопастями или червячным переме шивающим устройством и поворотным корпусом. Масса загружаемой сме си составляет 80-450 кг. Перемешивающие устройства могут вращаться в
..
.. ..
..
одном или противоположных направлениях. Перемешивание массы осу ществляется в процессе её перетирания между лопастями и стенками ко рыта Таким комбинированным действием достигается гомогенизация пе речешиваемой массы. Корпус смесителя может иметь рубашку для подачи
теплоили хладоаrента.
Массовая производительность смесителей периодического дейс1 вия Q, кг/ч, определяется:
V·v·K
Q= т з'
V - номинальный объём смесительной камеры, м3;
v - насыпная масса смеси, кг/м3;
К, - коэффициент заполнения смесительной 1<амеры;
Т - длительность производственного цикла смешивания, ч. Длительность производственного цикла смешивания определяют по
формуле:
Т=Т1 +Т2+Тз, где Т1 - время загрузки смесителя, ч;
Т2 - время смешивания, ч; Т - время выгрузки готовой смеси из смесителя, ч. Гранулирование3 . Подготовка гранулята является очень важной опе-
рацией в производстве твёрдых лекарственных форм и для её осуществле ния используются грануляторы с различным принципом действия: колеба тельные; центробежные; экструзионные; тёрки. Широкое распространение получили экструзионные грануляторы.
Этот гранулятор представляет собой перфорированный цилиндр со сплошным торцом. Внутри цилиндра вращается винтовой вал. Материал выдавливается через перфорированный цилиндр и попадает в специальный барабан, где происходит окончательная обработка. На предприятиях при меняются грануляторы типа 3027 (Мариупольского ЗТО), а также грануля торы немецкой фирмы «Glatt», производительность которых от 150 кг/ч, а
диаметр отверстий изменяется в интервале от 1 до 4 мм, через каждые 0,5
мм.
На сегодняшний день на предприятиях отдают предпочтение обору дованию, в котором совмещены операции СТ\1ешивания и гранулирования, что позволяет снизить затраты времени на проведение процесса и потери сырья. На рис.2 11 представлен смеситель-гранулятор фирмы «Glatt» VG-600, который представляет собой емкость с откидывающейся крыш кой, изготовленную из нержавеющей стали.
В днище ёмкости установлена трёхлопастная резцовая мешалка, вращающаяся со скоростью 4-8 об/с. В боковой части ёмкости внизу, со сторfны противоположной выгрузному отверстию находится импелл.ер - винт, оборудованный ножами, с помощью которого гомогенизированный материал измельчается в гранулят. Гранулят выводится из ёмкости через пневматически управляемое выгрузное отверстие.
34 |
35 |
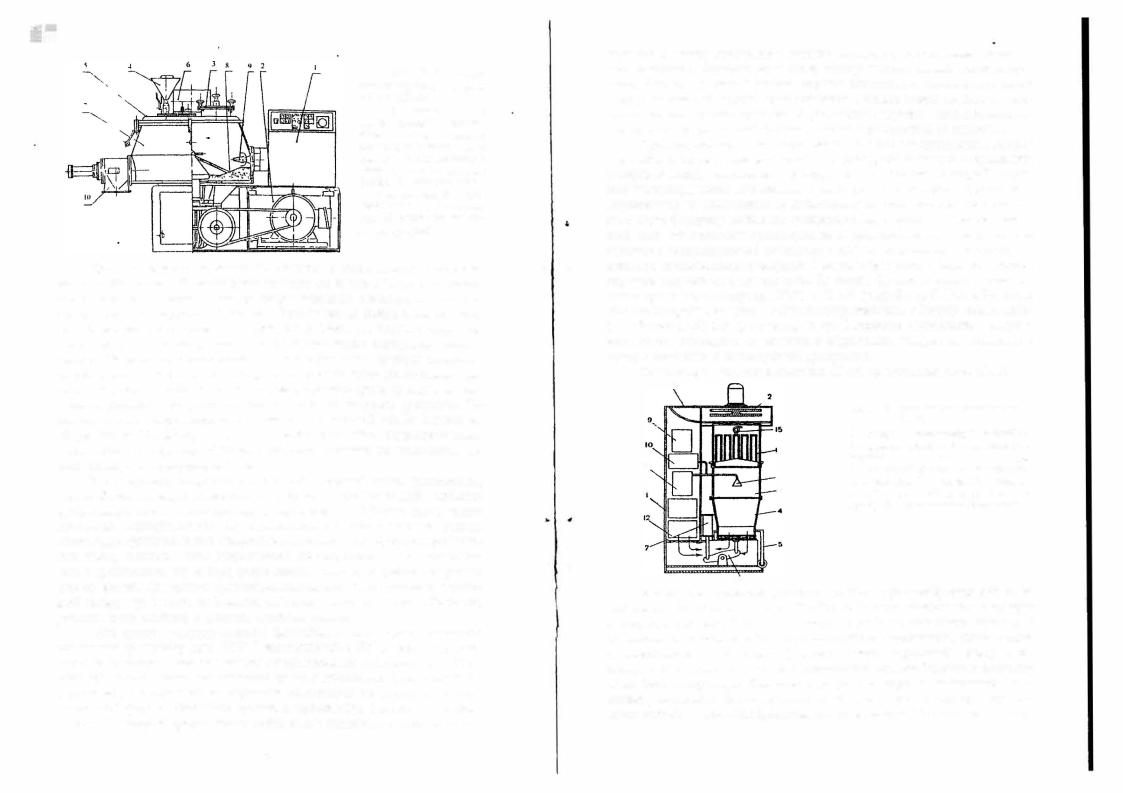
- .ьl
Рис 2.11 Смсси- 1ель-1·ранулятор фирмы
"Glatt» VG-600
1 - панель управле ния, 2 - привод, 3 - люк для загрузки сырья, 4 - мерник д.1я грануляцион1юй жидко сти, 5 - откидывающаясярышка, 6 - воздушный филь,р, 7 - емкость смеси теля-гранулятора, 8 - ре, цовая мешалка, 9 - имnел лер, 1О --<Jтверстие для вы грузки продукта
Крышка герметично закрывает ёмкость и закрепляется откидными болтами. На крышке ёмкости располагается воздушный фильтр, загрузоч ное отверстие, которое имеет предохранительную решётку, мерник для грануляционной жидкости. Крышка оборудована предохранителем, кото рый блокирует её открывание в процессе работы. Смеситель-гранулятор
смонтирован на станине, внутри которой размещены электродвигатель и привод. На станине смонтирована панель управления, которая позволяет
автоматически включать установку, регулировать скорость вращения ме шалки, параметры работы импеллера, регулировать время проведения опе рации и управлять устройством пневматической выгрузки гранулята. Та кие смесители-грануляторы могут иметь номинальный объём ёмкости от 25 до 600 л. Коэффициент заполнения ёмкости 75%. Технологический
цикл работы гранулятора 6-10 мин. Из этого времени на гомогенизацию идёт 2 мин., а на грануляцию 4-8 мин.
В тех случаях, когда компоненты таблетируемой массы разлагаются, теряют биологическую активность в присутствии увлажнителей - таблети
руемая масса подвергается сухому гранулирощшию. Обычно сухое грану лирование осуществляется на горизонтальных металлических валках, сжимаемых пружинами или гидравлическим поршнем. Продукт пропуска ется между валками в виде непрерывной полосы, которая затем измельча ется и просеивается через перфорированную пластину с требуемым разме
ром отверстий. Для сухого гранулирования может быть применен червяч ный экструдер, в котором колонка материала продавливается с большим усилием через пластину с нужным размером отверстий.
Для сухого гранулирования в фармацевтической промышленности применяют гранулятор типа 3027 (Мариупольского ЗТО). Производитель ность гранулятора в режиме сухого гранулирования составляет от 150 до 1000 кг/ч. Перспективными являются пресс-грануляторы фирмы «ХУТТ)) (Германия), в которых смесь порошков уплотняется до получения гранул чечевичной формы. Рабочими органами гранулятора являются прессую щие валки, которые представляют собой полые цилиндры с зубцами на по-
..
""1
-.
верхнос1 и, между ко1 орыми в стенках цилиндров расположены радиаль ные отn1:1к п1я. 13ер1икальный шнек принудительно подаёт порошковую массу. IЗалки, nращаясь в разные стороны, захватывают порошковую массу и продавливают её внутрь через отверстия в стенке полых валков, где спе циальный нож срезает гранулы. В результате получают высококачествен ные гранулы с одинаковой формой, массой и достаточной прочностью.
Граиулиртитие в «кипящем слое>> является перспективным, потому что в объёме одного аппарата возможно проведение операции смешива1n1я, гранулирования, высушивания и опудривания. Порошок, который подле жит гранулированию помещается в рабочую часть аппарата, rде он под держивается во взвешенном псевдоожиженном слое потоком воздуха. На него через форсунку наносится гранулирующая жидкость. Псевдоожижен ный слой обеспечивает кратковременное взаимодействие лекарствещ1ых веществ с гранулирующей жидкостью и нагретым воздухом, что благопри ятно для нестабильных препаратов. Получаемые гранулы характеризуются
хорошей текучестью и прочностью. На наших фармацевтических предпри ятиях применяют аппараты СГ-30 и СГ-60 (разработка С-Петербургского IШО «Прогресс)), выпуск - «Дезхимоборудование», г.Пенза), «Aeromatic» (Швейцария), «Glatt» (Германия) и др. Механизм образования гранул в
этом случае отличается от механизма образования гранул при увлажнении смеси в смесителе и последующей грануляции.
Принципиальная схема аппарата СГ-30 представлена на рис.2.12.
е
Рис.2 12. Сушилка-гранулятор типа
|
|
|
СГ-30. |
|
· |
1 - корпус, 2 - вентилятор, 3 - обечайка, |
|
|
4 |
- рабочая емкость, 5 - тележка, 6 - |
|
|
3 |
||
|
рычажная система, 7 - nневмоцилиндр, |
||
11 |
|
||
|
8 |
- воздушный фильтр, 9 - компрессор, |
з |
1 О - рессивер, 11 - насос, 12 - калори |
|
фер, 13 - рукавный фильтр, 14 - фор |
||
|
||
|
сунка, 15 - встряхивающее устройство |
6
В рабочую ёмкость загружается до ЗОкг порошкообразной таблеточ ной смеси При помощи тележки 5 рабочая ёмкость закатывается в аппарат и посредством воздействия пневмоцилиндра 7 на рычажную с11стему 6 поднимается до уровня обечайки, с которой она соединяется. Поток возду ха всасывается вентилятором 2, проходит через воздушный фильтр 8, ка
лорифер 12 и далее попадает непосредственно под дно ёмкости и проходит через li.eгo снизу вверх. При этом продукт приходит во взвешенное («ки пящее») состояние. Затем во взвешенный слой через форсунку l при по мощи насоса 11 подаётся гранулирующая жидкость. По окончании грану-
37
36
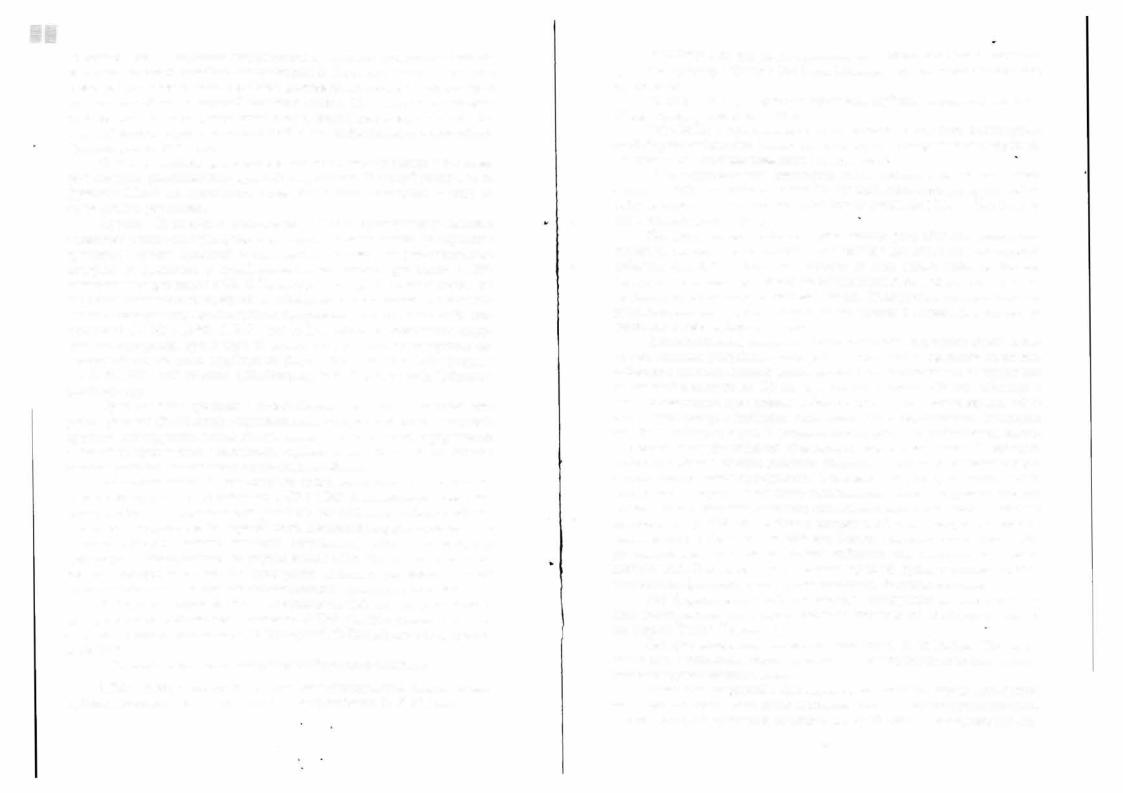
лирования подача жидкости прекращается и форсунка продувается сжатым воздухом, который подаётся компрессором 9. После этот гранулят сушится в режиме «кипящего слоя». При этом увлажнённый воздух проходит через установленный над форсункой рукавный фильтр 13, в котором задержива
ются мелкие частицы гранулированного и высушенного материала, а очи щенный воздух через ве_нтиляционный канал выбрасывается в атмосферу. Процесс длится 25-45 мин.
Одним из важных факторов при сушке и гранулировании в кипящем слое является распределение фракций по размерам. В данной установке на фракцию 0,25-2 мм приходится около 90 %. Этот показатель - одно из преимуществ установки.
Сушка На качество получаемых таблеток существенное влияние
оказывае;r влажность прессуемого материала. В зависимости от,характера гранулятов сушку проводят в полочных сушw,ках, вакуум-сушw,ьных
1икафах, в cy,uw,кax с псевдоо:,ки:нсенным слоем, сушилках с ИК
излучение"н ll суmилка.х с СВЧ. На сегодняшний день в производстве ча ще всего применяются сушилки с псевдоожиженным слоем. На отечест
венных предприятиях используются следующие типы сушилок этой кон струкции: СП-30; СП-60; СП-100, где цифра указывает количество загру
жаемого материала, кроме того на наших предприятиях используются ап параты такого же типа зарубежных фирм "Aeromatic-AG" (Швейцария);
UTPA-30, 200, 400 Munster (Швейцария); "Glatt" (Германия); "Manesty"
(Англия) и др.
Преимущества сушилок с псевдоожиженным слоем - высокая ско рость процесса (20-50 мин); сокращение энергозатрат и рабочих площадей; простота конструкции; возможность полной автоматизации и улучшение
условий обслуживания; возможность сушить термолабильные препараты; высокая скорость межфазного тепло- и массообмена.
Таблетирование. К конструкции таблеточных машин и их оснаще
нию в соответствии с требованиями ВОЗ и GМР предъявляются очень вы сокие требования: герметизация рабочего пространства таблеточной ма
шины для предупреждения перекрёстной контаминации; удобство о истки
машины; простота замены оснастки; изготовление рабочей камеры, где происходнт таблетирование из нержавеющей стали без применения лаки рованых поверхностей; наличие рессорного механизма установки машины
сцелью уыеньшения вибрации; автоматическое управление машинами.
ВУкраине и странах СНГ в производстве таблеток широко исполь зуют роторные таблеточные 111а иины (РТМ), разработчиками и изгото
вителями которых являются НПО "Прогресс" (С-Петербург) и Мариуполь ский зто
Широко применяются следующие таблеточные машины:
РТМ-41М2В, у которой 41 пара пресс-инструмента, максимальная глубина заполнения матрицы - 18 мм диаметр таблеток 5-15 и 20 мм.
"
.. ..
"4
..
РТМ-3028 - 57 пар пресс-инструмента, глубина заполнения маrриц1,1
до 18 мм, диаметр таблеток 16-18 мм. Машина предназначена для прямого прессова11ия.
РТМ43 - 43 пары пресс-инструмента, глубина заполнения матрицы 17 мм; диаметр таблеток 13-20 мм
РТМ-300М - применяется для изготовления таблеток цилиндриче ской формы небольших диаметров с плоскими и сферическими торцами. Максимальная глубина заполнения матриц до 12 мм.
Производительность некоторых типов таблеточных машин может достигать 495 тыс. таблеток в час. На предприятиях эксплуатируют табле точные машины известных западных производителей: Fette, Kilian (Герма ния); Manesty (Англия) и др.
Контроль массы таблеток производится устройством, производи тельность которого не менее 2000 операций/час при массе контролируемой таблетки 0,15-0,75 г. Установка состоит из узла отбора таблетоi,'" блоков контроля и сигнализации. В случае отклонения массы таблеток от заданно го значения включается сигнальная лампа. Конструкция современных за рубежных машин предусматривает их включение и остановку в случае от клонения массы таблеток от нормы.
Автоматический контроль на металлические включения производит ся при помощи устройства, которое обнаруживает и извлекает нз потока таблетки с металлическими включениями. Они обеспечивают обнаружение включений размером до 0,5 мм при скорости потока 100 тыс. таблеток в час. По окончании прессования таблетки помещают в установку для обес пыливания, которая снабжена пылесосом. Производительность установки до 150 кг таблеток в час. В современных зарубежных таблеточных маши нах обеспыливание таблеток производится сразу в машинах. На качество таблеток влияет величина давления, скорость прессования, состояние и из нщ:остойкость пресс-инструмента, а именно: твёрдость, качество, форма пуансонов и матриц. Более всего изнашивается пресс-инструмент, так как он испытывает большие нагрузки: частота циклов более 4 тыс./мин, усилия прессования до 100 кН. Стойкость матриц в 2-3 раза ниже, чем у пуансо нов. Поэтому в Украине и за рубежом большое внимание уделяется выбо ру материалов повышенной износостойкости для изготовления пресс инструмента. Это материалы на основе карбидов хрома и никеля, кобаль тохромовольфрамовые и азотированные стали, бронзовые сплавы.
Для формирования таблеток методом тритурации на некоторых на
ших предприятиях используют довольно сложные по конструкции маши ны фирмы "Fette" (Германия).
Оборудование для нанесения покрытия на таблетки Покрытия наносятся, в основном, двумя методами - в дражировочных котлах и аппа ратах,псевдоожиженного слоя,
Нанесение покрытий в дражировочных котлах широко применяет ся на предприятиях. Этот метод отличается высокой производительностью. В котёл который вр,ащается со скорос:rью 30-60 об/мин, помещают двояко-
38 |
39 |
|