
Основы менеджмента
.pdf
Типы производств. Типы планировок производств. Производственная мощность. Календарное планирование. Диспетчеризация
чить во времени использование системы машин для обработ- ки некоторого множества изделий. При этом должны быть упорядочены определенные технологические условия и обес- печено достижение оптимального значения заранее заданного критерия качества расписания.
Трудности решения задач теории расписаний обуслов- лены большим числом вариантов упорядочивания. Обычно используются методы, основанные на эвристических правилах предпочтения или на случайном поиске.
Задача календарного планирования работы участка единичного или мелкосерийного производства формулирует- ся следующим образом: m изделий (или серий) должны прой- ти обработку на одном или более из n типов станков.
Для каждого изделия (серии) задается технологический маршрут, т.е. последовательность номеров станков, на кото- рых оно обрабатывается. Известны трудоемкости соответст- вующих операций. Предполагается, что одновременно на станке выполняется не более одной операции; операция, на- чавшись не может быть прервана; последующая операция по обработке каждого изделия может начаться лишь по оконча- нии предыдущей; длительность операций не зависит от по- следовательности их выполнения; время на транспортировку и переналадку станков невелико.
Цель заключается в построении календарного графика обработки изделий, оптимального с точки зрения некоторого критерия.
Критерии оптимальности можно разделить на 2 типа:
1.в зависимости от заданных сроков готовности: мини-
мизация отставания от заданных сроков; минимизация издержек, связанных с невыполнением работы в срок; минимизация числа отстающих работ;
2.в зависимости от общей продолжительности обработ-
ки изделий: минимизация продолжительности кален- дарного графика; минимизация простоев станков или пролеживания деталей; максимизация некоторого пока- зателя использования оборудования; минимизация из- держек на незавершенное производство и т.д.
131
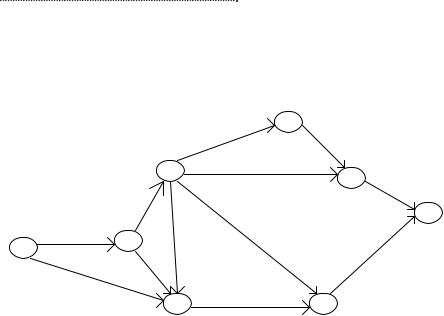
Основы менеджмента
Анализ отношений очередности операций удобно про- водить на сетевых графиках.
Сетевые графики представляют цепи работ и событий, от- ражаяихтехнологическуюпоследовательностьисвязь(рис. 31).
|
|
|
4 |
|
4 |
|
|
|
|
|
5 |
|
|
|
|
|
|
|
|
|
|
|
2 |
|
14 |
5 |
13 |
|
|
|
|
|||
|
|
|
|
|
||
|
|
10 |
|
|
|
7 |
|
|
|
|
|
|
|
0 |
5 |
1 |
|
|
5 |
|
|
|
|
4 |
|
||
|
4 |
|
|
|
||
|
|
|
|
|
||
|
|
|
|
|
|
|
|
3 |
|
|
10 |
|
|
|
|
3 |
|
6 |
|
|
|
|
|
|
|
Рис. 31. Сетевой график
В кружках указаны номера событий (результатов выпол- нения одной или нескольких работ), стрелки означают рабо- ты; цифры над ними называются временными оценками (они показывают ориентировочную продолжительность работ).
Реальные сетевые графики содержат сотни и даже тыся- чи работ и событий. Они могут приобретать вид таблицы (так называемое цифровое представление сети).
Методы и программы расчетов по сетевым графикам стандартны. Это позволяет вести расчеты на самых различных объектах.
Последовательность работ в сети, в которых каждое ко- нечное событие является исходным для начала других работ, называется путем.
Большое значение сетевые графики имеют для нахожде-
ния критического пути.
132

Типы производств. Типы планировок производств. Производственная мощность. Календарное планирование. Диспетчеризация
Критический путь – это непрерывная последователь- ность работ и событий от начального до конечного события, требующая наибольшего времени для ее выполнения.
Путь, наибольший по длине, определяет общую про- должительность изготовления изделия. Как бы быстро ни бы- ли завершены работы, лежащие на других путях, все равно придется дожидаться окончания первого (критического).
Разница между продолжительностью критического пути и продолжительностью любого другого пути называется ре-
зервным временем пути.
Резерв времени события показывает, на какой предельно допустимый период можно задержать свершение этого собы- тия, не увеличивая при этом общий срок создания объекта.
В нашем примере между событиями 2 и 7 проходят че- тыре пути:
1.через события 2, 5, 7;
2.через события 2, 6, 7;
3.через события 2, 3, 6, 7;
4.через события 2, 4, 5, 7. Подсчитаем длину путей:
1.14 + 13 = 27 минут;
2.5 + 4 = 9 минут;
3.4 + 10 + 4 = 18 минут;
4.4 + 5 + 13 = 22 минуты.
Таким образом, самый длинный (критический) путь со- ставляет 27 минут.
Вкачестве инструмента оперативного планирования и управления производством могут использоваться учетно- плановые графики Ганта (циклограммы).
Они позволяют наглядно представить соотношение вре- мени выполнения работ в планируемом периоде, загрузку оборудования.
Вкрайнем левом столбце таблицы записывают номера пунктов, в следующем – формируют содержание пунктов плана, наименование работ, используемое оборудование и
133
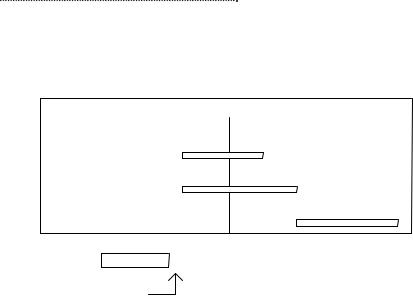
Основы менеджмента
т.п. Затем идут столбцы, соответствующие календарному вре- мени выполнения плана. В этих столбцах отмечается время начала работы по пункту плана, а продолжительность соот- ветствует длине отрезка, изображенного на плане (рис. 32).
№ |
|
Объект |
|
|
|
Календарный период |
|
|
|||||
|
планирования |
|
|
|
|
|
|
|
|
|
|
|
|
|
|
|
Понедельник |
|
Вторник |
Среда |
Четверг |
Пятница |
|||||
|
|
|
|
|
|||||||||
|
|
|
|
|
|
|
|
|
|
|
|
|
|
1 |
|
Станок 1 |
|
|
|
|
|
|
|
|
|
|
|
|
|
Изделие |
А |
|
|
|
|
|
|
|
|||
|
|
|
|
|
|
|
|
|
|
|
|
|
|
2 |
|
Станок 2 |
|
|
|
|
|
|
|
|
|
|
|
|
|
|
|
Изделие А |
|
|
|
|
|
|
|||
|
|
|
|
|
|
|
|
|
|
|
|
|
|
3 |
|
Станок 3 |
|
|
|
|
|
|
|
|
|
|
|
|
|
|
|
|
|
|
|
|
|
|
Изделие |
А |
|
Плановое |
|
|
|
Плановое |
|
|
|
|
|
|
|
|
|
|
|
|
|
|
|
|
|
|
|
|
|||
время |
|
|
|
время |
|
|
|
|
|
|
|
|
|
начала |
|
состояние |
|
окончания |
|
|
|
|
|
|
|
|
|
|
|
|
|
|
|
|
|
|
|
||||
|
|
|
|
|
|
|
|
|
|
|
|
|
|
|
|
работы |
|
|
|
|
|
|
|
|
|
|
|
Рис. 32. График Ганта
Под диспетчерским контролем, или диспетчеризаци-
ей понимают систему централизованного контроля и управ- ления производственными процессами, осуществляемую дис- петчером из центрального пункта при помощи технических средств связи, сигнализации, телемеханики и автоматики.
Его цель состоит в обеспечении равномерного и ком- плектного выполнения плана. Особое значение для ритмич- ного хода производства имеют функции предупредительного контроля отклонений от установленного графика.
Диспетчеризация включает:
•непрерывный учет и текущую информацию о фактиче- ском ходе работ по выполнению установленного графика;
•принятие оперативных мер по предупреждению и уст- ранению отклонений от плана;
•выявление и анализ причин отклонений;
•координацию текущей работы взаимосвязанных звеньев производства в целях обеспечения ритмичного хода ра- боты по установленному графику;
134

Типы производств. Типы планировок производств. Производственная мощность. Календарное планирование. Диспетчеризация
•организационное руководство оперативной подготовкой всего необходимого для выполнения сменно-суточных заданий и календарных графиков производства.
Вразных типах производства конкретное содержание диспетчерского руководства имеет ряд существенных особен- ностей.
Вединичном производстве основным объектом диспет- черского контроля за ходом производства являются сроки вы- полнения важнейших работ по отдельным заказам.
Диспетчерский контроль осуществляется в этих услови- ях применительно к разработанным сетевым графикам вы- полненных заказов.
Вусловиях серийного производства главным объектом диспетчерского наблюдения являются установленные по пла- ну сроки запуска и выпуска партий заготовок и деталей на всех участках производства, а также состояние складских заде- лов заготовок и степень комплектной обеспеченности сбороч- ных работ в соответствии с графиком.
Под контролем диспетчера также должны находится графики переналадки оборудования, учитывая, что серийное производство предусматривает постоянную переналадку обо- рудования.
Вусловиях массового производства диспетчерское на- блюдение должно быть направлено на проверку соблюдения установленного такта работы поточных линий и норм заделов на всех стадиях производственного процесса.
Такой контроль осуществляется, как правило, с помо- щью суточных и часовых графиков работы.
135

ТЕМА 9.
Управление качеством
Управление качеством – действия, осуществляемые при создании и эксплуатации или потреблении продукции, в це- лях установления, обеспечения и поддержания необходимого уровня ее качества.
Управление качеством продукции должно осуществляться системно, т.е. на предприятии должна оформиться и функцио- нировать система управления качеством продукции. В России былиразработаныразличныесистемыуправлениякачеством.
Наибольшую известность получили такие системы как БИП (бездефектное изготовление продукции), СБТ (система бездефектного труда), КАНАРСПИ (качество, надежность, ре- сурс с первых изделий), НОРМ (научная организация работ по повышению моторесурса двигателей), КСУКП (комплекс- ная система управления качеством продукции), КСПЭП (ком- плексная система повышения эффективности производства), КСУКП и ЭИР (комплексная система управления качеством продукции и эффективность использования ресурсов).
При управлении качеством продукции используется ряд методов:
•экономические методы, которые обеспечивают создание экономических условий, побуждающих коллективы предприятий улучшать продукцию;
•методы материального стимулирования, предусматри- вающие поощрение работников;
•организационно-распорядительные методы, осуществ- ляемые посредством обязательного исполнения дирек- тив, приказов, требований нормативной документации;
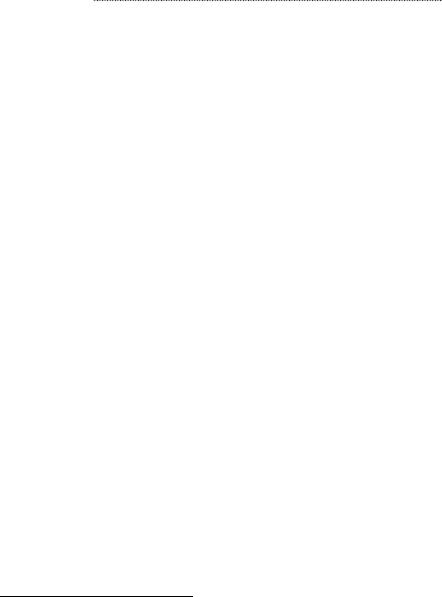
Управление качеством
•воспитательные методы, которые предполагают мораль- ное поощрение.
Впоследние годы сформировалась новая стратегия в управлении качеством. Ее отличительные черты состоят в следующем1:
•обеспечение качества понимается не как техническая функция, реализуемая определенным подразделением, а как систематический процесс, пронизывающий всю ор- ганизационную структуру фирмы;
•новому понятию качества должна отвечать соответст- вующая структура предприятия;
•вопросы качества охватывают не только рамки произ- водственного цикла, но и процесс разработок, конструи- рования, маркетинга, послепродажного обслуживания;
•качество должно быть ориентированно на удовлетворе- ние требований потребителя, а не изготовителя;
•повышение качества продукции требует применения новой технологии производства, начиная с автоматиза- ции проектирования и кончая автоматизированным из- мерением в процессе контроля качества;
•всеобъемлющее повышение качества достигается только
заинтересованным участием всех работников. Всеобъемлющий контроль качества (TQM – Total Quality
Management) предполагает наличие трех условий:
1.Качество как основная стратегическая цель деятельности признается высшим руководством фирм. Для этого уста- навливаются конкретные задачи и выделяются средства для их решения. Поскольку требования к качеству опре- деляет потребитель, уровень качества не может быть по- стоянным. Повышение качества должно идти по возрас- тающей, т.к. качество – постоянно меняющаяся цель.
2.Мероприятия по повышению качества должна затраги- вать все подразделения. От 80 до 90% мероприятий не подлежат контролю отделов качества.
1 Справочник директора предприятия / Под ред. М. Г. Лапусты. – 2-ое изд. – М.: ИНФРА-М, 1998. – С. 224.
137

Основы менеджмента
3. Непрекращающийся процесс обучения (ориентирован на определенное рабочее место) и повышение мотива- ции персонала.
Важным элементом в системах управления качеством из-
делий является стандартизация.
Главная задача стандартизации состоит в создании сис- темы нормативно-технической документации, определяющей прогрессивные требования к продукции, а также контроль за правильностью использования этой документации.
Внастоящее время сформировалась государственная система стандартизации Российской Федерации, которая рег- ламентирует процессы построения, изложения и распростра- нения стандартов в России.
ВРоссийской Федерации нормативные документы по стандартизации подразделяются на следующие категории:
•государственные стандарты (ГОСТ РФ);
•отраслевые стандарты (ОСТ);
•технические условия (ТУ);
•стандарты предприятий и объединений предприятий
(СТП);
•стандарты научно-технических обществ и инженерных союзов, ассоциаций и других объединений (СТО). Согласно Федеральному закону «о техническом регу-
лировании» от 27 декабря 2002 г. в России разрабатываются новые стандарты, которые называются техническими рег- ламентами.
Сертификация – деятельность уполномоченных орга- нов по подтверждению соответствия товара (работы, услуги) обязательным требованиям стандарта и выдаче документа со- ответствия.
В России национальным органом по сертификации яв- ляется Федеральное агентство по техническому регулирова- нию и метрологии.
Сертификационные испытания проводятся специаль- ными центрами (испытательными лабораториями).
Сертифицированная продукция – продукция, соответ-
ствующая конкретному стандарту или другому нормативно- му документу, удостоверяющему, что производимая продук-
138
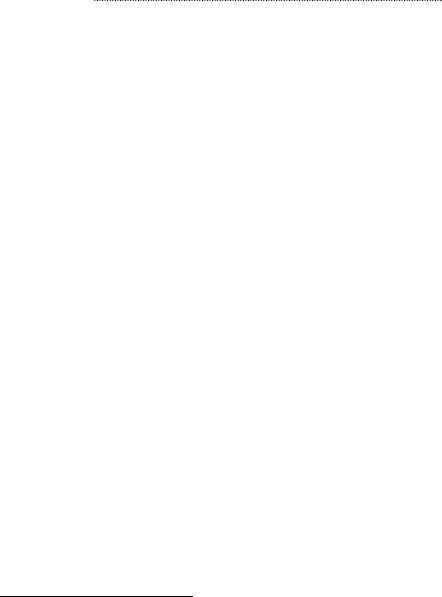
Управление качеством
ция отвечает требованиям соответствующих технических ус- ловий (техническим требованиям, требованиям технического регламента и др.).
Сертифицированная продукция должна иметь под- тверждающее доказательство – клеймо, специальный знак, этикетку, сопроводительный документ, сертификат.
Госстандарт России разработал специальный знак – «Знак соответствия», и любой продукт, произведенный в Рос- сии с сертификатом качества, должен иметь знак соответствия на каждой упакованной единице. Состоит он из двух частей: непосредственно знак в виде графического изображения букв «С», «Р», «Т» и код органа Госстандарта России, выдавшего сертификат, состоящий из двух букв и двух цифр.
Сертификация может быть:
•обязательной – для продукции, потенциально опасной для здоровья человека и окружающей среды, а также способной причинить вред имуществу потребителей;
•добровольной – по инициативе юридических лиц и гра- ждан на основе договора между заявителем и органом по спецификации. Сертификат, полученный при этом, яв- ляется дополнительной гарантией качества продукции,
что повышает ее конкурентоспособность.
Объектами сертификации может быть не только кон- кретная продукция, но и состояние производства, система управления качеством.
Первоначально вопросы изучения качества продукции ограничивались только лишь регистрацией и заменой де- фектных изделий.
Первые серьезные исследования, связанные с качест- вом, появились после второй Мировой войны. В 80-е гг. тре- бования к качеству стали главными в обеспечении конку- рентоспособности.
По оценкам зарубежных ученых, объективно необходи- мо, чтобы расходы на качество составляли не менее 15-25% со- вокупных производственных затрат1.
1 Кохно П. А., Микрюков В. А., Комаров С. Е. – Менеджмент. – М.: Фи- нансыистатистика, 1993. – С. 177.
139

Основы менеджмента
Первыми важность проблемы качества признали в Японии. При этом японцы основной акцент сделали на вовлечение всех работниковвдеятельностьпоулучшениюкачества.
Большое распространение в Японии получили кружки качества, механизм действия которых рассмотрен выше.
Движение кружков качества поддерживается специаль- ным общеяпонским штабом, имеющим свой журнал и прово- дящим ежегодные конференции.
Таким образом, можно сказать, что работа по улучше- нию качества выходит за рамки отдельных фирм и приобре- тает общенациональный характер.
Часто японские кружки качества связывают с нацио- нальными особенностями японцев, что выражается в коллек- тивизме и большом интересе к обучению (каждый рабочий хочет стать инженером).
Широкое распространение кружков качества требует от рабочих не только определенной психологии, но и достаточно глубокого знания статистических методов.
Одним из основных инструментов в обширном арсенале статистических методов контроля качества являются кон- трольные карты. Принято считать, что идея контрольной кар- ты принадлежит известному американскому статистику Уол- теру А. Шухарту. Она была высказана в 1924 г. и обстоятельно описана в 1931 г. Первоначально они использовались для ре- гистрации результатов измерений требуемых свойств про- дукции. Выход параметра за границы поля допуска свиде- тельствовал о необходимости остановки производства и про- ведении корректировки процесса в соответствии со знаниями специалиста, управляющего производством.
Это давало информацию о том, когда, кто, на каком оборудовании получал брак в прошлом.
Однако в этом случае решение о корректировке при- нималось тогда, когда брак уже был получен. Поэтому важ- но было найти процедуру, которая накапливала бы инфор- мацию не только для ретроспективного исследования, но и для использования при принятии решений. Это предложение опубликовал американский статистик И. Пейдж в 1954 г. Кар-
140