
МУ по выполнению ПЗ № 2 ОП
.pdf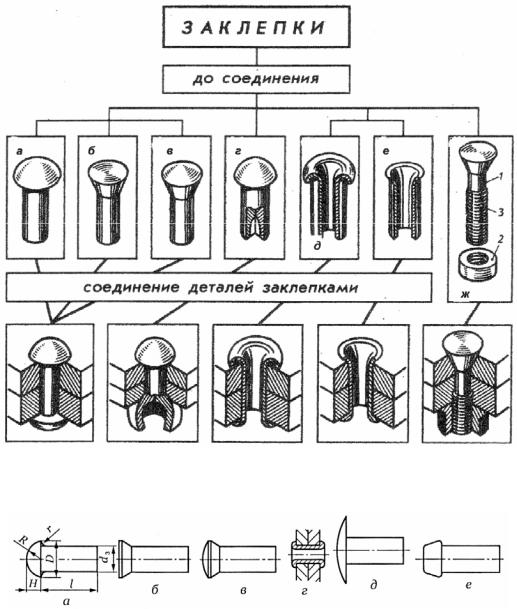
полукруглой головкой — ГОСТ 10299-80 (рисунок 14, а); с потайной
головкой — ГОСТ 10300-80 (рисунок 14, б); с полупотайной головкой —
ГОСТ 10301-80 (рисунок 14, в) и др.
Рисунок 13
Рисунок 14 – Основные типы заклепок:
а — с полукруглой головкой; б — с потайной головкой; в — с полупотайной головкой; г — пустотелая; д — с широкой головкой; е — с плоской головкой
Наиболее часто применяют сплошные стержневые заклепки с полукруглой головкой; в местах, где требуется обтекаемость, используют заклепки с потайной и полупотайной головками.
Соединения из мягких материалов выполняют с пустотелыми заклепками. Заклепки с широкой головкой применяют для соединения тонких
листовых материалов (рисунок 14, д).
31
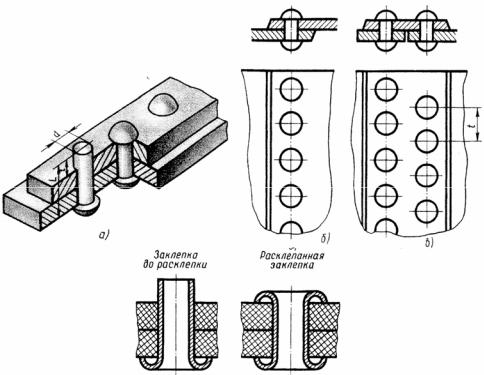
На рисунке 15, а показано соединение двух деталей при помощи заклепок с полукруглой (сферической) головкой.
Рисунок 15
В соединяемых деталях сверлятся отверстия, диаметр которых несколько больше, чем диаметр стержня заклепки. Заклепка вставляется в отверстия в деталях, и ее свободный конец расклепывается обжимками клепального молотка или машины, длина стержня заклепки L выбирается так, чтобы выступающая из детали часть была достаточной для придания ей в процессе расклепки необходимой формы.
В зависимости от диаметра заклепки она расклепывается в холодном или предварительно нагретом состоянии.
Заклепки со сплошным стержнем в продольном разрезе изображаются нерассеченными (рисунок 15, б и в). Заклепочные швы выполняются внахлестку (рисунок 15, б) или встык с накладками (рисунок 15, в).
По расположению заклепок в соединениях различают однорядные (рисунок 15, б) и многорядные (рисунок 15, в) заклепочные швы. Расположение заклепок в рядах может быть шахматное и параллельное.
32
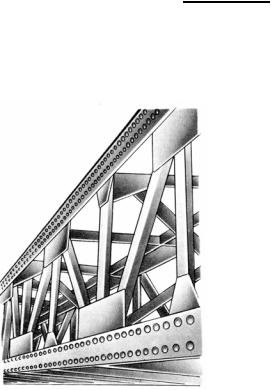
Шагом размещения заклепок t называется расстояние между осями двух соседних заклепок, измеренное параллельно кромке шва (рисунок 15, в).
В серийном и массовом производстве применяется механическая клепка, осуществляемая пневматическими молотками, клепальными машинами и прессами.
Материал заклепок зависит от материалов соединяемых деталей. При соединении деталей из цветных металлов и их сплавов применяют заклепки из цветных сплавов, например, латуни Л63, магниевого литейного сплава Мл3,
алюминиевого сплава АД1. Во избежание образования гальванических пар иногда такие заклепки покрывают антикоррозийным покрытием.
Детали из сталей соединяют стальными заклепками соответствующих марок. Стали, как правило, выбирают малоуглеродистые, обладающие высокой пластичностью, например, Ст.2, Ст.3.
4.2.1.2.1.2 Назначение и классификация заклепочных соединений
Заклепочные соединения применяются в конструкциях, работающих под действием ударных и вибрационных нагрузок. Например, при изготовлении металлоконструкций мостов кроме сварного соединения в некоторых случаях применяют заклепочное соединение (рисунок 16).
Рисунок 16
33
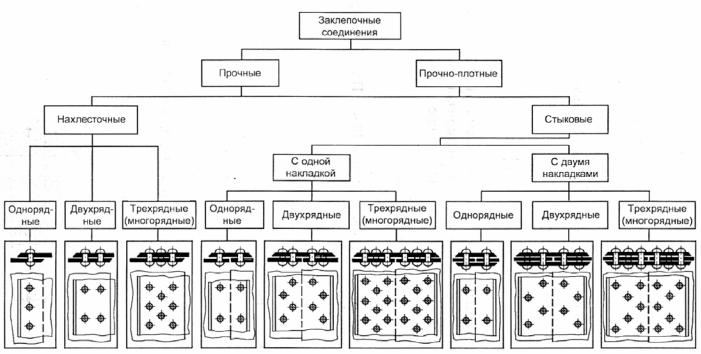
Виды заклепочных соединений представлены на рисунке 17.
Рисунок 17 – Классификация заклепочных соединений
По назначению заклепочные соединения разделяют на прочные (для восприятия внешних нагрузок) и прочноплотные, обеспечивающие также герметичность соединения.
Различают нахлесточные заклепочные соединения, соединения с одной и двумя накладками. Используются однорядные, двухрядные и многорядные соединения. Заклепки могут устанавливаться в шахматном порядке для увеличения прочности и облегчения установки заклепок. Увеличение рядов больше трех незначительно повышает прочность, поэтому многорядные швы применяют редко.
Достоинства заклепочных соединений:
–хорошо работают в конструкциях, подверженных вибрациям и повторным динамическим нагрузкам, где сварные соединения недостаточно надежны;
–применяют для соединения материалов, не поддающихся сварке или трудносвариваемых, недопускающих нагрев при сварке, коробящихся или меняющих механические характеристики.
Недостатки заклепочных соединений:
–повышенная металлоемкость;
34
–трудоемкость изготовления;
–невысокая технологичность.
Высокая металлоемкость связана с ослаблением сечения листов отверстиями, необходимостью увеличить толщину листов и с большим весом заклепок, составляющим до 5 % веса конструкции.
Трудоемкость связана с большим числом подготовительных операций, а процесс клепки сложнее сварки.
4.2.1.2.2 Сварные соединения
4.2.1.2.2.1 Основные способы сварки
Сварное соединение — неразъемное. Оно образуется путем сваривания материалов деталей в зоне стыка и не требует никаких вспомогательных элементов (болтов, винтов и т.д.). Прочность соединения зависит от неоднородности и непрерывности материала сварного шва и окружающей его зоны.
Сваркой называют процесс образования неразъемных соединений за счет создания атомно-молекулярных связей между элементарными частицами сопрягаемых деталей.
Впоследнее время разработаны технологии сварки металлов и их сплавов в однородных и разнородных сочетаниях, а также неметаллических материалов между собой и с металлами.
Применяемые в современном машиностроении способы сварки весьма разнообразны. Каждый из них имеет свои конкретные области применения.
Взависимости от метода получения соединений сварку делят на сварку плавлением и сварку давлением.
При сварке плавлением детали соединяют с помощью местного расплавления элементов соединяемых частей. Расплавляется только основной металл изделия по кромкам или основной и дополнительный металл (электрод и присадочный материал).
Сварку плавлением различают электрическую и газовую. Чаще
применяется электросварка плавлением.
35
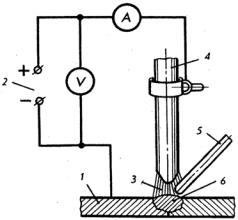
Наиболее широко распространена электрическая сварка плавлением.
При сварке давлением поверхности соединяемых деталей претерпевают совместную упруго-пластическую деформацию, поверхности выравниваются, разрушается поверхностный слой. Атомы поверхностей сближаются на расстояние активного взаимодействия, и образуется металлическая связь. Применяется предварительный нагрев поверхностей до пластического состояния.
Различают два основных вида электросварки: дуговую и контактную. Электродуговая сварка основана на использовании тепла
электрической дуги для расплавления металла.
При дуговой сварке (рисунок 18) в качестве источника энергии 2 используется электрический дуговой разряд 3, возникающий при контакте свариваемых деталей 1 к одному, а электрода 4 — к другому полюсу источника тока.
Рисунок 18
Движение электрода с дуговым разрядом и подведенным в его зону присадочным материалом (в виде прутка) 5 относительно кромок изделия заставляет перемещаться сварочную ванну, образующую сварной шов 6.
Для защиты расплавленного металла от вредного действия окружающего воздуха на поверхность электрода наносят толстую защитную обмазку, которая выделяет большое количество шлака и газа, образуя изолирующую среду. Этим обеспечивают повышение качества металла сварного шва, механические свойства которого могут резко ухудшиться под влиянием кислорода и азота воздуха.
36
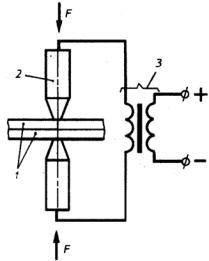
На производстве широко применяются полуавтоматическая дуговая сварка, сварка в среде защитного газа.
Контактная сварка относится к сварке с применением нагрева и давления и основана на использовании повышенного омического сопротивления в стыке деталей и осуществляется несколькими способами. Нагрев осуществляется электрическим током, который проходит через место контакта двух свариваемых деталей. Основное количество тепла выделяется в месте стыка, где имеется наибольшее сопротивление. Металл в этой зоне разогревается до пластического состояния или даже до поверхностного оплавления. Давление, необходимое для сварки, создается или электродами, подводящими электрический ток, или специальными приспособлениями.
Затем ток выключают, а разогретые детали сдавливают с некоторой силой
—происходит сварка.
Взависимости от способа сдавливания деталей различают три разновидности контактной сварки: точечную, стыковую, ленточную
или роликовую.
Точечная сварка осуществляется отдельными точками (рисунок 19), применяемую для тонколистовых конструкций из стали (кузова автомашин, железнодорожных вагонов, тонкостенных резервуаров и т.п.).
Рисунок 19
Свариваемые заготовки 1 зажимаются между электродами 2, через которые проходит электрический ток большой силы от вторичной обмотки понижающего
37
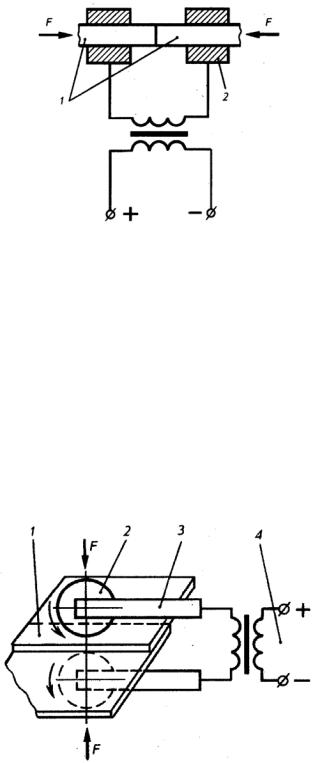
трансформатора 3. Место контакта свариваемых частей разогревается до высокой температуры и под давлением усилия F происходит сварка.
Стыковая сварка происходит оплавлением или давлением
(рисунок 20).
Рисунок 20
Она применяется для изготовления металлорежущего инструмента и др. В
этом случае свариваемые детали 1 с силой F стыкуются и удерживаются зажимами 2, к которым подводится электрический ток.
Роликовая сварка по принципу аналогична точечной сварке, только вместо точечных электродов применяют электроды с роликами (рисунок 21), где 1 — свариваемые детали, 2 — ролики, 3 — электроды, 4 — источник электроэнергии.
Рисунок 21
Роликовая сварка обеспечивает непрерывный (герметичный) или прерывистый шов.
38
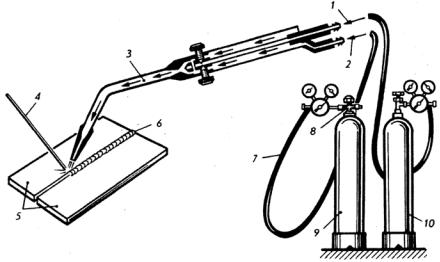
Все способы контактной сварки высокопроизводительны, их широко применяют в массовом производстве для сварки труб, арматуры, кузовов автомобилей, металлической обшивки железнодорожных вагонов, корпусов самолетов, тонкостенных резервуаров и т.д.
Оценивая сварное соединение, необходимо подчеркнуть, что оно является наиболее совершенным из неразъемных соединений, так как лучше других приближает составные детали к цельным. При сварном соединении проще обеспечиваются условия равнопрочности, снижения массы и стоимости изделия.
При газовой или автогенной сварке в качестве энергии используют пламя ацетиленокислородной горелки (рисунок 22), имеющей высокую температуру (около 3 000°С) и значительную мощность, зависящую от количества ацетилена (8 — редуктор для регулирования величины подачи газа), сгорающего в секунду.
Кислород 1 из кислородного баллона 10 и ацетилен 2 из ацетиленового баллона 9 подаются по шлангам 7 в газовую горелку, где образуется горючая смесь 3. На выходе из сопла горелки возникает пламя.
Рисунок 22
Когда нагреваемое место свариваемых деталей доводится до расплавленного состояния, к пламени подводят присадочный материал 4, который, расплавляясь вместе с кромками детали 5, образуют сварочный шов 6.
39
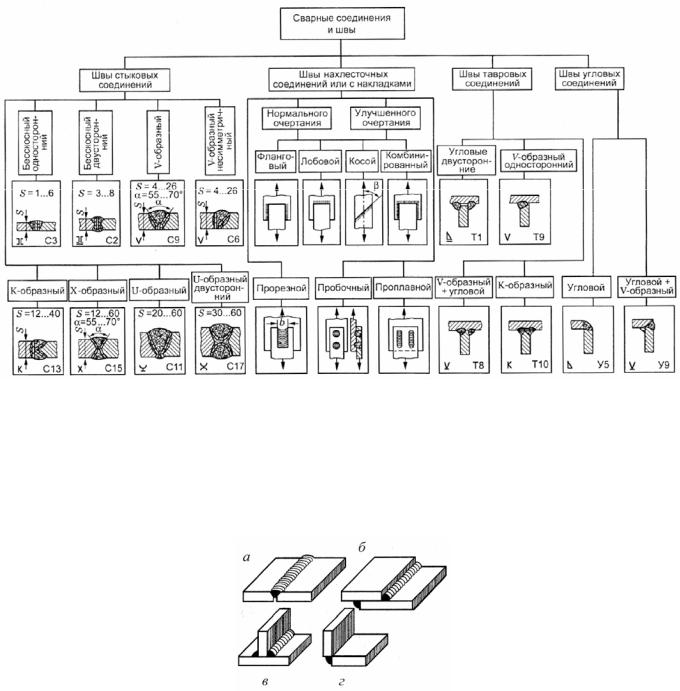
4.2.1.2.2.2 Виды конструктивных соединений деталей сваркой и классификация сварочных швов
Классификация сварных соединений и швов представлена на рисунке 23.
Рисунок 23 – Классификация сварных соединений и швов
Различают следующие виды конструктивных соединений деталей сваркой
(рисунок 24): стыковое (С3), внахлестку (Н1), тавровое (Т1), угловое
(У4).
Рисунок 24
Сварные соединения, изображенные на рисунке 24, выполняют электродуговой и газовой сваркой.
Различают следующие виды сварных швов: стыковой, точечный,
угловой, с проплавленными швами.
40