
МУ по выполнению ПЗ № 2 ОП
.pdf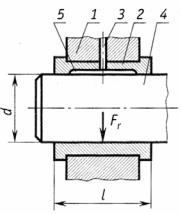
транспортных машинах (лебедки), в неответственных вспомогательных механизмах (механизмы управления) вместо подшипников качения, когда последние не удается встроить в корпус вследствие относительно больших наружных диаметров, и в других случаях.
В ходе практического занятия будут рассмотрены конструкции простейших подшипников скольжения, работающих в режиме полужидкостной смазки.
Подшипник скольжения (рисунок 121) состоит из корпуса 1, вкладыша 2, смазывающего устройства и уплотнений. Обычно корпус 1 подшипника является отдельной деталью, на которую опирается цапфа вала 4. Смазочный материал поступает к рабочей поверхности подшипника из канала 3 через смазочные канавки 5.
Рисунок 121 – Подшипник скольжения:
1 — корпус подшипника; 2 — вкладыш; 3 — смазочный канал; 4 — цапфа вала; 5 — смазочная канавка
Поверхность скольжения образуют цапфа вала и вкладыш. Основным элементом подшипника скольжения является вкладыш. Вкладыши подшипников скольжения устанавливают в отверстия стенок
корпусной детали (рисунок 122, а), в отверстие свободно вращающегося зубчатого колеса (рисунок 122, б), в отверстие сцепной полумуфты, свободно сидящей на валу (рисунок 122, в) и др.
121
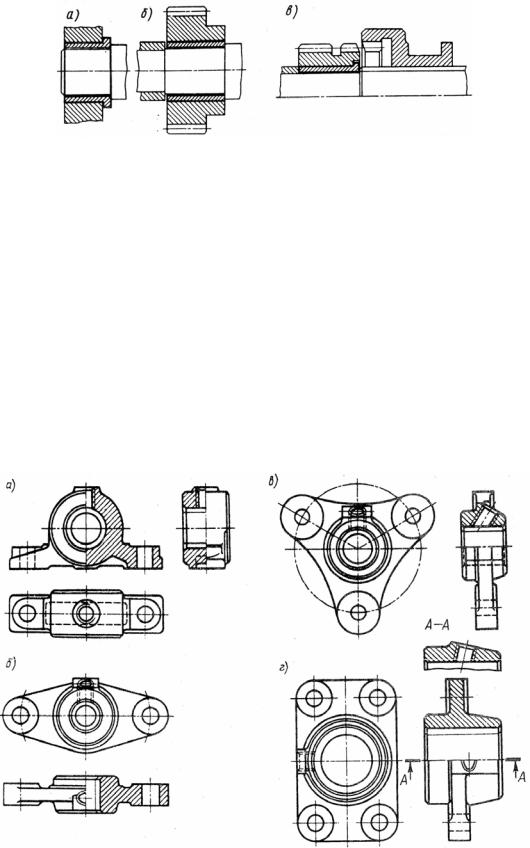
Рисунок 122
4.2.3.3.1.1 Классификация подшипников скольжения
По конструкции корпуса подшипники скольжения подразделяют на
неразъемные |
(ГОСТ |
11521-82...11525-82) |
и |
разъемные |
(ГОСТ 11607-82, ГОСТ 11611-82). |
|
|
|
На рисунке 123 показаны конструкции неразъемных корпусов. Опорная плоскость корпусов подшипников по рисунку 123, а параллельна, а по рисунку 123, б, в, г перпендикулярна оси основного отверстия. Это позволяет устанавливать их и на горизонтальных и на вертикальных стенках узлов.
Рисунок 123
Неразъемные корпуса просты в изготовлении. Их применяют для валов или осей небольшого диаметра, вращающихся с относительно малой
угловой скоростью, но при сравнительно малых давлениях на подшипник. Когда
122
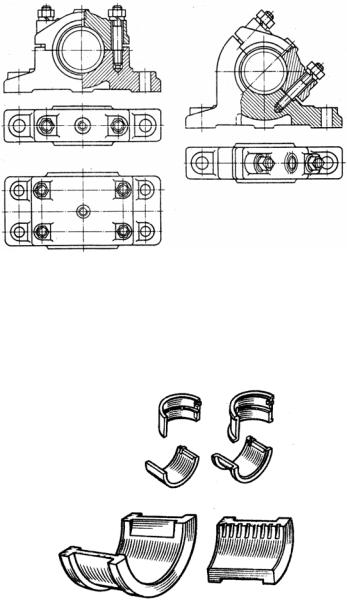
подшипник изнашивается и между цапфой и подшипником появляется зазор, в корпус подшипника перезапрессовывают втулку по размерам цапф.
Однако сборка узла при неразъемном корпусе не всегда удобна, а иногда и невозможна.
Разъемные корпуса облегчают монтаж валов и допускают регулирование зазоров в подшипнике. Поэтому они имеют преимущественное применение в общем и особенно тяжелом машиностроении. Крышку крепят к корпусу шпильками (рисунок 124).
Рисунок 124
При разъемных корпусах применяют два вкладыша. Конструкция вкладыша разъемного подшипника скольжения приведена на рисунке 125.
Рисунок 125 – Конструкция вкладыша разъемного подшипника скольжения
123
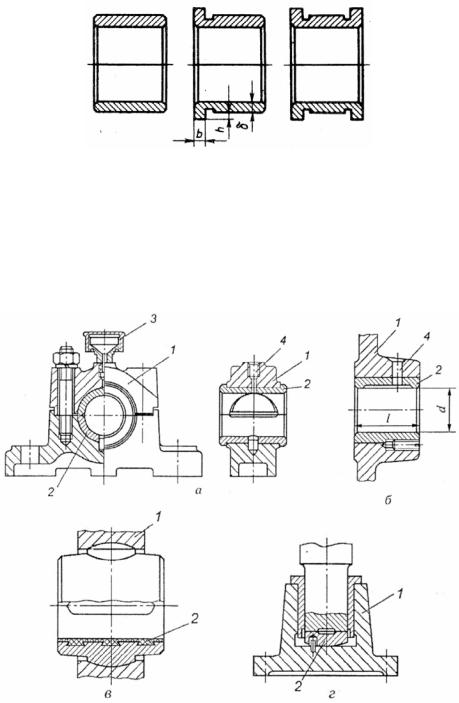
Вкладыши разъемного подшипника выполняют без буртов, с одним или двумя буртами (рисунок 126)
Рисунок 126
Разъемные подшипники облегчают монтаж валов и допускают регулировку зазоров посредством сближения крышки и корпуса.
Основные типы подшипников скольжения приведены на рисунке 127.
Рисунок 127 – Типы подшипников скольжения: а–в — радиальные; г — упорный;
1 — корпус; 2 — вкладыш; 3 — смазывающее устройство; 4 — отверстие для подвода смазывающего материала
По направлению воспринимаемых нагрузок подшипники скольжения разделяют на радиальные, воспринимающие нагрузки, перпендикулярные оси вала (рисунок 127, а–в), упорные — для восприятия нагрузок вдоль оси вала
124
(подпятник) (рисунок 127, г) и радиальноупорные, воспринимающие радиальные и осевые нагрузки.
Опоры скольжения для осевых нагрузок — подпятники (рисунок 127, г) бывают различных конструкций.
4.2.3.3.1.2 Вкладыши подшипников скольжения
Материалы вкладышей должны иметь низкий коэффициент трения, высокую теплопроводность, достаточную износостойкость и сопротивляемость заеданию, высокую сопротивляемость хрупкому и усталостному разрушениям.
Вкладыши подшипников скольжения изготовляют из стали, антифрикционного чугуна, бронзы, пластмасс и других материалов.
Вкрупносерийном производстве используют биметаллические вкладыши.
Вэтих вкладышах тонкий антифрикционный слой наплавлен на стальную, чугунную, а в ответственных подшипниках — на бронзовую основу. В качестве антифрикционных материалов применяют: оловянные и свинцовые бронзы, баббиты, а также неметаллические материалы (нейлон, фторопласт, текстолитовая крошка).
Чтобы уменьшить трение, рабочую поверхность стального, чугунного или бронзового вкладыша обычно заливают тонким слоем антифрикционного сплава баббита Б83 или Б89 и растачивают по размеру цапф.
Вмассовом производстве широко распространены вкладыши, штампуемые из биметаллической ленты.
Вединичном и мелкосерийном производстве чаще всего применяют более простые в изготовлении вкладыши из недорогих антифрикционных материалов: антифрикционного чугуна, текстолита, прессованной древесины и безоловянных бронз.
Чугунные вкладыши без заливки используют в малоответственных механизмах. В тихоходных механизмах применяют также металлокерамические вкладыши из порошков железа или меди с добавлением графита, свинца или олова. Кроме того, вкладыши изготавливают из пластмассы, древесины, резины и других материалов.
125

Из пластмассовых вкладышей наибольшее распространение получили вкладыши из текстолита и древесно-слоистых пластиков. Они применяются в прокатных станах, гидравлических и других машинах.
4.2.3.3.1.3 Смазка подшипников скольжения
Для того чтобы уменьшить трение в подшипниках осуществляют их смазку с помощью смазывающих устройств. Смазывание исключительно важно для работы подшипника.
Для смазывания используют жидкий или пластичный смазочный материал, который подают в разгруженную зону.
Основными смазывающими материалами являются жидкие масла (органические и минеральные), так как они имеют сравнительно низкий коэффициент трения, оказывают охлаждающее действие и их легко подавать к местам смазки.
Смазочный материал может подводиться в подшипник принудительно (разбрызгиванием и под давлением), самотеком и с помощью специальных приспособлений.
Наиболее совершенным способом смазки подшипников скольжения является кольцевая смазка. Она осуществляется кольцом, свободно висящим на цапфе 1, нижняя часть которого находится в масляной ванне (рисунок 128). Кольцо 2, вращаясь вместе с цапфой вала, захватывает масло из ванны, которое затем стекает на цапфу.
Рисунок 128 – Кольцевая смазка подшипника: 1 — цапфа вала; 2 — кольцо
126
В современном машиностроении широкое применением находит применение циркуляционная система смазки.
Достоинства подшипников скольжения:
–высокая надежность при переменных и динамических нагрузках;
–нормальная работа при высоких скоростях вращения;
–бесшумная работа;
–сравнительно малые радиальные размеры;
–разъемные подшипники облегчают монтаж, допускают установку на шейки коленчатых (непрямых) валов.
Недостатки подшипников скольжения:
–высокие требования к наличию смазочного материала, большой расход смазочного материала;
–сравнительно большие осевые размеры;
–значительные потери на трение, низкий КПД.
4.2.3.3.2 Подшипники качения
Подшипник качения (рисунок 129) состоит из тел качения 2 (шарики или ролики), наружного кольца 5, внутреннего кольца 4 и сепаратора 3 (деталь, удерживающая тела качения на определенном расстоянии одно от другого). Сепаратор изготовлен из двух деталей, соединенных заклепками 1. Кольца имеют дорожку, по которой перекатываются тела качения 2.
При установке подшипника его внутреннее кольцо 4 монтируют на валу, а наружное кольцо 5 устанавливают в корпусе. Нагрузка, воспринимаемая цапфой или корпусом, передается через тела вращения от цапфы к корпусу или, наоборот, от корпуса к цапфе.
Подшипники качения являются основным видом опор в машинах и широко применяются в различных областях машиностроения.
127
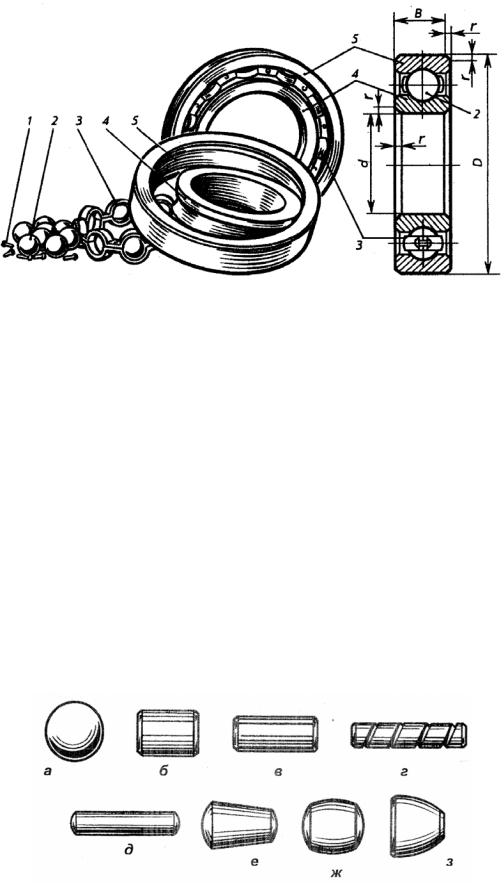
Рисунок 129 – Конструкция подшипника качения:
1 — заклепки сепаратора; 2 — тела вращения (шарики); 3 — сепаратор; 4 — внутреннее кольцо; 5 — наружное кольцо
4.2.3.3.2.1 Классификация и изображение подшипников качения
Подшипники качения классифицируют по форме тел качения
(шариковые и роликовые); по числу рядов тел качения (однорядные и двухрядные); по направлению воспринимаемой нагрузки (радиальные,
радиальноупорные, упорнорадиальные, упорные); по конструктивным особенностям (с канавками на наружном кольце, с
одной или двумя защитными шайбами и другими особенностями).
Типы форм тел качения представлены на рисунке 130.
Рисунок 130 – Типы форм тел качения подшипников:
а— шариковая; б — роликовая цилиндрическая короткая; в — роликовая цилиндрическая длинная; г — роликовая цилиндрическая витая;
д— игольчатая; е — коническая; ж, з — бочкообразные
128
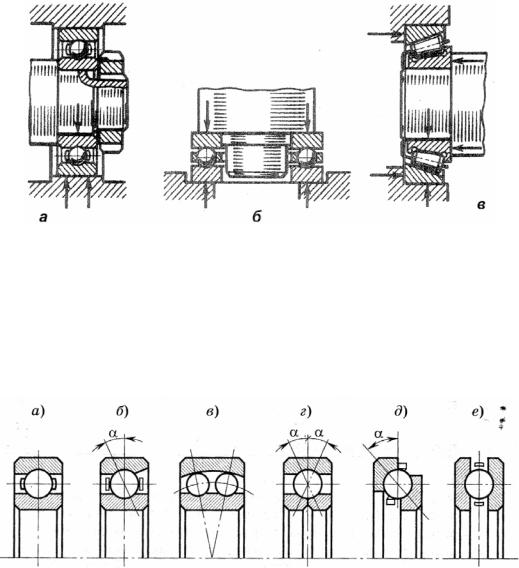
Варианты конструкций подшипников качения по направлению воспринимаемой нагрузки:
–радиальные, воспринимающие только радиальные нагрузки, направленные перпендикулярно к геометрической оси вала
(рисунок 131, а);
–радиальноупорные, служащие для восприятия радиальной и осевой нагрузки (рисунок 131, б);
–упорные, несущие нагрузку вдоль оси вращения (рисунок 131, в).
Рисунок 131 – Конструкции подшипников качения в зависимости от воспринимаемой нагрузки:
1 — радиальный; 2 — упорный; 3 — радиально-упорный
Конструкции шариковых подшипников представлены на рисунке 132, роликовых — на рисунке 133.
Рисунок 132 – Шарикоподшипники:
а — радиальный; б — радиально-упорный; в — радиальный двухрядный сферический; г — радиально-упорный однорядный; д — упорно-радиальный; е — упорный
129
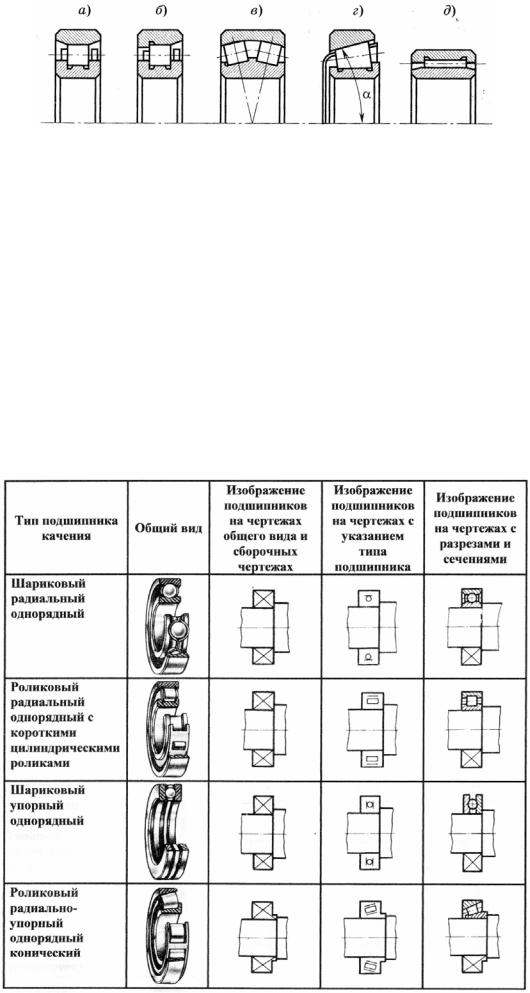
Рисунок 133 – Роликоподшипники:
а, б — радиальные с короткими цилиндрическими роликами; в — радиальный сферический двухрядный; г — радиально-упорный однорядный конический; д — игольчатый
На чертежах общих видов и сборочных чертежах подшипники качения в осевых разрезах изображаются, как правило, упрощенно по ГОСТ 2.420-69 без указания типа и особенностей конструкции. Контурное очертание подшипника здесь выполняется сплошными основными линиями по его контуру, внутри которого проводятся сплошными тонкими линиями диагонали (таблица 3).
Таблица 3 – Изображение подшипников качения на чертежах общего вида и сборочных чертежах
130