
zaharov
.pdf3.4. Контроль и испытания гидравлического оборудования |
163 |
пустимое давление на выходе из насоса; Pвху – абсолютное деление на входе в насос при ускоренных испытаниях; Pвх.б.к – абсолютное давление на входе в насос, обеспечивающее беcкавитационную работу насоса; tру.ж – температура рабочей жидкости при ускоренных испытаниях; tр.ж.пр – предельная температура рабочей жидкости.
Пределы увеличения Pн.пр устанавливают из условия бескавитаци-
онной работы насоса, прижима башмаков к плоскости наклонной шайбы и блока цилиндров к распределительному золотнику, значение давления Pвх.б.к из условия бескавитационно й работы насоса.
Максимальные температуры рабочей жидкости и окружающей среды устанавливают из условия максимально допустимой температуры для резиновых уплотнений и рабочей жидкости.
Методика анализа технического состояния насоса предусматривает разбиение конструкции на функциональные узлы, состояние деталей которых при испытаниях изменяется под воздействием основных физических процессов. Узлы, детали и основные процессы показаны на рис. 3.39.
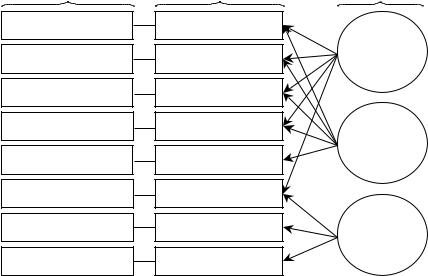
164 |
Глава 3. ГИДРАВЛИЧЕСКИЕ ПРИВОДЫ СИСТЕМ УПРАВЛЕНИЯ |
Функциональные |
Конструктивные |
Физические |
узлы |
элементы |
процессы |
Качающий узел |
Наклонная шайба |
|
Блок цилиндров |
|
|
|
|
|
|
|
Изнашивание |
Узел распределения |
Золотник распределения |
поверхностей |
|
Клапаны, пружины |
|
Узел регулятора подачи |
Сервопоршень, гильза, |
|
золотник, пружины |
|
|
|
|
|
Подшипники |
Подшипники |
Накопление |
|
|
|
|
|
усталостных |
Силовые элементы |
Корпус, крышка, вал, |
повреждений |
крепежные детали |
|
|
|
|
|
Уплотнения |
Торцевые, манжетные |
|
подвижных элементов |
|
|
Уплотнения |
Резиновые кольца |
Старение |
неподвижных элементов |
|
|
|
материалов |
|
|
|
|
Электромагниты |
Изоляция обмоток |
|
|
|
Рис. 3.39. Структурная схема испытаний элементов аксиально-поршневых насосов
При определении режимов ускоренных испытаний учитывают данные, полученные при расчетах, при испытаниях, в эксплуатации и при сравнительных испытаниях (рис. 3.40, 3.41).
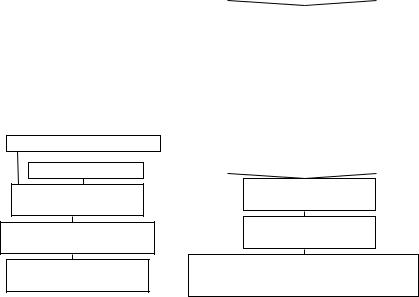
3.4. Контроль и испытания гидравлического оборудования |
165 |
|||||||||||||||
|
|
Расчетный метод |
Метод сравнения с результатами испытаний прототипа |
|||||||||||||
|
|
|
|
|
|
|
|
|
|
|
|
|
|
|
|
|
|
|
Расчет режимов ускоренных |
|
|
Анализ результатов |
|
|
|
Анализ результатов |
|
||||||
|
|
испытаний |
|
|
нормальных испытаний |
|
|
|
ускоренных испытаний |
|
||||||
|
|
|
|
|
|
насосов |
|
|
|
насосов |
|
|||||
|
|
|
|
|
|
|
|
|
|
|
|
|
|
|
|
|
|
|
|
|
|
|
|
|
|
|
|
|
|
|
|
|
|
|
|
Разработка программы |
|
|
|
|
Сравнение и оценка |
|
|
|
|
|||||
|
|
ускоренных испытаний |
|
|
|
|
результатов испытаний |
|
|
|
|
|||||
|
|
|
|
|
|
|
|
|
|
|
|
|
|
|
||
|
|
|
|
|
|
|
|
|
|
|
|
|
|
|
||
|
|
Принятие решения о |
|
|
Принятие решения о распространении программы |
|
|
|||||||||
|
|
внедрении ускоренных |
|
|
ускоренных испытаний прототипа на типовые насосы |
|
|
|||||||||
|
|
испытаний |
|
|
|
|
|
|
|
|
|
|
|
|
|
|
|
|
|
|
|
|
|
|
|
|
|
|
|
|
|
||
|
|
Внедрение программы в |
|
|
|
Внедрение в производство |
|
|
||||||||
|
|
производство без дополнительных |
|
|
|
программы ускоренных |
|
|
||||||||
|
|
испытаний |
|
|
|
|
испытаний |
|
|
|||||||
|
|
|
|
|
|
|
|
|
|
|
|
|
|
|
|
|
Метод сравнения с результатами эксплуатации
Результаты ускоренных испытаний
Результаты эксплуатации
Сравнение и оценка результатов
Принятие решения о внедрении программы ускоренных испытаний в производство
Внедрение в производство программы ускоренных испытаний
Результаты нормальных |
|
Результаты эксплуатации |
испытаний |
|
|
|
|
|
Сравнение и оценка результатов
Определение коэффициента ускорения
Принятие решения об использовании программы нормальных испытаний в качестве программы ускоренных испытаний на увеличенный ресурс
Рис. 3.40. Методы сравнения с результатами испытаний и эксплуатации
При этом техническое состояние насосов оценивают: по функциональным параметрам и характеристикам, заданным в нормативнотехнической документации (ТУ, ТЗ и др.): по структурным параметрам деталей и узлов и по состоянию поверхностей; по измеряемым величинам зазоров и люфтов; по величине износа в парах скольжения; по изменению характеристик пружин, по результатам неразрушающего или разрушающего контроля деталей, подверженных процессам усталостного разрушения.
При ускоренных испытаниях должно быть достигнуто состояние деталей и узлов насоса:
по условиям изнашивания поверхностей hу hн , где hу иhн – линейный износ.
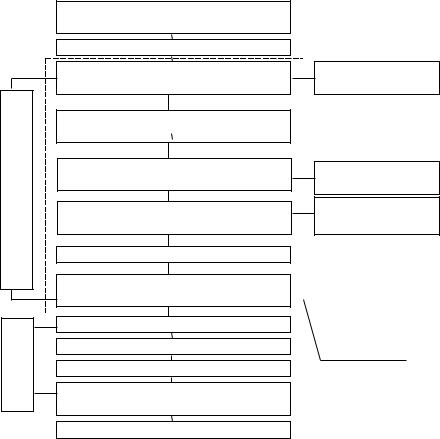
166 |
Глава 3. ГИДРАВЛИЧЕСКИЕ ПРИВОДЫ СИСТЕМ УПРАВЛЕНИЯ |
Уточнение программы Уточнение режимов ускоренных испытаний
Анализ исходных данных по ТЗ, ТУ, по программам испытаний, по данным эксплуатации изделия
Оценка режимов нагружения
Выбор режимов ускоренных испытаний по элементам и узлам
Расчет длительности ускоренных испытаний по нагрузкам деталей и узлов
Ограничения по условиям работоспособности насоса
Оценка режимов ускоренных испытаний по нагрузкам деталей и узлов
Выбор общей длительности ускоренных испытаний, уточнение длительностей для элементов
Расчет коэффициентов несоответствия для элементов
Оценка режимов ускоренных испытаний по коэффициентам несоответствия
Разработка программы ускоренных испытаний
Сравнительные испытания
Оценка результатов испытаний
Принятие решения о внедрении программы ускоренных испытаний
Внедрение программы ускоренных испытаний
Ограничения по предельным нагрузкам
Ограничения по общей длительности
испытаний
Первое расчетное приближение
Рис. 3.41. Метод проведения сравнительных испытаний
Индексы «у» и «н» здесь и далее означают, что параметры соответствуют режимам ускоренных и нормальных испытаний:
по условиям накоплений усталостных повреждений
|
|
н m |
N у N н |
, |
|
|
|
у |
|
|
где N н , N у – число циклов нагружения; н , у – напряжение в материале деталей; m – показатель степени уравнения кривой усталости;
3.4. Контроль и испытания гидравлического оборудования |
167 |
по старению материалов (изоляция электромагнитов)
mу mн ,
где mу и mн – масса состарившегося материала;по накоплению остаточных деформаций
у н ,
где у и н – величина относительной остаточной деформации;
Rу Rн ,
где Rу и Rн – усилия пружин.
Принятые допущения: процесс старения уплотнений до температуры 50 °С и влияние температуры до 200 °С на усталостную прочность стальных деталей незначительны и не учитываются, за температуру рабочей жидкости принимается температура жидкости на входе в насос.
Определение режимов ускоренных испытаний производят для функциональных узлов с учетом приведенных выше материалов и ГОСТ 20734-75, ГОСТ 18855-73, ОСТ 1 00128-74, ОСТ 1 00389-80.
Для сокращения времени испытаний следует увеличивать: давление нагнетания и частоту вращении вала, температуру рабочей жидкости и окружающей среды, давление в корпусе насоса, частоту срабатывания регулятора подачи, максимальную подачу.
Для выбранных режимом ускоренных испытаний рассчитывают возникающие при работе насоса нагрузки, напряжения, остаточные деформации и температуры в основных элементах конструкций.
Расчетные значения величин не должны превышать допустимых:
у |
доп |
, |
у |
|
пр доп |
; |
Pу P |
; |
у |
доп |
, |
|
|
|
пр |
|
|
к |
к доп |
|
|
|
|||
где доп , пр доп ; Pк доп |
– предельные |
допустимые |
значения нормаль- |
ных, касательных и контактных напряжений при выбранных режимах ускоренных испытаний; доп – предельное допустимое значение отно-
сительной остаточной деформации резиновых уплотнений.
Анализ результатов определения режимов испытаний. По ре-
зультатам расчета режимов ускоренных испытаний анализируют полу-

168 |
Глава 3. ГИДРАВЛИЧЕСКИЕ ПРИВОДЫ СИСТЕМ УПРАВЛЕНИЯ |
ченные значения длительностей испытаний для отдельных функциональных узлов и деталей, состояние которых изменяется при воздействии совокупности физических процессов. Анализ осуществляется с целью выбора таких значений режимов нагружения, которым будет соответствовать приемлемое общее время ускоренных испытаний (по изменению состояния функциональных узлов и деталей).
Общая длительность испытаний должна быть не менее длительности испытаний (Тi), необходимой для элементов с наименьшей долговечностью. Эти элементы рассматриваются как определяющие. По другим элементам допускается переработка без потери работоспособности насоса.
При выборе общего времени испытания (Tобщ ) должно быть обеспечено условие
Tобщ Ti .
Степень несоответствия для этого условия, связанную со статистическим разбросом параметров состояния деталей и узлов и неточностью расчетов, оценивают для состояния деталей и узлов величиной
Ki TобщTi .
Tобщ
Степень несоответствия, полученная расчетным путем или путем сравнения расчетных и замеренных величин для параметров состояния определяющих элементов, не должна превышать заданной величины.
Одним из возможных путей дальнейшего совершенствования контроля состояния гидроагрегатов является их установка на самолетах, которые проходят прочностные статические и повторно-статические испытания в лабораторных прочностных комплексах. В таких стендах вся гидросистема и ее части скомпонованы в летном варианте на ЛА и поэтому не требуется создавать специальный стенд и моделировать компоновку системы. Так, при ресурсных испытаниях самолета и его механической системы обязательными элементами в стендах являются штатные электрогидравлические агрегаты; рулевой привод (РП) и рулевой агрегат (РА). В этом случае целесообразно совместить испытания механической и гидравлической частей электродистанционного контура управления и проводить их по следующей методике.
Сигнал на перемещение проводки управления подается с помощью генератора в виде синусоидального изменения напряжения. Сигнал
3.4. Контроль и испытания гидравлического оборудования |
169 |
подается на вход системы дистанционного управления (СДУ) соответствующей рулевой поверхности самолета. СДУ состоит из блока управления и контроля (БУК) и РА. БУК в соответствии с сигналами генератора формирует и выдает сигнал на РА, который является исполнительным механизмом СДУ и предназначен для перемещения механической проводки управления золотником РП. Амплитуда перемещений РА контролируется по указателям перемещения на конструкции, по входному сигналу генератора и по сигналу датчика обратной связи (ДОС) РА. Наработка контролируется по счетчику циклов или по сигналам ДОС.
Нагрузка на рулевые поверхности создается механической системой нагружения, имитирующей полетную. Рулевой привод и рулевой агрегат подключаются к централизованной насосной станции.
Далее все технологические операции выполняются в соответствии с ТУ на конкретные РА и РП.
Для самолета ТУ-204, который проходит прочностные испытания, наработка РА 86 и РП 95 без отклонений от ТУ составила на первом этапе испытаний в циклах: руль высоты – 7 105; руль направления – 1,1 106; элерон – 4,6 106 и интерцепторы и воздушные тормоза – 7. 106.
Контроль показателей долговечности и безотказности агрегатов в процессе серийного производства. В процессе серий-
ного производства контролируют качество изготовления гидроагрегатов. При этом проводятся следующие виды испытаний: приемосдаточные испытания (ПСИ) каждого изготовляемого агрегата, периодические, специальные.
Приемосдаточные испытания проводят по регламентируемой программе в течение фиксированной длительности Ти испытаний партии агрегатов. При испытаниях определяется число агрегатов r, не прошедших испытания, и прошедших испытания N – r. По результатам испытаний определяется вероятность РПСИ успешного завершения ПСИ для партии агрегатов при заданной достоверности β.
Периодические испытания серийно выпускаемых агрегатов проводятся по специальным регламентированным программам. Результаты испытаний считаются успешными при нуле отказов. Периодические ресурсные испытания рекомендуется проводить по программам ускоренных испытаний на форсированных режимах.
Обычно периодическим ресурсным испытаниям подвергается один произвольно выбранный агрегат из числа серийных агрегатов данного
170 |
Глава 3. ГИДРАВЛИЧЕСКИЕ ПРИВОДЫ СИСТЕМ УПРАВЛЕНИЯ |
типа, выпущенных за определенный календарный период времени, например за квартал, или полугодие. По результатам периодических испытаний оценивают стабильность производственного процесса изготовления агрегатов данного тина.
Специальные испытания серийно выпускаемых агрегатов проводят в случае конструктивных доработок агрегатов по специально составленным программам.
Испытательные стенды. Стенд для испытания рукавов,
шлангов и трубопроводов. Стенд предназначен для испытания рукавов, шлангов и трубопроводов (далее – изделий) гидравлическим давлением (испытание на герметичность и запас прочности), для определения изменения длины испытываемого изделия при рабочем давлении и проведения динамических испытаний.
Технические данные стенда |
|
Рабочее тело ........................................................................... |
минеральные масла |
Давление рабочей жидкости, МПа: |
|
– от насосной станции..................................................................... |
20 |
– от ручного насоса ......................................................................... |
30 |
– на входе в мультипликатор.......................................................... |
15 |
– развиваемое мультипликатором................................................. |
150 |
Давление в сливной магистрали, МПа .......................................... |
не более 2 |
Отклонение давления от установленных значений, % ................ |
не более 3 |
Коэффициент усиления мультипликатора.......................................... |
10 |
Диапазон рабочих температур жидкости, °С .................................. |
20–93 |
Максимальная температура рабочей жидкости, °С .......................... |
100 |
Отклонения установившейся температуры жидкости, °С ................ |
±5 |
Частота изменения давления, циклы/мин ........................................ |
30–75 |
Напряжение питания стенда, В......................................................... |
220,27 |
Габаритные размеры, мм........................................................... |
2500 900 1700 |
Атмосферное давление и влажность окружающей среды не ограничиваются.
Стенд для испытания рукавов, шлангов и трубопроводов состоит из пульта, на передней панели которого находятся манометры для контроля давления, на боковой – вентили. В пульте расположены: ванна
3.4. Контроль и испытания гидравлического оборудования |
171 |
с защитным кожухом, гидравлический мультипликатор – для создания управления давления рабочей жидкости; гидравлический редукционный клапан – для подачи к проверяемому трубопроводу или шлангу требуемого давления рабочей жидкости; обратные клапаны – для обеспечения потока рабочей жидкости в одном направлении; дроссели – для создания более плавного подвода и отвода давления рабочей жидкости; фильтр – для очистки рабочей жидкости с тонкостью очистки 12...16 мкм; система нагрева жидкости; автомат импульсной системы (АИС).
На боковой панели расположены штуцера подвода рабочей жидкости к проверяемому изделию.
Для испытаний изделий на стенде, в зависимости от вида испытаний и типа изделий, предусмотрено три режима испытаний.
Для первого режима используется следующее оборудование (рис. 3.42): запорный вентиль 1, фильтр 25, редукционный клапан 4, гидрораспределитель 26, дроссельные вентили 8 и 9. Жидкость поступает через фильтр 25 к редукционному клапану 4, которым задается рабочее давление, поступающее через распределитель 26 и вентили 8 и 9 к испытываемому рукаву, шлангу или трубке 27. Замер давления осуществляется манометрами 5 и 36.
Для второго режима применяется оборудование: ручной насос 28, фильтр 29, обратный клапан 30 и вентили 12 и 13. Жидкость из расходного бака 31 поступает в насос 28 и подается через фильтр 29 к испытываемому изделию 32. Замер давления осуществляется манометром 15.
Для третьего режима и динамических испытаний используется следующее оборудование: фильтр 25, редукционный клапан 4, гидрораспределитель 26, мультипликатор 33, насос 41, подпитывающий бак 34 с нагревателями и системой автоматического поддержания заданной температуры жидкости, автомат импульсной системы.
В третьем режиме, как и в первом, жидкость поступает от МНС (маслонасосная станция) на гидрораспределитель 26, который поочередно подает жидкость в полости мультипликатора: «зарядка» (полость А) – «поддавливание» (полость Б). Заданное по условиям испытания высокое и сверхвысокое давление в изделии создается рабочей жидкостью поступающей из полости Б мультипликатора. Рабочая жидкость, поступающая в полость В, может быть различной.
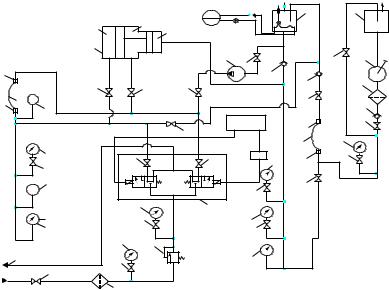
172 |
Глава 3. ГИДРАВЛИЧЕСКИЕ ПРИВОДЫ СИСТЕМ УПРАВЛЕНИЯ |
18 |
|
|
10 |
27 ТБ |
45 |
|
||
|
|
|
|
|
36 |
|
|
40 |
|
Р1 |
47 |
|
|
|
|
|
N |
|
|
46 |
МНС |
2 |
|
|
1 |
|
|
|
|
|
44 |
|
|
|
|
|
TR |
|
34 |
31 |
Б |
А |
|
|
|
|
|
3 |
|
|
|
|
|
|
|
|
|
|
33 |
|
|
|
|
13 |
|
|
41 |
42 |
|
|
|
|
35 |
28 |
||
|
|
|
|
|
|
|
|
|
|
37 |
|
6 |
7 |
43 |
|
|
29 |
|
|
|
|
17 |
|
|
|
|
|
|
30 |
|
11 |
|
АИС |
19 |
12 |
|
|
|
|
||
|
|
|
|
32 |
15 |
9 |
|
8 |
·РС |
28 |
14 |
|
|
21 |
|
||
|
|
|
|
|
|
|
|
|
20 |
16 |
|
|
|
|
|
|
5 |
26 |
|
39 |
22 |
|
23 |
||
|
||
3 |
4 |
|
|
||
|
24 |
38
25
Рис. 3.42. Схема стенда для испытания рукавов, шлангов и трубопроводов
При динамических испытаниях жидкость поступает от МНС на гидрораспределитель 26, который подает жидкость с заданной частотой и давлением в испытываемое изделие 27. Величина давления устанавливается на ЭКМ 46 и контролируется периодически датчиком давления 47 и манометром 36. Нагрев жидкости осуществляется в баке подпитки 34. Перед испытаниями жидкость насосом 41 прокачивается через изделие до тех пор, пока температура в нем не достигнет величины (93±5) °С. Контроль температуры производится термопарой с вторичным прибором 45. Термопара зачеканена в трубопровод на входе в изделие. При падении температуры на шланге необходимо вновь провести прокачку жидкости насосом 41.
Стенд для испытания электрогидравлических усилителей.
Стенд предназначен для испытания электрогидравлических усилителей (ЭГУ). Агрегат управления (например, АУ-38Б) при испытаниях подвергается проверке по следующим параметрам.
Зона чувствительности: