
- •ВВЕДЕНИЕ
- •1. СТРОЕНИЕ МЕТАЛЛОВ И СПЛАВОВ
- •Реальные кристаллы
- •Аморфные сплавы
- •Строение сплавов
- •2. ФАЗОВЫЕ ПРЕВРАЩЕНИЯ
- •Основные типы диаграмм
- •Системы с тремя компонентами
- •Основные структурные составляющие сплавов Fe – C
- •Диаграмма состояния Fe – Fe3C
- •Основные характеристики металлических материалов
- •Виды термической обработки материалов
- •Легирование
- •Поверхностное упрочнение (поверхностная закалка)
- •Железо и его сплавы
- •Стали
- •Чугуны
- •Твердые сплавы
- •Цветные металлы и сплавы
- •Алюминий и его сплавы
- •Медь и ее сплавы
- •Никель и его сплавы
- •Цинк и его сплавы
- •Магний и его сплавы
- •Титан и его сплавы
- •Припои
- •ЛИТЕРАТУРА
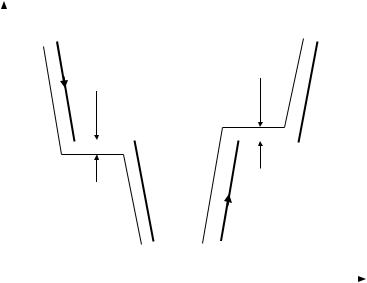
Износостойкость – сопротивление материала изнашиванию под действием физических и химических факторов (обычно испытывают трением). Количественно может оцениваться потерей массы материала на единицу трущейся поверхности в единицу времени: m / Sτ.
Виды термической обработки материалов
Температурно-временные зависимости t = f(Т) – называются кривыми охлаждения или нагрева сплава (рис. 36).
t, °C
1 1' |
|
|
2 2' |
|||
|
|
|
|
|
|
|
mn |
|
(mn)' |
||||
|
|
|
|
|
|
|
|
|
|
|
|
|
|
|
|
|
|
|
|
|
T
Рис. 36. Реальные (1,2) и теоретические (1', 2') кривые охлаждения и нагрева
В реальных металлах и сплавах необходимы определенные степени переохлаждения mn и определенная степень перегрева при плавле-
нии (mn)'.
Значения mn и (mn)' могут достигать нескольких десятков градусов. Чем выше mn, тем процесс кристаллизации идет с большей скоростью, и диффузионные процессы в сплаве замедляются (а при очень больших mn могут быть и подавлены).
Различают несколько видов термической обработки:
1)закалку;
2)отпуск;
3)отжиг I и II рода.
Закалка – это термическая обработка материалов, заключающаяся в их нагреве и последующем быстром охлаждении с целью фикса-
48
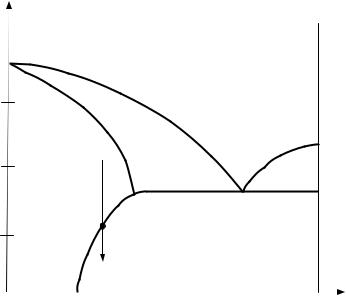
ции высокотемпературного состояния материала и подавления нежелательных процессов, происходящих при его медленном охлаждении.
Рассмотрим закалку на примере сплава Al – Cu (рис. 37).
t, °C
660
L
600 |
|
|
400 |
I |
L + α |
|
|
|
α |
А |
|
200 |
|
α + β |
|
|
|
Al |
|
40 Cu, % |
Рис. 37. Диаграмма состояния сплава алюминий – медь: α – твердый раствор Cu в Al; β – твердый раствор Al в Cu
При медленном охлаждении ниже tA из сплава I (твердый раствор α) в соответствии с диаграммой состояния выкристаллизовывается твердый раствор β, т. е. α → β, получается гетерогенный сплав.
При быстром охлаждении, т. е. при закалке, из α-области фиксируется твердый раствор, который при низких температурах сильно пересыщен медью. Это вызывает упрочнение кристаллической решетки. Следовательно, увеличивается твердость, прочность, но снижается пластичность.
Состояние сплава характеризуется термодинамической неустойчивостью. Поэтому проводят вторичный нагрев – отпуск.
Отпуск – это нагрев закаленного сплава ниже температуры равновесных превращений (до tA) с последующим медленным охлаждением. В результате отпуска сплав приближается к структурному равновесию, увеличивается пластичность.
Отпуск иногда называют старением.
Старение может быть естественным при комнатной температуре и искусственным при повышенной температуре.
49
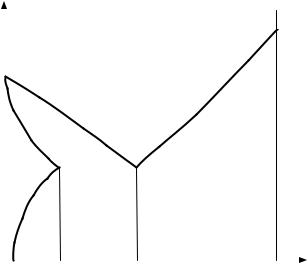
Отжиг – термическая операция, состоящая в нагреве сплава, имеющего неустойчивое состояние в результате предшествующей обработки (но не закалки), и приводящая сплав в более устойчивое состояние.
Примеры предшествующей обработки:
а) холодная пластическая деформация создает наклеп (искажение кристаллической решетки);
б) неравномерное приложение внешних напряжений приводит к появлению внутренних напряжений, неравномерному распределению упругой деформации.
Существует два вида отжига:
–отжиг I рода (для сплавов, не имеющих фазовых превращений) – это нагрев сплава с неравновесной структурой с последующим медленным охлаждением, приводящим сплав в более равновесное состояние;
–отжиг II рода, или фазовая перекристаллизация (для сплавов с фа-
зовыми превращениями), – это нагрев сплава с неравновесной структурой выше температуры фазовых превращений с последующим медленным охлаждением, приводящимсплаввболееравновесноесостояние.
Врезультате отжига снимаются внутренние напряжения в сплавах, наклеп, несколько понижается твердость, возрастают пластичность и ударная вязкость.
Основные виды термической обработки стали. Рассмотрим стальной участок диаграммы (рис. 38).
t, ºC
|
|
|
|
|
E |
910 G |
|
|
A |
|
|
|
А + Ф |
|
А + ЦII |
||
727 |
|
|
|
|
K |
|
P |
Ф + П S |
П + ЦII |
||
|
|
Ф+ ЦIII
Q
0,01 0,02
Феррит + цементит |
|
Перлит |
|
0,81 |
2,14 C, % |
Рис. 38. Стальной участок диаграммы
50
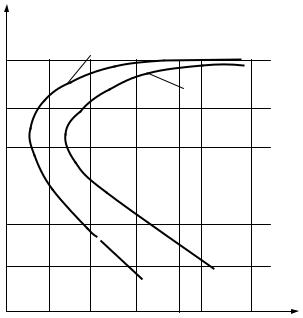
Выше линии GSE (на которой лежит критическая точка А3) – термодинамически устойчив аустенит, ниже линии PSK – фазовая смесь Ф + Ц.
При t = 727°С (линия PSK, нижняя критическая точка А1) протекает эвтектоидная реакция AS ↔ ФР + Ц или А↔П.
Чтобы отличить критическую точку при нагреве от критической точки при охлаждении, рядом с буквой А ставят букву с – при нагреве и r – при охлаждении.
Свойства и строение продуктов превращения аустенита зависят от температуры, при которой происходит его распад (рис. 39).
При малых степенях переохлаждения получается грубая смесь феррита и цементита – перлит. При более высокой степени переохлаждения дисперсность структур возрастает, мелкодисперсную смесь феррита и цементита называют сорбитом.
При еще более высокой степени переохлаждения образуется
троостит.
Перлит, сорбит, троостит – структуры с одинаковой природой фаз (Ф + Ц), отличающиеся степенью дисперсности феррита и цементита (рис. 40), и твердостью, которая возрастает с увеличением степени дисперсности.
t, °C |
|
Сталь 40 |
|
|
|
||
727 |
|
|
начало превращения А → П |
Аустенит |
|||
|
|
|
|
|
|
||
|
|
|
|
|
|
|
Перлит |
600 |
|
|
|
|
|
|
Сорбит |
|
|
|
|
|
|
|
Троостит |
500 |
|
|
|
|
|
|
Верхний |
|
|
|
|
|
|
|
бейнит |
|
|
|
|
|
|
|
Нижний |
300 |
|
|
|
|
|
|
бейнит |
|
|
|
|
|
|
|
|
200 |
Мн |
|
|
|
|
Мартенсит |
|
|
|
|
|
|
|
||
|
|
|
|
|
|
|
|
100 |
|
Мк |
|
|
1 000 10 000 T, с |
||
0,1 |
1 |
10 |
100 |
Рис. 39. Диаграмма изотермического превращения аустенита для доэвтектоидной стали (0,4% углерода); Мн – температурная линия начала
мартенситного превращения; Мн–Мк – интервал мартенситного превращения
51
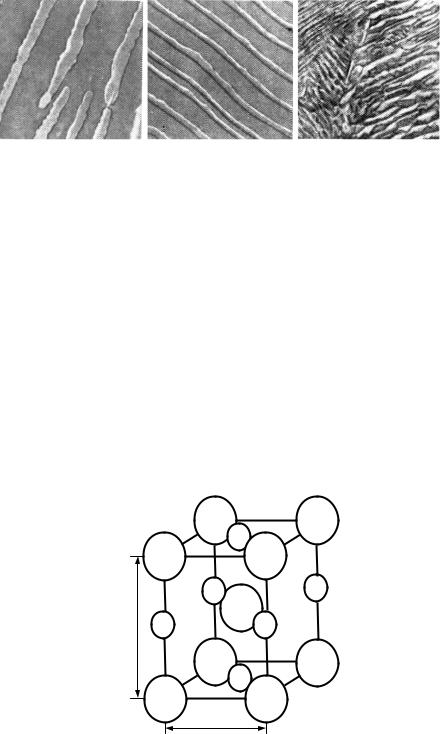
а |
б |
в |
Рис. 40. Микроструктура: а – перлит (×7500), распад при t = 700°С;
б– сорбит (×7500), распад при t = 650°С;
в– троостит (×16 000), распад при t = 600°С
При быстром охлаждении (vохл > vкрит), то есть при закалке, распад аустенита подавляется и происходит мартенситное превращение:
А → М или Feγ(C) → Fe*α(C).
Критической скоростью закалки называется такая наименьшая скорость охлаждения, при которой весь аустенит переохлаждается до мартенситного превращения.
Мартенсит – пересыщенный твердый раствор внедрения углерода в α-Fe. Объемно-центрированная решетка α-Fe из кубической переходит в тетрагональную (рис. 41). Ее искажения около внедренных атомов углерода вызывают упрочнение, следовательно, резко увеличивается твердость, прочность, но снижается пластичность.
c
Fe |
Fe |
|
C |
Fe |
Fe |
C |
C |
Fe |
|
C |
C |
Fe |
Fe |
|
C |
Fe |
Fe |
a |
|
Рис. 41. Объемно-центрированная тетрагональная (ОЦТ) решетка мартенсита (все октаэдрические междоузлия по оси с заняты атомами углерода)
Твердость мартенсита зависит от содержания в нем углерода (рис. 42). Мартенсит в стали, содержащей 0,1% С, имеет твердость примерно
52
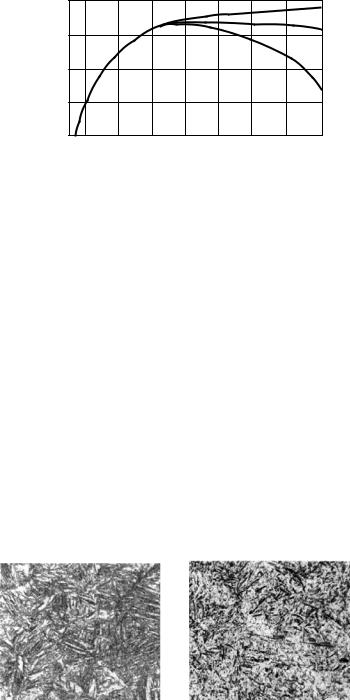
30 НRC. При 0,7% С твердость мартенсита достигает максимального значения (64 НRC) и при дальнейшем увеличении содержания углерода она существенно не увеличивается (рис. 42, кривая 2).
Твердость HRC
70 |
|
|
|
3 |
|
2 |
|
|
|
|
|
|
|
||
60 |
|
|
|
|
|
|
|
|
|
|
|
|
1 |
|
|
50 |
|
|
|
|
|
|
|
|
|
|
|
|
|
|
|
40 |
|
|
|
|
|
|
|
30 |
|
|
|
|
|
|
|
0,2 |
0,4 |
0,6 |
0,8 |
1,0 |
1,2 |
1,4 |
1,6 |
C, %
Рис. 42. Изменение твердости закаленной стали в зависимости от содержания углерода и температуры закалки: 1 – нагрев выше Ас3; 2 – нагрев выше Ас1
(770°С); 3 – твердость мартенсита
Особенности мартенситного превращения
1.Бездиффузионное: концентрация С в мартенсите такая же, как и
висходном аустените.
2.Механизм А → М носит сдвиговый характер: атомы смещаются на расстояния, не превышающие межатомные.
3.Решетка мартенсита – ОЦТ – объемно-центрированная тетрагональная (рис. 41).
Структура мартенсита – игольчатая. Кристаллы мартенсита имеют форму пластин или линз (рис. 43). Определены два основных структурных типа мартенсита – пластинчатый (двойниковый) и реечный (дислокационный); ихобразованиезависитоттемпературыформирования.
4.А → М не идет до конца: в сталях всегда остается так называемый остаточный аустенит.
а |
б |
Рис. 43. Структура мартенсита в сталях массового назначения: а – крупноигольчатый; б – мелкоигольчатый
53
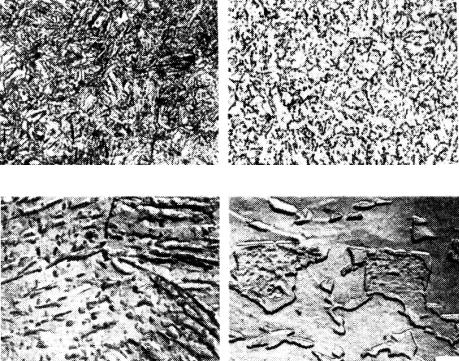
Мартенситное превращение реализуется в интервале температур Мн – Мк. Температуры начала Мн и конца Мк мартенситного превращения зависятотсодержанияуглеродаваустенитестали(рис. 39).
Существует также и промежуточное бейнитное превращение. Оно возможно в интервале температур ниже перлитного и выше мартенситного интервала превращений. Бейнит имеет игольчатую структуру
(рис. 44).
а |
б |
в г
Рис. 44. Структура бейнита: а, в – верхний бейнит; б, г – нижний бейнит (а, в – ×500; б, г – электронный микроскоп ×3000)
При бейнитном превращении отсутствует самодиффузия железа, но интенсивно протекает диффузия углерода (рис. 39). Для нижнего бейнита характерно γ → α-превращение.
Закалка и отжиг II рода для сталей может быть полным и неполным (табл. 8).
Для получения сталей с высокими механическими свойствами применяют закалку: для доэвтектоидных сталей проводят полную закалку; для заэвтектоидных сталей проводят неполную закалку.
Если при отжиге охлаждение проводят не в печи, а на спокойном воздухе (более быстрое охлаждение), то такой отжиг называют нормализацией (применяется для низкоуглеродистых сталей – дешевле).
54
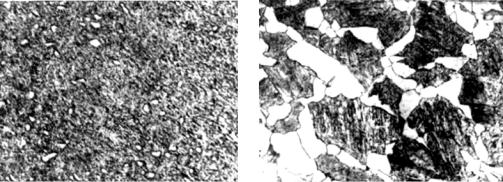
|
|
|
Таблица 8 |
|
Виды термообработки стали |
||
|
|
|
|
Температура |
Охлаждение |
Вид ТО |
Структура стали |
ТО |
|
|
после отжига или закалки |
tТО > tGSE |
Медленное |
Полный отжиг |
Доэвтектоидная сталь Ф + П |
(выше Ас3) |
|
II рода |
Эвтектоидная сталь П |
tPSK < tТО < tGSE |
Медленное |
Неполный отжиг |
Заэвтектоидная сталь П + Ц |
Ас1< tТО< Ас3 |
|
II рода |
|
tТО < tPSK (Ас1) |
Медленное |
Низкий отжиг |
Доэвтектоидная сталь Ф + П |
|
|
|
Эвтектоидная сталь П |
|
|
|
Заэвтектоидная сталь П + Ц |
tТО > tGSE (Ас3) |
Быстрое |
Полная закалка |
Мартенсит |
tPSK < tТО < tGSE |
Быстрое |
Неполная закалка |
Доэвтектоидная сталь М+ Ф |
Ас1< tТО< Ас3 |
|
|
Эвтектоидная сталь М |
|
|
|
Заэвтектоиднаясталь М + Ц |
Структуры заэвтектоидной и доэвтектоидной сталей показаны на рис. 45.
а |
б |
Рис. 45. Неполная закалка: а – мартенсит + цементит – заэвтектоидная сталь; б – феррит + мартенсит – доэвтектоидная сталь
Микротвердость некоторых фаз и структурных составляющих сплавов Fe – C и мартенсита приведены в табл. 5, 6.
Различают следующие способы закалки:
–в одном охладителе (для несложных деталей);
–прерывистая закалка, или закалка в двух средах;
–струйчатая закалка (обрызгивание) для части детали;
–закалка с самоотпуском (для ударного инструмента);
–ступенчатая закалка;
–изотермическая закалка.
55
В качестве закалочных сред используют:
–воду различной температуры;
–минеральное масло;
–растворы солей NaCl (1–30%);
Скорость охлаждения для различных закалочных сред представлена в табл. 9.
Для получения сплава с высокими механическими свойствами стремятся к тому, чтобы после закалки получилась мелкоигольчатая мартенситная структура (рис. 43, б).
Заключительной операцией термической обработки является отпуск стали, который включает в себя:
–нагрев закаленной стали до температур, лежащих ниже критической точки Ас1 (линия PSK);
–выдержку при данной температуре;
–последующее охлаждение с заданной скоростью.
Таблица 9
Охлаждающая способность различных закалочных сред
винтервалах температур перлитного превращения (650–450°С)
иоколо мартенситной точки стали (300–200°С)
|
Скорость охлаждения, град/с, |
|
Охлаждающая среда |
в интервале температур, °С |
|
|
650–450 |
300–200 |
Вода при 18°С |
600 |
270 |
Вода при 28°С |
500 |
270 |
Вода при 50°С |
100 |
270 |
Вода при 74°С |
30 |
20 |
Вода + 10% едкого натра при 18°С |
1200 |
300 |
Вода + 10% поваренной соли при 18°С |
1100 |
300 |
Вода + 10% серной кислоты при 18°С |
750 |
300 |
Вода мыльная при 18°С |
30 |
200 |
Вода дистиллированная |
250 |
300 |
Эмульсия масла в воде |
70 |
200 |
Машинное масло |
150 |
30 |
Керосин |
160–180 |
40–60 |
Медные плиты |
60 |
20 |
Железные плиты |
35 |
15 |
Спокойный воздух |
18 |
– |
При отпуске формируются окончательная структура и свойства изделия.
56