
- •ВВЕДЕНИЕ
- •1. СТРОЕНИЕ МЕТАЛЛОВ И СПЛАВОВ
- •Реальные кристаллы
- •Аморфные сплавы
- •Строение сплавов
- •2. ФАЗОВЫЕ ПРЕВРАЩЕНИЯ
- •Основные типы диаграмм
- •Системы с тремя компонентами
- •Основные структурные составляющие сплавов Fe – C
- •Диаграмма состояния Fe – Fe3C
- •Основные характеристики металлических материалов
- •Виды термической обработки материалов
- •Легирование
- •Поверхностное упрочнение (поверхностная закалка)
- •Железо и его сплавы
- •Стали
- •Чугуны
- •Твердые сплавы
- •Цветные металлы и сплавы
- •Алюминий и его сплавы
- •Медь и ее сплавы
- •Никель и его сплавы
- •Цинк и его сплавы
- •Магний и его сплавы
- •Титан и его сплавы
- •Припои
- •ЛИТЕРАТУРА
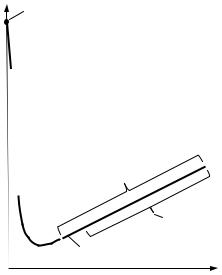
4. СПОСОБЫ ИЗМЕНЕНИЯ СТРУКТУРЫ И СВОЙСТВ МЕТАЛЛИЧЕСКИХ МАТЕРИАЛОВ
1.Основные характеристики металлических материалов.
2.Виды термической обработки материалов.
3.Легирование.
4.Поверхностное упрочнение (поверхностная закалка).
5.Химико-термическая обработка.
Основные характеристики металлических материалов
Прочность – способность материалов сопротивляться разрушению. Характеризуется пределом прочности при растяжении или разрыве (временным сопротивлением) – σ (МПа или Н/мм2).
Между пределом прочности при растяжении и твердостью пластичных материалов, определяемой способом вдавливания, существует количественная зависимость. Для большинства материалов σ = k НВ, где k – коэффициент пропорциональности k ≈ 0,3; НВ – твердость материала, определенная методом Бринелля, кгс/мм2.
Прочность металлических кристаллов зависит от количества дефектов (рис. 35).
Теоретическая прочность
Прочность усов
Прочность
Реальная прочность металлов
Металлы
упрочненные Чистые металлы
Искажения Рис. 35. Прочность кристаллов в зависимости от искажений решетки
42
Усы – нитевидные монокристаллы, иглообразные, высокопрочные материалы с большим соотношением длины к диаметру (100– 2500 / 1–10 мкм). Прочность монокристаллов приближается к теоретической прочности. Производство монокристаллов очень сложное и требует больших материальных затрат.
С увеличением плотности дислокаций прочность металлов вначале падает, а затем увеличивается, так как дислокации начинают мешать перемещаться друг другу.
Способы упрочнения металлов (ведут к увеличению полезной плотности дислокаций):
–механический наклеп;
–термическая обработка;
–измельчение зерна;
–легирование с образованием твердых растворов внедрения. Наклеп – искажение кристаллической решетки в результате пла-
стической деформации.
При пластической деформации зерна могут приобрести определенную структуру – текстуру. Беспорядочно ориентированные кристаллы под действием деформации поворачиваются осями наибольшей прочности вдоль направления деформации, с увеличением которой степень текстурированности возрастает. Текстура металла может возникнуть при литье, пластической деформации, отжиге, электроосаждении. Поликристаллические изделия с текстурой металла обладают анизотропией механических и физических свойств. В некоторых случаях текстуру получают намеренно – сплавы для постоянных магнитов, трансформаторная сталь.
Твердость – сопротивление металлов вдавливанию. При определении твердости производят вдавливание в испытуемый материал индентора, изготовленного из значительно более твердого материала, чем испытуемый.
Твердость характеризуется числом твердости в следующих единицах:
НВ – по методу Бринелля. Испытания проводят вдавливанием стального шарика определенного диаметра под нагрузкой в течение определенного времени (кгс/мм2);
HR – по методу Роквелла. Испытания на твердость проводят с помощью алмазного конуса с углом при вершине 120° (шкала А или С в зависимости от нагрузки) или стального закаленного шарика диаметром 1,588 мм (шкала В). В зависимости от способа испытания число твердости обозначают соответственно НRA, HRC, НRВ (табл. 3).
43
|
Выбор нагрузки и наконечника |
Таблица 3 |
||
|
|
|||
|
для испытаний на твердость по Роквеллу |
|||
|
|
|
|
|
Обозна- |
Вид наконечника |
Нагрузка, |
Обозначение |
Пределы измерения |
чение |
Н |
твердости |
в единицах твердости |
|
шкалы |
|
по Роквеллу |
по Роквеллу |
|
|
|
|||
|
|
|
|
|
А |
Алмазный конус |
600 |
HRA |
70–85 |
|
|
|
|
|
С |
Алмазный конус |
1500 |
НRC |
20–67 |
|
|
|
|
|
В |
Стальной шарик |
1000 |
НRВ |
25–100 |
|
|
|
|
|
Число твердости по Роквеллу – отвлеченное, выражается в условных единицах. За единицу твердости принята величина, соответствующая осевому перемещению наконечника на 0,002 мм. Число твердости по Роквеллу – HR рассчитывается по формулам:
– при измерениях по шкалам A и С |
HR = 100 – е. |
– при измерении по шкале В |
HR = 130 – е, |
Величина е определяется из выражения: |
|
е = (h − h0 ) |
, |
0,002 |
|
где h – глубина внедрения наконечника в испытуемый материал под действием общей нагрузки Р, измеренная после снятия основной нагрузки Р1, с оставлением предварительной нагрузки Р0; h0 – глубина внедрения наконечника в испытуемый материал под действием предварительной нагрузки P0;
HV – по методу Виккерса, в котором испытания проводят алмазной четырехгранной пирамидкой с квадратным основанием. Это измерение микротвердости, кг/мм2, Мн/м2.
Метод микротвердости является единственным методом, который позволяет определить твердость фаз и структурных составляющих многокомпонентных сплавов. Этим методом можно установить, как влияет термообработка, и какие легирующие компоненты играют главную роль в упрочнении исследуемого сплава. При измерении микротвердости чаще всего используют методы Виккерса (индентор с четырехгранной пирамидой и квадратным основанием) и Кнуупа (индентор с четырехгранной пирамидой и ромбическим основанием).
Между различными методами измерения твердости существует корреляция, хотя и не очень точная. Зная значение твердости, полученное одним способом, по соответствующим таблицам можно опре-
44

делить, какому числу твердости (и прочности) другого метода оно соответствует (табл. 4). Например, твердость в единицах HB приблизительно в 10 раз больше твердости, измеренной в единицах НRC.
Погрешность перевода чисел твердости по Виккерсу в единицы Бринелля составляет ±20 НВ, в единицы Роквелла – ±3 НRC (HRВ), в значения σ – ±10%.
Таблица 4
Сравнительная таблица значений твердости, полученных на различных приборах, и перевода в значения прочности
Предел проч- |
|
Твердость |
|
||
ности при рас- |
Виккерс |
Бринелль |
Роквелл |
Роквелл |
|
тяжении σ, |
|||||
HV |
НВ3000 |
HRB |
HRC |
||
МПа |
|||||
|
|
|
|
||
|
|
|
|
|
|
340 |
100 |
100 |
52,4 |
– |
|
510 |
150 |
150 |
79,9 |
– |
|
680 |
200 |
200 |
92,8 |
– |
|
780 |
230 |
230 |
98,4 |
– |
|
810 |
240 |
240 |
100,0 |
20,3 |
|
850 |
250 |
250 |
– |
22,1 |
|
1020 |
300 |
300 |
– |
30,2 |
|
1170 |
350 |
344 |
– |
36,3 |
|
1310 |
400 |
384 |
– |
40,5 |
|
1440 |
450 |
425 |
– |
44,5 |
|
1540 |
480 |
452 |
– |
46,8 |
Микротвердость некоторых фаз и структурных составляющих железо-углеродистых сплавов приведена в табл. 5, 6.
Микротвердость некоторых фаз |
Таблица 5 |
||
|
|||
и структурных составляющих сплавов Fe – C |
|
||
|
|
|
|
Наименование фазы или |
Марка стали |
Микротвердость |
|
структурной составляющей |
Мн/м2 |
кг/мм2 |
|
Феррит |
08 |
1 226 |
125 |
|
20 |
2 354–2 698 |
240–275 |
|
30 |
2 698–3 089 |
275–315 |
|
45 |
2 501 |
255 |
Сорбит (феррит с зернистыми |
20ХН |
2 698–3 197 |
275–325 |
карбидами) |
ШХ15 |
2 108–2 795 |
215–285 |
|
Х12 |
2 893–3 334 |
295–340 |
|
Х12М |
2 698–3 040 |
275–310 |
|
ЭИ229 |
2 942–3 060 |
300–312 |
45

|
|
|
Окончание табл. 5 |
|
|
|
|
|
|
Наименование фазы или |
Марка стали |
|
Микротвердость |
|
структурной составляющей |
|
Мн/м2 |
кг/мм2 |
|
|
|
2 |
698–3 138 |
|
Пластинчатый перлит |
20 |
275–320 |
||
|
30 |
3 |
197–3 383 |
325–345 |
|
У7 |
2 |
698–3 236 |
275–330 |
|
Чугун |
2 |
942–3 579 |
300–365 |
Карбидная фаза |
Чугун |
10 |
738–11 278 |
1 095–1 150 |
|
Х12М |
11 |
336–12 258 |
1 156–1 250 |
|
Х12 |
11 |
336–13 435 |
1 156–1 370 |
|
РК18 |
|
12 759 |
1 300 |
Аустенит |
Типа 18-8 |
|
1 716 |
175 |
|
Х12М |
|
5 099 |
520 |
|
Чугун |
4 |
168–4 854 |
425–495 |
Ледебуритная эвтектика |
Х12 |
7 |
355–8 336 |
750–850 |
|
Чугун |
9 807–11 032 |
1 000–1 125 |
|
Троостит |
– |
|
5 590 |
570 |
Бейнит |
– |
|
4 707 |
480 |
Стедит* |
– |
2 |
942–7 600 |
300–775 |
Графит |
– |
|
20–107 |
2–11 |
*Стедит – тройная фосфидная эвтектика – фосфид + цементит + феррит, образующаяся в структуре чугунов.
Оттоженный алюминий имеет твердость 200 Мн/м2 (20 кг/мм2). В отожженном состоянии твердость никеля составляет около 1000 Мн/м2 (100 кг/мм2). С увеличением температуры твердость
сплавов уменьшается.
|
|
Микротвердость мартенсита |
|
Таблица 6 |
|||
|
|
|
|
||||
|
|
|
|
|
|
|
|
|
Максимальная |
|
Mикротвердость мартенсита |
||||
Сплав |
микротвердость |
закалка |
закалка с температуры |
||||
|
мартенсита |
с температуры Ac1 |
оплавления |
||||
|
Мн/мм2 |
кг/мм2 |
Мн/мм2 |
|
кг/мм2 |
Мн/мм2 |
кг/мм2 |
20 |
10 297,0 |
1 050 |
7 109, 8 |
|
725 |
4 167,8 |
425 |
30 |
9 169,2 |
935 |
7 109,8 |
|
725 |
5 982,0 |
610 |
У7 |
9 904,7 |
1 010 |
6 962,7 |
|
710 |
8 924,0 |
910 |
20ХН |
6 227,2 |
635 |
5 050,4 |
|
515 |
4 413,0 |
450 |
ШХ15 |
10 198,9 |
1 040 |
5 785,9 |
|
590 |
7 845,3 |
800 |
Х12М |
8 727,9 |
890 |
3 922,7 |
|
400 |
5 001,4 |
510 |
ЭИ229 |
8 070,5–9 463,4 |
825–965 |
4 363,9 |
|
445 |
3 432,3 |
350 |
Чугун |
10 444,0 |
1 065 |
6 619,5– |
|
675–800 |
6 276,2 |
640 |
7 845,3 |
|
||||||
|
|
|
|
|
|
|
46
Микротвердость химических соединений приведена в табл. 7.
|
|
|
|
Таблица 7 |
|
Микротвердость некоторых карбидов, боридов, силицидов |
|||||
(по данным Мотта, Ковальского и др.) |
|
||||
|
|
|
|
|
|
Фаза |
Состав |
Нагрузка, |
Микротвердость |
||
Мн/мм2 |
кг/мм2 |
||||
|
|
г |
|||
Карбид бора |
ВС |
– |
36 285 |
3 700 |
|
Карбид ниобия |
NbС |
50 |
20 153–23 536 |
2 055–2 400 |
|
Карбид тантала |
ТаС |
50 |
15 171–17 652 |
1 547–1 800 |
|
Карбид титана |
TiС |
100 |
27 949–33 245 |
2 850–3 390 |
|
|
|
|
|
|
|
Карбид хрома |
Сr3С2 |
25 |
9 807–13 729 |
1 000–1 400 |
|
|
|
50 |
12 749 |
1 300 |
|
Карбид вольфрама |
WC |
100 |
15 544–16 956 |
1 585–1 730 |
|
|
|
50 |
23 536 |
2 400 |
|
|
W2C |
50 |
29 420–33 343 |
3 000–3 400 |
|
Карбид титана – вольфрама |
– |
– |
12 209–28 493 |
1 245–2 900 |
|
Карбид хрома – вольфрама |
– |
– |
14 710–23 536 |
1 500–2 400 |
|
Карбид железа – ванадия |
– |
25 |
17 770 |
1 812 |
|
Борид титана |
TiB2 |
50 |
33 343 |
3 400 |
|
Борид хрома |
СrВ2 |
50 |
17 652 |
1 800 |
|
Силицид титана |
Ti5Si3 |
100 |
9 669 |
986 |
|
Силицид хрома |
CrSi2 |
100 |
11 278 |
1 150 |
Относительное удлинение (δ) или относительное сужение (ψ) характеризуют пластичность материала. Пластичность – свойство твердых тел необратимо деформироваться под действием механических нагрузок. Пластичность определяет возможность обработки материалов давлением (ковка, прокатка).
Как правило, если прочность увеличивается, то пластичность уменьшается. Исключение – сталь, легированная никелем, который увеличивает пластичность и прочность.
Вязкость (внутреннее трение) – способность твердых и жидких тел оказывать сопротивление их течению (перемещению одного слоя тела относительно другого) под действием внешних сил.
Предел текучести – наименьшее напряжение σ0,2, после снятия которого обнаруживается пластическая деформация (0,2% от расчетной длины образца).
47