
- •ВВЕДЕНИЕ
- •1. СТРОЕНИЕ МЕТАЛЛОВ И СПЛАВОВ
- •Реальные кристаллы
- •Аморфные сплавы
- •Строение сплавов
- •2. ФАЗОВЫЕ ПРЕВРАЩЕНИЯ
- •Основные типы диаграмм
- •Системы с тремя компонентами
- •Основные структурные составляющие сплавов Fe – C
- •Диаграмма состояния Fe – Fe3C
- •Основные характеристики металлических материалов
- •Виды термической обработки материалов
- •Легирование
- •Поверхностное упрочнение (поверхностная закалка)
- •Железо и его сплавы
- •Стали
- •Чугуны
- •Твердые сплавы
- •Цветные металлы и сплавы
- •Алюминий и его сплавы
- •Медь и ее сплавы
- •Никель и его сплавы
- •Цинк и его сплавы
- •Магний и его сплавы
- •Титан и его сплавы
- •Припои
- •ЛИТЕРАТУРА
Отпуск полностью или частично устраняет внутренние напряжения, возникающие при закалке. Эти напряжения снимаются тем полнее, чем выше температура отпуска.
Наиболее интенсивно напряжения снижаются в результате выдержки в течение 15–30 мин. После выдержки в течение 1,5 ч напряжения снижаются до минимальной величины, которая может быть достигнута отпуском при данной температуре.
В соответствии с техническими требованиями, предъявляемыми к изделиям, применяют следующие виды отпуска:
–низкий;
–средний;
–высокий.
Низкий отпуск – нагрев закаленной стали до 150–200°С. Время выдержки при этом рекомендуется 2,0–3,0 ч. Выдержка должна обеспечить получение стабильной структуры.
Низкий отпуск применяется для частичного снятия внутренних напряжений, повышения вязкости и пластичности стали без заметного снижения твердости. Этому виду отпуска подвергают детали, для которых требуется высокая твердость и износоустойчивость (измерительный и режущий инструмент, изделия из цементируемых сталей). Структура стали – отпущенный мартенсит, твердость которого лежит в пределах 56–64 HRC.
Средний отпуск – нагрев закаленной стали до 300–400°С. Время выдержки рекомендуется 1,0–2,0 ч. При этом отпуске обеспечивается относительно высокая твердость изделия 40–45 HRC и максимальный предел упругости при достаточном пределе прочности. Данный вид отпуска чаще всего применяют при изготовлении рессор и пружин. После среднего отпуска получают структуру троостита отпуска.
Высокий отпуск – нагрев закаленной стали до 500–600°С. Время выдержки – 0,5–1,0 ч. Структура стали после высокого отпуска – сорбит отпуска, твердость 30–32 HRC. Высокий отпуск обеспечивает более полное снятие напряжений и дает наилучшее сочетание прочности, пластичности и ударной вязкости. Этот отпуск применяют при изготовлении шатунов, ответственных крепежных изделий и деталей машин, изготовляемых из конструкционных сталей.
Легирование
Легирование – это введение в состав металлических сплавов легирующих элементов для придания сплавам определенных физических, химических и механических свойств.
57
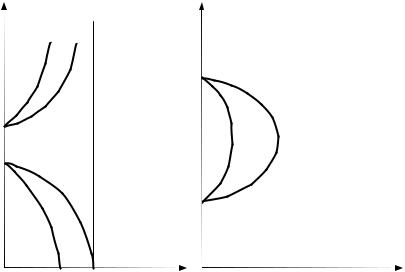
Все элементы, которые растворяются в железе, влияют на температурный интервал существования его аллотропических модификаций.
Никель Ni имеет гранецентрированную кубическую решетку с параметрами, близкими γ-Fe. Ni, Mn и другие металлы расширяют область существования γ-модификации Fe от комнатной температуры до температуры плавления (рис. 46, а).
Такие сплавы на основе железа называют аустенитными.
При содержании Si, V, Mo и других элементов свыше определенной концентрации устойчивым при всех температурах является α- состояние (рис. 46, б).
Такие сплавы на основе железа называют ферритными.
t, °C
αα+γ
γ |
γ α + γ |
α
αα + γ
Fe |
Ni, Mn,…, % Fe Cr, W, Mo, Ti, Si,…, % |
а б
Рис. 46. Диаграмма состояния сплава железо – легирующий элемент:
а– расширение γ-области; б – расширение α-области
Вотличие от других сплавов на основе железа аустенитные и ферритные сплавы не имеют превращений при нагреве и охлаждении.
Всплавах легирующие элементы могут находиться:
а) в свободном состоянии в виде включений; б) в форме интерметаллических соединений с железом или между
собой;
в) в виде оксидов (Al2O3, TiO2 и др.), сульфидов; г) в форме раствора с основным компонентом;
д) в виде раствора в цементите или в виде самостоятельных карбидов титана, ниобия, тантала, хрома, марганца, железа.
58
Карбиды TiC, NbC, смешанный карбид (Ti, Nb)C, TaC и Та2С относятся к карбидам II группы, имеют простую кристаллическую решетку и образуют фазы внедрения.
Карбиды Cr23C6 или (Cr, Mn, Fe)23C6; Сr7C3, Fe3C образуют карбиды I группы, имеют сложную кристаллическую решетку.
Карбиды I группы при нагреве стали легко растворяются в аустените, карбиды II группы (фазы внедрения) при нагреве не переходят в твердый раствор.
Все карбидные фазы имеют высокие температуры плавления и высокую твердость.
Легирующие элементы влияют на превращения в стали: на кинетику распада аустенита, мартенситное превращение и превращение при отпуске.
Рассмотрим влияние основных легирующих элементов на коррозионную стойкость стали.
Хром – пассиватор, увеличивает коррозионную стойкость и жаростойкость (Cr образует прочные пленки, устойчивые в агрессивной среде и при высоких температурах). Имеет решетку ОЦК, изоморф-
ную α-Fe.
Жаростойкость – способность металла не корродировать при высоких температурах (т. е. не окисляться). Жаростойкость в сталях повышают Cr, Al, Si.
Жаропрочность – способность сплава сохранять прочность, работоспособность при высоких температурах.
Никель увеличивает коррозионную стойкость в растворах и расплавах щелочей; увеличивает сопротивление коррозионной усталости. Ni имеет ГЦК с параметрами, близкими с решеткой γ-Fe; это дает образование непрерывного ряда твердых растворов Feγ(Ni).
Коррозионная усталость – разрушение металла при одновременном воздействии на него циклической нагрузки и коррозионной среды.
Молибден увеличивает прочность стали в хлорид- и хлорсодержащих средах, в органических кислотах и в восстановительных средах.
Молибден с ОЦК образует ограниченные твердые растворы с α-Fe. Максимальная растворимость Мо при 20°С – 5%; при 1450°С – 26%.
Алюминий и кремний повышают жаростойкость особенно в окислительных средах (образуются устойчивые при высоких температурах
Al2O3 и SiO2).
Титан и ниобий снижают склонность стали к межкристаллической коррозии, так как являются сильными карбидообразователями.
59

Поверхностное упрочнение (поверхностная закалка)
Целью поверхностной закалки является получение большой твердости в поверхностном слое детали с сохранением вязкой сердцевины. Поверхностное упрочнение заключается в нагреве поверхностного слоя детали с последующей закалкой.
Существует несколько методов поверхностного нагрева:
1)в расплавленных металлах или солях;
2)пламенем газовой горелки – пламенная закалка;
3)лучом лазера;
4)в электролитах;
5)токами высокой частоты – твч-метод.
Метод твч широко используется в промышленности, так как позволяет легко (изменяя силу тока) получать любую температуру и любую скорость нагрева:
Q = I2Rτ, |
(6) |
где Q – теплота, выделяющаяся в результате прохождения электрического тока, Дж; I – сила тока, А; R – сопротивление, Ом; τ – время воздействия тока (обычно берут небольшим), с.
Глубина прогрева детали δ определяется по формуле:
δ = 5030 |
ρ |
, |
(7) |
|
μf |
||||
|
|
|
где ρ – удельное сопротивление, Ом·см; μ – магнитная проницаемость, Тл/(А/м); f – частота тока, Гц.
Чем больше частота тока, тем на меньшую глубину прогревается металл.
Для получения большой глубины прогрева детали (δ = 2–3 мм), нагрев осуществляют машинными генераторами.
Химико-термическаяобработка
Химико-термическая обработка (ХТО) – это нагрев сплава в определенной химической среде с целью насыщения поверхности нужным элементом и придания ей определенных свойств. ХТО возможна для металлов, способных растворять различные элементы.
Достоинства ХТО:
–независимость от внешней формы изделия;
–большое различие между свойствами сердцевины и поверхности;
60
– последствия перегрева поверхности могут быть устранены последующей термической обработкой.
Основные виды ХТО
Цементация – насыщение поверхности малоуглеродистой стали углеродом, позволяет повысить твердость и износостойкость поверхностных слоев стали. После цементации детали подвергают закалке и для снятия внутренних напряжений отпуску при низкой температуре
(150–200°С).
В результате такой обработки (цементация + закалка + низкий отпуск) поверхность должна иметь твердость 58–62 HRC, а сердцевина – 25–35 HRC для легированных и менее 20 HRC для углеродистых сталей.
Цементацию рекомендуется проводить так, чтобы содержание углерода в наружном слое не превышало 1,1–1,2%. Более высокое содержание углерода приводит к образованию значительных количеств вторичного цементита, сообщающего слою повышенную хрупкость.
Структура цементированного слоя после медленного охлаждения от температуры цементации показана на рис. 47. Поверхностная зона, в которой углерода больше 0,8–0,9%, имеет структуру перлит + цементит – это так называемая заэвтектоидная зона; затем следует зона с содержанием углерода около 0,8% – это эвтектоидная зона и, наконец, доэвтектоидная зона, содержащая углерода менее 0,7%, плавно переходящая в структуру сердцевины.
По способу проведения различают:
–твердую цементацию (в древесном угле);
–жидкую цементацию;
–газовую цементацию.
Для массового производства газовая цементация является основным процессом цементации и только для мелкосерийного или единичного производства экономически целесообразен более простой способ твердой цементации.
Газовая цементация осуществляется в стационарных или методических (непрерывно действующих) конвейерных печах. Цементирующий газ приготавливают отдельно и подают в цементационную реторту.
Цементирующими газами являются оксид углерода и газообразные углеводороды. Разложение этих соединений приводит к образованию активного атомарного углерода (при 950°С):
2СО → СО2 + С; |
(8) |
СnН2n → 2nН + nС; |
(9) |
СnН2n + 2 → (2n + 2)Н + nС. |
(10) |
61
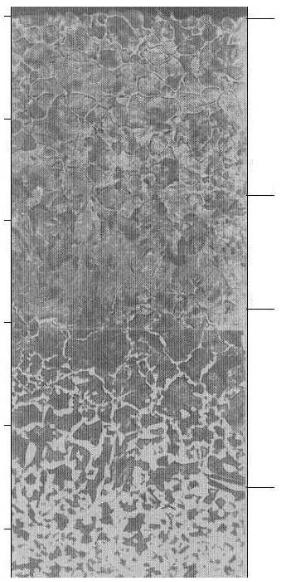
Расстояние от поверхности, мм
0,0
0,5
1,0
1,5
2,0
2,5
Сердцевина Доэвтектоидная зона Эвтектоидная Заэвтектоидная зона зона
Pиc. 47. Mикpocтpyктypa цeмeнтиpoвaннoгo слоя пocлe медленнoгo охлаждения
Наибольшее распространение в качестве газовых карбюризаторов получили предельные углеводороды (СnН2n + 2) – метан, этан, пропан, бутан и др., а из них – метан в виде природного газа (92–96% СН4).
Свободные атомы углерода, образовавшиеся по вышеприведенным реакциям, абсорбируются поверхностью сплава, а затем диффундируют вглубь металла.
Если поверхность стали не поглощает весь выделяющийся углерод (абсорбция отстает от диссоциации), то свободный углерод, кристаллизуясь из газовой фазы, откладывается в виде плотной пленки сажи на детали, затрудняя процесс цементации.
62
Поэтому для рационального ведения процесса газовой цементации нужно иметь газ определенного состава и регламентировать его расход.
Практически цементацию проводят при 900–930°С, но имеется тенденция повысить температуру цементации до 950–970°С и выше.
Повышение температуры цементации, как следует из общих представлений о процессе диффузии, резко увеличивает глубину слоя.
Азотирование – насыщение поверхности малоуглеродистой стали азотом (t = 500–600°С) с целью увеличения износостойкости и коррозионной стойкости.
После азотирования рабочая температура, при которой сохраняется износостойкость, – 550°С, а после цементации – 200°С.
Азот образует твердый раствор внедрения и нитриды: Fe2N, Fe4N (фазы внедрения), CrN, TiN.
Цианирование – одновременное насыщение стали азотом и углеродом, позволяющее повысить износостойкость, твердость, коррозионную стойкость средне- и низкоуглеродистой, быстрорежущей стали.
Способы осуществления:
–в расплаве цианистых солей KCN – NaCN 1:1;
–в смеси солей K4[Fe(CN)6] + Na2CO3.
Диффузионная металлизация используется для защиты изделий от коррозии, повышенияихжаростойкости, износостойкости, твердости.
Различают жидкую, твердую и газообразную металлизацию. Диффузионная металлизация является длительным процессом, проводится при высокой температуре (t ≈ 1200°C). Диффундирующие металлы образуют с железом твердые растворы замещения.
Чаще всего проводят хромирование (насыщение поверхности Cr); алитирование (Al); силицирование (Si повышает кислотоустойчивость стали), борирование (В, бориды обеспечивают высокую твердость). Борирование проводят электролизом расплава Na2B4O7.
63