
- •Глава 4 режимы резания
- •Строгание
- •25. Поправочный коэффициент Кyv учитывающий влияние ударной нагрузки на скорость рсзания при строганин
- •Мощность резания
- •Разрезание
- •Нарезание резьбы
- •Протягивание
- •Зубонарезание
- •§ 14. Нормирование шлифовальных работ
- •§ 15. Нормирование многоинструментных работ
- •Оглавление
- •Раздел II
- •Раздел III
- •Список литературы
Таблица 3.52. Припуски и предельные отклонения для гладких поковок круглого, квадратного и прямоугольного сечений (в мм) по ГОСТ 7829-70
Примечания:
1. Данные таблицы распространяются на детали с соотношением размеров: 1>1,5О для круглого сечения; ^>1,БВ и Н<В<1,5Я -для квадратного и прямоугольного сечений.
2. В случае обработки поверхности детали шероховатостью 6,3 мкм и ниже допускается увеличение соответствующих табличных значений припусков, но не более чем 1 мм на сторону.
3. Припуски и предельные отклонения для прямоугольного сечения детали назначаются в зависимости от наибольшего размера сечения.
Глава 4 режимы резания
Уровень режима резания находится в зависимости от типа и конструкции инструмента, материала и геометрии его режущей части, качества заточки, правильности установки и закрепления инструмента на станке, состояния системы СПИД и определяет силы резания и расходуемую при резании мощность.
При назначении и расчете режима резания учитывают тип и размеры инструмента, материал его режущей части, материал и состояние заготовки, тип оборудования и его состояние. При этом следует помнить, что элементы режима резания находятся во взаимной функциональной зависимости, устанавливаемой эмпири-ческими формулами, что глубина резания и подача непосредственно влияют на стойкость Т инструмента, с которой, в свою очередь, связана скорость резания.
Глубина резания t: при черновой обработке назначают по возможности максимальную t, равную всему припуску па обработку или большей части его; при чистовой обработке – в зависимости от требуемых степени точности и шероховатости обработанной поверхности.
Подача s: при черновой обработке выбирают максимально возможную подачу, исходя из прочности и жесткости системы СПИД, мощности привода станка и других ограничивающих факторов; при чистовой обработке – в зависимости от требуемых степени точности и шероховатости обработанной поверхности.
Скорость резания V рассчитывают по формулам, учитывающим величины глубины резания и подачи, установленной стойкости с внесением поправок на физнко-мех-анические свойства обрабатываемого материала, качество заготовки, вид обработки, материал режущей части инструмента, смазочно-охлаждающую жидкость и др.
Толщина срезаемого слоя а – кратчайшее расстояние между двумя последовательными положениями режущего лезвия.
Ширина срезаемого слоя b – расстояние между обработанной и обрабатываемой поверхностями, измеренное вдоль режущего лезвия.
Характеристики элементов резания для различных видов обработки приведены в табл. 1.
ТОЧЕНИЕ
Глубина резания: при черновой обработке глубина резания обычно равна всему припуску на обработку; при чистовой обработке с шероховатостью поверхности до 5-го класса чистоты включительно t = 0,5 ÷ 2,0 мм; для 6 и 7-го классов t = 0,1 ÷ 0,4 мм.
Подача (табл. 2-6). При черновой обработке выбранную подачу следует проверить по прочности державки резца и пластинки из твердого сплава, жесткости обрабатываемой детали и прочности механизма станка.
Прочность державки резца проверяют расчетом на изгиб (рис. 1) от действия вертикальной составляющей силы резания:
где[G ]u = 20 кГ/мм2 для державок из конструкционной стали.
Дли резцов с пластинками из твердого сплава выбранную подачу проверяют по прочности пластинки (табл. 7).
Проверку по жесткости обрабатываемой детали производят, исходя из точности обработки (стрела прогиба детали f в мм не должна превышать 0,25 поля допуска, соответствующего данной операции). В этом случае радиальную силу Ру, допускаемую точностью обработки, определяют по следующим формулам:
- деталь установлена в центрах;
- одно конец детали зажат в патроне,
второй - поджат центром;
- деталь закреплена в патроне;
Рис. 1. Расчетная схема для резца
здесь ℓ - длина детали (заготовки) в мм; Е – модуль упругости в кГ/мм2; J – момент инерции поперечною сечения детали.
Проверку подачи, исходя из прочности механизма подачи, производят по уравнению Рх <= Pcm , а исходя из прочности механизма коробки скоростей или мощности электродвигателя – по уравнению
2М <= 2Мcm ,
где Рх – осевая составляющая силы резания в кГ; 2М – двойной крутящий момент на шпинделе станка в кГ*м; Рст и 2Мст - осевая сила и двойной крутящий момент, допускаемые соответственно прочностью механизма подачи в коробки скоростей, устанавливаются по паспорту станка.
Скорость резания рассчитывают по следующим формулам: при наружном продольном и поперечном точении и растачивании
при отрезании, прорезании и фасонном точении
-
Рис. 2. Твердосплавный проходной резец с дополнительным лезвием
Среднее значение стойкости Т при одноинструментной обработке равно 60 мин, за исключением фасонного точения, для которого Т = 120 мин, и точения резцами с дополнительным лезвием (рис. 2), для которых Т = 30 - 45 мин.
Постоянная Сv для данных табличных условий резания и показатели степени xv, yv и т приведены в табл. 8.
Толщина пластинки из твердого сплава в мм |
Подача s мм/ об при глубине резания t в мм до |
Примечания |
|||
4 |
7 |
13 |
22 |
||
4 |
1,3 |
1,1 |
0,9 |
0,8 |
1.В зависимости от механических свойств стали на табличное значение подачи вводить поправочный коэффициент 1,2 при σв = 48 - 64 кГ/мм2, 1,0 при σв = 65 - 87 кГ/мм2и 0,85 при σв = =87 - 117 кГ/мм2. 2. При обработке чугуна на табличное значение подачи вводить поправочный коэффициент 1,6. 3. В зависимости от главного угла и плане на табличное значение подачи вводить поправочный коэффициент 1,4 при φ = 300; 1,0 при φ = 45°; 0,6 при φ =60°и 0,4 при φ =90°. 4. При обработке с ударами, подачу уменьшать на 20%. |
6 |
2,6 |
2,2 |
1,8 |
1,5 |
|
8 |
4,2 |
3,6 |
3,0 |
2,5 |
|
10 |
6,1 |
5,1 |
4,2 |
3,6 |
Общин поправочный коэффициент kv на скорость резания представляет собой произведение из отдельных коэффициентов (kv = Kмv Knv Kuv Kφv Kφ1v Krv Kqv Kov), каждый из которых отражает влияние определенного фактора на скорость резания: Kмv – качество обрабатываемого материала (табл. 9-13); Knv – состояние поверхности заготовки (табл. 14); Kuv – материал режущей части (табл. 15); Kφv , Kφ1v , Krv , Kqv – параметры резца; главный угол в плане, вспомогательный угол в плане, радиус при вершине, поперечное сечение державки (табл. 16). Последние три
коэффициента - только для резцов из быстрорежущей стали; Kov - вид обработки (табл. 17).
Режимы резания при обработке закаленной стали твердосплавными резцами приведены в табл. 18, а при тонком (алмазном) точении – в табл, 19,
Сила резания (рис. 3). Составляющие силы резания (тангенциальную Рz, радиальную Ру и осевую Рх) при наружном продольном и поперечном точении, растачивании, отрезании, прорезании и фасонном точении рассчитывают по формуле
Рz(Ру; Рх) = CPt xpyspvn ×pKP кГ.
При отрезании, прорезании и фасонном точении. t – длина лезвия резца.
Постоянная Ср для данных (расчетных) условий резания и показатели степени хр, ур а nр для каждой из составляющих силы резания приведены в табл. 20.
Поправочный коэффициент Кр представляет собой произведение из ряда коэффициентов (КР=KmpKφpKγpRrpKλp), учитывающих изменение против табличных условий резания.
Рис. 3. Схема расположения составляющих силы резания
19. Режимы резания при тонком (алмазном) точении на |
|
|
|
|
---|---|---|---|---|
|
|
|
|
|
Если механические свойства обрабатываемого материала отличаются от приведенных и табл. 20, вводят поправочный коэффициент на качество материала Кмр, определяемый для стали и чугуна по табл. 21 и 22, для медных и алюминиевых сплавов – по табл. 23.
Влияние геометрических параметров резца на составляющие силы резания учитывается коэффициентами Kφp, Kγp, Кrp, Kλp,х приведенными в табл. 24.
Тип станка |
Продольно-строгальный |
Поперечно-строгальный |
Долбежный |
Коэффициент Кyv |
1,0 |
- .0,8 |
0,6 |
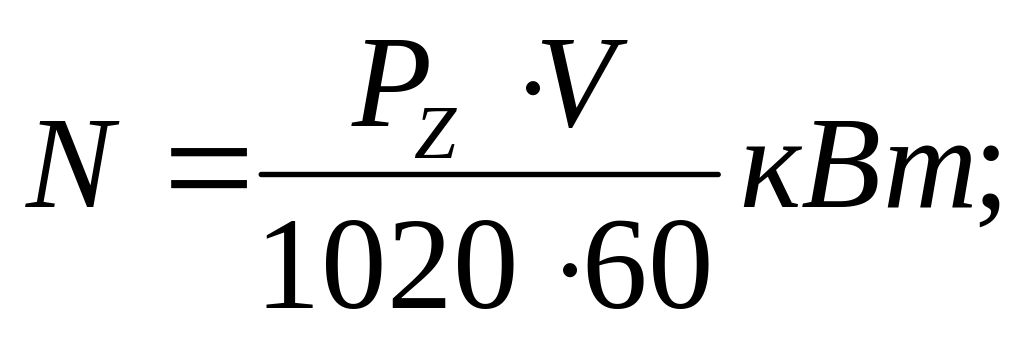
При одновременной работе несколькими инструментами эффективную мощность определяют как суммарную мощность для отдельных инструментов.