
Воробьев Ю.В. Учебно-методическое пособие по деталям машин
.pdf
|
|
|
YF Ft KFD KF KC |
|
|
Проч- |
|
|
|
σF 2 = 0,8 |
= |
|
ность по |
||
|
|
bw2mc |
|
напря- |
|||
|
|
|
|
|
|||
σF2 |
[3, (5.44)] |
= 0,8 3,74 5639 1 1 1,55 1,15 |
= |
жениям |
|||
|
|
|
45 4 3 |
|
|
изгиба |
|
|
|
= 58 МПа≤ [σF 2 ]= 262 МПа |
обеспеч |
||||
|
|
|
|
|
|
ена |
|
|
|
|
ПРОДОЛЖЕНИЕ ТАБЛ. 14 |
Определяемый параметр
Использованная литература
Численное значение |
Примеч |
|
ание |
||
|
||
|
|
2.5 Проверка на перегрузку по контактным напряжениям
|
|
|
|
|
|
|
|
|
|
|
σт = |
||
|
|
|
|
[σHmax ] = 2,8σт |
= 2,8 640 = |
1792 |
= |
675 |
|||||
[σHmax] |
[3,табл. 4.6] |
МПа |
|||||||||||
|
|
МПа |
|
||||||||||
|
|
|
|
|
|
|
[3. табл. |
||||||
|
|
|
|
|
|
|
|
|
|
|
|||
|
|
|
|
|
|
|
|
|
|
|
|
4.5] |
|
|
|
|
|
|
|
|
|
|
|
|
|
||
|
|
|
|
|
|
|
|
|
|
|
Условие |
||
|
|
|
|
|
|
|
|
|
|
|
статиче- |
||
|
|
|
|
|
|
|
Tп |
1,2 |
|
ской |
|||
σHmax |
|
[3, (4.43)] |
σHmax = σH |
T2 KНD = 484 |
1 1 = |
прочно- |
|||||||
|
|
= 581 МПа |
|
сти при |
|||||||||
|
|
|
|
|
|
|
пере- |
||||||
|
|
|
|
≤ [σH max ]=1792 МПа |
|
||||||||
|
|
|
|
грузке |
|||||||||
|
|
|
|
|
|
|
|
|
|
|
выпол- |
||
|
|
|
|
|
|
|
|
|
|
|
няется |
||
|
2.6 Проверка на перегрузку по напряжениям изгиба |
||||||||||||
|
|
|
|
|
|
|
|
|
|
|
|
|
|
[σ |
|
] |
|
|
|
|
~ |
|
|
|
|
|
|
Fmax |
[3, табл. 4.6] |
[σFmax ] = 2,7HB = 2,7 250 = |
|
|
|||||||||
|
|
= 675 МПа |
|
|
|
||||||||
|
|
|
|
|
|
|
|||||||
|
|
|
|
|
|
|
|
|
|
|
|
|
|
|
|
|
|
|
|
|
|
|
|
|
|
Запас |
|
|
|
|
|
|
|
|
|
|
|
|
статиче- |
||
|
|
|
|
|
Tп |
1,2 |
|
|
|
ской |
|||
|
|
|
|
σFmax =σF2 |
|
|
=58 |
|
= |
|
прочно- |
||
σFmax |
|
[3, (4.57)] |
T K |
FL |
1 1 |
|
|||||||
|
|
2 |
|
|
|
|
сти при |
||||||
|
|
|
|
|
|
|
|
|
|||||
|
|
|
|
= 69,6 МПа≤ [σF max ]= 650 |
МПа |
||||||||
|
|
|
|
|
пере- |
||||||||
|
|
|
|
|
|
|
|
|
|
|
грузке |
||
|
|
|
|
|
|
|
|
|
|
|
имеется |
3 Разработка сборочного чертежа планетарного редуктора [3, 7, 9, 15]. Сборочный чертеж планетарного редуктора показан в прил. 22.
Пример 6. Произвести полный расчет зацепления червячного редуктора приводной станции цепного конвейера. Схема привода и график его нагрузки показаны на рис. 24.
Дано: |
Ft |
= 1500 Н – окружное усилие на звездочке; vзв = |
= 0,607 м/с – окружная скорость на делительной окружности звездочки; z = 15 – число зубьев тяговой звездочки; t = 63 – шаг цепи; число звездочек – 2; срок службы – 10 лет; работа по 7 ч в сутки.
Рис. 24 Схема привода и график нагрузки: 1 – электродвигатель; 2 – муфта; 3 – червяк; 4 – колесо; 5 – корпус;
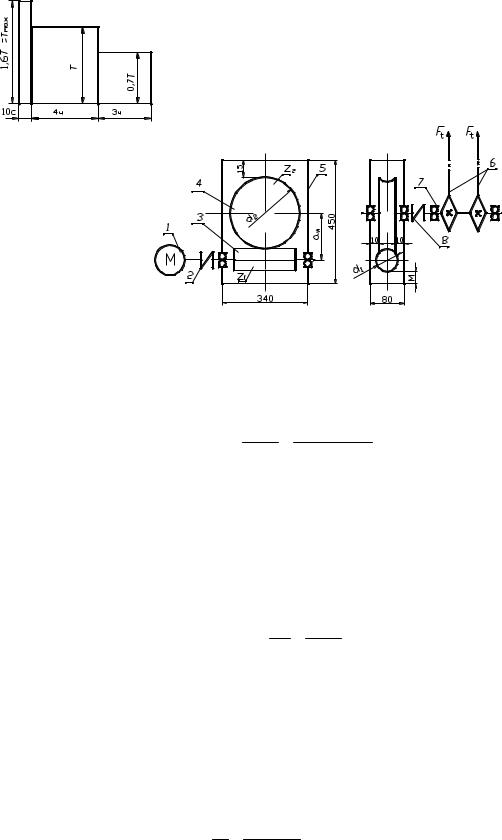
1 Кинематический и энергетический расчеты.
1.1Определим мощность на валу со звездочками
Pзв = 2Ft vзв = 2 1500 0,607 =1,785 кВт. 1000 1000
1.2 Рассчитаем потребную мощность [1, 3] электродвигателя
Pдв = |
Pзв |
= |
1,785 |
= 2,49 |
кВт, |
η3пηчзηм2 ηцп |
0,983 0,8 12 0,96 |
где ηп – кпд пары подшипников; ηм – кпд муфты; ηчз – кпд червячного зацепления; ηзв – кпд цепной
передачи.
1.3 Подбираем электродвигатель (прил. 7, 8):
Типоразмер 4А112МА6УЗ. Рдв = Р1 = 3 кВт; частота вращения (с учетом скольжения): nдв = n1 = 960 мин-1; Тmax/Tн = 2,2; Тп/Tн = 1,8.
ω1 = π30n1 = π 30960 =100,48 с–1.
1.4 Рассчитаем частоту вращения вала со звездочками:
n2 |
= |
60 1000vзв |
|
= |
60 1000 0,607 |
= 38,55 мин–1; |
|||
zt |
15 63 |
||||||||
|
|
|
|
|
|||||
|
|
ω2 = |
|
π 38,55 |
= 4,03 с–1. |
||||
|
|
|
|
||||||
|
|
|
|
|
|
30 |
|
|
1.5 Рассчитаем передаточное число редуктора
u = |
n1 |
= |
960 |
= 24,9 . |
|
n |
38,55 |
||||
|
|
|
|||
|
2 |
|
|
|
Вращающие моменты на валах:
T1 = P1 = 2,49 1000 = 24,78 Н·м = 24780 Н·мм; ω1 100,48
T2 = T1uηчз = 24,78 24,9 0,8 = 493,62 Н·м = 493620 Н·мм.
2Расчет зацепления [16]
2.1Выбор материалов и определение допускаемых напряжений. Червяк: Сталь 40Х, закаленная до HRC 45 … 55, червяк шлифованный.

Колесо: венец – бронза БрАЖ9-4Л (литье в землю), ступица – чугун СЧ15-32. В первом приближении оцениваем скорость скольжения:
vск = 4,5 10−4 n13 T2 = 4,5 10−4 9603 493,62 = 3,41 м/с.
По таблице 10.11 [16] выбираем допускаемые напряжения [σH ]=180 МПа, по табл. 10.10
σт = 200 МПа.
Допускаемые напряжения изгиба для бронзовых червячных колес при работе зубьев обеими сторонами (при реверсе):
[σ−1F ]= 0,16σв9 |
106 |
, |
|
NFE |
|
где σв =500 МПа – предел прочности бронзы БрАЖ 9-4Л [1]; NFE – эквивалентное число циклов нагружений:
|
9 |
|
|
|||
NFE = 60n2 ∑ |
Ti |
|
Lhi = 60 38,55(19 4 360 10 + 0,79 3 360 10) = |
|||
T |
||||||
2 |
|
|
|
|
||
= 34 106 , |
|
|
|
|
||
[σ−1F |
]= 0,16 5009 |
106 |
= 54,4 МПа . |
|||
34 106 |
||||||
|
|
|
|
|
2.2 Рассчитаем числа зубьев, выберем относительный диаметр и межосевое расстояние. Задаемся числом заходов червяка z1 = 2, тогда число зубьев колеса: z1 = 2·24,9 ≈ 50 > 28 – подрезания нет. Задаемся относительным диаметром червяка по табл. 10.1 [16] q = 10.
Коэффициент нагрузки: K H = K Hβ K Hυ ,
KHβ – коэффициент неравномерности нагрузки:
z |
2 |
3 |
|
50 |
3 |
|||
KHβ =1 + |
|
|
(1 − x)=1 + |
|
|
1 =1,19 , |
||
θ |
86 |
|||||||
|
|
|
|
|
где θ = 86 – коэффициент деформации червяка (табл. 10.6); х = 0 коэффициент смещения инструмента; KHυ – коэффициент динамической нагрузки.
Назначаем 8-ю степень точности передачи (по ст СЭВ 311–76), и учитывая ранее принятое значение
скорости скольжения vск |
= 3,41м/с, назначаем KHυ = 1,2. Тогда коэффициент нагрузки: |
||||||||||||||||
|
|
|
|
|
|
|
|
|
|
|
|
|
|
|
|
|
KH = KHβKHυ =1,19 1,2 =1,42 |
Рассчитываем межосевое расстояние: |
|||||||||||||||||
|
|
|
|
|
|
|
|
|
|
|
|
2 |
|
|
|
|
|
|
|
|
|
|
|
|
170 |
|
|
|
|
|
|
|
|||
|
|
|
|
|
|
|
|
|
|
|
|
||||||
a |
|
|
z2 |
|
|
|
T K |
|
|
|
|
||||||
|
= |
|
|
|
+1 |
3 |
|
|
|
|
|
|
= |
|
|
||
w |
|
|
|
|
|
|
H |
|
|
||||||||
|
|
|
|
|
|
z2 |
|
|
2 |
|
|
|
|||||
|
|
|
q |
|
|
[σH ] |
|
|
|
|
|
|
|||||
|
|
|
|
q |
|
|
|
|
|
||||||||
|
|
|
|
|
|
|
|
|
|
|
|
|
|
|
|
||
|
|
|
|
|
|
|
|
|
|
|
|
2 |
|
|
|
|
|
|
|
|
50 |
|
3 |
|
170 |
|
|
493,62 10 |
3 |
1,42 =174,34 мм. |
|||||
|
|
= |
+1 |
|
|
50 |
|
|
|||||||||
|
|
|
10 |
|
|
|
180 |
|
|
|
|
|
|
||||
|
|
|
|
|
|
|
|
|
|
|
|
|
|
|
|
|
|
|
|
|
|
|
|
|
|
10 |
|
|
|
|
|
||||
|
|
|
|
|
|
|
|
|
|
|
|
|
|
|
|
Определяем модуль зацепления
m = |
aw |
174,34 |
|
мм. |
|
|
= |
|
= 5,8 |
||
0,5(q + z2 ) |
0,5(10 + 50) |
По табл. 10.2 [16] подбираем наиболее близкие к расчетным значения величин q и m. Принимаем m = 6, q = 10, z1 = 2, z2 = 50, U = 50/2 = 25. Отклонение передаточного отношения от требуемого равно: ∆u = 25 −2524,9 100 = 0,4 % . Допускаемое отклонение [∆u] = (2...4) % .
Окончательно имеем:

d1 = qm =10 6 = 60 мм;
d2 = mz2 = 6 50 = 300 мм;
aw = |
d1 + d2 |
= |
60 + 300 |
=180 мм. |
|
2 |
|||
2 |
|
|
2.3 Проверим зацепление на прочность по контактным напряжениям. Используем формулу
|
|
|
|
|
|
|
z |
2 |
+1 |
3 |
|
|
|
|
|
|
170 |
|
|
|
|
|
|
||||
|
|
|
q |
|
|
|
|||||||
σ |
H |
= |
|
|
|
T K |
H |
= |
|||||
|
|
|
z2 |
|
|
|
aw |
|
2 |
|
|||
|
|
|
|
q |
|
|
|
|
|
|
|
|
|
|
|
|
|
|
|
|
|
|
|
|
|
= 17050
10
|
50 |
+ |
3 |
|
|
|
|
|
1 |
|
|
||
10 |
493,62 103 |
1,42 =173,7 МПа. |
||||
|
|
|
||||
|
180 |
|
|
|
||
|
|
|
|
|
|
|
|
|
|
|
|
|
Так как σН = 173,7 МПа < [σН] = 180 МПа, то условие прочности выполняется. Проверим скорость скольжения, для чего рассчитываем окружную скорость в зацеплении
|
v = |
πd1n1 |
|
= |
|
3,14 60 960 |
= 3,01 м/с. |
||||||||
|
|
|
|
|
|
|
|
||||||||
|
1 |
|
60 1000 |
|
|
|
|
60 1000 |
|||||||
|
v1 |
|
|
|
|
|
|||||||||
Скорость скольжения равна vск = |
|
, |
|
|
|
|
|
|
|
|
|
|
|
|
|
cos γ |
|
|
|
|
|
|
|
|
|
|
|
|
|||
|
|
|
|
|
|
|
|
|
|
|
|
|
|
||
где γ – угол подъема витков резьбы червяка: tg γ = |
|
z1 |
= |
|
2 |
; γ =11,31o . |
|||||||||
|
|
10 |
|||||||||||||
|
|
|
|
|
|
|
|
q |
|
|
|||||
|
|
|
vск = |
|
|
3,01 |
|
|
|
= 3,07 м/с. |
|||||
|
|
|
соs11,31 |
||||||||||||
|
|
|
|
|
|
|
Скорость скольжения меньше принятой ранее, поэтому поправка величины [σН] не требуется. 2.4 Рассчитаем геометрические размеры червяка и колеса.
Размеры червяка:
d1 = 60 мм ;
dα1 = d1 +2m = 60 + 2 6 = 72 мм;
d f 1 = d1 −2,4m = 60 −2,4 6 = 45,6 мм.
Длина нарезной части червяка [1]:
b1 = (11 + 0,06z2 )m = (11 + 0,06 50)6 = 84 мм.
Учитывая выход шлифовального камня, принимаем:
b1 = 84 + (25 ÷30)=110 мм.
Размеры колеса:
d2 = mz2 = 6 50 = 300 мм;
dα2 = d2 +2m = 300 +2 6 = 312 мм;
d f 1 = d 2 −2,4m = 300 −2,4 6 = 285,6 мм.
Ширина колеса bw2 ≤ 0,75dα1 = 0,75 72 = 54 мм, принимаем bw2 = 54 мм.
Наружный диаметр колеса dαм2 = |
d |
+ 6m |
|
312 + 6 6 |
= 321 мм. |
α2 |
|
= |
(2 + 2) |
||
(z |
+ 2) |
||||
|
1 |
|
|
|
|
2.5 Проверим зацепление на прочность по напряжениям изгиба (рис. 25). Действительные напряжения изгиба в зацеплении
σ = yF KF Ft 2 cos γ .
F 1,3m2q
По таблице 10.8 [11], в зависимости от эквивалентного числа зубьев zV путем интерполяции выбираем значение коэффициента формы зуба:

|
z |
|
= |
|
z2 |
|
= |
50 |
= 53 ; y |
F |
= 1,42; |
K |
= K . |
||||||
|
|
|
|
|
|
|
|
|
|||||||||||
|
V |
|
|
cos3 |
γ |
|
|
|
cos3 11,310 |
|
|
|
F |
Н |
|||||
|
|
|
|
|
|
|
|
|
|
|
|
|
|
||||||
Окружная сила на колесе |
F |
= |
T2 |
= |
49320 |
= 3291 Н. |
|
|
|
|
|||||||||
|
|
|
|
|
|
|
|||||||||||||
|
t |
|
|
d2 |
/ 2 |
|
300 / 2 |
|
|
|
|
|
|
|
|||||
|
|
|
|
|
|
|
|
|
|
|
|
||||||||
Действительные напряжения изгиба в зацеплении |
|
|
|
|
|||||||||||||||
|
|
|
σF |
= |
1,42 |
1,42 3200 cos11,31 |
=13,9 МПа. |
|
|||||||||||
|
|
|
|
|
|
||||||||||||||
|
|
|
|
|
|
|
|
|
|
|
|
1,3 62 10 |
|
|
|
|
Условие прочности выполняется: 13,9 МПа < 54,4 МПа. 2.6 Проверка зацепления на прочность при перегрузках.
• по изгибу:
[σF ]пред = 0,8σТ = 0,8 200 =160 МПа;
σF max =1,6σF =1,6 13,9 = 22,2 МПа < 160 МПа.
• по контактным напряжениям:
[σH ]пред = 2σТ = 2 200 = 400 МПа;
σH max = σH |
Tmax =173,7 1,6 = 219,7 МПа. |
|
T1 |
Условие прочности выполняется: 219,7 МПа< 400 МПа. 3 Определение кпд зацепления и выбор смазки
ηчз = |
tgγ |
= |
tg11,31 |
= 0,866 , |
′ |
tg(11,31 +1,6) |
|||
|
tg(γ + ϕ ) |
|
где ϕ′=1,6 – приведенный угол трения (табл. 10.5, [16]).
Выбираем масло с допустимой температурой t = 65 оС. 4 Расчет усилий, действующих в зацеплении (рис. 25).
Рис. 25 Схемасил, действующихвзацеплении
Окружная сила на червяке |
F |
= F |
a2 |
= |
2T1 |
= |
2 24780 |
= 826 Н. |
|
|
|||||||
|
t1 |
|
|
d1 |
60 |
|
||
|
|
|
|
|
|

Окружная сила на колесе |
F |
= F |
= |
2T2 |
= |
2 493620 |
= 3291 Н. |
|
|
||||||
|
t 2 |
a1 |
|
d 2 |
300 |
|
|
|
|
|
|
|
Радиальная сила Fr = Ft 2 tg α = 3291 0,364 =1198 Н.
5 Рассчитаем червяк на прочность и жесткость. 5.1 Построение эпюр для вала червяка (рис. 26).
|
|
|
|
|
|
|
|
|
Рис. 26 Расчетнаясхемачервяка |
||||
Принимаем |
конструктивно |
|
l |
|
|
= |
340 |
мм. |
Обычно |
a |
= |
b, |
тогда |
а = 170 мм, с = 100 мм (из условия закрепления муфты). |
|
|
|
|
|
|
|||||||
Изгибающий момент от силы Fr : |
|
|
|
|
|
|
|
|
|
|
|
||
|
M |
|
= F |
ab |
= |
1198 170 170 |
=101823 Н·мм. |
|
|
|
|
||
|
|
Fr |
r |
l |
|
|
340 |
|
|
|
|
|
|
Изгибающий момент от силы Fa1 :
|
|
|
|
|
M |
|
|
= |
F |
d f 1 a |
= |
|
3291 45,6 170 |
|
= 37517 Н·мм. |
||||||||
|
|
|
|
|
|
|
|
|
|
|
|
|
|||||||||||
|
|
|
|
|
|
|
2 l |
|
|
||||||||||||||
|
|
|
|
|
|
Fa1 |
|
a1 |
|
|
|
|
2 340 |
|
|
|
|
||||||
|
Изгибающий момент от силы Ft1 |
|
|
|
|
|
|
|
|
|
|
|
|
|
|
|
|||||||
|
|
|
|
|
|
|
M Ft1 |
= Ft1 ab |
= 826 170 170 |
= 70210 Н·мм. |
|||||||||||||
|
Изгибающий момент от силы FM |
|
|
l |
|
|
|
|
340 |
|
|
|
|
|
|||||||||
|
|
|
|
|
|
|
|
|
|
|
|
|
|
|
|
||||||||
|
|
|
|
|
|
|
|
|
|
|
|
|
|
M |
|
= F |
ca |
, |
|
|
|
||
|
|
|
2T1 |
|
2 24780 |
|
|
|
|
|
|
|
|
|
|
Fм |
M |
l |
|
|
|
|
|
где |
′ |
′ |
|
= 604,4 Н; здесь D1 = 82 мм – диаметр окружности, проходящей через |
|||||||||||||||||||
FM = 0,3FM ; |
FM = |
|
= |
|
|
||||||||||||||||||
D1 |
82 |
|
|||||||||||||||||||||
|
|
|
|
|
|
|
|
|
|
|
|
|
|
|
|
|
|
|
|
|
|
||
оси пальцев муфты на валу червяка. |
|
|
|
|
|
|
|
|
|
|
|
|
|
|
|
Н, |
|||||||
|
|
|
|
|
|
|
|
|
|
FM = 0,3 604,4 =181,3 |
|||||||||||||
|
|
|
|
|
|
M F = FМ |
с a |
= |
181,3 100 170 |
= 9065 Н·мм. |
|||||||||||||
|
|
|
|
|
|
l |
|
||||||||||||||||
|
|
|
|
|
|
|
|
|
|
|
|
|
|
|
340 |
|
|
|
|
|
Суммарный момент в сечении
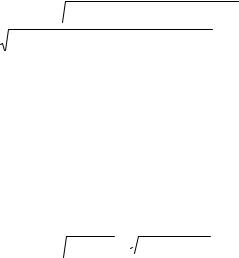
М= (МFr + МFa1 )2 + (МFt1 + МF )2 =
=(101 823 + 37517)2 + (70210 + 9065)2 =160312,7Н мм.
Изгибающие напряжения
σи = |
М |
|
= |
160312,7 |
=16,9МПа ≤[σи] = 750 МПа. |
|
0,1d |
3f 1 |
0,1 45,63 |
||||
|
|
|
Условие статической прочности выполняется с большим запасом, поэтому проверку на усталостную
прочность не делаем.
5.2 Рассчитаем червяк на прогиб. Равнодействующая, вызывающая прогиб червяка равна
R = Fr2 + Ft12 =
11982 +8262 =1455 Н.
ПРИ СИММЕТРИЧНОМ РАСПОЛОЖЕНИИ ОПОР ВЕЛИЧИНА ПРОГИБА РАВНА:
f = |
Rl3 |
≤ |
[f ]; E = 2,15 105 МПа; |
J = |
πd 4f 1 |
≈ |
0,05d 4 |
. |
|
|
64 |
||||||||
|
48EJ |
|
|
|
|
f 1 |
|
||
Допускаемый прогиб: [f ]= m(0,005K0,01)= (0,03K0,06) мм. |
|
|
|
|
|||||
|
f = |
|
1455 3403 |
= 0,025 мм; |
|
|
|||
|
|
48 2,15 103 0,05 45,64 |
|
|
Условие жесткости выполняется, так какf = 0,025мм < [ f ] = 0,03 мм. 6 Проверим редуктор на перегрев.
КОЛИЧЕСТВО ТЕПЛА, ВЫДЕЛЯЮЩЕГОСЯ ПРИ РАБОТЕ ПЕРЕДАЧИ ЗА ОДНУ CЕКУНДУ,
Q = (1 − ηчз )N1 = (1 − 0,8) 2490 = 498 Вт.
Количество тепла, отводимое корпусом за один час работы:
Q1 = KT (t1 −t0 )A ;
где Kт = 30 Вт/м2·°С – коэффициент теплопередачи, при обдуве редуктора вентилятором; t1 = 65 °C – допускаемая температура масла в редукторе; t0 = 20 °C – температура окружающей среды; А – площадь поверхности редуктора (без днища) (рис. 24).
A = 2 0,34 0,45 2 0,08 0,45 +0,08 0,34 = 0,397 м2;
Размер «м» корпуса редуктора (рис. 24) определяется из условия наполнения масла в корпус на высоту зуба червяка и объема масла из расчета 0,7 литра на 1 кВт мощности:
Q1 = 30 (65 −20) 0,397 = 540 Вт.
Так как Q1 < Q – то редуктор не перегревается.
7 Разработка сборочного чертежа редуктора [6, 7, 8]. Сборочный чертеж редуктора представлен в
прил. 19.
Пример 7. Для вала, передающего зубчатому колесу мощность P = 75 кВт при n = 300 мин–1 подобрать посадку с гарантированным натягом и проверить прочность деталей после запрессовки (рис. 27). Материал колеса и вала принять – сталь 45 (улучшенная σт = 450 МПа).
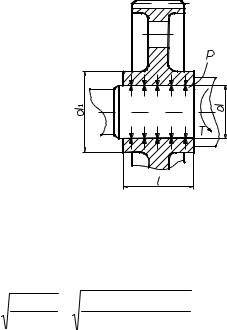
Рис. 27 Расчетнаясхемасоединенияснатягом
1 Определяем размеры соединения.
1.1 Диаметр вала
d = 3 |
30P |
30 75 103 |
м = 66,8 мм, |
πn0,2[τ] = 3 |
3,14 300 0,2 4 107 = 0,0668 |
где [τ]= 40 МПа – допускаемые напряжения кручения [1]. Используя ряд предпочтительных чисел, принимаем d = 70 мм. 1.2 Диаметр ступицы колеса [7]:
d1 =1,5 d +10 =1,5 70 +10 =115 мм. 1.3 Длину ступицы колеса [7] l =1,5 d =1,5 70 =105 мм;
2 Определим удельное давление в соединении, необходимое для передачи заданного вращающего момента
p = |
P 30 10 |
6 2 |
= |
75 30 106 2 |
|
= 29,55 МПа; |
π2 n d 2 |
|
3,14 300 702 105 0,1 |
||||
|
l f |
|
здесь f = 0,1 – коэффициент трения на поверхности соединения после сборки. 3 Определяем расчетный натяг по формуле Ляме:
C |
|
C |
2 |
|
|
3 |
|
0,7 |
2,48 |
|
|
3 |
|
мкм, |
||
|
1 |
|
|
|
|
|
|
|
|
|
|
|
||||
N = p d |
E |
+ |
E |
2 |
|
10 |
|
= 29,55 70 |
2,1 105 |
+ 2,1 105 |
|
10 |
|
= 31,3 |
||
|
1 |
|
|
|
|
|
|
|
|
|
|
|
|
|
|
где E1 = E2 = 2,1·105 МПа– модуль упругости для материала колеса и вала; С1 и С2 – коэффициенты, определяемые по формулам:
C1 =1−µ =1−0,3 = 0,7 ; |
|
d 2 |
+ d 2 |
|
1152 |
+ 702 |
+ 0,3 = 2,48 ; |
|
C2 = |
1 |
|
+ µ = |
1152 |
−702 |
|||
d12 |
− d 2 |
|||||||
|
|
|
|
здесь µ = 0,3 – коэффициент Пуассона для стальных деталей. 4 Определяем минимальный табличный натяг
Nmin = N + (Rz1 + Rz2 ) 1,2 = 31,3 +1,2(6,3 +10) = 50,86 мкм;
здесь Rz1 и Rz2 – максимальные высоты микронеровностей для поверхности вала и ступицы соответственно.
5 Выбираем посадку Ø70 H7u7 , схема полей допусков для которой показана на рис. 28. Тогда Nmin =
102 – 30 = 72 мкм > 50,86 мкм
6 Проверим прочность ступицы после сборки.

Рис. 28 Схема полей допусков вала и отверстия для посадки Ø70 H7u7
6.1 Рассчитаем давление в соединении при максимальном натяге:
pmax = |
Nmax −1,2(Rz1 + Rz2 ) |
= |
|
|
132 −19,6 |
|
|
=106 МПа. |
|||||||||
|
|
|
0,7 + 2,48 |
|
|
|
|||||||||||
|
C |
|
C |
2 |
|
|
3 |
|
|
|
3 |
|
|||||
|
|
1 |
+ |
|
|
10 |
|
70 |
|
|
|
|
10 |
|
|||
|
d |
E1 |
E2 |
|
|
|
|
2,1 10 |
5 |
|
|
|
|||||
|
|
|
|
|
|
|
|
|
|
|
|
|
|
6.2 Определим допускаемое давление в соединении:
|
d 2 |
− d 2 |
|
1152 −702 |
=142 МПа. |
[ p] ≤ σт |
1 |
|
= 450 |
2 1152 |
|
2d 2 |
|||||
|
|
1 |
|
|
|
Прочность ступицы колеса обеспечена, так как 106 МПа < 142 МПа. Также обеспечена и прочность вала при сплошном поперечном сечении [1].
Пример 8. По данным примера 7 рассчитать соединение зубчатого колеса с валом по двум вариантам:
1)призматической шпонкой;
2)прямобочными шлицами (зубьями). 1 Определим размеры соединений.
1)Поперечное сечение шпонки по ГОСТ 10748–79 ([7], прил. 14) – b = 20 мм, h = 18 мм, длину из
условия размещения внутри ступицы – lp = l −b −5 =105 − 20 −5 = 80 мм.
2) По ГОСТ 1139–80 ([7], прил. 15) выбираем легкую серию с центрированием по внутреннему диаметру – d −10 ×72 H7f7 ×78 ×12 F8f8 ; длину соединения – lp = l =105 мм.
2 Проверим работоспособность соединений.
1) На прочность по напряжениям смятия:
σсм = |
4Т |
= |
4P 30 |
= |
4 75 106 30 |
= 85,3 МПа. |
d hlp |
|
3,14 300 70 20 80 |
||||
|
|
πnd hlp |
|
Допускаемые напряжения [1] для шпонки из углеродистой стали и переходной посадки [σсм]=100 МПа, что больше чем σсм = 85,3 МПа, следовательно, условие прочности выполняется.
2) По обобщенному критерию работоспособности [1]
σсм = |
|
2Т |
= |
2P 30 |
|
= |
||
K z hdср lp |
πn K z hd |
|
|
|||||
|
|
|
ср lp |
|||||
= |
|
2 |
75 106 30 |
|
= 27 МПа, |
|||
3,14 300 |
0,75 10 3 75 105 |
|
где K = 0,75 – коэффициент неравномерности; z = 10 – число зубьев (шлиц); h = 0,5(D – d) = 0,5(78 – 72)
=3 мм – рабочая высота зубьев (шлиц); D = 78 мм – наружный диаметр шлицевого вала; dср = 0,5(D + d) =
=0,5(78 + 72) = 75 мм – средний диаметр шлицевого вала.
Допускаемые напряжения [1] для неподвижного соединения в средних условиях эксплуатации [σсм]= 60 МПа, что больше чем σсм = 27 МПа, следовательно, условие прочности выполняется.
Пример 9. Определить размеры лобового и фланговых швов сварного соединения (рис. 29). Соединение выполнено внахлестку сплошным нормальным швом: толщина накладки δ1, больше толщины полки уголка δ2. Материал свариваемых деталей сталь Ст3. Электрод Э42. Соединение должно быть равнопрочно основному материалу. Сварка ручная электродуговая.
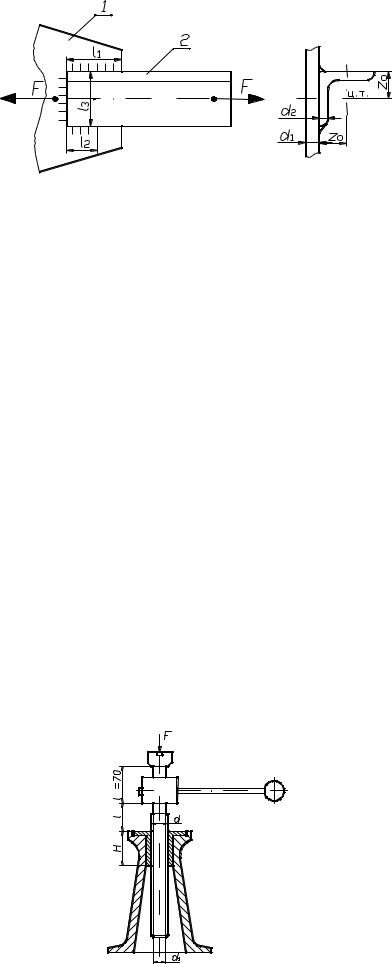
Рис. 29 Сварноенахлесточноесоединение
1 – накладка; 2 – уголок
1 Допустимую величину передаваемого усилия Р определим по условию прочности углового профиля на растяжение
σр = F A ≤ [σр],
где F – растягивающее усилие, А – площадь поперечного сечения уголка, [σр] – допускаемое напряже-
ние растяжения.
Свариваемые детали выполнены из стали Ст3 (прил. 5), для которой σт = 220 МПа, тогда [σр] = σт/n = 220/1,46 = 150 МПа, где n = (1,4 … 1,6) – запас прочности при расчете деталей на растяжение [1]. Площадь поперечного сечения уголка 160×160×12 находим по сортаменту [4] S = 3740 мм2. Тогда допускаемая величина передаваемого усилия
F = A[σр]= 3740 150 = 561000 Н. 2 Рассчитаем суммарную длину швов в соединении
(l |
+ l |
2 |
+ l |
3 |
)= |
F |
= |
561000 |
= 750 мм, |
|
|
||||||||
1 |
|
|
|
0,7k[τ′ср] |
|
0,7 12 90 |
|||
|
|
|
|
|
|
|
где [τ′ср] = 0,6[σр] = 0,6 150 = 90 МПа – допускаемые напряжения среза в сварных швах; k ≤ 12 мм – катет
сварного шва.
3 Определим длины фланговых швов, при zo = 43,9 мм. Суммарная длина фланговых швов, при l3 = 160 мм: (l1 + l2) = 750 – 160 =590 мм. Из условия равнопрочности швов:
l1 |
= |
l3 − z0 |
= |
160 − 43,9 |
= 2,64 . |
|
l2 |
z0 |
43,9 |
||||
|
|
|
Тогда l1 = 590 – l2 = 590 – 0,378 l1; l1 = 428 мм; l2 = 162 мм.
Пример 10. Рассчитать винт домкрата грузоподъемностью F = 32 кН (рис. 30). Максимальная высота подъема груза l = 600 мм. Коэффициент трения в резьбе (сталь-бронза) f = 0,15.