
Воробьев Ю.В. Учебно-методическое пособие по деталям машин
.pdf
Таблица 10
|
Величи- |
|
|
|
|
Варианты |
|
|
|
|
||
|
на |
1 |
2 |
3 |
4 |
5 |
6 |
7 |
8 |
9 |
10 |
|
|
|
а |
2 |
2,1 |
2,2 |
2,3 |
2,4 |
2,5 |
2,6 |
2,7 |
2,8 |
2,9 |
|
Ft, кН |
б |
3 |
3,1 |
3,2 |
3,3 |
3,4 |
3,5 |
3,6 |
3,7 |
3,8 |
3,9 |
|
|
в |
4 |
4,1 |
4,2 |
4,3 |
4,4 |
4,5 |
4,6 |
4,7 |
4,8 |
4,9 |
|
|
|
|
|
|
|
|
|
|
|
|
|
|
v, м/с |
0,5 |
0,55 |
0,6 |
0,65 |
0,7 |
0,75 |
0,8 |
0,85 |
0,9 |
1 |
|
|
t, мм |
160 |
160 |
160 |
125 |
125 |
125 |
125 |
100 |
100 |
100 |
|
|
z |
8 |
8 |
9 |
9 |
10 |
10 |
11 |
11 |
12 |
12 |
Задание 10. Спроектировать привод к винтовому толкателю по схеме (рис. 15) с графиком нагрузки, данным на рисунке. Мощность на ведомом валу редуктора Р3 и угловые скорости вращения этого вала: максимальная (при холостом ходе винта) ω3max и минимальная (при рабочем ходе винта) ω3min приведены в табл. 11.
ПРЕДСТАВИТЬ РАСЧЕТНО-ПОЯСНИТЕЛЬНУЮ ЗАПИСКУ С ПОЛНЫМ РАСЧЕТОМ ПРИВОДА И ЧЕТЫРЕ, ЛИСТА ЧЕРТЕЖЕЙ (ФОРМАТА A1): 1) ОБЩЕГО ВИДА ПРИВОДА; 2)МУФТЫ; 3) КОРОБКИ СКОРОСТЕЙ; 4) РАБОЧИХ ЧЕРТЕЖЕЙ ДЕТАЛЕЙ КОРОБКИ СКОРОСТЕЙ – КРЫШКИ КОРПУСА, ЗУБЧАТОГО КОЛЕСА БЫСТРОХОДНОЙ ПЕРЕДАЧИ И ЕГО ВАЛА.
Рис. 15 Схема привода и график нагрузки
Таблица 11
|
Величина |
|
|
|
|
Варианты |
|
|
|
|
|||
|
|
|
|
|
|
|
|
|
|
|
|
||
|
1 |
2 |
3 |
4 |
5 |
6 |
|
7 |
8 |
9 |
10 |
||
|
|
а |
5 |
6 |
7 |
5 |
6 |
7 |
|
5 |
6 |
7 |
5 |
|
Рз, кВт |
б |
8 |
9 |
10 |
8 |
9 |
10 |
|
8 |
9 |
10 |
8 |
|
|
в |
11 |
12 |
13 |
11 |
12 |
13 |
|
11 |
12 |
13 |
11 |
|
|
|
|
|
|
|
|
|
|
|
|
|
|
|
ω3max, рад/с |
2π |
2,1 |
2,2 |
2,3 |
2,4 |
2,5 |
|
2,6 |
2,7 |
2,8 |
2,9 |
|
|
|
|
|
π |
π |
π |
π |
π |
|
π |
π |
π |
π |
|
ω3min, рад/с |
0,8 |
0,8 |
0,9 |
0,9 |
π |
π |
|
1,1 |
1,1 |
1,2 |
1,2 |
|
|
|
|
π |
π |
π |
π |
|
|
|
π |
π |
π |
π |
Задание 11. Спроектировать привод к цепному конвейеру по схеме (рис. 16) и графику нагрузки,

данным на рисунке. Полезное окружное усилие на звездочке Ft , скорость цепи vmax и vmin шаг цепи t, число зубьев тяговой звездочки z приведены в табл. 12. Срок службы – 4 года, Kсут = 0,3, Kгод = 0,9. Половину срока службы транспортер работает с максимальной скоростью.
Представить расчетно-пояснительную записку с полным расчетом привода и четыре листа чертежей (формат А1): 1) общего вида привода; 2) муфты; 3) вариатора; 4) рабочих чертежей деталей вариатора.
Рис. 16 Схема привода и график нагрузки
Таблица 12
|
Ве- |
|
|
|
|
|
|
|
|
|
|
|
|
|
Варианты |
|
|
|
|
|
|
|
|
|
|
||||||
|
личина |
|
|
|
|
|
|
|
|
|
|
|
|
|
|
|
|
|
|
|
|
|
|
|
|
|
|
|
|
||
|
1 |
|
2 |
|
3 |
|
4 |
|
5 |
|
6 |
|
7 |
|
8 |
|
9 |
|
10 |
||||||||||||
|
|
|
|
|
|
|
|
|
|
|
|
|
|
|
|
|
|
|
|
|
|
|
|
|
|
|
|
|
|
|
|
|
Ft, |
|
а |
2,6 |
3,0 |
2,0 |
1,8 |
2,2 |
5,2 |
4,0 |
6,0 |
4,2 |
|
3,1 |
|||||||||||||||||
|
к |
|
б |
3,2 |
3,3 |
3,4 |
3,5 |
3,6 |
3,7 |
3,8 |
3,9 |
4,3 |
|
4,4 |
|||||||||||||||||
|
Н |
|
в |
2,3 |
2,4 |
2,5 |
2,7 |
2,8 |
2,9 |
1,6 |
1,7 |
1,9 |
|
2,0 |
|||||||||||||||||
|
vmax |
/vm |
0,3 |
0,5 |
0,4 |
|
0,3 |
|
|
0,5 |
|
|
0,6 |
|
|
1,0 |
|
|
0,9 |
|
|
0,6 |
|
0,45 |
|||||||
|
in,м/с |
0,1 |
|
0,2 |
0,2 |
|
0,1 |
|
0,2 |
|
0,2 |
|
0,4 |
|
0,3 |
|
0,2 |
|
0,15 |
||||||||||||
|
t, мм |
100 |
160 |
125 |
100 |
160 |
125 |
100 |
160 |
125 |
100 |
||||||||||||||||||||
|
z |
|
8 |
|
9 |
|
10 |
|
11 |
|
12 |
|
11 |
|
10 |
|
9 |
|
8 |
|
10 |
3 ПРИМЕРЫ РАСЧЕТОВ
ПРИМЕР 1. ОПРЕДЕЛИТЬ РАЗМЕРЫ КОСОЗУБОЙ ЦИЛИНДРИЧЕСКОЙ ПАРЫ В РЕДУКТОРЕ ДЛЯ ПРИВОДА ЦЕПНОГО КОНВЕЙЕРА. СХЕМА ПРИВОДА И ГРАФИК ЕГО НАГРУЗКИ ПОКАЗАНЫ НА РИС. 17.
Дано:
Ft = 1200 Н – окружное усилие на звездочке;
Dзв = 300 мм – диаметр делительной окружности звездочки; v = 2,5 м/с – скорость груза;
срок службы – 10 лет; работа по 7 ч. в сутки.

Рис. 17 Схема привода и график его нагрузки
1 Определение исходных данных
1.1 Определяем мощность на звездочках, необходимую для перемещения груза на цепном конвейере,
Pзв = 2Ft v = 2 1200 2,5 = 6 кВт. 1000 1000
1.2 Находим величину потерь в кинематической цепи привода [1 – 3]
η = η3пηм2 ηзηзв = 0,983 0,992 0,98 0,96 = 0,868 ,
где ηп – кпд пары подшипников; ηм – кпд муфты; ηз – кпд зубчатого зацепления; ηзв – кпд звездочки.
1.3Рассчитаем мощность электродвигателя, необходимую для перемещения груза
P = Pηзв = 0,8686 = 6,91 кВт.
1.4Подбираем электродвигатель по прил. 7 и 8.
Типоразмер 4А160S8УЗ. Мощность Рдв = 7,5 кВт. Частота вращения nдв = n1 = 735 мин–1 (с учетом скольжения S = 2,5 %, при синхронной частоте вращения 750 об/мин).
Характеристика двигателя:
•пусковая Тп/Тн = 1,4 (соответствует графику нагрузки);
•перегрузочная Тmax/Тн = 2,2.
1.5Рассчитаем передаточное число привода
u = i = |
n1 |
= |
n1 |
|
= |
|
735 |
|
= 4,62. |
|
v 60 1000 |
|
2,5 |
60 1000 |
|
||||
|
nзв |
|
|
|
|
||||
|
|
|
πDзв |
|
|
3,14 300 |
|
|
2 Расчет косозубой цилиндрической пары (в соответствии c ГОСТ 21354–87).
2.1 Выбор материалов для колес (прил. 5, [1], [3]).
Выбираем сравнительно недорогой и широко применяемый материал. Для шестерни принимаем более прочную сталь. Свойства сталей сводим в табл. 13.
Таблица 13
|
Свойства материа- |
Звенья передачи |
|
|
лов |
шестерня [1] |
колесо [3] |
|
|
|
|
|
Марка стали |
Сталь 45 |
Сталь 35 |
|
|
|
|
|
Термообработка |
Улучшение |
Нормализация |
|
|
|
|
|
Предел прочности |
σв1 = 850 |
σв2 = 550 МПа |
|
МПа |
||
|
|
|
|
|
Предел текучести |
σт1 = 580 |
σт2 = 270 МПа |
|
МПа |
||
|
|
|
|
|
Твердость сердце- |
241 … 285 |
173 … 187 НВ |
|
вины |
НВ |
|
|
|

2.2 Определяем допускаемые контактные напряжения [1] по формуле
[σH ]= σH limb KHL ,
SH
где σНlimb = σН0 = 2 HB + 70:
•для шестерни
HB1 = 241 + 285 = 263 HB и σН01 = 2 НВ1 + 70 = 2 263 + 70 = 596 МПа;
2
•для колеса
|
2 |
= |
173 + |
187 |
=180 HB и σН02 = 2 НВ2 + 70 = 2 180 + 70 = 430 МПа. |
HB |
|||||
|
|
|
2 |
|
|
Коэффициент безопасности SH = 1,1 (для нормализованных и улучшенных колес); коэффициент долговечности KHL определим в зависимости от эквивалентного числа циклов нагружений NHE (расчет по колесу – тихоходному звену, с наименьшим числом нагружений зуба).
|
|
|
|
|
|
Ti |
3 |
|
|
|
|
|
|
|
|
NHE = 60c∑ |
niti = |
|
|
|
|
||||
|
|
|
T |
|
|
|
|
|||||
|
|
|
|
|
|
H |
|
|
|
|
|
|
|
|
|
|
= 60 1 (13 159 |
12400 + 0,73 159 9300)=14,9 107 >1 107 |
= NH 0 , |
|
|||||
|
|
n1 |
|
735 |
|
|
|
–1 |
|
|
|
|
где |
( ni = n2 = |
|
= |
|
=159 |
|
|
мин ) |
– |
частота |
вращения |
колеса; |
u |
4,62 |
|
|
ti = t1 = 4 310 10 = 12 400 – время работы колеса за срок службы в режиме номинальной нагрузки при 310 днях работы в году; ti = t2 = = 3 310 10 = 9300 – время работы колеса в часах за срок службы в режиме неполной нагрузки; NН0 – базовое число циклов нагружений, так как NHE > NН0, то коэффициент долговечности KHL = 1.
Тогда допускаемые напряжения:
• для шестерни
[σH1 ]= |
σH 01 KHL = |
596 |
1 = 542 МПа; |
|||||||||
|
|
|
SH |
|
|
|
|
1,1 |
|
|
|
|
• для колеса |
|
|
σH 02 KHL = |
430 |
|
|
|
|
||||
[σH 2 ]= |
|
1 = 391 МПа; |
||||||||||
|
|
|
SH |
|
|
|
|
1,1 |
|
|
|
|
• для зубчатой передачи |
[σ |
|
]+[σ |
|
] |
|
|
|
|
|
|
|
[σH ]= |
H 1 |
H 2 |
= |
542 +391 |
= 466,5 МПа. |
|||||||
|
|
2 |
|
|
|
2 |
|
|
||||
|
|
|
|
|
|
|
|
|
|
Проверим опасность перегрузки [1] слабого звена по условию
[σH] = 466,5 МПа ≤ 1,25 391 = 488,8 МПа.
Перегрузки колеса нет.
2.3 Определим [1] допускаемые напряжения изгиба, используя формулу
[σF ]= σSF 0 KFS KFL ,
F
• для шестерни
σF 01 =1,8 HB1 =1,8 263 = 473,4 МПа;
• для колеса
σF 02 =1,8 HB2 =1,8 180 = 324 МПа.
Коэффициент безопасности SF = 1,75, коэффициент, учитывающий влияние двустороннего приложения нагрузки KFS =1 (передача нереверсивная), коэффициент долговечности KFL = 1, так как NFE > NF0 = 4 106.
• для шестерни |
[σF1 ]= |
σF 01 KFS KFL = |
473,4 |
1 1 = 271 МПа; |
|
|
SF |
1,75 |
|

• для колеса |
[σF 2 ]= |
σF 02 |
KFS KFL = |
324 |
1 1 =185 МПа. |
|
|
SF |
|
1,75 |
|
2.4 Определяем [1] допускаемые напряжения при перегрузках:
• для колеса по контактным напряжениям
[σH ]max 2 = 2,8σт2 = 2,8 270 = 756 МПа;
• для шестерни и колеса по изгибающим напряжениям:
[σF ]max1 = 0,8σт1 = 0,8 580 = 464 МПа; [σF ]max 2 = 0,8σт2 = 0,8 270 = 216 МПа.
2.5 Определяем вращающие моменты на колесе и на шестерне:
•вращающий момент на колесе
T2 = |
P2 |
= |
6000 30 |
= |
6000 30 |
|
=395 Н м; |
|
|
0,982 0,99 0,96 3,14 159 |
|||||
|
ω2 |
ηп2ηмηзвπn2 |
|
•вращающий момент на шестерне
T = |
T2 |
= |
395 |
=87,2 Н м. |
|
4,62 0,98 |
|||
1 |
uηз |
|
2.6 Определяем диаметр шестерни [1]
T1KHβ |
u +1 |
|
87,2 1,04 4,62+1 |
=54,5 мм, |
d1 = Kd 3 ψbd [σH ]2 |
u |
=680 3 |
1 466,52 4,62 |
где Kd = 680 (МПа)1/3, ψbd = 1, KHβ = 1,04 [1].
Предварительно принимаем d1 = 56 мм.
2.7 Рассчитываем геометрические параметры колес:
•рабочая ширина колеса bω = ψbd d1 = 1 56 = 56 мм;
•торцевой модуль mt = bω /ψm = 56/30 = 1,86 мм, где ψm = 30 [1].
По ГОСТ 9563–80 [1] принимаем mn = 2 мм.
Угол наклона зубьев найдем из условия обеспечения плавности:
sinβ = εβπmn = 2 3,14 2 = 0,2243 , bω 56
где εβ = 2 – коэффициент осевого перекрытия [1]; β = 12°57′, что находится в рекомендуемых пределах
(β = 12 … 20°).
Принимаем фаски на торцевых поверхностях зубьев по 0,1 мм, тогда
sin β = |
2 3,14 2 |
= 0,2252 ; β = 13°1′. |
||||||||||||||
|
|
|
|
|
||||||||||||
|
|
55,8 |
|
|
|
|
|
|
|
|
|
|
|
|||
Уточняем величину торцевого модуля |
|
|
|
|
|
|
|
|
|
|
|
|
|
|||
mt = |
mn |
|
= |
|
|
|
|
2 |
|
|
= 2,0527 |
мм. |
||||
cos β |
|
|
|
cos 13o1′ |
||||||||||||
|
|
|
|
|
|
|
|
|
|
|||||||
Число зубьев шестерни |
|
d1 |
|
|
|
|
|
56 |
|
|
|
|
|
|||
|
|
z1 = |
|
= |
|
|
|
= 27,3 . |
|
|||||||
Принимаем z1 = 27 > zmin = 17. |
|
|
2,0527 |
|
||||||||||||
|
|
mt |
|
|
|
|
|
|
|
|||||||
|
|
|
|
|
|
|
|
|
|
|
|
|
|
|
||
Тогда число зубьев колеса z2 = z1u = 27 4,62 125. |
|
|
|
|
||||||||||||
Уточняем размеры диаметров делительных окружностей |
|
|||||||||||||||
d1 = mt z1 = 2,0527 27 = 55,42 мм, |
|
d2 = mt z2 = 2,0527 125 = 256,58 мм. |
||||||||||||||
и межосевого расстояния |
|
|
|
|
|
|
|
|
|
|
|
|
|
|
|
|
aω = |
d1 + d2 |
= |
55,42 + 256,58 |
=156 мм. |
||||||||||||
|
|
|||||||||||||||
|
|
2 |
|
|
|
|
|
|
|
|
2 |
|
|
|
|
|
Принимаем аω = 156 мм и определяем окончательно геометрические параметры:
• шестерни
dω1 = d1 = 55,42 мм,
da1 = d1 +2mn = 55,42 +2 2 = 59,42 мм,

d f 1 = d1 −2,5mn = 55,42 −2,5 2 = 50,42 мм, bω1 = bω + 4 = 56 + 4 = 60 мм;
• колеса
d2 = dω2 = 256,58 мм,
da2 = d2 +2mn = 256,58 +2 2 = 260,58 мм,
d f 2 = d2 −2,5mn = 256,58 −2,5 2 = 251,58 мм,
bω2 = 56 мм.
2.8 Проверим зубчатую передачу на выносливость от действия контактных напряжений.
Уточним величину коэффициента динамической нагрузки [1]. Для этого рассчитываем окружную скорость в зацеплении
|
|
|
v = |
πd1n1 |
= |
3,14 55,42 735 = 2,13 м/с |
|
||||||
|
|
|
60 1000 |
|
|||||||||
|
|
|
|
|
|
|
60 1000 |
|
|
||||
и назначаем 8-ю степень точности [1]. Тогда коэффициент динамической нагрузки KHV = 1,2. |
|||||||||||||
Окружное усилие в зацеплении |
|
|
|
|
|
|
2 87,2 103 |
|
|
||||
|
|
|
|
|
2T |
|
|
|
= 3147 Н. |
|
|||
|
|
|
|
F = |
1 |
|
= |
|
|
|
|
||
|
|
|
|
|
|
|
|
|
|
||||
|
|
|
|
t |
d1 |
|
|
55,42 |
|
|
|
||
Удельная расчетная окружная сила |
|
|
|
|
|
|
|||||||
|
|
|
|
|
|
|
|
|
|||||
ωHt = |
Ft |
|
K HβK HV K Hα = 3147 1,04 1,2 1,06 = 74,2 |
Н/мм, |
|||||||||
b |
|||||||||||||
|
|
|
|
|
|
56 |
|
|
|
||||
|
ω |
|
|
|
|
|
|
|
|
|
|
где KHα = 1,06 табл. 8.7 [2, с. 184].
Определим [2] величину действующих нормальных контактных напряжений
σH = zH zM zε |
ωHt |
u +1 |
= |
|
|
|
d1 |
u |
|
|
|
||
|
|
|
|
|
||
=1,72 271 0,77 |
74,2 |
|
4,62 +1 |
= 458 МПа<[σH ]= 466,5 МПа, |
||
|
|
55,42 |
|
4,62 |
|
где zH, zM, zε – коэффициенты, учитывающие геометрию, механические свойства и перекрытие зубьев, соответственно:
zH = |
2cos |
2 |
β/ sin 2α = |
2cos |
2 |
|
o ′ |
|
|
|
|
|
o |
=1,72 , |
|
|
|
|
|
|
||||
|
|
13 1 / sin 40 |
|
|
|
|
|
|
|
|||||||||||||||
zM = |
E |
|
|
|
|
2,1 105 |
|
|
|
|
|
|
|
Н/мм, |
|
|
|
|
|
|
||||
[π(1−µ2 )]= |
|
3,14 (1−0,32 )= 271 |
|
|
|
|
|
|
||||||||||||||||
zε = |
1 = |
1 |
= |
0,77. |
|
|
|
|
|
|
|
|
|
|
|
|
|
|
|
|
|
|||
|
εα |
|
1,69 |
|
|
|
|
|
|
|
|
|
|
|
|
|
|
|
|
|
|
|
|
|
Коэффициент торцевого перекрытия εα определим по формуле |
||||||||||||||||||||||||
|
|
|
|
|
|
|
|
|
|
|
|
|
|
|
|
|
|
|
|
|
|
|
|
|
|
|
|
|
|
|
|
|
|
|
|
1 |
|
1 |
|
|
|
|
|
|
1 |
|
1 |
||
|
|
|
|
ε |
|
= 1,88−3,2 |
|
+ |
|
|
|
|
|
−3,2 |
|
|
+ |
|
0,97437=1,69. |
|||||
|
|
|
|
|
α |
|
|
|
|
z |
|
z |
2 |
|
|
|
|
|
|
27 |
|
125 |
||
|
|
|
|
|
|
|
|
|
1 |
|
|
|
|
|
|
|
|
|
|
|
|
|||
|
|
|
|
|
|
|
|
|
|
|
|
|
|
|
|
|
|
|
|
|
|
|
|
|
Так как действующие напряжения не превышают допустимые, тоусловие прочности по контактной усталости можно считать выполненным.
2.9 ПРОИЗВЕДЕМ ПРОВЕРОЧНЫЙ РАСЧЕТ ЗАЦЕПЛЕНИЯ ПО НАПРЯЖЕНИЯМ ИЗГИБА [2]. ИСПОЛЬЗУЕМ ФОРМУЛУ
σF = YF YεYβ ωFt , mn
где YF, Yε, Yβ – коэффициенты, учитывающие форму, перекрытие и наклон зубьев соответственно. Предварительно определим величины параметров, входящих в эту формулу.
Эквивалентное число зубьев: |
|
|
|
|||||
• шестерни zv1 = |
z1 |
|
= |
27 |
= |
27 |
= 29 ; |
|
cos3 |
β |
cos3 13o1′ |
0,925 |
|||||
|
|
|
|

• колеса zv2 = cosz23 β = cos1253 13o1′ = 0125,925 ≈135 .
По графику [2, рис. 12.23] YF1 = 3,81; YF2 = 3,6.
Определим слабое звено, по которому следует проверить прочность зуба. Рассчитаем отношение
[σF]/YF: |
[σF1 ] |
|
271 |
|
|
|
• для шестерни |
= |
= 71,5 |
МПа; |
|||
|
Y |
|
|
3,81 |
|
|
|
F1 |
|
|
|
|
|
• для колеса |
[σF 2 |
] |
= |
185 = 51,5 |
МПа. |
|
|
Y |
|
|
3,6 |
|
|
|
F 2 |
|
|
|
|
|
Меньшая величина отношения у колеса, поэтому проверку производим для зуба колеса. Коэффициент, учитывающий перекрытие зубьев Yε =1 [2].
Коэффициент, учитывающий наклон зубьев Yβ =1−140β o = 0,91.
Удельная расчетная окружная сила
|
ωFt = |
Ft |
K FαK FβK Fυ |
= 3147 1,22 1,1 1,06 = 80,5 Н/мм, |
||||
|
|
|||||||
|
|
|
b |
|
|
|
56 |
|
|
|
|
ω |
|
|
|
|
|
где KFα – коэффициент распределения нагрузки между зубьями; |
KFβ – коэффициент неравномер- |
|||||||
ности распределения нагрузки по ширине колеса; KFυ – коэффициент динамической нагрузки (KFα = |
||||||||
1,22) |
[2, с. 184]; KFβ = 1,1 [2, с. 186]; KFυ = 1,06 [2, с. 195]). |
|
||||||
|
σ |
|
|
=Y |
Y Y ωFt |
= 3,6 1 0,91 80,5 =131,8 |
МПа; |
|
|
|
F 2 |
|
F 2 |
ε β mn |
2 |
|
|
|
|
|
|
|
σF 2 =131,8 |
МПа < [σF 2 ]=185 МПа. |
|
Условие прочности по напряжениям изгиба выполняется.
2.10 Проверим прочность зубьев при перегрузках:
• по контактным напряжениям
σ |
H max |
=σ |
H |
Tmax = 458 1,4 =542 МПа<[σ |
] |
=756 МПа. |
|
|
TH |
H max |
|
||
|
|
|
|
|
|
СТАТИЧЕСКАЯ ПРОЧНОСТЬ ЗУБА КОЛЕСА ПО КОНТАКТНЫМ НАПРЯЖЕНИЯМ ПРИ ПЕРЕГРУЗКАХ ОБЕСПЕЧЕНА;
• по напряжениям изгиба
σ |
F max |
= σ |
F 2 |
Tmax |
=131,8 1,4 =184,5 |
МПа < [σ |
] = 216 МПа. |
|
|||||||
|
|
T |
|
F max |
|||
|
|
|
|
H |
|
|
Статическая прочность зуба колеса по напряжениям изгиба при перегрузках обеспечена.
Пример 2. Подобрать подшипники качения для быстроходного вала в одноступенчатом цилиндрическом редукторе. Вал соединяется с электродвигателем 4А1608У3 упругой втулочно-пальцевой муфтой (муфта 500-42-45-1-У3 – ГОСТ 21424–75). Передаваемый вращающий момент Т = 87,4 Н м. Диаметр делительной окружности шестерни d1= 55,42 мм, угол наклона зубьев β = 13°1′, l = 124 мм, l1 = 100 мм, lм = lэ = 100 мм, здесь dэ и lэ диаметр и длина вала электродвигателя под полумуфтой, соответственно [4], (диаметр полумуфты под вал двигателя dм1 = dэ = 42 мм, а под вал редуктора dм2 = 45 мм в соответствии с обозначением принятой муфты). Размеры вала определены после эскизной компоновки (рис. 18).
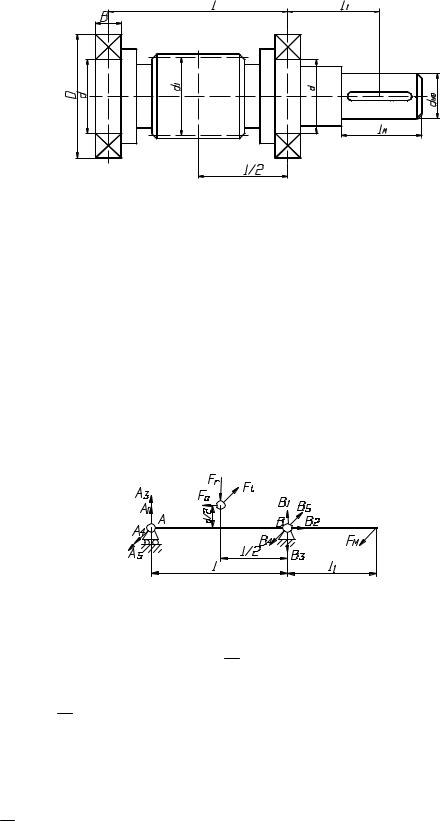
Рис. 18 Эскиз вала с шестерней и подшипниками
1 ОПРЕДЕЛЕНИЕ УСИЛИЙ, ДЕЙСТВУЮЩИХ НА ВАЛ.
1.1 |
Окружное усилие на шестерне F |
= |
2T1 |
= |
|
2 87,4 |
|
= 3154 H. |
|||||||||
|
|
|
|
|
|
|
|||||||||||
|
|
|
|
|
|
t |
|
|
|
d1 |
0,05542 |
|
|
||||
1.2 |
|
|
|
|
|
|
|
|
|
H. |
|||||||
Осевая сила в зацеплении Fa = Ft tgβ = 3154 tg13 1 = 729 |
|||||||||||||||||
|
|
|
|
|
|
|
|
|
|
|
|
o |
′ |
|
|
||
1.3 |
Радиальная сила F |
= F |
tgα |
= 3154 |
tg20o |
|
= |
1178 |
H. |
|
|
||||||
|
cos13o1′ |
|
|
||||||||||||||
|
r |
t cosβ |
|
|
|
|
|
|
|
|
|
|
|
|
|||
1.4 |
Неуравновешенная сила от муфты |
|
|
|
|
|
|
|
|
|
|
|
|||||
|
|
|
F |
|
= (0,2 ... 0,5) |
2T1 |
= |
T1 |
|
= |
87,4 |
|
= 624 H. |
||||
|
|
|
|
|
|
|
|
|
|||||||||
|
|
|
м |
|
|
D0 |
|
|
D0 |
0,140 |
|
||||||
|
|
|
|
|
|
|
|
|
|
Здесь D0 – диаметр окружности, проходящей через оси пальцев муфты [6] (определяется приближенно). 2 ОПРЕДЕЛЕНИЕ ОПОРНЫХ РЕАКЦИЙ.
Расчетная схема вала показана на рис. 19.
Рис. 19 Расчетная схема вала
2.1 Опорные реакции от силы Fr
A1 = B1 = F2r = 11782 = 589 H.
2.2 От осевой силы Fa = B2 = 729 H.
2.3 От момента Fa d1
2
A = −B |
= F |
d1 |
|
= 729 |
0,05542 |
=163 H. |
|
|
2 0,124 |
||||||
3 |
3 |
a 2 1 |
|
|
При реверсе силы А3 и В3 изменяют направление. 2.4 От силы Ft
A4 = B4 = F2t = 31542 =1577 H.
2.5 От силы Fм
A |
= F |
l1 |
= 624 |
0,1 |
= 503 |
H; |
||||
l |
0,124 |
|||||||||
|
5 |
м |
|
|
|
|
||||
B |
|
= F |
l1 |
+l |
= 624 |
0,1+0,124 |
=1127 H. |
|||
|
|
l |
|
|||||||
|
5 |
м |
|
|
|
|
0,124 |
|
2.6 Суммарные реакции в опорах (с учетом реверса)

A = (A1 + A3 )2 + A42 + A5 =
(589+163)2 +11572 +503= 2250 H;
B = (B1 +B3 )2 +B42 +B5 =
(589+163)2 +11572 +1127= 2874 H.
3 ПОДБОР ПОДШИПНИКОВ.
3.1 Дополним исходные данные.
Срок службы в часах (ресурс) при односменной работе [5] для редукторов Lh = 12 000 ч. Частота вращения вала 735 об/мин. Нагрузка с умеренными толчками. Рабочая температура t < 125 °С. Осевая нагрузка Fa составляет 35 % (допускается до 70 % от неиспользованной ради-
альной) от наименьшей радиальной, поэтому принимаем радиальные подшипники, однорядные, шариковые. Диаметр вала под подшипником d должен быть больше или равен 50 мм.
3.2 Определяем эквивалентную нагрузку
P = (XVFr +YFa )KδKt = (0,56 1 2874+1,99 729) 1,5 1 = 4590 H.
Здесь V = 1 – вращается внутреннее кольцо подшипника, Kδ = 1,5 – нагрузка с умеренными толчками; Kt = 1 – температура рабочей среды меньше 125 °С.
Коэффициенты X и Y выбираем [5, с. 93] по соотношению
Fa |
= |
|
729 |
0,25 > e = |
0,22 |
при |
Fa |
= |
729 |
= 0,029; |
|
VF |
1 2874 |
1 |
|
25 000 |
|||||||
|
|
|
C |
0 |
|
|
|||||
r |
|
|
|
|
|
|
|
|
|
|
здесь С0 – статическая грузоподъемность подшипника с внутренним диаметром d = 55 мм легкой серии
[5, с. 93].
3.3 Рассчитаем динамическую грузоподъемность подшипника. Долговечность подшипника
L= 60n Lh = 60 735 12 000 = 529,2 млн. об. 106 106
Расчетная динамическая грузоподъемность
Cp = P3 |
L |
= 45903 529,2 |
= 37 126 H, |
|
a1a2 |
1 1 |
|
где а1 = а2 = 1.
3.4 Подбираем подшипник 211 по ГОСТ 8338-75 (прил. 17), шариковый, однорядный, радиальный, легкой серии. Угол контакта α = 0°. Размеры подшипника d = 55 мм, D = 100 мм, В = 21 мм. Допускаемая динамическая грузоподъемность С = 43 600 Н.
3.5 Проверим подшипник 210 по динамической грузоподъемности. Определим эквивалентную нагрузку по отношению
e = |
0,23 |
при |
Fa |
= |
|
729 |
= 0,037, тогда X = 0,56, Y =1,90 |
1 |
|
19 800 |
|||||
|
|
C0 |
|
(X, Y – определяются интерполированием).
P = (0,56 1 2874 +1,90 729) 1,5 1 = 4492 H.
Расчетная динамическая грузоподъемность
Cp = P3 |
L |
= 44923 529,2 |
= 36 334 H. |
|
a1a2 |
1 1 |
|
(принимаем а1 = а2 = 1).
3.6 Так как Ср > С = 35 100 Н, то подшипник 210 не подходит по динамической грузоподъемности. Окончательно принимаем подшипник 211.
Пример 3. Спроектировать вариатор к мешалке для сыпучих материалов по данной схеме (рис. 20), если электродвигатель развивает мощность Рдв = 5,5 кВт, максимальная частота вращения вала мешалки
n2max = 2410 об/мин, минимальная – n2min = 482 об/мин.
Привод работает по семь часов в сутки при постоянном моменте сопротивления T2 = сonst. Нагрузка равномерная, без ударов и толчков.

n1 = var T1 = const
n2 = var T2 = const
Рис. 20 Схема привода мешалки:
1 – электродвигатель; 2 – вариатор;
3 – мешалка
1 Определяем диапазон регулирования |
Д = |
n2max |
= |
2410 |
= 5 , |
|
n2 min |
482 |
|||||
|
|
|
|
Полученная величина диапазона реализуется передачей с широким клиновым ремнем и двумя регулируемыми шкивами ([12], с. 17).
2 Подбираем двигатель и определяем максимальное и минимальное передаточные отношения. Ориентируясь на рекомендации [12] и существующие частоты вращения двигателей, задаемся максимальным передаточным отношением imax = 3, тогда ориентировочная частота вращения двигателя:
n1 = imax n2min = 3 482 = 1446 об/мин.
По n1 и Рдв, с помощью каталогов (прил. 7, 8) подбираем двигатель 4А112М4УЗ, Рдв=5,5 кВт, n1=1450 об/мин. Минимальное передаточное отношение
imin= |
nдв |
= 1450 = 0,6. |
|
n2 max |
|||
|
2410 |
3 Отношение максимального D1 и минимального d1 диаметров ведущего шкива
D1 |
= |
imax +1 |
|
= |
3 +1 |
= 2,5. |
|
d1 |
imin +1 |
0,6 +1 |
|||||
|
|
|
4Принимаем ремень типа 1-В (прил. 9) с углом профиля канавки ϕ = 26o и относительной шириной
ν= 3,1.
5Принимаем число ремней z = 1 (прил. 10)
6Определим относительный диаметр ведущего шкива ϑ1 = 8 (прил. 11).
7Рассчитаем допускаемые полезные напряжения
|
|
[k] = (20 – 4 ν) |
ϑ1 |
= (20 – 4 3,1) |
8 |
= 0,6 МПа. |
|
|
||||||
|
|
|
|
|
|
|||||||||
|
|
|
|
|
110 |
|
|
110 |
|
|
|
|
||
8 |
Рассчитаем наименьший расчетный диаметр ведомого шкива |
|
|
|
||||||||||
d2 = |
|
|
|
|
|
|
|
|
|
|
|
|
|
|
|
2T ϑ2 |
2N ηϑ2 974 104 |
= 3 |
2 5,5 0,9 122 974 10 |
4 |
|
|
|||||||
|
= 3 [k] z |
ν = 3 |
n2max [k]zν |
2410 0,6 1 3,1 |
=145 мм, |
|
|
|||||||
|
2 |
2 |
|
дв |
2 |
|
|
|
|
|
|
|
|
|
здесь |
ϑ2 =ϑ1 [( imax +1) /(imin +1)] imin |
= |
8[(3+1)/(0,6+1)] 0,6 |
= |
12; |
|||||||||
η = 0,9 – кпд вариатора. |
|
|
|
|
|
|
|
|
|
|
|
|
|
|
9 |
Уточняем размеры ремня: |
|
|
|
|
|
|
|
|
|
|
|
||
|
h = |
d2 |
= 145 |
≈12 мм; bр = hν = 12 3,1 = 37,2 мм. |
|
|
||||||||
|
ϑ2 |
|
|
|||||||||||
|
|
|
12 |
|
|
|
|
|
|
|
|
|
|
Выбираем (прил. 10) стандартный ремень 1-В40 кордшнуровый, зубчатый с размерами: bр = 40 мм, h = 13 мм, hр = 3,2 мм, площадью А1 = 508 мм2 погонным весом q = 6,3 H/м.
10 Определим диаметры шкивов:
•наибольший расчетный для ведущего шкива
D1 = |
d2 n2 max |
= |
|
145 2410 |
= 254 мм, |
|
nдв(1 − ε) |
1450 (1−0,05) |
|||||
|
|
|