
Курсовая работа3 / технология материалов курсовик Kondratiev
.pdf
Поскольку dVт = fSdt = VB0 dg , запишем dt = BfV0S dg. Подставим полученные соотношения в (5):
kC |
V0 |
dg |
− |
CV |
dg + (1 |
− |
g)V |
dC |
− |
C |
1 − B |
V |
dg + |
αF |
V |
(C |
− |
C |
)dg = 0 |
(6) |
|
|
|
||||||||||||||||||
|
B |
0 |
|
0 |
|
п |
B 0 |
|
fSB 0 |
|
р |
|
Учитывая, что kи = αFfS , kоб = kи + k, разделяем в (6) переменные и интегрируем, принимая во внимание, что при g = 0 концентрация примеси в расплаве С = С0. В этих условиях распределение примеси вдоль слитка в методе двойного капиллярного тигля примет вид:
|
|
|
k[C |
(1 |
− |
B) + k |
C |
] |
k[C0(k |
об − |
B) |
− |
C |
(1 |
− |
B) |
− |
k |
C |
] |
|
|
kоб−B |
|
||
C |
т |
= |
п |
|
и |
р |
|
+ |
|
|
п |
|
|
и |
р |
|
(1 |
− |
g) |
B |
(7) |
|||||
|
|
|
|
|
|
|
|
|
|
|
|
|||||||||||||||
|
kоб − B |
|
|
|
|
kоб − B |
|
|
|
|
|
|
||||||||||||||
|
|
|
|
|
|
|
|
|
|
|
|
|
|
|
|
|
Рассмотрим случай, когда выращивание кристалла происходит в вакууме (Ср = 0) и подпитка осуществляется чистым веществом (в подпитывающем тигле концентрация легирующей примеси Сп задается равной нулю).
Так как в моем задании примеси не летучие, то распределение примеси вдоль слитка в соответствии с (7) сводится к следующему выражению:
|
|
|
|
|
|
|
|
|
|
|
k−B |
|
|
|
|
|
(8) |
|
|
|
|
|
|
Cт = kC0(1 − g) B |
|
|
|
|
|
||||||||
Для распределения остаточных примесей аналогично, за исключением того что Сп 6= 0: |
|
|||||||||||||||||
|
kCп(1 |
− |
B) |
|
k[C0(k |
− |
B) |
− |
Cп(1 |
− |
B) |
|
|
k−B |
|
|||
C = |
|
|
|
+ |
|
|
|
|
|
(1 |
− |
g) B |
(9) |
|||||
т |
k |
− |
B |
|
|
|
|
k |
− |
B |
|
|
|
|
||||
|
|
|
|
|
|
|
|
|
|
|
|
|
|
|
|
Таким образом для нелетучей примеси (α = 0) условие однородного легирования принимает вид Ст = kС0, если k = В.
В методе двойного капиллярного тигля параметр подпитки B = Sобщ имеет значения 0.2 - 0.5. Следовательно, условия однородного легирования могут быть выполнены для тех примесей, у которых эффективный коэффициент распределения k , который находится по формуле Бартона - Прима - Слихтера:
k = |
k0 |
|
(10) |
|
k0 + (1 − k0) exp |
−fDδ |
|||
|
|
соответствует тому же диапазону значений. где f — скорость кристаллизации
δ — толщина диффузионного слоя
D — коэффициент диффузии примеси в жидкой фазе.
Толщина диффузионного слоя находится по формуле Слихтера:
1 |
1 |
−1 |
(11) |
δ = 1.6D 3 |
ν 6 |
ω 2 |
где ν — кинематическая вязкость ω — скорость вращения кристалла относительно тигля
3.3Определение массы и концентрации легирующей примеси
Концентрацию примесей в материале характеризуют либо числом атомов в единице объема Сi, либо в долях или процентах по массе yi. Первый способ выражения примесного состава используют при анализе электрофизических свойств, второй — при определении массы легирующих добавок и для характеристики химической чистоты исходных веществ и реагентов. При малом содержании примесей, когда можно пренебречь изменением плотности основного вещества d, справедливо следующее соотношение:
Ci = |
yiNad |
(12) |
|
Mi |
|||
|
|
11

где Na — число Авогадро
Mi — молярная масса примесного компонента.
При выращивании монокристаллов легирующую примесь вводят в расплав в виде твердофазной навески. В отдельных случаях, например, в методе бестигельной зонной плавки, примесь может вводиться в кристалл из газовой фазы. Для расчета массы легирующей примеси, вводимой в расплав полупроводника, необходимо знать условия выращивания монокристалла, массу расплава, содержание фоновых (остаточных) примесей, условия взаимодействия расплава с атмосферой и тиглем.
Количество примеси Qпр, которое должен содержать расплав с начальным объемом V0 для выращивания монокристалла с удельным сопротивлением ρ определяется так:
Qпр = CV0 = CтV0 k
Масса легирующей примеси mпр, которую необходимо ввести в расплав, рассчитывается следующим образом:
mпр = |
Qпр |
M = |
CтV0 |
M |
(13) |
Na |
|
||||
|
|
kNa |
|
В общем случае, несмотря на большой объем расплава, масса примеси при малом уровне легирования может составлять десятки миллиграммов. Введение в расплав столь малого количества вещества связано с существенной ошибкой, обусловленной погрешностью взвешивания или потерей легирующей навески из-за испарения или окисления. Поэтому легируют кристаллы полупроводников чаще всего с помощью лигатуры. Лигатура представляет собой полупроводниковый материал в виде полиили монокристалла с высоким уровнем легирования, близким к пределу растворимости примеси.
Масса лигатуры рассчитывается по формуле: |
|
|
|
||
mл = |
mрCтeµлρл |
= |
mpCт |
(14) |
|
k |
kCл |
||||
|
|
|
Масса лигатуры должна составлять 1–3% от массы исходной загрузки.
3.4Перераспределение остаточных примесей
Поскольку я выбрал такие условия , что подпитка осуществляется чистым веществом (в подпитывающем тигле концентрация легирующей примеси Сп задается равной нулю) , то только остаточные примеси будут влиять на выход годного материала. Выход годного материала будем смотреть по изменению удельной проводимости ( разброс значений для ρ 15% ).
Для каждой примеси найдем распределение концентрации по длине слитка по формулам:
(8)— для основной примеси,
(9)— для остаточных примесей
Для оценки выхода годного материала , запишем уравнение электронейтральности:
n(g) = CAsт (g) − CAlт (g) − CBт (g) |
(15) |
где n — концентрация с учетом 3 - х примесей.
Для перехода от концентрации к удельной проводимости воспользуемся следующей форму-
лой:
1
Cт = eµρ
где Ст = n.
После этого строим график удельной проводимости от доли закристаллизовавшегося кристалла и делаем вывод о возможности выращивания данного кристалла.
12

4Расчетная часть
4.1 Расчет массы легирующей примеси и массы загрузки
Табличные данные D = 2.4 · 10−04 [смc2 ] ν = 3.48 · 10−03 [смc2 ] k0 = 0.3
Данные выбранные самостоятельно ω = 50 [миноб ] f = 3 [минмм ]
Для определения концентрации легирующей примеси воспользуемся формулами (11),(10),(8):
1 |
1 |
−1 |
· (2.4 |
· 10− |
04 |
1 |
· (3.48 · 10− |
03 |
1 |
|
−1 |
|
|
· 10− |
02 |
[см] |
|||
δ = 1.6D 3 |
ν 6 |
ω 2 = 1.6 |
|
)3 |
|
)6 · |
(50 · 2π) 2 = 1.69 |
|
|||||||||||
k = |
|
|
k0 |
|
|
|
= |
|
|
|
0.3 |
|
|
|
= 0.379 |
|
|||
k0 + (1 − k0) exp − D |
0.3 + (1 − 0.3) exp |
−600· ·2.4··10−04 |
|
|
|||||||||||||||
|
|
|
|
|
fδ |
|
|
|
|
|
|
|
3 1.69 10−02 |
|
|
|
|
|
Концентрацию примеси в твердой фазе определим по таблице при заданном удельном сопро-
тивлении 0.1 Om · cm Cт = 9.18 · 1016[см−3]
Отсюда можно найти концентрацию примеси в жидкой фазе (из условия однородного леги-
рования) |
|
Ст |
|
|
9.18 · 1016 |
|
|
|
|
|
|
|
|
С0 |
= |
= |
|
= 2.424 |
· |
1017 |
[ |
см |
−3 |
] |
|||
|
k |
0.379 |
|||||||||||
|
|
|
|
|
|
|
|
Найдем рабочий объем V0, причем длину заготовки следует выбирать на 10% больше длины кристалла (L+10% = 110 [cm]), так как эти 10% идут на образование верхнего и нижнего конусов.
Так как диаметр кристалла Dкр = 8 [см] , |
то: |
|
|
|
|
|
|
|
||||||
V |
0 |
= |
|
π · Dкр2 |
L = |
π · (8)2 |
110 = 5.529 |
· |
1003 |
[ |
г |
] |
(16) |
|
4 |
4 |
см3 |
||||||||||||
|
|
|
|
|
|
|
Массу легирующей примеси найдем по формуле (13):
mпр = |
Qпр |
M = |
CoV0 |
MAs = |
2.424 · 1017 · 5.529 · 1003 |
75 = 0.167[г] |
|
|
6.022 · 1023 |
||||
|
Na |
Na |
|
Мы получили очень маленькую массу примеси поэтому будем использовать лигатуру (14): массу исходной загрузки, зная плотность расплава, можно найти так
|
|
|
mр = dV0 |
= 2.33 · 5.529 · 1003 = 1.288 · 1004[г] |
|
||||
m |
л |
= |
mрCтeµлρл |
= |
mpCт |
= |
1.288 · 1004 · 9.18 · 1016 |
|
= 312[ ] |
|
|
|
|||||||
|
|
k |
|
kCл |
0.379 · 1.000 · 1019 |
|
г |
||
|
|
|
|
|
|
4.2Расчет размеров конструкции
Пусть рабочий тигель будет по диаметру Dраб в 2 раза больше , чем диаметр кристалла который мы хотим получить:
Dраб = 8 · 2 = 16 [см]
Для расчета диаметра общего (подпитывающего) тигля Dобщ воспользуемся формулой (4), выразив площади через диаметры. Из условия однородного легирования следует, что параметр
подпитки B = kAs = 0.379, тогда:
B = Sраб = Dраб2 Sобщ Dобщ2
Dобщ = s |
|
Dраб2 |
|
|
r |
|
|
|
|
|
= |
|
162 |
|
= 26 [см] |
||||
|
B |
0.379 |
|
||||||
|
|
|
|
|
13

Чтобы определить высоту тиглей H, надо знать рабочий объем и диаметр рабочего тигля. Реальную же высоту тиглей надо взять чуть больше, чтобы избежать расплескивания расплава. Для этого увеличим высоту H на 10 [см], тогда согласно формуле (16):
|
|
|
|
V0 = |
π · Dраб2 |
H → |
|
|
|
|
|
|
4 |
|
|||
H = |
|
V0 |
+ 10 = |
5.529 · 1003 |
+ 10 = 37.5 [ |
] |
||
|
π·Dраб2 |
|
|
|||||
|
|
|
π·162 |
|
|
см |
||
|
4 |
|
|
4 |
|
|
|
|
|
|
|
|
|
|
|
Диаметр капилляра должен быть в диапазоне от 0.5 до 1[см], а длина капилляра должна быть в диапазоне от 0.5 до 1[см]. Для того чтобы сохранить состав подпитывающего расплава независимым от состава рабочего расплава, должно выполняться условие jж jд, поэтому Dкап надо взять минимальным, те Dкап = 0.5 [см], а длину - максимальной lкап = 1.0 [см]
Скорость подпитки fп умноженная на объем капилляра по смыслу равна количеству (объему) расплава проходящего через капилляр в единицу времени. Эта же величина должна быть равной объему расплава закристаллизовавшегося в слиток в единицу времени.
Таким образом найдем скорость подпитки:
|
|
|
πDкап2 |
= f · |
πDкр2 |
|
|
||||||
|
fп |
|
|
|
|
|
|
→ |
|
|
|||
|
4 |
|
|
|
4 |
|
|
||||||
|
f |
· |
|
πDкр2 |
|
|
3·π·82 |
|
|
см |
|
||
fп = |
|
4 |
= |
4·6002 |
= 1.280 [ |
] |
|||||||
|
|
2 |
c |
||||||||||
|
|
πDкап |
|
π·0.5 |
|
|
|
44
Условие jж jд эквивалентно условию fп D
lкап
f |
|
= 1.280 |
|
D |
= |
2.4 · 10−04 |
= 2.400 |
|
10−04 |
[ |
см |
] |
|
п |
lкап |
1.0 |
· |
c |
|||||||||
|
|
|
|
|
|
|
Значит были выбраны оптимальные размеры капилляра.
4.3Распределение концентраций легирующих примесей по длине кристалла
По формуле (12) определим концентрацию остаточных примесей: для Al
CAl = |
yiNad |
= |
5 |
· |
10−076.022 |
· |
1023 |
2.33 = 2.60 · 1016[см−3] |
||
|
Mi |
|
|
26.98 |
|
|
||||
для B аналогично |
|
|
|
|
|
|
|
|
|
|
CB = |
yiNad |
|
= |
2 |
· |
10−086.022 |
· |
1023 |
2.33 = 2.60 · 1015[см−3] |
|
|
Mi |
|
|
10.81 |
|
|
Расчет коэффициента диффузии и коэф. распределения аналогичен пункту (4.1), поэтому расчеты приводить не будем. kAl = 0.0056, kB = 0.844.
Расчет распределения концентраций легирующих примесей по длине кристалла осуществляется по формулам (8,9):
|
т |
|
k−B |
|
|
CAs(g) = kC0(1 − g) B |
|||
CAl,Bт (g) = |
kCп(1 − B) |
+ |
k[C0(k − B) − Cп(1 − B) |
|
k − B |
k − B |
|||
|
|
результат изображен на рис.4:
k−B
(1 − g) B
14
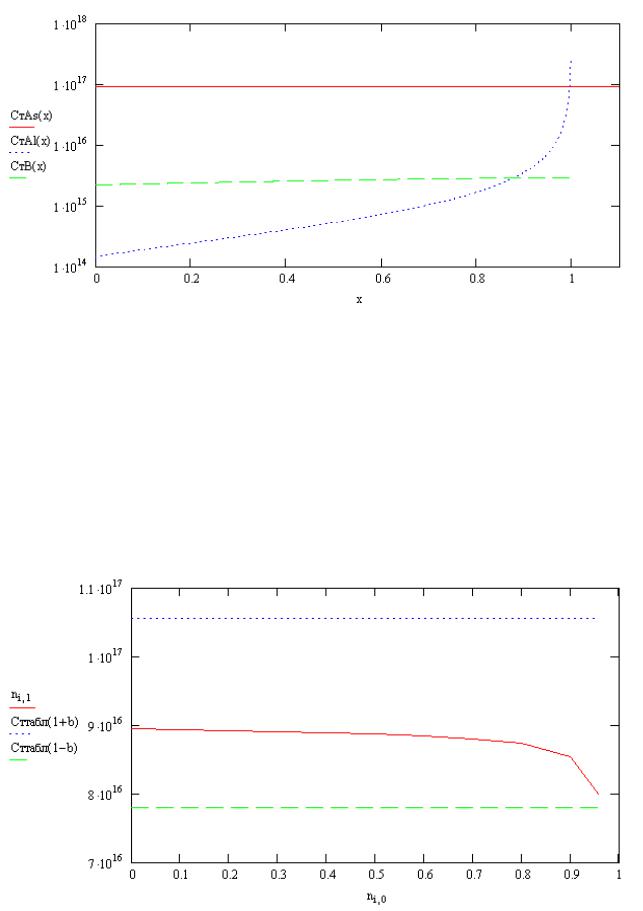
Рис. 4: Распределение концентраций легирующих примесей
4.4Оценка выхода годного материала
Найдем распределение концентрации с учетом 3-х примесей согласно уравнению электронейтральности (15).
n(g) = CAsт (g) − CAlт (g) − CBт (g)
Распределение концентрации с учетом 3-х примесей приведено на рис. 5, результаты расчетов сведены в таблицу 2.
Рис. 5: Распределение концентрации с учетом 3-х примесей
15

Для перехода от концентрации к удельной проводимости воспользуемся следующей форму-
лой:
1
Cт = eµρ
где Ст = n.
Результаты расчетов сведем в таблицу 2.
По рис. 6 видно , что выход годного материала равен 96%
Рис. 6: Изменение удельной проводимости по длине слитка
Таблица 2: Перераспределение остаточных примесей
g |
n(g) |
ρ |
Cт (g) |
Cт (g) |
Cт (g) |
|
|
|
As |
Al |
B |
0.00 |
8.946 · 1016 |
0.103 |
9.18 · 1016 |
1.464 · 1014 |
2.192 · 1015 |
0.10 |
8.933 · 1016 |
0.103 |
9.18 · 1016 |
1.890 · 1014 |
2.281 · 1015 |
0.20 |
8.919 · 1016 |
0.103 |
9.18 · 1016 |
2.423 · 1014 |
2.368 · 1015 |
0.30 |
8.904 · 1016 |
0.103 |
9.18 · 1016 |
3.106 · 1014 |
2.452 · 1015 |
0.40 |
8.886 · 1016 |
0.103 |
9.18 · 1016 |
4.015 · 1014 |
2.534 · 1015 |
0.50 |
8.866 · 1016 |
0.104 |
9.18 · 1016 |
5.284 · 1014 |
2.612 · 1015 |
0.60 |
8.839 · 1016 |
0.104 |
9.18 · 1016 |
7.182 · 1014 |
2.687 · 1015 |
0.70 |
8.801 · 1016 |
0.104 |
9.18 · 1016 |
1.033 · 1015 |
2.758 · 1015 |
0.80 |
8.732 · 1016 |
0.105 |
9.18 · 1016 |
1.660 · 1015 |
2.824 · 1015 |
0.90 |
8.539 · 1016 |
0.108 |
9.18 · 1016 |
3.526 · 1015 |
2.882 · 1015 |
0.96 |
7.982 · 1016 |
0.115 |
9.18 · 1016 |
9.052 · 1015 |
2.911 · 1015 |
16

5Заключение
1.Так как нам нужно было получить кристалл кремния с однородным распределением примеси по длине кристалла, то целесообразнее было использовать метод двойного капиллярного тигля. Метод двойного капиллярного тигля основан на подпитке рабочего расплава из жидкой фазы. Использование метода позволило существенно улучшить однородность распределения примеси вдоль слитка.
2.Рассчитали концентрацию легирующей примеси в жидкой фазе С0 = 2.424 · 1017[см−3], концентрацию примеси в твердой фазе Cт = 9.18 · 1016[см−3].
Также нашли массу примеси, она оказалась очень маленькой mпр = 0.167[г], поэтому мы рекомендуем использовать лигатуру с массой mл = 312 [г]
3.Масса загрузки основного материала составляет m = 1.288 · 1004[г]
4.Исходя из результатов показанных на рис.(4), можно заключить, что основной остаточной примесью ограничивающей выход годного материала является Al. Это связано с очень маленьким коэффициентом распределения kAl = 0.0056.
5.Рассчитали необходимые размеры установки:
•Диаметр рабочего тигля Dраб = 16 [см]
•Диаметр общего (подпитывающего) тигля Dобщ = 26 [см]
•Высота тиглей H = 37.5 [см]
•Диаметр капилляра Dкап = 0.5 [см]
•Длина капилляра lкап = 1.0 [см]
6.С учетом всех указанных параметров нам удалось получить кристалл с выходом годного материала 96% , (при условии что разброс значений для ρ 15%) см. рис.(6).
17
6Список литературы
1.Н.П. Богородицкий, В.В. Пасынков, Б.М. Тареев. «Электротехнические материалы». 1985г.
2.Александрова О. А., Сорокин В. С. «Технология полупроводниковых материалов», Практ. СПб.: Изд-во СПбГЭТУ "ЛЭТИ", 2003. 68с.
3.Нашельский А.Я. «Технология полупроводниковых материалов», Учебное пособие для повышения квалификации ИТР.М.: Металлургия, 1987.
4.Пасынков В.В., Сорокин В.С. «Материалы электронной техники», Учебник для студентов по спец. электронной технике. 3-е изд. – СПб.:Издательство «Лань»,2001.
5.Котельников И.А., Чеботаев П. З. «LATEX по-русски» 3-е издание, перераб. и доп.— Новосибирск: Сибирский хронограф, 2004. — 496 с
6.Конспект лекций и практики.
18