
Переработка нефти-2
.pdfvk.com/club152685050 | vk.com/id446425943
ИТС 30-2017
7 Перспективные технологии
7.1 Установка атмосферной перегонки нефтяного сырья (нефти, газового конденсата, их смесей)
7.1.1 Атмосферные трубчатые установки по перегонке нефти (газового конденсата) с использованием двух отбензинивающих колонн - (АТ)
Вкачестве перспективной технологии атмосферной перегонки нефтяного сырья следует указать атмосферные трубчатые установки по перегонке нефти (газового конденсата) с использованием двух отбензинивающих колонн - (АТ).
Атмосферная перегонка с использованием двух отбензинивающих колонн -
это процесс последовательной перегонки, позволяющий с минимальными суммарными затратами энергии разгонять нефти или конденсаты на углеводородные фракции, число и свойства которых оптимальны с учетом сложных схем НПЗ и ужесточающихся нормативов. Обычно эта технология рассчитана на применение на новых атмосферных или атмосферно-вакуумных установках, но может быть использована для ликвидации узких мест на существующих установках, например, для увеличения производительности процесса без добавления новой печи.
Процесс особенно пригоден в тех случаях, когда нужно получить более двух фракций нафты. Обычно в оптимальной версии процесса получают не менее трех фракций нафты, одну или две фракции керосина, две фракции атмосферного газойля, одну - вакуумного газойля, две - вакуумного дистиллята и вакуумный остаток.
Принципиальная схема процесса атмосферной перегонки нефти с использованием двух отбензинивающих колонн приведена на рисунке 7.1. Нефть подогревают и обессоливают (1), после чего подают в колонну (2) предварительной отгонки, снабженную кипятильником и работающую без острого пара, а далее - в колонну предварительной отгонки (3), работающую с острым паром. Верхние продукты этих колонн разгоняют в секции (4), получая сжиженный газ и фракции нафты.
Отбензиненную нефть, из которой отогнано около 2/3 содержавшейся в ней нафты, подогревают в обычной трубчатой печи и разгоняют в атмосферной колонне
(5). Затем, если нужно, мазут разгоняют в вакуумной колонне (6), рассчитанной на четкое разделение фракций - вакуумного газойля, двух вакуумных дистиллятов и вакуумного остатка, который может найти применение в качестве дорожного битума.
Синтез сетей рекуперативного теплообмена (в том числе с использованием пинч-технологий) позволяет минимизировать количество теплоты, передаваемой в огневых подогревателях и отводимой в воздушных и водяных холодильниках.
Процесс лучше всего подходит для крупных установок перегонки нефти производительностью от 24 до 40 тыс. м3/сут.
Внастоящее время данная технология представлена на двух установках фирмы «Technip» - на установке перегонки нефти и установке перегонки конденсата.
553
vk.com/club152685050 | vk.com/id446425943
ИТС 30-2017
СёДО
—
|
- e f ■ |
С р а д а ю а а ф т г |
I I |
|
|
______ __ |
|
|
|
|
Ведомый
Рисунок 7.1 - Установка АТ с использованием двух отбензинивающих колонн 1 - обессоливание; 2 - предварительная отгонка без острого пара;
3 - предварительная отгонка с острым паром; 4 - секция получения сжиженных газов и фракции нафты; 5 - колонна атмосферной перегонки; б - вакуумная колонна
Экономические показатели
Типичные энергозатраты на 1 м3 нефти:
сожженное топливо, МДж |
330-429 |
электроэнергия, кВт-ч |
5/7-7,5 |
пар, кг |
0-14 |
охлаждающая вода, м3 |
1,2-2,4 |
Суммарное потребление первичных энергоресурсов: для легкой аравийской нефти или российской экспортной смеси - 1,25 т топлива на 100 т нефти; для тяжелой аравийской нефти - 1 ,1 5 т топлива на 100 т нефти.
7.2 Коксование
7.2.1 Непрерывное коксование в токе теплоносителя с получением кокс (Fluidcoking)
Описание процесса
Процесс Fluidcoking по-другому называют непрерывным коксованием в псевдоожиженном слое с получением кокса, или термоконтактным коксованием. Целевым назначением процесса является получение из тяжелых нефтяных остатков дистиллятных продуктов, направляемых на последующую гидрокаталитическую переработку в высококачественные моторные топлива. Получающийся в этом процессе порошкообразный кокс является побочным малоценным продуктом, непригодным для изготовления анодных и графитированных изделий.
Кокс, полученный по технологии Fluidcoking, используется по следующим направлениям [2]:
554
vk.com/club152685050 | vk.com/id446425943
ИТС 30-2017
а) около 20% получаемого кокса сжигается для производства технологического
тепла;
б) кокс, получаемый на установках Fluidcoking, как правило, реализуется на рынках твердого топлива. Около половины его продается в качестве топлива для цементной промышленности, а другая половина сжигается в бойлерах и на электростанциях (кокс низкого качества);
в) газы процесса обычно направляют в котел-утилизатор (бойлер) дожига оксида углерода для утилизации теплоты.
Характеристика сырья процесса Fluidcoking представлена в таблице 7.1.
Таблица 7.1 - Характеристика сырья процесса Fluidcoking |
Значение |
|
Наименование показателей |
| |
|
Сырье - гудрон |
Т078 |
|
Плотность, кг/м-3 |
|
|
Коксуемость, % мае. |
Ж 1 _________________________________________ |
Технологическая схема процесса
Рисунок 7.2 - Схема установки непрерывного коксования в псевдоожиженном слое кокса (Fluidcoking)
1 - парциальный конденсатор (скруббер); 2 - реактор; 3 - коксонагреватель; 4 - топка; 5 - холодильник-классификатор кокса; 6 - ректификационная колонна; 7 - конденсатор; 8 - компрессор; 9 - холодильник; 10,14 - сепараторы; 11 - стабилизатор; 12 - отпарная колонна; 13 - котел-утилизатор;
I - Сырье; II - Пар; III - Рециркулят; IV - |
Флегма (тяжелый газойль) в ап.1; |
V - Холодный кокс; VI - Товарный кокс; VII - |
Тяжелый газойль; VIII - Легкий газойль; |
IX - Газ; X - Стабильный бензин; XI - Воздух; XII - Горячий кокс
Технологическая схема установки Fluidcoking показана на рисунке 7.2 [2]. Кокстеплоноситель (порошок - округлые частицы диаметром 0,075 - 0,3 мм) непрерывно циркулирует через систему реактор 2 - коксонагреватель 3. Оба аппарата работают в режиме псевдоожиженного слоя кокса. В реакторе псевдоожижение слоя кокса происходит путем подачи вниз водяного пара и частично при помощи паров и газов,
555
vk.com/club152685050 | vk.com/id446425943
ИТС 30-2017
образовавшихся при коксовании. В коксонагревателе псевдоожижение создают, подавая воздух; при этом часть кокса сгорает, а остальная масса нагревается до 600 - 620°С.
Сырье (гудрон) подают в реактор 2 при температуре (300-350°С) через систему распылителей под уровень псевдоожиженного слоя кокса. Пары и газы коксования пропускают через систему циклонных сепараторов для отделения коксовой пыли и направляют в скруббер - парциальный конденсатор 1, который для уменьшения закоксовывания передаточных линий располагают непосредственно на реакторе. За счет тепла циркуляционного орошения в нижней части скруббера конденсируют наиболее тяжелую часть дистиллята коксования; ее возвращают в реактор 2. Газопродуктовую смесь выводят с верха парциального конденсатора 1 и разделяют в ректификационной колонне 6. Газобензиновую смесь пропускают через систему, включающую конденсатор 7, холодильник 9, а также сепараторы 10 и 14, и подают в стабилизатор 11, где газ отделяют от бензина. В отпарной колонне 12 отделяют легкий газойль, а с низа колонны 6 выводят тяжелый газойль.
Поток кокса с нижней части реактора поступает в коксонагреватель, где частично выжигается, а основная часть возвращается в реактор 2. Избыток горячего кокса непрерывно выводится из коксонагревателя через холодильник-классификатор 5.
Материальный баланс процесса
Материальный баланс установки непрерывного коксования (Fluidcoking) тяжелого гудрона с содержанием серы 6,0 % (мае.) и углерода 28% (мае.) представлен в таблице 7.2.
Таблица 7.2 - Материальный баланс процесса Fluidcoking
Поступило: |
|
% мае. |
Гудрон |
|
|
Итого: |
100,0 |
|
Получено: |
6,2 |
|
Сухой газ (С1-С2) |
||
Жирный газ (С3-С4) |
12,4 |
|
Бензин (Сб-182 °С) |
ж |
з |
Легкий газойль (182-343 °С) |
|
|
Тяжелый газойль (343-524 °С) |
ж |
з |
Кокс |
Ж 2 |
|
Итого: |
ТТЩ ) |
Степень проработки
В настоящее время по технологии Fluidcoking эксплуатируются 8 установок суммарной мощностью -460 тыс. бар/сут. (-27 млн. т/г) на НПЗ США и Канады. В России подобных установок нет.
Достигаемые экологические преимущества
Достоинства процесса состоят в его непрерывности, исключении операций гидравлической резки и удаления кокса, очистки печных змеевиков от коксовых отложений, устранении циклических изменений температурных нагрузок аппаратуры, обеспечении собственным топливом, автономности теплоснабжения.
Экономические аспекты внедрения
556
vk.com/club152685050 | vk.com/id446425943
ИТС 30-2017
Одним из достоинств процесса непрерывного коксования является снижение удельных капиталовложений по мере укрупнения единичных мощностей вплоть до 6,0 млн т/год (15,9 тыс. м3 в сутки) и более.
Удельные капиталовложения в оборудование установки Fluidcoking, включая необходимые очистные сооружения, в диапазоне единичных мощностей 0,6-6,0 млн т. по сырью составляют 60,0 - 36,6 млн долл, на один млн т/год (для побережья Мексиканского залива США) [3].
7.2.2 Непрерывное коксование в токе теплоносителя с газификацией кокс (Flexicoking)
Описание процесса
Flexicoking представляет собой модифицированный вариант Fluidcoking, дополненный блоком газификации балансового кокса и очистки низкокалорийных топливных газов с получением углеводородных газов и жидких продуктов коксования. Топливный газ, получаемый газификацией (флексигаз) может сжигаться на собственном НПЗ или на соседних объектах.
Характеристика сырья процесса Flexicoking представлена в таблице 7.3.
Таблица 7.3 - Характеристика сырья процесса Flexicoking
Наименование показателей |
I З н а ч е н и е |
Сырье - гудрон |
1032 |
Плотность, кг/м-3 |
|
Коксуемость по Конрадсону, % мае. |
-2^В |
Содержание серы, % мае. |
ь,ё |
Продукты
Характеристика основных продуктов процесса Flexicoking представлена в таблице 7.4.
Таблица 7.4 - Характеристика основных продуктов процесса Flexicoking
Показатель |
Проектные |
Данные |
|
Фактические |
|
Бензин (после гидроочистки): |
до очистки |
после очистки |
ТТ75 |
|
|
бромное число |
0,4 |
|
содержание серы, % мае. |
3,5/0,01 |
0,00026 |
содержание азота, % мае. |
-/0,001 |
0,00003 |
Газойль коксования (после |
|
|
гидроочистки): |
5,3/0,1 |
|
содержание серы, % мае. |
0,05 |
|
содержание азота, % мае. |
-/0,13 |
ЩЗЗ |
Коксовый газ: |
-/0,002 |
0,0001 |
содержание сероводорода, % об. |
||
содержание серооксида углерода, % |
-/0,0142 |
0,0134 |
низшая теплопроводная способность, |
-/1148 |
"Т006 |
ккал/м3 |
|
|
Технологическая схема процесса
Технологическая схема установки Flexicoking показана на рисунке 7.3.
557
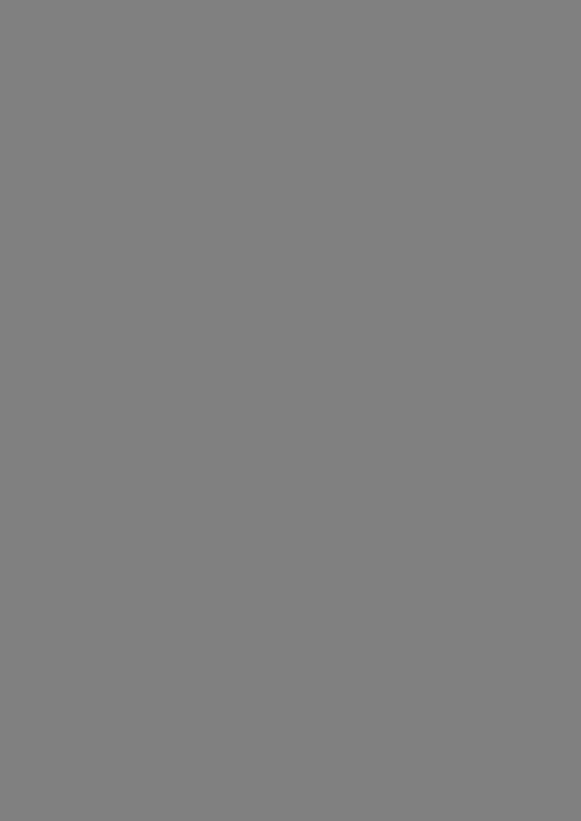
vk.com/club152685050 | vk.com/id446425943
vk.com/club152685050 | vk.com/id446425943
|
ИТС 30-2017 |
а) |
закрытая система; пневматическая транспортировка из реакторов с |
псевдоожиженным слоем в силосы для продукта; |
|
б) |
отсутствует пыль от открытых штабелей и транспортировки кокса; |
в) |
не требуется оборудование для удаления пыли из котлованов и площадок |
хранения кокса.
Низкие выбросы углеводородов:
а) непрерывный процесс, без частого открывания и цикличности работы оборудования;
б) отсутствуют выбросы углеводородов в результате цикличности работы оборудования и продувки емкостей для кокса;
в) не требуется оборудование для отвода паров из системы охлаждающей воды, котлованов и площадок хранения кокса.
Низкие выбросы SOx:
а) |
в результате газификации сера, содержащаяся в коксе, превращается в H2S, |
который уносится флексигазом; |
|
б) |
H2S легко удаляется из флексигаза до содержания < 10 ppm с помощью |
специального амина; |
|
в) |
при сжигании флексигаза в печах и бойлерах на НПЗ образуются низкие |
объемы SOx.
Низкие выбросы NOx:
содержащийся во флексигазе N2 снижает температуру адиабатического пламени при сгорании. Это дает более низкие объемы NOx, чем при сжигании природного или заводского топливного газа.
Экономические аспекты внедрения
Процесс Flexicoking экономически выгоден, когда:
-мощность НПЗ более 10 млн т/г;
-мощность самой установки более 1,0 млн т/г;
-в непосредственной близости находятся крупные потребители газа;
-высокие цены на природный газ и отсутствуют другие источники тепла на НПЗ.
7.2.3Газификация кокса
Описание процесса
Процесс газификации твердых остатков нефтепереработки и тяжелых нефтяных остатков, не находящих квалифицированного применения, получает в последние годы возрастающую популярность на европейских и североамериканских НПЗ для увеличения глубины переработки нефти, особенно в тех случаях, когда возникают проблемы с утилизацией «хвостов» с установок глубокой переработки и имеется большая потребность в водороде.
Газификация представляет собой конверсию твердого (кокс, уголь, отходы) или жидкого (гудрон, остаток висбрекинга, пек, асфальт) топлива в синтез-газ, главными компонентами которого является водород (Нг) и монооксид углерода (СО). Газификация исходного сырья протекает с недостатком кислорода: на газификацию используется только 20-30 % кислорода, теоретически необходимого для полного сгорания. Процесс проводят при высоком давлении (от 25 до 140 атм.) и температуре 1300-1500 °С.
В таблице 7.6 представлены наиболее известные технологии газификации [5].
559
vk.com/club152685050 | vk.com/id446425943
Таблица 7.6 - Сравнительная характеристика процессов газификации |
|
|
|||
№ |
Сравнительная |
|
Наименование фирмы |
|
|
|
характеристика |
GE Texaco |
Conoco Phillips |
5пёП |
Future Energy |
1 |
Сырье |
Остаточные жидкие |
Угли, нефтяной кокс. |
Тяжелые |
Жидкие, твердые отходы НПЗ |
|
|
нефтяные фракции с |
|
остаточные |
(нефтяной кокс, тяжелые |
|
|
высоким |
|
углеводородные |
остатки), химической |
|
|
содержанием серы и |
|
фракции с высоким |
промышленности и угли |
|
|
металлов, водная |
|
содержанием серы |
(антрацит, лигнит). |
|
|
суспензия коксовой |
|
и металлов, уголь, |
|
|
|
мелочи. |
|
нефтяной кокс. |
|
2 |
Продукты |
Водород, топливный |
Очищенный синтез-газ, |
Чистый синтез-газ, |
Чистый синтез-газ, водород, |
|
|
газ, синтез-газ, сера |
элементарная сера, |
ценные оксиды |
элементарная сера, сульфиды |
|
|
(в виде кислого газа), |
водород, пар, |
металлов (никеля и |
тяжелых металлов, |
|
|
лепешка с фильтра |
электроэнергия, |
ванадия), водород, |
стеклообразный |
|
|
(для извлечения |
шлаковые побочные |
элементарная сера, |
гранулированный шлак, пар, |
|
|
металлов), пар |
продукты. |
пар, |
электроэнергия. |
560 |
|
высокого давления, |
|
электроэнергия. |
|
Особенности |
электроэнергия. |
Двухступенчатая |
Двухступенчатая |
Реагенты подаются в аппарат |
|
3 |
Избыточное давление |
||||
|
процесса |
в аппарате |
газификация. Сухая |
промывка водой |
газификации через |
|
|
газификации 2,76-5,52 |
система очистки синтез- |
синтез-газа от сажи |
специальные горелки в верхней |
|
|
МПа, температура |
газа от твердых частиц. |
и золы. |
части камеры сгорания. После |
|
|
1260-1480 °С. Синтез- |
|
|
аппарата газификации |
|
|
газ для очистки от |
|
|
устанавливают либо систему |
|
|
сажи и золы |
|
|
закалки струями воды, либо |
|
|
промывается водой. |
|
|
котел-утилизатор. |
|
Промышленные |
Более 50 установок |
Установка газификации |
Более 150 |
Установка газификации бурого |
|
установки |
газификации |
нефтяного кокса (100%) |
установок в разных |
угля, шлама, масел, суспензий, |
|
|
остаточных продуктов |
на Wabash River, штат |
странах (в |
содержащих золу на заводе |
|
|
в разных странах. |
Индиана. Установка |
основном по |
Schwarze Pumpe, Германия. |
|
|
|
газификации нефтяного |
газификации |
Установка газификации жидких |
|
|
|
кокса (60%) и угля Татра |
тяжелых |
остаточных отходов в |
|
|
|
Electric, штат Флорида. |
остаточных УВ |
Мидлсборо |
|
|
|
|
фракций). |
|
2017-30 ИТС
vk.com/club152685050 | vk.com/id446425943
ИТС 30-2017
Наиболее распространен процесс CGP компании «Shell». По данной технологии эксплуатируются более 150 установок в разных странах. В Нидерландах на основе процесса CGP вырабатывают 250 МВт электроэнергии. В России таких установок нет.
На рисунке 7.4 представлена технологическая схема этого процесса.
Рисунок 7.4 - Технологическая схема газификации кокса компании Shell
1 - газификатор; 2 - котел-утилизатор; 3 - парогенератор; 4 - концевой скруббер; 5 - узел отмывки сажи; 6 - узел фильтрации; 7 - узел обработки лепешки фильтра;
I - Кокс; II - Кислород; III - Пар; IV - Синтез-газ; V - Кислая вода на переработку;
VI - Вода; VII - Соединения никеля и ванадия из золы
Кокс подают в газификатор 1, где происходит его окисление и газификация чистым кислородом и водяным паром. Суммарная реакция экзотермична и в результате получают газ, в основном состоящий из СО и Нг. В зависимости от конечного применения синтез-газа подбирают рабочее давление - от атмосферного до 65 атм. Газификатор обкладывают огнеупорной футеровкой, в нем расположены горелки, газификатор соединен с котлом-утилизатором 2, рассчитанным на выработку пара с давлением более 100 атм. (около 2,5 т пара на 1 т сырья). Газы выходят из котла-утилизатора с температурой, близкой к температуре пара, охлаждаются в пароперегревателе 3 и далее поступают в узел отмывки сажи 5. Сажу и золу отмывают в две ступени. После концевого скруббера 4 газ, практически не содержащий твердых частиц, поступает в систему селективной очистки от кислых компонентов (на схеме не показано). Балансовую воду из скрубберной секции направляют в узел отмывки сажи 5. Лепешку, снятую с фильтра (золу), окисляют, превращая золу в ценные оксиды ванадия. Чистый фильтрат возвращают в скруббер.
Степень проработки
Технология внедрена в промышленность. Достигаемые экологические преимущества
а) выработка пара и электроэнергии для внутреннего потребления и продажи электроэнергетическую систему;
561
vk.com/club152685050 | vk.com/id446425943
ИТС 30-2017
б) наименее ценные остаточные продукты превращаются в продукты высокой ценности;
в) удовлетворение потребностей в водороде и паре избавляет НПЗ от нестабильных цен на природный газ;
г) экологическая чистота процесса: из сырья удаляется до 99% серы, содержание окислов азота в отходящих газах сведены к минимуму;
д) конфигурация установки может быть легко приспособлена под разные требования по производству электроэнергии и водорода и позволяет варьировать их выпуск;
е) при необходимости установку можно оснастить системой улавливания СОг.
Экономические аспекты внедрения
Экономика процесса и собственно сама стоимость установки газификации определяется большим числом факторов: стоимостью сырья, вырабатываемым количеством водорода, электроэнергией и т.д. Кроме того, стоимость инвестиций в строительство установки существенно зависит от мощности: чем она меньше, тем выше необходимые инвестиции, а также от сырья, направляемого на газификацию (таблица 7.7).
Таблица 7.7 - Сопоставление вариантов использования процесса газификации
различных остатков |
________ |
_______ |
_______ __________ _____ |
|
|
Вариант 1 |
Вариант 2 |
Вариант 3 |
Вариант 4 |
Показатели |
Атмосферна |
Атмосферна |
Атмосферная |
Атмосферная |
я перегонка |
я перегонка |
перегонка |
перегонка |
|
|
+ |
+ |
+ |
+ |
|
вакуумная |
вакуумная |
вакуумная |
вакуумная |
|
перегонка |
перегонка |
перегонка |
перегонка |
|
+ |
УЗК |
+ |
+ |
|
газификаци |
деасфальтизац |
деасфальтизация |
|
|
я гудрона |
+ |
ия гудрона |
гудрона + УЗК |
|
|
газификаци |
+ |
асфальта |
|
|
я кокса |
газификация |
(А$СОТ) |
|
|
|
асфальта |
+ |
|
|
|
|
газификация |
Объем |
5683,7 |
2608,1 |
3432,1 |
кокса |
2933,7 |
||||
капиталовложени |
|
|
|
|
й, млн. долл. |
|
|
|
|
США |
19,86 |
^ 3 9 |
|
|
Срок |
|
|
||
окупаемости, год |
|
|
|
|
Вариант 2 с установкой замедленного коксования является наиболее предпочтительным (причем для случаев переработки любой нефти), учитывая минимальные капиталовложения на строительство этих установок и минимальный срок окупаемости. Однако недостаток данного варианта заключается в необходимости строительства УЗК большой единичной мощности для производства одинакового количества вырабатываемой электроэнергии. В данном случае представляется целесообразным подвергать газификации нефтяной кокс с нескольких УЗК разных НПЗ.
562