
технология бурения 2
.pdfvk.com/club152685050 | vk.com/id446425943
Спуск турбобура в скважину производится по существующим правилам ведения буровых работ в нефтяной и газовой промышленности. Спуск бурильного инструмента обычно приостанавливается в момент, когда долото не достает нескольких метров до забоя скважины. После этого включается буровой насос, и скважина промывается. Турбобур при этом запускается и работает в холостом режиме. Через некоторое время бурильщик начинает медленно опускать бурильную колонну. Долото, которое вращается с частотой холостого хода турбобура, касается забоя скважины. В этот момент снизу на долото начинает действовать сила реакции забоя, которая называется осевой нагрузкой. На долоте возникает крутящий момент, который оказывает сопротивление вращению вала турбобура. При увеличении осевой нагрузки момент на долоте растет, а частота вращения вала уменьшается.
Процесс бурения турбобуром обычно начинается при небольшой осевой нагрузке. В дальнейшем осевая нагрузка увеличивается до рабочих значений, рекомендованных технологией бурения для данных геологотехнических условий, и устанавливается относительно стабильный рабочий режим. При внезапных остановках турбобура из-за перегрузки, неустойчивости его работы или по другим причинам бурильный инструмент приподнимается, затем долото вновь доводится до забоя скважины, и бурение продолжается. Во время бурения рекомендуется медленно, постоянно или периодически, проворачивать бурильную колонну ротором для предотвращения ее зависания на стенках скважины.
После подъема турбобура на поверхность для смены долота или для других целей его необходимо тщательно осмотреть в подвешенном положении и замерить осевой и радиальный люфты (зазоры) вала. Турбобур должен быть заменен на новый, если осевой люфт превышает 5-6 мм, а радиальный – 3 мм. У секционных шпиндельных турбобуров обычно заменяется только шпиндель, который отправляется на ремонт.
В процессе эксплуатации турбобура необходимо следить за работой буровых насосов и контролировать возможные утечки в бурильных трубах. Неполадки в гидравлической системе часто являются причинами неустойчивой работы и отказов турбобура в процессе бурения. Также необходимо следить за качеством бурового раствора и не допускать возможного засорения забойного двигателя. При турбинном бурении весьма важно, чтобы эффективно работала система очистки бурового раствора. Наличие в промывочной жидкости абразивных механических частиц в объемном количестве более 1 % может привести к существенному увеличению темпа износа опор и турбины.
Если не произошел преждевременный отказ или не образовался чрезмерно большой люфт вала, то турбобур используется в бурении до достижения нормативного времени его работы, установленного для каждого типоразмера турбобуров технологической службой и руководством
39
vk.com/club152685050 | vk.com/id446425943
бурового (сервисного) предприятия. После завершения эксплуатации на буровой турбобур подлежит вывозу на ремонт.
8.6.2. Ремонт турбобуров
Для поддержания парка турбобуров в работоспособном состоянии на базах производственного обслуживания буровых или сервисных предприятий имеются цехи по ремонту ГЗД. Для производства качественного ремонта цех по ремонту турбобуров должен быть оснащен комплексом оборудования и инструмента, а также контрольно-измерительной аппаратурой, в т.ч.:
–специальным ключом для завинчивания/развинчивания резьбовых соединений турбобуров;
–стендом распрессовочным для извлечения из корпуса и сборки в корпус валов с установленными на них деталями;
–стендом для сборки и разборки деталей на валах турбинных и шпиндельных секций;
–установкой моечной для мойки и сушки отдельных деталей перед ремонтом;
–стеллажами для укладки длинномерных деталей – валов и корпусов.
Цех по ремонту турбобуров обычно разделяется на два участка. Первый – подготовительный, в котором осуществляется промывка турбобуров после их доставки с буровой и определяются дефекты турбинных и шпиндельных секций до их разборки. Второй – сборочный, здесь разбираются и собираются турбинные и шпиндельные секции, демонтируются и заменяются изношенные узлы и детали.
Турбобуры, подлежащие ремонту, должны быть промыты и разобраны вскоре после окончания их эксплуатации на буровой. Это требование обусловлено тем, что глинистый раствор, попавший в зазоры между отдельными деталями (статорами и корпусом, роторами и валом), может засохнуть и значительно затруднить операции разборки и ремонта. Содержание и объем ремонтных работ определяется после полной разборки турбобура.
Ремонт турбобура состоит из следующих основных работ: полная разборка; отбраковка и комплектация сменных деталей; замена изношенных деталей; проверка прямолинейности валов и корпусов; проверка резьбовых соединений. При сборке турбобура применяют новые детали, а также детали, отремонтированные в механических мастерских. Качество сборки в большей степени зависит от правильной комплектации, отбраковки и замены изношенных деталей.
Подготовке деталей к сборке предшествуют: мойка и очистка деталей, отбраковка, ремонт и реставрация. После полной разборки производится предварительный визуальный осмотр деталей. Детали, признанные годными, поступают на промывку и очистку. Длинномерные детали (валы,
40
vk.com/club152685050 | vk.com/id446425943
корпусы) отмывают в специальных ваннах или с помощью напорной струи. Детали турбинной и шпиндельной секций (статоры, роторы, радиальные и осевые опоры и др.) промывают в специальных моечных установках или ваннах.
Резьбы деталей турбобура (корпусов, валов, полумуфт, переводников и ниппелей) осматривают и контролируют резьбовыми калибрами, а также обязательно – путем свинчивания резьбового соединения. Перед проверкой резьба должна быть очищена металлической щеткой и промыта бензином.
Турбину, демонтированную с вала турбинной секции, предварительно осматривают, моют и чистят. Затем окончательно осматривают и измеряют геометрические параметры. При осмотре отбраковывают детали с сильной коррозией, имеющие трещины, поломки и погнутости лопаток, глубокие забоины и задиры на поверхностях, заметную эксцентричность ободов относительно ступиц и другие явно выраженные дефекты. На опорных поверхностях (торцах) не допускаются забоины, заусенцы, так как они могут привести к ослаблению закрепления системы ротора (статора) и потери герметичности торцов. Турбины, бывшие в работе, но не имеющие износа по высоте лопаток, с размерами, соответствующими техническим условиям, собирают в турбинные секции как новые. Турбины, имеющие износ лопаток по высоте до 1 мм, допускаются в сборку наравне с новыми турбинами. Характеристики турбобура, собранного из таких турбин, практически не отличаются от характеристик турбобура из новых турбин. Следует иметь в виду, что турбобуры, собранные из турбин с лопатками, изношенными по высоте более чем на 1 мм, нецелесообразно применять при бурении скважин глубиной более 3000 метров из-за потери мощности турбобура. Такие турбобуры следует использовать при бурении верхних интервалов скважин, где потери мощности турбобура с изношенными по высоте лопатками можно компенсировать увеличением подачи буровых насосов.
Шпиндельные секции являются наиболее изнашиваемым узлом турбобура. При их ремонте обычно заменяются все быстроизнашиваемые детали, кроме корпуса и вала: осевые и радиальные опоры, полумуфты и пр. Резинометаллические осевые опоры после демонтажа с вала шпиндельной секции моют и подвергают визуальному осмотру. При осмотре подпятников проверяют состояние резиновых обкладок и упорных торцов. Резиновая обкладка подпятника должна быть без надрывов, вырывов, отслаиваний, задиров, следов набухания и других повреждений. Металлические торцы не должны иметь выбоин и раковин. Опоры качения не должны иметь трещин, выкрашиваний, следов коррозии и других явно выраженных признаков разрушения шариков, а также беговых дорожек колец и рабочих поверхностей втулок подшипников. При осмотре втулок, колец и обойм подшипника качения необходимо проверять состояние беговых дорожек.
41
vk.com/club152685050 | vk.com/id446425943
Опоры качения с незначительным равномерным износом беговых дорожек шариков могут в отдельных случаях использоваться повторно.
Надёжность и долговечность работы турбобуров зависит от качества их сборки и регулировки. Турбобур должен быть собран и отрегулирован таким образом, чтобы осевые зазоры в турбине допускали необходимое осевое перемещение вала при эксплуатации. Неправильно отрегулированные осевые зазоры между роторами и статорами могут привести к соприкосновению их между собой, износу лопаток турбины по высоте и, как следствие, ухудшению рабочей характеристики турбобура. Неправильная регулировка шпинделей также может ухудшить рабочую характеристику турбобура.
8.7. Винтовые забойные двигатели
Несмотря на определенные усовершенствования в области техники и технологии турбинного бурения, показатели работы долот на протяжении ряда лет улучшались весьма незначительно. Хотя в 70-е годы началось разбуривание месторождений Западной Сибири, отличающихся благоприятными условиями бурения (мягкие породы, относительно неглубокие скважины), средняя проходка за рейс по эксплуатационному бурению существенно отставала от аналогичного показателя в нефтяной промышленности США в 3-4 раза. Так, в 1981–1982 гг. средняя проходка за долбление в США составила 350 м, в то время как в СССР этот показатель не превышал 90 м.
Серьезное отставание в проходке за долбление было связано с тем, что на протяжении 40 лет отечественная практика бурения базировалась на высокоскоростном бурении с применением многоступенчатых безредукторных турбобуров, характеристики которых, при использовании в качестве породоразрушающего инструмента современных высокомоментных (матричных, PDC) долот, не позволяли получать требуемые параметры режима углубления скважины. В связи с этим перед специалистами и организаторами бурения в нашей стране встал вопрос о создании высокомоментной техники для низкооборотного бурения.
Были определены оптимальные диапазоны частот вращения для эффективного использования современных типов долот: 40–80 об/мин – для твердых пород; 120–200 об/мин – для мягких пород.
Эффективное решение данной проблемы – это создание забойного гидравлического двигателя с характеристиками, отвечающими требованиям новых конструкций долот, за счет перехода от динамических машин, какими являются турбобуры, к объемным – винтовым забойным двигателям (ВЗД).
42

vk.com/club152685050 | vk.com/id446425943
Винтовые забойные двигатели, имеющие в своей основе героторный1 механизм, занимают ведущую позицию в буровой технике и технологии при разработке нефтяных и газовых месторождений. Применение винтовых двигателей способствовало существенному повышению техникоэкономических показателей бурения и возникновению новых технологий строительства скважин.
Объемные машины различают по назначению: для универсального применения (общего назначения); наклонно направленного и горизонтального бурения; для ремонта скважин (буровых работ внутри обсадных колонн и насосно-компрессорных труб); специального применения (например, двигатели для горизонтального бурения с вращением КНБК). Также по наружному диаметру: обычного исполнения (диаметром 127 мм и более); малогабаритные (диаметром от 54 до 127 мм); миниатюрные (диаметром менее 54 мм). По частоте вращения: обычные (п = 80–150 об/мин); быстроходные (п > 150 об/мин); тихоходные (п < 80 об/мин).
Серийно выпускаемые ВЗД различают по термостойкости: в обычном исполнении для температуры до 100 °С; термостойкие, предназначенные для бурения при забойной температуре 120–150 °С и более. Термостойкость ВЗД определяется физико-химическими свойствами эластичной обкладки статора и клея, обеспечивающего крепление обкладки с металлом. Для повышения термостойкости ВЗД используются специальные эластомеры, а также особые конструкции статоров, например со шлицевым креплением обкладки. В отечественной практике термостойкие двигатели серийно не выпускаются. За рубежом ряд компаний предлагают ВЗД, предназначенные для работы в условиях забойной температуры до 150 °С.
Поскольку в настоящее время большое внимание уделяется бурению глубоких (до 3500 м) и сверхглубоких (от 4000 до 11000 м) скважин, требуется создание ВЗД с возможностью его работы при температуре более 150 °С. Это вызвано разработкой, исследованиями и освоением продуктивных интервалов с подсчетами запасов нефти и газа. Температурный градиент по разрезу скважин составляет в среднем 3,3 °С на 100 м. Температура на забое скважин в интервалах от 4 000 до 11 000 м варьируется от 130 до 270 °С. Также при бурении скважин месторождений Севера Тюменской области встречаются интервалы с аномально высокими температурами (более 150 °С) на глубине от 3500 до 4600 м. Базовая конструкция винтовой пары не позволяет избежать выхода из строя эластичной (резиновой) обкладки статора. Прежде всего это связано со свойствами резиновых смесей статоров ВЗД, имеющих ограниченный температурный диапазон. Результаты испытаний применяемых резиновых смесей, например таких как Н-407-14 и ИРП-1226-3, показали, что условная прочность после термического воздействия от 120 до 140 °С снижается до 85 %. Снижение
1 Героторный механизм – механизм, аналогичный движению Земли.
43
vk.com/club152685050 | vk.com/id446425943
прочности эластичной (резиновой) обкладки статора при высоких забойных температурах в скважине приводит к отказу ВЗД вследствие прямоточных утечек закачиваемого под высоким давлением (от 4,0 до 8,0 МПа) реагента (бурового раствора) по профилю винтовых линий ротора и статора. Это приводит к частым остановкам и запускам двигателя, невозможности бурения ВЗД в условиях высоких забойных температур. Бурение скважин в местах высоких температур осуществляется роторным способом: путем вращения бурильной колонны. В результате взаимодействия – трения о стенки скважины происходит износ бурильных труб, элементов оснастки бурильной колонны, что снижает технико-экономические показатели бурения.
Как указывалось выше, винтовой забойный двигатель – это двигатель объемного типа, приводимый в действие давлением циркуляции бурового раствора. Двигатель передает энергию вращательного движения на долото с определенными значениями крутящего момента и частоты вращения долота.
Для работы двигателя в качестве промывочной жидкости используется вода или буровой раствор и газожидкостная система (ГЖС) плотностью от 700 до 1600 кг/м3 с содержанием абразивных частиц до 1 % по весу, крупностью не более 1 мм и нефтепродуктов до 10 %, при забойной температуре не более 100 °С. Разработанные в последнее время винтовые забойные двигатели могут использоваться и при более высоких забойных температурах (до 135 °С).
Безотказная работа двигателя и его долговечность зависят от качества бурового раствора. Система очистки раствора должна быть оборудована виброситами и пескоотделителями. Для тонкой очистки раствора рекомендуется использовать илоотделители и центрифуги.
Двигатели объемного принципа действия со все увеличивающейся наработкой на отказ в сочетании с долотами новейшей в буровой отрасли конструкции являются теперь для буровиков альтернативой традиционному роторному и турбинному бурению.
При их использовании увеличивается частота вращения долота (в сравнении с роторным бурением), а также механическая скорость проходки с возможностью увеличения нагрузки на долото. Общепризнанно, что ВЗД, подобранный под буровое долото и пласт, обеспечивает лучшую скорость проходки, чем роторное бурение, уменьшает износ и усталость компонентов бурильной и обсадной колонны, а также оборудования устья: вертлюга, ведущей трубы и привода ротора.
При бурении с ВЗД возможен более эффективный контроль за отклонением и резким искривлением скважины.
Бурение с помощью ВЗД более экономично, т.к. мощность, подаваемая на буровые насосы для приведения в действие двигателя и бурового
44
vk.com/club152685050 | vk.com/id446425943
долота, меньше мощности, которая нужна для вращения бурильной колонны с сопутствующими потерями на трение.
При бурении ВЗД в твердых породах проходка на долото увеличивается более чем в два раза, а в мягких – на 20–30 % по сравнению с турбобуром, механическая же скорость бурения в обоих случаях ниже на 20–50 %. Тем не менее при глубине скважины свыше 1500–2000 м ВЗД выгодны, ибо обеспечивают более высокую рейсовую скорость, которая, напомним, является интегральным показателем эффективности механического бурения.
ВЗД находит все более широкое применение во многих районах для бурения различных по твердости, пластичности, абразивности горных пород. Он проще по конструкции, имеет значительно меньшую длину и массу по сравнению с турбобуром. Небольшая длина двигателя очень выгодна для бурения наклонных и особенно горизонтальных скважин, поскольку можно до минимума снизить радиус искривления ствола и, соответственно, его длину. Максимальное снижение диаметра и длины двигателя при сохранении приемлемых энергетических параметров позволило значительно увеличить проходимость компоновки при большом угле перекоса и обеспечить радиус искривления ствола скважины до 10 м.
При бурении ВЗД имеется возможность контролировать отработку долота по давлению в циркуляционной системе (на стояке), поскольку перепад давления на двигателе пропорционален вращающему моменту, потребляемому долотом. Так, при значительном износе опоры наблюдается её периодическое подклинивание, которое проявляется на поверхности скачкообразными возрастаниями давления на стояке. При изнашивании зубьев, напротив, давление будет снижаться при неизменной нагрузке на долото. ВЗД в принципе весьма перспективны для бурения долотами ИСМ, РСД с крупными резцами из алмазосодержащих композиционных материалов, шарошечными с маслонаполненными герметизированными опорами скольжения.
В основу объемных двигателей положена схема планетарного эксцентричного редуктора с внутренним зацеплением и винтовыми зубьями.
Двигатель состоит из двух основных узлов (рис. 8.15): секции двигательной 1 и секции шпиндельной 6, которые соединяются между собой переводником 5.
Секция двигательная предназначена для преобразования энергии движущего потока буровой жидкости во вращательное движение ротора и передачи этого движения на вал шпиндельной секции. Секция двигательная включает героторный механизм, статор 2 и ротор 3, шарнирное соединение 4 (или торсионное соединение) и корпусной переводник 5. Рабочие органы, ротор и статор представляют собой зубчатую пару с внутренним косозубым зацеплением с разницей в числах зубьев, равной единице. Статор 2 выполнен в виде стального корпуса с привулканизированной резиновой обкладкой, имеющей внутренние винтовые зубья левого направления.
45

vk.com/club152685050 | vk.com/id446425943
1
2
3
Ротор 3, на наружной поверхности которого нарезаны винтовые зубья левого направления (на один зуб меньше, чем у статора), выполняется из коррози- онно-стойкой стали или из конструкционной стали с хромированием зубьев. Ось ротора смещена относительно оси статора на величину эксцентриситета e (условно равную половине высоты зуба).
Рис. 8.15. Конструкция винтового забойного двигателя: 1 – героторный механизм; 2 – статор; 3 – ротор;
4 –шарнирное соединение; 5 – переводник;
6 – шпиндель; 7 – вал шпинделя
4
5
6
Зубья ротора и статора, находясь в непрерывном контакте, образуют замыкающиеся на длине шага статора единичные рабочие камеры. Чтобы при работе двигателя создавались камеры высокого и низкого давления, необходимо соблюдение следующих условий:
– число заходов винтовой нарезки статора z1 должно быть на единицу больше числа заходов винта ротора
z2 ;
–отношения шага нарезки статора T к шагу винта
ротора t должно быть пропорционально соотношению
числа зубьев: T / t = z1 / z2 ;
– передаточное (кинематическое) отношение механизма двигателя i = z1 / z2 .
Таким образом, винтовой механизм одновременно выполняет роль двигателя и понижающего редуктора, что удачно решает проблему забойного привода
7 долота.
Буровой раствор, поступающий в двигатель, проворачивает ротор внутри обкладки статора. Ротор обкатывается по зубьям статора под действием неуравновешенных гидравлических сил. При этом ротор совершает планетарное движение: геометрическая ось
ротора вращается относительно оси статора против часовой стрелки (переносное движение), а сам ротор поворачивается по часовой стрелке (абсолютное вращение).
Для снижения отрицательного влияния такого вращения ротор двигателя соединяется с валом шпинделя шарнирным соединением (карданом) или торсионом – гибким стальным валом (рис. 8.16).
46
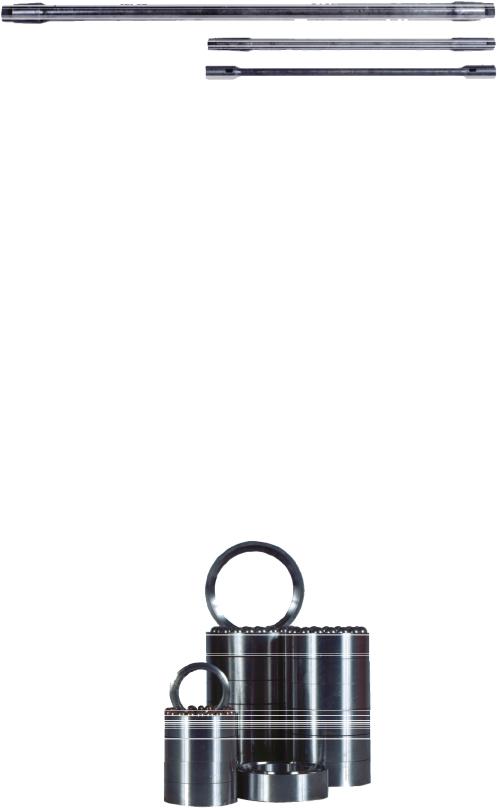
vk.com/club152685050 | vk.com/id446425943
Рис. 8.16. Гибкий вал и торсион
ООО «ВНИИБТ-Буровой инструмент»
Шпиндель 6 включает амортизированную осевую опору (типа ШШО), уплотнения – торцевые сальники, специальные распорные втулки. В отечественных ВЗД в качестве осевой опоры применяются преимущественно упорно-радиальные подшипники качения (рис. 8.17), радиальные верхняя резинометаллическая и нижняя металлическая опоры скольжения (табл. 8.4).
Таблица 8.4 Технические характеристики гибкого вала и торсиона фирмы
ООО «ВНИИБТ-Буровой инструмент»
Обозначение |
Диаметр наруж- |
Длина, |
Масса, кг |
Применение |
|
ный, мм |
мм |
|
|
Вал Д1-54 |
32 |
700 |
2,32 |
Д1-54 |
Вал гибкий Д-85 |
30 |
700 |
3,3 |
Д1-85 |
Торсион Д1-105 |
40 |
1840 |
14,5 |
Д1-105 |
Торсион Д1-127 |
50 |
1360 |
13 |
Д1-127 |
Рис. 8.17. Шариковые радиально-упорные подшипники
ООО «ВНИИБТ-Буровой инструмент»
47
vk.com/club152685050 | vk.com/id446425943
Таблица 8.5 Техническая характеристика шариковых радиально-упорных подшипников
фирмы ООО «ВНИИБТ-Буровой инструмент»
|
Диаметр |
Диаметр |
мм |
Количество |
кг |
|
|
|
Длина, |
Масса, |
|
||||
Обозначение |
наружный, |
внутрений, |
Применение |
||||
рядов |
|||||||
|
мм |
мм |
|
||||
|
|
|
|||||
|
|
|
|
|
|||
|
|
|
|
|
|
|
|
296 708 |
70 |
42 |
100 |
4 |
1,5 |
Д-85, Д-85М |
|
296 710 |
88 |
50 |
175 |
6 |
4,3 |
Д-105 |
|
296 712 |
105 |
60 |
175 |
6 |
6,0 |
Д-127 |
|
128 721Р* |
|
|
|
|
|
3СТШ1-195, ТВ1-195, |
|
165 |
105 |
105 |
15 |
4,4 |
Д1-195, ШО-195, |
||
|
|
|
|
|
|
ТРМ-195 |
Секция шпиндельная предназначена для восприятия осевых и радиальных нагрузок, действующих на двигатель.
Шпиндель является одним из главных узлов двигателя. Он передает осевую нагрузку на долото, воспринимает гидравлическую нагрузку, действующую на ротор двигателя, и уплотняет выходной вал, способствуя созданию необходимого перепада давления на долоте. Подшипники шпинделя должны также воспринимать радиальные нагрузки, возникающие от действия долота и шарнирного соединения.
Существующие компоновки двигателя во многом определены конструктивными средствами, обеспечивающими возможность выполнения планетарного движения ее элементов РО.
В серийно выпускаемых ВЗД наиболее распространен вариант компоновки (рис. 8.18), характеризующийся подвижным наружным элементом и планетарно вращающимся внутренним. Этот вариант имеет следующие преимущества:
–распределение полостей высокого и низкого давления осуществляется внутри РО, т.е. не требуется каких-либо дополнительных сальниковых устройств;
–имеется возможность непосредственно соединять статор с колонной бурильных труб (реактивный момент на статоре закручивает резьбовые соединения бурильных труб).
Двигатели с РО по варианту II используют в КНБК, предназначенных для поддержания вертикальности скважины или при необходимости – для расширения ствола, поскольку на наружной поверхности вращающегося статора весьма просто разместить опорно-центрирующие или режущие элементы. Однако этот вариант имеет существенный недостаток – необходимость уплотнения между неподвижным корпусом и вращающимся статором.
48