
технология бурения 2
.pdfvk.com/club152685050 | vk.com/id446425943
Известно, что измерение веса бурового инструмента и контроль осевой нагрузки на долото с помощью наземных приборов может производиться следующими методами:
–по натяжению неподвижного конца талевого каната;
–непосредственными измерениями на буровом крюке или вертлюге;
–измерением усилий, передаваемых кронблоком на подкронблочные балки.
Измерение веса бурового инструмента по натяжению неподвижного конца талевого каната, получившее широкое распространение, отличается от других простотой монтажа силоизмерительного датчика.
Этому способу измерения присущи следующие существенные недостатки:
–показания датчиков зависят от диаметра и жесткости каната. Поскольку профиль витого каната изменяется вдоль его длины, величина прогиба каната в датчике, установленном на буровой, может отличаться от прогиба, существовавшего во время тарировки. Вследствие этого ошибка
визмерениях может достигать 10–15 %;
–перемещение подвижного среднего ролика под действием измеряемой силы изменяет угол и, следовательно, вызывает нелинейность измерителя;
–при растяжении каната происходит его смещение относительно опорных роликов. Возникающие при этом в роликах силы трения являются причиной искажения в показаниях измерителей (до 2,5 %).
Измерение натяжения неподвижного конца каната может производиться также датчиком, размещенным между рамным брусом и канатом.
В этом случае одна сторона датчика прикрепляется к рамному брусу, а другая служит для присоединения неподвижного конца. Недостатками такой конструкции являются усложнение монтажа и демонтажа датчика и увеличение его габаритов, поскольку датчик полностью воспринимает растягивающие усилия на неподвижном конце. В настоящее время подобные конструкции используются лишь в буровых станках ЗИФ для колонкового геологоразведочного бурения (динамометры ДПУ механического типа и ДНР с магнитоупругим датчиком).
Также возможно измерение веса бурового инструмента непосредственно на буровом крюке или вертлюге. Данный метод является наиболее точным, поскольку полностью исключает влияние трения в талевой системе. Контроль можно осуществлять с помощью датчика, подвешенного между крюком и вертлюгом. В этом случае конструкция датчика вместе с элементами крепления получается громоздкой, увеличивается длина наземного бурового оборудования, что может затруднить работу бурильщика.
Наиболее целесообразным решением является установка датчика непосредственно на крюке или вертлюге. При этом обеспечивается
149
vk.com/club152685050 | vk.com/id446425943
лучшая защита датчиков от ударов, конструкция получается герметичной и компактной.
Размещение датчиков на вращающемся переводнике, связывающем вертлюг с квадратом, требует применения контактных токосъемов, что снижает надежность устройства.
Наиболее распространенным способом определения веса бурильной колонны и нагрузки на долото остается определение по гидравлическому индикатору веса (ГИВ). Работа, например, ГИВ-6 основана на определении веса и нагрузки на долото по натяжению концов талевого каната. Изменение показателей веса и нагрузки определяется в зависимости от оснастки талей, поэтому одно и то же показание индикатора веса может соответствовать разным действительным весам колонны.
Вследствие потерь на трение и жесткости каната натяжение в каждой струне талевого каната во время работы изменяется. Это объясняется тем, что натяжение в неподвижном и ходовом концах каната различно. Так как направление вращения роликов зависит от выполняемой операции (спуск или подъем инструмента), распределение усилий в канатах будет неодинаковым. При этом значения кажущейся нагрузки на долото в современных компьютеризированных станциях геолого-технических исследований (ГТИ) определяются автоматически после проведения операции «взвешивание инструмента», заключающейся в отрыве долота от забоя и подъеме инструмента над забоем на 3-4 метра с продолжением циркуляции. Однако операция «взвешивание» может быть использована при бурении скважин с углом искривления скважины не более 45 град. При углублении скважины, превышающем угол 45 град., контролировать истинный вес инструмента и нагрузку на долото практически невозможно. В этом случае требуется постоянный проворот ротором (либо верхним приводом) бурильной колонны с целью снижения трения колонны о стенки скважины, а также оперативный автоматизированный контрольи корректировка показателей нагрузки на долото.
Усовершенствование средств измерений, методов оперативного управления и контроля параметров бурения позволит обеспечить безаварийность проводки скважин в сложных горно-геологических и технологических условиях.
10.2. Средства измерений параметров бурения
Для контроля параметров процесса бурения скважины используется достаточно большое количество измерительного оборудования. Рассмотрим некоторые из средств измерений, входящих в состав буровых установок БУ 3000, ЭУК-1М и Т-502: датчик крутящего момента на роторе ДКМ и индикатор крутящего момента на роторе ГИМ-1; датчик расхода промывочной жидкости; датчик давления жидкости в манифольде; датчик определения указанных параметров по натяжению «мертвого» конца талевого
150
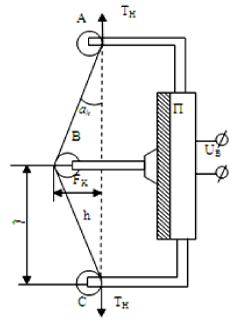
vk.com/club152685050 | vk.com/id446425943
каната; индикатор ГИМ-1; преобразователь частоты вращения ротора (бурильной колонны) ПЧР; преобразователь давления ПДР; верхний привод National Oilwell Varco с регулятором управления и контроля параметров бурения TDS-8.
Измерители веса бурового инструмента по способу монтажа датчика делятся на две группы. К первой группе относятся измерители, в которых датчики монтируются непосредственно на канате. В измерителях второй группы датчики устанавливаются в специальном устройстве, предназначенном для крепления каната.
Измерители с датчиками, монтируемые непосредственно на канате, работают по принципу измерения горизонтальной составляющей натяжения неподвижного конца талевого каната, предварительно преломленного на упругом элементе, что позволяет производить монтаж датчиков без рассечки каната. Принципиальная схема датчика показана на рисунке 10.2.
Талевый канат проходит через крайние ролики А, С и преломляется в среднем ролике В на угол αк, под действием веса бурового инструмента канат растягивается усилиями Тн. Горизонтальная составляющая растягивающих усилий Fk, действующая на средний ролик, определяется как
Fk = 2Tн sinαk.
Поскольку угол αк мал, то можно принять sinαk ≈ tgαk ≈ h/l.
Тогда
Tн = Fk∙l/2h.
С помощью гидравлического электрического или электромеханического преобразователя П, связанного со средним роликом, сила Fк преобразуется в пропорциональные величины давления или электрического напря-
жения Uв, которые измеряются вторичными приборами.
Рис. 10.2. Схема работы датчика веса бурильного инструмента (монтируется непосредственно на неподвижный конец талевого каната)
Для более точного измерения веса бурильного инструмента на установке поставлено устройство для крепления неподвижного конца каната со встроенным датчиком (рис. 10.3).
151
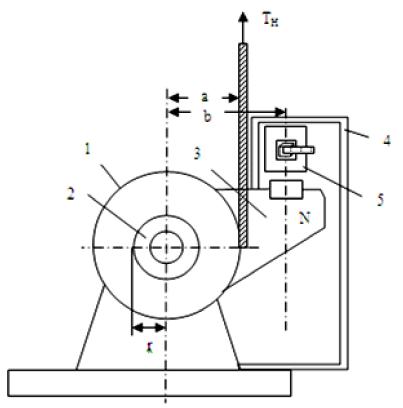
vk.com/club152685050 | vk.com/id446425943
Барабан 1, жестко связанный с рычагом 3, насажден на подшипник и может поворачиваться относительно оси 2. Конец каната наматывается тремя витками на барабан и закрепляется на рычаге. Под действием веса инструмента канат натягивается, барабан поворачивается, и рычаг давит на датчик 5, закрепленный на опоре 4.
Рис. 10.3. Устройство для крепления неподвижного конца талевого каната со встроенным датчиком
Уравнение моментов сил, действующих на барабан при увеличении нагрузки:
Тн∙а – Fтр∙r – N∙b = 0, |
(10.1) |
где Тн – натяжение неподвижного конца талевого каната; |
|
а, r – соответственно диаметры подшипника и барабана по линии каса- |
|
ния его канатом; |
|
N – усилие, передаваемое рычагом на датчик; |
|
b – расстояние между осью датчика и вертикальной осью барабана; |
|
Fтр – сила трения в подшипнике барабана. |
|
Fтр = Qб∙fб, |
(10.2) |
где Qб – нагрузка подшипника барабана; |
|
fб – коэффициент трения покоя подшипника барабана.
Изменяя расстояние b, можно изменять усилие N, передаваемое на датчик, и, следовательно, регулировать чувствительность измерителя.
Приведенная сила трения, определяющая порог чувствительности датчика к изменениям нагрузки на крюке:
152
vk.com/club152685050 | vk.com/id446425943
= б ∙ ∙ б ∙ = б ∙ , (10.3)
где п – число рабочих струн талевой системы.
Усилия, передаваемые рычагом, могут измеряться гидравлическими, электромеханическими и электрическими датчиками.
Для применяемых гидравлических и электромеханических датчиков предельная измеряемая нагрузка не превышает 49 кН, что значительно меньше предельных значений Т", поэтому значением N можно пренебречь.
Тогда |
= б ∙ |
∙ ∙ = б ∙ кр, |
|
|
(10.4) |
где Qкр – нагрузка на крюке.
Коэффициент трения покоя подшипника барабана равен примерно 0,01, а составляет от 0,5 до 0,75. Подставляя эти значения в формулу, получим, что уже при нагрузке на крюке, равной 100 Т (980 кН), величина порога чувствительности составляет примерно 0,5 Т (4,9 кН).
Натяжение концов талевого каната находится в зависимости от оснастки талей, поэтому одно и то же показание индикатора веса может соответствовать разным действительным весам колонны. В условиях покоя натяжение концов каната Р должно быть равно величине усилия на крюке Qкр (вес колонны), деленной на число струн талевого каната п, несущих талевый блок:
Р = Q/n |
(10.5) |
Вследствие потерь на трение и жесткость каната натяжение в каждой струне талевого каната во время работы изменяется. Это объясняется тем, что натяжение в неподвижном и ходовом концах каната различно. Так как направление вращения роликов зависит от выполняемой операции (спуск или подъем инструмента), распределение усилий в канатах будет неодинаковым.
Усилия в ходовом конце талевого каната, по данным А. В. Си-
нельникова, определяются следующими зависимостями: |
|
||
– в условиях покоя |
= кр |
|
|
– при спуске |
|
(10.6) |
|
= |
∙ кр |
|
|
|
(10.7) |
153
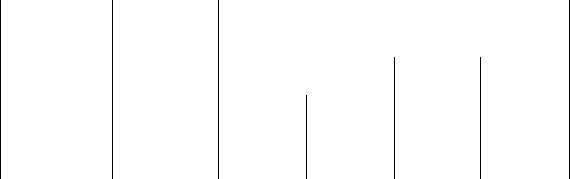
vk.com/club152685050 | vk.com/id446425943
В таблице 10.1 представлено соотношение между нагрузкой на крюке и усилиями на концах талевого каната (по А. В. Синельникову).
Таблица 10.1 Соотношение между нагрузкой на крюке и усилиями
на концах талевого каната
Состояние |
Обозначение |
|
Оснастка талевой системы |
|
|||
талевого ме- |
усилия |
2×3 |
|
3×4 |
4×5 |
|
5×6 |
ханизма |
|
|
|
Число рабочих струн |
|
||
|
|
4 |
|
6 |
8 |
|
10 |
Подъем |
Р |
0,262 |
|
0,177 |
0,136 |
|
0,111 |
Спуск |
Р1 |
0,243 |
|
0,158 |
0,117 |
|
0,09 |
|
|
0,236 |
0,154 |
1,113 |
|
|
|
|
|
|
|
|
|
|
|
Покой |
Р0 |
0,254 |
0,172 |
0,132 |
|
0,01 |
|
|
|
0,250 |
0,167 |
0,125 |
|
|
|
|
|
|
|
|
– при подъеме: |
=∙ ∙ кр |
|
|
|
|
(10.8) |
||
где η = 0,98 – к.п.д. одного вращающегося ролика. |
|
|
||
|
Усилия в неподвижном конце талевого каната: |
|
|
|
|
– в условиях покоя: |
|
|
|
|
– при спуске: |
S0 = Qкр /η; |
(10.9) |
|
|
S1 = Р1∙ηм /ηn; |
(10.10) |
||
|
– при подъеме: |
|||
|
= Р2∙ ηn /ηм, |
(10.11) |
||
|
S2 |
|||
где ηм = 0,99 – к.п.д. последнего ролика кронблока под неподвижным кон- |
||||
цом талевого каната. |
|
|
|
|
|
При определении веса бурильной колонны и нагрузки на долото при |
помощи гидравлического индикатора веса цена деления шкалы индикатора находится по паспорту, прилагаемому к каждому прибору. Когда долото находится над забоем скважины, вес бурильной колонны Q будет выражен величиной А, показанной индикатором веса. Так как отсчет по шкале ве-
дется от 10-го деления, цена деления С = Q/(А – 10). |
|
Приближенно вес бурильной колонны |
|
= ж К, |
(10.12) |
где g – ускорение свободного падения;
d и d1 – наружный и внутренний диаметры труб, м; L – длина колонны бурильных труб, м;
ρ – плотность материала труб, кг/м3;
154
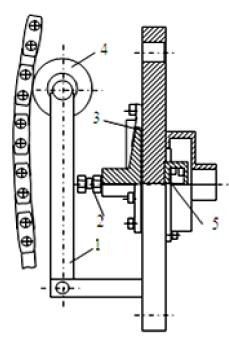
vk.com/club152685050 | vk.com/id446425943
ρж – плотность бурового раствора, кг/м3; К ≈ 1,1 – коэффициент, учитывающий вес замков. Вес бурильной колонны
Q = Lq + Lqз/l , |
(10.13) |
где L – длина колонны бурильных труб, равная глубине скважины в данный момент, м;
l – длина одной свечи, м;
q – вес 1 м бурильных труб, кН; qз – вес замка, кН.
Если в момент бурения показание индикатора веса равно В, то нагрузка на долото равна Р = (А – В)С.
Наиболее важным параметром, определяющим условия работы бурильной колонны, ее состояние в процессе бурения, является момент на роторе. При управлении процессом бурения скважин осуществлялся контроль момента вращения бурильной колонны.
Крутящий момент устанавливают по изменению упругих свойств вала, углу его закручивания, тангенциальным напряжениям на поверхности или по изменению силы активного тока ротора электродвигателя. В качестве преобразователей крутящего момента в электрический сигнал использовались индуктивныe, индукционные, емкостные, магнитоупругие, струнные, тензометрические типы датчиков.
Момент на роторном столе контролировался по усилию, передаваемому ротором подроторному основанию. Крутящий момент измерялся независимо от направления вращения ротора и натяжения цепной передачи.
Рис. 10.4. Датчик крутящего момента на роторе ДКМ
155
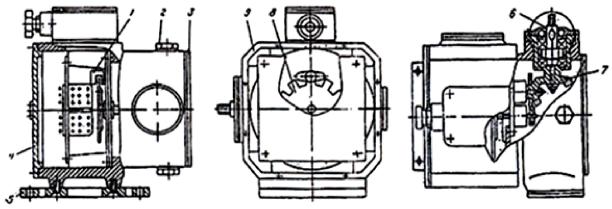
vk.com/club152685050 | vk.com/id446425943
Крутящий момент роторного стола, приводящего во вращение колонну труб с инструментом, определялся по изменению натяжения цепной передачи датчиком ДКМ, который устанавливают под ведущей ветвью цепи привода. Датчик работает следующим образом (рис. 10.4). При помощи регулировочного болта 2 и тарельчатой пружины 3 создается начальная стрела прогиба цепи привода роторного стола в месте соприкосновения звездочки 4, установленной на рычаге 1, с цепью. При изменении крутящего момента натяжение цепи меняется, что приводит к перемещению траверсы 5. Перемещение последней влечет за собой деформацию тарельчатой пружины и смещение рычага 1, связанного с измерительной обмоткой преобразователя и вторичным прибором. Погрешность измерения не превышает 2,5 %.
Также на установке в качестве вспомогательного оборудования устанавливался индикатор крутящего момента на роторе ГИМ-1.
Контроль частоты вращения ротора на установке осуществляется датчиками, которые установлены в измерительном комплексе СКУБ. Для измерения частоты вращения ротора применялся преобразователь ПЧР (рис. 10.5). ПЧР работает следующим образом. Вращение входного вала 6 с коническим зубчатым колесом 7, кинематически связанным с валом привода посредством зубчатых передач, передается диску 8 с прямоугольными зубцами, число которых равно 10. При вращении диска 8 его зубцы поочередно проходят через щель катушки бесконтактного датчика 1. Генерируемые в катушках высокочастотные колебания затухают при перекрывании щели катушки зубцами диска. На вход ПЧР поступают пакеты импульсов, ширина и длительность которых зависят от частоты вращения диска.
Рис. 10.5. Преобразователь для замера частоты вращения ротора ПЧР
В качестве привода бурильной колонны и замера момента на установке Т-502 (буровая компания KCA Deutag) наиболее часто используется верхний привод Oilwell Varco – TDS-8 (рис. 10.6).
156
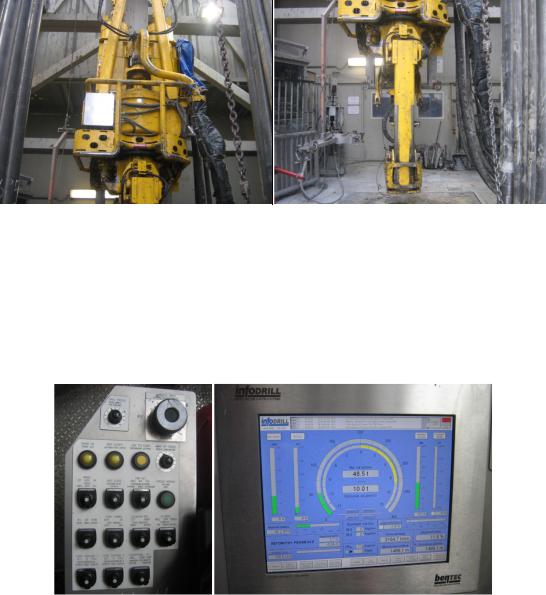
vk.com/club152685050 | vk.com/id446425943
Рис. 10.6. Верхний привод Oilwell Varco
Замер параметров бурения – давления в системе Р и частоты вращения бурильной колонны n, нагрузки на долото G – фиксируется на блоке управления и контроля TDS-8. На рисунке 10.7 представлен вид пульта (блока) – регулятора управления и контроля параметров бурения на верхнем приводе Varco.
Рис. 10.7. Пульт – регулятор управления и контроля параметров бурения на верхнем приводе Varco
Неотъемлемой частью управления параметрами режимов бурения является контроль давления промывочной жидкости в манифольде буровой установки. Осуществление контроля данного параметра позволяет судить о работе насоса и, например, объемного двигателя (ВЗД), состоянии всей циркуляционной системы, об эффективности промывки скважины и изменении гидравлических потерь в элементах циркуляционной системы.
Для контроля давления в нагнетательной линии насосов часто применяются механические (показывающие) и электрические (с электрическим выходным сигналом) манометры. Преобразователь давления ПДР (рис. 10.8) используется в комплексе станции контроля процесса бурения (СКУБ) и предназначен для преобразования давления ПЖ
157
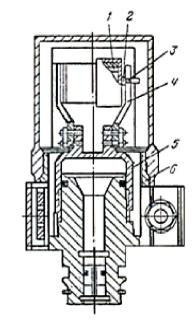
vk.com/club152685050 | vk.com/id446425943
в нагнетательной линии в пропорциональный электрический сигнал напряжением 0…10 В.
Преобразователь давления ПАР работает следующим образом (рис.
10.8).
Давление жидкости воздействует на чувствительный элемент – мембрану 5 с кронштейнами 4, которая, прогибаясь, перемещает плунжер 2 дифференциального трансформатора. Перемещение плунжера 2 преобразовывается преобразователем ПДР в пропорциональное напряжение на выходе.
Рис. 10.8. Датчик давления бурового раствора
Чувствительный элемент преобразователя – мембрана 5 навернута на резьбовую втулку, которая является составной частью свaрнoгo цилиндрического корпуса 6 и служит для присоединения к манифольду буровой. С мембраной 5 жестко связаны кронштейны 4, на которых установлены катушка 1 с экраном и плунжep 2. В первоначальное положение относительно катушки 1 плунжер 2 устанавливается при помощи резьбового соединения с кронштейном 4 и фиксируется болтом 3.
10.3. Технические средства и технологии, направленные на оптимизацию режимов бурения, оперативного управления и автоматизацию процесса углубления скважин
На сегодняшний день оперативный контроль (управление) за режимами бурения c учетом корректировки текущего положения ствола гори-
158