
Методические указания 1 (основа)
.pdf2.8 . Нормирование сварочных и наплавочных работ
Основное время, затрачиваемое на восстановление детали ручной электродуговой и автоматической сваркой (мин), определяется по следующей формуле
То |
0 ,06 F L Kc |
Kс , |
|
||
|
н J |
Где F – площадь поперечного сечения шва (валика), мм2; L – длина шва, мм;
γ– плотность наплавляемого металла, г/см3 (сталь – 7,8; чугун – 7,0; медь – 8,9; латунь
–8,6; цинк – 7,0; алюминиевые сплавы – 2,8);
Кп - коэффициент разбрызгивания металла (Кп = 0,9); αн - коэффициент наплавки (αн = 12 г/А ч – при автоматической и полуавтоматиче-
ской наплавке); αн = 8 г/Ач - при ручной сварке (наплавке); αн - при вибродуговой одноэлектронной наплавке);
J - cила сварочного тока, А;
Кс – коэффициент, учитывающий сложность выполняемой работы (Кс =1 – при автоматической сварке (наплавке) плоскостей сверху; Кс = 1,5 – при ручной наплавке цилиндрических деталей диаметром d= 40…50 мми сварке по горизонтальной плоскости снизу Кс = 1,3 – при ручной наплавке цилиндрических деталей диаметром d> 50 мм и сварке на вертикальной плоскости). Кс
Величины силы тока J и коэффициент наплавки αн выбираются в зависимости от марки свариваемого (наплавляемого) материала и марки и диаметра электрода, по табл. 2.7.
Вспомогательное время Тв на установку, поворот и снятие изделия определяется по табл. 2.8 и 2.9.
Дополнительное время Тоб и Тот составляет 3…6% от оперативного времени Топ. Подготовительно-заключительное время Тпз в расчетах принимают 10…20 минут на
партию деталей.
|
|
|
|
Таблица 2.7 |
|
Параметры электросварки и наплавки |
|
||
|
|
|
|
|
Марка |
Применяемость |
Диаметр |
Сила свароч- |
Коэффициент |
электрода |
электрода |
электрода, мм |
ного тока, А |
наплавления |
1 |
2 |
3 |
4 |
5 |
СМ-5 |
Сварка углеродистых и |
4…6 |
160…280 |
7,2 |
ЦМ-7, ИМ-7С |
низколегированных |
4…6 |
160…320 |
10,6 |
ВСЦ-1, 2, 3 |
сталей |
3…5 |
80…220 |
10,0 |
УОНИ-13/45 |
|
2…6 |
45…240 |
8,5…10 |
УОНИ-13/55 |
|
2…6 |
45…240 |
8,5…10 |
УОНИ-13/85 |
|
2…6 |
45…240 |
8,5…10 |
МР-1, 3 |
|
3…6 |
100…320 |
7,8…8,5 |
ОЗС-2, 4, 6 |
|
3…5 |
80…250 |
8,5 |
|
|
|
|
|
ОЗН-25ОУ |
Наплавка деталей из |
|
|
|
|
ОЗН-30ОУ |
малосреднеуглероди- |
4,5 |
170…240 |
8,2…8,4 |
|
ОЗН-35ОУ |
стых и низколегирован- |
||||
|
|
|
|||
ОЗН-40ОУ |
ных сталей |
|
|
|
|
|
|
|
|
|
|
ОМЧ-1 |
Сварка и наплавка дета- |
6…8 |
250…450 |
|
|
МНЧ-1, 2 |
лей из чугуна |
3…5 |
90…100 |
15,2 |
|
ОЗЧ-1, 2 |
|
3…4 |
60…120 |
|
|
|
|
|
|
|
Таблица 2.8
Вспомогательное время на установку, поворот и снятие изделия (мин) при ручной и механизированной наплавке (сварке)
Элементы операции |
|
|
Масса изделия, кг |
|
||
до 5 |
5…10 |
|
10…15 |
15…20 |
20…200 |
|
|
|
|||||
Поднести, уложить, снять и от- |
|
|
|
|
|
|
нести деталь: |
|
|
|
|
|
|
- работа на столе |
0,24 |
0,3 |
|
0,49 |
0,53 |
2,7 |
- работа в приспособлении |
0,35 |
0,58 |
|
0,71 |
0,78 |
2,7 |
Повернуть деталь |
0,12 |
0,19 |
|
0,24 |
0,23 |
1,6 |
Таблица 2.9
Вспомогательное время на установку, закрепление и снятие детали, мин (автоматизированная наплавка)
Способ установки и |
|
|
|
Масса изделия, кг |
|
|
|
||||
закрепления детали |
до 1 |
1…3 |
3…5 |
5…8 |
8…12 |
12…20 |
20…30* |
30…50* |
|||
|
1 |
|
2 |
3 |
4 |
5 |
6 |
7 |
8 |
9 |
|
В |
самоцентрирую- |
|
|
|
|
|
|
|
|
||
щем патроне с кре- |
0,2 |
0,27 |
0,32 |
0,38 |
0,48 |
0,6 |
1,9 |
2,1 |
|||
плением ключом |
|
|
|
|
|
|
|
|
|||
В |
патроне с |
цен- |
0,26 |
0,33 |
0,38 |
0,45 |
0,55 |
0,7 |
2,3 |
2,4 |
|
тром задней бабки |
|||||||||||
|
|
|
|
|
|
|
|
||||
В |
центрах с |
наде- |
0,20 |
0,24 |
0,29 |
0,35 |
0,42 |
0,5 |
1,6 |
1,7 |
|
ванием хомутика |
|||||||||||
|
|
|
|
|
|
|
|
||||
В центре без наде- |
0,12 |
0,15 |
0,18 |
0,22 |
0,26 |
0,31 |
1,4 |
1,5 |
|||
вания хомутика |
|||||||||||
|
|
|
|
|
|
|
|
||||
На |
планшайбе с |
|
|
|
|
|
|
|
|
||
угольником в |
цен- |
0,31 |
0,37 |
0,43 |
0,47 |
0,51 |
0,6 |
2,0 |
2,1 |
||
трирующем |
при- |
||||||||||
|
|
|
|
|
|
|
|
||||
способлении |
|
|
|
|
|
|
|
|
|

* - при работе с подъемником.
2.9. Нормирование гальванических работ
Основное время, необходимое для наращивания требуемого слоя металла в гальванических ваннах определяется по формуле
T
60 1000h ,
o |
Pk C |
|
Где То – основное время, мин;
h – толщина наращиваемого слоя, мм;
γ – плотность осаждаемого металла, г/см3; Рк – катодная плотность тока, А/дм2; С – электрохимический эквивалент, г/Ач; η – выход по току, в процентах.
Значения выбираются по таблице 2.10.
Таблица 2.10
Основные данные при гальваническом восстановлении детали
|
|
Плотность |
|
Электро- |
|
|
|
|
|
химиче- |
|
||
|
Толщина |
осаждаемого |
Плотность |
Выход по |
||
Вид покрытия |
ский экви- |
|||||
слоя, мм |
металла, |
тока, А/дм2 |
току, % |
|||
|
|
г/см3 |
|
валент, |
|
|
|
|
|
|
г/Ач |
|
|
1 |
2 |
3 |
4 |
5 |
6 |
|
Никелирование |
0,015… |
8,9 |
3 |
1,095 |
95 |
|
|
0,02 |
|
|
|
|
|
Железнение |
0,2…0,3 |
7,8 |
30…50 |
1,042 |
95 |
|
Цинкование |
0,02…0,01 |
7,1 |
2 |
1,220 |
95 |
|
Меднение кислое |
0,003… |
8,9 |
3 |
1,185 |
100 |
|
|
0,03 |
|
|
|
|
|
Хромирование износо- |
0,2…0,3 |
6,9 |
30…60 |
0,324 |
13 |
|
стойкости |
|
|
|
|
|
|
Хромирование защитно- |
0,001 |
6,9 |
30…25 |
0,324 |
13 |
|
декоротивное |
|
|
|
|
|
|
Вспомогательное время определяется по следующей формуле |
|
|||||
|
|
Тв Т'в Т"в , |
|
|
где Тв – вспомогательное время, мин; Т’в – вспомогательное время, перекрывающееся основным временем, мин;
Т”в – вспомогательное время, не перекрывающееся основным временем, мин. Вспомогательное перекрываемое время затрачивается на монтаж деталей в приспо-
соблении, защиту мест, не подлежащих покрытию (восстановлению). Данные работы выполняются в период работы ванны и поэтому в расчет не включаются.
Вспомогательное неперекрываемое время затрачивается на загрузку и выгрузку деталей из ванны и другие работы при неработающей ванне. Данное время включается в норму времени на операцию и выбирается по таблице 2.11.
Таблица 2.11
Нормы вспомогательного неперекрываемого времени, мин
Масса приспособление с |
|
Время на одно приспособление |
|
||
специальное |
одиночная |
|
|
||
деталями, кг |
кораина |
подвеска |
|||
приспособл. |
подвеска |
||||
|
|
|
|||
1 |
2 |
3 |
4 |
5 |
|
до 1,0 |
0,09 |
0,05 |
0,06 |
0,07 |
|
1…2,0 |
0,1 |
0,06 |
0,07 |
0,08 |
|
2,0…4,0 |
0,13 |
0,07 |
0,08 |
0,09 |
|
4,0…8,0 |
0,16 |
0,11 |
0,12 |
0,13 |
|
8,0…12,0 |
0,20 |
0,15 |
0,16 |
0,17 |
|
12,0…16,0 |
0,25 |
- |
0,19 |
0,21 |
Норма штучно-калькуляционного времени на одну деталь определяется
Тшк |
То Т'В 0 ,12( То Т"В ) |
|
Тnз |
, |
m |
|
|||
|
|
N |
где m – количество деталей, одновременно загружаемых в ванну; N – количество деталей в партии.
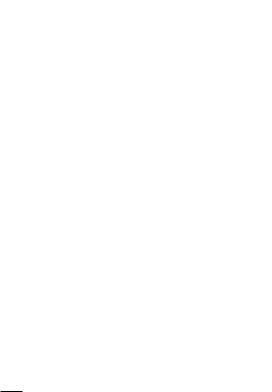
2.10. Нормирование разборочно-сборочных работ
Штучно-калькуляционное время на разборочно-сборочные работы определяется по формуле
|
К |
, |
|
|
|
|
Тшк Тшт Тоn 1 |
|
|
|
|
|
|
|
|
|
|
|||
|
100 |
|
|
|
|
|
где К- коэффициент, учитывающий сумму времени (ТВ Тоб Тоt |
Тnз ) |
|||||
Коэффициент К выбирается по таблице 2.12. |
|
|
|
|
|
|
|
|
|
|
|
|
Таблица 2.12 |
Значение коэффициента К % |
|
|
|
|||
|
|
|
|
|
|
|
Наименование и состав затрат рабочего времени по |
|
|
|
|
Значение |
|
элементам |
|
|
сборка |
|
разборка |
|
1 |
|
|
2 |
|
|
3 |
Время на организационно-техническое обслуживание |
|
|
|
|
|
|
рабочего места: |
|
|
|
|
|
|
раскладка и уборка инструмента, уборка рабочего места |
|
|
4 |
|
|
5 |
в процессе работы, обслуживание оборудования, смена |
|
|
|
|
|
|
и заточка инструмента |
|
|
|
|
|
|
Время на отдых и естественные надобности |
|
|
7 |
|
|
7 |
Подготовительно-заключительное время: |
|
|
|
|
|
|
изучение задания и технологии изготовления; ознаком- |
|
|
3 |
|
|
2 |
ление с чертежом детали; получение инструмента, при- |
|
|
|
|
||
|
|
|
|
|
|
|
способлений; сдача готовой продукции |
|
|
|
|
|
|
2.11. Нормирование работ на металлорежущих станках
Штучно-калькуляционное время на выполнение операций механической обработки в единичном и серийном производстве определяется расчетно-аналитическим методом по формуле
Тшк Тшт ТNnз ,
где Тшк – штучно-калькуляционное время, мин; Тшт – штучное время, мин;
Тnз – подготовительно-заключительное время, мин; N – количество деталей в обрабатываемой партии.
Штучное время определяется по следующей формуле
Тшт То ТВ Тоб Тот ,
где То – основное время, мин; ТВ – вспомогательное время, мин;
Тоб – время на обслуживание рабочего места, мин (принимается 2…4% от оперативного времени, кроме шлифовальных, для которых оно принимается 3,5…13%);
Тот – время перерывов на отдых, мин (принимается 4…6% от оперативного). Оперативное время состоит из основного (технологического) и вспомогательного
времени, т.е.
Топ То ТВ ,
Основное время определяется по формуле
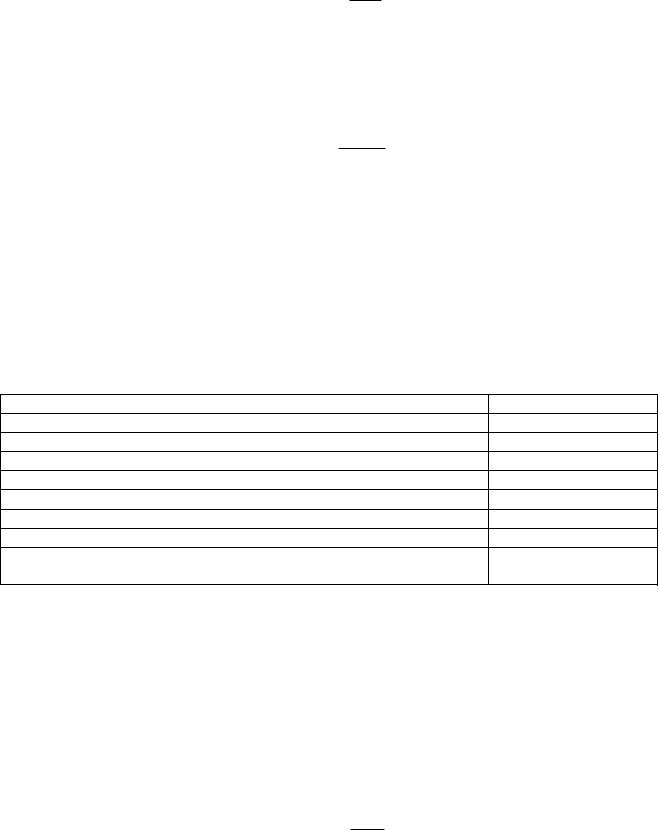
То Lp i , n S
где Lp – расчетная длина обработки, мм; i – число проходов;
n – частота вращения детали или инструмента, об/мин; S – подача, м/об (принимается по таблице П.3.1…П.3.5
Частота вращения детали или инструмента определяется по формуле
n
1000 V ,
Д
где V – расчетная (табличная) скорость резания, м/мин;
Д – диаметр обрабатываемой детали или инструмента, мм.
Для операций сверления или растачивания расчетная длина обработки определяется
Lp l l1 l2 ,
Где l – длина (глубина) обрабатываемого отверстия, мм;
l1 + l2 =0,3Д – величина врезания и выхода инструмента, мм; Д – диаметр сверла, мм.
Вспомогательное время ТВ выбирается по таблице 2.13
Вспомогательное время на установку и снятие детали cо станка
Способ установки детали и характер выверки
1
В центрах
В центрах с люнетом
В самоцентрирующем патроне:
без выверки
в самоцентрирующем патроне с выверкой
В цанговом патроне
В четырехкулачковом патроне с необработанной и по контуру не размеченной поверхностью
Подготовительно-заключительное время определяется по формуле
Тпз Тшк N K ,
где К – коэффициент, учитывающий потери времени на подготовительно-заключительные работы.
В зависимости от серийности производства коэффициент К принимается:
- для единичного, мелкосерийного |
К = 0,14…0,18; |
- для среднесерийного |
К = 0,08…0,13; |
- для крупносерийного |
К = 0,04…0,08. |
По известной величине штучно-калькуляционного времени определяется норма выра-
ботки
HТсм ,
Тшк
где H – норма выработки, шт;
Тсм – продолжительность смены, мин.
ПРИЛОЖЕНИЕ 3
ТАБЛИЦЫ ПАРАМЕТРОВ РЕЖИМОВ ОБРАБОТКИ, КОЭФФИЦИЕНТОВ И ПОКАЗАТЕЛЕЙ СТЕПЕНЕЙ, ИСПОЛЬЗУЕМЫХ В РАСЧЕТНЫХ ФОРМУЛАХ
Таблица П.3.1
Подачи при черновом наружном точении резцами и пластиками из твердого сплава и быстрорежущей стали
Диаметр |
Сталь конструкционная углеродистая легированная |
|
|
Чугун |
|
||||
|
|
Подача S мм/об, при глубине резания t, мм |
|
|
|
||||
детали, мм |
|
|
|
|
|
||||
До 3 |
3…5 |
5…8 |
8…12 |
До 3 |
3…5 |
|
5…8 |
8…12 |
|
|
|
||||||||
до 20 |
0,3-0,4 |
|
|
|
|
|
|
|
|
20…40 |
0,4-0,5 |
0,3-0,4 |
|
|
0,4-0,6 |
|
|
|
|
40…60 |
0,5-0,9 |
0,4-0,8 |
0,3-0,7 |
|
0,6-0,9 |
0,5-0,8 |
|
0,4-0,7 |
|
60…100 |
0,6-1,2 |
0,5-1,1 |
0,5-0,9 |
0,4-0,8 |
0,8-1,4 |
0,7-1,2 |
|
0,6-0,10 |
0,5-0,9 |
100…4000 |
0,8-1,3 |
0,7-1,2 |
0,6-1,0 |
0,5-0,9 |
1,0-1,5 |
0,8-1,9 |
|
0,8-1,1 |
0,6-0,9 |

|
|
|
|
|
|
|
|
|
|
|
|
|
|
|
|
Таблица П.3.2 |
|
|
|
|
Подачи при чистовом точении стали и чугуна |
|
|
|
|||||||||
|
|
|
|
|
|
|
|
|
|
|
|
|
|
|
|
|
Параметр шероховатости |
|
|
|
|
|
|
Радиус при вершине резца r, мм |
|
|
|
||||||
|
0,4 |
|
0,8 |
|
1,2 |
|
1,6 |
|
2,0 |
|
2,4 |
|||||
поверхности, мкм |
|
|
|
|
|
|
||||||||||
|
|
|
|
|
|
Подача S мм/об |
|
|
|
|||||||
|
|
|
|
|
|
|
|
|
|
|
|
|||||
0,63 |
|
|
|
0,07 |
|
0,10 |
|
0,12 |
|
0,14 |
|
0,15 |
|
0,17 |
||
1,25 |
|
|
|
0,10 |
|
0,13 |
|
0,165 |
|
0,19 |
|
0,21 |
|
0,23 |
||
2,50 |
|
|
|
0,144 |
|
0,20 |
|
0,246 |
|
0,29 |
|
0,32 |
|
0,35 |
||
|
20 |
|
0,25 |
|
0,33 |
|
0,42 |
|
0,49 |
|
0,55 |
|
0,60 |
|||
|
40 |
|
0,35 |
|
0,51 |
|
0,63 |
|
0,72 |
|
0,80 |
|
0,87 |
|||
|
60 |
|
0,47 |
|
0,66 |
|
0,81 |
|
0,94 |
|
1,04 |
|
1,14 |
|||
|
|
|
|
|
|
|
|
|
|
|
|
|
|
|
|
Таблица П.3.3 |
|
|
Подачи при сверлении стали, чугуна и цветных сплавов сверлами из быстрорежущей стали |
|
|||||||||||||
|
|
|
|
|
|
|
|
|
|
|
|
|
|
|
|
|
Диаметр |
|
|
|
|
|
Сталь |
|
|
|
|
|
|
Чугун и цветные сплавы |
|||
сверла, |
|
|
|
|
|
|
|
|
Подача S мм/об |
|
|
|
||||
мм |
|
НВ 160 |
НВ 160…240 |
|
|
НВ 240…300 |
|
НВ 300 |
|
НВ 170 |
|
НВ 170 |
||||
4…6 |
|
0,13…0,19 |
0,10…0,15 |
|
|
0,07…0,11 |
|
0,06…0,09 |
|
0,18…0,27 |
|
0,12…0,18 |
||||
6…8 |
|
0,19…0,26 |
0,15…0,20 |
|
|
0,11…0,14 |
|
0,09…0,12 |
|
0,27…0,36 |
|
0,18…0,24 |
||||
8…10 |
|
0,26…0,32 |
0,20…0,25 |
|
|
0,14…0,17 |
|
0,12…0,15 |
|
0,36…0,45 |
|
0,24…0,31 |
||||
10…12 |
|
0,32…0,36 |
0,25…0,28 |
|
|
0,17…0,20 |
|
0,15…0,17 |
|
0,45…0,55 |
|
0,31…0,35 |
||||
12…16 |
|
0,36…0,43 |
0,28…0,33 |
|
|
0,20…0,23 |
|
0,17…0,20 |
|
0,55…0,66 |
|
0,35…0,41 |
||||
16…20 |
|
0,43…0,49 |
0,33…0,38 |
|
|
0,23…0,27 |
|
0,20…0,23 |
|
0,66…0,76 |
|
0,41…0,47 |
||||
20…25 |
|
0,49…0,58 |
0,38…0,43 |
|
|
0,27…0,32 |
|
0,23…0,26 |
|
0,76…0,89 |
|
0,47…0,54 |
||||
25…30 |
|
0,58…0,62 |
0,43…0,48 |
|
|
0,32…0,35 |
|
0,26…0,29 |
|
0,89…0,96 |
|
0,54…0,60 |
||||
30…40 |
|
0,62…0,78 |
0,48…0,58 |
|
|
0,35…0,42 |
|
0,29…0,35 |
|
0,96…1,19 |
|
0,60…0,71 |
||||
40…50 |
|
0,78…0,89 |
0,58…0,56 |
|
|
0,42…0,48 |
|
0,35…0,40 |
|
1,19…1,35 |
|
0,71…0,81 |

Таблица П.3.4
Подачи при черновом фрезеровании торцевыми, цилиндрическими и дисковыми фрезами
Мощность |
Сталь |
|
|
Чугун |
||
станка, |
|
|
Подача на зуб фреза Sz , мм при твердом сплаве |
|
|
|
кВт |
Т15 К6 |
|
Т5 К10 |
ВК6 |
|
ВК8 |
5…10 |
0,09…0,18 |
|
0,12…0,18 |
0,14…0,24 |
|
0,20…0,29 |
Св. 10 |
0,12…0,18 |
|
0,15…0,24 |
0,18…0,28 |
|
0,25…0,38 |
|
|
|
|
|
|
|
|
Таблица П.3.5 |
|
|
Параметры резания при шлифовании |
|
|
|
|||
|
|
|
|
|
|
|
|
|
Обрабатываемый |
Характеристика |
|
Скорость |
Скорость |
|
Глубина |
Продольная |
Радиальная |
процесса |
|
круга, V м/с |
заготовки, |
|
шлифования, |
подача, |
подача, |
|
материал |
|
|
||||||
шлифования |
|
|
Vз, м/мин |
|
t, мм |
S, мм |
Sp, мм/об |
|
|
|
|
|
|||||
Конструкционматериалыные |
|
|
Круговое наружное шлифование |
|
|
|||
С продольной подачей: |
|
|
|
|
|
|
|
|
|
|
|
|
|
|
|
|
|
|
предварительное |
|
30…35 |
12…25 |
|
0,01…0,025 |
(0,03…0,7)В |
|
|
окончательное |
|
|
15…55 |
|
0,005…0,015 |
(0,2…0,4)В |
|
|
Врезное: |
|
|
|
|
|
|
|
|
предварительное |
|
30…35 |
30…50 |
|
|
|
0,0025…0,075 |
|
окончательное |
|
|
20…40 |
|
|
|
0,001…0,005 |

|
|
|
|
|
|
|
|
Таблица П.3.6 |
|
|
|
|
Значение допусков, мм |
|
|
|
|
|
|
|
|
|
|
|
|
|
|
|
|
Диаметр отверстия, |
|
|
|
Квалитеты |
|
|
|
|
|
мм |
7 |
8 |
9 |
10 |
11 |
12 |
13 |
|
14 |
10…18 |
0,018 |
0,027 |
0,043 |
0,070 |
0,110 |
0,180 |
0,270 |
|
0,430 |
18…30 |
0,021 |
0,033 |
0,052 |
0,084 |
0,130 |
0,210 |
0,330 |
|
0,520 |
30…50 |
0.025 |
0,039 |
0,062 |
0,100 |
0,160 |
0,250 |
0,390 |
|
0,620 |
50…80 |
0,030 |
0,046 |
0,074 |
0,120 |
0,190 |
0,300 |
0,460 |
|
0,740 |
80…120 |
0,035 |
0,054 |
0,087 |
0,140 |
0,220 |
0,350 |
0,540 |
|
0,870 |
120…180 |
0,040 |
0,063 |
0,100 |
0,160 |
0,250 |
0,400 |
0,630 |
|
1,000 |
180…250 |
0,045 |
0,072 |
0,115 |
0,185 |
0,290 |
0,460 |
0,720 |
|
1,150 |
|
|
|
|
|
|
|
|
Таблица П.3.7 |
|
Минимальные припуски на черновое обтачивание и растачивание заготовок, |
|
||||||
|
|
полученных горячей штамповкой из проката |
|
|
||||
|
|
|
|
|
|
|
||
Диаметр заготовки, |
Для горячештампованных заготовок из стали |
Для проката обычной точности |
||||||
|
|
Припуск Zmin на диаметр при длине, мм |
|
|
||||
мм |
|
|
|
|
||||
до 120 |
120…250 |
|
260…500 |
до 120 |
|
120…250 |
260…500 |
|
|
|
|
||||||
до 50 |
1,7 |
2,0 |
|
2,4 |
1,3 |
|
1,5 |
2,0 |
50…120 |
2,0 |
2,2 |
|
2,6 |
1,5 |
|
1,8 |
2,2 |
120…250 |
2,2 |
2,4 |
|
2,7 |
1,8 |
|
2,2 |
2,4 |