
технология ремонта масляного насоса дизеля и его привода
.pdf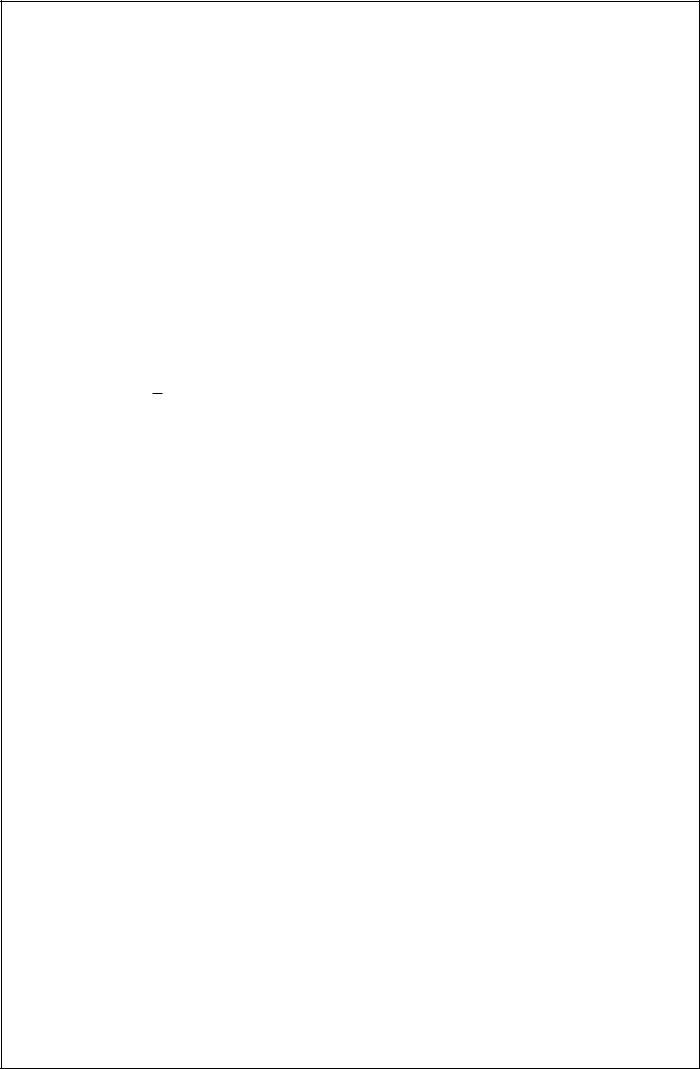
мастерских 12, 18 м (допустимо 6 м); - высота здания должна определяться с учетом выемки и перемещения агре-
гатов и деталей локомотивов.
Длина ремонтного стойла ТР-3, равная 90,14 м, что обеспечивает ремонт всех серий грузовых локомотивов при крупно-агрегатном методе ремонта. При проектировании здания текущего ремонта ТР-3 я расположил:
на пути номер 1 размещаем 2 стойла для ремонта локомотива.на пути номер 2 размещаем 3 стойла.
путь номер 3 оставляем сквозным. Тогда длина цеха составит:
А = L |
× 3 = 90,14 × 3 = 270,42 м. |
ТР |
3 |
|
|
В соответствии с требованиями ГОСТ 23837–79, в части шага строительства колон, принимаем длину цеха равную А = 276 м. Ширину участка принимаем В = 24 м. Унифицированная ширина зданий, участков нового строительства локомотивных и мотор-вагонных депо равна 24 м с разбивкой по осям железнодорожных путей 5-7-7-5 м.
Найдем площадь и объем участка:
|
S |
участка |
= А × В = 276 × 24 = 6624 м |
2 |
. |
|
|
|
|
|||||||
|
|
|
|
|
|
|||||||||||
|
|
|
|
|
|
|
|
|
|
|
|
|
|
|
||
|
|
|
|
|
|
|
|
|
|
|
|
|
||||
|
|
|
|
|
|
|
|
|
|
|
||||||
|
Vучастка = Sучастка × h = 6624 ×13,2 = 87436,8 м3. |
|
||||||||||||||
|
|
|
|
|
|
|
|
|
|
|
|
|
|
|||
|
Полученные данные сведем в таблицу 1. |
|
|
|
|
|
|
|
|
|||||||
|
|
|
|
|
|
|
|
|
|
|
|
|
|
|
||
|
Таблица 1 |
|
|
|
|
|
|
|
|
|
|
|
|
|
||
|
|
|
|
|
|
|
|
|
|
|
|
|||||
Вид |
|
Число путей в |
|
Число сто- |
Длина це- |
Ширина |
Высота |
|
|
Площадь |
Объем це- |
|||||
ремонта |
|
цехе |
|
ил (шт) |
ха, м |
цеха, м |
цеха, м |
|
|
цеха, м |
ха, м3 |
|||||
|
|
|
|
|
|
|
|
|
|
|
|
|
||||
ТР-3 |
|
|
3 |
|
|
5 |
276 |
276 |
13,2 |
|
6624 |
87437 |
||||
|
|
|
|
|
|
|
|
|
|
|
|
|
|
|
|
|
|
|
|
|
|
|
|
|
|
|
|
|
|
|
|
|
|
|
|
|
|
|
|
|
|
|
|
|
|
|
|
|
|
|
|
|
|
Лист |
|
|
|
|
|
|
|
|
|
|
|
|
|
|
|
|
|
КП 23.02.06.15.03.01 ПЗ |
|
|
|
|
|
|
|
|
|
|
|
|
|
|
|
|
|
|
|
|
|
|
||
|
|
|
|
|
|
|
|
|
|
|
|
||||||||
|
|
|
|
|
|
|
|
|
|
|
|
|
|
|
|
11 |
|
|
|
|
|
|
|
|
|
|
|
|
|
|
|
|
|
|
|
|
|
|
|
|
Изм |
|
|
Лист |
|
|
№ документа |
|
|
Подпись |
|
|
Дата |
|
|
|
|
|
|
|
|
|
|
|
|
|
|
|
|
|
|
|
|
|
|||||
|
|
|
|
|
|
|
|
|
|
|
|
|
|
|
|
|
|
|
|
|
|
|
|
|
|
|
|
|
|
|
|
|
|
|
|
|
|
|
|
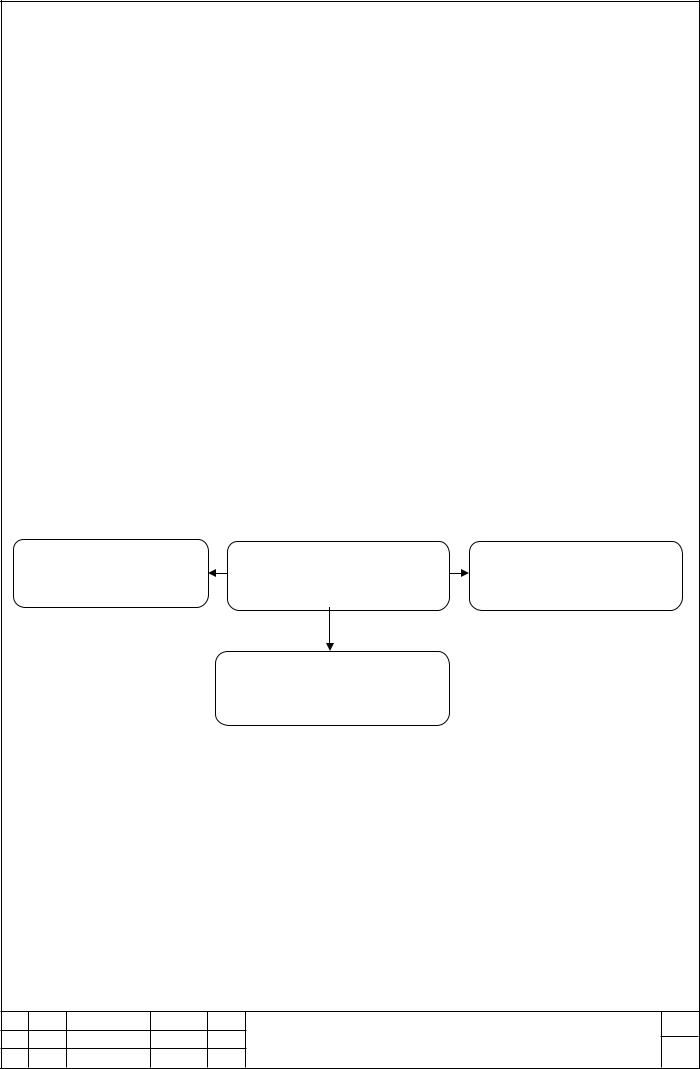
|
2 Раздел 2 Разработка производственного |
отделения участка |
(отделе- |
||
ния, цеха) |
|
|
|
|
|
|
2.1 Общие сведения проектируемого отделений депо по ремонту дизеля |
||||
|
В депо, отделения по ремонту дизеля определяют следующий набор опера- |
||||
ций: |
|
|
|
|
|
|
-Демонтаж узлов и агрегатов; |
|
|
||
|
-Мойка и очистка агрегатов 4 способами (механический, абразивный, |
||||
|
термический, химический) перед началом ремонтом; |
|
|||
|
-Безразборная проверка технического состояния; |
|
|||
|
-Дефектовка деталей; |
|
|
||
|
-Ремонт деталей и сборочных единиц; |
|
|
||
|
-Сборка деталей; |
|
|
|
|
|
-Испытание объектов ремонта; |
|
|
||
|
Схема связи участка с другими подразделениями депо показан на рисунке 2 |
||||
Механизмы и узлы |
Отделение по ремонту |
Топливный насос вы- |
|||
коленчатого вала |
топливной аппаратуры |
сокого давления |
|||
|
|
|
Механизмы и узлы ко- |
|
|
|
|
|
ленчатого вала |
|
|
|
Рисунок 2 Схема связи участка с другими подразделениями депо |
||||
|
Полный объём работы участка цеха определяется в натурных единицах: |
||||
число отремонтированных локомотивов или комплектов колесных пар, топливный |
|||||
насос высокого давления т.п., которое напрямую зависит от объема работы всего |
|||||
депо. В данном случае натурной единицей считается Дизель внутреннего сгорания, |
|||||
тепловоза 2ТЭ10 |
|
|
|
|
|
|
Для организации работы цеха нужно упорядочить производственную про- |
||||
грамму, то есть размер работ, который нужно исполнить силами ремонтных рабо- |
|||||
|
|
|
|
|
Лист |
|
|
|
КП 23.02.06.15.03.01 ПЗ |
12 |
|
Изм Лист |
№ документа |
Подпись |
Дата |
|
|
|
|
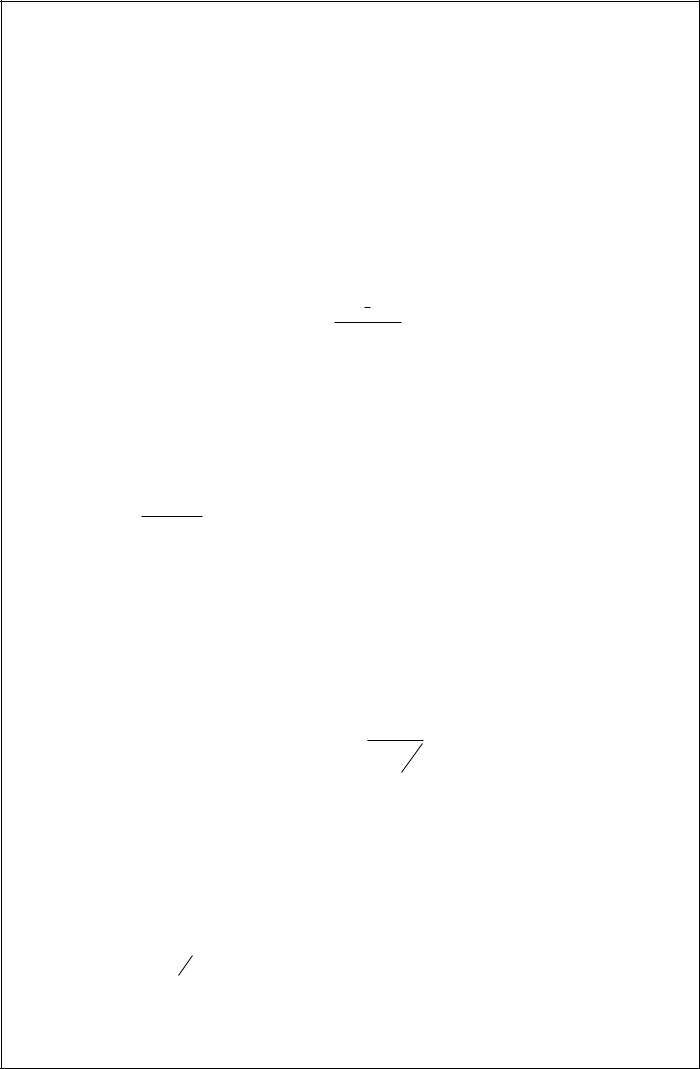
чих данного цеха. Данный размер зависит от программы ремонтов локомотивов,
которая задана.
При определении объема работы цеха нужно принимать во внимание его технологические и технические связи с другими цехами и подразделениями депо.
Кроме того, при расчете надо иметь в виду, что квалификация работ у состава ра-
бочих цеха, так и уровни разряда работ в цехе могут отличаться.
Месячный объем работы отделения определяется по следующей формуле:
|
|
М |
n |
|
|
|
ТР 3 |
М |
мес |
|
, |
|
|
12 |
|
|
|
|
где МТР-3 – годовой объем работы, МТР-3 = 300шт.
n – Количество дизелей на 2 секциях тепловозе 2ТЭ10, n = 2шт;
М |
|
|
300 2 |
50шт. |
|
мес |
12 |
||||
|
|
|
|||
|
|
|
|
(1.7)
Кроме плановой ремонтируемой продукции учитывается и объем работ в запас, для пополнения его, не выполнившими поставленный межремонтный про-
бег (1.9):
|
|
|
М |
|
|
|
М |
клад |
= |
мес |
• p, |
||
100 |
0 |
|||||
|
|
|
||||
|
|
|
|
|||
|
|
|
0 |
|
||
|
|
|
|
|
где Ммес - месячный объем работы, Ммес = 50шт;
р — процент увеличения объема работ в отделении (р = 10 %).
(1.8)
|
|
|
|
|
|
|
М клад |
50 |
10% |
5шт |
|
|
|
|
|
||||||||||
|
|
|
|
|
|
|
|
|
|
|
|
|
|
|
|
|
|||||||||
|
|
|
|
|
|
|
100 |
0 0 |
|
|
|
|
|
||||||||||||
|
|
|
|
|
|
|
|
|
|
|
|
|
|
|
|
|
|
|
|
||||||
|
|
|
|
|
|
|
|
|
|
|
|
|
|
|
|
|
|
|
|
|
|
|
|
|
|
|
|
|
|
|
|
|
|
|
|
|
|
|
|
|
|
|
|
|
|
|
|
|
|
|
|
|
|
|
|
|
|
|
|
|
|
|
|
|
|
|
|
|
|
|
|
|
|
|
Лист |
|
|
|
|
|
|
|
|
|
|
|
|
|
|
|
|
|
|
|
|
|
|
|
КП 23.02.06.15.03.01 ПЗ |
|
|
|
|
|
|
|
|
|
|
|
|
|
|
|
|
|
|
|
|
|
|
|
|
|
|
|
|||
|
|
|
|
|
|
|
|
|
|
|
|
|
|
|
|
|
|
|
|
|
13 |
|
|
||
|
|
|
|
|
|
|
|
|
|
|
|
|
|
|
|
|
|
|
|
|
|
|
|
|
|
|
Изм |
|
|
Лист |
|
|
№ документа |
|
|
|
|
Подпись |
|
|
Дата |
|
|
|
|
|
|
|
|||
|
|
|
|
|
|
|
|
|
|
|
|
|
|
|
|
|
|
|
|||||||
|
|
|
|
|
|
|
|
|
|
|
|
|
|
|
|
|
|
|
|
|
|
|
|
|
|
|
|
|
|
|
|
|
|
|
|
|
|
|
|
|
|
|
|
|
|
|
|
|
|
|
|

Следует предусмотреть внеплановый ремонт дизеля 2ТЭ10 от общего объема работы отделения. Число внеплановых ремонтов принимается за 10 % от Ммес,
тогда (2.0):
Мвнепл = |
|
Ммес |
•10 0 0 |
|
|
|
|||
|
100 |
0 |
(2.0) |
|
|
|
|
0 |
М |
|
|
50 |
10% |
5шт |
||
внепл |
100 |
0 |
|||||
|
|
|
|
||||
|
|
|
0 |
|
|||
|
|
|
|
|
|||
|
|
|
|
|
|
Окончательный объем работы отделения Моконч определяется, по формуле
(2.1):
М |
оконч |
= М |
мес |
+М |
клад |
+М |
внепл |
|
|
|
|
М |
оконч |
50 5 5 60(шт) |
|
|
|
|
|
|
(2.1)
Получаем, что полный объём работы отделения по ремонтному цеху будет равен 60 дизелей 2ТЭ10, беря в расчет 2 секции.
2.2 Разработка технологического процесса ремонта масляного насоса на отделений по ремонту дизеля
2.2.1 Назначения, конструкция, технические данные масляного насоса дизеля локомотива 2ТЭ10
Масляная система и ее оборудование должны: подавать масло в достаточном количестве к трущемся деталям дизеля; поддерживать определенный температурный режим масла; обеспечить необходимую частоту масла.
Соблюдение перечисленных требований и к маслу, и к системе повышают экономичность и надежность дизеля. Масляная система тепловоза подразделяется
|
|
|
|
|
|
|
|
|
|
|
|
|
|
|
|
|
|
|
|
|
|
|
|
|
|
|
|
|
|
|
|
|
|
|
|
|
Лист |
|
|
|
|
|
|
|
|
|
|
|
|
|
|
|
|
|
КП 23.02.06.15.03.01 ПЗ |
|
|
|
|
|
|
|
|
|
|
|
|
|
|
|
|
|
|
|
|
|
|
||
|
|
|
|
|
|
|
|
|
|
|
|
||||||||
|
|
|
|
|
|
|
|
|
|
|
|
|
|
|
|
14 |
|
|
|
|
|
|
|
|
|
|
|
|
|
|
|
|
|
|
|
|
|
|
|
|
Изм |
|
|
Лист |
|
|
№ документа |
|
|
Подпись |
|
|
Дата |
|
|
|
|
|
|
|
|
|
|
|
|
|
|
|
|
|
|
|
|
|
|||||
|
|
|
|
|
|
|
|
|
|
|
|
|
|
|
|
|
|
|
|
|
|
|
|
|
|
|
|
|
|
|
|
|
|
|
|
|
|
|
|
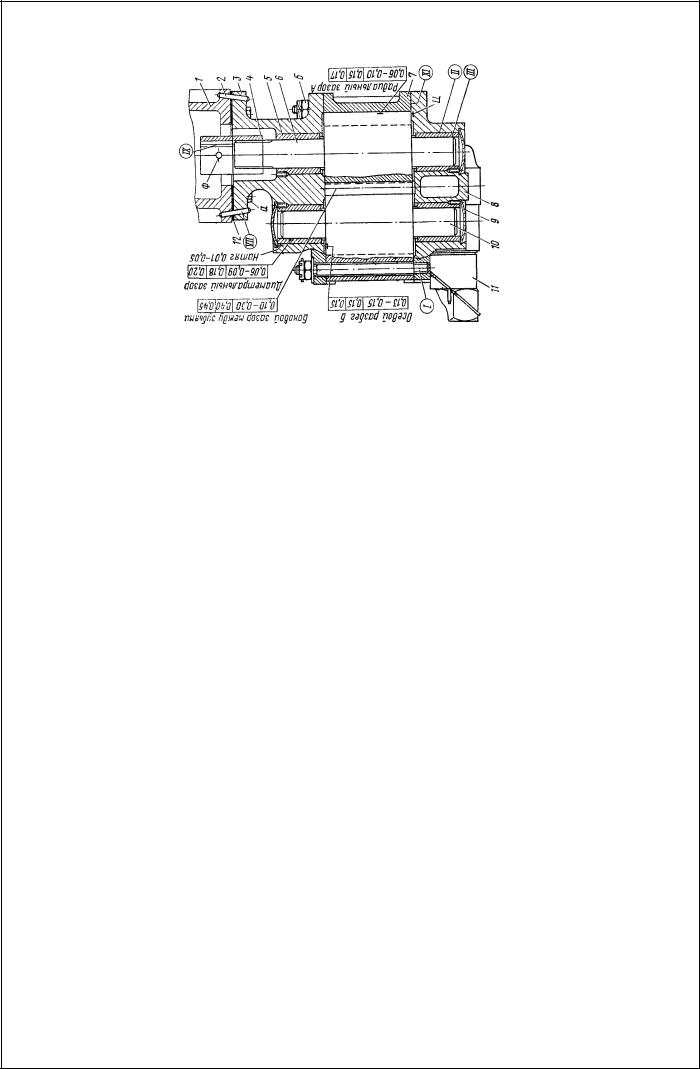
на внутреннею и внешнюю рисунок 1
Рисунок 1 Внутренняя система смазки и масляного охлаждения поршня ди-
зеля:
1 – подвеска коренного подшипника; 2 – коленчатый вал; 3 - трубка для перетока масла от коренного подшипника к шатунному; 4 – подвод масла из кол-
лектора к коренному подшипнику; 5 – шатунный подшипник; 6 шатун; 7 поршень;
8 – поршневой палец.
Внешняя масляная система (рисунок 1) включает в себя масляные насосы,
охлаждающие устройства, фильтры и соединяющие их трубопроводы. Перед пус-
ком дизеля, для того чтобы заполнить его систему маслом и подвести смазку ко всем трущимся частям до начала работы, включают масло-прокачивающий агре-
гат.
2.2.2 Основные неисправности масляного насоса тепловоза 2ТЭ10, при-
чины их возникновения и способы предупреждения
Характерными неисправностями масляных насосов являются: уменьшение подачи; падение давления в нагнетательной полости; трещины и износ корпусов, подшипниковых планок, крышек, втулок; разрушение подшипников. Падение давления и подачи насоса является следствием увеличенного бокового зазора между зубьями шестерен и торцевого зазора между шестернями и корпусными деталями.
|
|
|
|
|
|
|
|
|
|
|
|
|
|
|
|
|
|
|
|
|
|
|
|
|
|
|
|
|
|
|
|
|
|
|
|
|
Лист |
|
|
|
|
|
|
|
|
|
|
|
|
|
|
|
|
|
КП 23.02.06.15.03.01 ПЗ |
|
|
|
|
|
|
|
|
|
|
|
|
|
|
|
|
|
|
|
|
|
|
||
|
|
|
|
|
|
|
|
|
|
|
|
||||||||
|
|
|
|
|
|
|
|
|
|
|
|
|
|
|
|
15 |
|
|
|
|
|
|
|
|
|
|
|
|
|
|
|
|
|
|
|
|
|
|
|
|
Изм |
|
|
Лист |
|
|
№ документа |
|
|
Подпись |
|
|
Дата |
|
|
|
|
|
|
|
|
|
|
|
|
|
|
|
|
|
|
|
|
|
|||||
|
|
|
|
|
|
|
|
|
|
|
|
|
|
|
|
|
|
|
|
|
|
|
|
|
|
|
|
|
|
|
|
|
|
|
|
|
|
|
|
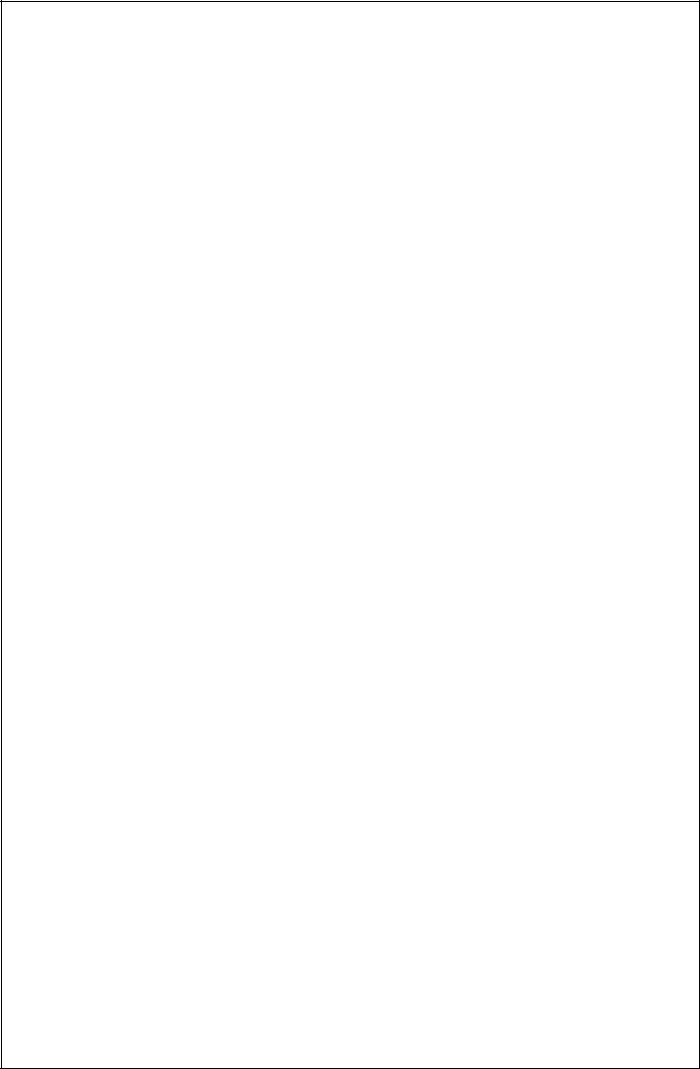
Внасосах центробежного типа наблюдается ослабление посадки крыльчатки на валу, износ по окружности крыльчатки, всасывающей головки и корпуса, нарушение плотности сальникового уплотнения, трещины в корпусе, износ и дефекты подшипников.
Втопливоподкачивающих насосах нарушается плотность сальникового уплотнения, снижается подача из-за износа втулки, вала, возникают трещины в корпусе, крышке.
При техническом обслуживании ТО-3 у топливоподкачивающего насоса проверяют наличие утечек топлива, надежность крепления и состояние резиновой муфты, у водяных насосов — каплепадение через сальник, допускается 30—100 капель в 1 мин при л = 400 об/мин коленчатого вала и не более 20 капель в 1 мин для текстолитового уплотнения
При текущем ремонте ТР-1 основной топливоподкачивающий насос снимают с тепловоза для проверки подачи на стенде с последующим контролем соосности после установки на место. У масляного насоса с синхронными зубчатыми колесами (подача 95 м3/ч) снимают крышку, осматривают состояние координационных зубчатых колес и проверяют надежность их крепления.
При текущем ремонте ТР-2 у насосов снимают всасывающую головку и обследуют крепление гайки и прочность посадки крыльчатки на валу. Масляный насос с подачей 95 м3/ч с дизеля снимают для осмотра состояния подшипников, вала привода, муфты и зубчатого поводка. Другие масляные насосы снимают на текущем ремонте ТР-2 при обнаружении дефектов.
2.2.3 Способы очистки, осмотра и контроля технического состояния
масляного насоса тепловоза 2ТЭ10
Различают четыре вида очистки — механическую, химическую, гидравли-
ческую и комбинированную (химико-механическую). К механическим относятся следующие способы очистки: пневматический, гидравлический, механическим ин-
струментом, абразивный.
Пневмоочистку применяют для сдувания с очищаемых поверхностей сухой
|
|
|
|
|
|
|
|
|
|
|
|
|
|
|
|
|
|
|
|
|
|
|
|
|
|
|
|
|
|
|
|
|
|
|
|
|
Лист |
|
|
|
|
|
|
|
|
|
|
|
|
|
|
|
|
|
КП 23.02.06.15.03.01 ПЗ |
|
|
|
|
|
|
|
|
|
|
|
|
|
|
|
|
|
|
|
|
|
|
||
|
|
|
|
|
|
|
|
|
|
|
|
||||||||
|
|
|
|
|
|
|
|
|
|
|
|
|
|
|
|
16 |
|
|
|
|
|
|
|
|
|
|
|
|
|
|
|
|
|
|
|
|
|
|
|
|
Изм |
|
|
Лист |
|
|
№ документа |
|
|
Подпись |
|
|
Дата |
|
|
|
|
|
|
|
|
|
|
|
|
|
|
|
|
|
|
|
|
|
|||||
|
|
|
|
|
|
|
|
|
|
|
|
|
|
|
|
|
|
|
|
|
|
|
|
|
|
|
|
|
|
|
|
|
|
|
|
|
|
|
|
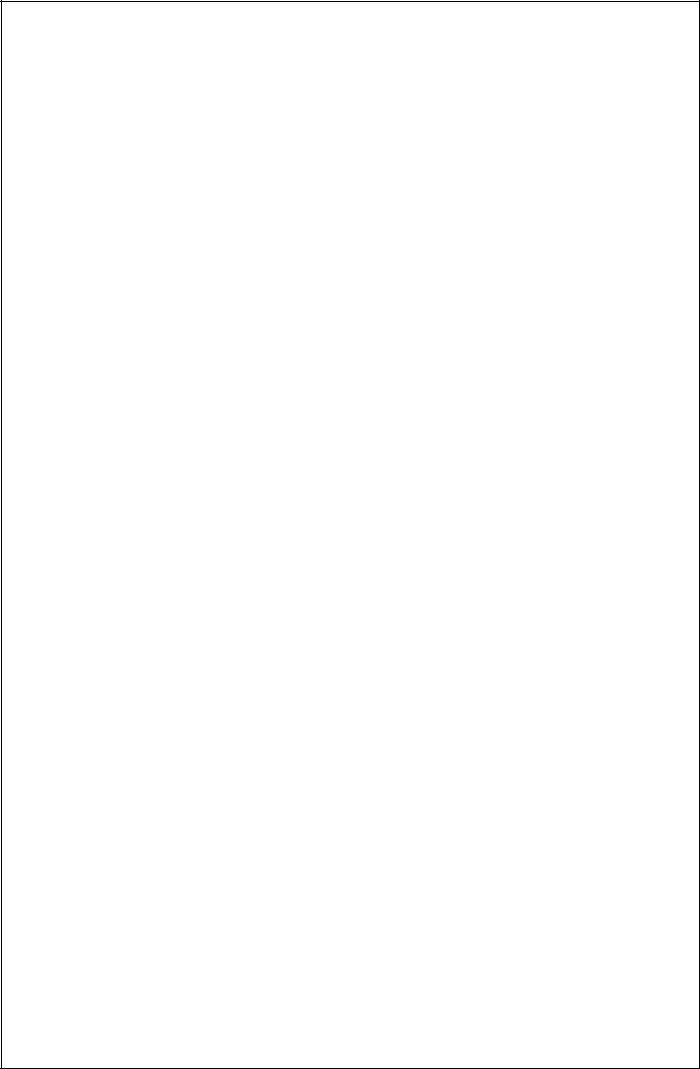
пыли сильной струей воздуха, подаваемого через сопловой наконечник. Давление воздуха перед сопловым наконечником рекомендуется поддерживать в пределах
(1,5÷5,0) 105 Па. Очистка ведется в специально оборудованных помещениях с мощной вытяжной вентиляцией, продувочных камерах или шкафах и на площад-
ках.
Гидравлическая очистка подразделяется на гидро-душевую и гидро-
циркуляционную. Гидро-душевая очистка в сочетании с набором моющих щеток широко используется для наружной мойки.
В цилиндрах масло соприкасается с горячими газами (температура 1700–
2000 С), нагретыми поверхностями цилиндров и поршней (температура 300–
400 °С). При этом масло частично сгорает и коксуется. Часть масла запекается в виде тонкой лаковой пленки на стенках цилиндров и днищах поршней, образуя нагар. При работе дизеля частицы нагара, сажи, золы под давлением газов из каме-
ры сгорания через зазоры между гильзами, поршнями и поршневыми кольцами попадают в картер дизеля и накапливаются в нем масло, в процессе циркуляции стекающее из поршней в картер, разбрызгивается и, соприкасаясь с воздухом кар-
тера, окисляется. При окислении масла в нем образуются как твердые частицы, так и густые осадки, которые, отлагаясь на стенках маслопроводов, уменьшают их се-
чения и затрудняют циркуляцию масла. Кроме того, в масло постоянно попадают мелкие металлические частицы, в результате истирания поверхностей деталей ди-
зеля и его агрегатов. Из-за циркуляции старого масла увеличиваются износ тру-
щихся деталей. Неблагоприятной особенностью твердых частиц любого проис-
хождения, накапливающихся в смазочном масле, является их высокая дисперс-
ность (размеры частиц до 1–2 мкм).
В результате накопления твердых частиц, продуктов сгорания и окисления ухудшаются смазочные свойства масла. Так называемое «старение» масла в про-
цессе работы требует периодической его замены, так как «состарившееся» масло увеличивает износа деталей дизеля, но и может способствовать его увеличению из-
за высокого содержания абразивных частиц. Для продления срока службы масла из него необходимо отделять накапливающиеся твердые частицы и осадки. При хо-
|
|
|
|
|
|
|
|
|
|
|
|
|
|
|
|
|
|
|
|
|
|
|
|
|
|
|
|
|
|
|
|
|
|
|
|
|
Лист |
|
|
|
|
|
|
|
|
|
|
|
|
|
|
|
|
|
КП 23.02.06.15.03.01 ПЗ |
|
|
|
|
|
|
|
|
|
|
|
|
|
|
|
|
|
|
|
|
|
|
||
|
|
|
|
|
|
|
|
|
|
|
|
||||||||
|
|
|
|
|
|
|
|
|
|
|
|
|
|
|
|
17 |
|
|
|
|
|
|
|
|
|
|
|
|
|
|
|
|
|
|
|
|
|
|
|
|
Изм |
|
|
Лист |
|
|
№ документа |
|
|
Подпись |
|
|
Дата |
|
|
|
|
|
|
|
|
|
|
|
|
|
|
|
|
|
|
|
|
|
|||||
|
|
|
|
|
|
|
|
|
|
|
|
|
|
|
|
|
|
|
|
|
|
|
|
|
|
|
|
|
|
|
|
|
|
|
|
|
|
|
|
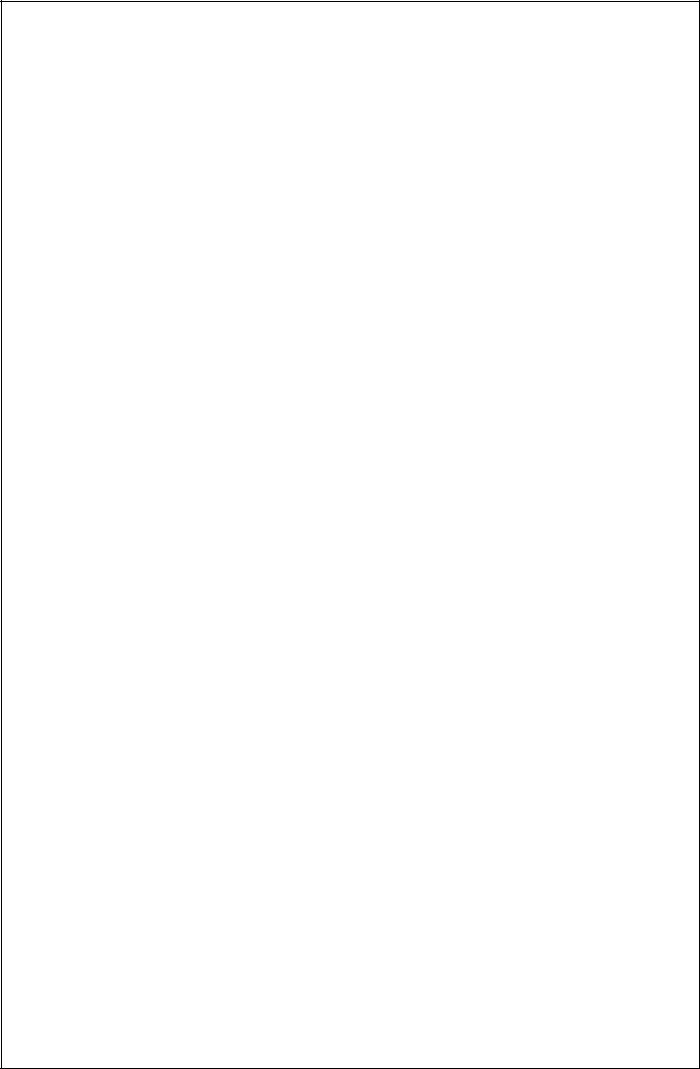
рошей очистке срок службы масла можно увеличить в два-три раза с одновремен-
ным уменьшением износа деталей дизеля. Очистка масла в системах смазки тепло-
возных дизелей осуществляется непрерывной его фильтрацией. Для надежности очистки система фильтрации масла состоит обычно из нескольких различных фильтров, включенных последовательно или параллельно.
2.2.4 Технология ремонта масляного насоса
Для снятия насоса с дизеля отсоединяют всасывающий и нагнетательный трубопроводы, выпрессовывают конические штифты, отворачивают гайки шпилек и снимают насос. Чтобы судить о степени износа зубьев зубчатых колес, корпуса и подшипниковых планок, перед разборкой насоса измеряют радиальный зазор меж-
ду зубьями колес и корпусом насоса и осевой разбег зубчатых колес между под-
шипниковыми планками. С увеличением этих размеров сверх допустимых снижа-
ется подача насоса ввиду того, что часть масла из нагнетательной полости перете-
кает во всасывающую. Радиальный зазор желательно замерить при рабочем поло-
жении зубчатых колес, для чего через всасывающий или нагнетательный патрубок между зубьями вставляют свинцовую проволоку диаметром 2-3 мм и медленным вращением за зубчатый поводок прокатывают проволоку между зубьями. В таком положении зубчатых колес щупом измеряют зазор между каждым колесом и кор-
пусом со стороны всасывающего и нагнетательного патрубков, который должен быть в пределах 0,20-0,30 мм. По толщине прокатанной свинцовой проволоки определяют боковой зазор между зубьями шевронных зубчатых колес (0,55-1,0
мм). Осевой разбег зубчатых колес (0,25-0,4 мм) определяют при снятой крышке с помощью индикаторного приспособления при установленной подшипниковой планке.
При разборке насоса отворачивают гайки крепления и снимают зубчатый поводок, переднюю крышку с поршнем осевого упора, с хвостовика ведущего зуб-
чатого колеса снимают упорный шарикоподшипник с шайбой, с хвостовиков ве-
домого зубчатого колеса отворачивают по два болта и снимают упорные шайбы.
|
|
|
|
|
|
|
|
|
|
|
|
|
|
|
|
|
|
|
|
|
|
|
|
|
|
|
|
|
|
|
|
|
|
|
|
|
Лист |
|
|
|
|
|
|
|
|
|
|
|
|
|
|
|
|
|
КП 23.02.06.15.03.01 ПЗ |
|
|
|
|
|
|
|
|
|
|
|
|
|
|
|
|
|
|
|
|
|
|
||
|
|
|
|
|
|
|
|
|
|
|
|
||||||||
|
|
|
|
|
|
|
|
|
|
|
|
|
|
|
|
18 |
|
|
|
|
|
|
|
|
|
|
|
|
|
|
|
|
|
|
|
|
|
|
|
|
Изм |
|
|
Лист |
|
|
№ документа |
|
|
Подпись |
|
|
Дата |
|
|
|
|
|
|
|
|
|
|
|
|
|
|
|
|
|
|
|
|
|
|||||
|
|
|
|
|
|
|
|
|
|
|
|
|
|
|
|
|
|
|
|
|
|
|
|
|
|
|
|
|
|
|
|
|
|
|
|
|
|
|
|
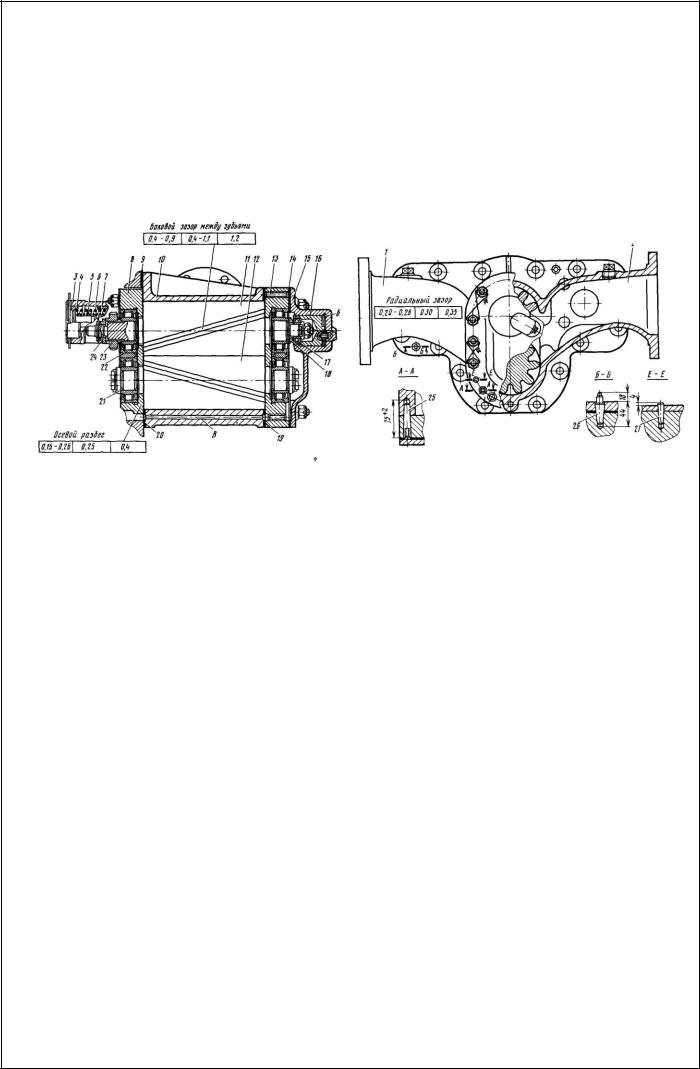
Подшипниковые планки отжимают выжимными болтами от корпуса, вынимают из корпуса зубчатые колеса ведущее и ведомое. При отсутствии на них меток спарен-
ности наносят их керном или краской. Сохраняют фиксирующие штифты, которые при сборке устанавливают на свои места. В редукционном клапане освобождают нажимную гайку, вынимают из корпуса пружину и клапан.
Масляный насос дизеля типа Д100:
12 — всасывающий и нагнетательный патрубки, 3— корпус редукционного клапана; 4 — нажимная гайка, 5,6 — пружины, 7 — клапан, 8 внутренняя планка подшипников, 9,14,19,20—прокладки, 10— корпус; 11,12 ведущее и ведомое зуб-
чатые колеса; 13 — наружная планка подшипников, 15 — крышка:
16 — поршень; 17 — шарикоподшипник; 18,21 — шайбы, 22 — роликовый подшипник; 23— зубчатый поводок; 24 — гайка; 25,26,27 - конические штифты;
В— полость, В — канал
Вредукционном клапане проверяют на станке посадочное место и прити-
рают его к корпусу. Уменьшение толщины дна клапана допускается до 2 мм. Кла-
пан с трещинами заменяют. Обследуют состояние пружины, ослабшие или лоп-
нувшие пружины заменяют. Корпус клапана с трещинами и сорванной резьбой под нажимную гайку заменяют. Если в насосе не заменяют подшипниковые планки,
зубчатые колеса и рабочие поверхности корпуса не повергались восстановлению,
то насос собирают в такой последовательности: на цапфы зубчатых колес монти-
руют внутренние кольца подшипников, а в планки подшипниковнаружные коль-
|
|
|
|
|
|
|
|
|
|
|
|
|
|
|
|
|
|
|
|
|
|
|
|
|
|
|
|
|
|
|
|
|
|
|
|
|
Лист |
|
|
|
|
|
|
|
|
|
|
|
|
|
|
|
|
|
КП 23.02.06.15.03.01 ПЗ |
|
|
|
|
|
|
|
|
|
|
|
|
|
|
|
|
|
|
|
|
|
|
||
|
|
|
|
|
|
|
|
|
|
|
|
||||||||
|
|
|
|
|
|
|
|
|
|
|
|
|
|
|
|
19 |
|
|
|
|
|
|
|
|
|
|
|
|
|
|
|
|
|
|
|
|
|
|
|
|
Изм |
|
|
Лист |
|
|
№ документа |
|
|
Подпись |
|
|
Дата |
|
|
|
|
|
|
|
|
|
|
|
|
|
|
|
|
|
|
|
|
|
|||||
|
|
|
|
|
|
|
|
|
|
|
|
|
|
|
|
|
|
|
|
|
|
|
|
|
|
|
|
|
|
|
|
|
|
|
|
|
|
|
|
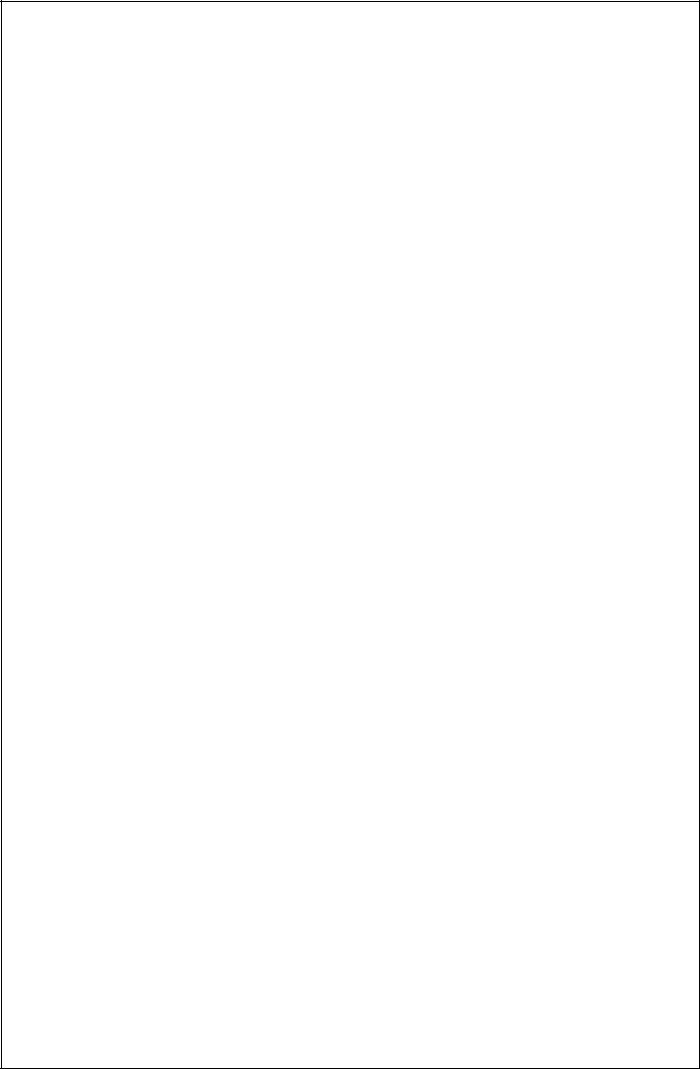
ца; внутреннюю планку подшипников (со стороны привода) крепят к корпусу и фиксируют штифтами; в корпус насоса согласно меткам спаренности устанавли-
вают зубчатые колеса, на шпилькипрокладку,
устанавливают наружную планку и временно закрепляют гайками. Изме-
ряют и регулируют осевой разбег зубчатых колес. Если разбег менее 0,15 мм, тол-
щину прокладок под планкой увеличивают, при разбеге более 0,26 мм – уменьша-
ют. Если прокладками уменьшить осевой разбег не удается, допускается шлифовка и шабровка торцовых поверхностей корпуса. Затем отворачивают гайки крепление планки, устанавливают шайбу на цапфу ведомого зубчатого колеса и болты. На цапфе ведущего зубчатого колеса закрепляют гайкой упорной шарикоподшипни-
ком и крышку насоса в сборе с поршнем крепят к корпусу. На шлицы цапфы ве-
дущего зубчатого колеса надевают зубчатый поводок и закрепляют его гайкой. К
корпусу насоса крепят редукционный клапан в сборе. В собранном насосе зубча-
тые колёса должны проворачиваться свободно от руки. Редукционный клапан ре-
гулируют на давление (5,5/6,0) 10(5) Па при испытании на стенде или опрессовке насоса.
При замене планок, зубчатых колес или ремонте корпуса требуется прове-
рить и восстановить центровку подшипниковых планок относительно корпуса так,
чтобы оси отверстий в корпусе под зубчатые колеса совпадали с осями отверстий в подшипниковых планках. Для этого используют технологические зубчатые колёса с цапфами, которые устанавливают в расточки корпуса. Между зубчатыми колеса-
ми и корпусом сверху и снизу закладывают фольгу одинаковой толщины так, что-
бы исчез зазор между горизонтальными лысками зубчатых колес, при этом рассто-
яние между осями цапф технологических колес должно соответствовать чертеж-
ному размеру. Затем на цапфы технологических зубчатых колес с обеих сторон надевают планки в сборе с подшипниками, закрепляют их гайками и устанавлива-
ют новые конические штифты. Последующую сборку насоса производят в после-
довательности, указанной выше.
Масляный насос устанавливают на плиту насосов на старых прокладках и
|
|
|
|
|
|
|
|
|
|
|
|
|
|
|
|
|
|
|
|
|
|
|
|
|
|
|
|
|
|
|
|
|
|
|
|
|
Лист |
|
|
|
|
|
|
|
|
|
|
|
|
|
|
|
|
|
КП 23.02.06.15.03.01 ПЗ |
|
|
|
|
|
|
|
|
|
|
|
|
|
|
|
|
|
|
|
|
|
|
||
|
|
|
|
|
|
|
|
|
|
|
|
||||||||
|
|
|
|
|
|
|
|
|
|
|
|
|
|
|
|
20 |
|
|
|
|
|
|
|
|
|
|
|
|
|
|
|
|
|
|
|
|
|
|
|
|
Изм |
|
|
Лист |
|
|
№ документа |
|
|
Подпись |
|
|
Дата |
|
|
|
|
|
|
|
|
|
|
|
|
|
|
|
|
|
|
|
|
|
|||||
|
|
|
|
|
|
|
|
|
|
|
|
|
|
|
|
|
|
|
|
|
|
|
|
|
|
|
|
|
|
|
|
|
|
|
|
|
|
|
|