
metody
.pdfРАЗДЕЛ №2 МЕТОДЫ ОБРАБОТКИ ПОВЕРХНОСТЕЙ
ТИПОВЫХ ДЕТАЛЕЙ
Глава 9
ОБРАБОТКА ПОВЕРХНОСТЕЙ ФОРМЫ ТЕЛ ВРАЩЕНИЯ
39. ОБЩИЕ ПОЛОЖЕНИЯ
Детали, имеющие форму тел вращения, можно разбить на три класса: валы, втулки и плоские детали вращения— диски.
В класс валов входят валы, валики, оси, пальцы, цапфы и другие детали, которые образуются в основном наружной поверхностью вращения (цилиндрической;
аиногдаконической) и несколькими торцовыми поверхностями.
Кклассу втулок относят втулки, вкладыши, гильзы, буксы и другие детали, характеризующиеся наличием наружнойи внутренней цилиндрических поверхностей.
В класс дисков входят диски, шкивы, маховики, кольца, фланцы и другие детали, которые характеризуются небольшой длиной (шириной) и большими диаметрами, т. е. большими торцовыми поверхностями.
Заготовки выбираются в зависимости от типа производства. В единичном и мелкосерийном производстве заготовки для деталей класса валов получают отрезкой от горячекатаных или холоднотянутых прутков. Затем они поступают непосредственно на механическую обработку. Заготовки из проката применяются при изготовлении не только гладких валов, но и ступенчатых с не большим числом ступеней и незначительными перепадами их диаметров. Эти заготовки используются также и в крупносерийном производстве.
В массовом производстве, а также при изготовлении валов сложной формы, имеющих большое число ступеней, значительно отличающихся по диаметру, заготовки целесообразно получать ковкой, штамповкой, периодическим прокатом, обжатием наротационно-ковочныхмашинах и другими методами.
При механической обработке валов на настроенных и автоматизированных станках желательно применять точные заготовки. Заготовки, полученные методом ротационной ковки, отличаются малыми величинами припусков и высокой точностью.
Детали, относящиеся к классам втулок и дисков, выполняют из проката, поковок, штамповок и реже из отливок. Из проката изготовляют как небольшие, так и значительные по размерам детали (150—200 мм).
Способы обработки. В зависимости от требований, предъявляемых к шероховатости поверхности и точности размеров, различают несколько способов обработки. Основным способом обработки наружных цилиндрических поверхностей деталей всех трех классов является обтачивание.
Черновое (обдирочное) обтачивание применяется при грубой и предварительной обработке, при этом достигается точность обработки до 5-го класса, а
шероховатость поверхности — до 3-го класса чистоты.
Чистовое обтачивание обеспечивает точность обработки до 4-го класса, а шероховатость поверхности — до 6-го класса.
При чистовом точном и точном обтачивании точность обработки соответствует 2- му классу, а шероховатость поверхности— 9-муклассучистоты.
Оборудование. Детали всех трех классов обрабатываются на токарных, токарнокопировальных, револьверных, карусельных, горизонтальных многорезцовых станках инавертикальныходношпиндельныхимногошпиндельных автоматах.
Из станков токарной группы наиболее универсальным является токарный станок общего назначения, на котором можно выполнять наибольшее количество самых -разнообразных операций. Однако его универсальность
обусловливает его малую производительность по сравнению со специальными станками. Поэтому он типичен для единичного и мелкосерийного производства и совершенно непригоден для массового.
Вединичном и мелкосерийном производствемеханическая обработка ступенчатых валов производится на токарных станках общего назначения, оборудованных копировальными устройствами с гидросуппортом КСТ-1.
40. УСТАНОВКА И ЗАКРЕПЛЕНИЕ ДЕТАЛЕЙ
В зависимости от заданной точности, размеров и конфигурации деталей их обрабатывают на токарных станках в центрах и в патронах, на угольниках и оправках.
Обработка в центрах. Самым распространенным способом обработки деталей типа валов является обработка в центрах (рис. 54), при этом в торцовых поверхностях заготовки делают центровые отверстия. При установке заготовки на станок в центровые отверстия вводят передний 2 и задний 4 центра (рис. 54, а). Для передачи заготовке вращения служат поводковый патрон 1 и хомутик 3, закрепляемый винтом 5 на конце заготовки. Свободный конец хомутика с помощью паза или пальца 6 (рис. 54, б) поводкового патрона приводит деталь во вращение. В первом случае хомутик 3 делается отогнутым (см. рис. 54, а), а во втором — прямым (см. рис. 54, б). Прямой хомутик менее опасен в работе.
Преимуществом обработки в центрах является то, что при установке детали отпадает какая-либо необходимость в ее выверке.
Натокарных станках применяются различные типы центров.
Наиболее распространенными являются центра упорные (рис. 55, а) (ГОСТ 13214-67), полуцентра упорные (рис. 55, б) (ГОСТ 2576-67) и центра упорные с отжимной гайкой (рис. 54, в) (ГОСТ 2575-67). Центра упорные и упорныесотжимной гайкой могут быть оснащены пластинками твердого сплава или наплавлены прутковым сормайтом.
При чистовом точении с большими скоростями и незначительными нагрузками центра следует оснащать вставками из твердого сплава марки ВК6, при получистовом точении со средними скоростями и нагрузками — марки Т5К10, при черновом точении с небольшими скоростями, но значительными нагрузками — марки ВК8.
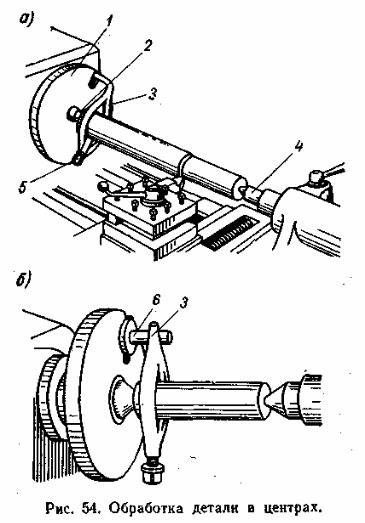
Задний центр токарного станка в отличие от переднего играет роль подшипника, так как между ним и заготовкой происходит относительное движение, а следовательно, и трение.
Поэтому при обработке деталей на больших скоростях (v >75 м/мин) применяют вращающиеся задние центра с шарикоили роликоподшипниками, конструкции которых стандартизованы для малых, средних и тяжелых нагрузок.
Недостатком вращающихся центров является их малая жесткость и склонность вызывать вибрации при резании, в особенности при некотором износе и увеличении зазоров в подшипниках.
Чтобы избежать этих явлений, применяют вращающиеся центра, встроенные в пиноль задней бабки (рис. 56, а). В этом случае обыкновенный центр 1 вставляется в шпиндель 5, который вращается в пиноли 8 задней бабки в подшипниках 3 и 7. Осевые силы, действующие на центр 1, воспринимаются упорным подшипником 4. Радиальный зазор в роликовом подшипнике 3 регулируется резьбовым кольцом 2. Для выталкивания заднего центра служит стержень 6. Если пиноль 8 используется для закрепления сверл, зенкеров и других инструментов, то шпиндель 5 фиксируется стопором9.
В процессе обработки деталь нагревается и длина ее увеличивается, что приводит к повышению нагрузки на центра и к искривлению детали. Во избежание искривления в некоторых современных станках применяется такая конструкция пиноли задней бабки, которая дает возможность свободного удлинения детали

(благодаря введению компенсирующих устройств старельчатыми пружинами). Базирование деталей на центрах станка не обеспечивает стабильного положения
их вдоль оси, так как глубина центровых отверстий может быть различной. Чтобы обеспечить одинаковое базирование всех деталей вдоль оси при
различной глубине центровых отверстий в передней бабке токарного и многорезцового станков, применяют плавающие центра (рис. 56, б). Такой центр 5, смонтированный внутри корпуса 2, вставляют в коническое отверстие шпинделя передней бабки. Пружина 1 стремится отжать центр вправо и создать контакт его с деталью. Установленная в центра деталь при налиме пиноли задней бабки доводится торцом до упора 4, прикрепленного к торцу корпуса 2. После этого плавающий центр стопорится болтом 3 на время обработки детали. После окончания обработки он должен быть освобожден.
Схема установки детали на жестком переднем центре приведена на рис. 57, а, а на плавающем — на рис. 57, б. При установке детали на жесткий передний центр и параллельной обработке торцов погрешность базирования для размера а равна нулю (см. рис. 57, а). Для размера b от левого торца, являющегося измерительной базой, эта погрешность не будет равна нулю, потому что глубина центровых отверстий неодинакова. Следовательно, величина погрешности базирования для размера b определяется допуском на глубину центрового отверстия.
При установке той же детали на плавающий передний центр (см. рис. 57, б) положение левого торца вала для заготовок всей партии будет определяться упором и сохраняться постоянным относительно резцов, установленных на размеры С
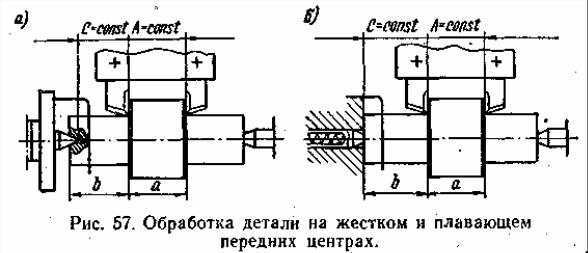
= const и А = const. В этом случае установочная и измерительная базы совместятся, и погрешность базирования для размера b будет также равна нулю.
Применение поводкового патрона с хомутиком связано с рядом недостатков. К ним относятся: большое вспомогательное время на установку и снятие хомутика; невозможность обработки детали по всей длине без ее перестановки; трудность обеспечения безопасных условий работы из-за выступающих частей у хомутика и поводкового патрона и т. п.
Указанных недостатков не имеют быстродействующие поводковые устройства современных конструкций, которые обеспечивают как правильное базирование детали, так и передачу крутящего момента без использования хомутика.
Конструкция поводкового устройства Ленинградского станкостроительного завода им. Свердлова приведена на рис. 58. В корпусе 3 центра поводка расположен подвижный центр 4, находящийся под действием пружины 2. На корпус навернута втулка 5, внутри которой имеется шайба 6 с двумя полуцилиндрическими выступами А. Выступы входят в такие же канавки на торце корпуса. Кроме того, во втулке расположена шайба 7, на левом торце которой имеются полуцилиндрические выступы С, входящие в соответствующие канавки в шай. Выступы в шайбах 6 и 7 расположены крестообразно. Благодаря этому, если торец обрабатываемой детали не перпендикулярен к ее оси, то при поджиме задним центром (обязательно вращающимся) он коснется правого торца шайбы 7, при
этом центр 4 несколько переместится влево, оставаясь под действием пружины 2, а зубья В на торце шайбы 7 врежутся в торец детали и передадут ей вращательное движение шпинделя.
Центр-поводок снабжается набором шайб 7 с различными диаметрами D рабочей части. Диаметр рабочей части шайбы должен быть несколько меньше диаметра конца обтачиваемой детали, обращенного к передней бабке, чтобы можно было обработать всю поверхность детали и снять фаску на ее торце. Пружина 2 центраповодка должна быть отрегулирована при помощи пробки 1 на давление около 30
кг.
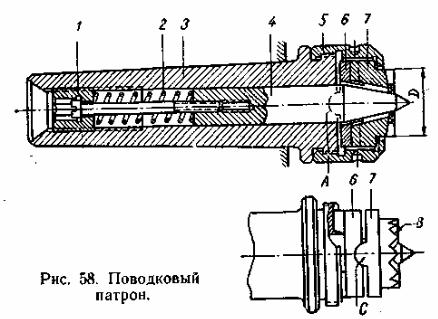
При обработке длинных деталей, когда отношение длины детали к ее диаметру l:d>12—15, применяют люнеты. Различают подвижные и неподвижные люнеты.
Нежесткие ступенчатые и особо тяжелые детали обрабатывают с помощью неподвижного люнета (рис. 59), который устанавливают и закрепляют на станине станка.
При обработке нежестких гладких цилиндрических деталей на станке с высотой центров менее 500 мм применяют подвижный люнет (рис. 60), который устанавливается и закрепляется на суппорте и в процессе работы перемещается вместе с ним.
Для установки детали с неподвижным люнетом необходимо проточить на ней шейку под кулачки люнета (рис. 61). Так как шейка является для детали дополнительной базой, то она должна быть обработана с минимальными отклонениями от геометрической формы. Точность размеров шейки зависит от количества обрабатываемых деталей. Жесткие допуски на диаметр шейки (3—4-й классы точности) оправдывают себя в крупносерийном и массовом производстве при работе на настроенных станках. В серийном и мелкосерийном производстве шейку можно обрабатывать по 7-му классу точности и грубее.
Если в качестве заготовки применяют холоднотянутый прокат, то кулачки люнета устанавливают по необработанной поверхности.
Для точной установки детали с неподвижным люнетом требуется совмещение оси шейки с осью станка. В этом случае базовые поверхности кулачков люнета должны располагаться на одной окружности, центр которой совпадает с осью станка.
При обработке особо нежестких валов, когда проточить шейку под кулачки люнета трудно, вместо нее используют втулку с обработанной наружной поверхностью (рис. 62). Такая втулка 2 закрепляется на валу 1 с помощью восьми болтов 4 (по четыре у каждого конца втулки). Положение ее относительно центровой линии станка проверяется по ее наружной поверхности рейсмусом или индикатором 3 и регулируется при помощи ввернутых болтов. Наружная поверхность такой втулки и будет являться опорой для кулачков люнета.
При обработке большой партии нежестких валов в корпусе 1 неподвижного
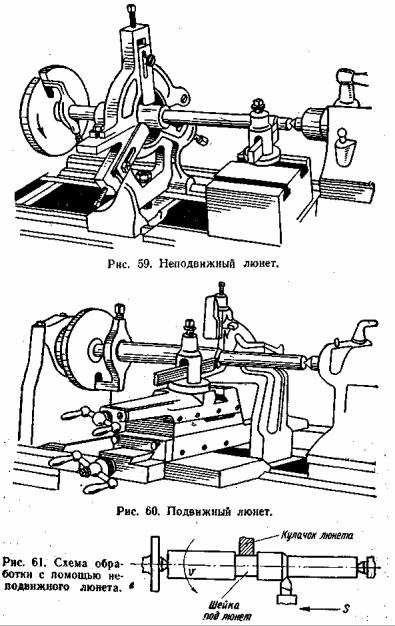
люнета (рис. 63) целесообразно расточить отверстие, ось которого должна совпадать с осью станка. Такое отверстие дает возможность сравнительно быстро и точно установить кулачки 2 люнета по шейке детали 3. Регулировку кулачков осуществляют путем измерения в нескольких местах расстояния h от поверхности шейки до выточки.
При обработке детали с подвижным люнетом шейку протачивать на ней не надо, так как базой для установки кулачков 1 люнета (рис. 64) служит обработанная поверхность, по которой они и перемещаются. При использовании подвижного люнета расстояние а между точкой приложения усилия резания и опорой, создаваемой кулачками, остается постоянным в течение всей обработки детали.
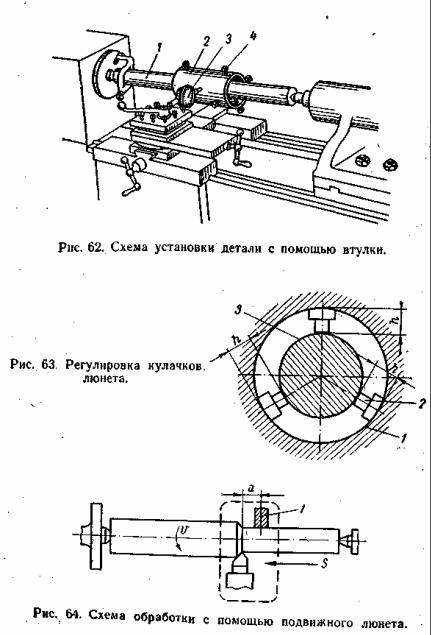
Обработка в патронах. В патронах обрабатываются, как правило, жесткие и короткие ( l : d = 1,5) детали.
Существует большое число различных типов патронов: четырехкулачковые с индивидуальным приводом кулачков, самоцентрирующие трех- и двухкулачковые, самозажимные, цанговые, мембранные, магнитные и др.
Вединичном производстве при обработке деталей сложной и несимметричной или некруглой формы применяют четырехкулачковые патроны с индивидуальным и независимым ручным приводом. Независимое перемещение каждого кулачка позволяет иногда использовать четырехкулачковые патроны при точной обработке деталей тел вращения.
Впроизводствах всех типов широко распространены самоцентрирующие патроны. Они пригодны для установки деталей с базовыми поверхностями любой формы. 'Для этого достаточно к основным кулачкам патрона прикрепить специальные губки илидополнительные кулачки.
Примеры использования самоцентрирующих патронов с дополнительными
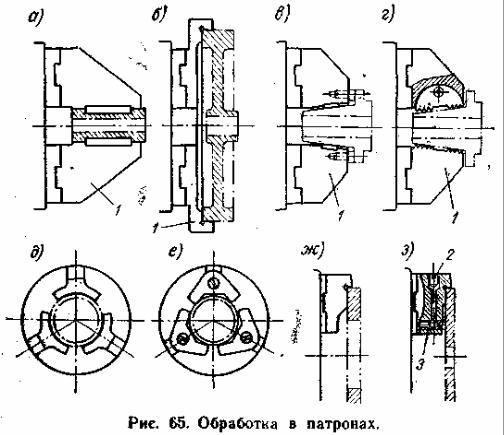
кулачками приведены на рис. 65. Дополнительные кулачки 1 для закрепления длинных и большого диаметра деталей показаны на рис. 65, а и б. Возможно закрепление детали за обработанную коническую поверхность (рис. 65, в), если угол уклона конуса не превышает 4—6°. Если на дополнительные кулачки нанести насечку, то закрепление деталей за необработанную поверхность может быть надежным и при большем угле уклона конуса. При необработанных конических поверхностях детали только один из трех кулачков патрона может быть жестким, а остальные два должны быть снабжены качающимися губками (рис. 65, г).
Для закрепления тонкостенных втулок с обработанными наружными поверхностями применяют дополнительные кулачки с увеличенными рабочими поверхностями (рис. 65, д). Нежесткие дополнительные кулачки (рис. 65, е) можно использовать для закрепления тонкостенных втулок с необработанной наружной поверхностью. Примеры закрепления тонкостенных дисков в па-
троне с дополнительными кулачками показаны на рис. 65, ж и з. Очень тонкий диск с обрабатываемым в нем отверстием небольшого диаметра (рис. 65, з) поддерживается пружинными подпорками 3, расположенными в дополнительных кулачках. Закреплены подпорки 3 винтами 2.
Основным недостатком самоцентрирующих патронов является невысокая точность центрирования: 0,06— 0,12 мм у патронов со спиральным диском и 0,03— 0,08 мм — у клиновых и рычажных патронов.
Для установки тонких дисков при обработке торцовых поверхностей применяют электромагнитные патроны и патроны с постоянными магнитами.
Обработка на угольниках. В тех случаях, когда форма детали не позволяет установить и закрепить ее в патроне или непосредственно на планшайбе, применяют дополнительное устройство в виде угольника, который крепится непосредственно к
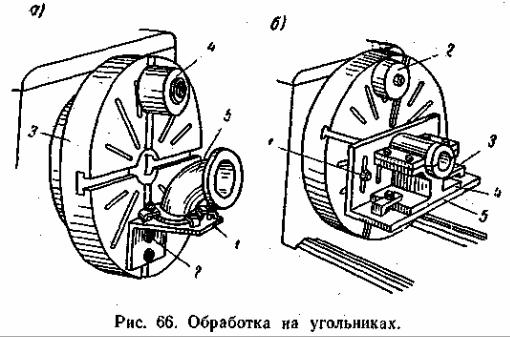
планшайбе. Установка и закрепление подобных деталей при подрезке торца у фланца показаны на рис. 66, а. Угольник 1 с точными
взаимно-перпендикулярными плоскостями закреплен болтами 2 на планшайбе 3. Деталь 5 в виде патрубка устанавливают так, чтобы обрабатываемая плоскость была расположена параллельно планшайбе. При обработке деталей на угольниках с несимметричным расположением вращающихся масс относительно оси шпинделя необходимо произвести балансировку путем прикрепления к планшайбе груза 4.
Другой пример обработки детали 4 типа подшипника на угольнике приведен на рис. 66, б для обработки отверстия, находящегося на точном расстоянии от нижней плоскости плиты. Двумя планками 3 деталь прикрепляют к угольнику 5 и при помощи болтов 1 устанавливают его в рабочее положение. Для уравновешивания детали и угольника на планшайбе закрепляют противовес 2.
В серийном производстве применяют специальное приспособление типа угольника, которое предназначено для обработки одной детали.
Обработка на оправках. При обтачивании наружных поверхностей у деталей с уже точно обработанным отверстием для установки и закрепления их применяют оправки. Имеются различные конструкции оправок. Одна из самых простых по конструкции оправокприведена нарис. 67, а.
Средняя часть оправки изготовляется с очень небольшой конусностью — 1/2000. Диаметр D1 делается несколько меньше наименьшего возможного диаметра отверстия обрабатываемой детали. Деталь насаживается на оправку ударами медного молотка или под прессом и удерживается на ней силой трения. Недостатком конусной оправки является то, что положение детали на ней зависит от величины допуска на изготовление. Для работы на настроенном станке такая оправка непригодна.
На оправке, приведенной на рис. 67, б, положение детали в осевом направлении определяется буртиком А оправки.