
ves_kurs / theory
.pdfМодульные ленты выполняются из термопластичных пластмассовых модулей, которые соединены между собой прочными пластмассовыми стержнями, цельная конструкция из пластмассы обеспечивает долгий срок службы, кирпичное соединение создает возможность для сборки различной ширины и обеспечивает высокую боковую и диагональную прочность и жесткость.
При использовании модульных лент имеется возможность изменения длины ленты добавлением или удалением модулей при ее постепенном вытягивании, наращивании или сокращении длины самого конвейера.
Преимуществами модульных полимерных лент являются большое количество и разнообразие их типов; широкий диапазон рабочих температур (от –70°С до +190°С); удобство монтажа и демонтажа; ремонтопригодность; большой диапазон варьирования площади контакта продукта с лентой (от 10% до 90%); возможность обработки моющими горячими и активными растворами; допуск к контакту с пищевыми продуктами (нетоксичны); устойчивость к химическим веществам.
2.2 Ходовые опорные устройства
Опорными устройствами для лент (иногда для пластинчатого настила) являются стационарные ролики, обеспечивающие большой срок службы грузонесущего органа и малое сопротивление его движению.
Для опоры ленты используют роликоопоры или настил – сплошной (из дерева, стали, пластмассы) или комбинированный (чередование настила и роликоопор), наибольшее распространение имеют роликоопоры различных типов и конструкций.
Ролики изготавливают из металлической трубы, закрепленной с помощью подшипников на оси; в настоящее время широкое использование получили ролики, выполненные из керамики или высокопрочных полимерных материалов.
При транспортировании штучных грузов и пассажиров ленточные конвейеры снабжают опорами скольжения в виде неподвижного настила для обеспечения плавного движения ленты и предотвращения ее провеса под действием массы груза в промежутках между опорами. Ходовые катки служат опорными элементами пластинчатого настила скребков, ковшей, ступеней эскалаторов, несущих цепей, тележек подвесных, тележечных и грузоведущих напольных конвейеров. К опорным устройствам относятся также направляющие и подвесные пути, станины конвейеров.
В некоторых конструкциях скребковых конвейеров цепи снабжают ползунами, перемещающимися по неподвижным направляющим путям. Опорным элементом цепей конвейеров сплошного волочения является непосредственно днище желоба.
Опорные устройства должны обеспечивать малый коэффициент сопротивления движению; экономичность конструкции; высокую прочность и износостойкость; надежность; удобство обслуживания и ремонта .
2.3 Натяжные устройства
Натяжные устройства (рис. 2.15, 2.16) служат для обеспечения первоначального натяжения тягового элемента; ограничения провеса тягового элемента между
31
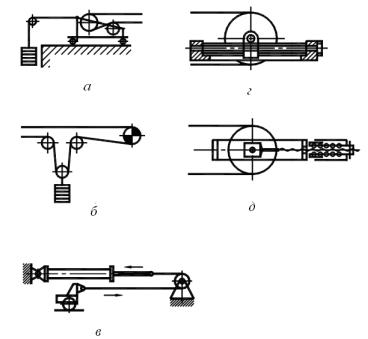
опорными устройствами; компенсации вытяжки тягового элемента в процессе эксплуатации.
Натяжные устройства по способу действия и конструкции классифицируют на механические; пневматические; гидравлические; грузовые; грузолебедочные; лебедочные.
Преимущества механических натяжных устройств: простота конструкции; малые габаритные размеры; компактность. Недостатки механических натяжных устройств: переменное значение натяжения и возможность чрезмерного натяжения тягового элемента; жесткость крепления и отсутствие подвижности при случайных перегрузках; необходимость периодического наблюдения и подтягивания.
Пневматические и гидравлические натяжные устройства имеют малые габаритные размеры, но требуют установки специального оборудования для подачи под постоянным давлением воздуха или масла.
Преимущества грузового натяжного устройства: приводится под действием свободно висящего груза; автоматически обеспечивает постоянное усилие натяжения; компенсирует изменения длины тягового элемента; уменьшает пиковые нагрузки при перегрузках.
Рис. 2.15-Натяжные устройства:
а– хвостовое грузовое; б – промежуточное грузовое; в – гидравлическое;
г– винтовое; д – пружинно-винтовое
Недостатки грузового натяжного устройства: большие габаритные размеры; большая масса груза для мощных и длинных ленточных конвейеров.
Для снижения массы груза применяют рычаги, полиспасты, приводные лебедки. Ход натяжного устройства выбирается в зависимости от длины и конфигурации трассы и типа тягового элемента, ход натяжного устройства должен обеспечивать компенсацию удлинения тягового элемента и выполнение монтажных работ .
Х = хр + х0, |
(2.5) |
где хр – рабочий ход; х0 – монтажный ход.
32
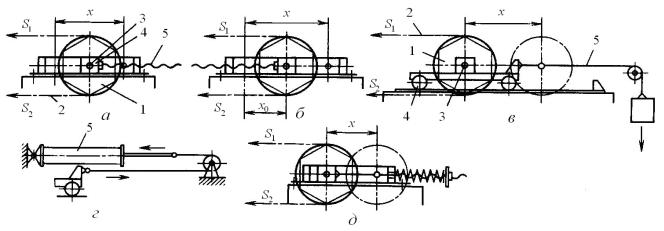
Рис. 2.16-Схемы натяжных устройств:
а, б – винтовые; в – тележечное грузовое; г – пневматическое (гидравлическое);
д– пружинно-винтовое; 1 – поворотное устройство; 2 – тяговый элемент; 3 – ось поворотного устройства; 4 – ползуны; 5 – натяжной механизм
Рабочий ход НУ для ленточных конвейеров, м:
хр ≥ Kн Ks εy L, |
(2.6) |
где Kн – коэффициент, зависящий от угла наклона конвейера β;
Ks – коэффициент использования ленты по натяжению (при классах ис пользования Ц1; Ц2; Ц3 значение Ks соответственно равно 0,63; 0,8; 1,0); εy – относительное упругое удлинение ленты (для резинотканевых лент εy = 0,015, для резинотросовых лент εy = 0,0025);
L – длина конвейера между центрами концевых барабанов, м.
Натяжное устройство обычно устанавливается на одном из поворотных устройств (барабане, блоке, звездочке), расположенном на участке малого натяжения тягового элемента. Натяжное усилие, Н:
Рн = S1 + S2 + Т, |
(2.7) |
где S1 – натяжение набегающей ветви конвейера, Н; S2 – натяжение сбегающей ветви конвейера, Н;
Т – усилие перемещения ползунов или натяжной тележки, Н.
Наибольшее натяжение должно быть в период пуска конвейера, при установившемся режиме оно должно автоматически уменьшаться (лебедочные и грузолебедочные натяжные устройства с автоматическим управлением, с датчиком контроля натяжения). На грузовых натяжных устройствах в крайних положениях натяжной тележки устанавливают конечные выключатели.
2.4 Приводы конвейеров
Приводной механизм служит для приведения в движение тягового и грузонесущего элементов конвейера.
33
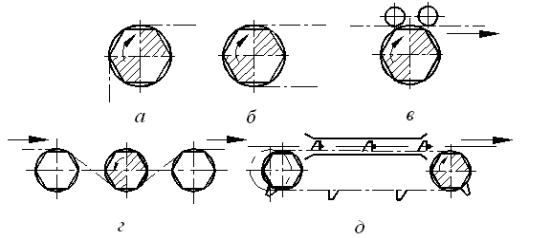
По способу передачи тягового усилия различают приводы: с передачей усилия зацеплением; фрикционные: однобарабанные (одноблочные), двух-, трехбарабанные и специальные промежуточные.
Приводы с передачей тягового усилия зацеплением (рис. 2.17):
-угловые со звездочкой или кулачковым блоком устанавливаются на повороте трассы на 90 или 180°;
-прямолинейные (гусеничные) с приводной цепью и кулаками (устанавливаются на прямолинейном участке).
Рис. 2.17-Схемы приводов с передачей тягового усилия зацеплением: а, б, в – угловые со звездочкой (поворот на 90° и 180°); г – на отклонении цепи; д – прямолинейный гусеничный
Преимущества гусеничного привода: меньший диаметр приводной звездочки (по сравнению с угловым); меньший крутящий момент и размеры механизмов; возможность установки на любом горизонтальном участке трассы конвейера. Недостатки гусеничного привода: сложность устройства; высокая стоимость. В конвейерах используются гусеничные приводы с плоскими электромагнитами и фрикционные прямолинейные приводы.
По числу приводов конвейеры бывают одноприводные и многоприводные (рис. 2.18). У многоприводных конвейеров размещают до 12 промежуточных приводных механизмов с отдельными электродвигателями. Использование промежуточных приводов позволяет уменьшить натяжение тягового элемента.
От расположения привода зависит натяжение тягового элемента на разных участках контура трассы, поэтому привод необходимо располагать так, чтобы уменьшить наибольшее натяжение тягового элемента.
Применение нескольких приводов позволяет снизить максимальное натяжение гибкого тягового элемента, т. е. использовать гибкий тяговый элемент меньшей прочности; многоприводные конвейеры могут иметь большую длину при правильно выбранной системе приводов.
При определении рационального места установки привода на трассе конвейера основным фактором является достижение минимального натяжения тягового элемента и снижение натяжения на поворотных и криволинейных участках, поэтому рациональной является установка привода в пунктах поворота контура трассы.
34
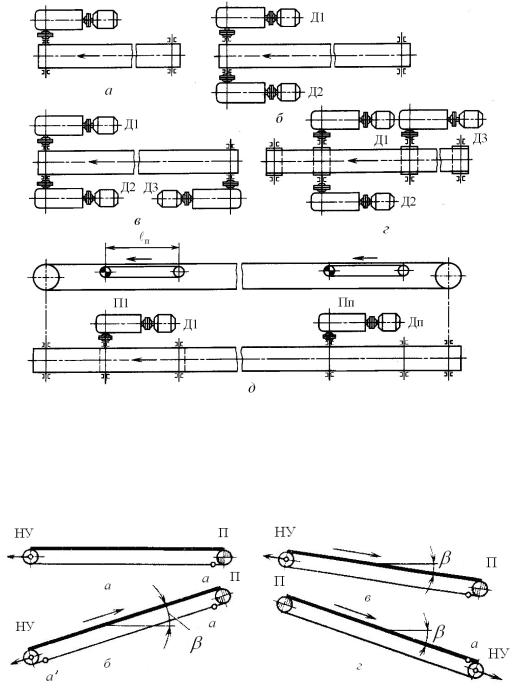
Рис. 2.18-Схемы расположения приводов:
а– с одним двигателем; б – с двумя двигателями; в, г – с тремя двигателями;
д– многоприводного с промежуточными приводами
Если конвейер состоит из одного участка (горизонтального или наклонного), то привод располагается в головной части, т.е. в конце грузовой ветви (рис. 2.19).
Рис. 2.19-Расположение привода в головной части конвейера (а – точка минимального натяжения):
а, б – на горизонтальном конвейере; в, г – на наклонном конвейере
При движении груза вниз при небольшом угле наклона сопротивление движению на грузовой ветви больше, чем на обратной – привод в головной части конвейера, при движении груза вниз при значительном угле наклона сопротивление движению на грузовой ветви меньше, чем на обратной – привод в хвостовой части конвей-
ера (рис. 2.19, г).
Для того, чтобы сохранить требуемое натяжение тягового элемента на длинных ленточных конвейерах, натяжное устройство устанавливают ближе к приводу
(рис. 2.20).
35
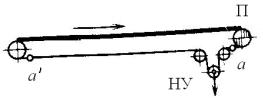
Оптимальное количество приводов на конвейере определяется техникоэкономическим расчетом, при проектировании и выборе оптимального числа приводов целесообразным является использование меньшего числа приводов повышенной мощности. Использование прямолинейных промежуточных приводов в цепных конвейерах со сложной конфигурацией трассы позволяет обеспечить наиболее оптимальное их расположение на всем протяжении контура трассы.
Рис. 2.20-Схема расположения привода и натяжного устройства на конвейере с увеличенной длиной трассы
Для быстрой остановки конвейера и предотвращения его обратного движения под действием силы тяжести груза в наклонных конвейерах на входном валу редуктора устанавливают тормоз. Для предупреждения обратного движения грузонесущего элемента под действием силы тяжести груза в случае нарушения кинематической связи между тормозным валом и приводным элементом конвейера устанавливают храповые остановы.
Для предохранения цепных конвейеров от обрыва цепи и поломок приводного механизма из-за внезапных перегрузок (заклинивание цепи, попадание посторонних предметов) применяют муфты предельного момента, а также ловители – устройства для автоматической остановки цепи при случайном ее обрыве.
Мощность на приводном валу:
NВ = Pв v, |
(2.8) |
где Pв – тяговое усилие на валу приводного барабана (звездочки): |
|
Pв = Р0 + Wиз + Wоч + Wп, |
(2.9) |
где Р0 – тяговое усилие без учета потерь на приводном барабане (звездочке); |
|
Wиз – потери от перегиба тягового элемента; |
|
Wоч – сопротивление очистительных устройств; |
|
Wп – сопротивление подшипников вала. |
|
Установочная мощность приводного двигателя: |
|
N = kз NВ / η. |
(2.10) |
По рассчитанной установочной мощности выбирают электродвигатель по каталогу. По выбранному двигателю подбирается редуктор в соответствии с расчетным передаточным числом.
Поддерживающая металлоконструкция зависит от конструкции конвейера, изготавливается из прокатной профильной стали секциями длиной 3-6 м. Привод и натяжное устройство имеют самостоятельные сварные конструкции. Поддерживающая металлоконструкция должна быть прочной, жесткой, легкой, удобной для монтажа и обслуживания.
36
ЛЕКЦИЯ 3. ОБЩАЯ ТЕОРИЯ ТРАНСПОРТИРУЮЩИХ МАШИН
3.1 Производительность транспортирующих машин непрерывного действия.
Потребная производительность транспортирующей машины (установки) определяется количеством насыпного или штучного груза, который поступает на нее в единицу времени и должен быть ею перемещен в заданном направлении и на заданное расстояние. Производительность может быть выражена массой, весом или объемом груза в единицу времени. За единицу времени принимают обычно час. Иногда потребную производительность указывают за смену или за сутки. В отдель-
ных случаях для некоторых типов машин, например погрузочных, указывается технически возможная производительность за более короткое время - за минуту.
Если производительность указана за смену Qсм, т/смену и продолжительность смены равна Тсм часам, а время, в течение которого машина работает, Тм (так называемое «машинное время»), то средняя часовая производительность за время Тм ,т/ч:
Qср= Qсм/Тм = Qсм/ (Тсм .Квр), |
(3.1) |
где Квр = Тм/Тсм < 1, коэффициент равный отношению машинного времени в течение смены ко всей ее продолжительности, определяет степень использования транспортирующей машины во времени.
Если поступление груза в течение машинного времени происходит неравномерно и в отдельные периоды возрастает в k раз по отношению к средней производительности (коэффициент k > 1 носит название коэффициента неравномерности),
то производительность машины должна быть не меньше, чем: |
|
Q= k .Qср = Qсм .k/ (Тсм .Квр). |
(3.2) |
В случае насыпных грузов производительность нередко указывают в объем- |
ных единицах. Если производительность задается в весовых единицах, например Qв, |
|
кН/ч и насыпной вес груза γв=10.g.γ (кН/м3, где g (м/сек2) – ускорение силы тяжести), |
|
то соответствующая величине Qв объемная производительность находится из выра- |
|
жения, м3/ч: |
|
V= Qв / γв= Vсм .k/ (Тсм .Квр), |
(3.3) |
где γ (т/м3) - объемная насыпная масса груза. |
|
По величине V, Q или Qв определяют расчетом основные потребные конструктивные параметры производительности машины, вследствие чего эта величина производительности носит название расчетной или конструктивной производительности.
Параметры производительности транспортирующих машин непрерывного действия определяют для трех случаев транспортирования: 1) перемещение насыпных грузов непрерывным потоком; 2) перемещение насыпных грузов отдельными количествами («порциями») и 3) перемещение штучных грузов. Во всех случаях основными факторами производительности служат средняя величина количества груза на единице длины грузонесущего элемента и рабочая скорость перемещения.
Среднее количество груза на единице длины грузонесущего элемента (погонная нагрузка) выражается в единицах объема qoб (л/м), массы q (кг/м) или веса qв
37
(Н/м). Секундная производительность получается умножением погонной нагрузки на величину скорости перемещения v (м/сек), а часовая - из выражений, м3/ч, т/ч и кН/ч соответственно:
V=3600 . qoб/1000, Q =3600 . q/1000 и Qв =3600 . qв /1000. (3.4)
При перемещении штучных грузов массой G (кг) или весом Gв (Н) каждого отдельно или партиями по z (шт.) и при расположении грузов или партий грузов с шагом а (м) погонная нагрузка составит, кг/м:
q=G/a или qв=Gв/a. |
(3.5) |
Производительность транспортирующих машин непрерывного действия, перемещающих штучные грузы, иногда определяется по количеству штук в единицу времени. Интервал времени между единичными грузами или партиями грузов:
t=a/v, |
(3.6) |
а следовательно, часовая производительность при перемещении груза штука- |
|
ми или при перемещении партиями по z штук, шт/ч: |
|
Z=3600/t=(3600 . v)/a и Z=(3600 .z . v)/a. |
(3.7) |
При этом производительность, т/ч и кН/ч соответственно: |
|
Q=(G .Z)/1000 и Qв=(Gв .Z)/100. |
(3.8) |
Как видно из приведенных выражений для производительности транспортирующих устройств непрерывного действия, величина скорости перемещения является одним из двух основных параметров производительности. В расчетах обычно скорость перемещения назначают в зависимости от типа устройства, требуемой производительности, условий погрузки и разгрузки, а при поточном производстве — в зависимости от требований выполнения технологических процессов и пр.
В случае транспортирования насыпного груза и перемещения его непрерывной струей, по заданной производительности и принятой величине рабочей скорости находят поперечные геометрические размеры грузонесущего органа, например сечение желоба или трубы, ширину ленты и пр., а при перемещении отдельными количествами - емкость сосудов и расстояние (шаг) между ними. В случае кусковатых грузов полученные расчетом поперечные размеры грузонесущего органа должны быть сообразованы с размерами кусков. В случае транспортирования штучных грузов их размеры и требующееся расположение на грузонесущем органе, а также расстояние между ними имеет особое значение при установлении геометрических параметров транспортирующего устройства.
3.2 Расчет мощности привода
В общем случае транспортирование груза связано с перемещением его как в горизонтальном, так и в вертикальном направлении, причем конечная точка перемещения груза может быть расположена выше или ниже начальной. Трасса перемещения груза может быть прямолинейная или изогнутая в одной плоскости или в
38
разных плоскостях (пространственная трасса). В частном случае перемещение может происходить только в горизонтальной плоскости или только в вертикальной вверх или вниз, а также только в вертикальном направлении.
Если груз перемещается вверх на высоту Н (м) и производительность транспортирующего устройства, выраженная в единицах массы или веса, равна соответственно Q (т/ч) или Qв (кН/ч), то мощность двигателя, необходимая только для подъема груза, без учета вредных сопротивлений, (т. е. полезная мощность, кВт):
N=1000 .Qв.H/(3600 . 100)=Qв .H/360= Qв .H/36,7. |
(3.9) |
Если η - к.п.д. транспортирующего устройства, то величина потребной мощ- |
|
ности двигателя, кВт: |
|
Nп=N/ η= Q в.H/(360 .η). |
(3.10) |
Чем выше к. п. д., тем меньше относительная величина вредных сопротивле-
ний.
Но к. п. д. не может характеризовать механических свойств транспортирующей установки и для этого нужен другой показатель, не теряющий общности независимо от рода установки и направления перемещения на ней груза - вверх или вниз по вертикали, по наклону или по горизонтали. Таким показателем может быть коэффициент сопротивления. Величина коэффициента сопротивления равна отношению сил вредного сопротивления при перемещении груза к его весу.
Пользуясь коэффициентом сопротивления, учитывают отдельно работу подъема, которая может быть положительной, отрицательной или равной нулю, и работу на преодоление сил вредного сопротивления, которая всегда больше нуля.
Обозначим через qв (Н/м) весовую погонную нагрузку на транспортирующей установке, L (м) - ее длину и w - общий коэффициент сопротивления. Сила вредного сопротивления на установке, Н:
Wвр=qв .L. w, |
(3.11) |
и соответственная мощность, кВт: |
|
Nвр= (Wвр. v /1020)= (qв .L. w . v) /1020= (Qв .L. w)/3670. |
(3.12) |
Следовательно, общая мощность двигателя транспортирующего устройства, обусловленная силами сопротивления подъему груза и силами вредного сопротивления, кВт:
N= Nп +Nвр= Q в.H/(360 .η) + (Qв .L. w)/3670= Qв(10H+L. w)/3670. |
(3.13) |
3.3 Компоновка основных узлов.
3.3.1 Расположение привода на концевой станции.
Расположение привода на конвейере нередко определяется местными строительными, конструктивными и эксплуатационными условиями, например удобством сооружения фундаментов и помещения для привода, удобством управления и обслуживания, а также условиями подвода тока к приводу в определенном месте и пр.
Если местные условия не имеют решающего значения, то определение места расположения привода необходимо производить исходя из требований: возможное
39
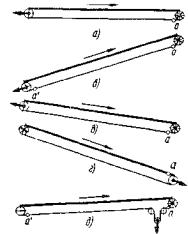
уменьшение наибольшего натяжения тягового элемента (по которому рассчитываются его прочные размеры); возможное уменьшение натяжения тягового элемента при сгибании им криволинейных участков и поворотных пунктов с целью уменьшения на них расхода энергии на преодоление вредных сопротивлений и, что особенно важно, уменьшения износа. Для этого при сложном контуре конвейера целесообразно устанавливать привод по ходу тягового элемента после участка или группы участков с наибольшим сопротивлением и перед группой близко друг к другу расположенных поворотных пунктов или криволинейных участков, которые в этом случае тяговый элемент огибает со стороны сбегания с привода, т. е. при пониженном натяжении.
В случае передачи на тяговый элемент движущей силы трением привод целесообразно располагать в той точке контура, где повышенное натяжение получается «естественным путем», например, после участка с наибольшим сопротивлением. При этом иногда удается избегнуть необходимости повышать натяжение на натяжном устройстве и снизить наибольшее натяжение тягового элемента.
Рис. 3.1-Схемы расположения привода и натяжного устройства
В простейшем случае, если конвейер состоит из двух параллельных ветвей и расположен горизонтально или с наклоном и движение груза происходит вверх по наклону (рис. 3.1, а и б) привод следует располагать в головной части конвейера, т. е. в конце грузовой ветви. Если движение груза происходит по наклону вниз и общее сопротивление на грузовой ветви (т. е. алгебраическая сумма сил вредного сопротивления и составляющей веса) Wгр>0, то привод целесообразно располагать тоже в головной части конвейера (рис. 3.1, в), а в противном случае, при Wгр < 0, - в хвостовой части конвейера (рис. 3.1, г). В последнем случае, в зависимости от того, является ли общее сопротивление на конвейере величиной положительной или отрицательной, электродвигатель работает в двигательном или генераторном режиме.
Наименьшее натяжение тягового элемента на горизонтальном конвейере всегда имеет место у привода на сбегающей ветви (точка а). На наклонном конвейере с движением груза вверх при сопротивлении на обратной ветви Wп>0 наименьшее натяжение тягового элемента тоже будет на сбегающей ветви у привода (точка а), а при сопротивлении Wn<0 - в нижней точке обратной ветви (точка а'). При движении груза по наклону вниз и Wгр>0 точка наименьшего натяжения тягового элемен-
40