
4_Метод_указ_2176
.pdfструктуре феррита, карбидов или Аост ухудшает все пружинные свойства. Чем мельче зерно, тем выше сопротивление стали малым пластическим деформациям.
Наиболее часто для изготовления пружин вагонов, многих автомобильных рессор и т.п. используются стали 55С2, 60С2А, 70С3А, 65Г.Однако эти стали склонны к обезуглероживанию при горячей обработке, что снижает их предел выносливости. Дополнительное легирование Cr, Mn, W, Ni увеличивает их прокаливаемость и уменьшает склонность к обезуглероживанию.
Стали 60С2ХФА и 65С2ВА применяют для изготовления крупных высоко-нагруженных пружин и рессор. Для изготовления автомобильных рессор широко применяют сталь 50ХГА. Для клапанных пружин 50ХФА. Оптимальная твердость рессор для получения максимального предела выносливости 42-48 HRCэ. При более высокой твердости предел выносливости, а, следо-вательно, долговечность рессор и пружин резко снижается.
Шарикоподшипниковые стали. ГОСТ 801-78
Эти стали применяют для изготовления деталей подшипников качения: шариков, роликов и подшипниковых колец. Стали после термической
обработки (закалка и низкий |
отпуск) должен |
обладать |
высокой |
твердостью, износостойкостью и сопротивлением контактной |
усталости. |
||
В сталях недопустима карбидная |
неоднородность |
и неметаллические |
включения, т.к. они вызывают преждевременное усталостное разрушение. Для получения оптимального сочетания прочности и контактной выносливости кольцо и ролики подшипников должны иметь после закалки и отпуска твердость 60-65 HRCэ. Структура стали после термической обработки состоит из мартенсита, мелких вторичных карбидов и Аост. Однако присутствие Аост в структуре уменьшает стабильность размеров подшипников. Поэтому для подшипников, которые должны иметь высокую стабильность размеров после закалки перед отпуском применяют обработку холодом при -70...-80 градусах. Для изготовления тел качения и подшипниковых колец используют высокоуглеродистые ( 0,95-1,05% углерода) хромистые стали ШХ15, ШХ15СГ, ШХ4. Буква Ш указывает, что это сталь шарикоподшипниковая, буквы Х, С и Г - легирующие элементы, цифра после буквы «Х» показывает содержание хрома в десятых долях процента.
30
Износостойкие стали. ГОСТ 2176-77
Износостойкие стали применяются для изготовления деталей, работающих на износ в условиях абразивного трения и высоких давлений и ударов, например, для траков гусеничных машин, щек дробилок, черпаков землечерпальных машин, лопастей смесеприготовительных машин, крестовин железнодорожных путей. Для их изготовления применяется сталь 110Г13Л. Структура стали после литья состоит из аустенита и избыточных карбидов (Fe,Mn)3С , выделяющихся по границам зерен, что снижает прочность и вязкость стали. В связи с этим литые изделия закаливают с нагревом до температуры 1100 градусов и охлаждением в воде. При таком нагреве растворяются карбиды, и сталь после закалки приобретает более устойчивую аустенитную структуру. Сталь с аустенитной структурой характеризуется низким пределом текучести и сильно
упрочняется под действием пластической деформации |
(наклепывает- |
ся). Высокой износостойкостью сталь обладает только при |
ударных на- |
грузках, когда происходит деформационное упрочнение аустенита и образование E-мартенсита с ГПУ решеткой.
При небольших ударных нагрузках в сочетании с абразивным изнашиванием либо при чистом абразивном изнашивании мартенситное пре-вращение не протекает и износостойкость стали 110Г13Л невысокая. Твер-дость стали в процессе работы возрастает с 20-25 HRCэ до 50-55 HRCэ. Сталь трудно обрабатывается резанием и применяется после литья.
Коррозионные стали. (Нержавеющие стали).ГОСТ 5632-72 Нержавеющими называются стали устойчивые электрохимиче-
ской коррозии, вызываемой воздействием атмосферных условий, |
реч- |
|
ной и морской воды, растворами кислот, щелочей и солей. |
|
|
Механизм электрохимической коррозии сводится к следующему: ес- |
||
ли в электролит (влажный воздух, водные растворы кислот, |
щелочей, |
со- |
лей) поместить два соприкосающихся металла, образуется |
гальваниче- |
|
ский элемент. При этом, металл, который легче, отдает электроны, |
слу- |
жит анодом, а другой - катодом. В процессе работы гальванического элемента анод разрушается.
Микрогальванические элементы возникают также между различными фазами сплавов и даже в чистых металлах, где роль анодов играют
границ зерен и другие дефектные участки, а роль катода |
- тело |
зерна. |
|||
Чем больше отдельные фазы (участки) металла отличаются |
электрохими- |
||||
ческими потенциалами, тем быстрее происходит разрушение. В |
неод- |
||||
нородном металле |
различают |
местную |
(точечную, |
пятнистую) |
|
и интеркристаллическую, распространяющуюся по границам зерен, |
кор- |
||||
розии. Наиболее опасна последняя, т.к. резко |
снижает |
механические |
|||
свойства без заметных внешних признаков. |
|
|
|
31
Из вышесказанного следует, что материалы с однофазной крупнозернистой структурой без дефектов поверхности и с высокой чистотой обработки поверхности обладают высокой коррозионной стойкостью.
Сталь становится коррозионностойкой при введении в ее состав 13% и более хрома. Хром, растворяясь в железе, скачкообразно изменяет электрохимический потенциал стали. Потенциал из отрицательного становится резко положительным, а сталь из активного состояния переходит в пассивное. В этом случае хром образует на поверхности плотную защитную оксидную пленку типа (Cr,Fe)2O3.
Увеличение содержания углерода в стали снижает ее коррозионную стойкость, т.к. углерод связывает хром в карбиды и удаляет его из твердого раствора. Кроме того, выделение карбидов превращает структуру из однофазной в двухфазную. Коррозионная стойкость стали повышается термической обработкой: закалка с высоким отпуском.
Нержавеющие стали можно разделить на два основных класса:
1)хромистые, имеющие после охлаждения на воздухе ферритную (12Х17, 15Х25Т, 15Х17Н2Б), мартенситно-ферритную (12Х13) и мартенситную (20Х13, 3ОХ13, 40Х13) структуры;
2)хромо-никелевые, имеющие аустенитную (12Х18Н9, 10Х14Г14Н4Т, 10Х14АГ15), аустенитно-мартенситную (09Х15Н8Ю) и аустенитно- феррит-ную (08Х21Н6М2Т) структуры.
Применение нержавеющих сталей
12Х13 и 20Х13 применяются для изготовления деталей с повышенной пластичностью, подвергающихся ударным нагрузкам, клапанов гид- равличес-ких прессов, а также предметов домашнего обихода. В отожженном состоя-нии структура состоит из феррита и перлита.
30Х13, 40Х13 - для карбюраторных игл, пружин, хирургических инструментов и т.д. Первая в отожженном состоянии имеет структуру перлита, а вторая - перлита со вторичными карбидами.
15Х25Т, 015Х17М2Б - используют без термической обработки для сварных конструкций и деталей, работающих в более агрессивных средах. После любой термообработки имеют ферритную структуру.
12Х18Н9 - холоднокатанный лист и лента повышенной прочности для деталей и конструкций, свариваемых точечной сваркой, а также для изготовления труб и других деталей, работающих в коррозионной среде.
10Х14Г14Н4Т - для изготовления разнообразного сварного оборудования,работающего в средах химических производств слабой агрессивности, криогенной техники до -253 градусов, а также в качестве жаростойкого и жаропрочного материала до 700 градусов.
08Х22Н6Т, 08Х18Н10Т - сварные аппараты и сосуды, камеры горения газовых турбин, фланцы, диски, детали внутренних устройств аппара-
32
тов, работающих при температуре от -10 градусов до +300 |
градусов |
под давлением в присутствии коррозионных сред. |
|
08Х21Н6М2Т - крепежные детали, работающие в средах повы- |
|
шенной агрессивности при 600 градусах. |
|
Магнитомягкие стали. ГОСТ 21427-75 |
|
Эти стали применяют для изготовления магнитопроводов |
постоян- |
ного и переменного тока, якорей, роторов, статоров двигателей. К ним предъ-являются требования высокой магнитной проницаемости, низкой коэрци-тивной силы, малых потерь при перемагничивании и потерь на вихревые токи.
Для получения необходимых свойств ферромагнитный материал должен быть чистым от примесей и включений, иметь гомогенную (однофазную) крупнозернистую структуру. Даже слабый наклеп снижает магнитную проницаемость и повышает коэрцитивную силу (Нс), поэтому материал должен быть полностью рекристаллизован.
В качестве магнитомягких |
материалов используются низ- |
коуглеродистые (0,05-0,005% углерода) |
стали. В состав сталей вводит- |
ся кремний (0,8-4,8%). Кремний вызывает рост зерна феррита, тем самым снижает коэрцитивную силу, а, растворяясь в феррите, - уменьшает потери на вихревые точки.
Электротехническая сталь маркируется цифрами: первая цифра определяет структуру и вид прокатки (1-горяче катаная изотропная, 2- холодно катаная изотропная); вторая цифра указывает содержание кремния (0 - до 0,4%; 1 - 0,4-0,8%; 2 - 0,8-1,8%; 3 - 1,8-2,8%; 4 - 2,8-3,8%; 5 - 3,8-4,8%); третья цифра - потери на гистерезис и тепловые потери; четвертая цифра - код нормируемого параметра.
Примеры марок: 1212, 1511, 2011, 2212 и т.д.
Структура сталей ферритная.
Э к с п е р и м е н т а л ь н а я ч а с т ь
1.Получить коллекцию легированных сталей.
2.Исследовать микроструктуру различных марок легированных сталей.
3.Схематично зарисовать микроструктуры сталей, обозначив структурные составляющие.
4.Связать микроструктуру со свойствами стали.
5.Объяснить, почему у сталей одинакового химического состава микроструктуры различны.
6.Расшифровать изучаемые марки сталей и указать их применение.
7.Оформить отчет.
Отчет по работе должен содержать теоретическую и экспериментальные части.
33
К о н т р о л ь н ы е в о п р о с ы
1.Преимущества легированных сталей по сравнению с углеродистыми.
2.Распределение легирующих элементов в сталях и их влияние на свойства.
3.Классификация легированных сталей по назначению и структуре.
4.Маркировка легированных сталей.
5.Строение, назначение и свойства изучаемых в работе сталей.
34
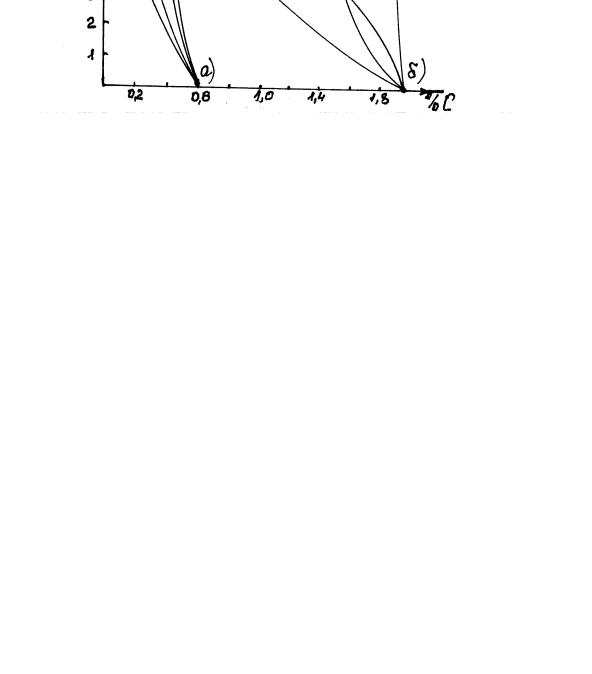
Рис.1. Влияние легирующих элементов на изменение твердости (а) и ударной вязкости (б).
Рис. 2. Схема влияния легирующих элементов на точку (а) и точку (б).
35

Рис. 3. Схема влияния легирующих элементов на полиморфизм железа.
36

Рис. 4. Классификация легированных сталей.
37
Л А Б О Р А Т О Р Н А Я Р А Б О Т А N 5
ЛЕГИРОВАННЫЕ ИНСТРУМЕНТАЛЬНЫЕ СТАЛИ
Цель работы: получить навыки по классификации и свойствам
инструментальных сталей, изучить важнейшие марки инструментальных сталей и влияние легирующих элементов после различных видов термообработки.
Т е о р е т и ч е с к а я ч а с т ь
Основными материалами для изготовления инструментов являются инструментальные стали. Создание новых инструментальных материалов с более высокими свойствами не влечет за собой сильного сокращения производства ранее созданных инструментальных сталей, успешно применяемых в промышленности. Доля многих из них в общем производстве инструментальных сталей остается преобладающей и обеспечивающей производительность при обработке материалов, более мягких или с умеренным сопротивлением пластической деформации.
Таким образом, еще более возрастает число инструменатальных ста-
лей, различающихся по составу, свойствам и особенностям обработки |
и |
применения. |
|
Любой инструмент в процессе работы изнашивается, поэтому |
к |
инструменту помимо требований, предъявляемых к конструкционным деталям, предъявляются требования высокой износостойкости, а в ряде слу-
чаев - теплостойкости, обеспечивающей сохранение высокой |
твердо- |
сти при нагреве инструмента. |
|
Для обеспечения высокой твердости и износостойкости большинст- |
|
во инструментальных сталей имеет высокое содержание углерода |
от 0,7 |
до 1,3%. |
|
Для лучшей ориентации при выборе сталей для инструментов проводят классификацию инструментальных сталей по двум признакам : по свойствам и по назначению.
На рис. 1 приведена схема классификации инструментальных сталей по свойствам, предложенная Ю.А.Геллером.
За основное свойство при этой классификации принята теплостойкость стали, т.к. она определяет природу упрочнения стали при термообработке и во многих случаях условия использования стали. Теплостойкость характеризует температура нагрева, при которой сталь после закалки начинает интенсивно терять свою твердость, а, значит, и износостойкость. По теплостойкости различают три группы инструментальных сталей: теплостойкие, полутеплостойкие, нетеплостойкие.
38
Н е т е п л о с т о й к и м и являются углеродистые и легированные стали, которые после закалки имеют высокую твердость и износостойкость в результате мартенситного превращения. При нагреве до 200300 градусов основное количество углерода выделяется из мартенсита и начинается коагуляция карбидов цементитного типа. В результате сталь теряет твердость, износостойкость.
П о л у т е п л о с т о й к и м и |
являются |
средние и высоколеги- |
рованные (в основном хромом) стали. |
Твердость |
этих сталей также дос- |
тигается закалкой на мартенсит. Однако при отпуске образуется более легированный цементит и специальные карбиды, благодаря чему сталь сохраняет повышенную твердость до 300-500 градусов.
Т е п л о с т о й к и м и являются высоколегированные стали, которые приобретают твердость: а) в результате мартенситного превращения при закалке; б)дисперсионного твердения при высоком отпуске (500-625 градусов) за счет выделения дисперсных фаз-упрочнителей. Этими фазами являются сложные карбиды вольфрама, молибдена, ванадия.
Теплостойкие стали имеют преимущества перед нетеплостойкими не только потому, что инструмент из таких сталей допускает обработку
при интенсивных режимах, когда остальные |
стали теряют твердость и |
||
износостойкость. Теплостойкие стали имеют |
и |
другие |
положитель- |
ные особенности. Как известно, большинство |
инструментов после |
||
термообработки подвергают шлифованию для |
получения |
необходимой |
чистоты рабочей поверхности. Это повышает вязкость и прочность инструмента. В процессе шлифования имеет место достаточно высокий местный нагрев поверхностных слоев обрабатываемого изделия, что может привести к частичному распаду мартенсита. Естественно, что для теплостойких сталей местный нагрев менее опасен и менее влияет на понижение твердости и износостойкости.
При закалке инструментальных сталей, особенно легированных, наряду с мартенситом в структуре стали остается повышенное количество остаточного аустенита Аост. При малых количествах он почти не снижает твердость инструмента, но снижает прочность (Gт, Sот, Gв, КСU) и шлифуемость стали (от разогрева поверхности может иметь место превращение Аост Мотп, что вызывает дополнительные напряжения и возможность образования шлифовочных трещин). Поэтому необходимо стремиться к снижению Аост при термообработке. Устранение Аост для нетеплостойких сталей отпуском без снижения твердости затруднительно. Применение обработки холодом значительно усложняет технологический процесс. В теплостойких сталях, подвергаемых отпуску при 500-600 градусах, остаточный аустенит переходит в мартенсит отпуска без потери твердости и износостойкости. Поэтому такие стали имеют более высокие показатели прочности, хорошо сопротивляются пластической деформации.
39