
5_Метод_указ_2924
.pdfФизико-механические свойства некоторых термопластичных материалов приведены в таблице 1.
|
|
|
|
|
|
|
Таблица 1 |
|
|
|
|
|
|
||
Материал |
Плот- |
Времен- |
Относи- |
Твер- |
Ударная |
||
|
ность, |
ное сопро- |
тельное |
дость |
вязкость |
||
|
кг/м3 |
тивление, |
удлине- |
по Бри- |
(образцы с |
||
|
|
|
в , МПа |
ние при |
неллю |
надрезом), |
|
|
|
|
|
разрыве, |
|
|
кДж/м2 |
|
|
|
|
% |
|
|
|
Полиэтилен ПЭВД |
918 |
– 930 |
10 – 17 |
150 – 600 |
1,4 |
– 2,5 |
не ломается |
ПЭНД |
949 |
– 955 |
22 – 30 |
300 – 800 |
4,5 |
– 3,8 |
150 |
Полипропилен |
920 |
– 930 |
25 – 30 |
200 – 800 |
6,0 |
– 6,5 |
50 – 120 |
Фторопласт-4 |
2150 |
– 2240 |
14 – 25 |
250 – 500 |
3,0 |
– 4,0 |
100 |
Полистирол |
1000 |
– 1050 |
31 – 50 |
2 – 12 |
14 |
– 20 |
10 – 22 |
Полиамиды |
1112 |
– 1160 |
50 – 100 |
50 – 150 |
14 |
– 15 |
80 – 130 |
Поливинилхлорид |
1350 –1420 |
40 – 60 |
5 – 100 |
13 |
– 16 |
20 – 100 |
1.2. Композиционные материалы на основе полимеров
Композиционные материалы (композиты) представляют собой гетерофазные системы, состоящие из двух и более разнородных компонентов, имеющих границы раздела между ними. Компонент, непрерывный по всему объему материала, обеспечивающий его монолитность, называется матрицей или связующим. Компоненты, распределенные в матрице, называются наполнителями.
По типу матрицы различают композиционные материалы на полимерной, металлической и керамической основе. Матричный материал более вязкий и обеспечивает перераспределение действующей нагрузки по объему, защиту наполнителя от воздействия внешней окружающей среды, определяет электрические и теплофизические свойства, стойкость к старению, технологические и другие свойства композита. Композиционные материалы на основе полимеров называют пластмассами, т. к. эти материалы при нагревании размягчаются, становятся пластичными.
Наполнители в композиционные материалы вводят с целью улучшения механических, теплофизических, электрических, магнитных и других свойств. В качестве наполнителей используют твердые, жидкие и газообразные вещества органического и неорганического происхождения.
Наиболее распространенные наполнители – твердые, представляющие собой высокодисперсные порошки, волокна, (стеклянные, углеродные, полимерные, металлические), слоистые наполнители (ткани, фольга, шпон и др.).
В качестве дисперсных наполнителей широкое применение получили: древесная мука, сульфатная целлюлоза, графит, тальк, слюда, каолин, диоксид кремния, силикаты алюминия, кальция, магния, порошки металлов и
20
сплавов. Некоторые металлические наполнители придают композитам специфические свойства. Например, железо и его сплавы – ферромагнитные; чешуйки алюминия, никеля, серебра – низкую газо- и паропроницаемость; порошки алюминия и меди – декоративность; свинца, кадмия, вольфрама – защитную способность при воздействии излучений высоких энергий.
Дисперсно-упрочненные композиционные материалы с равномерно распределенным в объеме материала наполнителем обладают изотропностью свойств, т. е. одинаковыми свойствами во всех направлениях. Для создания материалов антифрикционного назначения широко используются слоистые твердые смазки МоS2, МоSе2, ВN, СdO, СаF2, графит и другие, а также жидкие наполнители, в качестве которыхприменяютминеральные масла.
В качестве волокнистых наполнителей используют хлопковые и льняные очесы, стекловолокно, асбест, углеродное волокно. Все более широкое применение получают синтетические волокна, в частности, полиамидные и полиэфирные. Пластмассы, содержащие синтетические волокна, характеризуются высокой коррозионной и химической стойкостью, малым коэффициентом трения и высокой износостойкостью, однако обладают низкой теплостойкостью.
Современные композиционные материалы содержат в качестве наполнителей угольные и графитовые волокна, волокна бора и др.
Упрочненные волокнами материалы анизотропны, кроме случая хаотического расположения волокон. Упрочняющий эффект при наполнении волокнами диаметром 3 – 12 мкм сказывается уже при их длине, равной 2 – 4 мм, благодаря взаимному переплетению и снижению напряжений в связующем. С увеличением длины волокон увеличиваются прочность и ударная вязкость. В свою очередь, упрочняющие волокна в композитах могут быть дискретными и непрерывными, а непрерывные волокна могут быть однонаправленными или направленными в разные стороны.
Из слоистых наполнителей применяются: бумага (для получения гетинакса); хлопчатобумажная ткань, стеклоткань, асботкань, углеграфитная ткань (в различного рода текстолитах); древесный шпон (в древопластиках). Слоистые (двухмерно-армированные) композиты представляют собой набор слоев из одинаковых или разных армирующих материалов, пропитанных связующим.
Слоистые материалы отличаются анизотропией свойств – имеют высокую прочность при растяжении вдоль слоев армирующего наполнителя
инизкую в перпендикулярном направлении. Этот недостаток отсутствует
уобъемно-тканых или трехмерно-армированных материалов.
При создании поро- и пенопластов используют газообразные наполнители (углекислый газ, азот, воздух и инертные газы).
21
Достоинства и недостатки материалов на основе полимеров.
К преимуществам полимеров и материалов на их основе перед металлами относятся:
–низкая плотность, которая у большинства пластмасс находится в диапазоне от 900до2000 кг/м3;
–высокие антифрикционные свойства в условиях трения без подвода смазки, что позволяет применять их в качестве самосмазывающихся материалов для изготовления подшипников скольжения;
–легкость введения в полимеры твердых, жидких и газообразных, компонентов (наполнителей и армирующих элементов), которые могут в широких пределах изменять их свойства;
–высокие электроизоляционные свойства, особенно у фторопласта, полиэтилена, полипропилена, полистирола, стеклопластиков;
–удовлетворительная стойкость к действию абразивной среды;
–стойкость к действию многих .агрессивных сред (кислот, щелочей, растворов солей);
–хорошие технологические свойства – многие пластмассы легко перерабатываются в изделия методами литья под давлением, экструзией, вакуумным и пневматическим формованием, хорошо свариваются, склеиваются, обрабатываются резанием и т. д.
Однако наряду с названными выше ценными свойствами пластмасс можно привести и их недостатки, к которым относятся:
–невысокая теплостойкость, особенно это относится к термопластам на основе, полистирола, полиэтилена, полиамида, теплостойкость которых
не превышает 110 С. Теплостойкость термореактивных пластмасс на основе, фенольных, эпоксидных, полиамидных и кремнийорганических смол несколько выше и составляет до 150 – 250 С;
–низкий модуль упругости и ударная вязкость по сравнению с металлами;
–склонность пластмасс к старению под действием света, кислорода
воздуха и тепла;
–высокий коэффициент линейного расширения, он в десятки раз больше чем у металлов, что необходимо учитывать при проектировании металлополимерных соединений;
–низкая теплопроводность, во много раз ниже, чем у металлов.
2.Экспериментальная часть
2.1.Изучение микроструктуры пластмасс
Получить у преподавателя образцы и изучить микроструктуру пластмасс с помощью оптического микроскопа в отраженном свете, зарисовать микроструктура определить фазовый состав материала.
22

2.2. Определение временного сопротивления разрушающим напряжением при растяжении ( в ) и относительного удлинения при раз-
рыве ( )
Испытания на растяжение проводятся в соответствии с ГОСТ 11262-80 на образцах в виде двухсторонних лопаток, форма которых приведены на рис. 4.
В
l0
L
Рис. 4. Образец для испытаний на растяжение
Порядок проведения испытаний
Замерить ширину (В), толщину ( ) и длину участка постоянного поперечного сечения (l0) испытуемых образцов.
Закрепить образцы в зажимах разрывной машины РМИ-5. Установить нуль на шкале измерения нагрузки и скорость перемещения подвижного зажима 50 мм/мин.
Включить механизм нагружения.
Определить по шкале циферблата максимальную нагрузку Рmax при разрушении образца и соответствующее ей абсолютное удлинение рабочего участка образца l .
Временное сопротивление разрушающим напряжениям при растяжении вычислить по формуле:
в ВPmax ,
где Рmax – максимальная нагрузка при разрыве;
В и – ширина и толщина рабочего участка образца. Относительное удлинение при разрыве вычислить по формуле:
l 100 %, l0
где l – абсолютное удлинение;
23
l0 – базовая длина рабочего участка образца, мм. Результаты испытаний занести в таблицу 2.
Таблица 2
№ |
Материалы |
Толщина |
Ширина |
Базовая |
l, |
Pmax, Н |
в, |
, |
п/п |
|
образца, |
рабочего |
длина |
мм |
|
МПа |
% |
|
|
, мм |
участка, |
рабочего |
|
|
|
|
|
|
|
В, мм |
участка, |
|
|
|
|
|
|
|
|
l0, мм |
|
|
|
|
|
|
|
|
|
|
|
|
|
|
|
|
|
|
|
|
|
|
2.3. Определение ударной вязкости пластмассовых образцов
по Шарпи
Ударная вязкость определяется как отношение энергии удара, затраченной на разрушение образца, к площади поперечного сечения образца в месте разрушения.
Испытания проводятся на маятниковых копрах путем разового разрушения свободно лежащего на опорах образца под действием падающего маятника со скоростью 2 – 4 м/с, вращающегося вокруг горизонтальной оси. Схема испытаний и форма образца испытаний приведены на рис. 5.
Ударная вязкость согласно ГОСТ 4647-80 определяется на образцах с надрезом и без надреза. Ударную вязкость образцов с надрезом (ак) вычисляют по формуле:
a |
к |
|
Aк |
103 , |
|
||||
|
|
В Sк |
где Ак – энергия, затраченная на разрушение образца с надрезом, Дж; В – ширина образца по его середине, мм; Sк – толщина образца под надрезом, мм.
При испытании образцов без надреза ударная вязкость обозначается аn и определяется по формуле:
a |
n |
|
An |
103 , |
|
В S |
|||||
|
|
|
где Аn – энергия удара, затраченная на разрушение образца без надреза, Дж; В– ширина и S толщина образца по его середине, мм.
24

а
б
Рис. 5. Схема испытаний (а) и форма образца с надрезом (б): 1 – испытуемый образец; 2 – опора; 3 – боек маятника;
4 – направление удара маятника
Порядок проведения испытаний
Установить указатель шкалы величины энергии так, чтобы он касался ведущего кулачка маятника, когда он находится в положении, при котором боек маятника касается образца.
Замерить геометрические размеры образца и установить образец на опоры копра так, чтобы ось бойка и середина образца имели отклонение не более 0,5 мм.
Отвести маятник на угол , соответствующий необходимому запасу энергии, зафиксировать его. Записать величину запаса потенциальной энергии Е0.
25
Плавно отпустить маятник, освободив его от фиксатора. Определить по шкале копра показание оставшейся после разрушения образца энергии Е1. Энергия, затраченная на разрушение образца, определяется как разность между Е0 и Е1. Потерями на трение пренебрегаем.
Ударную вязкость вычислить по приведенным выше формулам. Все данные занести в таблицу 3.
|
|
|
|
|
Таблица 3 |
|
|
|
|
|
|
№ |
Материалы |
В, |
Sк (S), |
Ак (Аn), |
ак (аn), |
п/п |
|
мм |
мм |
кДж |
кДж/м2 |
|
|
|
|
|
|
3. Содержание отчета
1.Цель работы.
2.Основные теоретические сведения об особенностях свойств пластмасс.
3.Методики определения временного сопротивления и ударной вязкости.
4.Результаты испытания.
4.Контрольные вопросы
1.Особенности строения и свойств полимерных материалов.
2.Особенности стеклообразного состояния полимеров.
3.Особенности поведения полимеров в высокоэластическом состоянии.
4.Вязкотекучее состояние полимеров.
5.Термомеханические кривые для аморфныхи кристаллическихполимеров.
6.Особенности структуры и свойств термопластичных и термореактивных полимеров.
7.Композиционные материалы на основе полимеров и их состав.
8.Основные виды наполнителей и их влияние на свойства композитов.
9.Достоинства и недостатки материалов на основе полимеров.
Литература
1.Кенько В.М., Неметаллические материалы и методы их обработки. –
Мн.: Дизайн ПРО, 1988. – 240 с.
2.Лахтин Ю.М., Леонтьева В.П., Материаловедение. – М.: Машинострое-
ние, 1980. – 487 с.
3.ГОСТ 4647-80. Пластмассы. Метод определения ударной вязкости по Шарпи.
4.ГОСТ 11262-80. Пластмассы. Метод испытания на растяжение.
26
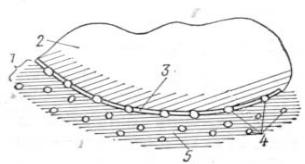
Лабораторная работа № 15
АНТИФРИКЦИОННЫЕ МАТЕРИАЛЫ
Цель работы: ознакомиться с составом, маркировкой, микроструктурой, применением антифрикционных материалов.
Приборы и материалы: микроскоп ММУ-3, травитель, спирт, фильтровальная бумага, вата, коллекция микрошлифов.
Выполнение работы рекомендуется проводить в следующем порядке:
1. Ознакомиться по методическому указанию с маркировкой, свойствами, структурой и применением антифрикционных материалов
Антифрикционными называются сплавы, предназначенные для по-
вышения срока службы трущихся поверхностей механизмов и машин. Эти сплавы используются для изготовления подшипников скольжения. Применяют их в виде вкладышей.
Поверхность вала и вкладыша должны быть разделены пленкой смазки (рис. 1).
Рис. 1. Поверхность раздела вкладыш – вал (схема): 1- вкладыш, 2 – вал, 3 – пространство для смазки, 4 – твердые включения, 5 – мягкая основа
Материал вкладыша должен обладать:
–низким коэффициентом трения;
–высокой теплопроводностью;
–хорошей прирабатываемостью к валу;
–хорошими технологическими свойствами.
В связи с этим, строение антифрикционных сплавов должно быть гетерогенным: с мягкой пластичной основой и равномерно распределенными мелкими твердыми частицами.
27

Твердые частицы служат опорой вала и уменьшают трение, а мягкая пластичная основа обеспечивает прирабатываемость. Кроме того, в этой основе (изнашивающейся при трении) образуются мельчайшие каналы, по которым распределяется смазка.
К сплавам для подшипников скольжения относятся антифрикционные бронзы и чугуны; легкоплавкие сплавы на основе Pb, Sn, Zn, Al, а также металлокерамические материалы и неметаллические материалы.
Антифрикционные бронзы.
Вкладыши подшипников изготавливают из оловянистых и свинцовистых бронз.
У оловянистых бронз мягкой основой является – твердый раствор,
светлая составляющая, а твердыми включениями – эвтектоид ( + ) темная составляющая (рис. 2).
(I)
(II)
а |
б |
Рис. 2. (I) Диаграмма состояния системы Cu-Sn (II) Микроструктуры литой оловянистой бронзы (а, б)
28

Для изготовления вкладышей применяются Бр.ОЦС5-5-6,
Бр.ОЦС4-4-17, Бр.ОЦС 3,5-7-5, Бр.ОЦС 4-4-2,5.
В бронзах кроме олова (О) содержится цинк (Ц) и свинец (С). Цифры в марке указывают процентное содержание элементов в той же последовательности, а остальное до 100 % – медь. Zn повышает механические свойства и жидкотекучесть, а Pb – улучшает антифрикционные свойства и жидкотекучесть оловянистых бронз.
Свинцовистые бронзы типа Бр.С30 являются заменителями оловянистых бронз.
а |
б |
Рис. 3. а – диаграмма состояния сплавов системы Cu – Pb; б – микроструктура свинцовистой бронзы
Как видно из диаграммы состояния Cu и Pb не растворяются в твердом состоянии, а образуют механическую смесь мягких зерен Pb (мягкая основа) и более твердых зерен Cu (твердые включения). Однако относительно невысокая твердость зерен Cu позволяет достигать хорошей прирабатываемости вкладышей.
Антифрикционные бронзы используются для изготовления вкладышей, работающих в особо тяжелых условиях эксплуатации (значительные удельные давления и числа оборотов вала), но недостатком бронз является их высокая стоимость и сравнительно невысокая прочность, поэтому их иногда наплавляют на стальную ленту.
Антифрикционные чугуны
Для менее ответственных вкладышей в машиностроении применяют серый чугун АЧС-1 и АЧС-2, обладающий перлитной структурой и повы-
29