
тех оборудование практика / Практическая работа часть 1
.pdf
в нижней зоне
|
|
|
(17) |
Тогда общая разность, кДж/ч: |
|
|
|
|
. |
|
(18) |
Расход воздуха, нагреваемого в калорифере, кДж/ч: |
|
|
|
[ |
( |
] ( |
(19) |
Расход свежего (добавочного) воздуха, кДж/ч: |
|
|
|
|
|
|
(20) |
Расход теплоты, отдаваемой калорифером нагреваемому воздуху, кДж/ч:
|
|
( |
|
(21) |
|
Учитывая, что потери при сжигании топлива |
|
общего расхода |
|||
теплоты калорифера, общий расход теплоты в сушилке, кДж/ч: |
|
|
|||
|
[ |
( |
] |
(22) |
|
Расход теплоты на 1 кг высушенного солода, кДж/ч: |
|
|
|||
|
|
|
⁄ |
|
(23) |
Таблица 1 – Варианты индивидуальных заданий |
|
|
|||
|
|
|
|
|
|
Номер варианта |
Gсуш, кг/ч |
|
Номер варианта |
Fр, м2 |
|
|
|
|
|
|
|
1 |
500 |
|
14 |
|
520 |
|
|
|
|
|
|
2 |
480 |
|
15 |
|
430 |
3 |
520 |
|
16 |
|
440 |
|
|
|
|
|
|
4 |
550 |
|
17 |
|
560 |
|
|
|
|
|
|
5 |
450 |
|
18 |
|
410 |
|
|
|
|
|
|
6 |
470 |
|
19 |
|
570 |
|
|
|
|
|
|
7 |
530 |
|
20 |
|
390 |
|
|
|
|
|
|
8 |
540 |
|
21 |
|
600 |
|
|
|
|
|
|
|
|
21 |
|
|
9 |
490 |
22 |
620 |
|
|
|
|
10 |
460 |
23 |
535 |
|
|
|
|
11 |
400 |
24 |
515 |
|
|
|
|
12 |
420 |
25 |
485 |
|
|
|
|
13 |
510 |
26 |
630 |
|
|
|
|
22

Практическая работа №4
Машины для измельчения солода и не соложеных материалов 1 Вальцовые дробилки
Теоретическая часть
Дробление высушенного солода представляет собой тонкое измельчение мучнистого ядра солода для быстрого осахаривания во время варки пивного сусла без повреждения оболочек, которые обеспечивают пористость слоя пивной дробины при фильтрации сусла. Солододробилки выпускаются четырех- и шестивальцовыми.
Основными рабочими органами дробилки (рисунок 1) служат три пары вальцов для предварительного дробления, отделения мякинных оболочек и получения крупки, а также плоские вибросита с двумя рядами отверстий в каждом. Они разделяют проходящий через пары вальцов помол на три части: грубая составляющая часть – шелуха с прилипшей крупкой или шелуха; средняя составляющая часть – крупка; тонкая составляющая часть – крупка и мука. Мука отводится непосредственно в бункер для помола, так как её больше не измельчают. Оболочки размалываются на второй паре вальцов с максимальным их сохранением. На третьей паре вальцов измельчается крупка до любых размеров.
Рисунок 1.1 – Схема шестивальцовой дробилки с виброситами
Расчет вальцовой дробилки
Рассчитать производительность и необходимую мощность четырехвальцовой
дробилки с диаметром и длиной вальцов |
, окружная скорость которых |
||
составляет |
, если насыпная плотность товарного солода |
, |
|
средний диаметр поступающих на измельчение частиц солода |
, |
||
динамический коэффициент трения частиц солода о поверхность вальцов |
. Угол |
||
захвата |
, а коэффициент неравномерности подачи на размол |
. |
|
|
|
23 |
|
Зазор между вальцами с учетом того, что условие нормального дробления солода
выдержано, т. е. |
( |
, м: |
|
|
|
|
|
|
|||
|
|
[ ( |
|
) ( |
|
|
|
) |
|
]. |
(1) |
|
|
|
|
|
|
В соответствии с условием дробления полученный зазор должен находиться в диапазоне , и если это условие не выполняется, меняем угол захвата .
= 2,5 мм.
Частота вращения вальцов, с-1:
( |
. |
(2) |
Фактическая производительность дробилки, кг/ч:
(3)
Для ориентировочного сравнения определим производительность солододробилки, исходя из условия, что на каждую 0,1 м длины вальцов приходится
высушенного солода, кг/ч:
|
|
( |
(4) |
|
Если фактическая производительность |
значительно отличается от |
|
ориентировочной |
и эта разность составляет |
и более, изменяем |
|
частоту вращения вальцов. |
|
||
|
Необходимая мощность для вращения вальцов, кВт/ч: |
||
|
|
|
(5) |
где |
– удельная мощность, |
на каждый килограмм часовой |
производительности дробилки.
Таблица 1 – Варианты индивидуальных заданий
Номер |
Dвлц, м |
, м |
, м/с |
|
Номер |
Dвлц, м |
, м |
, м/с |
варианта |
|
варианта |
||||||
|
|
|
|
|
|
|
||
|
|
|
|
|
|
|
|
|
1 |
0,25 |
0,5 |
1,5 |
|
14 |
0,22 |
0,56 |
1,4 |
|
|
|
|
|
|
|
|
|
2 |
0,26 |
0,45 |
1,4 |
|
15 |
0,23 |
0,5 |
1,55 |
|
|
|
|
|
|
|
|
|
3 |
0,28 |
0,4 |
1,6 |
|
16 |
0,26 |
0,6 |
1,5 |
|
|
|
|
|
|
|
|
|
4 |
0,24 |
0,53 |
1,55 |
|
17 |
0,27 |
0,45 |
1,5 |
|
|
|
|
|
|
|
|
|
|
|
|
|
24 |
|
|
|

5 |
0,26 |
0,56 |
1,45 |
18 |
0,2 |
0,55 |
1,4 |
|
|
|
|
|
|
|
|
6 |
0,23 |
0,45 |
1,66 |
19 |
0,28 |
0,5 |
1,5 |
|
|
|
|
|
|
|
|
7 |
0,2 |
0,58 |
1,5 |
20 |
0,26 |
0,4 |
1,55 |
|
|
|
|
|
|
|
|
8 |
0,29 |
0,6 |
1,45 |
21 |
0,25 |
0,55 |
1,6 |
|
|
|
|
|
|
|
|
9 |
0,25 |
0,5 |
1,5 |
22 |
0,23 |
0,5 |
1,4 |
|
|
|
|
|
|
|
|
10 |
0,29 |
0,45 |
1,6 |
23 |
0,22 |
0,58 |
1,6 |
|
|
|
|
|
|
|
|
11 |
0,21 |
0,48 |
1,55 |
24 |
0,28 |
0,49 |
1,5 |
|
|
|
|
|
|
|
|
12 |
0,24 |
0,52 |
1,45 |
25 |
0,26 |
0,55 |
1,55 |
|
|
|
|
|
|
|
|
13 |
0,21 |
0,55 |
1,4 |
26 |
0,25 |
0,5 |
1,5 |
|
|
|
|
|
|
|
|
2 Молотковые дробилки
Теоретическая часть
Для измельчения несоложеных материалов (рис, кукуруза, пшеница, овес, рожь и др.) без осахаривания оболочки используют молотковые дробилки (рисунок 1).
Принцип действия молотковой дробилки с подвешенными молотками заключается в многократном разрушении измельченного продукта ударами молотков с истиранием частиц. Штампованные сита сменные, их диаметр составляет 1…5 мм. Диапазон окружных скоростей рабочих органов (молотков), закрепленных на вращающемся роторе, составляет 40…200 м/с. Молотковые дробилки изготавливают с реверсивным вращением ротора для снижения затрат труда на замену сит и изношенных молотков, а также для увеличения коэффициента их использования.
Рисунок 1 – Схема молотковой дробилки
Расчет молотковой дробилки
Рассчитать производительность, дробилки и спроектировать с учетом дробилки с подвешенными молотками
основные размеры ротора вала молотковой
полученных |
результатов ротор молотковой |
длиной |
м, если минимальная окружная |
25
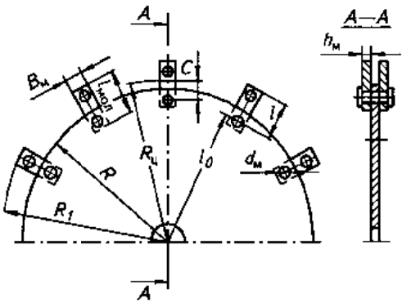
скорость молотков , а конструктивные размеры молотка прямоугольной формы следующие: длина Lмол=0,1 м, ширина Bмол, м и толщина hмол, м.
Рисунок 3 – Схема ротора молотковой дробилки
Расстояние от центра тяжести молотка до оси вращения, м:
⁄( |
(1) |
Квадрат радиуса инерции молотка относительно его центра тяжести, м2:
( |
⁄ |
(2) |
Квадрат радиуса инерции молотка относительно его оси подвеса, м2:
. |
(3) |
Расстояние от конца молотка до его оси подвеса, м:
. |
(4) |
Проверяем условие обеспечения безударной работы молотка:
|
|
|
(5) |
Если | |
| |
, то конструктивно изменяем расстояние от центра тяжести |
|
молотка до оси вращения C на величину |
м и расчет повторяем. |
||
Во избежание |
нарушения устойчивости |
работы молотковой дробилки |
конструктивно назначаем расстояние от оси подвеса молотка до оси ротора l0 так, чтобы оно было в 2 раза больше расстояния от конца молотка до оси его подвеса l, тогда l0=2l.
Радиус наиболее удаленной от оси ротора точки молотка, м:
26
(6)
Угловая скорость ротора, рад/с:
⁄ |
(7) |
Центробежная сила инерции молотка, Н:
|
|
|
|
|
|
|
(8) |
где |
– масса молотка, кг; |
|
|
|
|
|
|
|
– радиус окружности расположения центров тяжести молотков, м; |
|
|||||
|
|
|
|
|
. |
|
(9) |
где |
– плотность стали, из которой изготовлен молоток, кг/м3 ( |
⁄ . |
|||||
|
|
|
|
|
|
|
(10) |
|
Диаметр оси подвеса молотка, м: |
|
|
|
|
|
|
|
|
|
|
|
|
|
|
|
|
√( |
|
⁄[ ] |
(11) |
||
где [ |
] – допускаемое напряжение при изгибе, Па ([ ] |
|
|
|
|||
|
Толщина ротора, м: |
|
|
|
|
|
|
|
⁄( |
[ |
] . |
|
|
(12) |
|
где [ |
] – допускаемое напряжение при смятии, Па ([ |
] |
|
|
|||
|
Минимальный размер перемычки между отверстиями под осью подвеса и |
||||||
наружной кромкой диска, м: |
|
|
|
|
|
|
|
|
|
|
⁄( |
[ |
] ) |
|
(13) |
где [ |
] – допускаемое напряжение на срез, Па ([ |
] |
|
|
|
||
|
Наружный радиус диска, м: |
|
|
|
|
|
|
|
|
|
|
|
. |
|
(14) |
|
Производительность дробилки, кг/ч: |
|
|
|
|
|
|
|
|
27 |
|
|
|
|
|
(15)
где – коэффициент, учитывающий физико-химические свойства зерен, тип и размер ячеек ситовой поверхности ( );
–плотность массы зерна, кг/м3 ( = 1330 кг/м3);
–диаметр ротора, м (
–длина ротора, м.
Частота вращения ротора, с-1:
⁄( |
. |
(16) |
Необходимая мощность для привода молотковой дробилки, кВт:
⁄ .
где – коэффициент тонкости измельчения, равный отношению диаметра частиц до измельчения к диаметру частиц после измельчения (
Таблица 1 – Варианты индивидуальных заданий
Номер |
vмол, |
Lрот, м |
Вмол, м |
hмол, м |
Номер |
vмол, |
Lрот, м |
Вмол, м |
hмол, м |
|
варианта |
м/с |
варианта |
м/с |
|||||||
|
|
|
|
|
|
|||||
|
|
|
|
|
|
|
|
|
|
|
1 |
45 |
0,2 |
0,05 |
0,025 |
14 |
55 |
0,25 |
0,04 |
0,03 |
|
|
|
|
|
|
|
|
|
|
|
|
2 |
40 |
0,25 |
0,04 |
0,02 |
15 |
60 |
0,3 |
0,05 |
0,025 |
|
|
|
|
|
|
|
|
|
|
|
|
3 |
50 |
0,3 |
0,06 |
0,03 |
16 |
45 |
0,2 |
0,04 |
0,02 |
|
|
|
|
|
|
|
|
|
|
|
|
4 |
55 |
0,25 |
0,05 |
0,03 |
17 |
60 |
0,35 |
0,06 |
0,025 |
|
|
|
|
|
|
|
|
|
|
|
|
5 |
60 |
0,2 |
0,04 |
0,025 |
18 |
55 |
0,2 |
0,04 |
0,02 |
|
|
|
|
|
|
|
|
|
|
|
|
6 |
40 |
0,3 |
0,05 |
0,02 |
19 |
40 |
0,25 |
0,05 |
0,03 |
|
|
|
|
|
|
|
|
|
|
|
|
7 |
55 |
0,35 |
0,06 |
0,025 |
20 |
65 |
0,3 |
0,06 |
0,03 |
|
|
|
|
|
|
|
|
|
|
|
|
8 |
65 |
0,25 |
0,04 |
0,02 |
21 |
50 |
0,2 |
0,04 |
0,025 |
|
|
|
|
|
|
|
|
|
|
|
|
9 |
50 |
0,25 |
0,05 |
0,03 |
22 |
45 |
0,25 |
0,05 |
0,02 |
|
|
|
|
|
|
|
|
|
|
|
|
10 |
40 |
0,3 |
0,06 |
0,03 |
23 |
50 |
0,3 |
0,06 |
0,03 |
|
|
|
|
|
|
|
|
|
|
|
|
11 |
55 |
0,2 |
0,04 |
0,025 |
24 |
60 |
0,25 |
0,05 |
0,03 |
|
|
|
|
|
|
|
|
|
|
|
|
12 |
65 |
0,25 |
0,05 |
0,02 |
25 |
65 |
0,3 |
0,04 |
0,025 |
|
|
|
|
|
|
|
|
|
|
|
|
13 |
60 |
0,3 |
0,06 |
0,03 |
26 |
55 |
0,2 |
0,06 |
0,02 |
|
|
|
|
|
|
|
|
|
|
|
28
Практическая работа №5
Варочные агрегаты
Теоретическая часть
К основным аппаратам для приготовления пивного сусла относятся заторный котел, фильтрационный аппарат и сусловарочный котел. В зависимости от мощности предприятия варочные агрегаты выпускают двух-, четырех- и шестиаппаратными, в основном периодического действия, единовременной переработки зернопродуктов от 500 до 5000 кг. Двухаппаратный варочный агрегат состоит из одного аппарата для затирания и варки сусла и одного фильтрационного аппарата. Варочный агрегат с четырьмя аппаратами включает два заторных аппарата, один фильтрационный и один сусловарочный. Шестиаппаратный варочный агрегат состоит из двух заторных аппаратов, двух фильтрационных и двух сусловарочных.
Расчет варочного агрегата
Рассчитать и спроектировать варочный агрегат пивоваренного завода, если
избыточное давление греющего пара |
, удельная энтальпия греющего пара |
|||
, |
удельная энтальпия конденсата |
, удельная теплота |
||
парообразования |
, температура холодной воды |
, температура |
||
воды для затирания |
, температура воды для промывания дробины |
, |
расход воды для затирания и промывания дробины составляет соответственно по 400 л на каждые 100 кг солода. Способ варки сусла двухотварный. Количество единовременно
перерабатываемого солода |
при влажности |
и удельной теплоемкости |
|||||
сухих веществ солода |
|
( |
. Начальная концентрация сухих веществ в |
||||
сусле |
, конечная |
. |
Содержание воды в |
сусле |
%, |
||
коэффициент динамической вязкости воды |
|
|
; плотность заторной |
||||
массы |
|
. Отношение объема твердых частиц солода в заторной массе к |
|||||
общему |
объему суспензии |
⁄ |
. Внутренний |
диаметр аппарата |
. |
||
Диаметр |
окружности, |
описываемой лопастями мешалки, |
|
Ширина |
лопасти |
||
мешалки |
|
. Высота слоя заторной массы в аппарате |
. Частота |
||||
вращения мешалки |
. |
Тепловой КПД заторного и сусловарочного аппаратов |
Расход теплоты на нагревание воды для затирания, кДж:
( |
. |
(1) |
Удельная теплоемкость солода, кДж/(кг∙К):
( |
⁄ |
⁄ |
(2) |
29
Принимаем, что температура солода |
|
, тогда температура заторной |
массы, °С: |
|
|
( |
⁄( |
(3) |
Общее количество получаемой заторной массы, кг:
(4)
Удельная теплоемкость заторной массы, кДж/(кг∙°С):
( ⁄ (5)
Отбираем во второй заторный аппарат 40% общего количества заторной массы, кг:
|
(6) |
Расход теплоты на нагревание первой отварки от |
до кипения, кДж: |
( |
(7) |
Принимаем, что за время кипячения выпаривается в виде воды 2% общего количества заторной массы, и определяем количество теплоты для кипячения первой отварки, кДж:
|
|
(8) |
Принимая тепловой КПД заторного аппарата |
|
, вычисляем действительный |
расход теплоты на первую отварку, кДж: |
|
|
( |
⁄ |
(9) |
После кипячения первой отварки в заторном аппарате останется заторная масса, кг:
(10)
Количество заторной массы, которая осталась без нагревания в аппарате, кг:
(11)
Исходя из условия, что за время первой отварки температура заторной массы, находящейся в первом заторном аппарате, снизилась с до на 4 °С, после смешивания обеих частей заторной массы температура массы, °С:
( |
⁄( |
(12) |
|
30 |
|