
ПОДДУБСКИЙ / МЭРХО / Лекции по монтажу
.pdf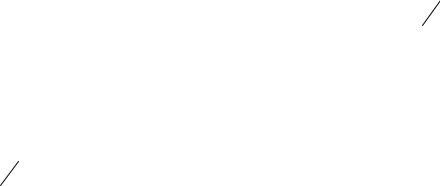
Определяется по термометру установленному на расстоянии200 – 300мм от запорного нагнетательного вентиля.
|
1.2.6. |
Технико-экономические |
показатели |
работы |
холодильно |
||
|
|
|
|
|
|
|
|
установки. |
|
|
|
|
|
|
|
|
6.1. |
Нормирование |
расхода |
электроэнергии, воды, хладагента, |
|
смазочных масел.
Эффективность работы холодильной установки устанавливают путем сравнения значений расходов электроэнергии, воды, хладагента, смазочного масла и для рассольных систем – соли.
Расход |
кВт |
|
электроэнергии определяют по показанию счетчиков |
час . |
|
Для точного |
определения расхода электроэнергии целесообразна установка |
счетчиков у наиболее энергоёмких электродвигателей. Нормативный расход электроэнергии нужно определять по графикам потребления электроэнергии из заводской документации (паспортов).
Расход свежей воды определяют по показаниям счетчика в начале и в конце отчетного периода и сопоставляют его с установленной нормо
потребления на 1 |
кВт |
выработанного холода. При отсутствии этого норма |
|
час |
|
можно определить абсолютный расход свежей воды за отчетный период. Например, в АХУ с ИН, зная паспортный унос охлажденной воды и время работы ИН, можно найти массу унесенной воды Gw .
5. Перегрев пара на всасывании
Определяется по термометру установленному на расстоянии200 – 600 мм от запорного вентеля и мановакуументу расположенному как можно ближе к испарителю.
для одноступенчатых КМ
DtBC = 5 -10o C - NH 3
DtBC = 20 - 40o C - хладон для нижней ступени
DtBC = 10 - 20o C - NH 3
Отклонения от оптимального режима. 1. Понижение температуры кипения.
Q0 = kFDt
kF – характеристика испарителя
tga = kF
Снижение температуры кипения может вызываться снижением коэф. теплопередачи, уменьшением F.
1. Уменьшение К вызывается:
1)образованием инея или льда на поверхности приборов охлаждения;
2)загрязнение маслом поверхности испарителя
3)уменьшение скорости движения воздуха в воздухоохладителях, или хладоносителей в испарителях;
2. Уменьшение активной поверхности испарителя:
1)уменьшение подачи хладагента в течении длительного времени (снижение уровня)
2)скопления в испарителе масла;
3)в открытых испарителях – скопление соли на дне;
4)заглушение части труб или панелей.
Несоответствие между производительностью компрессора и испарителя также приводит к снижению температуры кипения.
Работа с пониженной температурой кипения приводит к:
1.Уменьшению производительности компрессора на 4% на 1 градус
2.Увеличение удельного расхода электроэнергии на 2-3% на 1 градус
3.Повышению температуры нагнетания
4.К возможному подмораживанию охлажденных грузов.
5.К возможному замерзанию хладоносителя в И.Г.
6.К увеличению усушки продуктов.
В |
схемах |
с |
верхним |
расположением |
ОЖ |
из-за |
|||||
гидростатического |
столба |
жидкости |
требуется поддерживать |
давление |
|||||||
(температуру) всасывания ниже оптимальной по расчету. |
|
|
|||||||||
Давление всасывания может быть понижено по отношению к давлению |
|||||||||||
кипения из-за значительного сопротивления всасывающего трубопровода. |
|
||||||||||
2. Повышенная температура конденсации. |
|
|
|||||||||
|
|
w ) |
|
|
|
|
|
||||
Q0 = kF(tК - t |
|
|
|
|
|
||||||
tgb = kF = |
QK |
|
|
|
|
|
|||||
|
|
|
|
|
|
|
|
|
|
||
|
|
tK - t |
W |
|
|
|
|
|
|||
Температура |
|
конденсации |
является |
|
|||||||
самоустановливающимся. |
|
|
|
|
Повышение температуры конденсации вызывается: 1. Уменьшение коэффициента теплопередачи:
1)загрязнение поверхности труб;
2)замасливание
3)из-за наличия неконденсирующихся примесей(образование газовой пленки)
2.Снижение эффективной теплообменной поверхности
1)из-за подтопления КД жидким хладогентом(например из-за недостаточной емкости лин. ресивера)
2)из-за нарушения распределительных устройств(форсунок) испарительных конденсаторов;
3)Из-за закупорки (заглушки) теплообменных труб;
3.увеличения температуры охлаждающей среды;
1)из – за уменьшения расхода охлаждающей среды;
2)из-за несоответствия между производительностью КМ и КД.
4.Из-за роста давления в конденсаторе (из-за воздуха)
5.Из-за значительного сопротивления нагнетательных трубопроводов.
Повышение температуры конденсации 1на градус приводит к увеличению удельного расхода электроэнергии на2-2,5% и уменьшению холодопроизводительности на 1 – 2%.
3. Повышенная температура конца сжатия. Может быть вызвана:
1.Повышенным перегревом пара на всасывании а) недостаточная подача хладагента в И.С.
б) большая протяженность всасывающего трубопровода; в) снижение эффективности теплоизоляции
2.чрезмерно низкая температура кипения или чрезмерно высокая температура конденсации;
3.Наличие в системе неконденсирующихся газов.
4.значительные потери давления на всасывании.
5.Неисправности в самом компрессоре.
а) износ цилиндров; б) неплотности нагнетательных и всасывающих клапанов;
в) недостаточная подача охл. воды в рубашку компрессора, либо её высокая температура.
г) отлажение водяного камня; д) нарушение системы смазки
Для винтовых компрессоров температура конца сжатия определяется расходом и температурой смазочного масла.
4. Влажный ход компрессора (низкий перегрев).
Наиболее опасный режим для поршневого КМ, т.к. это может привести к гидроудару, что может повлеч разрушение клапанов, цилиндров из-за механических и тепловых ударов; замерзанию воды в блоке цилиндров; к повышенному износу цилиндров из-за ухудшения условий смазки.
Признаки влажного хода:
1.Уменьшение перегрева пара;
2.Резкое снижение темпереатуры нагнетания;
3.Обмерзание блока цилиндров компрессора
4.Изменение звука работы клапанов.
Причины влажного хода:
1. Переполнение испарителя хладогентом;
2. Резкое повышение тепловой нагрузки;
3. Быстрое снижение давления кипения
4. Образование зон скопления жидкого хладагента.
Если в цилиндры попала жидкость(глухой стук |
клапанов), то |
|
необходимо выключить компрессор, в другом случае необходимо закрыть |
||
вентели нагнетания и всасывания КМ |
|
|
1.2.4 Техническое обслуживание холодильного оборудования. |
|
|
1. Обслуживание и основные неполадки в работе КМ. |
|
|
Обслуживание заключается в постоянном надзоре |
за состояние |
|
компрессоров. |
|
|
При эксплуатации поршневых ,КМмогут встречаться следующие |
||
неисправности: |
|
|
1. Повышенный нагрев трушихся деталей( подшипников, |
цилиндра, |
|
сальника). В общем случае допускается нагрев 50до – |
60 |
градусов. |
Температуру можно определить рукой или косвенно (по температуре масла в картере или температуре нагнетания). Многие современные компрессора имеют автоматическую защиту от повышенного нагрева.
Причинами повышенного нагрева являются:
1) Недостаточная подача масла к точкам смазки: а) засорение маслопроводов; б) неисправности маслонасоса; в) засорение фильтров; г) недостаток масла в картере;
д) негерметичность масляной системы; Недостаточную подачу масла определяют по падению давлени.
Давление масла должно быть не менее 0,2 – 0,4 МПа.
2)Использование масла несоответствующей вязкости или загрязненного.
3)неправильная сборка сопрягаемых деталей.
2. Появление посторонних стуков в сопрягаемых деталях:
1)Увеличение зазоров между сопрягаемыми трущимися деталями
2)Неисправности клапанной группы (поломка клапанов)
3)Поломка поршневых колец;
4)Потеря упругости буферной пружины;
5)Малая величина линейного мертвого пространства
6)Влажный ход компрессора;
7)Попадание в цилиндр посторонних деталей, воды повышенного количества масла.
3. Повышенный унос масла:
1)износ поршневых и маслосъемных колец;
2)переполнение картера маслом;
3)засорение отверстий поршня под маслосъемным кольцом
4)Повышенная температура конца сжатия;
5)высокая разность давлений в картере и сальнике.
Обслуживание винтовых компрессоров.
1. Особенности пуска винтовых компрессоров Перед пуском КМ необходимо проверить температуру масла. Если
температура |
масла ниже15 o С , |
то его необходимо |
подогреть. При |
|
температуре масла выше 45 o С , его необходимо охладить. |
|
|
||
Пуск |
ВКМ осушествляется с открытием нагнетательного вентеля, |
|||
регулятор |
производительности |
устанавливается |
в |
положение«min». |
Всасывающий вентиль открывается после снижения давления в полости всасывания ВКМ, до величины указанной заводом изготовителем.
Обслуживание |
ВКМ |
осуществляется |
в |
наблюдении |
за , |
КИП |
||
контролем |
температуры |
и |
давления |
. маслаСвоевременной |
замене |
|||
маслофильтров, очистке маслоохладителя. Температура масла должна быть |
||||||||
25 - 45 o С , давление масла на входе в ВКМ должно быть на0,3 – 0,5 МПа |
|
превышать давление нагнетания ВКМ.
Режим влажного хода менее опасен. Однако при большом количестве
жидкого |
хладагента |
возможно |
заклинивание |
ротора |
и |
разруш |
подшипников. |
|
|
|
|
|
Обслуживание ротоционных КМ.
Основное внимание при эксплуатации необходимо уделять рабочим пластинам, изготовленным из текстолита, т.к. они поглощают аммиак и воду и, увеличиваются в размерах, что приводит к заклиниванию в пазах ротора и могут сломаться.
Чтобы избежать заклинивания необходимо при непродолжительной остановке поддерживать низкое давление(0,1 МПа) в цилиндре КМ, для этого необходимо производить пуск компрессора на1 – 2 часа один раз в сутки.
При длительном |
останове пластины |
необходимо |
извлечь из |
КМ |
|||
хранить в герметичной упаковке в сухом виде. |
|
|
|
||||
Влажный |
ход |
не |
приводит |
к |
аварийной |
,ситуацииоднако |
под |
воздействием жидкого аммиака пластины становятся хрупкими и могут разрушиться.
Особенности эксплуатации центробежных КМ.
Особенностью турбокомпрессоров является жесткая зависимост объемной производительности от развиваемого напора. При увеличении температуры конденсации ТК должны обеспечивать больший напор, однако при достижении определенного значения напора ТК переходят в помпажный
режим. При помпажном режиме происходит срыв потока газа в рабочем колесе, что может привести к аварии КМ.
При эксплуатации необходимо так регулировать производительность, чтобы не допустить помпаж.
Для защиты от помпажа устанавливают дросслелирующий вентиль, байпасный вентиль для перепуска пара с нагнетания на всасывание.
Пуск ТК осуществляется в следующей последовательности:
1) Для разгрузки электродвигателя в |
период пуска предварительно |
снижают давление в испарителе и во |
всасывающем трубопроводе, при |
помощи вспомогательного компрессора. |
|
2)в ТК работающих на пропане перед пуском продувают пусковой контур парами хладагента и отводят их в линию факельных сбросов.
3)Подготавливают масляную систему:
а) удаляют воздух; б) подают воду на маслоохладители;
в) проверяют исправность аварийного маслонасоса; г) рапускают рабочий маслонасос;
д) при помощи регулирующих вентилей регулируют давление масла
перед подачей в точки смазки. |
|
|
|
|
|
|
|
||
4) |
Включают и настраивают регулятор поддержания |
постоянного |
|||||||
давления на стороне всасывания. |
|
|
|
|
|
|
|||
5) включают антипомпажный регулятор; |
|
|
|
|
|||||
6) |
|
Включают электродвигатель |
и |
при отсутствии |
перегрузок |
||||
помпажного режима, ТК переводят с пускового контура на рабочий. |
|
|
|||||||
При |
обслуживании |
ТК |
особое |
внимание |
уделяют |
темпера |
|||
подшипников и давлению масла. |
|
|
|
|
|
|
Обслуживание теплообменного оборудования.
Основная задача обслуживания ТО заключается в обеспече высокоэффективного теплообмена при обеспечении эксплуатации АХУ. С этой целью контролируют:
1)температуру охл. сред на входе и на выходе
2)уровень жидкого хладагента в испарителях затопленного типа
3)уровень хладоносителя в открытых испарителях;
4)герметичность аппаратов
Показатели работы ( Dt ) регистрируются через каждые 2 часа. Контроль за уровнем жидкого хладагента осуществляется непрерывно(визуально или посредством приборов) Температура сред определяется термометрами ТП или ТС.
Обслуживание конденсаторов.
Основной причиной снижения интенсивности теплообмена является снижение коэффициента теплопередачи из-за загрязнений. Со стороны хладагента дополнительное сопротивление создает масло, со стороны охл. среды (воды) – накипь, водяной камень.
Для очистки конденсаторов используют следующие методы:
1.механический с помощью щеток
2.химический
3.пескоструйный
4.гидропневматический
5.тепловой (для испарительных КД)
При механическом способе через теплообменные трубы прогоняют
специальные щетки, приводимые в движение с помощью гибкого вала. |
|
||||||||
Химический |
способ |
очистки |
широко |
распространен |
и |
включ |
|||
следующие |
|
операции: |
кислотную |
обработку, |
нейтрализацию |
и |
|||
пассивирование (Рис. ) |
|
|
|
|
|
|
|
||
В баке 1 готовят 10% раствор ингибированной соляной кислоты. Из бака |
|
||||||||
1 насосом 2 раствор подается в конденсатор и затем сливается в бак. Когда |
|
||||||||
концентрация |
кислоты |
прекращает |
снижаться, циркуляцию |
|
раствора |
||||
прекращают. |
|
|
|
|
|
|
|
|
|
Затем КД промывают водой и содовым раствором. |
|
|
|
|
|||||
В |
оборотных |
системах |
водоснабжения |
применяют |
с |
||||
водоподготовки : |
|
|
|
|
|
|
|
|
|
а) магнитную |
|
|
|
|
|
|
|
|
|
б) химическую |
|
|
|
|
|
|
|
||
Магнитная обработка воды теряет способность к накипеобразованию. |
|||||||||
Добавление |
химических |
реактивов |
в . водуохл |
также |
препятствует |
||||
накипеобразованию. |
|
|
|
|
|
|
|
||
Один раз в месяц берут пробы охл. воды (в КД) и рассола (в И) для |
|
||||||||
определения возможных утечек аммиака. Проверку проводят с помощью |
|||||||||
реактива Несслера. |
|
|
|
|
|
|
|
||
Обслуживание испарителей заключается |
в |
периодической оттайке |
|||||||
снеговой шубы и удалении шлака, а также в контроле работы вентиляторов, |
|
||||||||
мешалок, рассольных насосов. |
|
|
|
|
|
|
|||
В испарителях для охлаждения жидких хладоносителей: контролируют |
|
||||||||
температуру на входе и выходе из испарителя, контролируют концентрацию |
|
||||||||
рассола по плотности и температуре. Температура начала замерзания должна |
|
||||||||
быть на 5 |
o С |
ниже t0 |
для открытых |
и на |
8 o С |
ниже для |
закрытых |
испарителей.
В испарителе типа ИТГ для охлаждения воды температура кипения не должна быть ниже2 o С . Из маслосборников испарителей2-3 раза в месяц проводят выпуск масла.
Рис. – Схема химической очистки концентратора.
Обслуживание вспомогательного оборудования. 1. Ресиверы При эксплуатации ресиверов контролируется:
а) давление в аппарате б) постоянно уровень жидкого хладагента
в) герметичность ресиверов
г) состояние предохранительных клапанов д) работоспособность приборов КИПиА.
Периодически проводится удаление масла и тех освидетельствование сосудов.
2. Насосы В сальниковых центробежных насосах контролируется:
1) давление нагнетания снижение давления может произойти из-за износа рабочего колеса,
разрушения лопастей рабочего колеса, из-за подсоса воздуха через сальник или неплотности всасывающего трубопровода(при этом стрелка манометра резко колеблется)
2) температуру подшипников, t не более 60 – 70 o С , через 1000 ч производится осмотр
3)состояние и затяжку набивки сальников
4)расход электроэнергии
3. Теплоизоляционные конструкции (ТИК)
В процессе эксплуатации ТИК необходимо недопускать течи в кровлях с целью недопущения увлажнения теплоизоляции. Внутренние повреждения увлажнения необходимо моментально устранять. Нельзя допускать длительного повышения температуры в помещениях в зимнее время, т.к. это может привести к увлажнению ТИК.
Периодически необходимо теплоизоляции и влажность ТИК путем отбора проб.
С целью обеспечения бережной эксплуатации необходимо периодически производить проверку знаний персонала, проверять неисправность ПК и приборов защитной автоматики АХУ, проводить ТО аппаратов и сосудов.
Периодичность проверки знаний:
Вводный инструктаж – при поступлении на работу Первичный инструктаж на рабочем месте– перед допуском к работе
АХУ (для машинистов ч/з 1 место обучение)
Повторный инструктаж на рабочем месте – один раз в три месяца Внеплановый инструктаж на рабочем месте – по мере необходимости Обучение на предприятии – один раз в год Проверка знаний персоналом – 1 раз в год
Инструкции по БЭ АХУ и оказанию доврачебной помощи
Периодичность проверки исправности ПК, ПРУ, КИПиА. Проверка ПРУ – 1 раз в 10 дней; Проверка автоматических приборов – 1 раз в месяц;
Проверка ПК на аппаратах – 1 раз в 6 месяцев. Проверка ПК компрессоров – 1 раз в год
Проверка манометров на предприятии – 1раз в 6 месяцев
Проверка манометров с апломбированием – 1 раз в год Проверка противогазов – 1 раз в 6 месяцев.
Периодичность проведения ТО сосудов.
Внутренний осмотр – 1 раз в 2 года Пневматическое испытание сосудов недоступных для осмотра – 1 раз в 2
года
Пневматическое испытание сосудов доступных для осмотра– 1 раз в 8
лет. |
|
|
|
|
|
|
|
1.2.5 Выполнение |
вспомогательных |
операций |
при |
обслуживании |
|
|
|
|
|
|
|
|
холодильной установки |
|
|
|
|
|
|
|
1.2.5.1 Оттайка приборов охлаждения. |
|
|
|
|
|
|
Оттайку приборов |
непосредственного |
охлаждения |
производят для |
||
удаления снеговой шубы и удаления масла |
|
|
|
|
Пополнение системы хладагентом.
Первоначальное заполнение и дозаправку АХУ аммиаком производят через регулирующую станцию.
Рис. – Схема слива аммиака из цистерны |
|
|
|||
После прибытия цистерны начальник контрольного цеха |
проверяет |
||||
наличие |
пломб, состояние |
внешнего |
кожуха |
цистерны, наличие |
ПК, |
отсутствие утечек аммиака. |
|
|
|
|
|
При |
обнаружении |
неисправностей |
или |
несоответствию |
стандарт |
окраски слив аммиака запрещается. В этом случае составляется акт. |
|
||||
Цистерну закрепляют на рельсах башмаками и ограждают переносными |
|||||
сигналами. От представителя ж/б цистерну принимает начальник к..ц, |
затем |
он отмечает номер и состояние цистерны в книге для регистрации слива и делает заключение о возможности слива.
При первичном заполнении слив аммиака производится в аппараты и сосуды, в которых предварительно создается вакуум. При пополнении сисмемы хладагент сливают в часть испарительной системы1Ив которой предварительно снижается давление путем отсоса паров компрессором. После снижения давления в И1 открываются вентили 8,1,9,6. Под действием разности давлений аммиак из цистерны поступает в испарительную систему И1. После выравнивания давлений в И1 и цистерне поступление аммиака в И1 прекращается и жидкостной трубопровод ЖТ оттаивает. Дальнейший слив проводят в испарительную систему2, Ив которой предварительно снижают давление. Для этого закрывают вентиль6 и открывают вентиль 7.
Во время слива вентиль5 и 4 закрыты. Переключение цистерн на части ИС производят до полного освобождения цистерн от аммиака. Окончание слива определяют по падению давления в цистерне и оттаиванию жидкостного трубопровода.
При заполнении системы аммиаком из баллонов заправку производят через заправной коллектор .ЗКБаланы присоединяют к ЗК стальными трубками испытанными под давлением2 МПа. Предварительно взвешенные баллоны установливают на подшовку вентелем вниз. Опаражненные баллоны определяют по падению давления и оттаиванию нижней части баллонов.
Пополнение системы хладоносителем.
В |
системах с промежуточным хладоносителем широко применяют |
водные |
растворы солей, иногда используют этилен– гликоль, водно – |
спиртовой раствор глицерина.
Наиболее широко применяется раствор CaCl2 .
Раствор получают в баке для разведения рассола. В баке устанавливают сетку, на сетку насыпают фильтрующий слой кокса; - на него слой соли. С помощью насоса вода прокачивается через слой соли растворяя. Поеё достижении требуемой концентрации раствор закачивают в систему.
Удаление смазочного масла.
Количество масло уносимого в систему зависти от режима работы компрессора и его технического состояния. Наиболее совершенные маслоотделители отделяют до90% масла уносимого из компрессора. При постоянной работе системы масло из маслоотделителей необходимо удалять через 5 дней. Масло из МО и из аппаратов необходимо удалять только ч/з маслосборники.
Рис. – Схема включения маслосборника. Для удаления масла необходимо:
1.Понизить давление в маслосборнике
2.Открыть вентили слива масла из аппаратов и на МС
3.Перепустить масло
4.Отсосать аммиак из МС
5.Удалить масло из МС.
Дозаправка системы маслом
В АХУ применяется масло марок ХА-30; ХА-34;ХА-23. В связи уноса масла из КМ необходимо периодически производить дозаправку КМ маслом.
Нормальная работа смазочной системы характеризуется: |
|
||||||
1. |
Уровень масла в картере ПК в |
пределах1/3 – |
2/3 от диаметра |
||||
смотрового стекла. |
|
|
|
|
|
|
|
2. |
Разность |
давлений |
в |
масляной |
системе |
создаваемая |
насос |
соответствует исходной. |
в |
картере |
ПКМ не |
превышает50 С |
при |
||
3. |
Температура масла |
||||||
|
|
|
|
|
|
o |
|
температуре окр. среды не выше 30 o С .
4. Нагрев сальника должен быть меньше 60 o С