
Волынский ТКМиП
.pdf203
10.7. Характеристики станков для обработки кускового шпона
Параметр |
Для вырубки шипов |
Для сращивания |
||
Производительность, м3 / час |
2,5 |
2,5 |
||
Скорость подачи, м / мин |
1040 |
1020 |
||
Давление воздуха, МПа |
0,6 |
|
- |
|
Давление склеивания, МПа |
- |
0,2 |
- |
0,5 |
Число резов ножниц в минуту |
- |
10 |
- |
60 |
Установленная мощность, кВт |
1,1 |
0,6 |
||
Габаритные размеры, м |
0,96 х 1,35 х 1,15 |
2,3 х 1,0 х 1,2 |
||
Масса, кг |
750 |
1600 |
Исследования и опыт предприятий показали, что обрезки шпона и фанеры мо- гут быть эффективно использованы для изготовления заполнителя комбиниро- ванных материалов - реечных, ячеисто-решетчатых и ячеисто-сотовых строи- тельных и мебельных щитов, а также ребровой фанеры.
Обрезки фанеры раскраивают на полосы необходимой длины и ширины на круглопильном станке и сортируют. Заполнитель для одного щита должен быть одной толщины и одной породы древесины, допускаются стыки по длине, но с расстоянием между стыками в соседних заготовках не менее 150 мм. Комплект заполнителя собирается на рабочем столе в реечную или решетчатую конструк- цию и подается на сборку пакета, включающего в себя рамку, заполнитель и об- лицовки. Рейки заполнителя располагаются поперек направления волокон на- ружных слоев.
10.3.2. Переработка отходов в дробленку и технологическую щепу
Дробленка представляет собой материал, полученный в дробилках и предна- значенный на топливо. К этому материалу не предъявляется каких - либо требо- ваний по размеру и качеству частиц. В дробилки направляются обычно шпон- рванина от неокоренных чураков, обрезки шпона и фанеры и другие отходы, пе- реработка которых на другую продукцию нерентабельна. В настоящее время около половины всех кусковых отходов в отрасли направляется на топливо, хо- тя такое положение нельзя считать нормальным.
Схема переработки включает в себя транспортные средства подачи отходов, дробилки и бункера-накопители. Для измельчения обрезков шпона и фанеры применяют дробилки марок ДШ-3, ДР-5, МРБ-1, "Варкаускас" и др. В последнее время получили распространение измельчающие фрезы в комплекте с пилами, например на форматно - обрезном станке.
Повышение эффективности производства требует увеличенного производства технологической щепы, которая отличается от дробленки более высокими тре- бованиями к размерам частиц и наличию посторонних включений. Чтобы обес- печить измельчение в щепу шпона - рванины, обрезков шпона и фанеры, в тех-
нологический процесс необходимо включить операции обнаружения и удаления металлических включений, сортировки щепы с удалением крупной фракции, мелочи и пыли. Желательно предусмотреть и доизмельчение крупной фракции, особенно при больших масштабах производства.
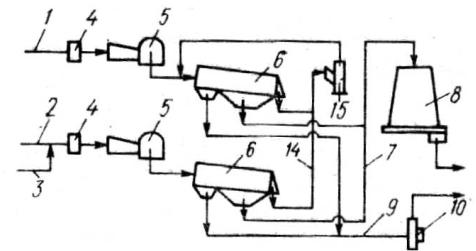
204
Оптимальной следует считать такую технологическую схему, при которой имеются два потока отходов - отдельно для влажных (шпон - рванина и обрезки сырого шпона) и сухих (обрезки сухого шпона и фанеры). Полученная щепа по- сле сортировки и доизмельчения крупной фракции направляется в общий бун- кер, где она усредняется по своим свойствам (фракционному составу и влажно- сти), соответствующим стандарту на щепу марки ПС (рис.10.7).
В данной схеме головным оборудованием являются барабанные рубительные машины марок ДШ-1М, ДШ-2, ДРС-1М, ДШ-3А, ДУ-2А, МРБ-10, ДШ-4. Их ос- новное отличие от барабанных дробилок заключается в том, что гравитационный способ подачи изменен на принудительный. При синхронизации скоростей по- дачи и резания достигается получение более точных размеров щепы. Наиболее совершенной по конструкции является машина ДШ-4 (табл.10.8).
Рис.10.7. Схема переработки кусковых отходов в щепу : 1, 2, 3- конвейеры для отхо- дов, 4 - металлоискатели. 5 - рубительные машины, 6 - сортирова для щепы, 7 - кон- вейер для кондиционной щепы, 8 - бункер для кондиционной щепы, 9 - конвейер для дробленки и отсева щепы, 10 -пневмоустановка, 14 - конвейер для крупной фракции, 15 - дезинтегратор.
В качестве металлоискателя используют устройство марки ЭМИ-64П, работа которого основана на изменении амплитуды генерируемых колебаний при по- падании металла в поле датчика. Датчик состоит из двух катушек в плоском не- металлическом корпусе. Минимальная масса регистрируемых датчиком предме- тов из черных и цветных металлов, проходящих в зоне его действия на расстоя- нии 300 мм от рабочей поверхности, составляет 0,2 кг. Металлоискатель входит в комплект поставки станка ДШ-4 (табл.10.8).
Наилучшими марками сортировок для щепы, получаемой из шпона являются барабанные одно - и двухситовые СБЩ-1, СБЩ-2, СБЩ-3, в которых для круп- ной фракции размеры ячеек составляют 35 х 35 мм, а для мелкой - 6 х 6 мм. Сортировки не имеют качающихся масс и не требуют мощного фундамента, в них достигается самоочищение сит.
205
10.8. Характеристика барабанной рубительной машины ДШ-4:
Производительность, пл.м3 / ч |
до 30 |
Диаметр ножевого барабана, мм |
1200 |
Число ножей / контрножей |
18 / 2 |
Частота вращения барабана, мин-1 |
500 |
Ширина загрузочного отверстия, мм |
1070 |
Высота загрузочного отверстия, мм |
365 |
Скорость подачи, м/мин |
90 |
Установленная мощность, кВт |
125 |
Размеры (L x B x H), м |
4,45 х 3,1 х 1,65 |
Масса, кг |
14 900 |
Доизмельчение крупной фракции проводят в дезинтеграторах марки ДЗН-02 или фирмы “Raute” (IH-1, IH-II). Последние могут измельчать также другие кус- ковые отходы (оторцовки, обрезки фанеры, шпона).
10.3.3.Переработка кусковых отходов в технологическую и упаковочную стружку и частицы для пресс-масс
Известны технические решения по переработке шпона - рванины в техноло- гическую стружку непосредственно у лущильного станка с помощью специаль- ных измельчителей, пристраиваемых к станку. Специальная ножевая головка вместо обычной оцилиндровки срезает с чурака стружку, которая сбрасывается в воронку и затем, с помощью конвейера, проходящего вдоль фронта лущильных станков, попадает в бункер - накопитель. Аналогично поступают и при обрезке фанеры с помощью пильно - фрезерных головок. Однако качество стружки при этом часто не соответствует требованиям плитного производства.
Более эффективным может оказаться переработка шпона - рванины и обрез- ков сырого шпона в упаковочную стружку. При этом следует из общей массы отходов отбирать материал, не содержащий коры, формировать из него пачки и обрезать их по формату, соответствующему размерам магазина древошерстного станка. Строгают пакеты на серийно выпускаемом станке СД-4А или подобном. По договоренности с потребителем можно поставлять стружку большей влажно- сти, чем по стандарту. В этом случае стружка не сушится, а только выдержива- ется определенное время в производственном помещении. Размеры упаковочной стружки: по длине 300-450 мм, по ширине 1,5-5,0 мм, по толщине 0,2-0,5 мм.
Отходы в виде обрезков сухого шпона являются ценным сырьем для получе- ния древесных частиц, применяемых в производстве пресс-масс МДПК (пресс- крошка). Технологический процесс включает в себя подготовку отходов к пере- работке, их измельчение и сортировку, создание промежуточного запаса и дози- рованную выдачу частиц в производство. Размеры древесных частиц согласно ГОСТ 11368 - 79 указаны в табл.10.9.
Для измельчения применяют молотковые дробилки, наиболее распространена дробилка КДУ-М. Как и при других способах измельчения, точные размеры час- тиц в дробилке не достигаются, поэтому обязательна последующая сортировка в эксцентриковых грохотах. Хранение запасов - в серийных бункерах типа ДБО.
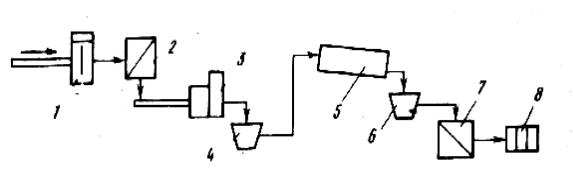
206
10.9. Размеры древесных частиц для пресс-крошки
Марка продукции |
Длина мм |
Ширина, мм |
Толщина, мм |
МДПК-Б |
80 |
5 |
1,8 |
МДПК-Б1 |
50 |
8 |
1,8 |
МДПК-Б2 и МДПК-Б4 |
80 |
10 |
0,6 |
МДПК-Б5 |
50 |
5 |
1,8 |
.
10.3.4. Переработка кусковых отходов в товары хозяйственного и культурно - бытового назначения
Из кусковых отходов фанерного производства предприятиями отрасли изго- товляется свыше 60 наименований различной продукции:
-разделочные доски для пищевых продуктов;
-заготовки для настенных (навесных) вешалок;
-комплекты заготовок для посылочных ящиков;
-планки для детских санок;
-подрозетники;
-пучинные карточки для железных дорог;
-ярлыки для маркировки грузов;
-вкладыши и планки для намотки рулонных материалов и пр.
Во всех случаях основная операция заключается в отборе отходов, которые удовлетворяют размерам и качественным показателям на продукцию, особенно в части допуска сучков, грибных окрасок, ложного ядра и т.п. Основным видом
оборудования здесь является круглопильный станок для смешанной распиловки типа Ц-6. Могут потребоваться сверлильный станок типа СВП, шлифовальный ШЛПС, фрезерный ФЛ. Широко применяются собственные разработки пред- приятий и ручной электрифицированный инструмент.
Из обрезков шпона наиболее массовой продукцией являются палочки для мо- роженого, медицинские шпатели и различные заготовки из шпона. Технологиче- ский процесс при этом предусматривает отбор кусков, вырубание полос шпона заданной ширины, рубку палочек из полос, сушку и шлифование палочек, их сортировку и упаковку. Соответствующая схема показана на рис.10.8.
Рис.10.8. Схема изготовления палочек для мороженого и шпателей: 1 - гильотинные ножницы, 2 - подстопное место, 3 - делительный станок или штамп, 4, 6 - лоток или контейнер, 5 - сушильно - шлифовальный аппарат, 7 - сортировочный стол, 8 - упа- ковочная машина.
207
Сушильно-шлифовальный аппарат представляет собой вращающийся бара- бан, обтянутый шлифовальной лентой и сеткой и снабженный системой цирку- ляции подогретого воздуха. При использовании сухого шпона процесс идет без сушки. Сортировка и упаковка проводится вручную или с использованием спе- циальной машины модели 19 итальянской фирмы “Лаффи”. Объем производства палочек для мороженого в системе бывшего Главфанспичпрома в 1987 году со- ставил около 2 млрд. штук.
В целом же нужно отметить, что объем использования кусковых отходов зна- чительно меньше, чем крупномерных. Примерно 60% из них расходуется на то- пливо, поэтому здесь имеются еще огромные резервы для получения предпри- ятиями дополнительной прибыли.
10.4. Переработка мягких отходов
10.4.1. Переработка отходов для производства древесных плит
Наибольший интерес для производства плит представляют опилки, образую- щиеся при разделке фанерного сырья и форматной обрезке фанеры. Исследова- ния показали, что опилки можно применять во внутреннем слое древесностру- жечных плит в объеме до 50% без потери прочности и снижения других показа- телей ДСтП. Для этого необходимо наладить сбор опилок, обеспечить удаление металлических включений с помощью железоотделителей, сортировку в СЩ-1М или рассевах типа ДРС-1М с целью удаления крупных частиц (сколов) и пыли.
Впроизводстве пятислойных плит можно использовать такое соотношение объемов: 1/3 - cредний слой из опилок или станочной стружки, 1/3 - промежу- точный слой из специальной стружки и 1/3 - наружные слои из тонкой стружки, микростружки и древесной пыли.
Взарубежной практике широкое распространение получила технология пе- реработки опилок, станочной стружки и отсева щепы в волокно для наружных слоев плит путем размола на рафинерах, дефибрерах. Однако распространение этого опыта сдерживается большой энергоемкостью процесса размола. Лучшие результаты достигаются при переработке этих отходов на дробилках и мельни- цах, вырабатывающих специальную тонкую стружку или микростружку. При
переработке опилок на молотковой дробилке или шаровой мельнице частицы уменьшаются по толщине и ширине в 2-3 раза по сравнению с опилками, но имеют исходную длину.
Представляют товарную ценность и такие отходы, как мельчайшие частицы и древесная пыль. Если такие частицы не содержат коры в виде включений разме- ром более 1 мм, то для наружных слоев они не менее эффективны, чем специ- ально изготовленная микростружка или волокно. Технология переработки опи- лок, станочной стружки и пыли требует применения специального оборудования
-закрытой пневмосистемы для сбора отходов, специальных циклонов для отде- ления пыли в две стадии, малых бункеров для хранения частиц и пыли. При па- раллельном изготовлении фанерной продукции и древесностружечных плит та- кая утилизация может оказаться вполне рентабельной.
208
10.4.2. Использование отходов для гидролиза, пресс-масс и прессизделий
Сырьем, пригодным для гидролизного производства (спиртовой, дрожжевой и фурфурольный профили), являются опилки, получаемые при разделке древесно- го сырья. Опилки не должны содержать более 8% коры, 5% гнили и 0,5% мине- ральных включений. Сортировка опилок должна осуществляться с использова- нием верхнего сита с отверстиями 30-35 мм и нижнего - не более 3-6 мм. Очень важен породный состав опилок. Для дрожжевого производства породный состав опилок не регламентируется, для фурфурольного пригодны только опилки ли- ственных пород, а для спиртового - допустима смесь хвойных (не менее 70%) и лиственных пород. В производстве пищевого ксилита опилки должны быть только из березовой древесины или с примесью осины до 10% .
Более широко опилки и станочная стружка используются для выработки пресс масс и пресс-изделий. В соответствии с ГОСТ 11368 - 79 из опилок лиственных и хвойных пород и их смеси, имеющих размеры по длине не более 4,5 мм и по толщине не более 1,8 мм могут быть получены пресс массы марок МДПО-Б и МДПО-В. Из станочной стружки и из ее смеси с опилками, имеющие длину не более 15 мм, ширину не более 5 мм и толщину не более 12 мм, получают пресс- массу МДПС-М. Первые две марки пресс-масс пригодны для производства раз- личных конструкционных деталей в машиностроении, а также сидений стульев, рукояток инструментов, погонажных изделий. Пресс-масса МДПС-М нашла применение в производстве подоконных досок (с облицовкой пленками), от- дельных деталей мебели и игрушек.
Технологический процесс близок к производству ДСтП, особенно в части подготовки осмоленной стружки. Производство пресс-массы МДПО-В освоено, например, на Уфимском ДФК. Особенностью производства является автомати-
ческое дозирование всех компонентов и организация прессового отделения для изготовления готовых изделий - втулок, вкладышей, шкивов, роликов и т.п.
Производство из опилок пьезотермопластика освоено на Костромском ФК. Здесь нет участка клееприготовления, но имеется участок автоклавов для обра- ботки опилок паром при температуре 170 - 180 0С и давлении 1 МПа. Через 2 ча- са обработки массу при влажности 100 - 130% направляют через циклон в при- емник. Полученные при такой обработке опилки имеют коротковолокнистую структуру. Содержание лигнина и целлюлозы количественно не изменяется, а содержание пентозанов падает в 5-7 раз. Частицы несколько уменьшаются в размерах и приобретают темно-коричневый цвет. Затем масса сушится в бара- банных сушилках, проходит отделение крупных частиц в сите - бурате, смеши- вается в смесителе с водой и олеиновой кислотой и формуется в пресс-формах в брикеты, которые в горячем прессе прессуются до окончательной толщины при давлении 150 МПа и температуре 160 0С. Полученные плитки охлаждают и вы- держивают не менее суток, затем шлифуют, снимают облой и фаски. Плитки ис- пользуют для покрытий пола и других целей, их цвет может регулироваться до- бавкой цветного порошка в пресс - формы. Форма плиток может быть квадрат- ной, прямоугольной или шестигранной.
На Киевском ДОКе освоено производство тырсолита и паркелита. Смесь опилок и станочной стружки (для паркелита) и древесной пыли (для тырсолита)
209
отделяется от крупных частиц, сушится до влажности 4-10 %, смешивается со связующим и прессуется. Тырсолит получают между плитами пресса в виде листов толщиной до 8 мм, а паркелит - в пресс-формах в виде плиток 300 х 300 мм, толщиной 18 мм. Свойства описанных материалов указаны в табл.10.10.
10.10. Свойства продукции из опилок
Показатель |
Пластик из МДПО |
Пьезотермо- |
Тырсолит и пар- |
||
|
|
пластик |
келит |
||
Плотность, кг/м3 |
1200 -1380 |
1350-1430 |
950 -1100 |
||
Предел прочности , МПА |
|
|
|
|
|
при статическом изгибе |
49 -80 |
25 - 40 |
23 |
- |
28 |
при сжатии |
98 - 108 |
60 -80 |
|
- |
|
при растяжении |
- |
20 -25 |
|
- |
|
Твердость по Бринелю, |
2 - 3,1 |
1,5 - 1,9 |
0,9 |
- |
1,2 |
МПа |
|
|
|
|
|
Водопоглощение,% |
2 - 3 |
2- 4 |
15 |
- |
45 |
Разбухание по толщине, % |
0,4 - 1,0 |
2 - 4 |
10 |
- |
25 |
10.4.3. Использование отходов как топлива
Возможны два способа использования мягких отходов в виде топлива - сжи- гание вместе с щепой и дробленкой или в самостоятельном потоке. Однако на- личие мелкой фракции (опилок и пыли) резко снижает производительность и КПД топок и сушильных агрегатов, повышает их пожароопасность. Поэтому широко применяется модернизация существующих топок и систем топливопо- дачи путем перевода их на факельный или факельно - вихревой способ сжигания смеси мягких отходов с газом или мазутом. Такой опыт имеют Усть-Ижорский ФК и ПДО “Житомирдрев”, Таганрогский МК и другие предприятия.
В последние годы мягкие отходы все шире используют на топливо в виде брикетов или окатышей для квартирных печей и каминов (табл.10.11). Плот- ность брикетов в 2,5 - 3 раза выше, чем у исходного материала, поэтому требу- ются меньшие емкости для хранения и транспортировки, достигается повышен- ная температура горения, не требуются системы дозирования и взвешивания. Наиболее широко производство брикетов распространено в США, Японии, За- падной Европе.
Предпочтительная форма брикетов - цилиндрическая или шашечная, так как она требует более простой брикетирующей установки. Цилиндрические могут изготовляться с внутренним отверстием диаметром 13 - 17 мм, что повышает интенсивность горения. Для этой же цели в смесь прессуемых отходов вводят специальные добавки (1,5 - 3%).
Схема производства брикетов показана на рис. 10.9. По такой схеме исполь- зуются отходы на Таллиннском ФМК, имеющем импортную установку из Фин- ляндии. Имеет перспективы и производство топливных брикетов - окатышей диаметром 3 - 12 мм и длиной 6 - 25 мм, причем начальная влажность сырья мо- жет быть до 35%.
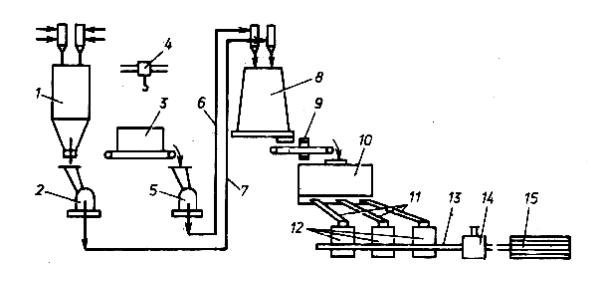
211
10.5. Переработка и использование коры
Кора может использоваться во внутреннем слое трех - и пятислойных стру- жечных плит. При отсутствии окорки измельчению подлежит шпон - рванина с корой, а при наличии окорочных станков - самостоятельный поток коры. Иссле- дования ЦНИИФ показали, что трехслойные плиты при любом содержании коры во внутреннем слое в 1,2 - 1,5 раза прочнее, чем однослойные. Во внутреннем слое может содержаться до 40 - 50% измельченной березовой коры. Несколько худшие результаты дает осиновая кора, для которой приходится увеличивать со- держание связующего с 9 - 9,5% до 10,5 - 11% во внутреннем слое (от массы аб- солютно сухой древесины).
Шпон - рванина может содержать до 30 - 35% коры. Она измельчается снача- ла на барабанных рубительных машинах, а затем на центробежных стружечных станках ДС-5 или ДС-7. При этом наблюдается повышенное содержание мелких частиц и пыли, на 40 - 50% состоящих из коры. После отсортировывания этих фракций содержание коры в стружке уменьшается до 20 - 25%, что благоприят- но влияет на все физико - механические показатели плит.
Использование коры, отбираемой непосредственно от окорочных станков, не получило промышленного применения из-за сложностей технологии. По данным ЦНИИМОД, наиболее целесообразно перерабатывать такие отходы путем одно- кратного измельчения в специальных корорубках, мельницах или дробилках (табл.10.13). Как показали исследования, полученный продукт при переработке коры хвойных пород содержит не более 7 - 13% крупной фракции (- / 7) и 13 - 15% мелкой фракции (1/0) и вполне пригоден для использования в плитном про- изводстве.
10.13. Оборудование для измельчения коры
Параметр |
Корорубка |
Мельница |
|
|
КР-6 |
МК-5-1 |
МК-10 |
Производительность, пл.м3/ч |
6 |
5 |
10 |
Диаметр ротора, мм |
540 |
600 |
1000 |
Количество, шт.: |
|
|
|
ножей |
2 |
4 |
8 |
бил |
17 |
24 |
32 |
контрножей |
2 |
24 |
32 |
Частота вращения ротора, мин-1 |
950 |
1500 |
735 |
Мощность привода, кВт |
40 |
55 |
75 |
Размеры, (L хB х H), м |
1,64 х 1,06 х 1,39 |
2,15 х 0,9 х 2,0 |
2,21 х 1,24 х 1,55 |
Масса, кг |
2 400 |
2 400 |
3 300 |
Кора является также объектом химической переработки. Из березовой и оси- новой коры получают фармакопейную смолу и деготь. Традиционная технология предусматривает сухую перегонку соковой бересты без доступа воздуха при вы- сокой температуре. Однако соковая береста является дефицитным продуктом, а сама технология отличается тяжелыми условиями труда. Учитывая необходи-
мость химической переработки отходов окорки в фанерном производстве в ЛТА
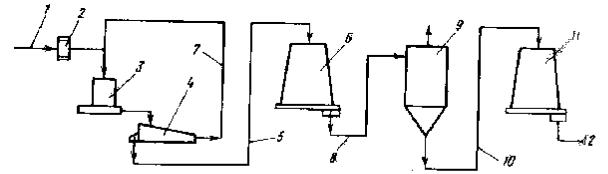
212
разработан способ получения дегтя методом газификации коры и последующей термообработки смол.
Подготовка коры к газификации заключается в удалении металлических включений и посторонних примесей, измельчении коры и отделении от нее луба. Последняя операция проводится методами флотации (береста легче воды), про- сеивания (частицы луба имеют меньшие размеры), либо пневмосепарации (час- тицы луба, как более тяжелые, оседают в начале камеры). Лучшие результаты обеспечивает последовательная работа механического отделителя и пневмосе- паратора.
Некоторые фанерные предприятия осуществляют заготовку коры и постав-
ляют ее как полуфабрикат на специализированные предприятия в соответствии с ТУ 13 - 707 - 83 на бересту. Наибольший опыт химической переработки бересты накоплен в ПО “Киевдревпром”, имеющем установку по производству дегтя мощностью до 5 т. Выход дегтя составляет 25% от массы сухой бересты, чис- ленность рабочих - 3 чел.
Луб, содержание которого в березовой коре составляет 60 - 80 %, может пере- рабатываться в муку, пригодную в качестве наполнителя к синтетическим клеям взамен дефицитной древесной муки. Процесс состоит из сушки луба до влажно- сти 4 - 8 % и размола на мельнице до однородной мелкой фракции, близкой к древесной муке №140 по ГОСТ 16361 - 80. Частицы муки имеют не плоскую, а овальную форму, но это не отражается на качестве клея и фанеры. Оптимальное количество наполнителя - 4 %.
Кора является очень важным топливным ресурсом. Гипродревом и рядом
других организаций создан типовой комплект оборудования и проект участка подготовки коры к сжиганию производительностью до 3 т/ч (рис.10.10).
Рис.10.10. Схема подготовки отходов окорки как топлива: 1 - конвейер для отходов окорки, 2 - металлоискатель, 3 - мельница, 4 - виброгрохот, 5,8,10 - конвейеры конди- ционной щепы; 6,11 - бункеры - накопители коры, 9 - сушильный агрегат
Сушка коры возможна по двум вариантам - в циклонно-спиральной сушилке отходящими газами котельной или в топочно - сушильном агрегате в комбина- ции с барабаном. В первом случае кора имеет влажность 50 - 60% и подается в топку. Во втором случае примерно половина коры подается в бункер как товар- ная, а вторая половина направляется в топку котлоагрегата, где сжигается, а га- зы подаются в циклонно - спиральную сушилку.