
РГВ, Пилипец В.И. Часть 1
.pdf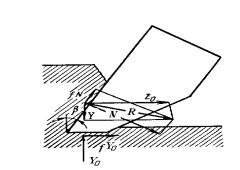
Суммарное усилие при резании угля равно
Pz + fPy + fPx,
где f — коэффициент трения.
Эти составляющие в процессе резания не остаются постоянными, так как процесс носит неравномерный скачкообразный характер, что связано с физико-механическими свойствами угля и периодичностью отделения элементов среза. Составляющие суммарного усилия могут быть определены экспериментально с помощью трехкомпонентного динамометра.
При движении резца (рис. 2.4), на его переднюю грань действуют по нормали сила N и сила трения разрушенного угля о переднюю грань резца fN. Равнодействующая этих сил R может быть разложена на две составляющие: сопротивление резанию передней гранью резца Z0 и сопротивление подаче резца на забой Y. При затуплении резца на его торцовую площадку действует сила Y0 и сила трения fY0.
Рис.2.4 Схема сил, действующих на резец
На боковые грани резца действуют нормальные и касательные силы, которые также могут быть разложены на составляющие в направлении осей х, у, z.
Геометрическая сумма проекций всех действующих сил на ось z представляет собой силу резания Pz, на ось y — силу подачи Py, на ось х — результирующую боковую силу Px, действующую на резец.
Из всех действующих сил только сила Pz совершает полезную работу, разрушая уголь. Для уменьшения остальных сил резцы должны быть заточены, иметь рациональную форму и размеры; кроме того, должен быть подобран рациональный режим резания.
Срез породы, создаваемый резцом характеризуется тол-
11
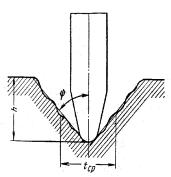
щиной, шириной и формой.
Толщина среза h (рис.2.5)— это заглубление резца при его подаче на забой, измеренное по нормали от предыдущей линии резания.
Средняя ширина среза tср
соответствует средней ширине борозды, образовавшейся за один проход резца при установившемся режиме резания.
Рис.2.5 Элементы среза породы
Угол бокового развала ,
это угол между боковой поверхностью борозды резания и плоскостью, проходящей по оси резца и перпендикулярной поверх-
ности забоя. Обычно = 25 — 85°. Для вязких углей его значение меньше, чем для хрупких. С уменьшением толщины среза h
значения увеличивается.
Сечение среза определяется из выражения
S = tcp h.
Согласно ОСТ 24.070.03 для забойных резцов рекомендуется принимать следующие минимальные значения средней величины сечения среза:
при бароцепных исполнительных органах S = 20 35мм2; при буровых - S = 50 60 мм2;
при барабанных и шнековых - S = 150 250 мм2. Меньшие значения сечения среза в указанных диапазонах
принимаются для машин, работающих на вязких углях. Различают следующие формы среза.
1.Блокированный срез в щели (рис. 2.6 а). Развал борозды отсутствует; резец работает в тяжелых условиях; усилия резания и энергозатраты максимальны.
2.Полублокированный (угловой) срез (рис. 2.6 б). Резание производится в углу, когда развал борозды возможен только в одну сторону. Срез такого вида образуется, например, при ра-
12

боте резцов, занимающих крайние положения в режущей цепи врубовой машины или исполнительном органе комбайна, и при работе нижнего ножа струга. Энергозатраты здесь ниже, чем в первом случае.
Рис.2.6 Формы среза
3.Эталонный срез с выровненной поверхностью (рис.2.6в).
Развал борозды при таком срезе возможен в обе стороны. При работе исполнительных органов угледобывающих машин эталонный срез не наблюдается, так как после резания поверхность забоя неровная. Энергозатраты на разрушение здесь ниже, чем при предыдущих срезах.
4.Полублокированный повторный срез (рис. 2.6 г). Степень обнажения забоя в таком срезе больше, чем в рассмотренных вариантах, т.к. создается две плоскости обнажения. Эта схема эффективна и характерна для большинства исполнительных органов выемочных машин. Примером повторного среза может служить работа резцов режущей цепи, кроме крайних и средних.
5.Шахматный (сотовый) срез (рис. 2.6 д) представляет со-
бой разновидность полублокированного повторного среза, когда четные срезы чередуются с нечетными и резание производится по целичкам угля высотой h. Особых преимуществ перед предыдущей схемой эта схема не имеет.
13
6. Тангенциальный (подрезной) срез (рис. 2.6 е) отличается от полублокированного повторного среза расположением
оси резца под углом к поверхности разрушения. Удельные энергозатраты на разрушение при таком срезе в 1,3—1,8 раза меньше, чем при других, поэтому тангенциальное резание является новым перспективным способом резания угля.
Толщина среза порoды принимается равной b = 05h. Тангенциальные резцы снимают срез большей толщины (h = 50-80 мм), что улучшает сортность угля и снижает энер-гозатраты.
Величина углубки, т.е. толщина стружки, которую снимает каждый резец породоразрушающего инструмента определяется из выражения
h = Vп /n i,
где Vп –скорость подачи резца, м; n-число оборотов породоразрушающего инструмента, об/мин; i-число резцов в породоразрушающем инструменте, шт.
Величину углубки можно определить по формуле, учиты-
вающей геометрию резца
h = cos α cos2 φm P /sin (α + 2 φm) σв d ,
где α-угол заточки резца, градус; φm-угол трения, градус; σв- предел прочности породы на вдавливание, Па.
Сила подачи резца равна
Т = 0,5 σсж i(kхр μк h + 0,5 c2) d, Н,
где σсж –временное сопротивление породы сжатию, Па; kхр- коэффициент, учитывающий хрупкость породы; μк – уоэффициент трения о породу; c –ширина торцовой площадки на периферии главной кромки резца,м; d –длина резца,м.
Угол наклона винтовой линии, описываемой любой точкой лезвия резца равен
θ=arctg h/2 π rх ,
где rх -расстояние от оси вращения резца до точки лезвия относительно которой определяется угол наклона.
Истинная глубина внедрения резца h0 равняется высоте лезвия резца, находящегося в непосредственном контакте с породой в момент скалывания элемента стружки g (рис.2.1).
В процессе работы резец затупляется. Если предположить что резец находится в статическом равновесии, то проекция опорной поверхности резца на породу SД, т.е. на плоскость,
14
перпендикулярную геометрической оси породоразрушающего инструмента, будет определяться как
Sд =Р/Рш (1+r/Рш),
где r –удельное сопротивление внедрению резца, вызванное действием сил трения на гранях резца.
Исследования Ф.А.Шамшева позволяют принять для твердых пород условие r « Рш. При таком условии отношение r/Рш « 1 и им по отношению к 1 можно пренебречь. Поэтому можно принять
Sд =Р/Рш.
Величина Р/Рш =Sк есть конечная площадь затупления резца на границе фазы объемного и усталостного разрушения породы. Если время работы резца в фазе объемного разрушения записать tк, можно принять
Sд =d lк tgα,
где d –площади износа (длина резца); α –угол заострения лезвия резца.
Из этого выражения, с учетом того, что Р/Рш =Sк можно найти высоту изношенной части лезвия резца за время tк
lк=Р/ Рш d tgα.
Средняя скорость износа резца в момент времени tк равна
Vи= lк / tк..
Оптимальное время затупления резца можно определить из
выражения
tк..=Р/ 2 n ηз μк tgα π D d Рш2,
где n –число оборотов породоразрушающего инструмента, об/мин; ηз –коэффициент износа резца, мм/Нмм; μк –коэф- фициент трения на контакте резца с породой в момент tк.;D –ди- аметр породоразрушающего инструмента,мм.
Мощность, затрачиваемая на разрушение породы в начале работы резца (по Ф.А.Шамшеву) равна
W1 = 0,137 10-5 P π D n /60, кВт.
Мощность, затрачиваемая на трение резцов о породу в конце работы породоразрушающего инструмента определяется из
выражения
W2 = 10-5 P μк π D n /60, кВт.
Суммарная мощность
W = W1+W2.
15
W = (0,137 + μк) 10-5 P π D n /60, кВт.
При выводе формулы суммирование составляющих мощности произведено с учетом того, что износ и глубина разрушения породы больше в начальный момент работы незатупленными резцами. Однако чтобы учесть снижение W1 при износе резца, в составляющую W2 введен коэффициент трения μк. Кроме того, при выводе формулы использовано отношение Генки
Рш/ σсж = 2 π +1.
Истиранием порода разрушается при использовании мелкоалмазного породоразрушающего инструмента (коронок) с хорошо закрепленными в металлической матрице алмазами.
Торец такой коронки обладает шероховатостью. Выступами шероховатости (элементарными резцами), являются мелкие алмазы или неровности на рабочей поверхности более крупных алмазных резцов. Такой торец мелкоалмазной коронки относится к грубой шероховатости и характеризуется линейным распределением выступов шероховатости по высоте. Если слой алмазов, возвышающийся над поверхностью матрицы, представить рассеченным по высоте рядом параллельных равноотстоящих плоскостей и подсчитать число элементарных резцов, которое попадает в каждую плоскость, начиная отсчет от нулевой плоскости (m =0), касательной к алмазам с наибольшим выступом, то число резцов х, попадающих в m-ю плоскость можно определить из выражения
х = а + к m,
где а- число шероховатостей, касающихся начальной плоскости; к- постоянная величина; m- порядковый номер секущей плоскости.
Торец коронки, обладая линейной разновысотностью резцов, непрерывно восстанавливается в процессе разрушения породы вследствие количественного износа алмазов.
Разновысотность алмазов оказывает существенное влияние на распределение осевого усилия между элементарными резцами, так как от нее зависит число одновременно работающих резцов на забое.
16
Осевое усилие на мелкоалмазный инструмент выбирается из выражения
С = qуд S,
где qуд –удельное давление на инструмент; S – площадь торца породоразрушающего инструмента.
Удельное давление зависит от крепости пород и типа алмазной коронки и принимается в пределах 0,05 – 0,15 Н/м2.
Алмазные резцы защищены от скалывания телом матрицы. Если осевое усилие на забой остается постоянным, то алмазы затупляются и инструмент теряет свою режущую способность. Для того чтобы алмазы по мере износа постепенно обнажались и происходило дальнейшее разрушение породы необходимо осевое усилие увеличивать.
К окончанию работы коронки осевое усилие обычно возрастает вдвое.
Число оборотов мелкоалмазной коронки может быть очень высоким и достигать значений 2000 об/мин.
Ограничение числа оборотов связано с возник-новением чрезмерных напряжений в инструменте и вибраций, вызванных действием центробежных сил. При возникновении вибрации нормальный процесс разрушения нарушается, расход мощности сильно возрастает, проходка прекращается.
При работе мелкоалмазного породоразрушающего инструмента мощность затрачивается на разрушение породы и на трение алмазов (резцов) о породу. Наибольшие затраты мощности расходуются на разрушение породы.
Расчетная формула для определения мощности при разрушении горных пород истиранием мелкоалмазным породораз-
рушающим инструментом имеет вид
W = 2 10-7 P D n, кВт.
Для повышения эффективности разрушения процесс резания и скалывания совмещается с вдавливанием. При таком способе вдавливание происходит за счет ударов, наносимых по породе твердым телом.
По способу приложения осевого усилия и силовых ударных нагрузок к породе различают:
ударно-поворотный способ; ударно-вращательный способ;
17
вращательно-ударный способ.
Ударно-поворотный способ разрушения породы
При ударно-поворотном способе разрушение породы происходит за счет нанесения периодических ударов с частотой от 1700 до 3700 ударов в минуту по породе инструментом, прижатым к породе с небольшим осевым усилием, достаточным для прижатия породоразрушающего инструмента к породе с целью лучшей передачи энергии удара. Причем перед каждым следующим ударом породоразрушающий инструмент поворачивается на некоторый угол (обычно 150), что обеспечивает равномерное разрушение породы по окружности.
Ударно-вращательный способ разрушения породы
При ударно-вращательном способе разрушения непрерывно вращающимся твердосплавным породоразрушающим инструментом (скорость вращения 10-40 об/мин) происходит совместное воздействие на породу постоянно прикладываемого осевого усилия (10-15 кН, достаточного для преодоления силы отдачи, возникающей в момент удара и для постоянного внедрения резца в породу), крутящего момента и слабых непрерывных ударных импульсов частотой 2000-3500 ударов в минуту, генерируемых ударным механизмом (гидроударником или пневмоударником). Причем дополнительное воздействие ударных импульсов, передаваемых породе, значительно повышает эффективность ее разрушения.
Такой способ обычно применяется в породах небольшой крепости (f=6-14).
Втвердых и крепких породах, для которых характерно хрупкое разрушение, основной эффект обеспечивается ударными импульсами, а перемещение резцов по забою между ударами имеет второстепенное значение и способствует выравниванию и подчистке забоя.
Впластичных и вязких породах основное влияние в разрушении принадлежит резанию, которое обеспечивается крутящим моментом и осевым усилием.
Согласно волновой теории удара, при соударении бойка ударного механизма с нижней наковальней, связанной с поро-
18
доразрушающим инструментом возникает волна напряжения сжатия, которая, перемещаясь по наковальне, достигает породоразрушающего инструмента, внедряя резцы в породу.
Эффективность передачи ударных импульсов зависит от положения резцов относительно забоя в момент удара. Оптимальная передача энергии удара достигается в том случае, когда резцы контактируют с горной породой в момент прихода волны напряжения сжатия. Если такого момента нет, то волна напряжения сжатия отражается, не выполняя полезной работы, и хотя она через короткое время возвращается, но теряет часть своей энергии. Практически после каждого удара резец отходит от забоя в результате упругих свойств породы. При затупленных резцах инструмент может отходить почти сразу же по достижении ударным импульсом забоя.
Таким образом, даже при оптимальных условиях, т.е. при максимальном к.п.д. передачи энергии удара, наблюдается отход инструмента от забоя на некоторое расстояние. Следовательно, величину осевого усилия нужно выбирать так, чтобы она обеспечивала надежный контакт с горной породой.
В твердых и крепких породах, с высоким модулем упругости на контакте резец - порода, возникают большие напряжения сжатия при достижении критических значений которых, превышающих предел прочности породы на вдавливание происходит скалывания породы.
Наиболее эффективного использования ударной энергии при определенной частоте ударов можно добиться в том случае, если после каждого удара резцы будут перемещаться на новое место, соответствующее оптимальному углу поворота инструмента. Угол поворота или расстояние от одного положения резца к другому, измеряемое по периферийной окружности забоя, определяется размерами лунки разрушения. Для наиболее эффективного использования ударной энергии, лезвие резца должно перемещаться после каждого удара на ширину лунки разрушения. В этом случае удар будет наноситься по новому месту, а образованная предыдущим ударом лунка разрушения будет способствовать наилучшему сколу и проработке поверхности забоя.
19
Таким образом, оптимальное число оборотов породоразрушающего инструмента можно определить из выражения
n0 = nу 60 / n1,
где n0- оптимальное число оборотов породоразрушающего инструмента, об/мин; nу- частота ударов ударного механизма, 1/c; n1- количество ударов, необходимое для разрушение забоя за один оборот породоразрушающего инструмента, 1/с.
Количество ударов, необходимое для разрушение забоя за один оборот определяется по формуле
n1 = π dк tgφ0 /2 h i,
где dк- наружный диаметр породоразрушающего инструмента,м; φ0- угол наклона образующей лунки разрушения, град; h- величина углубки резцов в горную породу, м; i- число резцов в породоразрушающем инструменте, шт.
Известно, что при ударных видах разрушения, в случае армирования породоразрушающего инструмента клиновыми резцами, образуются лунки разрушения, у которых угол наклона образующих лунки разрушения имеет вполне определенную величину, в зависимости от характеристики пород.
Углы наклона образующих лунок разрушения для некоторых горных пород приведены в таблице 2.1.
|
Таблица 2.1 Углы наклона образующих лунок |
|
|
разрушения |
|
|
Наименование пород |
Угол наклона лунки, |
|
|
град |
|
Мягкий глинистый |
32 |
|
сланец |
26 |
|
Глинистый сланец |
32 |
|
Известняк плотный |
25 |
|
Песчаник мягкий |
18 |
|
Песчаник крепкий |
29 |
|
Мрамор крупнозерни- |
25 |
|
стый |
17 |
|
Мрамор мелкозерни- |
27 |
|
стый |
20 |
|
Базальт |
15 |
|
Диабаз |
|
|
Гранит мелкозерни- |
|
|
стый |
|
|
Кварцит крепкий |
|
20 |
|
|
|
|