
КПСБ-задание / Материалы курсового / Пособие по СБ
.pdf
По назначению винты делятся на крепежные и установочные. На рис. 21, а-г показаны соединения крепежными винтами. Установочные винты имеют специальную форму и применяются для фиксации одной детали относительно другой (см. рис. 21, д).
а) |
б) |
в) |
г) |
д) |
Рис. 21. Винтовые соединения
ПОДБОР СТАНДАРТНЫХ КРЕПЕЖНЫХ ДЕТАЛЕЙ ВИНТОВОГО СОЕДИНЕНИЯ
ПРИМЕР 1. Выполнить соединение крышки 1 с корпусом 2 винтом по ГОСТ 1491 – 80 с шайбой по ГОСТ 11371 − 78 (рис. 22, а). Изображения представлены в масштабе 2:1. Материал корпуса Сталь 45.
а) |
б) |
в) |
г) |
Рис. 22. Изображение на чертежах соединения винтом с цилиндрической головкой и шайбой. Винт ввинчивается в глухое резьбовое отверстие
1.Определим форму винта и шайбы. В указанных стандартах находим, что соединение необходимо осуществить винтом с цилиндрической головкой и обычной нормальной шайбой в виде плоского тонкого диска с отверстием.
2.Определим диаметр резьбы винта и диаметр отверстия шайбы. Для определения диаметра резьбы винта необходимо измерить диаметр резьбы в отверстии корпуса 2 и пере-
21
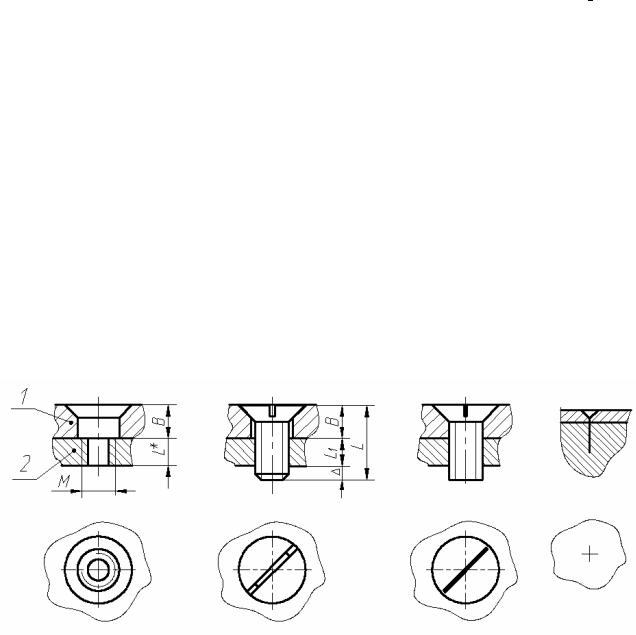
считать в действительный размер с учетом масштаба (у нас разделить на два). Так для измеренного размера резьбы 10 мм действительный размер резьбы в отверстии будет 5 мм. Такая же резьба М5 должна быть и у винта. Для резьбы М5 по ГОСТ 1491 – 80 определяем размеры головки винта. Для винта с резьбой М5 необходимо применить шайбу с условным обозначе-
нием «Шайба 5…».
3. Определим длину винта по вышеприведенной формуле L = S + B + L1. Обращаем внимание, что в длину данного винта входит его длина без головки. Толщину шайбы S определим по ГОСТ 11371 − 78. Для выбранной шайбы толщина равна 1мм. Пусть измерение размера B дало величину 9 мм. Значит, действительная толщина крышки 1 равна 4,5 мм. Глубина завинчивания винта в резьбовое отверстие корпуса L1 должна быть для стали не менее диаметра резьбы, т.е. не менее 5 мм. В то же время винт не должен доходить до границы резьбы в резьбовом отверстии, т.е. он должен быть короче его максимальной длины, которая определяется глубиной резьбы L*. Для измеренного значения L* равного 18 мм, его действительная величина 9 мм и тогда расчетная максимальная длина винта равна 15 мм. Таким образом, расчетная минимальная длина винта равна 10,5 мм, расчетная максимальная длина равна 15 мм. По ГОСТ 1491 – 80 выбираем винт М5 длиной 11 мм (подсчитанное значение минимальной длины винта нужно округлить до ближайшего большего стандартного значения).
4. Дополним изображения крышки 1 и корпуса 2 изображениями подобранных винта с шайбой в масштабе 2:1. Построенное таким образом по действительным размерам составных частей изображение винтового соединения называют конструктивным (см. рис. 22, б).
На сборочных чертежах согласно ГОСТ 2.109 − 73, соединения показывают, как правило, упрощенно, так как изображено на рис. 22, в. На рис. 22, г показано условное изображение данного винтового соединения для случая, когда стержень винта на чертеже приходится вычерчивать диаметром 2 мм и менее.
ПРИМЕР 2. Выполнить соединение пластины 1 с основанием 2 винтом по ГОСТ 17475-90 (рис. 23, а). Изображения выполнены в масштабе 1:1. Материал основания латунь
Л63.
Рис. 23. Изображение на чертежах соединения винтом с потайной головкой. Винт ввинчивается в сквозное резьбовое отверстие
1.Определим форму винта. По ГОСТ 17475-90 устанавливаем, что для соединения указанных деталей нужно применить винт с потайной головкой.
2.Определим диаметр резьбы винта. Измеренное значение резьбы в отверстии основания равно 6 мм. Поэтому выбираем винт с такой же резьбой М4. Для резьбы М4 по ГОСТ 17475-90 определяем размеры головки винта.
3.Определим длину винта. Отметим, что в длину данного винта входит его полная длина с головкой (см. стандарт). Далее отметим, что глубина завинчивания винта в резьбовое
22
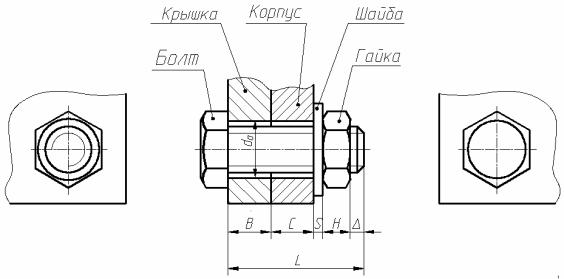
отверстие детали из латуни должна быть не менее диаметра резьбы. Существует рекомендация: если толщина дет. 2 соизмерима с диаметром резьбы в сквозном отверстии, то винт должен ввинчиваться на всю толщину этой детали, а его конец должен выступать за пределы дет.2 на величину не менее ∆=2..3р (здесь р – шаг резьбы), что соответствует 0,25М, где М – диаметр резьбы винта. И тогда длина винта определится формуле L = B + L* + ∆. Пусть измеренное значение толщины B равно 5 мм, а толщины L* равно 4 мм. Таким образом, расчетная минимальная длина винта равна 10 мм. По ГОСТ 17475-90 выбираем винт М4 с ближайшим большим значением длины 11 мм.
4. На рис. 23, б показано конструктивное изображение рассчитанного соединения, на рис. 23, в – его упрощенное изображение, на рис. 23, г – условное изображение.
3.1.3. Болтовое соединение
В комплект болтового соединения входят (рис. 24):
1)соединяемые детали, которые имеют гладкие сквозные цилиндрические отверстия. Диаметр отверстий несколько больше диаметра резьбы болта;
2)крепежные стандартные детали: болт, гайка, шайба (при маленьких значениях диаметра резьбы в качестве болта применяется винт).
Рис. 24. Болтовое соединение
Конструктивное изображение болтового соединения в данном задании разрабатывается, исходя из известных величин: диаметра отверстия d0 в соединяемых деталях и их толщины
В и С.
Форма и геометрические размеры болта, гайки и шайбы определяются указанными в задании стандартами. Диаметр резьбы болта М должен быть немного меньше диаметра отверстий. Диаметры резьбы гайки и шайбы должны быть равны диаметру резьбы болта. Конец болта должен выступать за гайку на величину ∆=2..3р (здесь р – шаг резьбы), что соответствует 0,25М, где М – диаметр резьбы болта.
Длина болта вычисляется по формуле:
L=B+С+S+H+ ∆.
Полученное значение L округляется до ближайшего стандартного.
В спецификацию учебного чертежа болты и гайки записывают по типу:
Болт М5х30 ГОСТ …, где М5 – метрическая резьба с внешним диаметром 5 мм, крупным шагом 0,8 мм (см. табл. 1), 30 – длина стержня болта в мм;
Гайка М5 ГОСТ …, где М5 – метрическая резьба диаметром 5 мм.
23
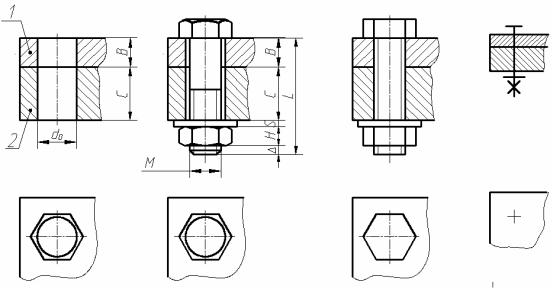
Пример записи шайбы приведен в п. 3.1.2.
При построении конструктивных изображений резьбовых соединений со стандартными крепежными деталями принято:
1) стандартные крепежные детали в продольных разрезах показывают нерассеченны-
ми;
2)зазор между стенкой отверстия и крепежной деталью, когда он на чертеже получается меньше 1 мм, допускается для удобства вычерчивания немного увеличить (до 1 мм);
3)шлиц для отвертки в головке винта вычерчивается так, как показано на рис. 18 и на рис. 20, 21 под углом 45°;
4)шестигранные головки болтов и гаек на главном изображении показывают с максимальным количеством граней (рис. 25, б, в).
ПОДБОР СТАНДАРТНЫХ КРЕПЕЖНЫХ ДЕТАЛЕЙ БОЛТОВОГО СОЕДИНЕНИЯ
ПРИМЕР 3. Выполнить соединение дет. 1 и дет. 2 болтом по ГОСТ 7805-79 с гайкой по ГОСТ 5916-70 и шайбой по ГОСТ 11371-78 (см. рис. 25,а). Масштаб изображений 1:1.
а) |
б) |
в) |
г) |
|
Рис. 25. Изображение на чертежах болтового соединения |
|
1.По указанным в задании стандартам устанавливаем, что для соединения дет.1 и дет.2 нужно применить болт с шестигранной головкой, низкую шестигранную гайку и обычную нормальную шайбу.
2.Диаметр стержня болта должен иметь ближайшее меньшее значение по отношению
кдиаметру отверстия в соединяемых деталях. Для диаметра отверстия в дет. 1 и дет. 2 равного 12 мм по ГОСТ 7805-79 определим ближайшее меньшее значение диаметра резьбы болта 10 мм. Такую же резьбу будет иметь гайка. Для болта с резьбой М10 применим шайбу с условным обозначением Шайба 10….
3.Длину болта определим по формуле L = B + C + S + H + ∆. Пусть В = 8 мм С = 20 мм. Толщина шайбы S по ГОСТ 11371-78 равна 2 мм. Толщина гайки H по ГОСТ 5916-70 равна 6 мм. Длина выступающего за пределы гайки конца болта ∆ выбираем равным 0,25М, что соответствует 2,5 мм. Расчетное значение длины болта равно 38,5 мм. По ГОСТ 7805-79 выбираем ближайшее большее стандартное значение длины 40 мм.
4.На рис. 25, б показано конструктивное изображение рассчитанного соединения, на рис. 25, в – его упрощенное изображение, на рис. 25, г – условное изображение.
24
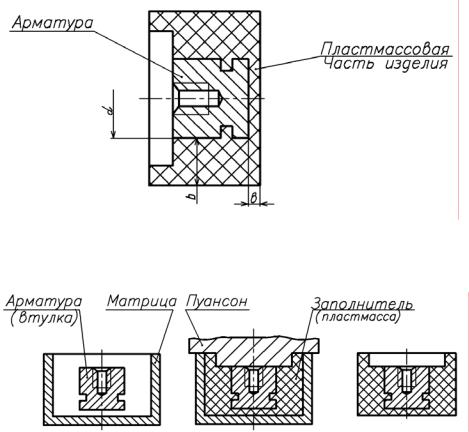
3.2. СОЕДИНЕНИЕ ОПРЕССОВКОЙ
В радиоэлектронных устройствах достаточно широко применяются соединения опрессовкой. Соединение опрессовкой представляет собой неразъемное соединение, которое получается при обволакивании поверхностей металлических деталей (их называют арматурой) жидкой пластмассой с дальнейшей её полимеризацией. Изделия, получаемые опрессовкой, принято называть армированными изделиями. Соединение опрессовкой показано на рис. 26.
Рис. 26. Армированное изделие (соединение опрессовкой)
а) |
б) |
с) |
Рис. 27. Технология изготовления армированного изделия
Технологический процесс опрессовки отображен на рис. 27. Сначала изготавливают пресс-форму (матрицу), внутренняя полость которой повторяет формы пластмассовых поверхностей армированного изделия. Потом в пресс-форму устанавливают в заданном положении готовую арматуру (см. рис. 27, а) и загружают туда нагретую до расплавленного состояния пластмассу. Под воздействием пуансона расплавленный состав заполняет формообразующую полость пресс-формы (см. рис. 27, б). Через некоторое время пластмасса полимеризуется и готовое армированное изделие (см. рис. 27, в) вынимают из матрицы.
К особенностям соединения опрессовкой относится то, что пластмассовая часть соединения отдельно от арматуры в виде детали не существует и отдельный чертеж на неё не разрабатывается. Все сведения, необходимые для формирования пластмассовой части, должны быть приведены на чертеже соединения (это форма и размеры пластмассовых поверхностей и размеры, определяющие положение в ней арматуры, а также указание марки пластмассы, которая записывается в спецификацию).
Арматура бывает различных типов: втулочная (рис. 28), стержневая (рис. 29), проволочная (рис. 30), листовая (рис. 31). Для того, чтобы арматура прочно соединялась с опрессовываемым материалом, ей придают специальную конфигурацию за счет канавок, проточек, вырезов, отверстий, отгибов, рифлений и т.п.
25
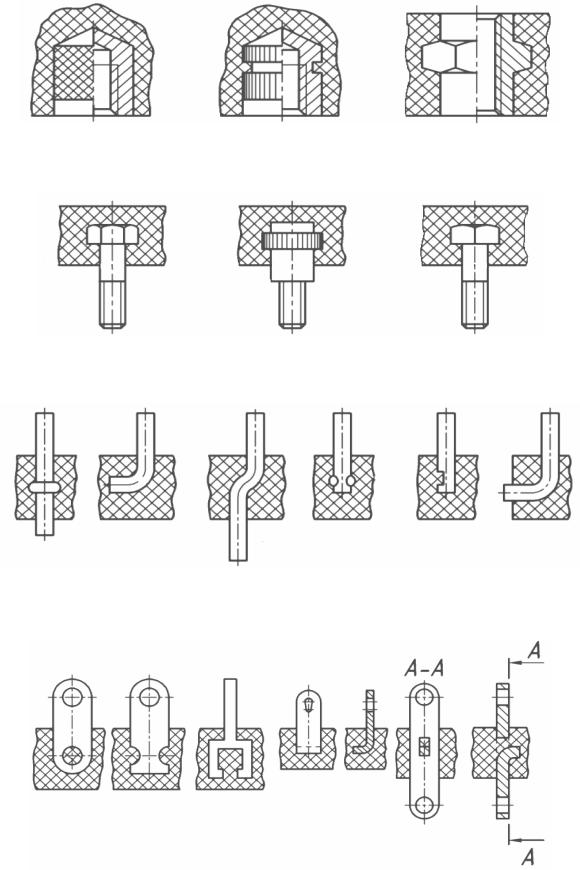
а) |
б) |
в) |
Рис. 28. Втулочная арматура
а) |
б) |
в) |
Рис. 29. Стержневая арматура
а) |
б) |
в) |
г) |
д) |
е) |
Рис. 30. Проволочная арматура
а) |
б) |
в) |
г) |
д) |
е) |
ж) |
Рис. 31. Листовая арматура
В радиоэлектронных изделиях арматура применяется в основном для увеличения механической прочности изделия и в качестве токопроводящих элементов.
26
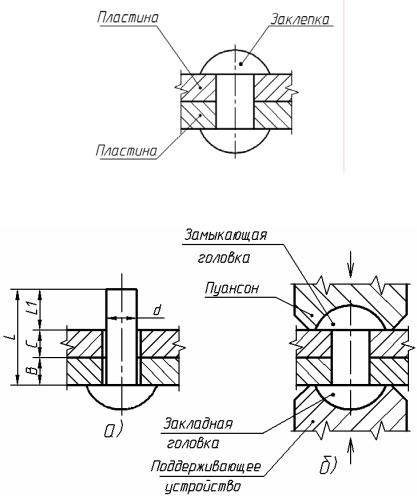
3.3 КЛЕПАНЫЕ СОЕДИНЕНИЯ
Соединения клепкой широко применяются в радиоприборостроении для прочного и надежного соединения изделий из различных материалов в таких конструкциях, где другие виды соединения применять нецелесообразно или невозможно. Существенным достоинством этого вида соединения является простота его выполнения.
Соединения клепкой являются неразъёмными и разделяются на два типа:
а) соединения составных частей при помощи специальных деталей-заклепок, конструкция которых стандартизирована;
б) соединения при помощи расклепывания, завальцовки или развальцовки непосредственно конца одной из соединяемых деталей.
3.3.1. Соединение заклепкой
На рис. 32 показано соединение двух пластин заклепкой с полукруглой головкой. Процесс получения такого соединения разъясняет рис. 33.
Рис. 32. Соединение заклепкой
Рис. 33. Процесс получения соединения заклепкой
В соединяемых деталях пробивают или сверлят отверстия несколько большего диаметра, чем диаметр заклепки. Затем вставляют заклепку (см. рис. 33, а) неподвижно закрепляют при помощи поддерживающего устройства ее закладную головку и ударяют пуансоном по выступающему концу заклепки. При этом формируется замыкающая головка (см. рис. 33, б), а стержень заклепки деформируется и заполняет отверстие без зазора.
Длину заклепки должна быть больше, чем толщина соединяемых деталей на величину L1, необходимую для формирования замыкающей головки (см. рис. 33, а). Величина L1 определяется формой замыкающей головки и выбирается по табл. 3.
27
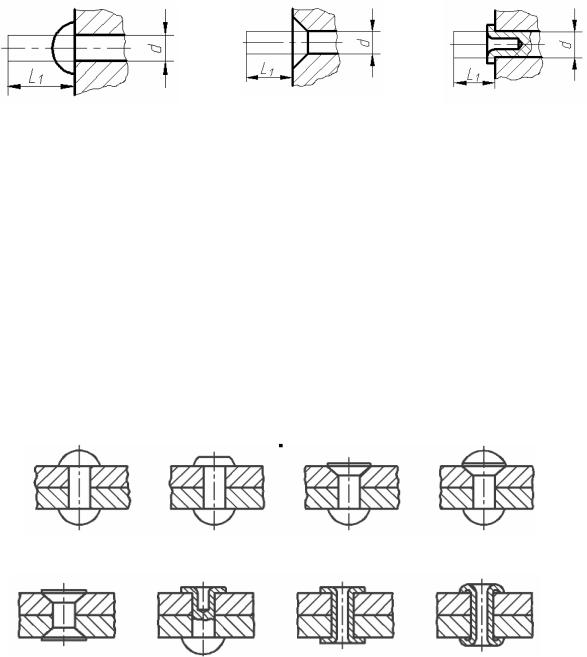
Длина заклепки вычисляется по формуле (см. рис. 33):
L= B + C + L1,
где L1 берется из табл. 2.
Полученное значение L округляется до ближайшего стандартного.
Вспецификации учебных чертежей приводят упрощенное условное обозначение заклепок по типу Заклепка 3х20 ГОСТ…, где 3 – диаметр заклепки в мм., 20 – длина стержня в мм.
Втабл. 3 приведены значения L1 в зависимости от диаметра заклёпки и формы замыкающей головки.
|
Длина выступающей части заклепки для формирования |
Таблица 3 |
|||
|
|
||||
|
|
замыкающей головки |
|
|
|
|
|
|
|
|
|
|
|
|
|
|
|
d |
L1 |
|
L1 |
d |
L1 |
0,8 |
1,4 |
|
0,6 |
1,2 |
0,9 |
1,0 |
2,0 |
|
0,8 |
1,6 |
1,0 |
1,6 |
2,3 |
|
1,0 |
2,0 |
1,0 |
2,0 |
2,5 |
|
1,3 |
3,5 |
1,2 |
2,5 |
3,5 |
|
1,4 |
3,0 |
1,3 |
3,0 |
4,0 |
|
1,6 |
4,0 |
1,5 |
4,0 |
5,0 |
|
2,6 |
5,0 |
2,0 |
5,0 |
6,0 |
|
3,0 |
6,0 |
2,5 |
На рис. 34 показаны соединения деталей стандартными заклепками: а…г –с полукруглой головкой; д – с потайной головкой; е – полупустотелой с полукруглой головкой; ж – пустотелой с плоскими краями; з – пустотелой со скругленной головкой.
На этом же рисунке показаны основные типы замыкающих головок (они показаны сверху): а – полукруглая; б – плоская; в, д – потайная; г – полупотайная; е, ж – цилиндрическая с плоскими краями; з – цилиндрическая со скругленными краями.
а) |
б) |
в) |
г) |
д) |
е) |
ж) |
з) |
Рис. 34. Соединения стандартными заклепками
28
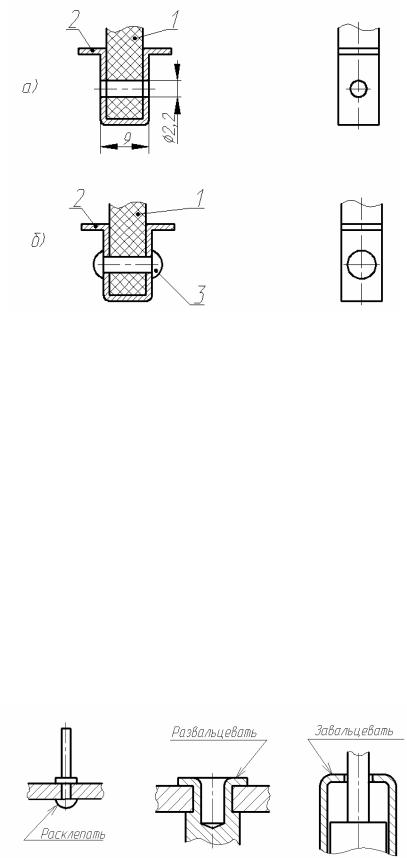
ПОДБОР СТАНДАРТНЫХ ЗАКЛЕПОК
ПРИМЕР 4. Выполнить соединение пластины 2 с корпусом 1 (рис. 35, а) заклепкой по ГОСТ 10299-80. Масштаб изображения 1:1.
Рис. 35. Подбор заклепки
Пусть измеренные значения общей толщины скрепляемых деталей и диаметра сквозного отверстия под заклепку равны соответственно 2,2 мм и 9 мм.
По ГОСТ 10299-80 находим, что ближайшее стандартное меньшее значение диаметра стержня заклёпки для этого отверстия равно 2 мм.
Для расчёта требуемой длины заклёпки к общей толщине скрепляемых деталей 9 мм прибавляем длину стержня, необходимую для расклёпывания L1=2,5 мм, взятую из табл. 3 для полукруглой головки и диаметра стержня 2 мм. В итоге получаем требуемую длину заклёпки, равную 11,5 мм. По ГОСТ 10299-80 выбираем из ряда стандартных длин ближайшее большее значения, т.е. 12 мм
На рис. 35, б показано соединение дет. 1 и дет. 2 подобранной заклёпкой 3.
3.3.2.Соединения расклепыванием, завальцовкой, развальцовкой
Вуказанных соединениях крепление деталей осуществляется за счет деформирования (расклепывания, завальцовки, развальцовки) конца одной из деталей, входящей в соединение. Для данного вида клепаных соединений на чертеже необходимо указывать на линии-выноске вид деформации (рис. 36).
Рис.36. Виды клепаных соединений
29
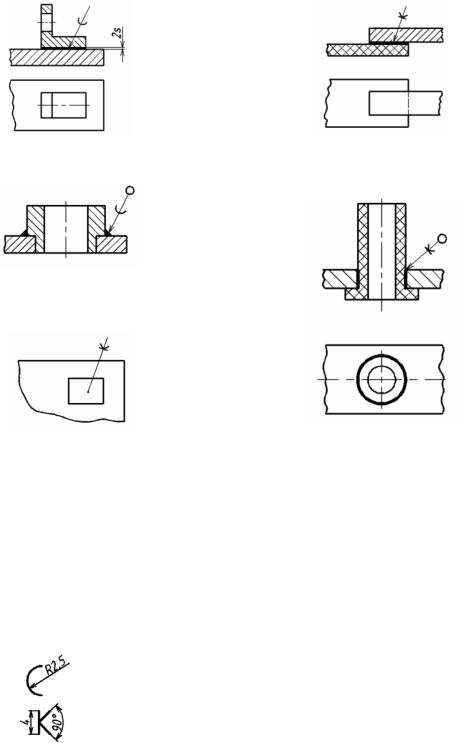
3.4 КЛЕЕВЫЕ И ПАЯНЫЕ СОЕДИНЕНИЯ
Паяные и клеевые соединения широко используют при монтаже электронной аппара-
туры.
В паяных и клеевых соединениях скрепляющим детали элементом является шов (соответственно паяный и клеевой).
Пайкой соединяют металлические детали, склеиванием можно соединять детали, сделанные из неоднородных материалов, например, металла и пластмассы.
Большинство припоев и клеев стандартизованы.
Соединение деталей пайкой показано на рис. 37, 39; склеиванием на рис. 38, 40, 41.
Рис. 37. Соединение пайкой |
Рис. 38. Соединение склеиванием |
Рис. 39. Соединение пайкой по замкнутому контуру
Рис. 41. Обозначение невидимого |
Рис. 40. Соединение склеиванием по |
|
замкнутому контуру |
||
клеевого шва |
||
|
Швы, которые получены пайкой и склеиванием, на чертежах (на видах и в разрезах) показывают по ГОСТ 2.313-82 условно линиями толщиной 2s, где s – толщина толстой сплошной линии (основной). Допускается в необходимых случаях паяные швы показывать так, как показано на рис. 39.
Для обозначения пайки и склеивания применяют условные знаки, которые помещают на линии-выноске:
–для пайки;
–для склеивания.
Условные знаки выполняются сплошной толстой линией, линию-выноску – сплошной тонкой. Линию-выноску заканчивают стрелкой, которая должна упираться в шов (см. рис. 37, рис. 38), или точкой, если указываются невидимые поверхности соединения (см. рис. 41).
30